I remember the first time I needed to choose the size and place for a point gate. It felt very overwhelming! Every detail matters in injection molding, particularly when creating precise parts.
Choose the right point gate size by considering diameter and length based on your product’s thickness. Position gates to minimize visible marks, using small gates for thin-walled items and large ones for thick products.
Do you remember my first project with small mobile phone buttons? I quickly understood the importance of gate diameter. A diameter of 0.8mm was perfect. It filled the thin walls without causing any short shots. On the other hand, with larger plastic toys, I increased the diameter to around 2mm. This size probably filled every corner well. No unsightly marks were left.
Positioning is equally important. For example, when designing a toy dinosaur, I placed the gates underneath. Hidden gates kept the front looking clean. Carefully considering both appearance and function is crucial, especially with complex shapes. It feels like balancing art and science with every creation.
Smaller gates are best for thick-walled items.False
Smaller gates suit thin-walled products, not thick-walled items.
Gate positioning affects visible marks on the product.True
Proper gate positioning helps minimize visible marks on products.
How Do You Choose the Right Gate Diameter?
I still remember the first time I understood how important choosing the right gate diameter is for injection molding. This discovery transformed product quality. It also significantly improved manufacturing efficiency.
Gate diameter selection depends on product size, wall thickness and how fluid the plastic is. Smaller diameters suit thin-walled items very well. Larger diameters are necessary for thicker products. Proper flow and fill of thicker items rely on larger diameters.

Product Size and Wall Thickness
In my early mold design days, I remember designing tiny mobile phone buttons. These were small items with thin walls. A precise touch was necessary. We often used a smaller gate diameter (0.5-1.5mm). This allowed the material to fill the mold quickly, reducing the chance of defects. For larger, thick-walled items, a bigger gate diameter (1.5-3mm) was very important. This allowed enough material flow to fill the mold properly.
Product Type | Recommended Gate Diameter |
---|---|
Thin-walled products | 0.5-1.5mm |
Thick-walled products | 1.5-3mm |
Material Fluidity
The fluidity of the plastic is very important. Some materials flow easily through smaller gates. I once worked with high-flow polymers; adjusting the gate diameter was key to a smooth injection process.
Aesthetic and Functional Requirements
Aesthetics can be very important. I worked on transparent, shiny products once where gate marks1 could ruin the look, so we positioned the gate in hidden areas to keep the appearance sleek.
Mold Design Considerations
Mold design details are fascinating. Shorter gate lengths (0.5-2mm) help reduce pressure loss and achieve higher cavity pressure, supporting material flow and demolding processes.
Additionally, consider the positioning of the gate relative to structural parts like ribs to avoid weld marks and trapped air.
Summary Table
Throughout years of practice, mastering these elements has improved mold performance and product quality:
Factor | Impact on Gate Diameter |
---|---|
Product Size | Larger size = Larger diameter |
Wall Thickness | Thicker walls = Larger diameter |
Material Fluidity | Higher fluidity = Smaller diameter possible |
Aesthetic Requirements | Non-visible placement recommended |
Mold Design | Shorter lengths aid pressure management |
A perfect balance is vital; it is really about getting things right.
Thin-walled products need smaller gate diameters.True
Thin walls require 0.5-1.5mm gates for quick filling and reduced short shots.
High fluidity materials require larger gate diameters.False
High fluidity allows smaller gates as the material flows easily through them.
How Does Gate Length Affect Injection Molding?
Do you ever think about how something small like gate length might really cause a big change in injection molding?
Gate length influences injection molding. It controls melt pressure and flow into the mold cavity. This directly impacts product quality. Shorter gate lengths reduce pressure loss. They allow efficient filling. Demolding becomes smoother.
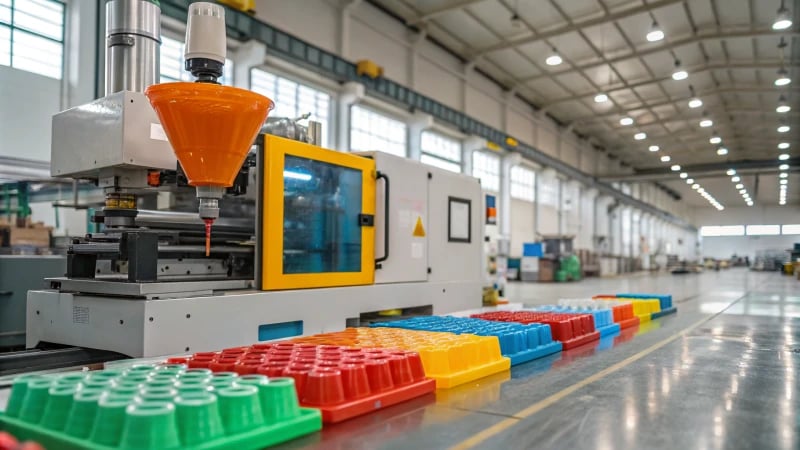
Importance of Gate Length in Injection Molding
When I began learning about injection molding, I did not realize how important the gate length was. Imagine pouring syrup on a pancake. If you pour too slowly or unevenly, you get a sticky mess. Similarly, in injection molding, the gate length, often between 0.5-2mm, affects how well the plastic flows into the mold. A shorter gate length allows the plastic to flow smoothly, reducing pressure loss. This helps the melt enter the mold cavity with higher pressure. This is really important for thin-walled parts, where you want to prevent defects like short shots.
Balancing Gate Length and Diameter
Balancing gate length and diameter is like creating the perfect recipe. You don’t want too much salt or too little spice. In molding terms, a smaller gate diameter increases pressure and speed. However, a long gate length might slow down the flow and cause defects.
For example:
Product Type | Gate Diameter (mm) | Gate Length (mm) |
---|---|---|
Small Phone Buttons | 0.8 | Optimal |
This setup helps fill effectively without lowering appearance quality.
Impact on Product Quality
Short gate lengths help in the demolding process by lowering stress in the gate area—imagine your cake not sticking to the pan after baking. Fewer marks mean better-looking products, especially those with shiny finishes. Positioning point gates wisely can hide any marks on parts that are not visible.
Considerations for Complex Shapes
Every detail counts with complex-shaped products. I learned that choosing the correct gate position2 and length is crucial. The goal is for the melt to fill all areas smoothly to avoid weld marks. By picking the right gate placement, you guide the flow efficiently around features like ribs or thin walls.
For designers like me, balancing these factors is needed to meet functional and aesthetic needs in projects. Tools like CAD software3 really help simulate different gate designs and predict results better.
- Key Takeaway: Shorter gates are really good for reducing pressure loss and ensuring smooth mold filling while minimizing visible defects during demolding. Smart positioning and sizing improve overall product quality and manufacturing effectiveness.
Explore more about gate design4 to understand better and use best practices in your projects.
Shorter gate lengths reduce pressure loss.True
Shorter gates minimize pressure loss, aiding efficient cavity filling.
Longer gate lengths enhance flow efficiency.False
Longer gates hinder flow efficiency, increasing defects in molding.
Why is Gate Position Critical for Product Appearance?
Have you ever thought about how small details in product design influence its appearance? Let’s explore the world of gate positioning in injection molding.
Gate position is very important in injection molding. It affects the look by reducing visible marks. It provides smooth flow of the material. Proper placement avoids blemishes on important surfaces. This keeps the product looking good.
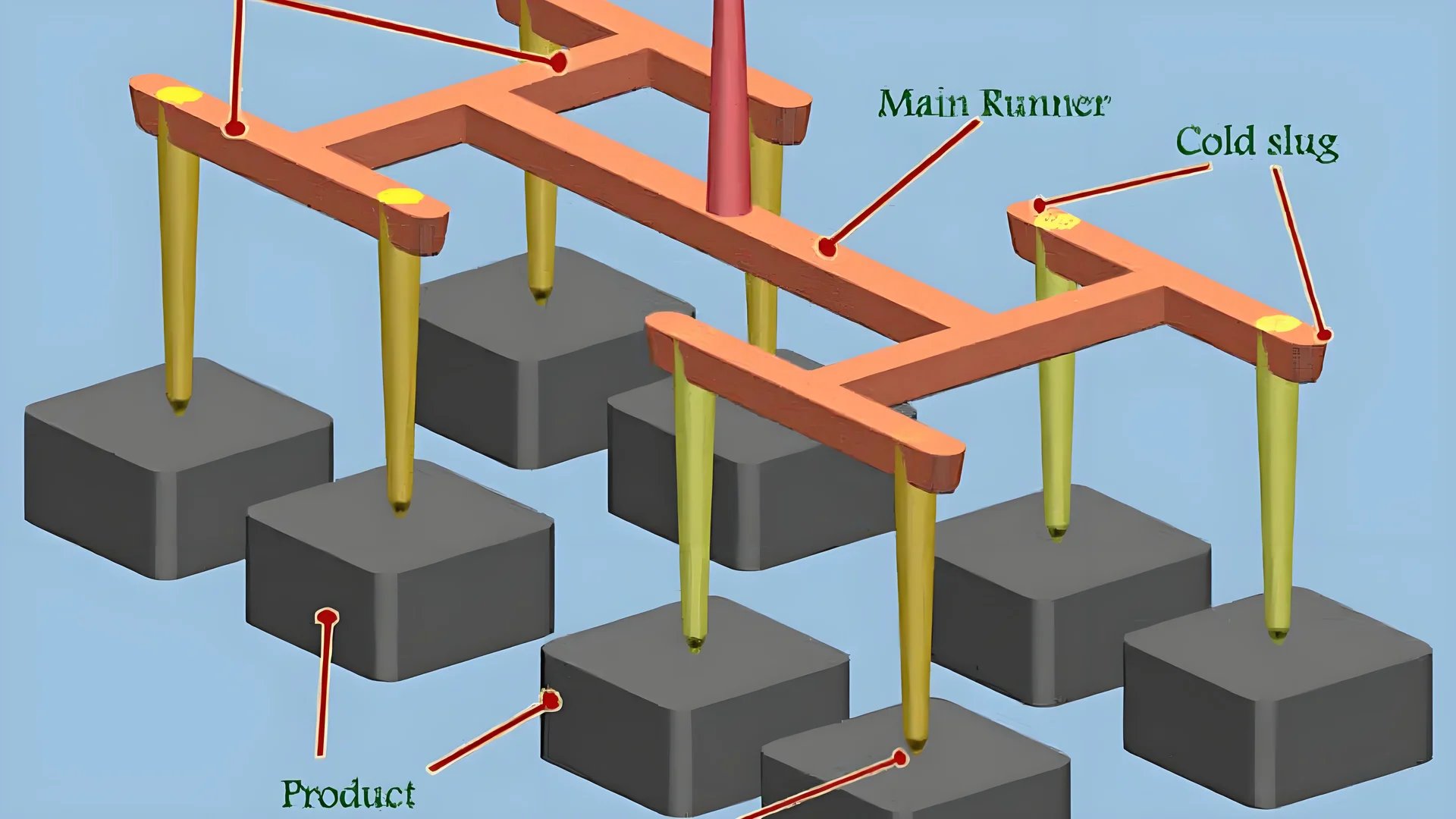
Understanding the Role of Gate Position
I recall my first big project in injection molding. I stared at a mold design like it was a treasure map. The gate position5 was this mysterious "X" marking the spot. It directed how molten plastic traveled through the mold. This detail was more than just technical; it was crucial in preventing those annoying blemishes that ruin a finished product’s look. For transparent items, a wrongly placed gate could be disastrous, leading to ugly flow lines.
Influence on Aesthetic Quality
From my experience, I have learned something important: a strategically placed gate becomes a hidden hero in product aesthetics. Hiding gates in less visible areas, like the back or underside, is clever and avoids marring main surfaces. This matters significantly in consumer electronics where every visual detail counts.
Balancing Flow and Appearance
Balance is everything here. For complex shapes with thin-walled ribs, placing the gate near the rib’s start is smart as it ensures proper flow and helps avoid short shots or weld lines that could harm appearance. Perfecting this balance took several trials and errors for me, but the flawless product at the end was worth it—really worth it.
Practical Considerations in Gate Design
Gate Size and Length Table
Product Type | Gate Diameter (mm) | Gate Length (mm) |
---|---|---|
Small, thin-walled | 0.5 – 1.5 | 0.5 – 2 |
Large, thick-walled | 1.5 – 3 | 0.5 – 2 |
Choosing the right gate size is like solving a puzzle where every piece must fit perfectly. Smaller gates work well for speed and pressure in thin walls, while larger ones guarantee sufficient flow for thicker sections.
Case Study: Impact on High-Gloss Products
Working with high-gloss plastics taught me valuable lessons: gate placement is crucial to prevent flow lines and keep that perfect shine intact—a well-positioned gate truly affects a product’s allure.
Key Takeaways for Designers
For designers like Jacky6 and myself, understanding these subtleties is very important—not just about creating something functional but crafting products that amaze and delight. Gaining insights into gate positioning equips us to design with both function and beauty in mind so our creations not only meet but exceed expectations.
Improper gate placement causes flow lines in transparent products.True
Incorrect gate positions disrupt flow, creating visible lines in clear items.
Smaller gates are used for large, thick-walled products.False
Larger gates are needed for thicker walls to ensure adequate flow.
What Are the Common Mistakes in Gate Design?
Have you ever become caught in mistakes with gate design? This happens to many people. Let’s learn how to avoid these typical errors.
Common mistakes in gate design include picking the wrong gate size. Poor gate positioning is another mistake. Designers often forget about how the gate looks. Successful design needs careful thought. One should look at the product size and wall thickness. Aesthetic preferences are also important. Thus, they should be factored in.
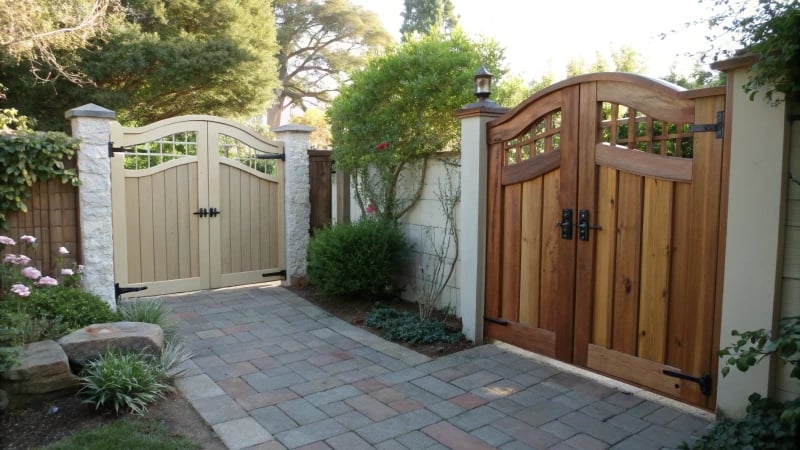
Mistake 1: Incorrect Gate Size Selection
Once, I underestimated the importance of gate size in a project. I thought it was simple. However, a small gate diameter7 can cause short shots in thin-walled products, while a large gate lengthens solidification time, disrupting the production process.
Key Considerations:
Product Type | Recommended Diameter |
---|---|
Small/Thin-Walled | 0.5-1.5 mm |
Large/Thick-Walled | 1.5-3 mm |
Here’s a helpful guide I wish I had back then.
Mistake 2: Poor Gate Position
Gate positioning resembles real estate—location is key! Once, I placed a gate where it left visible marks, which was undesirable. Gates should be positioned in less visible spots to protect the product’s look. For toys, place the gate at the back to maintain front aesthetics.
Position affects not only appearance but also molding quality. Ensure melt flow is smooth8 to avoid defects like weld marks.
Mistake 3: Ignoring Aesthetic Requirements
I recall a glossy product ruined by gate marks because I ignored its aesthetic needs. High-gloss or clear items suffer from these marks as they damage visual charm.
Visual Impact Table:
Material Type | Aesthetic Concern |
---|---|
Transparent | Visibility of Marks |
High-Gloss | Gloss Disruption |
Always consider how gate placement9 affects transparency and shine to keep designs sleek and attractive.
By understanding these common mistakes and adjusting designs accordingly, you can enhance both functionality and appearance. Explore specific resources if curious about gate design10. Every decision impacts your final product’s performance and looks.
Small gate diameters cause short shots in thin-walled products.True
Small gates restrict material flow, leading to incomplete filling.
Ignoring aesthetics in gate design affects product transparency.True
Gate marks can be visible on transparent materials, reducing appeal.
Conclusion
Choosing the right size and location for a point gate in injection molding is crucial for product quality, aesthetics, and manufacturing efficiency, balancing diameter, length, and position effectively.
-
Explore effective strategies for positioning gates to enhance product aesthetics and functionality. ↩
-
Understanding melt flow helps in optimizing gate design to ensure efficient cavity filling and defect reduction. ↩
-
CAD software allows for precise simulations of gate designs, enhancing the prediction of molding outcomes. ↩
-
Exploring best practices provides insights into efficient gate design, enhancing product quality and manufacturing efficiency. ↩
-
Discover how gate position affects material flow and product quality. ↩
-
Learn how strategic gate placement enhances product design and manufacturing. ↩
-
Learn why small gate diameters are crucial for thin-walled products to prevent short shots. ↩
-
Explore techniques ensuring smooth melt flow in complex shapes to avoid defects. ↩
-
Discover how gate placement influences the aesthetic quality of molded products. ↩
-
Find comprehensive guidelines on effective gate design for optimal results. ↩