Have you ever faced the frustration of a collapsed polypropylene part during production? You’re not alone. Understanding the nuances behind these collapses can help you avoid costly mistakes.
Injection molded polypropylene parts may collapse due to issues such as material shrinkage, poor fluidity, insufficient injection pressure, or improper mold design. Addressing these factors is crucial for maintaining part integrity.
Let’s dive deeper into the complex world of polypropylene manufacturing and uncover the key factors that contribute to these challenges.
Uneven wall thickness causes polypropylene part collapse.True
Uneven wall thickness leads to differential cooling, causing internal stress and collapse.
How Does Material Shrinkage Affect Polypropylene Parts?
Material shrinkage is a significant factor affecting the quality and integrity of polypropylene parts. Understanding its impact is key to preventing collapse.
Material shrinkage in polypropylene parts can lead to structural weaknesses, causing collapses post-production. This occurs due to inherent material properties and process variations during injection molding.
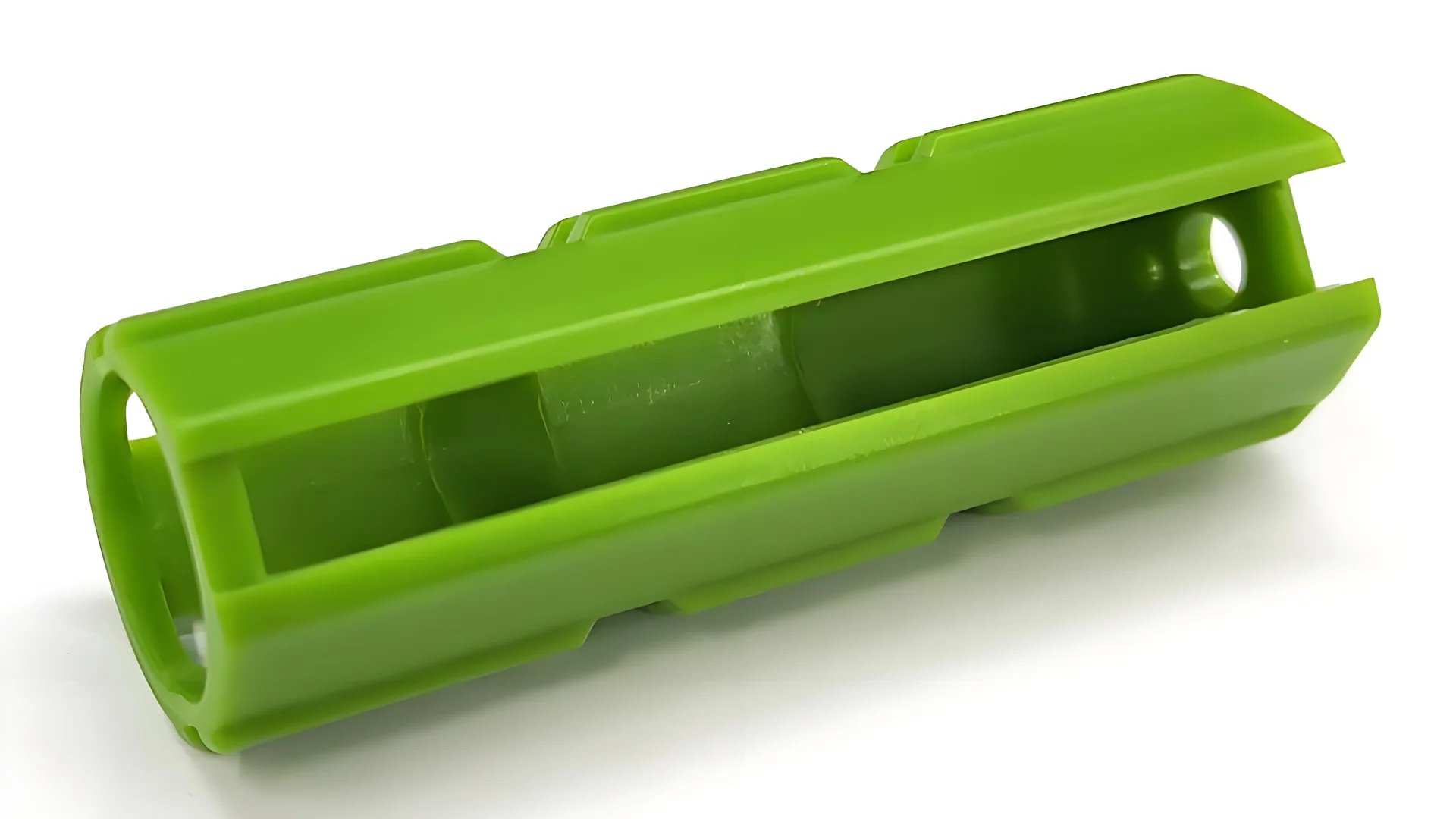
Understanding Polypropylene’s Shrinkage Characteristics
Polypropylene (PP) is known for its shrinkage characteristics, which can significantly influence the final dimensions and stability of molded parts. Typically, polypropylene exhibits a shrinkage rate between 1.5% to 3%. This variance depends on the specific grade of polypropylene used. If not adequately accounted for, shrinkage can lead to dimensional inaccuracies1 and even part collapse.
Different grades of polypropylene present varying shrinkage rates. Manufacturers must carefully select materials based on their intended application and performance requirements. Opting for a grade with a higher shrinkage rate without necessary design or process adjustments increases the risk of collapse.
Impact on Dimensional Stability
Shrinkage affects the dimensional stability of parts, leading to potential deviations from specified tolerances. This can be particularly problematic for components that require high precision. For instance, uneven wall thicknesses can exacerbate shrinkage effects, where thicker sections cool slower and shrink more than thinner sections. This uneven cooling can introduce internal stresses that compromise the structural integrity of the part.
Process Adjustments to Mitigate Shrinkage Effects
To mitigate the impact of shrinkage, manufacturers can implement several process adjustments:
- Material Selection: Choose polypropylene grades with predictable shrinkage properties suitable for the part’s application.
- Mold Design: Ensure uniform wall thickness across the part to reduce differential cooling and shrinkage.
- Process Parameters: Optimize injection pressures and temperatures to control flow and cooling rates effectively.
A thorough understanding of these factors enables manufacturers to anticipate potential issues and make informed decisions to maintain part integrity.
Monitoring and Quality Control Measures
Implementing robust quality control measures2 is crucial in detecting shrinkage-related defects early in the production process. Techniques such as dimensional analysis, visual inspection, and non-destructive testing can identify areas prone to collapse, allowing for timely adjustments.
Regular monitoring and adjustments based on observed shrinkage patterns ensure that the final products meet quality standards and functional requirements.
Polypropylene shrinkage leads to structural weaknesses.True
Shrinkage affects dimensions and stability, causing potential collapses.
Uneven wall thickness reduces shrinkage effects in polypropylene.False
Uneven thickness increases differential cooling, exacerbating shrinkage.
What Role Does Injection Pressure Play in Part Integrity?
Injection pressure is a pivotal factor in ensuring the structural integrity of polypropylene parts, directly influencing their strength and durability.
Injection pressure ensures that molten polypropylene fully occupies the mold cavity, preventing defects and ensuring part integrity. Low pressure can lead to incomplete filling, causing internal weakness and potential collapse.
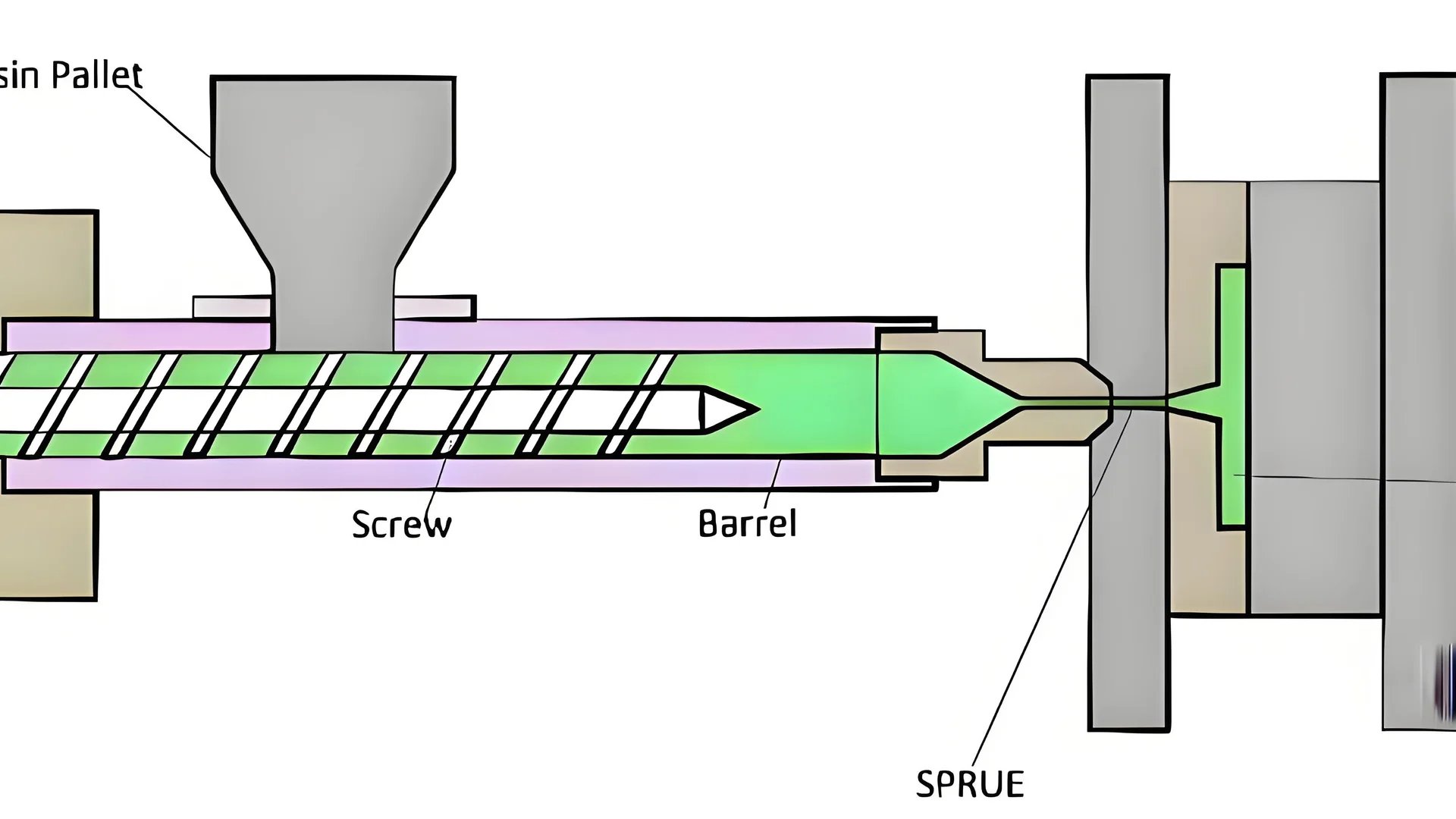
The Importance of Injection Pressure in Polypropylene Molding
Injection pressure is crucial in injection molding as it ensures that molten polypropylene can adequately fill the mold cavity. This pressure must be high enough to overcome resistance and maintain the flow of material into every nook of the mold. If the injection pressure is too low, it can result in incomplete filling, leading to weaknesses and potential collapses once the part cools.
Impact on Structural Integrity
When molten polypropylene is injected into a mold with insufficient pressure, the material may not reach all areas, especially in complex or intricate designs. This lack of material distribution can create voids or weak points within the part, making it susceptible to collapse under stress or during handling. By increasing injection pressure, manufacturers can ensure that the material fills even the smallest sections of the mold, thus enhancing overall part strength.
Adjusting Injection Pressure for Optimal Results
-
Part Design Considerations
The shape and complexity of the part significantly influence the required injection pressure. For instance, intricate designs with thin walls may necessitate higher pressures to ensure complete filling without defects. Conversely, simpler designs might not require as much pressure.
-
Material Properties
Different grades of polypropylene exhibit varying degrees of fluidity and shrinkage characteristics. For example, a high-fluidity grade3 may fill the mold more easily at lower pressures than a more viscous grade.
-
Mold Configuration
Factors such as the number and size of gates, venting systems, and cooling channels can impact how effectively the pressure is applied throughout the mold. Proper mold design can help manage these aspects to ensure uniform distribution of pressure.
Balancing Pressure with Other Variables
While increasing injection pressure can help improve part integrity, it’s also essential to balance it with other parameters such as holding time and cooling rate. Excessive pressure may lead to other issues like increased internal stress or flashing.
Utilizing a systematic approach to adjust and balance these factors can significantly enhance the quality and performance of polypropylene parts. Evaluating each element in detail allows for targeted improvements that help prevent collapse while maintaining efficiency and cost-effectiveness in production.
High injection pressure prevents mold filling defects.True
High pressure ensures molten polypropylene fills the mold completely, avoiding defects.
Low injection pressure strengthens polypropylene parts.False
Low pressure can cause incomplete filling, leading to weak points in the part.
Why is Mold Design Crucial for Preventing Collapse?
A well-designed mold is critical in preventing structural collapse in polypropylene parts, ensuring durability and function.
Mold design is vital in preventing collapse of polypropylene parts by addressing factors such as wall thickness uniformity, gate positioning, and exhaust efficiency. Proper mold design ensures even material distribution, reduces internal stress, and enhances part stability.
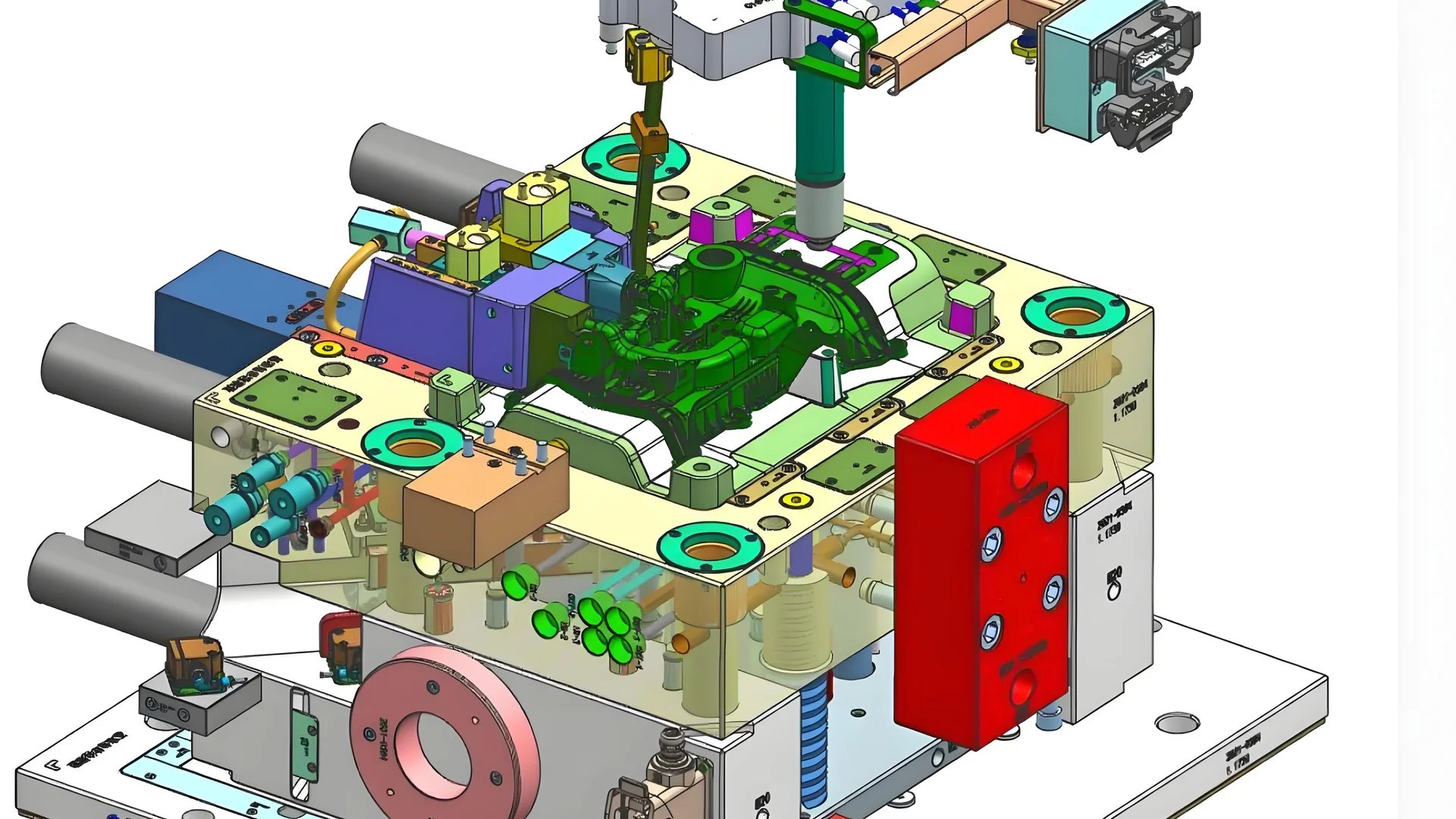
The Importance of Uniform Wall Thickness
One of the fundamental aspects of mold design is ensuring that the wall thickness of the parts remains uniform. When polypropylene parts have uneven wall thickness, the cooling and shrinkage rates differ significantly across the part. Thick-walled sections cool more slowly and shrink more, leading to internal stress that can cause collapse upon demolding.
To mitigate this issue, designers should aim for consistent wall thickness throughout the part. If variations are unavoidable, incorporating structural features such as ribs and transition fillets can help distribute stress more evenly and reduce collapse risk.
Gate Positioning for Even Material Flow
The position of the gate is another crucial factor in mold design that affects part quality. An improperly placed gate can lead to uneven material distribution, resulting in either material shortages or excesses in different areas of the part. This inconsistency during the cooling phase often results in collapse.
Designers must carefully consider the flow characteristics of polypropylene, alongside the part’s geometry, to select a gate position that ensures uniform filling. For instance, placing gates at strategic points can facilitate balanced flow paths that minimize potential weaknesses.
Efficient Exhaust Systems
Efficient gas exhaust from the mold is essential to prevent high-pressure areas that can impede material flow and lead to insufficient filling. Poor exhaust design traps air, causing compression and subsequent collapse after cooling.
Implementing a well-thought-out exhaust system, which may include exhaust grooves or vents between parting surfaces, allows gases to escape smoothly. This not only enhances material distribution but also contributes to overall part stability.
Explore more about mold design techniques4 to deepen your understanding of how these strategies can be implemented in practice. By focusing on these key elements of mold design, manufacturers can significantly enhance the structural integrity of polypropylene parts.
Uniform wall thickness prevents part collapse.True
Consistent wall thickness reduces stress and shrinkage differences.
Improper gate positioning leads to material shortages.True
Incorrect gate placement causes uneven material distribution.
How Can Cooling Time Influence the Structural Stability?
Cooling time is a critical factor in injection molding, impacting the structural stability of polypropylene parts.
Proper cooling time ensures polypropylene parts solidify fully, reducing the risk of collapse due to insufficient cooling.
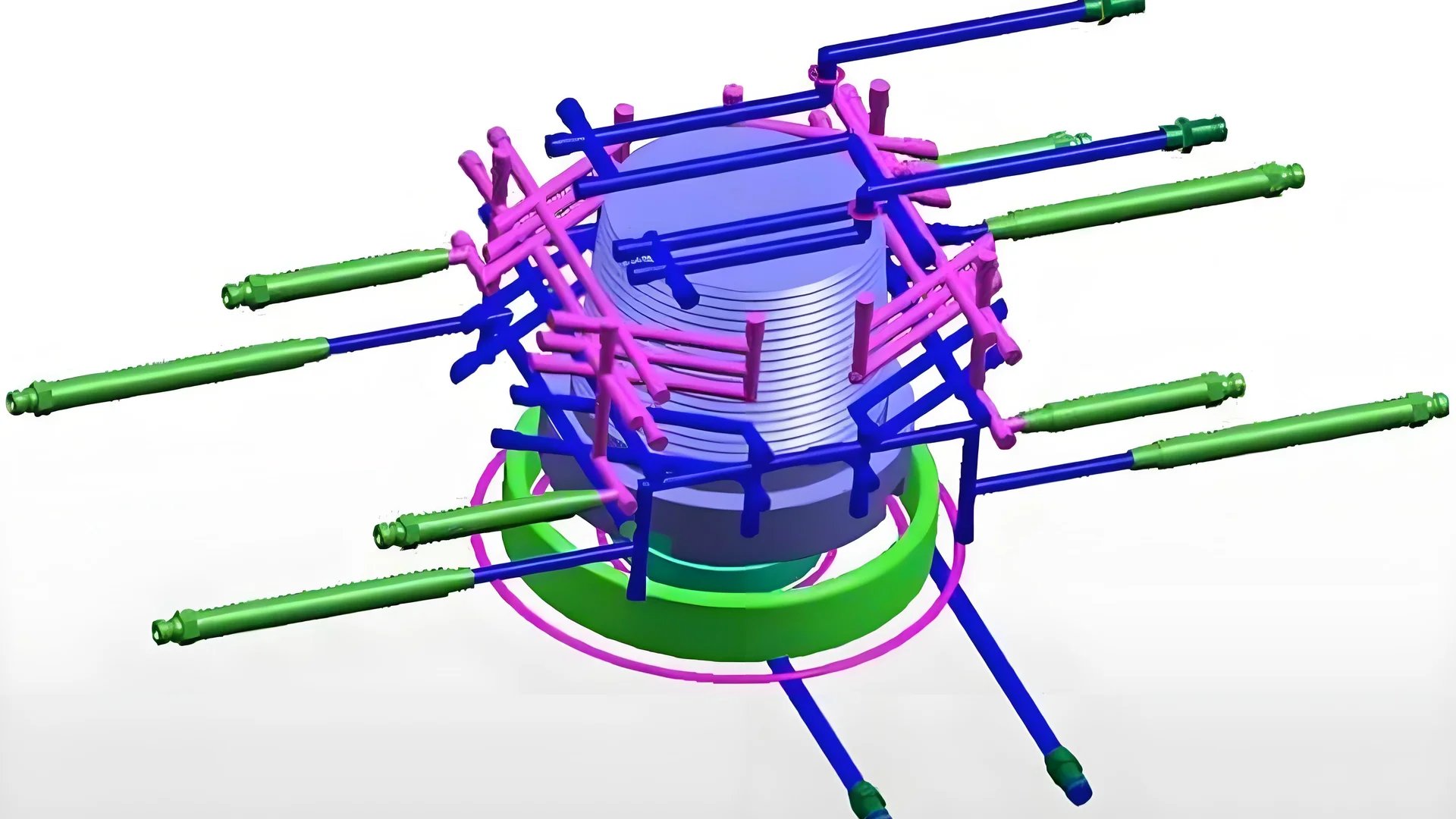
The Science Behind Cooling Time
In the world of injection molding5, cooling time is a pivotal parameter. It directly affects how well a polypropylene part solidifies and its subsequent structural stability. Inadequate cooling can leave the material in a semi-solid state, increasing the likelihood of collapse under weight or stress. Conversely, excessive cooling may lead to longer production cycles, impacting efficiency.
Material Solidification
During the cooling phase, the transition from a molten to a solid state occurs. This phase is crucial as it determines the final strength and stability of the molded part. If cooling is cut short, areas within the part may not reach full solidification, leading to weak points that are prone to collapse.
Cooling Scenario | Outcome |
---|---|
Insufficient Cooling | Partially solidified sections, risk of collapse |
Optimal Cooling | Complete solidification, structural integrity |
Excessive Cooling | Increased cycle time, reduced efficiency |
Considerations for Optimal Cooling
- Part Thickness: Thick sections require longer cooling times to ensure uniform solidification. Thin-walled parts cool faster but may still need attention to avoid warp or shrinkage.
- Mold Temperature: Maintaining an appropriate mold temperature ensures that heat is efficiently extracted from the part, aiding in uniform cooling.
- Cooling Channels: Properly designed cooling channels within the mold can enhance heat dissipation, promoting even cooling throughout the part.
Balancing Efficiency and Quality
While it’s essential to ensure adequate cooling time to prevent structural failures, manufacturers also face the challenge of maintaining efficient production rates. This balance can be achieved by:
- Optimizing cooling channel design to enhance heat extraction efficiency.
- Adjusting process parameters like mold temperature and cycle time based on part geometry.
- Utilizing simulation software to predict cooling behavior and optimize settings.
In conclusion, managing cooling time effectively is not just about preventing collapse but also about achieving a delicate balance between quality and production efficiency. For manufacturers, understanding these dynamics can lead to more robust and reliable polypropylene parts.
Insufficient cooling causes polypropylene collapse.True
Without adequate cooling, parts remain semi-solid, risking collapse.
Excessive cooling enhances production efficiency.False
Excessive cooling increases cycle time, reducing production efficiency.
Conclusion
By addressing material properties, process parameters, and mold design, manufacturers can significantly reduce the risk of collapse and enhance product reliability.
-
Learn how shrinkage impacts dimensional accuracy in molded parts.: From these results, the shrinkage for a specific grade and part can be accurately predicted by starting with the desired part thickness. This is a fixed … ↩
-
Explore effective quality control strategies for injection-molded parts.: The first stage is the design stage, followed by Mold and Pre-Production Inspection and In Process Quality Control and Final Inspection. ↩
-
Discover different grades that offer better mold filling capabilities.: The high fluidity and high gloss of Moplen RP5007 enable processing temperatures to be reduced by 10 to 20°C, injection speeds to be increased, … ↩
-
Discover advanced mold design strategies to enhance part integrity.: Six examples of part designs with undercuts: a TE cap, CT cap, threaded collar, prescription, dosing, and long thread run design. Undercut … ↩
-
Explore the significant effects of cooling time in injection molding.: 80%. That is how much of the molding cycle is spent cooling the plastic part. That’s a pretty big chunk of the process, so it’s important to … ↩