Have you ever experienced the frustration of waiting on a machine due to a blocked cooling pipe? It can be a nightmare for productivity!
To effectively clean blockages in injection mold cooling pipes, identify the blockage first, then choose a suitable cleaning method such as manual cleaning, chemical cleaning, or ultrasonic cleaning. Each method targets different types of obstructions efficiently.
But there’s so much more to it! Let’s dive into each method, explore the underlying causes of these blockages, and uncover expert tips that will enhance your injection molding efficiency.
Ultrasonic cleaning is the best method for all blockages.False
Ultrasonic cleaning is effective but not suitable for all blockage types.
What Are Common Causes of Blockages in Cooling Pipes?
Understanding why blockages occur in cooling pipes is essential for maintaining efficient mold operations.
Blockages in cooling pipes commonly result from mineral scale, debris accumulation, and biological growth. These obstructions hinder fluid flow, causing temperature irregularities and inefficiencies in the cooling process. Regular monitoring and maintenance can help mitigate these issues.
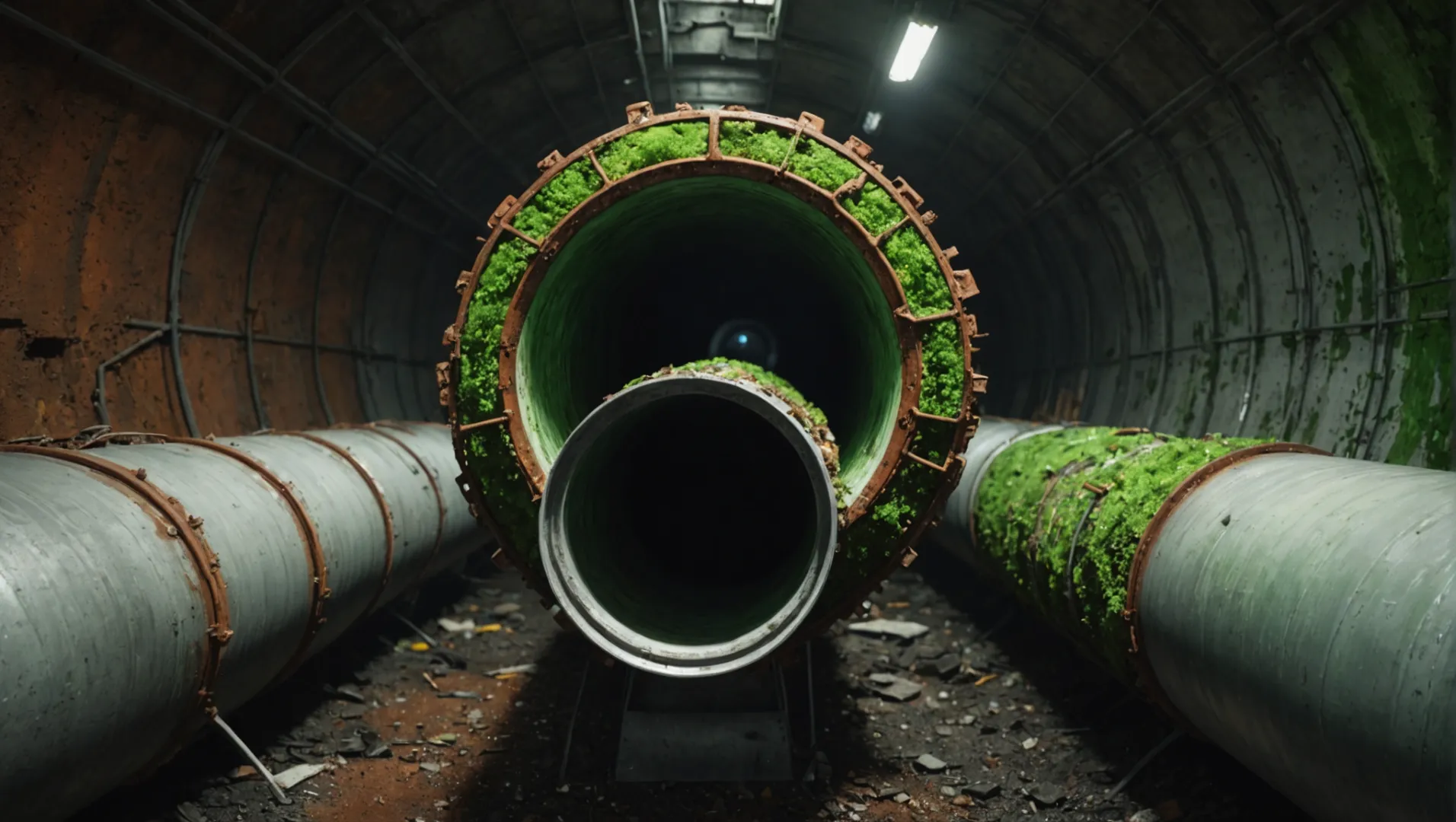
Mineral Deposits and Scale Formation
Mineral deposits, particularly calcium carbonate, form when hard water circulates through cooling pipes. Over time, these minerals precipitate out of the water and adhere to pipe walls, creating scale. This scale restricts water flow, leading to inefficient cooling.
To address this, regular water quality monitoring and treatment are crucial. Implementing a water softening system1 can reduce mineral content in the water, thus preventing scale buildup.
Debris and Particulate Matter
Debris such as rust flakes, dirt, and dust particles can accumulate in cooling pipes, especially if the system lacks proper filtration. As debris settles, it narrows the pipe’s effective diameter and disrupts fluid dynamics.
Installing an effective filtration system2 helps capture these particles before they enter the cooling circuit. Regular filter inspections and replacements are also necessary to ensure optimal performance.
Biological Growth
In some cases, biological growth like algae and bacteria can thrive in cooling systems, especially when water stagnates or the system runs at moderate temperatures. This growth can form biofilms that further obstruct pipes.
To prevent such occurrences, maintaining appropriate flow rates and using biocides as needed can control microbial proliferation. A thorough sanitization protocol3 should be established to keep biological growth at bay.
Corrosion
Corrosion of metal pipes can lead to the formation of rust and other corrosive products that flake off into the system. This not only contributes to debris-related blockages but also compromises pipe integrity.
Regular maintenance checks for signs of corrosion and using corrosion inhibitors can extend the life of cooling pipes. Materials like stainless steel or coated pipes can also be considered to minimize corrosion risks.
Summary Table of Causes and Solutions
Cause | Solution |
---|---|
Mineral Scale | Water softening system |
Debris | Installation of filtration systems |
Biological Growth | Use of biocides and regular sanitization |
Corrosion | Use corrosion inhibitors and inspect regularly |
By understanding these causes, operators can implement targeted solutions to keep their cooling systems running smoothly. Exploring each cause and adopting appropriate measures will significantly enhance operational efficiency.
Mineral scale is the primary cause of blockages.True
Mineral deposits, especially calcium carbonate, form scales that obstruct pipes.
Biological growth rarely affects cooling pipes.False
Algae and bacteria can form biofilms, causing significant blockages.
How Does Blockage Affect the Injection Molding Process?
Blockages in injection mold cooling pipes can lead to significant inefficiencies and defects in molded products.
Blockages in injection mold cooling pipes can disrupt thermal regulation, leading to product defects, increased cycle times, and potential equipment damage.
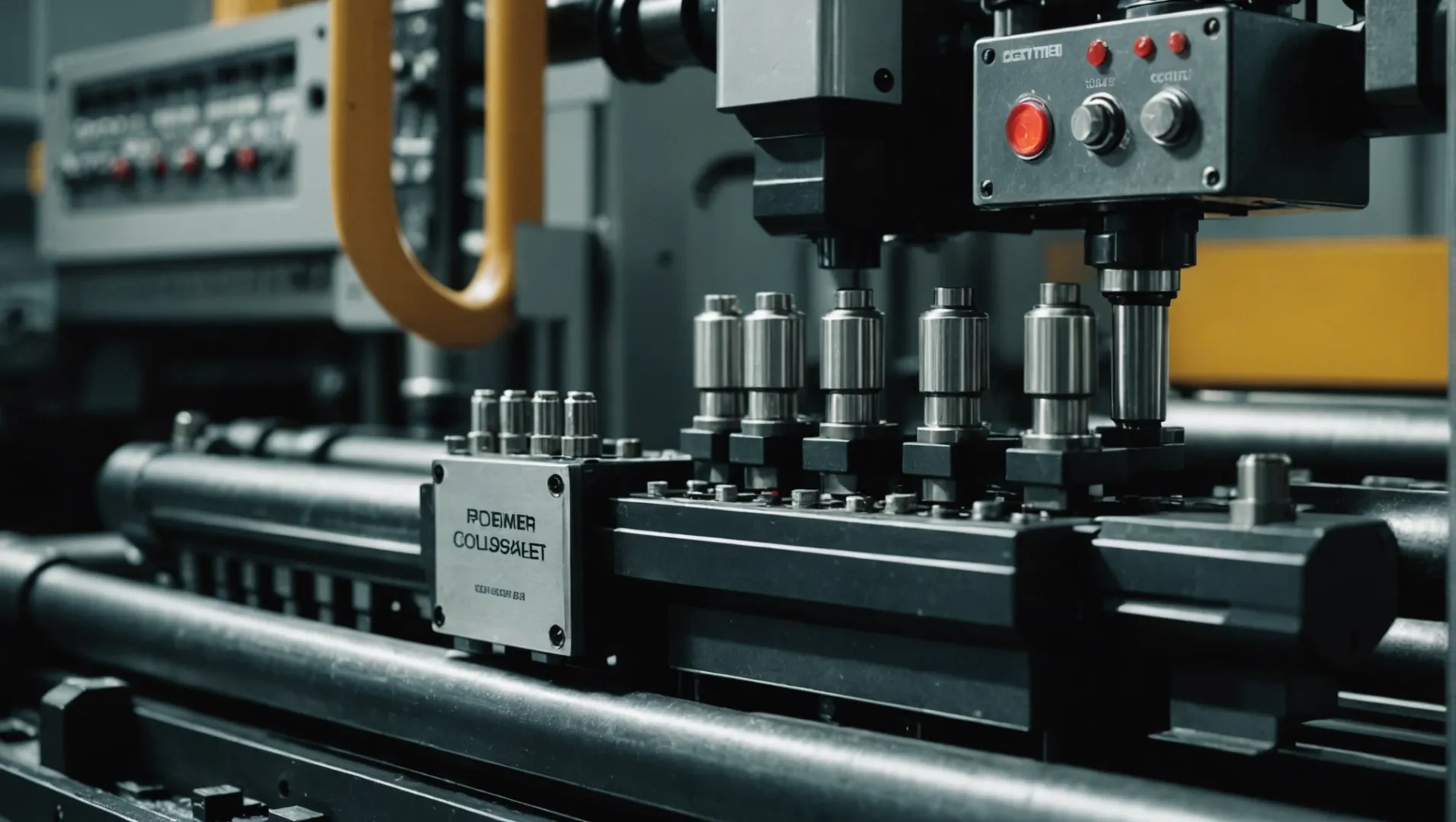
Understanding the Impact on Thermal Regulation
The cooling system in injection molding is critical for maintaining the mold at an optimal temperature. When blockages occur in the cooling pipes, it can significantly disrupt this thermal regulation. As the cooling efficiency decreases, the mold temperature may rise uncontrollably, causing defects such as warping or shrinkage in the molded products. Injection mold temperature control issues4 are a common challenge that can be traced back to cooling pipe blockages.
Increased Cycle Times and Production Costs
A blocked cooling system often results in increased cycle times as the mold takes longer to cool down to the desired temperature. This delay not only reduces the number of parts produced per hour but also increases production costs due to higher energy consumption and extended machine usage. In some cases, manufacturers may need to employ additional resources to monitor and manage the production process, further escalating costs.
Risk of Equipment Damage
Persistent blockages can lead to a pressure build-up within the cooling system. If not addressed promptly, this could cause leaks or even burst pipes, potentially damaging the mold or other equipment. Regular maintenance and blockage prevention strategies5 are essential to mitigate these risks and ensure the longevity of your injection molding equipment.
Quality Control Challenges
The inconsistency in mold temperature resulting from blockages can also compromise quality control efforts. The variations in thermal conditions can lead to uneven material distribution, impacting the structural integrity and appearance of the final product. This often necessitates additional quality checks and rework, thereby affecting overall production efficiency.
By understanding these impacts, manufacturers can implement targeted cleaning and maintenance routines to prevent blockages and maintain optimal injection molding performance.
Blockages increase injection molding cycle times.True
Blockages slow cooling, extending time needed to reach optimal temperatures.
Blockages improve thermal regulation in molds.False
Blockages disrupt cooling, causing mold temperature fluctuations and defects.
Which Cleaning Method is Best for Your Situation?
Choosing the right cleaning method for your cooling pipes ensures efficient blockage removal and prolonged equipment life.
The best cleaning method depends on the blockage type, with options including manual, chemical, or ultrasonic cleaning. Each method has unique benefits suited for specific obstructions, ensuring optimal performance and maintenance of injection mold cooling pipes.
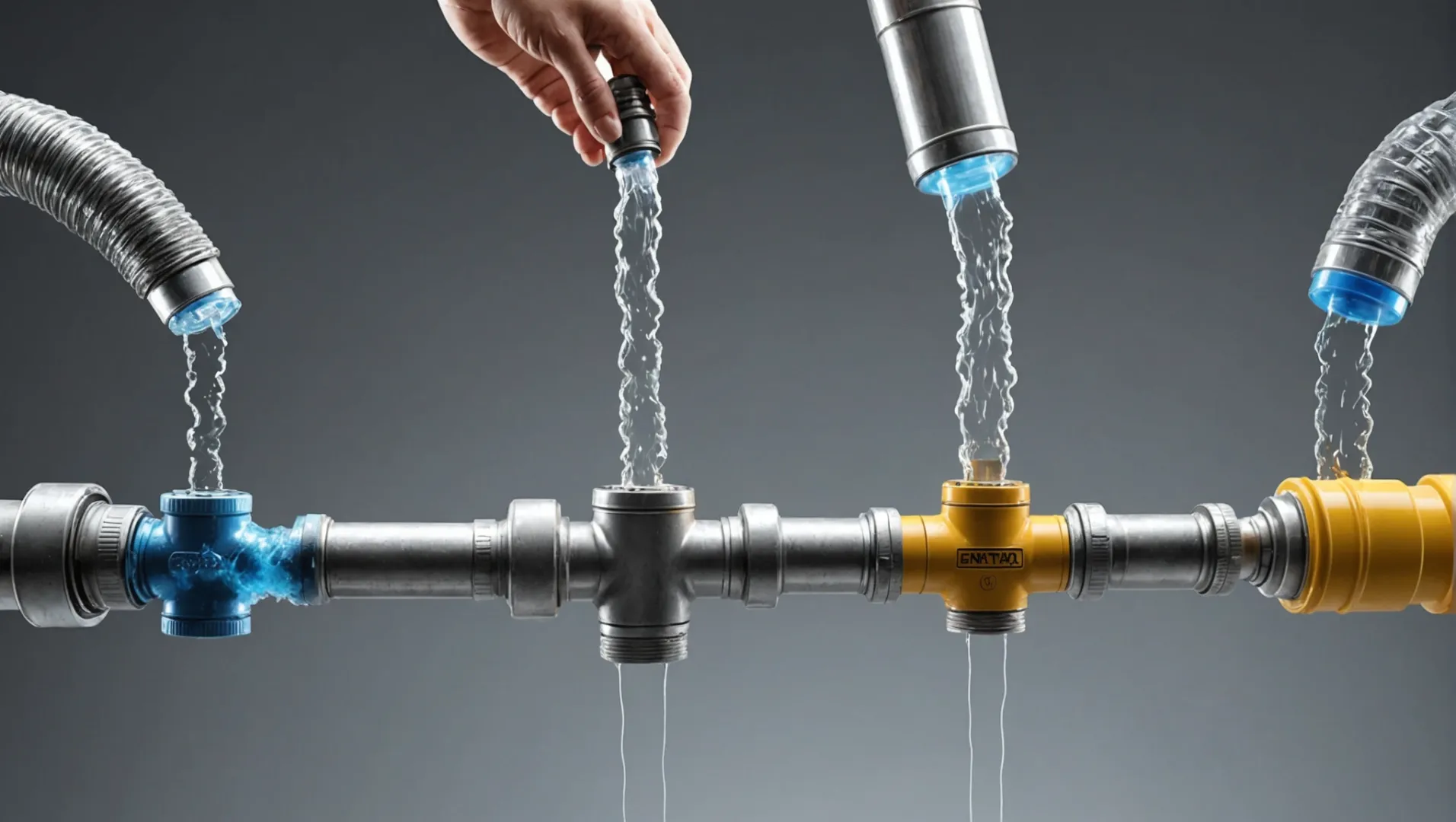
Understanding Blockage Types
Before selecting a cleaning method, it’s crucial to understand the nature of the blockage. Common types include scale buildup, residue from plastic materials, and oil deposits. Identifying the type helps in choosing the most effective cleaning technique.
- Scale Buildup: Often caused by hard water, scale is best tackled with chemical cleaning agents.
- Residue from Plastic Materials: These may require manual intervention using mechanical tools.
- Oil Deposits: Addressed effectively through chemical or ultrasonic cleaning.
Manual Cleaning: Precision in Action
Manual cleaning involves physically removing blockages using tools like iron or steel wire. This method is ideal for hard residues or when precision is needed.
Pros:
- Direct and precise blockage removal
- Cost-effective for small-scale operations
Cons:
- Labor-intensive and time-consuming
- Risk of pipe damage if not handled carefully
Chemical Cleaning: For Persistent Scales and Oils
Chemical cleaning involves using specific agents to dissolve blockages. This method is particularly effective against scale and oil deposits.
Blockage Type | Recommended Agent | Soaking Time (Approx.) |
---|---|---|
Scale | Acidic agent | 30-60 minutes |
Oil | Alkaline agent | 15-30 minutes |
Pros:
- Efficient for stubborn deposits
- Minimal physical labor required
Cons:
- Requires careful handling of chemicals
- Potential environmental concerns
Ultrasonic Cleaning: Advanced Technology at Work
Ultrasonic cleaning uses high-frequency sound waves to remove blockages. It’s effective for intricate or delicate cooling systems.
Pros:
- Non-invasive and thorough cleaning
- Quick process with minimal manual intervention
Cons:
- Higher initial setup cost
- Not suitable for all types of pipes or blockages
Choosing the Right Method for Your Needs
Consider your specific situation when choosing a cleaning method:
- For quick fixes or small operations: Manual cleaning is often sufficient.
- For persistent, large-scale issues: Chemical cleaning provides a more comprehensive solution.
- For advanced systems or delicate components: Ultrasonic cleaning is ideal due to its non-intrusive nature.
Evaluating these options ensures you select a method that aligns with your operational needs and budget constraints. For further insights into optimizing your cleaning process, consider exploring expert opinions on choosing the best cleaning agents6 or implementing ultrasonic technology7.
Manual cleaning is ideal for oil deposits.False
Manual cleaning is best for hard residues, not oil deposits.
Ultrasonic cleaning uses sound waves for blockage removal.True
Ultrasonic cleaning uses high-frequency sound waves to clean pipes.
How Can You Prevent Future Blockages in Cooling Pipes?
Preventing blockages in cooling pipes is crucial for maintaining consistent mold temperatures and avoiding costly disruptions.
Prevent future blockages in cooling pipes by implementing regular maintenance, water quality treatments, installing filters, and ensuring correct operational practices to keep your systems running smoothly.
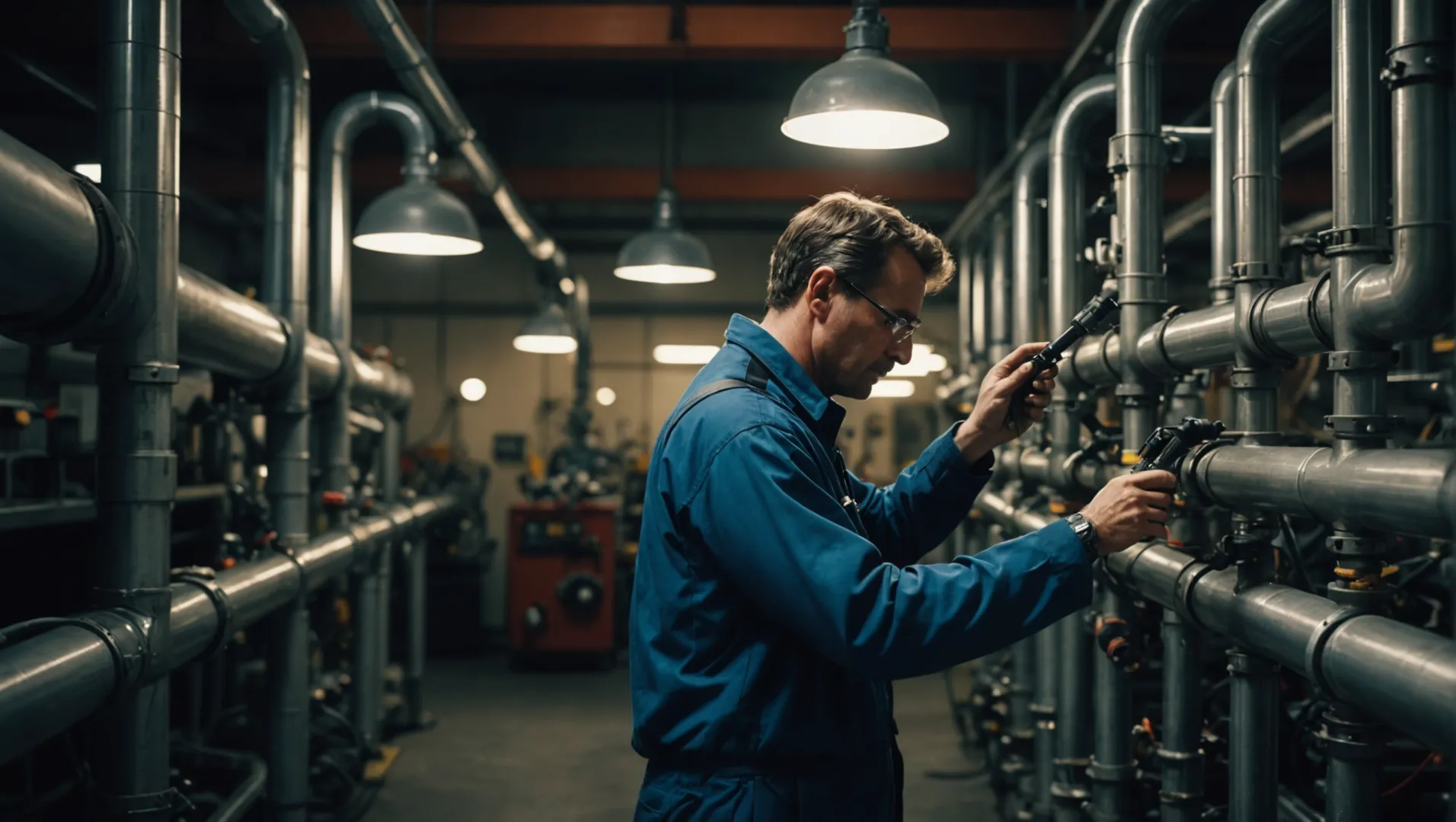
Importance of Regular Maintenance
Regular maintenance is essential to prevent blockages in cooling pipes. By routinely inspecting and cleaning the cooling system, you can identify potential issues before they become serious. This includes checking for loose connections and ensuring all components are functioning properly.
Consider setting a maintenance schedule that includes:
- Monthly inspections of the cooling pipes for any signs of wear or blockage.
- Bi-annual comprehensive cleanings using a combination of manual, chemical, or ultrasonic methods.
- Annual audits of the entire cooling system to address any long-term issues.
Water Quality Treatment
The quality of water circulating through cooling pipes can significantly affect their longevity and efficiency. Untreated water may contain impurities and minerals that lead to scale formation, which is a common cause of blockages.
Implement water treatment procedures such as:
- Using water softeners to remove hardness components.
- Filtering out impurities through sediment filters or reverse osmosis systems.
- Testing water quality regularly to ensure it meets the required standards.
Installing Filter Devices
Filters are a preventative measure to capture impurities before they enter the cooling pipes. Installing a filter device is a simple yet effective way to reduce the risk of blockages.
There are several types of filters available, such as mesh filters, cartridge filters, and self-cleaning filters. When choosing a filter, consider the following:
- Mesh Size: Ensure the mesh size is appropriate for capturing the impurities present in your cooling system.
- Maintenance Requirements: Opt for filters that are easy to clean and replace.
- Flow Rate Compatibility: Check that the filter supports the flow rate required by your system.
Correct Operational Practices
Finally, adopting correct operational practices can minimize stress on cooling pipes and prevent blockages. High temperatures and pressures during injection molding can exacerbate issues within the cooling system.
Here are some guidelines:
- Maintain consistent operational temperatures and pressures as per manufacturer’s recommendations.
- Avoid abrupt changes in operational settings that could shock the system.
- Train staff on best practices for operating and monitoring the cooling system effectively.
By integrating these preventive strategies into your maintenance routine, you can significantly reduce the risk of future blockages, ensuring a smoother production process and extending the lifespan of your equipment. For more information on maintaining injection mold systems, explore preventive maintenance tips8.
Regular maintenance prevents cooling pipe blockages.True
Routine inspections and cleanings help identify issues early.
Untreated water does not affect cooling pipe efficiency.False
Impurities in untreated water cause scale formation, leading to blockages.
Conclusion
By effectively managing blockages in cooling pipes, you ensure smoother operations and higher-quality products. Regular maintenance and proper water treatment are key to preventing future issues.
-
Learn how water softening systems prevent mineral buildup.: Save money on cleaning products · Improve the efficiency of your water heater · Help treat skin conditions · No more bad hair days · Reduce cleaning … ↩
-
Find effective filtration solutions for your cooling system.: Extend the life of your cooling tower, reduce cleanings and maintenance, and increase efficiency with LAKOS Cooling Tower Filtration products. ↩
-
Discover effective sanitization methods to prevent biofilm.: Scale, corrosion, sediment controls, and system cleaning are critical for cooling tower operations and Legionnaires’ disease prevention. ↩
-
Explains how temperature fluctuations affect product quality and manufacturing efficiency.: Higher melt temperatures increase energy consumption, degrade the polymer, and extend the cooling time needed to create a dimensionally stable … ↩
-
Offers strategies to prevent blockages and ensure smooth operation.: 5. Avoid Cooling at Weld Lines: Since weld lines are the coolest areas, avoid placing cooling channels near them to prevent exacerbating weld line defects and … ↩
-
Learn which agents efficiently dissolve blockages in cooling pipes.: Slide is the brand we use for cleaning our molds and we run a chemical unit from PPE with CLR pumping through it for our water circuits. Works pretty well. ↩
-
Discover how ultrasonic waves offer efficient cleaning solutions.: Ultrasonic cleaning uses a process called cavitation – the implosion of billions of micron-sized vacuum air bubbles – against surfaces immersed … ↩
-
Gain deeper insights into maintaining injection mold cooling systems efficiently.: Inspect the molding machine cylinders. Look for leakage at gland seals or the head seals (pistons). Make sure that the cylinder rod of the … ↩