Injection molding is more than just a manufacturing process; it’s an art that shapes our everyday products. Understanding the clamping methods involved can revolutionize production efficiency and product quality.
The main clamping methods in injection molding include hydraulic, hydraulic-mechanical, mechanical, direct pressure, and center clamping. Each has unique working principles and ideal applications, from large automotive parts to precision electronic components.
While this overview provides a basic understanding, delving deeper into each method reveals how they can be strategically applied in different manufacturing scenarios to optimize performance and efficiency.
Hydraulic clamping is ideal for large automotive parts.True
Hydraulic clamping provides the strong force needed for large molds.
- 1. How Does Hydraulic Clamping Enhance Production Efficiency?
- 2. What Are the Advantages of Hydraulic-Mechanical Clamping for Mass Production?
- 3. Why Is Mechanical Clamping Preferred for Small Precision Products?
- 4. When Should Direct Pressure Clamping Be Used for High-Precision Products?
- 5. Conclusion
How Does Hydraulic Clamping Enhance Production Efficiency?
Hydraulic clamping systems are pivotal in injection molding, offering robust solutions to enhance production efficiency across various applications.
Hydraulic clamping enhances production efficiency by providing stable and adjustable clamping force, crucial for large, complex, and high-precision product manufacturing. This system ensures mold integrity and reduces cycle times, thereby improving overall productivity.
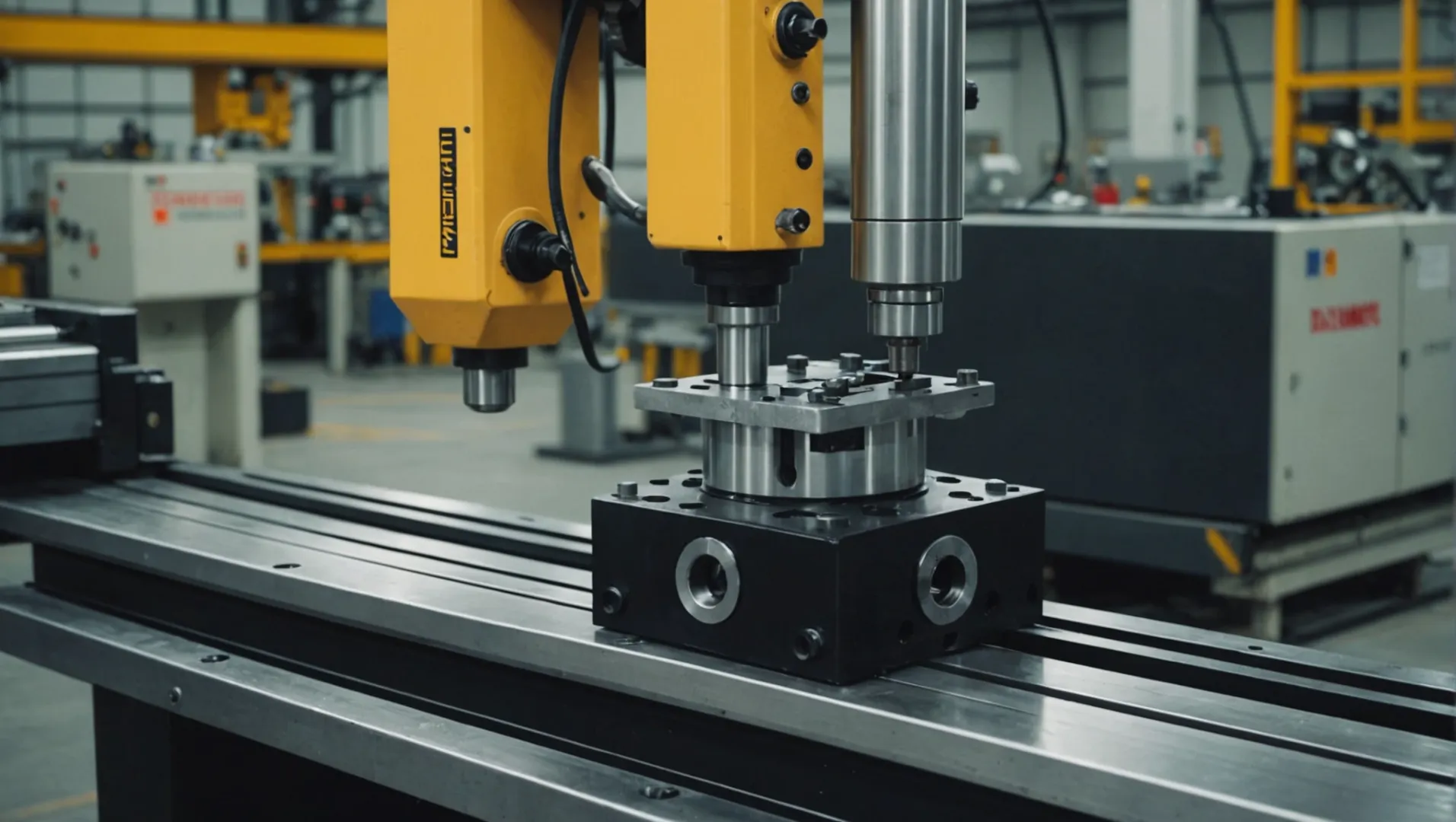
Understanding Hydraulic Clamping
Hydraulic clamping uses hydraulic systems to generate a clamping force that secures the mold during the injection molding process. The primary component is the hydraulic cylinder, which, through hydraulic oil pressure, pushes the clamping mechanism to close and lock the mold. This process ensures that the mold remains tightly sealed against the pressure of the injected material.
Applications in Production
-
Large Product Manufacturing
Hydraulic clamping is ideal for producing large-scale products, such as automotive parts and home appliance housings, where substantial clamping force is required. The ability to maintain a strong grip on large molds without compromising on the integrity of the product is a significant advantage. The stability offered by hydraulic systems ensures that even under high pressure, the mold remains intact, minimizing defects.
-
Complex Shape Product Manufacturing
For products with intricate designs or irregular mold parting lines, hydraulic clamping provides flexibility and precision. It can adapt to various mold structures, ensuring all parts fit seamlessly. This adaptability is crucial for maintaining high-quality standards in complex shapes, reducing waste and rework costs.
-
High-Precision Product Manufacturing
Despite a slower response time compared to other systems, hydraulic clamping is valuable in scenarios requiring precise force adjustment. In manufacturing settings that demand high accuracy but not necessarily speed, such as small to medium-sized high-precision products, hydraulic clamping can be finely tuned to provide the exact pressure needed without overexerting or under-clamping.
Benefits Over Other Clamping Methods
Hydraulic systems stand out due to their ability to apply consistent and adjustable pressure. Unlike mechanical systems that might offer limited adjustability, hydraulic clamping can be modified in real-time to accommodate variations in product design or material properties. This adaptability can significantly enhance production efficiency by reducing setup time and enabling quick transitions between different product lines.
A key comparison can be seen in the table below:
Feature | Hydraulic Clamping | Mechanical Clamping | Direct Pressure Clamping |
---|---|---|---|
Clamping Force | Adjustable and stable | Fixed range | Directly applied |
Adaptability | High | Low | Medium |
Precision | High | Medium | High |
Setup Time | Moderate | Low | Fast |
Hydraulic clamping not only supports various product sizes and complexities but also contributes to a more sustainable manufacturing process1. Its ability to efficiently handle large production runs while maintaining precision makes it a preferred choice in many industries.
Hydraulic clamping reduces cycle times in production.True
Hydraulic clamping ensures mold integrity and stability, decreasing cycle times.
Mechanical clamping offers higher precision than hydraulic systems.False
Hydraulic systems provide higher precision due to adjustable pressure capabilities.
What Are the Advantages of Hydraulic-Mechanical Clamping for Mass Production?
In the fast-paced world of mass production, efficient and reliable clamping methods are essential to meet demand and maintain product quality.
Hydraulic-mechanical clamping combines hydraulic power with mechanical leverage to offer superior efficiency, speed, and stability in mass production settings, particularly for medium and large injection molded products.
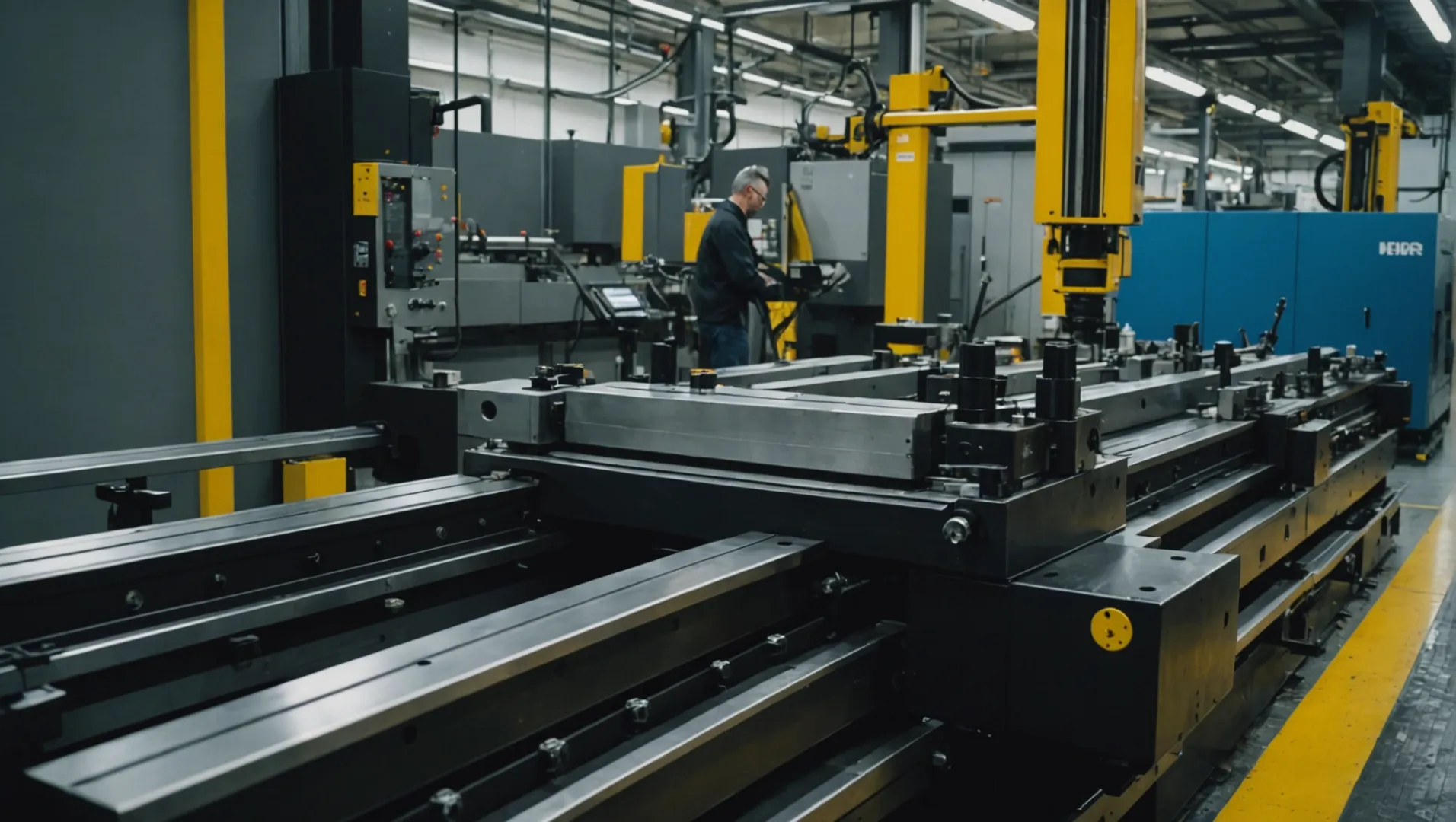
Understanding Hydraulic-Mechanical Clamping
Hydraulic-mechanical clamping leverages the strengths of both hydraulic and mechanical systems. Initially, hydraulic power is used to initiate the clamping process, while a mechanical structure amplifies this force, enabling the system to exert substantial clamping pressure efficiently. This combination allows for the use of smaller hydraulic systems, minimizing energy consumption and maintenance.
Efficiency in Mass Production
In mass production environments, time and precision are of the essence. Hydraulic-mechanical clamping excels in these settings by providing rapid cycle times due to its quick clamping action. The mechanical components act swiftly, reducing overall cycle time and increasing throughput. This is particularly beneficial in the production of medium and large products like plastic barrels2 and plastic pallets3, where production volumes are high.
Feature | Benefits |
---|---|
Combined Force System | Efficient use of power, reduced wear |
Quick Clamping Action | Shortened cycle times |
Stability | Consistent quality across high volumes |
Lower Hydraulic Demand | Reduced energy consumption and costs |
Application in High-Speed Production
The ability of hydraulic-mechanical systems to handle high-speed injection molding is another significant advantage. By utilizing a mechanical structure, these systems achieve faster clamping speeds compared to purely hydraulic ones. This speed is crucial for producing thin-walled plastic products that require rapid injection processes to maintain quality.
Stability and Consistency
The dual mechanism ensures a more stable clamping force, reducing the likelihood of defects in products. In mass production settings, where quality consistency is paramount, hydraulic-mechanical clamping provides a reliable solution. It minimizes variations in clamping force that can arise from wear in purely mechanical systems or fluctuations in hydraulic pressure alone.
Hydraulic-mechanical clamping thus represents an optimal choice for manufacturers seeking to enhance productivity without compromising on quality, especially when dealing with large-scale injection molding operations.
Hydraulic-mechanical clamping reduces energy costs by 30%.False
The context doesn't specify a 30% reduction in energy costs.
Quick clamping action shortens cycle times in production.True
The context states that quick clamping reduces cycle times.
Why Is Mechanical Clamping Preferred for Small Precision Products?
Mechanical clamping offers stability and precision, making it ideal for small, intricate injection molded products.
Mechanical clamping is favored for small precision products due to its stability, cost-effectiveness, and ability to maintain dimensional accuracy. The simple structure and reliable performance make it a preferred choice in scenarios where high precision and quality consistency are paramount.
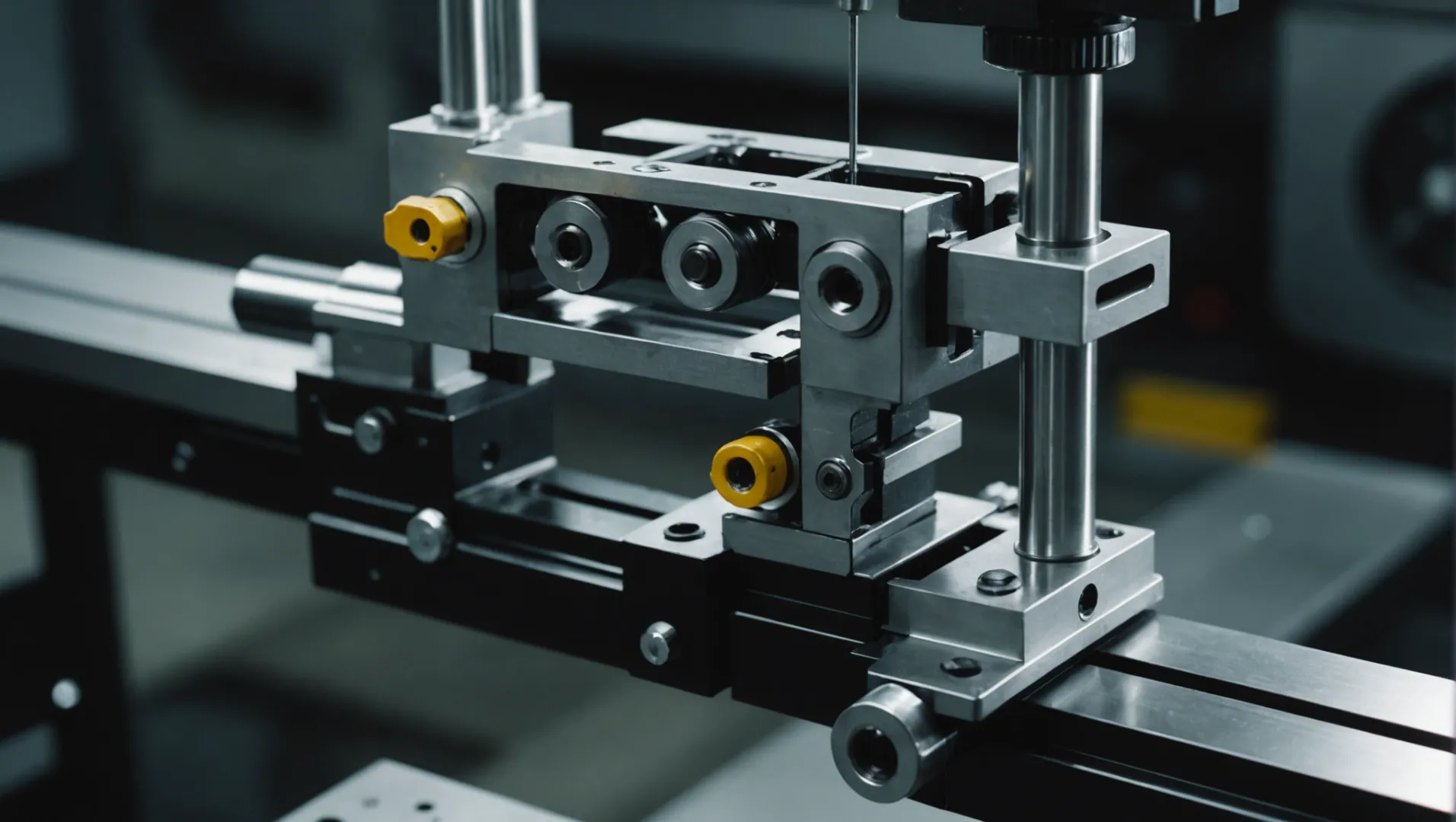
The Mechanics Behind Mechanical Clamping
Mechanical clamping relies on a mechanical linkage mechanism, often utilizing an elbow or toggle system, to achieve the necessary clamping force. This method is characterized by its simplicity and reliability, which are critical when producing small precision products. The clamping force is generated through the geometric arrangement and mechanical principles of the linkage, ensuring consistent pressure throughout the molding process.
Advantages of Mechanical Clamping in Precision Molding
-
Stability and Consistency: Mechanical clamping systems provide consistent clamping force, which is essential for maintaining the dimensional accuracy of small products. This stability helps in achieving uniformity across production batches, reducing defects and enhancing product quality.
-
Cost-Effectiveness: Compared to other clamping methods like hydraulic or direct pressure systems, mechanical clamping typically incurs lower maintenance costs. Its simple structure not only minimizes potential points of failure but also makes it more affordable to operate over time.
-
Precision: For small precision products, slight deviations can lead to significant quality issues. The precise nature of mechanical clamping ensures that molds close correctly and that each part remains true to its intended design.
Ideal Scenarios for Mechanical Clamping
-
Production of Small Toys and Gadgets: Products such as miniature toys or electronic gadgets benefit from the accuracy provided by mechanical clamping. The method’s ability to deliver consistent results across numerous cycles is invaluable in these applications.
-
High-Volume Production: When large quantities of small parts are required, mechanical clamping systems prove advantageous due to their durability and low operational costs. The reliability of these systems ensures minimal downtime, crucial for high-volume manufacturing.
In conclusion, the precision and reliability of mechanical clamping make it an ideal choice for the production of small precision products, where maintaining high standards of accuracy and consistency is essential. For further insights into how different clamping methods compare, explore our detailed guide on injection molding techniques4.
Mechanical clamping is more cost-effective than hydraulic systems.True
Mechanical clamping incurs lower maintenance costs than hydraulic systems.
Mechanical clamping cannot maintain dimensional accuracy in small products.False
It provides consistent force, ensuring precision and accuracy.
When Should Direct Pressure Clamping Be Used for High-Precision Products?
Direct pressure clamping is pivotal in manufacturing high-precision products, ensuring unparalleled accuracy and quality.
Direct pressure clamping is ideal for high-precision products like optical lenses and precision electronic components. It applies even pressure, ensuring tight mold closure and dimensional accuracy, minimizing defects from uneven clamping.

Understanding Direct Pressure Clamping
Direct pressure clamping stands out due to its straightforward mechanism. Unlike other methods that rely on complex systems of levers or hydraulics, direct pressure clamping uses a linear drive device to apply force directly onto the mold. This method is devoid of intermediate mechanical transmissions, making it highly efficient for ensuring uniform pressure distribution across the mold.
Ideal Scenarios for High-Precision Production
Direct pressure clamping is particularly suited for products requiring extreme precision. For instance, when manufacturing optical lenses or the plastic casings of precision electronic components, maintaining mold integrity is crucial. By delivering direct and consistent pressure, this method minimizes the risk of defects such as warping or misalignment, which can arise from uneven clamping forces.
Moreover, direct pressure clamping ensures that the dimensional accuracy of the product is maintained, which is vital in sectors like electronics where even minor deviations can lead to significant performance issues.
Advantages in Frequent Mold Change Scenarios
In production environments where mold changes are frequent, such as small injection molding facilities handling diverse orders, the simplicity of direct pressure clamping offers a significant advantage. The straightforward design allows for quick and easy installation and removal of molds, drastically reducing downtime and boosting overall production efficiency. This feature makes it an attractive choice for businesses that need to switch between different product lines swiftly.
Practical Considerations and Limitations
While direct pressure clamping offers numerous benefits, it’s essential to understand its limitations as well. For instance, it may not provide the same level of force amplification found in hydraulic-mechanical systems, which could limit its application in producing very large or exceptionally complex parts.
Nevertheless, for most high-precision small to medium-sized products, the direct pressure clamping method5 remains unmatched in delivering consistent quality and precision.
In conclusion, understanding when and how to apply direct pressure clamping can significantly enhance the quality and efficiency of high-precision manufacturing processes.
Direct pressure clamping uses hydraulic systems.False
It uses a linear drive device, not hydraulic systems, for force application.
Direct pressure clamping minimizes mold warping.True
It ensures uniform pressure, reducing defects like warping or misalignment.
Conclusion
Understanding these clamping methods can enhance your injection molding processes. Aligning strategies with product requirements ensures improved efficiency and quality.
-
Explore how hydraulic systems contribute to sustainable manufacturing practices.: Hydraulic chucks contribute to sustainability in machining. The clamping technology conserves resources, improves workpiece quality and reduces … ↩
-
Explore why plastic barrels are essential in various industries.: They can be cost-effectively sealed inside the barrels, enabling easy access to the liquids inside. ↩
-
Learn how plastic pallets improve logistics efficiency.: The main benefit of plastic pallets is that they can be reused for a long time without breakage. They are perfect for storage and reuse in … ↩
-
Discover more about various clamping techniques and their applications.: There are 3 kinds of quick mold change systems: mechanical, hydraulic and magnetic clamping system. ↩
-
Explore how direct pressure clamping enhances precision in manufacturing.: The pressure in the interior of the injection mold is a key performance indicator of the quality of the molded part. Continuously measurement and control of the … ↩