Imagine having a tool that brings precision and efficiency to your creative vision like never before.
CNC machining revolutionizes injection mold manufacturing by improving precision, reducing lead times, and enhancing efficiency through automated, accurate crafting of complex mold designs, leading to superior product quality.
I remember the first time I encountered CNC machining; it was like witnessing magic. Watching the machine transform a block of material into a meticulously detailed mold sparked a realization about its potential. CNC machining isn’t just about automation—it’s about unlocking creativity and efficiency, taking what was once a time-consuming process and streamlining it into something almost effortless.
By diving deeper into CNC‘s applications, you see its true impact. It allows us to push the boundaries of design, giving life to intricate forms that were once too complex to create. This technology isn’t just about making molds; it’s about revolutionizing how we think about manufacturing. It opens doors to innovations that can redefine entire industries.
CNC machining reduces lead times in mold manufacturing.True
CNC technology speeds up production, cutting down the time needed for mold creation.
Traditional methods are more precise than CNC machining.False
CNC machining offers higher precision due to computer-controlled automation.
- 1. What Are the Key Benefits of CNC Machining in Mold Production?
- 2. How Does CNC Technology Improve Design Precision in Injection Molding?
- 3. What Are the Cost Implications of Adopting CNC Machining for Mold Manufacturers?
- 4. How Does CNC Machining Enhance Production Scalability and Flexibility?
- 5. What Challenges Might Arise When Implementing CNC Technology in Mold Manufacturing?
- 6. How Is CNC Machining Influencing Future Trends in Injection Mold Manufacturing?
- 7. Conclusion
What Are the Key Benefits of CNC Machining in Mold Production?
Ever wondered how technology could revolutionize your mold designs? CNC machining is the game-changer, offering precision, speed, and flexibility that transform ideas into reality effortlessly.
CNC machining in mold production enhances precision and efficiency, minimizes human error and waste, supports complex designs, and improves product quality.
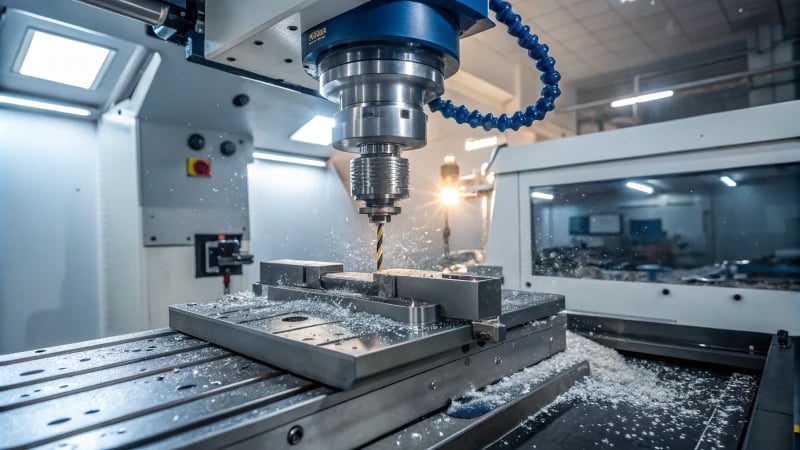
Precision and Accuracy
I remember the first time I saw a CNC machine1 in action at a manufacturing plant. It was like watching an artist sculpting with incredible precision—something I never thought possible with such intricate detail. This level of accuracy is what makes CNC machining so invaluable in mold production. Every part is crafted to meet exact specifications, which means fewer errors and consistent quality across the board. It’s like having a reliable partner that never misses a beat.
Feature | Description |
---|---|
Precision | Achieves tight tolerances; ideal for complex designs. |
Repeatability | Ensures consistent output with minimal variance. |
Efficiency and Speed
When I switched to CNC machining, the increase in speed was mind-blowing. The machines operate continuously, churning out parts at a rate that traditional methods could never match. It’s like having an extra pair of hands working tirelessly around the clock. This not only speeds up production but also drastically reduces lead times2, allowing projects to be completed faster than ever.
- Reduced Downtime: Machines can run with minimal supervision.
- Automated Processes: Tasks are completed without constant human intervention.
Cost-Effectiveness
I was initially hesitant about the cost of setting up CNC machining3, but let me tell you—it pays off in the long run. The reduction in material waste and labor costs adds up to significant savings over time. Plus, with fewer defects, there’s less rework, saving even more resources. It’s like investing in peace of mind.
Design Flexibility
One of the most exciting aspects of CNC technology is the creative freedom it offers. I could experiment with intricate shapes and complex geometries that seemed impossible before. This flexibility not only fuels innovation but also speeds up the time it takes to get unique products to market.
Material Versatility
The ability to work with a variety of materials—from metals to plastics—makes CNC machines essential tools in mold production. This versatility means I can choose the best material for each project without worrying about compatibility issues. Imagine the freedom to design without limits!
Explore material options4 that suit your specific design needs and ensure optimal performance in end products.
CNC machining improves mold production precision.True
CNC machining ensures molds are produced to exact specifications, enhancing precision.
CNC machines require constant human supervision.False
CNC machines operate with minimal supervision, allowing continuous production.
How Does CNC Technology Improve Design Precision in Injection Molding?
I remember the first time I saw a CNC machine in action, and it felt like watching a master artist at work. The precision was mesmerizing!
CNC technology enhances injection molding precision through high accuracy, repeatability, and complex geometries, reducing human error and improving quality control for consistent mold production.
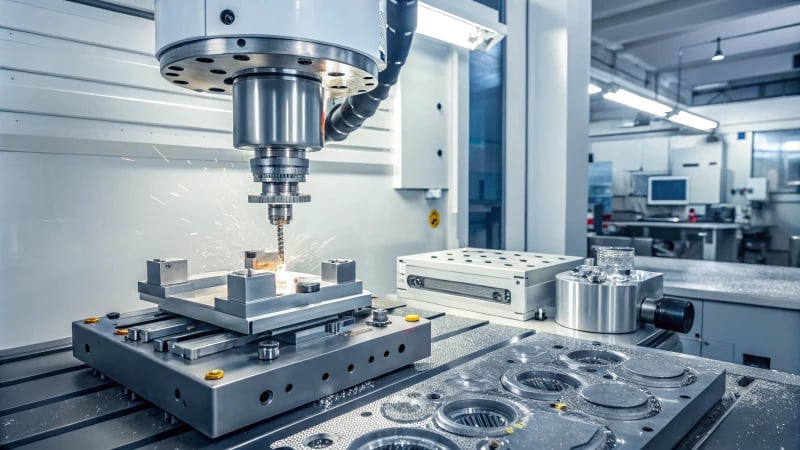
Understanding CNC Technology’s Role in Precision
When I first learned about CNC (Computer Numerical Control) technology, I was intrigued by how it transformed the world of injection molding5. Imagine having a tool that can automate the control of machines with computer precision, making even the most intricate designs a reality. It’s like having a magic wand that ensures every component is crafted to perfection, reducing human error to almost nil.
Key Benefits of CNC in Injection Molding:
Benefit | Description |
---|---|
High Accuracy and Consistency | With CNC machines, I’ve seen firsthand how they follow CAD6 models with remarkable accuracy. It’s like having a detailed map that ensures every mold aligns perfectly with the designer’s blueprint, minimizing defects. |
Improved Quality Control | The precision of CNC machining makes stringent quality control measures feel like a walk in the park. Each mold is produced with exact specifications, meaning less variability and a higher quality final product. |
Efficient Production Processes | By cutting down on the need for manual tweaks and checks, CNC technology streamlines production. This efficiency not only sharpens precision but also slashes production time and costs. |
Applications in Complex Mold Designs
The ability of CNC to craft complex geometries opens up endless design possibilities in injection molding. It’s like giving designers a playground for creativity where intricate patterns and shapes are no longer daunting tasks but exciting challenges to embrace.
Example of Complex Design Benefits:
- Consumer Electronics: Intricate internal structures can be accurately replicated, improving product functionality.
- Automotive Components: High-precision molds ensure parts fit together seamlessly, enhancing performance.
Adopting CNC for Enhanced Mold Production
For manufacturers7 aiming to up their game, embracing CNC technology is like discovering a treasure trove of potential. Not only does it boost precision, but it also offers scalability and flexibility across various projects. Integrating CNC into current operations could be your ticket to elevated design quality and production efficiency.
CNC technology reduces human error in injection molding.True
CNC automates processes, minimizing manual intervention and errors.
CNC machines can't produce intricate injection mold designs.False
CNC excels at creating complex geometries, enhancing design flexibility.
What Are the Cost Implications of Adopting CNC Machining for Mold Manufacturers?
Navigating the world of CNC machining costs can feel like a wild ride for mold manufacturers. Getting a handle on the expenses is key to making smart financial choices.
CNC machining reduces mold manufacturing costs through decreased labor, enhanced precision, and faster production, but initial setup and maintenance expenses must be considered.
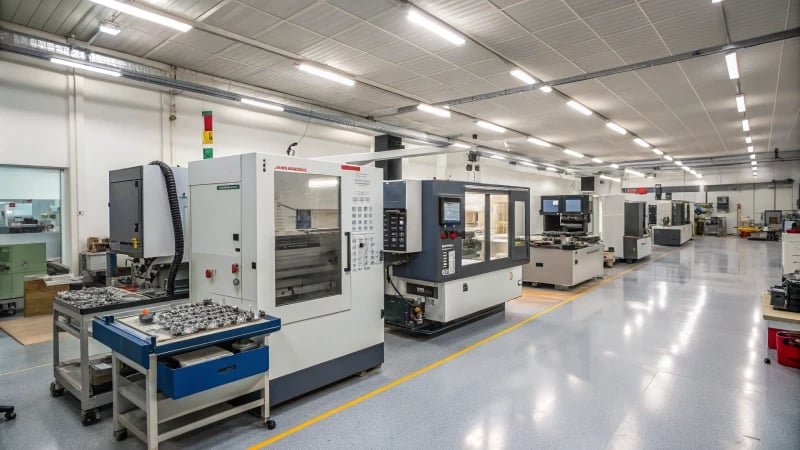
Initial Setup Costs
I remember when I first delved into CNC machining—it felt like stepping into a whole new world. The initial investment was like a tidal wave, with machines costing anywhere from $50,000 to $500,000 depending on their capabilities. And it wasn’t just about buying the machine; there were software licenses8 and employee training costs that seemed to add up faster than I could say "computer numerical control."
Item | Estimated Cost |
---|---|
CNC Machine | $50,000 – $500,000 |
Software License | $1,000 – $15,000/year |
Employee Training | $1,000 – $5,000 per employee |
Operational Costs and Savings
The beauty of CNC machining is its efficiency. I noticed a significant drop in manual labor needs, which meant fewer skilled operators were required—a bittersweet realization as it changed the dynamic of our team. But automation9 was a game-changer. Of course, these machines consume a fair amount of power, so our utility bills took a hit, but the trade-off was worth it in terms of productivity.
Material Costs and Waste Reduction
One of the most satisfying aspects was seeing how CNC technology optimized our material usage. Precise cutting meant less waste and fewer errors. Over time, this translated into substantial material savings, which made me breathe easier when reviewing budgets.
Maintenance and Long-term Financial Impact
Regular maintenance is not something you can skimp on if you want to avoid costly downtimes. The expenses for spare parts and professional services were like taxes—unavoidable but necessary. Calculating these against potential savings helped me truly grasp the long-term financial impact.
Comparison with Other Methods
I spent countless hours comparing CNC with traditional methods. While the upfront costs of CNC were undeniably steep, I couldn’t ignore the lower operational costs down the line—thanks to reduced labor and increased accuracy.
Consider using a table to compare specific costs between CNC and traditional methods:
Method | Initial Cost | Operational Cost | Material Waste |
---|---|---|---|
CNC | High | Low | Low |
Traditional | Low | High | High |
These insights have been instrumental in helping mold manufacturers like myself make informed decisions about adopting CNC machining technology. By exploring the various cost implications, I’ve ensured a comprehensive understanding of both immediate and future financial impacts. Explore further10 insights to aid in decision-making.
CNC machines cost between $50,000 to $500,000.True
The context specifies that CNC machines range from $50,000 to $500,000.
CNC machining increases manual labor needs.False
The context states CNC machining reduces manual labor through automation.
How Does CNC Machining Enhance Production Scalability and Flexibility?
I remember the first time I saw CNC machines in action—it was like watching a futuristic dance of precision and speed. They promised something incredible: a revolution in how we think about production.
CNC machining boosts production scalability and flexibility by allowing quick volume adjustments, supporting design changes, and managing complex geometries efficiently, all while maintaining high quality and reducing lead times.
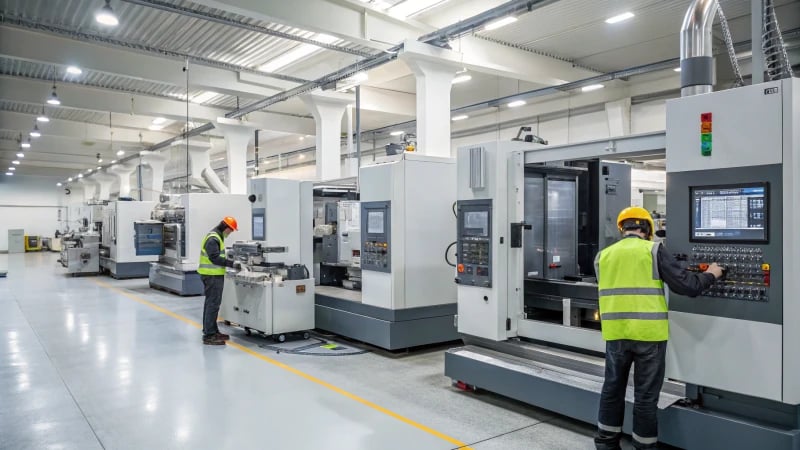
The Role of CNC in Scaling Production Volumes
Reflecting on my early days in manufacturing, I recall the constant challenge of scaling production without sacrificing quality. CNC machining became a game-changer. With its ability to automate machining processes11, transitioning from crafting a few prototypes to full-scale production became seamless. This automation cut down on manual interventions, drastically reducing errors and ensuring every batch was consistently top-notch.
Benefits | Details |
---|---|
Reduced Setup Time | CNC systems use pre-programmed instructions, cutting down setup time significantly. |
Consistent Quality | Ensures uniformity in product output, essential for large-scale production. |
Quick Adaptation | Easily adapts to changes in production demand without major overhauls. |
Enhancing Flexibility with CNC Technology
In my experience as a product designer, flexibility is more than just a buzzword; it’s a necessity. CNC machining was like a breath of fresh air. Imagine having the freedom to implement design changes without starting from scratch! A fellow designer, let’s call him Jacky12, once shared how he could swiftly update CAD designs, knowing that CNC machines would execute these changes in real-time. It was like having an artist’s brush with the precision of a laser.
- Design Complexity: CNC machines manage complex shapes effortlessly, which traditional methods might find challenging. This allows for innovative design options.
- Material Versatility: Capable of working with a broad range of materials, CNC machines enhance product variety without extensive reconfiguration.
The Economic Impact of CNC Machining on Scalability and Flexibility
The economic benefits of CNC technology are undeniable, even if the initial investment can be daunting. I’ve seen firsthand how savings quickly accumulate through reduced labor costs and minimal waste. In fact, research13 highlights that CNC machines boost operational efficiency, making them an economical choice for scaling operations.
- Labor Efficiency: Automation reduces the need for extensive manual labor, reallocating resources towards other strategic areas.
- Lower Waste Production: Precision machining minimizes material waste, aligning with sustainable manufacturing goals.
Overall, integrating CNC technology into manufacturing processes allows businesses to nimbly respond to market demands while upholding high standards of quality and efficiency. This adaptability is especially crucial in fast-paced industries where staying ahead means constantly innovating and adapting.
CNC machining reduces setup time significantly.True
CNC uses pre-programmed instructions, cutting down setup time.
CNC machines struggle with complex shapes.False
CNC machines handle complex shapes effortlessly, aiding innovation.
What Challenges Might Arise When Implementing CNC Technology in Mold Manufacturing?
Ever felt like diving into CNC technology for mold manufacturing was a leap of faith? Trust me, it’s an adventure worth exploring, but it comes with its own set of hurdles.
Implementing CNC technology in mold manufacturing faces challenges like high initial costs, the need for technical expertise, and complex integration, but overcoming these can enhance precision and efficiency.
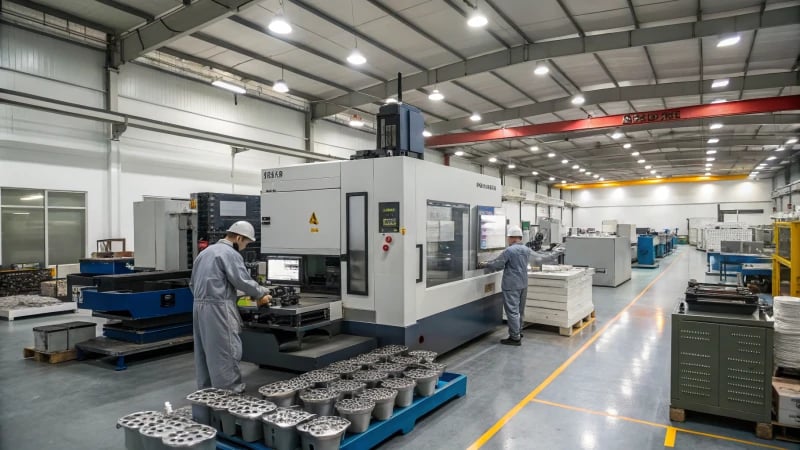
High Initial Investment
When I first considered bringing CNC technology into my business, the staggering cost was enough to make me hesitate. Imagine buying a luxury car, and then realizing you also need to purchase premium fuel, insurance, and maintenance packages. That’s what stepping into CNC feels like. It’s not just the machine; it’s the software licenses14 and the specialized training that come with it. For a company my size, these costs can feel like standing at the base of a financial mountain.
Cost Factors | Details |
---|---|
Machine Purchase | High upfront cost |
Software Licenses | Ongoing subscription fees |
Training Programs | Specialized training required |
Technical Expertise Requirements
In my journey, finding skilled workers who can deftly maneuver CAD software and understand the intricacies of CNC machines was like searching for unicorns. These skills don’t just appear overnight. I realized that investing in either training my existing team15 or hiring new talent was crucial, yet it also meant rethinking our current staffing strategy.
System Integration Complexity
Integrating CNC technology isn’t a simple plug-and-play scenario. It’s more like trying to fit a square peg into a round hole unless you’re ready for some serious workflow reengineering. Updating equipment and resolving compatibility issues with older systems can be quite the puzzle.
Maintenance and Downtime
CNC machines are like high-performance cars; they need regular upkeep to keep them running smoothly. I learned this the hard way when unexpected malfunctions caused production hiccups, throwing off our schedules. Setting up a robust maintenance schedule16 became non-negotiable.
Customization Challenges
While CNC machines promise precision, customizing them for specific mold designs often turns into a programming saga. It’s like tailoring a suit; it takes a skilled hand to get that perfect fit. This means engaging skilled programmers17 to ensure our designs hit the mark.
Adapting to Technological Changes
The tech world moves fast—blink, and you might miss an update. Staying on top of CNC advancements is essential to stay competitive. Whether it’s upgrading software18 or hardware, adapting can feel like a relentless race to keep up.
Understanding these challenges has allowed me to better prepare for the transition to CNC technology. Tackling these issues head-on has not only enhanced productivity but also streamlined our mold manufacturing processes, setting us up for future success.
CNC machines require minimal maintenance.False
CNC machines need regular maintenance to avoid downtime and ensure efficiency.
High initial investment is a challenge for CNC adoption.True
Purchasing CNC machines involves significant costs, including hardware and training.
How Is CNC Machining Influencing Future Trends in Injection Mold Manufacturing?
Ever wondered how CNC machining is reshaping the future of injection mold manufacturing? It’s all about precision, speed, and sustainability. Let me take you through this exciting transformation!
CNC machining transforms injection mold manufacturing with increased precision, reduced production times, and efficient complex design capabilities, essential for adapting to industry demands.
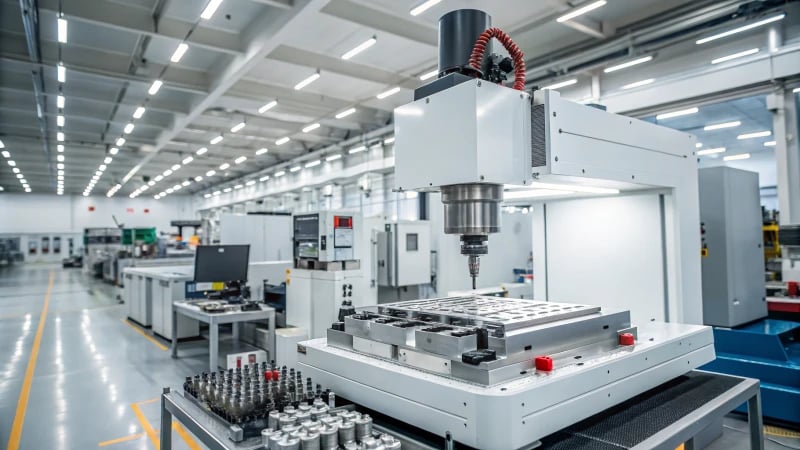
Enhanced Precision and Accuracy
As someone who’s been knee-deep in the intricacies of mold design for a while, I’ve seen firsthand how CNC machining can be a game-changer. The sheer precision it offers is like a breath of fresh air. Imagine crafting molds that meet those tight tolerances every single time. It’s not just about getting it right; it’s about getting it perfect. For us designers, this means fewer do-overs and way less material waste during the product design phase19.
CNC machines bring to life intricate details that seemed impossible with older methods. Suddenly, we’re not just following trends but creating them with bold, complex designs.
Reduced Production Times
I remember when waiting for molds felt like an eternity. But now, with CNC machining, those days are long gone. By automating the process, we can churn out molds faster than I could have imagined. This means we can tackle market shifts or customer whims without breaking a sweat.
In my team, especially in a mid-sized company20 focusing on consumer electronics, this quick turnaround is not just a perk—it’s a necessity. It keeps us agile and ready to pounce on new opportunities.
Facilitating Sustainable Practices
Sustainability isn’t just a buzzword for me; it’s something I care deeply about. And CNC machining fits right into this ethos by minimizing waste and optimizing energy use. Plus, it gives us the chance to recycle materials that might otherwise end up in the trash, which feels like a win-win.
With these capabilities, we’re not just keeping pace with industry trends but helping shape them.
Benefits | Impact |
---|---|
Enhanced Precision | Higher quality, intricate designs |
Reduced Lead Times | Faster response to market changes |
Sustainable Practices | Reduced waste and energy consumption |
For folks like me in the field of mold design, understanding these trends isn’t optional—it’s essential. Embracing CNC technology helps us refine our processes and contribute positively to our company’s success.
Looking ahead, I’m curious about advancements in materials compatible with CNC machines and how further automation might enhance these processes. By staying informed, we can make savvy choices about incorporating emerging technologies21 into our work. It’s all about staying one step ahead.
CNC machining reduces mold production times significantly.True
CNC automates processes, leading to faster mold production.
CNC technology increases material waste in manufacturing.False
CNC minimizes waste by optimizing material use and recycling.
Conclusion
CNC machining is revolutionizing injection mold manufacturing by enhancing precision, reducing lead times, and enabling complex designs, ultimately improving production efficiency and sustainability in the industry.
-
Understanding how CNC machining achieves high precision will help you appreciate its role in producing accurate molds consistently. ↩
-
Reducing lead times is crucial for competitive advantage; explore how CNC machining contributes to faster production cycles. ↩
-
Discover how CNC machining can lead to significant cost savings over traditional manufacturing methods. ↩
-
Learn about the diverse materials compatible with CNC machining to maximize design versatility and product performance. ↩
-
Discover how CNC technology is transforming injection molding processes by increasing precision and efficiency. ↩
-
Learn how integrating CAD with CNC machines enhances accuracy and precision in manufacturing. ↩
-
Explore steps to successfully integrate CNC technology into your manufacturing operations for improved outcomes. ↩
-
Discover comprehensive training options that ensure efficient machine utilization. ↩
-
Understand how automation can cut down operational costs in mold manufacturing. ↩
-
Learn more about how CNC can financially outperform traditional machining methods. ↩
-
Explore how CNC automation transforms manufacturing processes by enhancing efficiency and reducing human errors. ↩
-
Learn how CAD integration with CNC enhances design precision and flexibility. ↩
-
Understand the cost-effectiveness of CNC machining in large-scale production. ↩
-
Understanding the breakdown of costs for CNC adoption can help budget effectively for this transition. ↩
-
Learn about specialized training programs to enhance your team’s CNC proficiency. ↩
-
Find strategies to establish an effective maintenance schedule for CNC equipment. ↩
-
Explore solutions for overcoming customization challenges in CNC machine operations. ↩
-
Stay informed on essential upgrades for CNC technology to maintain a competitive edge. ↩
-
Explore how CNC machining improves the product design phase by allowing for intricate designs and precise manufacturing. ↩
-
Learn how CNC machining offers flexibility and efficiency advantages for mid-sized companies in rapidly changing markets. ↩
-
Discover emerging technologies in CNC machining that could further enhance precision and efficiency in manufacturing. ↩