Imagine this: you have a wonderful product idea, but selecting the correct polyethylene (PE) material seems like a puzzle.
When selecting a PE material, consider factors such as environmental conditions, mechanical requirements, and cost. HDPE, MDPE, LDPE, and LLDPE each offer distinct advantages depending on temperature resilience, chemical resistance, and processing capabilities.
Continue reading as we explain the details of choosing PE materials. Learn important information that helps you decide what suits your product best.
HDPE is ideal for high-temperature applications.True
HDPE tolerates temperatures above 80°C, rendering it suitable for warm conditions.
How Does Temperature Affect My Choice of PE Material?
Knowing how temperature affects your selection of polyethylene (PE) material is important for top performance.
Temperature conditions significantly influence the selection of PE material. High temperatures favor HDPE for its heat resistance, while low temperatures suit LDPE and LLDPE for their flexibility and cold resistance.

Understanding Temperature Sensitivity in PE Materials
When selecting a polyethylene (PE) material, temperature resilience is a paramount consideration. The four main types of PE — High Density Polyethylene (HDPE), Medium Density Polyethylene (MDPE), Low Density Polyethylene (LDPE), and Linear Low Density Polyethylene (LLDPE) — each respond differently to temperature variations.
-
High Temperature Applications:
In environments where temperatures reach or exceed 80°C, HDPE is preferred. Its robust structure endows it with a higher melting point, making it ideal for products such as hot water piping systems. For instance, HDPE applications1 include not only piping but also containers that need to withstand consistent heat.
-
Low Temperature Environments:
Conversely, for environments that experience freezing temperatures, LDPE and LLDPE are more suitable due to their superior flexibility and resistance to becoming brittle. These properties make them excellent choices for products like frozen food packaging, where maintaining integrity at low temperatures is critical.
Chemical Resistance and Temperature
Apart from handling temperature variations, the chemical exposure of the PE material can also impact its suitability. While most PE variants offer good chemical resistance, each type can behave differently under specific chemical conditions, especially when combined with varying temperatures.
Comparative Analysis
The table below outlines the temperature resilience of different PE types:
PE Type | High Temp. Suitability | Low Temp. Suitability |
---|---|---|
HDPE | Excellent | Moderate |
MDPE | Good | Moderate |
LDPE | Poor | Excellent |
LLDPE | Poor | Excellent |
Case Studies in Temperature Application
- HDPE in Heat: Used in hot water systems2 due to its ability to withstand high temperatures without losing form or function.
- LDPE in Cold: Ideal for products like plastic bags for frozen foods, LDPE maintains flexibility and resists cracking even in extremely cold conditions.
Understanding these temperature dynamics allows for informed decisions that ensure product longevity and performance across varying environmental conditions.
HDPE is suitable for high temperature applications.True
HDPE's strong design and high melting point suit it perfectly for heat.
LDPE is preferred for high temperature environments.False
LDPE suits low temperatures because it bends easily.
What Mechanical Properties Are Essential for My Product?
Grasping mechanical attributes helps in choosing the correct PE material.
Essential mechanical properties for product selection include strength, impact resistance, and flexibility. HDPE is ideal for high-strength needs, while LDPE and LLDPE are suitable for flexibility. LLDPE offers superior impact resistance. Assess these attributes to choose the optimal polyethylene type for your product’s performance requirements.

Understanding Strength Needs
Choosing a polyethylene (PE) material involves checking its strength. If products need to be very strong, look at HDPE3. It has high tensile strength, bending ability, and hardness because of its tight molecular shape. Good for big storage boxes or strong buckets.
If flexibility is more important than strength, LDPE and LLDPE4 work better. These can bend a lot without breaking, making them great for cling film and plastic bags.
Checking Impact Resistance
Impact resistance matters a lot for products facing hits or pressure. LLDPE offers better impact strength than HDPE and LDPE. Useful for packaging boxes often handled or hit.
Flexibility Needs
How well a product bends without breaking matters for fit and use. LDPE and LLDPE give great flexibility, fitting for stretchy needs like films or food bags.
Deep Look at Mechanical Features
Property | HDPE | LDPE | LLDPE |
---|---|---|---|
Strength | High | Low | Medium |
Impact Resistance | Medium | Low | High |
Flexibility | Low | High | High |
Matching Features to Product Needs
Using the right mechanical traits helps the product work well while staying good in quality. By studying each PE type’s strong points and limits, choosing a material fitting your needs becomes easier.
Learning more about how these materials act in different surroundings and ways of use will appear in later parts.
HDPE has higher impact resistance than LLDPE.False
LLDPE provides better impact strength than HDPE.
LDPE is more flexible than HDPE.True
LDPE offers high bendability, unlike HDPE, which is less bendable.
How Do Processing Methods Influence PE Material Selection?
Ways of processing greatly influence the selection of polyethylene (PE) material.
Processing methods such as injection molding, extrusion, and blow molding dictate the choice of PE material. For instance, LDPE and LLDPE excel in injection molding due to their fluidity, whereas HDPE is preferred for strength in blow-molded products. Understanding these methods ensures optimal material performance and cost-effectiveness.
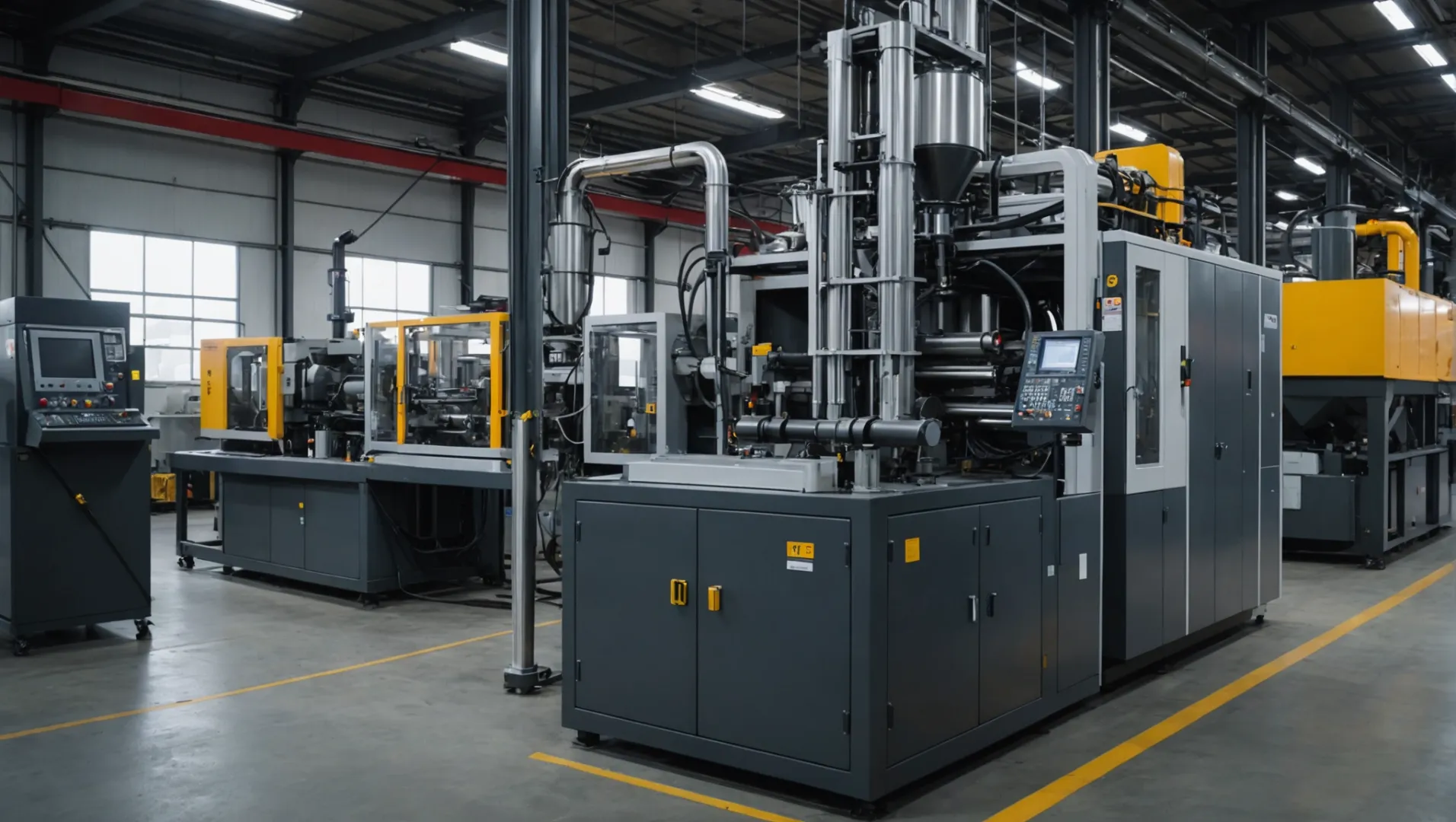
Injection Molding Considerations
Injection molding uses materials with good flow to accurately fill complex molds. LDPE and LLDPE5 are chosen for this because they flow well and are perfect for small items like toys or tiny plastic parts. For bigger items like garbage cans, HDPE‘s strength is helpful, even if it requires changes to the process due to its lower flow.
Extrusion Molding Uses
Extrusion molding helps create films, pipes, and shapes. The flexibility of LDPE and LLDPE suits film production, such as in farms and for wrapping. On the other hand, HDPE6 performs well in thicker uses like pipes because it is strong and stiff. This makes it a good pick for strong products.
Blow Molding Aspects
For blow molding, which makes hollow items like bottles and drums, HDPE and LLDPE are often used. HDPE‘s strength and stiffness are great for bottles holding chemicals or liquid fertilizers. Conversely, LLDPE‘s flexibility and toughness are better for items regularly moved or hit, like drink bottles.
Cost and Efficiency Balance
Thinking about these methods includes looking at costs. LDPE and LLDPE7 usually cost less to process because they handle easier in molds. HDPE might cost more due to needing higher heat and pressure.
Understanding how each PE type fits with different methods helps choose the right material for your needs and budget carefully.
LDPE is preferred for extrusion molding.False
LDPE suits injection molding and film extrusion, not thick extrusion.
HDPE requires higher temperatures in processing.True
HDPE’s strength requires hotter temperatures and greater pressures for molding.
What Are the Cost Implications of Different PE Materials?
Exploring the price landscape of polyethylene (PE) materials may feel difficult.
The cost implications of different PE materials, including HDPE, MDPE, LDPE, and LLDPE, hinge on factors like material price and processing expenses. HDPE typically incurs higher costs due to its superior strength and processing requirements, while LDPE and LLDPE offer cost savings with easier processing but lower strength.

Material Price Comparison
The cost of polyethylene materials changes a lot based on their features and uses. Usually, LDPE (Low Density Polyethylene) and LLDPE (Linear Low Density Polyethylene) are cheaper, which attracts projects with tight budgets. On the other hand, HDPE (High Density Polyethylene) costs more because it is very strong and lasts longer.
Material | Average Cost (per kg) | Key Characteristics |
---|---|---|
HDPE | High | High strength, durability |
LDPE | Low | Flexibility, low strength |
LLDPE | Low | Impact resistance, flexibility |
Deciding on these materials often means considering the cost against what your project needs.
Processing Costs
Also, processing expenses affect the total costs when using different PE materials. LDPE and LLDPE are chosen for their good flow qualities, making them good for complex shapes and using less energy during production. This leads to lower processing costs with methods like injection molding or extrusion. On the other hand, HDPE needs higher processing temperatures and pressures because it flows less easily, so energy use and operational costs increase.
Balancing Cost with Performance
Picking cheaper materials like LDPE or LLDPE might sound good, but product quality or performance should not suffer. If high strength and durability are necessary, investing in HDPE at the start can save money later by reducing failure rates and maintenance costs.
Imagine HDPE used in piping systems8 that must handle high temperatures and pressures — in this situation, its better mechanical properties make up for the higher initial costs.
In conclusion, understanding the cost effects of different PE materials needs careful thought about both material prices and processing costs. By balancing these with performance needs, it becomes possible to pick materials that are smart and cost-effective.
HDPE is more economical than LDPE.False
HDPE tends to be pricier because of its toughness and long-lasting nature.
LDPE has lower processing costs than HDPE.True
LDPE's superb flow qualities lower energy and operating expenses.
Conclusion
Check your product’s surroundings, mechanical requirements, looks, processing techniques and budget limits to select the best PE material. Reaching this balance achieves both performance and cost savings.
-
Explore diverse HDPE applications, emphasizing heat resistance benefits.: Given its temperature resilience, HDPE is an ideal material for many industrial applications, including: · Piping systems: Used extensively for hydraulic, gas, … ↩
-
Learn about HDPE’s suitability for hot water systems, enhancing durability.: Durability · HDPE pipe can be heat fused together to form a joint that is as strong or stronger than the pipe itself and is leak free. · The Life Cycle Cost of … ↩
-
Discover HDPE’s advantages in strength and durability.: Pros Of Using HDPE · Superior tensile strength · Impressive strength-to-density ratio · Overall high-impact resistance · High melting point … ↩
-
Learn about LDPE and LLDPE’s superior flexibility and use cases.: LLDPE is blended form of LDPE where the film has much more flexibility, tensile strength, and more conformability. It is more pliable and softer. LLDPE is used … ↩
-
Learn how LDPE and LLDPE improve mold filling accuracy.: Compared to LDPE material, it has a higher softening temperature and melting point, boasting advantages such as greater strength, good toughness, increased … ↩
-
Explore why HDPE is ideal for strong, thick profiles.: Overall, polyethylene is flexible, lightweight, and resistant to chemicals, corrosion, and impacts. Polyethylene is also FDA compliant, with food-grade PE … ↩
-
Understand the cost differences in processing these materials.: LLDPE C4 film was assessed at $1080-1100/ton while HDPE film stood at $1070-1090/ton at the time of writing. The last time LDPE went below LLDPE … ↩
-
Learn how HDPE’s properties make it ideal for high-pressure applications.: HDPE pipes are durable and resistant to physical damage, corrosion, common chemicals, and other environmental hazards. They are a cost-effective choice for long … ↩