Are you exploring the possibilities of Liquid Silicone Rubber (LSR) for your manufacturing project?
If you’re thinking about using Liquid Silicone Rubber (LSR) for your next project, you’re in for a treat! LSR injection molding is known for its incredible adaptability and efficiency. It boasts rapid curing times and impressive temperature resistance, making it the perfect fit for complex designs in various industries.
But that’s just scratching the surface. Let’s dive deeper into the unique properties of LSR and discover how it can elevate your manufacturing capabilities.
LSR injection molding is more efficient than compression molding.True
LSR's fast curing and automation enhance production efficiency over compression molding.
What Makes LSR Superior to Other Materials?
When it comes to manufacturing, Liquid Silicone Rubber (LSR) stands out for its exceptional properties, making it a top choice for various applications.
LSR excels over other materials due to its low viscosity, excellent chemical resistance, and superior temperature tolerance. These attributes make LSR ideal for producing high-precision components that require durability and flexibility in challenging environments.

Unmatched Material Adaptability
One of the key factors that make LSR superior is its low viscosity, which allows it to flow into thin, complex mold areas effortlessly. This property is crucial for products with intricate designs requiring high precision.
Moreover, LSR‘s good fluidity ensures uniform mold cavity filling, minimizing defects such as material shortages or surface pores. This characteristic enhances the quality consistency1 of manufactured products.
Superior Production Efficiency
Fast curing is another significant advantage of LSR over traditional rubber materials. The rapid curing time shortens the molding cycle, facilitating quicker turnaround times and higher production rates. This is particularly beneficial in mass production environments where high degree of automation can be utilized to control the entire process from mixing to demoulding automatically.
Exceptional Product Performance
LSR products are renowned for their excellent physical properties. They exhibit high elongation, tear strength, and tensile strength, which are maintained across a wide range of temperatures—from -50℃ to 250℃. This makes LSR an excellent choice for applications that demand high durability and reliability.
Additionally, LSR‘s chemical resistance allows it to withstand exposure to acids, alkalis, and salts, making it ideal for use in harsh chemical environments. This is why it’s commonly used in industries like medical2 and chemical manufacturing.
Flexible Design Freedom
LSR offers remarkable design flexibility. It supports complex shape molding, enabling the integration of multiple functional components into a single part. This not only reduces assembly processes but also enhances product reliability and integration.
Furthermore, LSR can be customized in terms of color and transparency, catering to personalized product designs and innovations. This versatility opens up numerous possibilities for product designers seeking to push creative boundaries.
LSR Attributes | Benefits |
---|---|
Low Viscosity | Allows complex design molding |
Fast Curing | Increases production efficiency |
Excellent Temperature | Operates across a wide temperature range |
Chemical Resistance | Suitable for harsh environments |
By leveraging these properties, manufacturers can produce components that not only meet but exceed industry standards, ensuring their products stand out in competitive markets.
LSR has low viscosity for complex mold designs.True
LSR's low viscosity allows it to fill thin, intricate molds.
LSR cannot withstand harsh chemical environments.False
LSR is known for its excellent chemical resistance capabilities.
How Does LSR Injection Molding Enhance Production Efficiency?
Discover how Liquid Silicone Rubber (LSR) injection molding optimizes production by offering speed, automation, and precision.
LSR injection molding enhances production efficiency through fast curing cycles, high automation levels, and precision molding, reducing material waste and improving product consistency.

Fast Curing Cycles
One of the standout features of Liquid Silicone Rubber (LSR) injection molding is its rapid curing time. This characteristic significantly shortens the molding cycle compared to traditional rubber molding methods like compression molding. The quick curing process is particularly advantageous for mass production, enabling manufacturers to scale up operations without sacrificing quality.
High Automation Levels
LSR injection molding is highly compatible with automation. From material mixing and injection to product demoulding, the entire process can be automated. This minimizes manual labor and reduces the likelihood of human error, resulting in a smoother production flow and consistent product quality. Automation also facilitates continuous operations, which further boosts efficiency.
Precision Molding
The precision offered by LSR injection molding is unparalleled. The material’s low viscosity allows it to flow into intricate mold designs, ensuring detailed and high-accuracy production. This precision is beneficial for industries that require exacting standards, such as medical devices and electronics.
Reduced Material Waste
LSR injection molding uses a cold runner system that accurately controls material injection volumes. This precision leads to minimal material waste, making it an eco-friendly option. Given that LSR is a high-value material, reducing waste is not only environmentally beneficial but also cost-effective for manufacturers.
High Production Consistency
With good fluidity and adaptability, LSR fills molds evenly, maintaining dimensional accuracy across products. This consistency reduces defects and improves the overall reliability of the manufacturing process.
By integrating these features, LSR injection molding stands out as a transformative process in manufacturing. Its ability to enhance efficiency while maintaining high-quality standards makes it an attractive choice for industries seeking to optimize their production capabilities. For more insights on how LSR compares to other materials3, explore our related articles.
LSR injection molding reduces production cycle time.True
LSR's rapid curing significantly shortens the molding cycle.
Manual labor is essential in LSR injection molding.False
LSR processes are highly automated, minimizing manual labor.
In What Industries Can LSR Injection Molding Be Most Beneficial?
Are you curious about which industries benefit the most from LSR injection molding? Its unique properties offer unparalleled advantages across diverse sectors.
LSR injection molding is most beneficial in industries such as medical, automotive, electronics, and consumer goods due to its excellent material properties, design flexibility, and high precision capabilities.
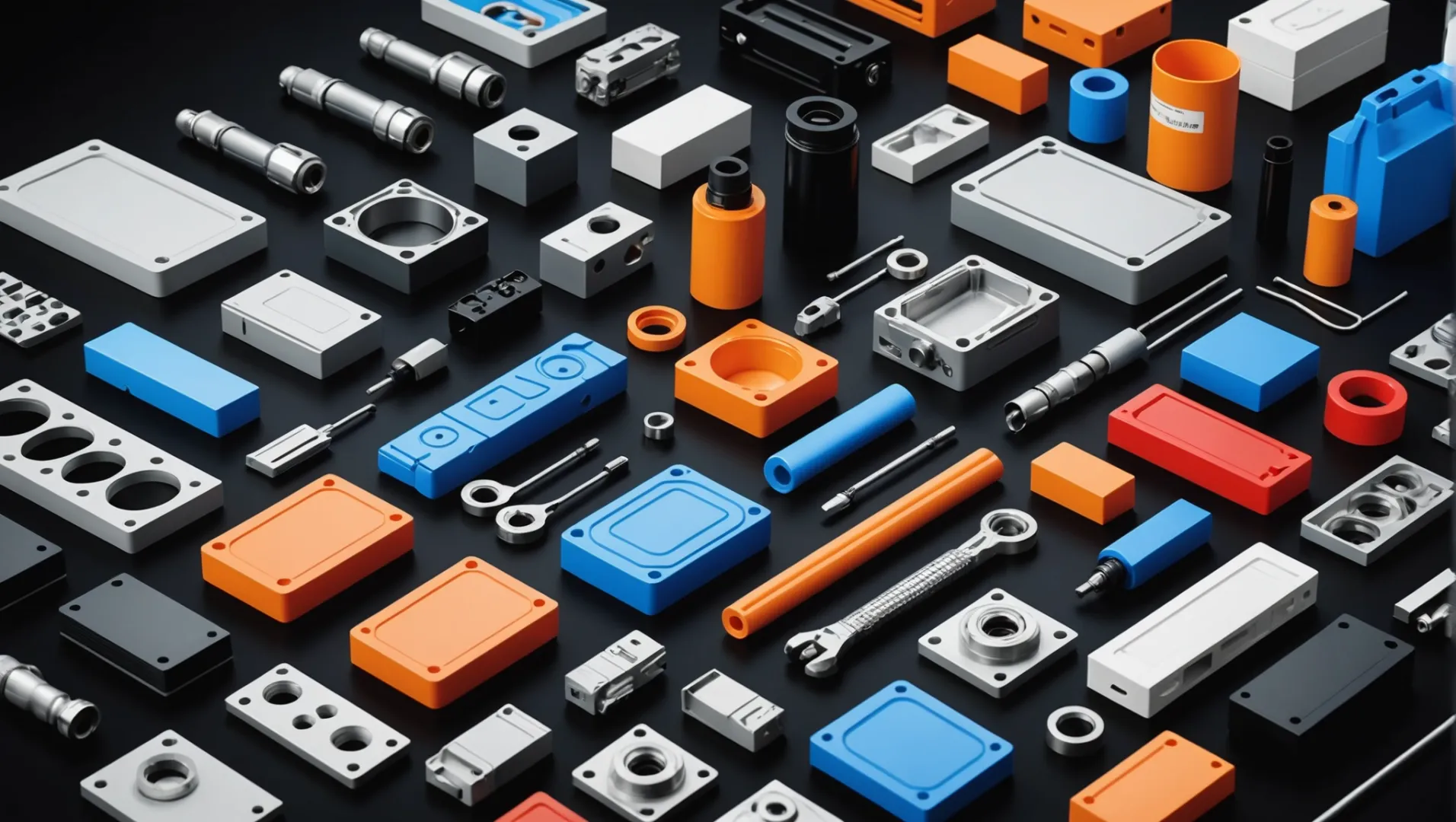
Medical Industry
The medical sector4 is a leading beneficiary of LSR injection molding due to its stringent requirements for precision, safety, and durability. LSR‘s biocompatibility ensures it can safely interact with human tissues, making it ideal for manufacturing medical devices, implants, and prosthetics. Additionally, its chemical resistance is crucial for products exposed to various medical environments.
Automotive Industry
In the automotive industry, LSR injection molding supports the production of components that require high temperature resistance and durability. Parts like gaskets, seals, and electrical connectors benefit from LSR‘s stability over a broad temperature range (-50°C to 250°C). Furthermore, its ability to produce complex shapes with high precision aids in developing integrated parts that reduce weight and enhance vehicle performance.
Electronics Industry
For electronics, LSR provides excellent electrical insulation properties. This makes it an invaluable material for producing connectors, keypads, and other components that require reliable insulation. Moreover, LSR‘s low viscosity allows for the manufacturing of intricate parts with minimal defects.
Consumer Goods
In consumer goods, LSR‘s customizable color and transparency cater to aesthetic requirements while maintaining superior performance. Products ranging from kitchenware to wearable technology can be enhanced by LSR‘s durability and design flexibility. Its resistance to environmental factors ensures longevity and safety in everyday use.
Chemical Industry
The chemical industry also benefits from LSR‘s exceptional chemical resistance. Components used in harsh environments can be crafted to withstand exposure to acids, alkalis, and other corrosive substances, ensuring product integrity and reliability.
Industry | Key Benefits of LSR |
---|---|
Medical | Biocompatibility, chemical resistance |
Automotive | Temperature resistance, durability |
Electronics | Electrical insulation, precision |
Consumer Goods | Customization, environmental resistance |
Chemical | Chemical resistance |
LSR is ideal for high-precision medical devices.True
LSR's biocompatibility and precision suit medical device production.
LSR is not used in consumer goods due to low durability.False
LSR's durability and design flexibility benefit consumer goods.
What Are the Environmental Benefits of Using LSR?
Exploring sustainable manufacturing? Liquid Silicone Rubber (LSR) offers eco-friendly advantages that can revolutionize production processes.
Using Liquid Silicone Rubber (LSR) in manufacturing promotes sustainability through reduced waste, energy efficiency, and minimal environmental impact during production. Its durability extends product life, reducing the frequency of replacements and associated waste.

Reduced Material Waste
One of the primary environmental benefits of LSR is its ability to minimize waste. LSR injection molding utilizes a cold runner system5 which precisely controls material use, reducing excess and waste. This aspect is critical given the high value of LSR as a material.
Energy Efficiency
The fast curing properties of LSR mean that molds spend less time in heating cycles, thereby conserving energy. Compared to traditional rubber molding techniques, this efficient process results in lower energy consumption, making it a greener alternative6.
Long-Lasting Products
LSR‘s outstanding durability and resistance to extreme temperatures and chemicals extend the lifespan of products, diminishing the frequency of replacements. This results in fewer resources being spent on production over time, ultimately contributing to a more sustainable lifecycle.
Minimal Environmental Impact
The production of LSR products involves fewer harmful emissions compared to other polymers or plastics. Its inert nature means it doesn’t leach harmful substances into the environment during use or disposal. This characteristic is particularly beneficial in applications involving human contact7.
Biocompatibility and Safety
In sectors like healthcare, where biocompatibility is crucial, LSR‘s compatibility with human tissues reduces environmental hazards associated with alternative materials. This makes it a safer option for medical applications and contributes to sustainability in healthcare8 by reducing potential waste from less durable materials.
These factors underscore why companies aiming for greener manufacturing processes increasingly consider LSR. Its low environmental footprint combined with superior product performance positions it as a sustainable choice across various industries.
LSR molding reduces material waste significantly.True
LSR's cold runner system precisely controls material use, minimizing waste.
LSR products have a shorter lifespan than traditional rubber.False
LSR's durability extends product life, reducing replacement frequency.
Conclusion
Incorporating LSR injection molding into your manufacturing process not only enhances efficiency but also opens doors to innovative designs. Embrace the versatility of LSR and witness your production capabilities soar.
-
Explore how LSR ensures consistent quality in manufacturing.: LSRs have a lower viscosity, meaning they flow more readily and are easy to process via injection molding. ↩
-
Discover why LSR is favored in the medical industry.: Sterilization: LSR can be sterilized using a variety of methods. · Chemical and physical resistance: LSR is also highly resistant to chemicals … ↩
-
Discover detailed comparisons between LSR and other manufacturing materials.: LSR and other engineering elastomers typically cost more per pound than standard elastomers. Additionally, LSR has a specific gravity that is 20% higher than … ↩
-
Explore LSR’s biocompatibility and precision advantages in medical applications.: The following characteristics of LSR injection molded parts offer significant advantages for use in medical devices: Sterilization: LSR can … ↩
-
Discover how the cold runner system minimizes waste in LSR molding.: Cold runner system of Liquid Injection Mold keeps the liquid silicone cold until the Liquid Silicone Rubber inject into the hot cavities of the mold. ↩
-
Learn how fast curing enhances energy efficiency in manufacturing.: A LSR injection mold with high energy efficiency of vulcanization can provide potential applications in the LSR injection molding industry … ↩
-
Explore why LSR’s inert properties are environmentally friendly.: Inert: Since LSR parts are inert, they are not chemically reactive and won’t degrade or alter their structure in response to natural gas and … ↩
-
Understand how biocompatibility supports sustainability in medical applications.: Biocompatibility is “the ability of a material to be in contact with a living system without producing an adverse effect” [4]. Biostability is “ … ↩