Injection molding in high temperature environments can feel like a high-stakes game. The stakes? Your product’s integrity.
The primary challenges of injection molding in high temperatures include altered material properties, mold complications, increased equipment demands, and reduced production efficiency. Solutions involve selecting heat-resistant materials, optimizing mold design, adjusting equipment systems, and refining process parameters.
While understanding these basic challenges is crucial, delving deeper into specific strategies and innovations can significantly enhance your production processes. Let’s explore detailed insights that could transform your approach to high temperature injection molding.
High temperatures cause plastic fluidity changes in injection molding.True
High temperatures reduce plastic viscosity, complicating control over filling speed and volume.
How Do High Temperatures Affect Material Properties in Injection Molding?
The properties of materials during injection molding can drastically change when subjected to high temperatures.
High temperatures in injection molding can alter plastic fluidity and induce thermal degradation, affecting product quality and strength. These challenges necessitate selecting appropriate materials and optimizing processes for effective production.
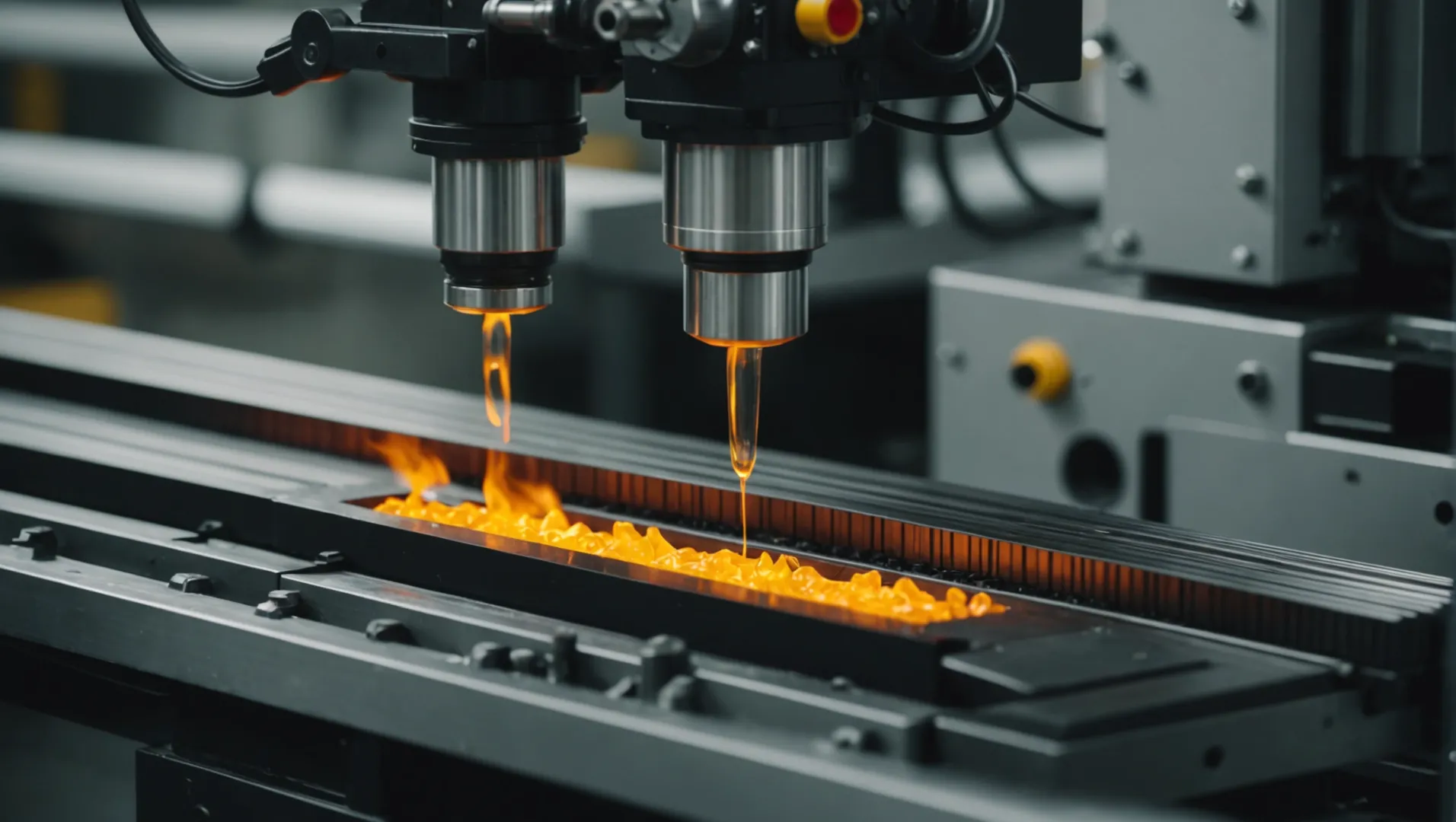
Understanding Material Changes in High Temperatures
In the realm of injection molding, materials often respond dynamically to temperature variations. As temperatures soar, the fluidity of plastic raw materials changes significantly. This alteration affects the filling speed and volume, making the process prone to defects like flash and burrs. Moreover, excessive heat can lead to thermal degradation, compromising the strength and toughness of the molded products.
Fluidity and Control Challenges
When exposed to high temperatures, the viscosity of plastics decreases, which may lead to an overly fluid state. This state complicates the control over filling speed and volume1, as well as increasing the risk of molding defects. Engineers must adapt their strategies by adjusting parameters such as injection speed and pressure to maintain precision.
Thermal Degradation Effects
Thermal degradation is a critical concern at elevated temperatures. It involves the breakdown of polymer chains, leading to diminished mechanical properties. The consequences of this breakdown include reduced tensile strength, impact resistance, and durability. Selection of high-temperature resistant polymers can mitigate these adverse effects.
Selecting Materials for Heat Resistance
To counteract these challenges, choosing materials that can withstand higher temperatures is essential. High-performance engineering plastics are designed to retain stability under extreme conditions. Polymers such as PEEK (polyether ether ketone) and PPS (polyphenylene sulfide) are often preferred due to their excellent thermal stability and mechanical properties.
Example Table: Common High-Temperature Plastics
Material | Maximum Operating Temperature | Key Properties |
---|---|---|
PEEK | 250°C | High strength, chemical resistance |
PPS | 200°C | Dimensional stability, flame retardant |
PTFE | 260°C | Low friction, non-reactive |
Process Optimizations for Better Quality
Adjusting process parameters is crucial for maintaining quality in high-temperature environments. By refining cooling cycles and ensuring adequate ventilation, manufacturers can prevent defects such as warping and voids. Additionally, employing robust cooling systems within molds helps regulate temperature effectively.
Importance of Cooling Systems
Effective cooling systems are vital for dissipating heat rapidly from molds. They help in maintaining dimensional accuracy and surface quality by preventing overheating. Consider implementing advanced cooling technologies such as conformal cooling channels to enhance efficiency.
By addressing these considerations, manufacturers can better navigate the complexities of injection molding in high-temperature settings, ensuring product integrity and operational efficiency.
High temperatures increase plastic fluidity in molding.True
Increased heat decreases viscosity, making plastics more fluid.
PEEK can withstand temperatures up to 300°C.False
PEEK's maximum operating temperature is 250°C.
What Role Does Mold Design Play in High Temperature Environments?
Mold design is pivotal when dealing with high temperature environments in injection molding.
In high temperature environments, mold design impacts cooling efficiency, material compatibility, and product quality. Effective cooling systems, durable mold materials, and regular maintenance are crucial to minimize temperature-induced issues and ensure product precision.
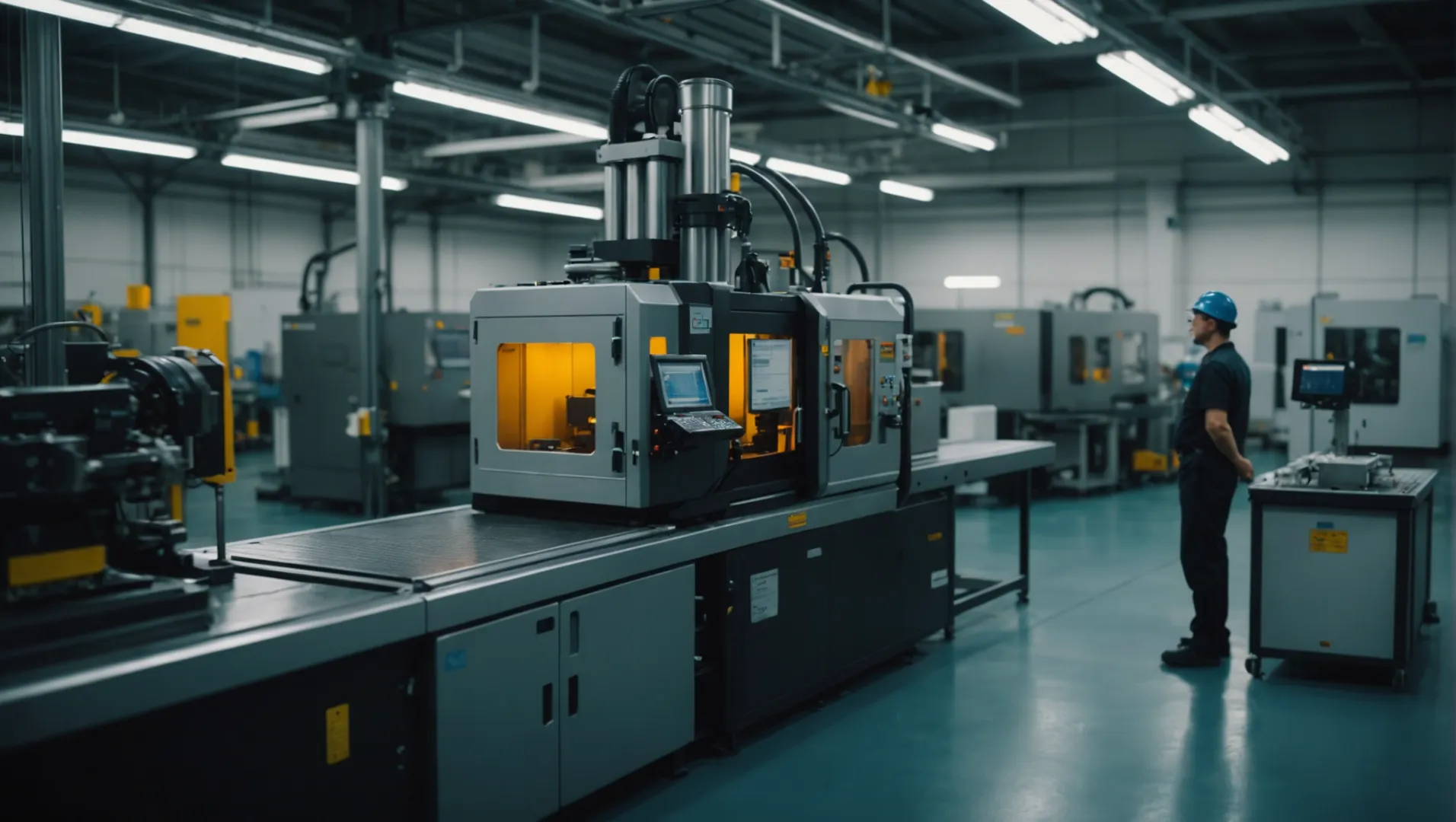
The Impact of High Temperatures on Mold Functionality
In high temperature environments, the performance of the mold is significantly affected. Cooling efficiency is a primary concern. Molds in such conditions heat up rapidly, necessitating advanced cooling systems to maintain optimal temperatures. Without effective cooling, product dimensions and surface quality can suffer.
Material selection for molds is equally critical. Using materials resistant to high temperatures and corrosion can extend the mold’s lifespan. Regular maintenance is essential to address wear and tear promptly, reducing downtime and improving production consistency.
Designing Cooling Systems for Efficiency
A sophisticated cooling system is indispensable for maintaining mold performance in high temperatures. Increasing the number of cooling channels and optimizing their diameter can enhance heat dissipation. This not only preserves product quality but also boosts production efficiency by reducing cooling time.
Moreover, leveraging advanced technologies such as conformal cooling can result in more uniform temperature distribution across the mold, further preventing defects like warping or uneven shrinkage.
Maintenance Strategies for Long-Lasting Mold Use
Proactive maintenance strategies are vital. Regular inspections can identify potential issues such as erosion or cracking early on. Incorporating high-quality components in the mold design minimizes unexpected failures.
Additionally, implementing a predictive maintenance schedule using sensors to monitor real-time performance data can preemptively address issues, thereby avoiding costly downtime and ensuring consistent product quality.
By focusing on these aspects of mold design, manufacturers can mitigate many of the challenges posed by high temperature environments, leading to more reliable and efficient injection molding processes.
Conformal cooling reduces mold defects.True
Conformal cooling provides uniform temperature distribution, reducing warping.
High-temperature molds require less maintenance.False
High temperatures increase wear, necessitating more frequent maintenance.
How Can Equipment Performance Be Optimized for Heat Resilience?
In high-temperature environments, optimizing equipment performance is key to maintaining efficiency and quality.
Enhancing heat resilience in equipment involves upgrading systems with heat-resistant components, improving cooling systems, and ensuring regular maintenance. This strategic approach minimizes failures and maintains operational stability.
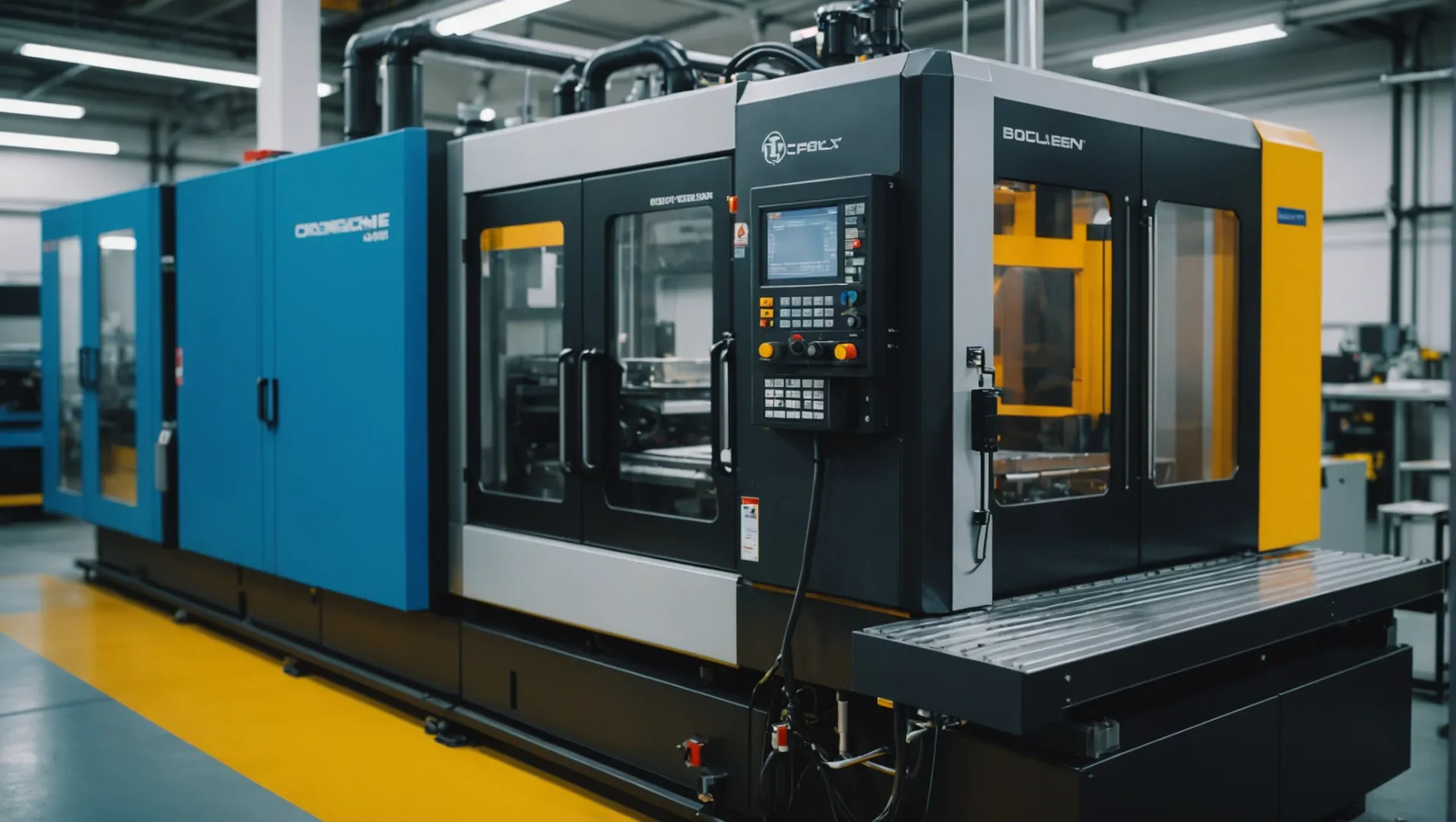
Understanding Equipment Challenges in High Heat
High temperatures can strain an injection molding machine’s core systems. Electrical components, for instance, risk overheating, leading to potential failures. Meanwhile, hydraulic oils may degrade faster, impacting the system’s performance.
To mitigate these risks, consider implementing several strategies:
-
Upgrade Electrical Components:
Use components that are specifically designed to withstand higher temperatures. These can help ensure reliable operation even when environmental conditions push the limits. -
Optimize Hydraulic Systems:
Invest in high-quality hydraulic oils that retain their properties under extreme heat. Regularly monitor oil levels and replace them promptly to avoid any degradation-related issues. -
Enhance Cooling Systems:
A robust cooling system is crucial for maintaining equipment temperature. Consider increasing the number of cooling channels or upgrading existing ones to handle higher loads.
Component | Suggested Upgrade | Benefits |
---|---|---|
Electrical | Heat-resistant components | Minimizes overheating risks |
Hydraulic | High-quality, heat-tolerant oils | Ensures stable system performance |
Cooling System | Expanded or upgraded channels | Efficient heat management |
Maintenance and Monitoring
Regular maintenance is critical to ensure all systems function optimally in high temperatures. This includes:
- Routine Inspections: Conduct thorough checks of electrical and hydraulic systems to identify wear or damage.
- Scheduled Maintenance: Develop a maintenance schedule that includes cleaning, lubricating, and replacing parts as necessary.
- Real-time Monitoring: Utilize sensors to track temperature changes and system pressures. These provide early warnings of potential issues.
For example, real-time monitoring solutions2 can alert operators to irregular temperature spikes, allowing for immediate corrective action.
Implementation of Heat Mitigation Strategies
Finally, implementing heat mitigation strategies can further enhance equipment resilience:
- Ventilation Enhancements: Improve air circulation around equipment by installing fans or ventilation ducts.
- Use of Insulating Materials: Apply insulation to critical parts of the machine to prevent heat transfer.
- Training for Personnel: Equip operators with the knowledge to handle equipment under high temperature scenarios effectively.
By integrating these strategies, manufacturers can significantly enhance their equipment’s heat resilience, ensuring consistent performance and reduced downtime during high-temperature operations. Explore more on effective heat management3 for injection molding equipment.
Heat-resistant components reduce equipment overheating.True
Using heat-resistant components minimizes overheating risks in high-temperature environments.
Regular maintenance decreases equipment failure risk.True
Scheduled maintenance ensures equipment operates efficiently, reducing failure chances.
What Process Adjustments Are Necessary for Efficient Production?
Streamlining production in high-temperature settings demands strategic process adjustments for optimal efficiency.
Efficient production in high-temperature environments requires adjusting injection speed and pressure, optimizing cooling cycles, and ensuring precise temperature control. These changes enhance material handling, improve product quality, and maintain dimensional stability.
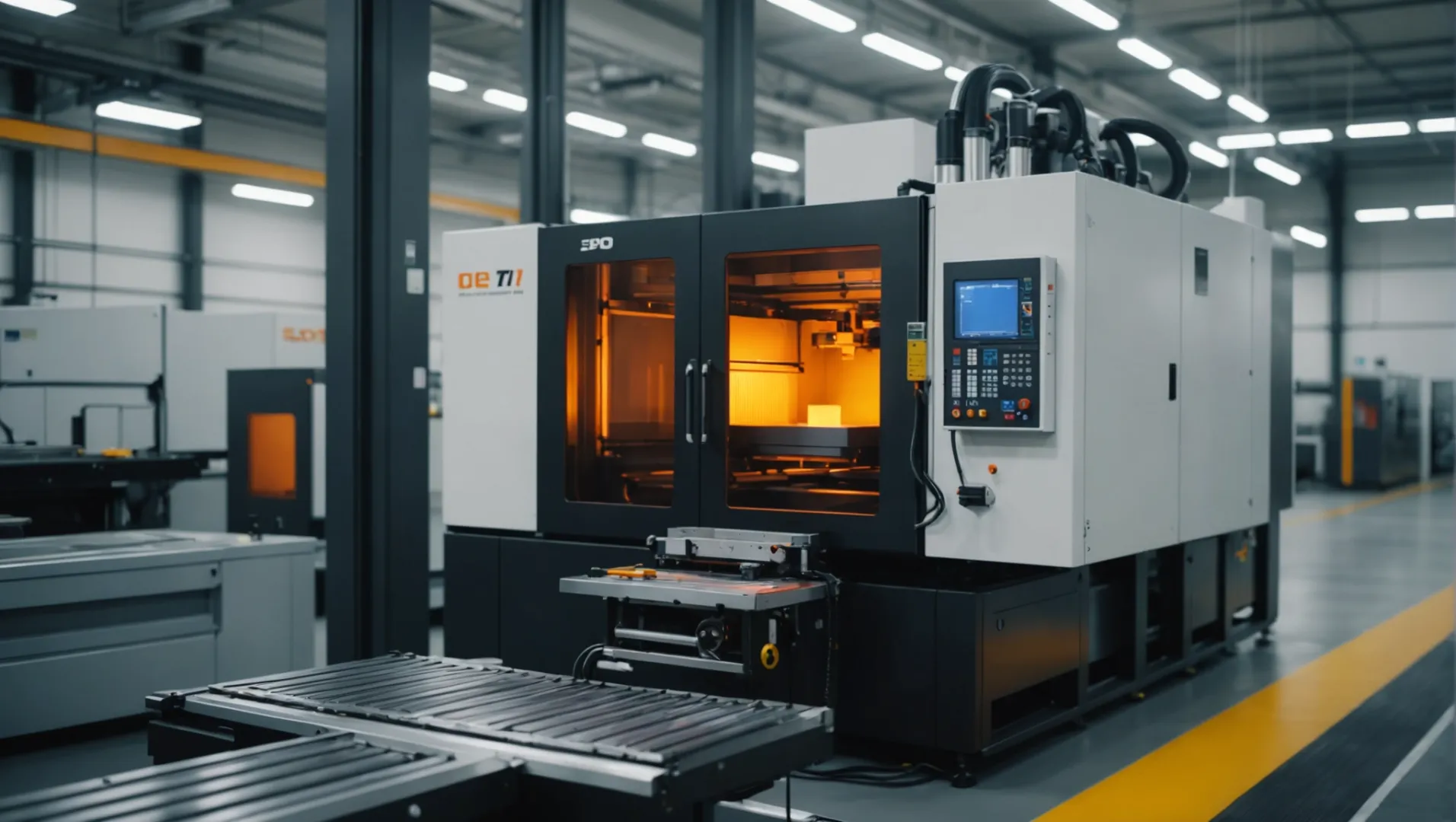
Adjusting Injection Parameters
To achieve efficient production, it is crucial to adjust injection molding parameters such as the speed and pressure of injection. In high-temperature environments, materials may become overly fluid, making precise control necessary to prevent defects like flash and burrs. Reducing injection speed allows for better management of material flow, while adjusting pressure ensures that the material fills the mold correctly without causing stress or distortion.
Optimizing Cooling Cycles
Incorporating optimized cooling cycles is another pivotal adjustment. This involves setting appropriate cooling times and ensuring the entire mold cools uniformly to avoid warping or shrinkage. An efficient cooling system can be enhanced by increasing the number or diameter of cooling channels, facilitating faster heat dissipation.
A comparative table of cooling methods4 used in high-temperature environments can aid in selecting the most effective strategy:
Cooling Method | Description | Advantages |
---|---|---|
Increased Ventilation | Enhances air circulation around the mold | Cost-effective |
Advanced Water Systems | Uses water channels for rapid cooling | Highly effective |
Cryogenic Cooling | Utilizes liquid nitrogen for extreme cooling | Fastest cooling rate |
Ensuring Precise Temperature Control
High-temperature injection molding necessitates accurate temperature control within the machinery. Fluctuating temperatures can impact material properties and lead to inconsistent product quality. Utilizing advanced sensors and controllers helps maintain steady temperatures, ensuring uniform product characteristics and reducing material degradation.
Regular Maintenance and Monitoring
Regular maintenance is integral to efficient production, particularly in demanding environments. Routine checks and timely servicing of equipment reduce downtime due to unexpected failures. Implementing a robust monitoring system5 allows for real-time tracking of equipment performance, enabling quick responses to any anomalies.
By embracing these targeted process adjustments, manufacturers can significantly enhance their production efficiency even under challenging high-temperature conditions.
Reducing injection speed prevents defects like flash and burrs.True
Slower injection speed allows better material flow control, reducing defects.
Cryogenic cooling is the slowest method for mold cooling.False
Cryogenic cooling uses liquid nitrogen, offering the fastest cooling rate.
Conclusion
By addressing the challenges of high temperature injection molding head-on, you can ensure quality and efficiency in your production processes. Let’s embrace these strategies for success.
-
Explore detailed impacts of plastic fluidity changes on molding precision.: The fluidity of plastic molding material refers to the ability of plastic materials to flow within the injection mold in the manufacturing of plastic products. ↩
-
Discover advanced monitoring solutions to prevent overheating.: We specialize in real-time production monitoring for the plastics industry, primarily injection molding machines. Book a free demo with us. ↩
-
Learn about comprehensive strategies to manage equipment heat.: Plastics injection molds are equipped with internal cooling channels, which accept a steady flow of circulating coolant (usually water) at a set temperature. ↩
-
Explore diverse cooling techniques for enhanced mold efficiency.: Cool consistently in both halves of the mold. There are several design aspects of cooling channels that can help achieve good channel design. ↩
-
Discover systems for tracking equipment performance effectively.: MachineMetrics production monitoring software monitors OEE, machine utilization, and downtime for maximum production efficiency and deep operational insights. ↩