Color plays a pivotal role in the success of any product made through injection molding. But how do we ensure that vibrant shade of red or that deep blue remains consistent throughout?
Common colorant mixing technologies in injection molding include dry mixing, masterbatch coloring, paste colorant coloring, and pigment pre-dispersion. Each method varies in cost, ease of use, and the uniformity of the coloring effect.
With this foundational knowledge, let’s delve deeper into each method and uncover the nuances that can truly transform your production processes.
Dry mixing is the cheapest colorant method in injection molding.True
Dry mixing is simple, low-cost but often results in uneven coloring.
How Does Dry Mixing Compare to Other Technologies?
Dry mixing in injection molding is a straightforward method, but how does it measure up against other techniques?
Dry mixing is a cost-effective, simple method but often results in uneven coloring compared to masterbatch, paste, and pre-dispersion methods.
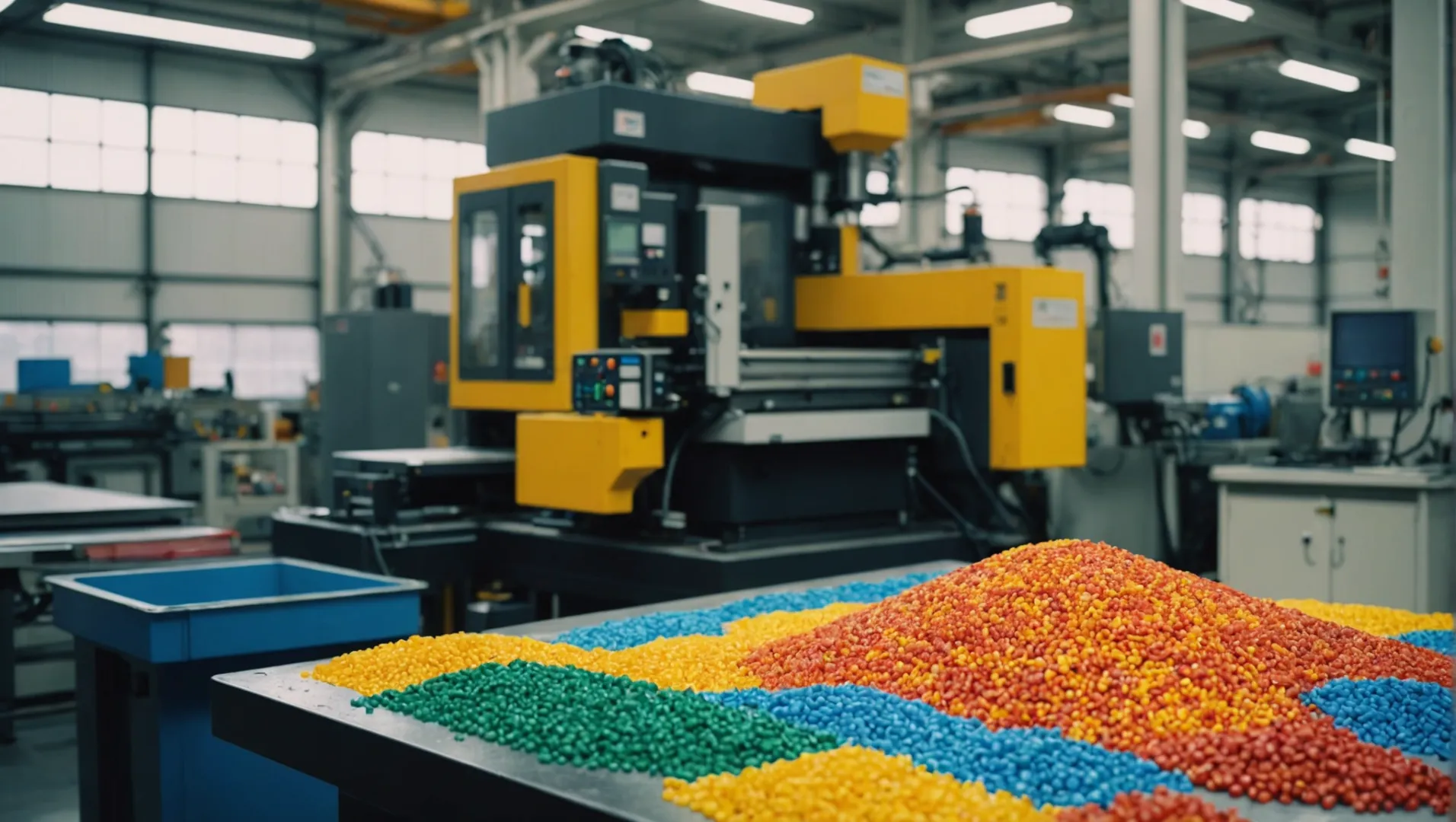
Dry Mixing: The Basics
Dry mixing involves directly blending color powder with plastic particles before injection molding. This method stands out for its simplicity and low cost. However, it’s crucial to note that dry mixing might not deliver the most uniform color and can result in dust issues.
Comparing Technologies: An Overview
To truly understand how dry mixing measures up, let’s compare it with other prevalent techniques:
-
Masterbatch Coloring: Here, color powder is combined with a carrier resin to form a masterbatch, which is then mixed with plastic particles. This process ensures even coloring and minimizes dust. However, it can be more expensive.
-
Paste Colorant Coloring: This method involves creating a paste colorant by mixing color powder with a liquid carrier. Like masterbatch, it offers uniform coloring and low dust emissions but at a higher cost.
-
Pigment Pre-dispersion: In this approach, a small amount of resin or dispersant mixes with the color powder to create a pigment pre-dispersion. It results in excellent coloring effects and minimal dust, yet it remains costly.
Technology | Cost | Color Uniformity | Dust Issues |
---|---|---|---|
Dry Mixing | Low | Moderate | High |
Masterbatch Coloring | High | High | Low |
Paste Colorant Coloring | High | High | Low |
Pigment Pre-dispersion | High | Very High | Very Low |
Factors to Consider
Choosing the right coloring technology depends on several factors:
- Product Requirements: Consider the product’s specific needs regarding color, performance, and cost.
- Production Process: Analyze production characteristics such as the type of injection molding machine and process parameters.
- Color Paste Performance: Evaluate dispersion, stability, and temperature resistance.
Practical Applications
For manufacturers prioritizing cost-effectiveness over precision, dry mixing can be an excellent choice. However, if uniformity and dust control are critical, technologies like masterbatch coloring1 might be more suitable. Ultimately, understanding these technologies enables better decision-making tailored to specific manufacturing objectives.
Dry mixing is the most cost-effective method.True
Dry mixing is noted for its low cost compared to other methods.
Masterbatch coloring results in high dust emissions.False
Masterbatch coloring minimizes dust emissions, unlike dry mixing.
What Are the Advantages of Masterbatch Coloring?
Masterbatch coloring offers precision and consistency in color application for injection molding, making it a preferred choice despite higher costs.
Masterbatch coloring ensures uniform color distribution, minimizes dust, and enhances color stability compared to other methods, albeit at a higher cost.

Enhanced Color Uniformity
Masterbatch coloring stands out for its ability to deliver superior color uniformity. By mixing color pigments with a carrier resin to form a concentrated masterbatch, this method ensures that colors are evenly dispersed throughout the plastic material. Unlike dry mixing coloring2, where color powders are directly mixed with plastic particles leading to potential streaks and inconsistencies, masterbatch coloring avoids these pitfalls.
Dust Minimization
In industrial settings, maintaining a clean environment is crucial. Masterbatch coloring significantly reduces the likelihood of dust formation, a common issue with dry mixing. This not only improves workplace conditions but also reduces the risk of contamination in the final product.
Stability and Customization
Masterbatch coloring also allows for enhanced stability in the final product. It can be tailored to meet specific requirements such as UV resistance or thermal stability. By working closely with suppliers, manufacturers can develop masterbatches that match exact specifications, ensuring that the end product performs as expected in various environments.
Cost Analysis
While masterbatch coloring is more expensive than some other methods, its advantages often justify the investment. The table below compares the costs and benefits:
Coloring Method | Cost | Color Uniformity | Dust Formation |
---|---|---|---|
Dry Mixing | Low | Inconsistent | High |
Masterbatch Coloring | High | Consistent | Low |
Paste Colorant Coloring | High | Consistent | Low |
Pigment Pre-dispersion | High | Consistent | Low |
Application Flexibility
The flexibility offered by masterbatch coloring in terms of applications is another significant advantage. It can be effectively used in various production processes and for products requiring precise color matching and performance properties. This flexibility makes it an attractive choice for industries ranging from automotive to consumer goods.
Choosing the right coloring method depends on several factors, including product requirements, production processes, and desired performance outcomes. By understanding the benefits of each technique, manufacturers can make informed decisions that optimize their production efficiency and product quality.
Masterbatch coloring ensures superior color uniformity.True
It evenly disperses pigments, preventing streaks common in dry mixing.
Dry mixing results in lower dust formation than masterbatch coloring.False
Masterbatch coloring significantly reduces dust compared to dry mixing.
Is Paste Colorant Coloring Worth the Higher Cost?
The choice between different colorant technologies in injection molding often comes down to cost versus quality. Is paste colorant coloring truly worth the investment?
Paste colorant coloring offers superior uniformity and reduced dust compared to other methods, but its higher cost requires careful consideration of product requirements and production processes.
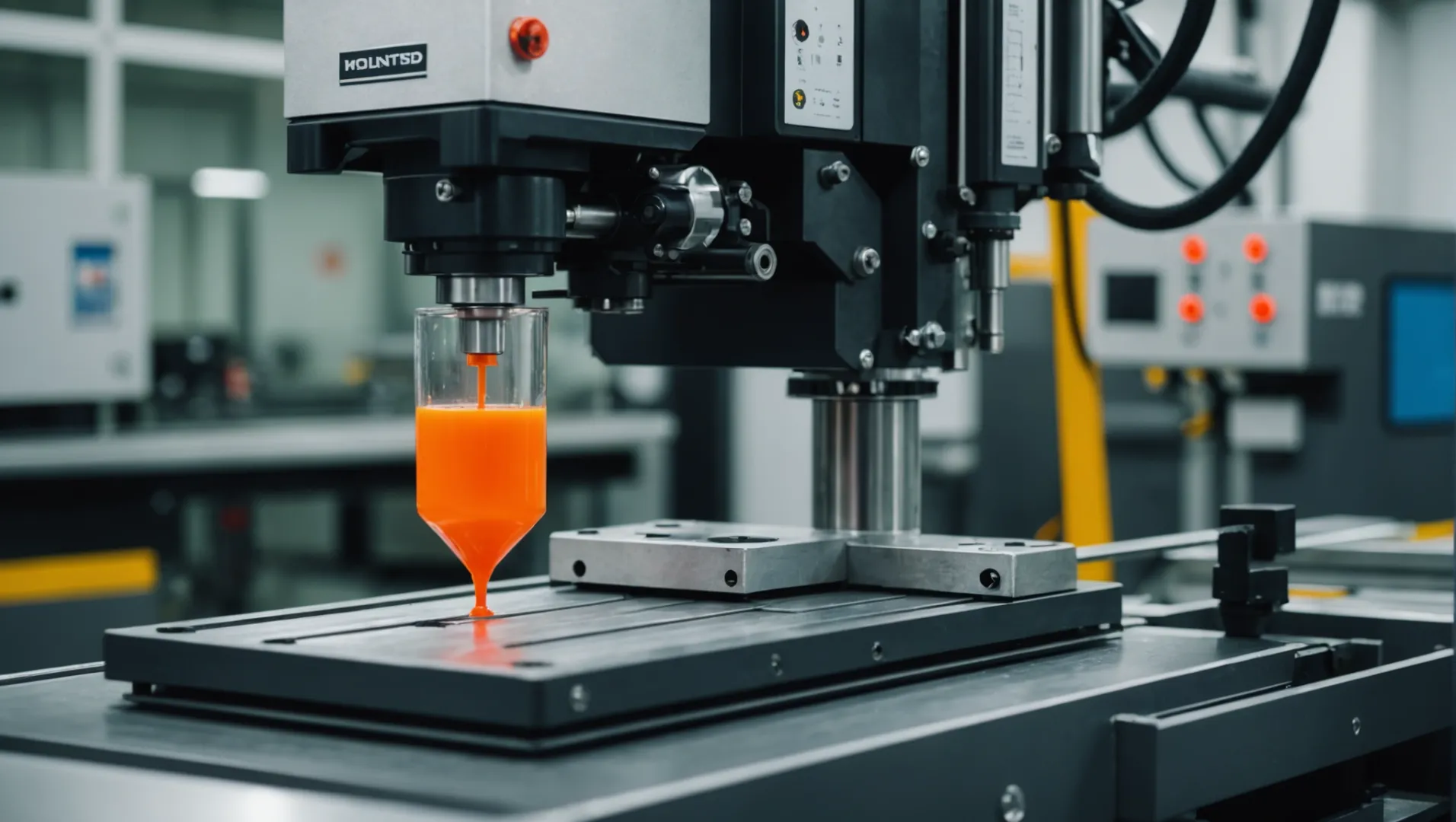
Understanding Paste Colorant Coloring
Paste colorant coloring stands out due to its ability to achieve highly uniform color dispersion without the issues of dust that can accompany dry mixing coloring3. This method involves mixing color powder with a liquid carrier to create a paste, which is then combined with plastic particles for injection molding. The paste ensures a consistent distribution of color, making it ideal for products where precision is key.
Evaluating Cost versus Benefits
While paste colorant coloring can be more expensive than alternatives like masterbatch coloring4, it offers several advantages:
- Uniformity: The liquid medium aids in dispersing the pigment evenly, reducing the likelihood of color variations in the final product.
- Dust Control: By utilizing a liquid carrier, this method minimizes airborne particles, enhancing workplace safety and cleanliness.
- Efficiency: For high-value products where color consistency is paramount, the higher initial cost may be offset by reduced wastage and higher product quality.
Technology | Uniformity | Dust Control | Cost |
---|---|---|---|
Dry Mixing | Low | Poor | Low |
Masterbatch | High | Good | High |
Paste Colorant | Very High | Excellent | Very High |
Pigment Pre-dispersion | High | Excellent | High |
When to Choose Paste Colorant Coloring
Deciding whether to invest in paste colorant coloring should involve a thorough assessment of the product requirements5 and production processes:
- Product Specifications: For items demanding exacting color standards or those made from complex materials, the benefits of paste colorant coloring can justify its cost.
- Production Scale and Equipment: In scenarios where the production environment already supports liquid handling systems, integrating paste colorant coloring can be more cost-effective.
Considerations for Implementation
To successfully implement paste colorant coloring, consider:
- Mixing Equipment: Ensure compatibility with your existing systems, such as high-speed mixers or twin-screw extruders.
- Mixing Order and Conditions: Control factors like temperature and time meticulously to achieve optimal dispersion.
Ultimately, whether paste colorant coloring is worth its price depends on balancing these benefits against budget constraints and product objectives. By evaluating your specific needs, you can determine if this investment will provide long-term value for your production line.
Paste colorant offers excellent dust control.True
Paste colorant uses a liquid carrier, minimizing airborne particles.
Dry mixing provides better uniformity than paste colorant.False
Dry mixing has low uniformity compared to paste colorant's very high.
How to Ensure Uniform Pigment Pre-dispersion?
Achieving uniform pigment pre-dispersion is essential for consistent coloring in injection molding processes. Understanding the factors and methods involved can help ensure optimal results.
To ensure uniform pigment pre-dispersion, select appropriate mixing equipment, control mixing time and temperature, and follow the correct order of adding color paste. This method offers superior coloring effects but requires careful attention to details.
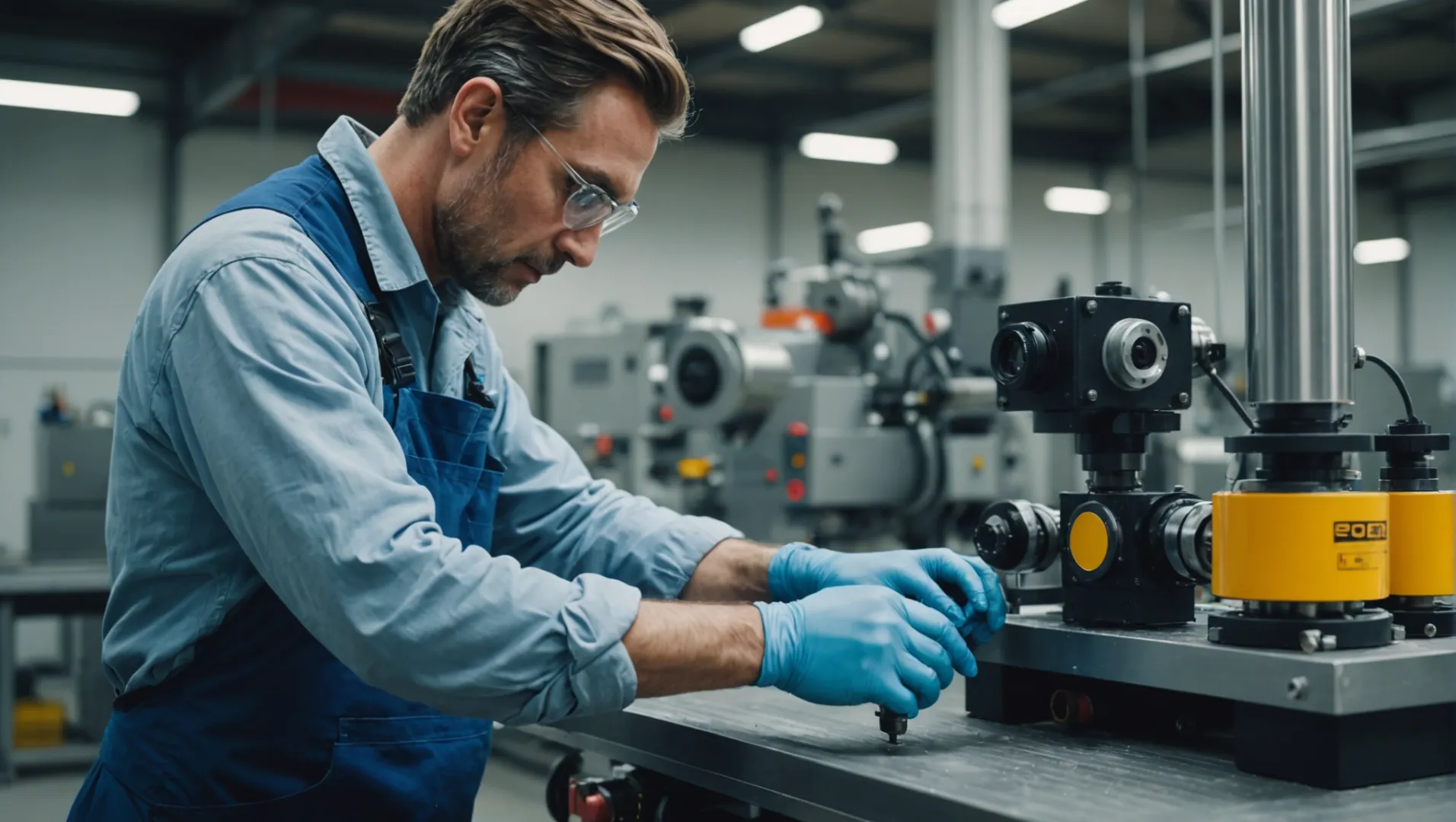
The Importance of Equipment Selection
Choosing the right mixing equipment is crucial in ensuring uniform pigment pre-dispersion. Depending on the production process and properties of the color paste, options include high-speed mixers, low-speed mixers, and twin-screw extruders.
- High-Speed Mixers: These are excellent for achieving quick dispersion but might generate heat, affecting temperature-sensitive pigments.
- Low-Speed Mixers: Suitable for delicate pigments, providing gentle mixing with less heat generation.
- Twin-Screw Extruders: Offer precise control over mixing parameters, ideal for complex formulations.
Controlling Mixing Time and Temperature
The properties of the color paste and characteristics of the mixing equipment dictate the ideal mixing time and temperature.
- Mixing Time: Over-mixing can lead to degradation of pigments, while under-mixing results in inconsistent coloring.
- Temperature Control: Maintaining optimal temperatures prevents overheating and ensures pigment stability. Use temperature-controlled equipment where possible.
Correct Order of Addition
The sequence in which materials are added can greatly affect dispersion quality.
- Add Carrier Resin or Plastic Particles First: This allows for a base matrix to be established before pigments are introduced.
- Introduce Pigment Pre-dispersion: This should be done gradually to allow even distribution throughout the base matrix.
Balancing Cost and Quality
While pigment pre-dispersion offers superior coloring effects, it is more expensive than other methods. However, the investment can be justified by the consistency and quality of the final product.
For manufacturers looking to optimize costs, consider conducting a cost-benefit analysis6 to determine if the benefits of improved quality outweigh the initial expense.
Understanding these variables helps manufacturers achieve consistent results with pigment pre-dispersion, ultimately leading to higher-quality products that meet industry standards.
High-speed mixers are ideal for temperature-sensitive pigments.False
High-speed mixers generate heat, affecting temperature-sensitive pigments.
Correct order of addition affects pigment dispersion quality.True
Adding materials in the right sequence ensures even pigment distribution.
Conclusion
Understanding these colorant mixing technologies empowers you to make informed choices that enhance product quality and efficiency.
-
Explore how masterbatch coloring improves color uniformity in injection molding.: Color masterbatch is mainly used as a colorant added in the plastic processing process to make plastic products form their intended colors. How … ↩
-
Learn about the limitations of dry mixing compared to masterbatch coloring.: However, the one thing that can prove difficult to manage is looking over the ratio of pigment to plastic, which like the previous point of color-mixing in … ↩
-
Discover why dry mixing might not meet your quality standards.: Slow-Drying Acrylic Paint: Pros & Cons Explained! … How to Mix Perfect Brown & Earthy … ↩
-
Learn how masterbatch compares to paste colorants.: Masterbatch coloring · 1. Improved environmental pollution caused by flying toner · 2. It is easy to change color during use, so there is no need … ↩
-
Explore factors affecting your choice in colorant technology.: 5 Factors that Affect Injection Molding Quality · Design of the Mold · Thickness of the Product Walls · Runner Presence · Surface Finishing · Raw Materials. ↩
-
Learn how cost impacts quality in pigment pre-dispersion.: The viscosity of a pre-mixed dispersion is one of the main parameters to consider when selecting a particular milling equipment for grinding of pigment. ↩