Selecting the perfect injection mold steel can feel daunting, but it’s essential for success in manufacturing.
Choosing the right injection mold steel involves considering properties such as wear resistance, hardness, and corrosion resistance tailored to your project needs. An evaluation of production batch size, costs, and supplier reputation will lead to an informed decision.
Let’s dive deeper into each factor that influences your choice—understanding these intricacies can significantly impact the success of your injection molding projects.
Wear resistance affects mold longevity.True
High wear resistance in steel extends mold life by reducing degradation.
What Are the Key Properties to Consider in Mold Steel?
Selecting the right mold steel is vital for ensuring efficiency and longevity in manufacturing.
Key properties to consider in mold steel include wear resistance, hardness, and corrosion resistance. These factors determine the mold’s performance and durability, directly impacting production quality. Evaluating these properties ensures the selection of steel that meets specific project requirements, ultimately enhancing the overall manufacturing process.

Wear Resistance
Wear resistance is critical when the injection molded product involves abrasive materials like glass fiber reinforced plastic. For such high-wear conditions, opting for a steel like Sweden’s ASSAB S136, with a hardness of HRC48-52 after quenching and tempering, can significantly extend mold life due to its excellent wear resistance.
For less demanding applications, where wear is not a significant concern, more economical options like P20 steel provide sufficient durability without unnecessary cost.
Hardness
The hardness of mold steel affects both its deformation resistance and wear resistance. Typically, injection molds should have a hardness above HRC30. For molds requiring higher precision or longevity, steels like H13, which can reach HRC42-50 after proper treatment, are ideal. However, higher hardness can reduce toughness, necessitating a balance.
For large-scale production where toughness is paramount, selecting a steel that maintains this balance is crucial to avoid frequent replacements or failures.
Corrosion Resistance
For injection molding materials containing corrosive substances such as halogens or acids, corrosion-resistant steels like S136 are imperative. These steels prevent damage from corrosion, ensuring long-term mold integrity.
When corrosion risks are lower, cost-effective alternatives such as 420 stainless steel provide adequate protection at reduced costs, making them suitable for less aggressive environments.
Balancing Properties for Optimal Performance
Property | High Requirement Example | Low Requirement Example |
---|---|---|
Wear Resistance | S136 | P20 |
Hardness | H13 | P20 |
Corrosion Resistance | S136 | 420 stainless |
By carefully evaluating these properties—wear resistance1, hardness, and corrosion resistance—manufacturers can make informed decisions that align with their project needs and budget constraints. This approach not only improves production efficiency but also enhances the quality and reliability of the final products.
Mold steel hardness should exceed HRC30.True
Mold steel must have a hardness above HRC30 for deformation resistance.
P20 steel is ideal for high-wear conditions.False
P20 steel is not ideal for high-wear; S136 is better for such conditions.
How Do Production Batch Size and Cost Influence Steel Choice?
The choice of steel for injection molds hinges significantly on production batch size and cost considerations, influencing both performance and budget.
Production batch size determines the necessary durability and cost-effectiveness of mold steel. Smaller batches can use economical steels, while larger batches need high-performance options. Balancing cost with production needs ensures efficient and effective manufacturing.

Understanding Production Batch Sizes
Production batch size plays a crucial role in determining the type of steel used for injection molds. For small batch production2, choosing mold steel like P20 is often viable due to its low cost and good processing capabilities. These steels are sufficient for limited runs where extensive wear resistance isn’t paramount.
In contrast, large batch production demands mold steels with high wear resistance and durability, such as NAK80. This ensures that the molds withstand extended use without significant degradation, which could otherwise lead to increased maintenance costs and downtime.
Batch Size | Recommended Steel | Key Characteristics |
---|---|---|
Small Batch | P20 | Economical, versatile |
Large Batch | NAK80 | Durable, high wear resistance |
Evaluating Cost Factors
Cost is another critical factor when selecting injection mold steel. The price of mold steel can vary greatly based on its properties like hardness and corrosion resistance. High-performance steels tend to be more expensive but may offer savings in the long run through reduced maintenance and longer mold life.
Moreover, processing and maintenance costs should also be considered. Some high-grade steels, despite their initial cost, can decrease total expenses by reducing machining time and minimizing tool wear. However, steels requiring special treatments can add to overall costs.
Cost Consideration | Implications |
---|---|
Initial Material Cost | High-performance steels are more expensive |
Processing Cost | Some steels reduce machining time |
Maintenance Cost | Durable steels lower repair and replacement needs |
Balancing Performance with Budget
Finding a balance between performance requirements and budget constraints is essential. For projects with limited budgets but requiring high durability, investing in higher-grade steels might save costs in the long run due to reduced frequency of mold replacements.
Ultimately, the decision should align with the specific needs of the project, anticipated production volume, and available budget. Consulting with experts or engineers can provide valuable insights into making the most cost-effective yet efficient choice for mold steel.
P20 steel is ideal for small batch production.True
P20 steel is economical and versatile, making it suitable for limited runs.
NAK80 steel is unsuitable for large batch production.False
NAK80 steel's durability and wear resistance make it ideal for large batches.
What Processing and Heat Treatment Requirements Should You Know?
Understanding the processing and heat treatment requirements of mold steel is crucial for ensuring optimal performance and longevity of injection molds.
The processing and heat treatment of mold steel involve selecting materials with good machinability, appropriate hardness, and compatibility with specific heat treatment processes to achieve desired performance attributes.
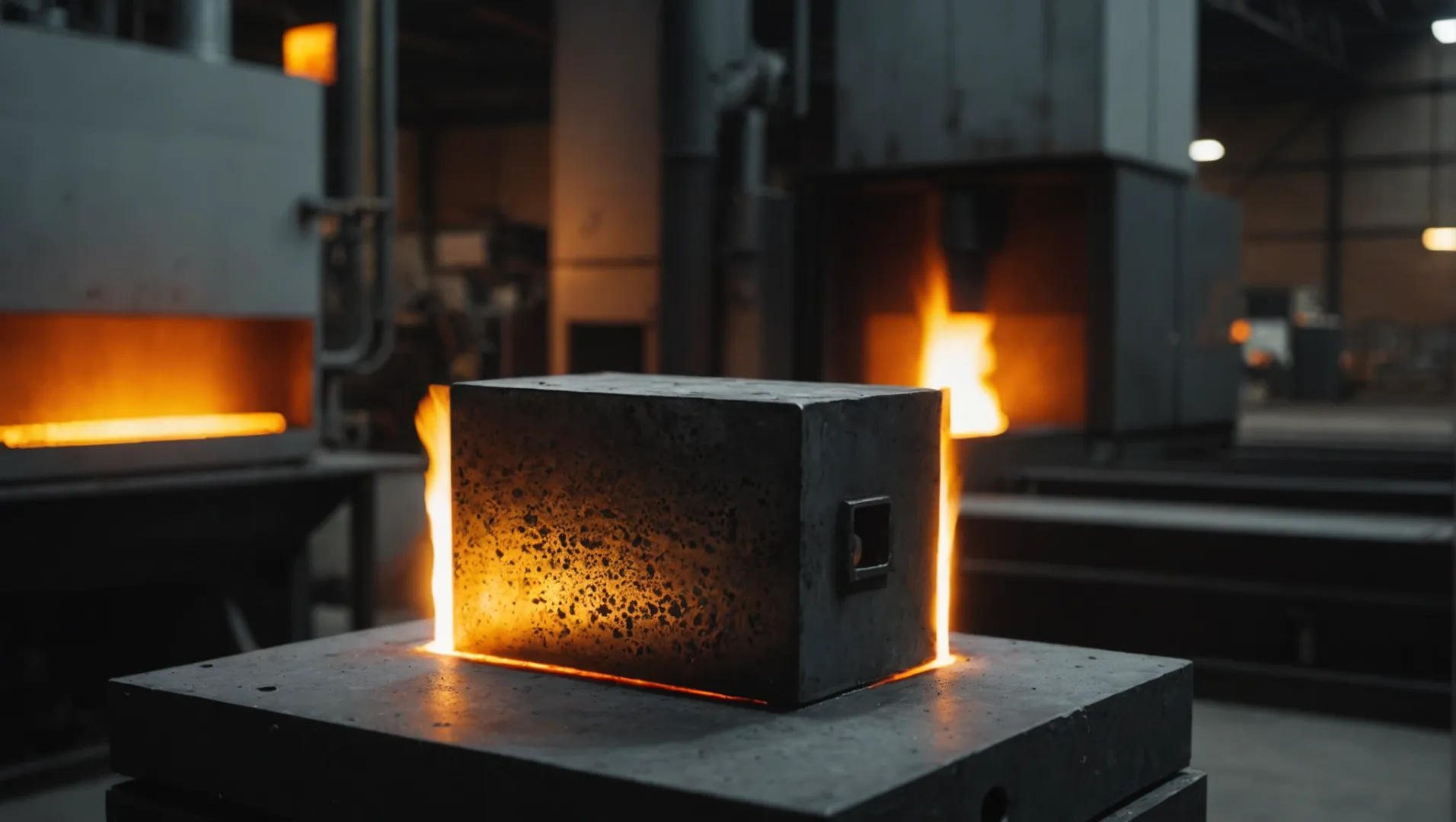
Understanding Processing Performance
Choosing a mold steel with good processing performance is vital to reduce manufacturing costs and time. This involves selecting materials that are easy to cut, polish, and machine. For instance, 718H steel is renowned for its excellent cutting and polishing properties, making it ideal for manufacturing complex-shaped injection molds.
Some high-hardness steels may require advanced processing techniques such as Electric Discharge Machining (EDM)3 or wire cutting to achieve precise shapes and dimensions.
Steel Type | Key Processing Features |
---|---|
718H | Excellent cutting and polishing |
H13 | Requires EDM for complex shapes |
Importance of Heat Treatment
The heat treatment of mold steel is essential to achieve the desired hardness and toughness. Different types of mold steel have specific heat treatment requirements. For example, H13 steel needs quenching and tempering to enhance its mechanical properties.
The heat treatment process must be strictly controlled, considering factors like temperature, time, and cooling methods, which significantly impact the final performance of the steel. Ignoring these parameters can lead to inadequate hardness or brittleness, affecting the mold’s efficiency.
Steel Type | Heat Treatment Process | Desired Outcome |
---|---|---|
S136 | Quenching and tempering | High wear resistance |
H13 | Quenching with controlled cooling | Enhanced hardness and toughness |
Balancing Hardness and Toughness
While high hardness improves wear resistance, it often reduces toughness, leading to brittleness. Thus, a balance between hardness and toughness is necessary. For instance, H13 steel, when properly treated, reaches a hardness of HRC42-50, suitable for high-demand plastic products but still maintains sufficient toughness.
Steel selection should consider the specific demands of the injection molded product. For highly abrasive materials, such as glass fiber-reinforced plastics, using a steel like ASSAB’s S136 provides necessary wear resistance while balancing other properties through proper heat treatment.
Conclusion
Understanding the processing performance and heat treatment requirements of mold steels is not just about selecting materials; it’s about optimizing them for specific applications. This involves a comprehensive approach that considers all aspects of processing and heat treatment to ensure that the mold performs effectively over its lifespan. By adhering to these requirements, manufacturers can significantly improve the durability and quality of their molds.
718H steel is ideal for complex mold shapes.True
718H's excellent cutting and polishing properties suit complex molds.
H13 steel does not require heat treatment.False
H13 requires quenching and tempering for enhanced properties.
Why Is Supplier Reputation Crucial in Steel Selection?
Supplier reputation plays a pivotal role in selecting steel for injection molds, ensuring quality and performance.
A reputable supplier guarantees high-quality steel, reliable performance, and excellent after-sales service, reducing risks in your production process.

Ensuring Material Quality
When choosing steel for injection molds, the material’s quality is paramount. Reputable suppliers often have stringent quality control measures that ensure consistent material properties. This reliability helps prevent production issues such as unexpected wear or corrosion. For instance, well-known suppliers of S136 or H13 steel offer products that meet industry standards, ensuring their suitability for specific applications.
Evaluating Supplier Credentials
A supplier’s reputation can be gauged through their credentials, such as certifications and industry accolades. These certifications are indicators of compliance with international standards. Checking customer reviews and testimonials also provides insights into their reliability and service quality. Engaging with reputable suppliers like those offering Sweden’s ASSAB steel4 can often lead to long-term partnerships that benefit your production needs.
The Role of After-Sales Support
After-sales service is an essential aspect of a supplier’s reputation. Quality suppliers provide comprehensive after-sales support, including technical consultations and troubleshooting assistance. This service is crucial when dealing with complex materials requiring specific processing techniques. For example, if your mold steel requires precise heat treatment, a supplier offering detailed heat treatment guidance5 can be invaluable.
Risk Mitigation through Supplier Reliability
Working with a reputable supplier minimizes risks associated with material inconsistencies or failures. Reliable suppliers ensure that their products undergo rigorous testing before reaching the customer, thus reducing the likelihood of defective material affecting your operations. This reliability is especially critical when dealing with high-stakes projects where failure could lead to significant financial losses.
Building Trust through Consistency
Consistency in product quality fosters trust between the supplier and the buyer. Suppliers who consistently deliver high-quality materials create a foundation for a trusting relationship, which is essential for long-term collaborations. Over time, this trust can lead to preferential treatment in supply chains, such as priority shipping or exclusive access to new materials.
In summary, the reputation of a supplier plays an instrumental role in ensuring that the steel used in injection molds meets your project’s demands for quality, reliability, and support.
Reputable suppliers ensure consistent steel quality.True
Reputable suppliers have stringent quality control measures ensuring consistent material properties.
All suppliers provide comprehensive after-sales support.False
Not all suppliers offer comprehensive after-sales support; it varies by supplier.
Conclusion
Choosing the right mold steel requires thoughtful consideration of various factors. Consult with experts to refine your selection for optimal performance.
-
Learn how wear resistance impacts mold longevity and efficiency.: A strong enhancement of the wear resistance can only be achieved by existing of a second harder phase. Of great influence therefore are the carbide content, … ↩
-
Explore why P20 steel is ideal for small batch production.: The main advantage of this type of steel is its convenience, as it saves on production time and costs by reducing the risk of dimensional distortion during heat … ↩
-
Learn about EDM’s role in enhancing machining precision.: Electrical discharge machining (EDM), also known as spark machining, spark eroding, die sinking, wire burning or wire erosion, is a metal fabrication process … ↩
-
Learn about the high standards and consistent quality of ASSAB steel.: Established in 1945, ASSAB has been active in marketing high quality tool steel from Sweden. Anchoring the distribution network for Uddeholm in Asia, ASSAB … ↩
-
Explore detailed instructions on effective heat treatment processes.: For tempering time, a rule of thumb is one hour per inch of thickness with a two hour minimum. Longer tempering times are not detrimental and it is essential … ↩