Diving into the world of plastic component design can feel overwhelming, especially when deciding on those crucial B side features.
When selecting plastic B side features, consider material properties, structural integrity, manufacturability, and cost efficiency to optimize design for functionality and production.
While this gives a quick snapshot, understanding each factor in depth can really boost your design process and results. I remember when I first started out, the complexities seemed endless. But diving deeper into these aspects ensured my designs not only looked good but performed even better. Let’s explore these factors to make sure your designs tick all the right boxes.
Material properties impact B side feature choice.True
Material properties determine durability and compatibility with design needs.
Cost efficiency is irrelevant in B side feature selection.False
Cost efficiency is crucial to maintain budget constraints in production.
- 1. How Do Material Properties Influence B Side Design?
- 2. How Does Structural Integrity Impact B Side Features?
- 3. Why is manufacturability important for plastic B side features?
- 4. How Does Cost Efficiency Influence Design Decisions?
- 5. What are the common challenges in designing plastic B side features?
- 6. How can designers effectively balance aesthetic and functional requirements?
- 7. Conclusion
How Do Material Properties Influence B Side Design?
Ever wondered why some gadgets just work perfectly and others seem to fall apart? It often comes down to the materials used in their design.
Material properties such as strength, flexibility, and thermal resistance are crucial in B side design, impacting durability, functionality, and cost-effectiveness of products. Selecting appropriate materials is essential for optimal performance.
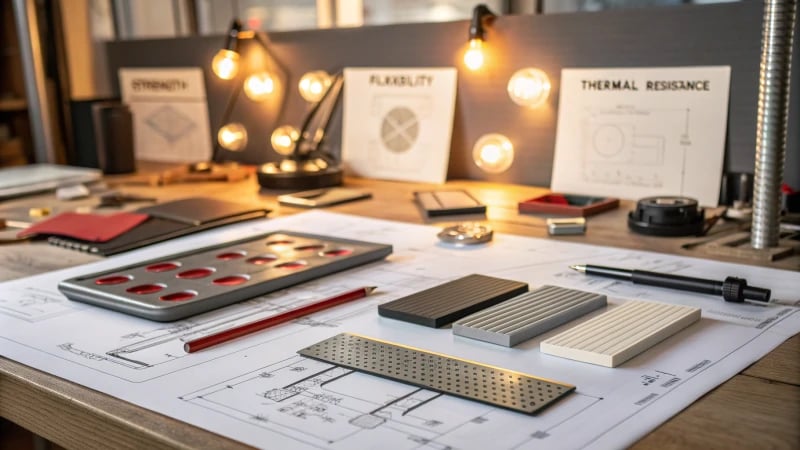
Importance of Mechanical Properties
I remember when I first realized the importance of mechanical properties in design. It was during a project where I had to select materials for a new smartphone case. The client wanted it to be lightweight yet strong enough to withstand drops. That’s when I dove deep into understanding tensile strength1 and impact resistance.
Table: Mechanical Properties Impact
Property | Influence on Design |
---|---|
Tensile Strength | Dictates load-bearing capacity |
Flexibility | Allows for complex shapes |
Impact Resistance | Essential for durability |
Role of Thermal Properties
Thermal properties were another game-changer for me. Picture this: you’re designing a device that needs to function in both freezing winters and scorching summers. If the material expands too much with heat, the entire design could be compromised. That’s why materials with low thermal expansion rates are like gold.
Chemical Resistance Considerations
I’ve also learned the hard way about chemical resistance. Once, I picked a material that looked great on paper but failed miserably when exposed to cleaning agents. Understanding how materials interact with chemicals is crucial to avoid costly mistakes.
Table: Chemical Interaction
Material | Resistance to |
---|---|
Polypropylene | Acids & Bases |
PVC | Alkalies |
Aesthetic vs. Functional Trade-offs
Balancing aesthetics with functionality is like walking a tightrope. I recall a client who was fixated on a glossy finish for their product, but we had to ensure it didn’t compromise performance. It’s all about finding that sweet spot where beauty meets functionality.
In essence, getting familiar with these material properties can make your designs not just look good, but perform brilliantly as well. Understanding these nuances can guide you in making informed decisions that enhance product longevity and efficiency. Dive deeper into material selection2 to refine your design process.
High tensile strength is crucial for load-bearing parts.True
Materials with high tensile strength support stress, enhancing durability.
Thermal expansion is irrelevant in B side design.False
Low thermal expansion ensures dimensional stability under temperature changes.
How Does Structural Integrity Impact B Side Features?
Ever wondered how the invisible parts of a product hold everything together? That’s where structural integrity comes in, especially with B side features.
Structural integrity ensures that B side features withstand stress, maintaining form and function, preventing defects, and enhancing the reliability of injection-molded products.
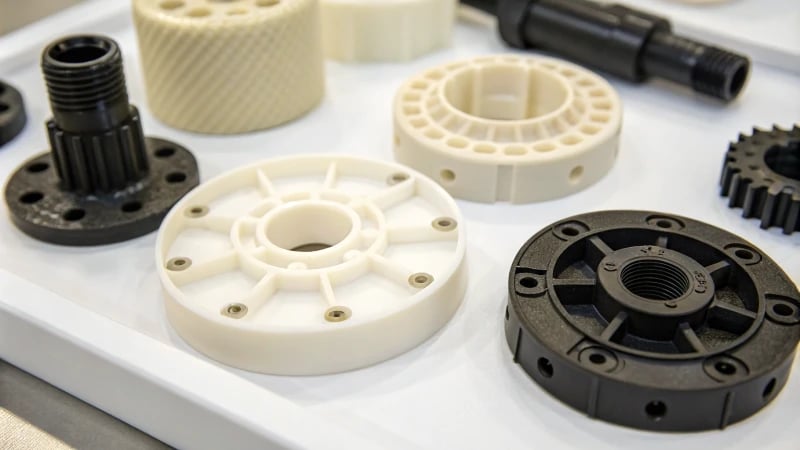
Understanding B Side Features
B side features have always intrigued me. They’re the unsung heroes in design, often hidden from view but absolutely essential for the mechanical function of products. These might include ribs, bosses, and snap-fits—elements that ensure everything stays in place and works smoothly. I remember one time when a tiny rib I’d designed almost went unnoticed, yet it was crucial for the product’s stability. Ensuring these features maintain their structural integrity3 is crucial, as they are the backbone of operational loads.
Importance of Structural Integrity
- Load-Bearing Capacity: I’ve learned over the years that proper structural integrity is what allows B side features to bear loads without crumbling under pressure. It’s like having a reliable friend who never lets you down, ensuring that everything stays intact.
- Material Efficiency: Balancing material use while maximizing strength is an art form in itself. It’s about being smart and resourceful—something that becomes second nature when optimizing design for cost-effective production.
- Durability: By keeping structural integrity in check, products can withstand the test of time. It’s like giving them a suit of armor against wear and tear, prolonging their lifespan.
Factors Affecting Structural Integrity
- Material Selection: Choosing the right material is like picking the perfect ingredient for a recipe—it affects the product’s strength and flexibility.
- Design Considerations: Integrating features like ribs can reinforce areas prone to stress. Whenever I’m using CAD tools, I feel like I’m crafting a masterpiece.
- Manufacturing Processes: Variations in injection molding parameters can affect outcomes. It’s about understanding these nuances to achieve consistent quality.
Factor | Impact on Structural Integrity |
---|---|
Material Choice | Affects strength and flexibility |
Design Elements | Reinforces specific areas |
Process Parameters | Influences consistency and quality |
Case Study: Optimizing Design
I once faced a situation where a product’s performance was compromised due to a weak rib design on the B side. It was frustrating, yet enlightening. By analyzing the failure4, I could make adjustments to its thickness and material, leading to a significant improvement in performance.
These experiences underscore why optimizations are vital for designers like Jacky, striving to balance functionality with production efficiency. Exploring advanced design techniques5 enables us to create robust components that truly stand the test of time.
B side features are visible parts of a product.False
B side features are non-visible elements essential for mechanical function.
Material choice impacts the strength of B side features.True
Different materials have varying tensile strengths, affecting integrity.
Why is manufacturability important for plastic B side features?
Ever wonder why those hidden plastic parts matter so much? It’s all about manufacturability!
Manufacturability is crucial for plastic B side features to ensure cost-effectiveness, functionality, and production efficiency, preventing redesigns and facilitating smooth mass production integration.
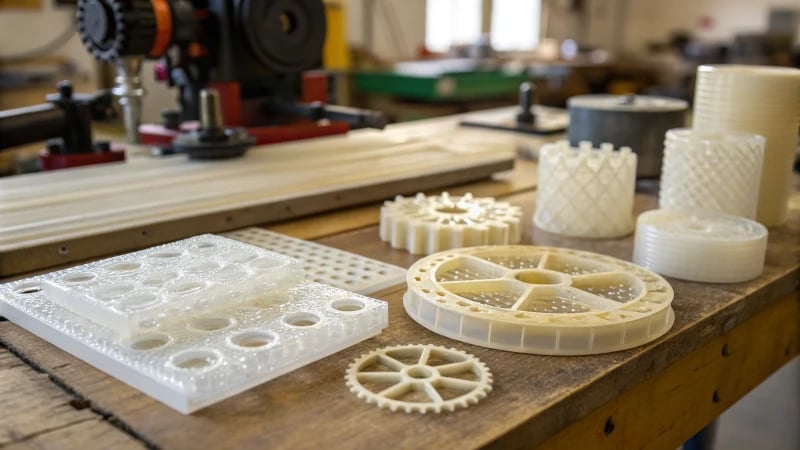
Understanding B Side Features in Plastics
I remember the first time I realized how crucial B side features were in my designs. These are the unsung heroes of plastic components—like screw bosses and ribs—that quietly ensure everything functions smoothly. They might be hidden, but their impact on production efficiency and overall product quality is huge. Ignoring manufacturability6 at this stage can lead to unexpected headaches down the line, as I learned the hard way.
Key Benefits of Manufacturability
Cost-Effectiveness
Early in my career, I designed a part that looked great on paper but turned out to be a nightmare to produce. The lesson? Manufacturability saves money. By integrating it during the design phase, we reduce waste and labor costs. For example, well-designed features can be molded efficiently, shaving precious minutes off production time.
Feature Type | Cost Impact |
---|---|
Screw Boss | Moderate |
Ribs | Low |
Internal Geometries | High |
Functionality
One of my favorite projects involved optimizing rib structures. They add strength without the bulk, maintaining a perfect balance between durability and usability. When B side features are thoughtfully designed, the product not only meets but often exceeds its intended function.
Production Efficiency
Thinking about manufacturability from the start has always paid off for me, especially in high-volume settings where every second counts. It streamlines the molding processes7, reduces cycle times, and boosts throughput.
Common Challenges in Manufacturability
Complex Geometries
I once worked on a design with such intricate details that molding it felt like trying to put together a jigsaw puzzle blindfolded. Simplifying these designs without losing functionality is truly an art form.
Material Selection
Choosing the right material can feel like solving a mystery. Different materials behave in unpredictable ways during molding. I’ve spent countless hours understanding material behavior8 to make informed choices that balance cost and durability.
Tooling Constraints
Precision tooling is vital for quality outputs, yet it can be expensive. Balancing these costs with feature complexity has taught me the importance of strategic planning. Collaborating with engineers early on has always led to better outcomes.
By delving into these factors, I’ve come to appreciate why manufacturability is a cornerstone of designing plastic B side features. Engaging with engineers and understanding manufacturing limitations can lead to stronger collaborations and successful products.
Manufacturability impacts plastic B side feature costs.True
Designing for manufacturability reduces material waste and labor costs.
Complex geometries simplify manufacturability in plastics.False
Complex geometries increase molding difficulty, complicating manufacturability.
How Does Cost Efficiency Influence Design Decisions?
Ever found yourself torn between an exciting design idea and the constraints of a tight budget?
Cost efficiency impacts design by guiding material selection, manufacturing methods, and product complexity to keep designs innovative and financially viable.
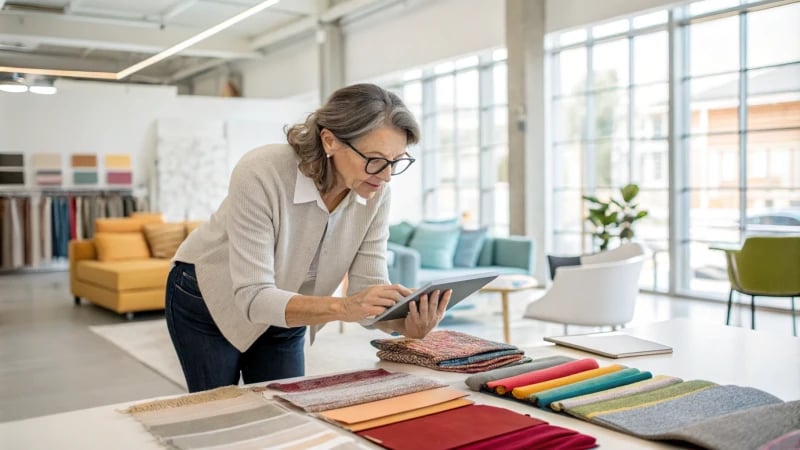
I remember my early days as a designer when I faced the challenge of creating something spectacular with limited resources. It was like being a kid in a candy store, but with only a dime to spend! Cost efficiency isn’t just about pinching pennies—it’s about making smart choices that balance innovation with reality.
The Role of Material Selection
Material selection is one of those decisions where cost efficiency really makes its mark. It’s like choosing the right ingredients for a recipe; the quality of your materials can make or break your design. Imagine you’re picking between ABS plastic, polycarbonate, and aluminum. Each has its own price tag and durability:
Material | Cost per Unit | Durability Rating |
---|---|---|
ABS Plastic | $1.50 | High |
Polycarbonate | $2.00 | Very High |
Aluminum | $3.50 | Medium |
In my experience, opting for materials that strike the right balance between cost and durability has been key. It’s like finding the perfect middle ground where quality meets affordability.
Streamlining Manufacturing Processes
In the hustle of manufacturing, efficiency is your best friend. Techniques like injection molding9 can be game-changers by slashing production time and cutting waste. I once worked on a project where automation not only reduced costs but also improved the precision of our products. It was a win-win!
Simplifying Product Complexity
Sometimes less is more. Simplifying a product can trim down production costs without sacrificing quality. Think of it as decluttering your closet—keeping only what adds value. Modular design approaches, for example, let you scale and customize without breaking the bank.
Embracing ‘Design to Cost’ Methodology
The ‘Design to Cost’ methodology is like having a financial GPS for your design process. By setting clear cost targets from the get-go, I found it easier to make informed design decisions that aligned with budgetary limits and market needs.
I’ve seen companies thrive by embedding this approach into their ethos, achieving not just cost savings but also sustainable success.
Understanding these aspects transforms cost efficiency from a limiting factor into a strategic advantage—one that doesn’t just cut costs but enhances the very fabric of our design choices. Whether you’re a seasoned designer or just starting out, integrating these insights can elevate your craft to new heights.
For those eager to explore further, dive into resources that unpack these methodologies and discover their real-world applications in today’s fast-paced market.
ABS plastic is more durable than aluminum.True
ABS plastic has a higher durability rating compared to aluminum.
Modular design increases production costs.False
Modular design allows for cost-efficient customization and scalability.
What are the common challenges in designing plastic B side features?
Navigating the nuances of plastic B side design isn’t just about crafting what’s unseen; it’s about mastering the hidden artistry that supports the entire structure.
Designing plastic B side features involves challenges such as ensuring proper draft angles, managing undercuts, and maintaining structural integrity, while balancing cost and manufacturability, requiring meticulous attention and innovative solutions.
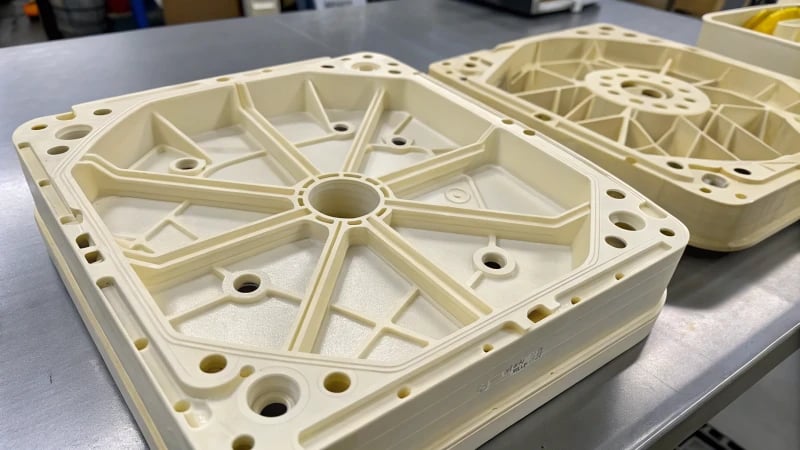
The Complexity of Draft Angles
You know, draft angles can be tricky. It’s a bit like trying to find that sweet spot between keeping your shoes snug and not too tight. I’ve spent countless hours tweaking designs, balancing just the right amount of draft. Not enough draft, and it’s like trying to get a stuck shoe off; too much, and you risk losing the sleek look.
Draft Angle | Effect on Ejection |
---|---|
< 1° | High risk of part sticking |
1° – 3° | Generally acceptable |
> 3° | Easier ejection but may affect aesthetics |
Undercuts and Their Implications
Ah, undercuts! They’re the pesky little details that can make or break a design. I remember my first project involving undercuts—what a learning curve! These elements are fantastic for complex shapes but can complicate the mold-making process significantly. It’s a constant juggle between creating those jaw-dropping designs and not driving the production costs through the roof.
Undercuts often require side-actions or lifters, increasing the cost and complexity of the mold. Engineers need to weigh the benefits against potential manufacturing hurdles10.
Structural Integrity vs. Cost
Now, keeping everything sturdy without blowing the budget is something of an art form. I often feel like a tightrope walker balancing on a thin line between cost and quality. Whether it’s choosing the right materials or adding ribbing for strength without overdoing it, every choice counts.
- Material Selection: It’s like choosing the right gear for a hike—crucial for durability and comfort.
- Ribbing: Adds strength without excess weight or cost.
Managing Warpage and Shrinkage
Nothing quite like designing intricate features on the B side only to have warpage mess it all up. It’s here that simulation software11 becomes a savior, helping me predict and tweak designs before they hit the real world. It’s a game-changer in avoiding those frustrating "back-to-the-drawing-board" moments.
Tooling Considerations
Tooling is like setting up your camping gear—every piece has its place for an efficient setup. From selecting tool materials to planning cooling channels and gate design, every detail needs collaboration with tooling engineers to get things just right.
- Cooling Channels: Streamline cycle time and minimize warpage.
- Gate Design: Critical for even filling and reducing defects.
Each challenge in designing plastic B side features is like a puzzle piece fitting into a larger picture—it’s all about careful consideration and balancing factors to achieve a successful design outcome. Understanding these aspects means we’re well on our way to crafting designs that are not just manufacturable but also perform brilliantly.
Insufficient draft angles cause ejection issues.True
Draft angles less than 1° can lead to parts sticking in the mold.
Undercuts reduce mold complexity and cost.False
Undercuts increase complexity, requiring side-actions, raising costs.
How can designers effectively balance aesthetic and functional requirements?
Navigating the intricate dance between aesthetics and functionality isn’t just a challenge—it’s an art form.
Designers can balance aesthetics and functionality by employing user-centered design, using prototyping tools, and maintaining ongoing communication with stakeholders to ensure visually captivating and seamlessly functioning designs.
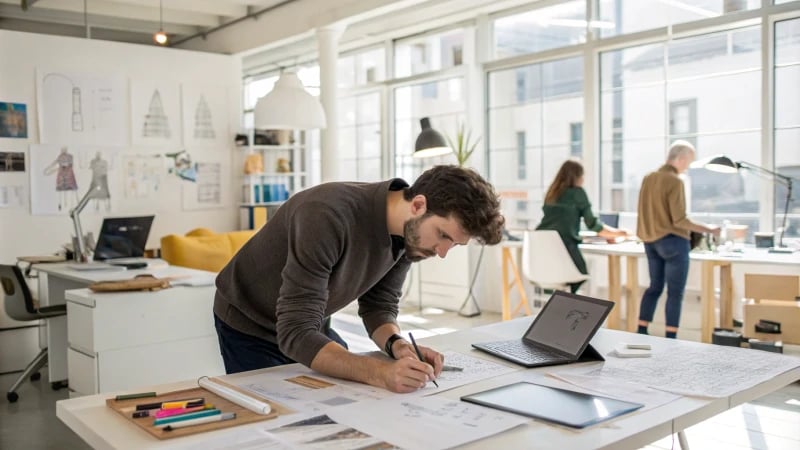
Understanding the Core Elements
I remember the first time I faced the aesthetic versus functionality dilemma. It was like standing at a crossroads, one path leading to visual allure and the other to practical efficiency. As designers, we must delve into what makes something look good and work well. Aesthetics are all about visual appeal—think of color, shape, and texture, like painting on a canvas. Functionality is the nuts and bolts of usability and efficiency. Before diving into a design, I ask myself: What does my audience truly need?
Implementing User-Centered Design
One of my most enlightening projects involved designing a product for a group whose preferences I initially underestimated. This experience taught me the value of putting users at the heart of every design decision. By understanding their needs and preferences, I could create something that wasn’t just eye-catching but also intuitive and practical. Tools like user personas12 and journey maps became my go-to resources, helping me visualize user interactions and refine my design choices.
Leveraging Prototyping Tools
When I first started using prototyping tools like Sketch and Figma, it felt like unlocking a new level of creativity. These tools allowed me to play with design elements without committing to them immediately. The instant feedback I received was invaluable, letting me tweak both the aesthetics and functionality before going into full production. The rapid iteration process helped ensure that every final product not only met expectations but often exceeded them.
Tool | Primary Use | Benefits |
---|---|---|
Sketch | UI/UX Design | Intuitive interface, vector support |
Figma | Collaborative Prototyping | Real-time collaboration |
Maintaining Communication with Stakeholders
In my early days, I learned the hard way that assuming stakeholders understood my vision without regular updates was a recipe for disaster. Keeping lines of communication open with stakeholders is not just beneficial; it’s essential. Through collaborative meetings and feedback loops, I could align our objectives, reducing misunderstandings and enhancing the overall design quality. Incorporating a feedback system13 early in the design phase helps identify potential issues before they become problems.
Examples of Successful Integration
Reflecting on companies that masterfully blend aesthetics with functionality provides endless inspiration. Take Apple, whose sleek designs are synonymous with high functionality, or Tesla, where modern aesthetics meet cutting-edge technology. Studying such examples helps me understand what works and why, offering insights into successful strategies. By examining these case studies, I’ve picked up best practices14 that I now apply to my own projects, ensuring they are both beautiful and functional.
User-centered design focuses on aesthetic requirements.False
User-centered design prioritizes user needs, balancing aesthetics and functionality.
Prototyping tools help test both aesthetics and functionality.True
Prototyping tools allow designers to experiment and receive feedback on designs.
Conclusion
Choosing plastic B side features involves considering material properties, structural integrity, manufacturability, and cost efficiency to optimize design for functionality and production.
-
Learn about tensile strength to understand how it affects the durability and performance of materials in design. ↩
-
Gain insights into effective material selection to optimize your design process. ↩
-
Understanding the role of structural integrity can enhance your product design process, ensuring better durability and performance. ↩
-
Explore real-world examples of structural integrity issues to learn from past design failures and improve future projects. ↩
-
Discover innovative design strategies that enhance structural integrity, helping you create more reliable and efficient products. ↩
-
Explore the comprehensive definition of manufacturability and how it influences design choices. ↩
-
Discover how different molding techniques affect production efficiency and design outcomes. ↩
-
Learn about material properties and their role in manufacturability during the design process. ↩
-
Discover why injection molding is a preferred method for cost-efficient mass production in various industries. ↩
-
Explore how undercuts complicate the molding process and what techniques can mitigate related challenges. ↩
-
Learn about top simulation tools that help anticipate and mitigate warpage issues in plastic components. ↩
-
Discover how user personas help tailor designs to meet specific audience needs effectively. ↩
-
Learn about the importance of incorporating feedback systems in the design process. ↩
-
Explore real-world examples of successful designs harmonizing aesthetics and functionality. ↩