Navigating the world of multi-material molding can feel like tackling a complex puzzle, each piece demanding precision and care.
Challenges in molding multi-material components include ensuring material compatibility, designing intricate molds, and maintaining efficient production processes, all of which impact product quality and cost-effectiveness.
Thinking back to my early days in mold design, I vividly remember the thrill and frustration of my first multi-material project. It was like trying to fit together pieces from different jigsaw puzzles. Yet, every challenge overcome was a lesson learned. In this post, I’ll walk you through these common hurdles and share strategies I’ve picked up along the way to turn these obstacles into stepping stones for innovative design.
Material compatibility is crucial in multi-material molding.True
Ensuring materials work well together prevents defects and ensures quality.
Designing simple molds suffices for multi-material components.False
Complex molds are necessary to accommodate different materials effectively.
- 1. How Do Material Compatibility Issues Affect Multi-Material Molding?
- 2. What Are the Essential Design Considerations for Complex Molds?
- 3. How Can You Optimize Production Efficiency in Multi-Material Molding?
- 4. What Are the Latest Advancements in Additive Manufacturing for Multi-Materials?
- 5. How Can I Enhance Quality Control in Multi-Material Molding?
- 6. Conclusion
How Do Material Compatibility Issues Affect Multi-Material Molding?
Ever tried juggling? That’s what multi-material molding feels like—balancing different materials to create one seamless product.
Material compatibility issues in multi-material molding can cause defects such as delamination, poor adhesion, and warping, affecting the product’s mechanical and visual quality, necessitating careful material selection.
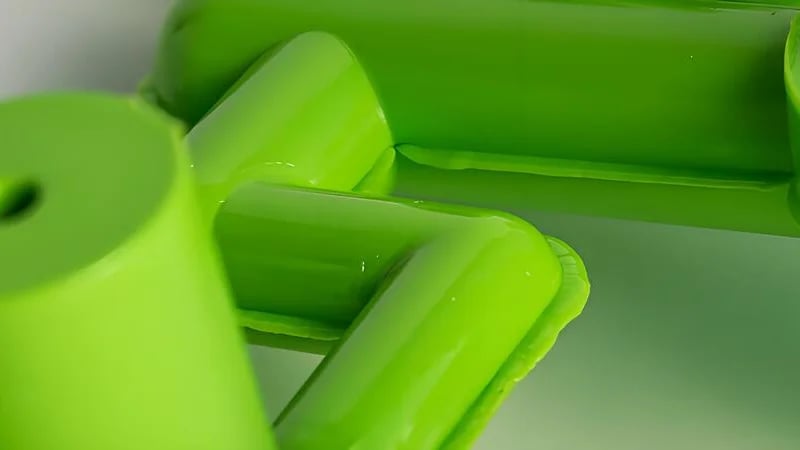
Understanding Material Compatibility
Imagine trying to make a perfect smoothie with ingredients that don’t mix well—some might clump, others might separate. That’s kind of what happens in multi-material molding1, where different polymers or materials are molded together. The challenge? Making sure these materials blend as smoothly as possible.
Key Factors Influencing Compatibility
I remember when I first realized how complex this could get. Thermal expansion, for example, can be a real pain. Different materials expand at different rates when heated, which can lead to stress and possible deformation. Picture a winter day: you leave your car outside, and the metal parts contract while the plastic parts react differently. Similar stuff happens here.
Material A | Material B | Expansion Rate |
---|---|---|
Polymer X | Polymer Y | Low |
Polymer X | Polymer Z | High |
Another factor is adhesion. If materials don’t stick together properly, delamination can occur, which compromises the whole structure. And don’t even get me started on chemical reactivity. Some materials just don’t get along chemically, affecting the durability of the bond.
Common Defects from Incompatibility
- Delamination: Like peeling paint on a wall, layers separate, leading to visible defects.
- Warping: Uneven thermal expansion can cause parts to twist or bend—imagine a warped record that won’t play.
- Surface Imperfections: Poor surface finishes that affect the aesthetics.
To dodge these bullet points of disaster, I learned that designers need to evaluate material properties thoroughly and employ rigorous compatibility testing2.
Strategies for Effective Material Selection
Here’s what works:
- Use of Coupling Agents: These improve bonding between dissimilar materials.
- Simulation Tools: Think of them like a crystal ball predicting potential issues before they happen.
- Prototyping: Test compatibility in real-world conditions—think of it as a dress rehearsal before the big show.
These strategies not only help reduce defects but also boost production efficiency and cost-effectiveness.
Exploring Further
For anyone like me who’s really into this stuff, exploring multi-material injection molding techniques3 can provide deeper insights into overcoming compatibility challenges in manufacturing.
Application in Industry
In industries like automotive and consumer electronics, it’s like walking a tightrope—multi-material components must meet rigorous standards. Understanding compatibility is vital for ensuring products not only function well but also look good doing it.
In summary, dealing with material compatibility in multi-material molding is about combining scientific know-how with practical testing. Embracing advanced tools and strategies can significantly ease these challenges.
Thermal expansion affects multi-material molding outcomes.True
Different materials expand at varying rates, causing stress and deformation.
Chemical reactivity is irrelevant in multi-material molding.False
Chemical interactions can affect the durability of bonded areas.
What Are the Essential Design Considerations for Complex Molds?
Ever wondered what goes into designing a complex mold? It’s more than just shapes and sizes—it’s an art that requires balancing creativity with practicality.
Designing complex molds involves key considerations such as material selection, geometric complexity, wall thickness, draft angles, and undercuts. These factors are essential in ensuring the mold’s efficiency, performance, and durability during large-scale production.
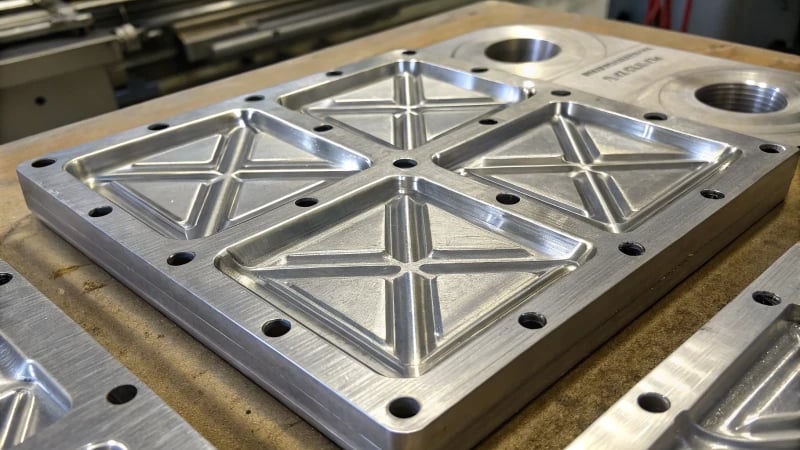
When I first started delving into the world of mold design, it felt like I was trying to solve a never-ending puzzle. Each piece—material choice, geometry, thickness—had to fit just right for everything to work seamlessly. Let me share some insights from my journey.
Material Selection
Picking the right material is like choosing the perfect ingredient for a recipe. It has to withstand high pressures and temperatures. I’ve found that aluminum molds4, steel molds5, and copper alloys each bring something unique to the table. Aluminum molds, for example, are lightweight and have excellent thermal conductivity, which can significantly cut down cycle times—something I always keep in mind when deadlines loom. On the flip side, steel molds are my go-to for high-volume productions due to their durability.
Geometric Complexity
Navigating through geometric complexity often feels like walking a tightrope. When tackling intricate designs with ribs and detailed finishes, techniques like conformal cooling6 are lifesavers. They help manage heat distribution effectively, ensuring even cooling and reducing the risk of warpage.
Wall Thickness
I learned early on that maintaining consistent wall thickness is vital. Too thin, and you risk defects like sink marks; too thick, and you waste material and money.
Material | Recommended Wall Thickness (mm) |
---|---|
Plastic | 1-3 |
Metal | 2-4 |
For plastic molds, sticking to walls between 1-3 mm is typically my rule of thumb.
Draft Angles
Draft angles might seem trivial, but they play a big role in getting the part out of the mold without a hitch. I usually aim for at least a 1-2 degree angle, though complex shapes might call for more.
Undercuts
Undercuts can be tricky—they often require additional tooling like side actions or lifters. It’s essential to address these early on in the design phase to avoid costly reworks. Utilizing advanced CAD tools7 has been invaluable in identifying and designing around these features.
By weaving these considerations into every design, I’ve managed to create molds that not only meet aesthetic expectations but also perform efficiently under production pressures.
Aluminum molds reduce cycle times due to thermal conductivity.True
Aluminum's excellent thermal conductivity aids in faster heat dissipation.
Draft angles over 5 degrees are standard for all mold designs.False
Standard draft angles are 1-2 degrees, varying with complexity.
How Can You Optimize Production Efficiency in Multi-Material Molding?
Ever felt like multi-material molding is a puzzle with missing pieces? Let’s piece it together by optimizing your production efficiency with these proven strategies.
Optimize multi-material molding efficiency by selecting suitable materials, advanced mold design, and process automation. Implement real-time monitoring and predictive maintenance to enhance performance while minimizing downtime.
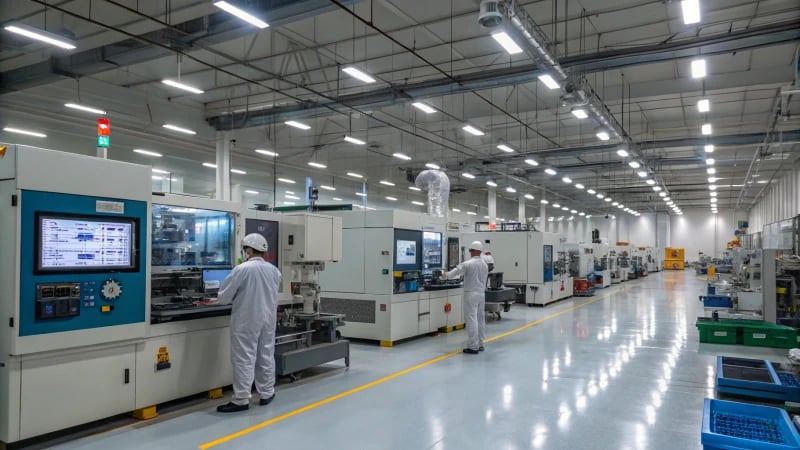
Understanding Material Selection
I remember the first time I had to choose materials for a complex molding project. It felt like trying to find the perfect blend of coffee—too strong, and it overwhelms; too weak, and it doesn’t satisfy. Selecting the right materials in multi-material molding is just as crucial. Each material should complement the other, ensuring quality and durability. For instance, I’ve combined a rigid polymer with a softer elastomer to achieve both strength and flexibility.
I’ve also found that using advanced polymers with enhanced thermal stability8 or UV resistance can significantly reduce defects and enhance product longevity. This approach not only saves time but also boosts customer satisfaction.
Advanced Mold Design Techniques
I once spent hours tweaking a mold design, only to realize the solution lay in using conformal cooling techniques. These innovations can slash cycle times and boost cooling efficiency9. Using CAD tools has been my go-to strategy for simulating and optimizing material flow, ensuring everything fits together seamlessly and with minimal waste.
Another trick up my sleeve is modular mold designs. They offer the flexibility to make quick adjustments without causing lengthy downtimes—a real game-changer when deadlines are tight.
Process Automation and Integration
Automation was like discovering a secret weapon in my manufacturing arsenal. Integrating robotics for tasks like material handling has minimized human error and increased throughput. It’s like having an extra pair of hands that never tire.
Investing in a robust Manufacturing Execution System (MES)10 has also streamlined operations for me. With real-time data on production status at my fingertips, identifying and resolving bottlenecks has never been easier.
Real-Time Monitoring and Predictive Maintenance
Picture this: sensors and IoT devices working round-the-clock to provide insights into machinery performance. This data has allowed me to perform predictive maintenance, cutting down unexpected breakdowns significantly.
A well-maintained machine is like a well-oiled bicycle—smooth, reliable, and always ready to go. Setting up a monitoring dashboard helps my team catch any deviations from optimal performance before they become costly problems.
Using Data Analytics for Continuous Improvement
Data analytics is like having a crystal ball that reveals trends and patterns in production processes. By analyzing these trends, I’ve been able to make informed decisions that enhance efficiency further.
Setting up a framework for continuous improvement11 involves regularly reviewing performance metrics and implementing changes based on data-driven insights. This proactive approach ensures that my production line remains optimized over time.
Here’s a quick overview:
Strategy | Benefits |
---|---|
Precise Material Selection | Reduces defects, enhances durability |
Advanced Mold Design | Improves flow, reduces cycle times |
Process Automation | Increases throughput, reduces errors |
Real-Time Monitoring | Minimizes downtime, ensures quality |
Data Analytics | Enables informed decision-making |
Combining rigid polymers with elastomers enhances durability.True
Rigid polymers add strength, while elastomers provide flexibility, improving durability.
Conformal cooling increases cycle times in mold design.False
Conformal cooling reduces cycle times by improving cooling efficiency in molds.
What Are the Latest Advancements in Additive Manufacturing for Multi-Materials?
Let’s dive into the cutting-edge world of multi-material additive manufacturing, where possibilities are endless and innovation is the name of the game.
Recent advancements in multi-material additive manufacturing, such as voxel-based printing and novel material blends, enable unparalleled customization, improved performance, and innovative designs across industries.
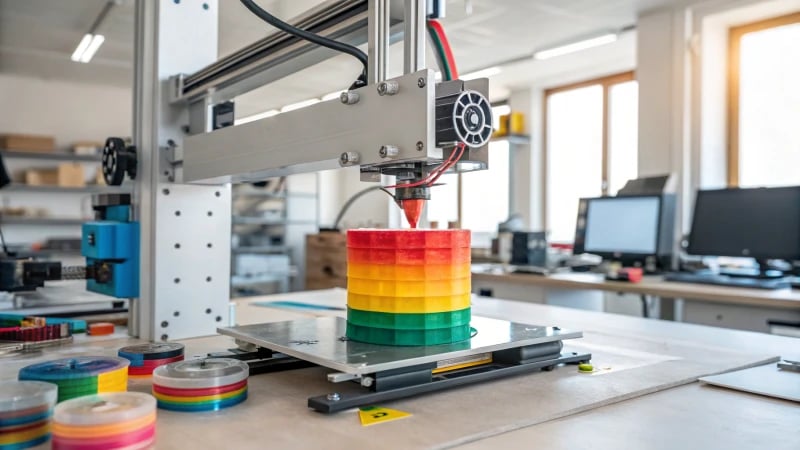
Revolutionizing Material Combinations
Imagine being able to control every tiny detail of a material’s properties—like designing a Lego masterpiece where every block has a different function. That’s what voxel-based printing feels like to me. Recently, this incredible advancement in additive manufacturing12 has opened up possibilities I could only dream of as a young designer. By controlling materials at a microscopic level, I’m able to integrate different materials with varied mechanical and thermal properties, creating structures that seemed impossible just a few years ago.
Feature | Benefits |
---|---|
Voxel-Based Printing | Customizable material distribution, enhanced performance |
Novel Material Blends | Improved strength, flexibility, and application versatility |
Applications Across Industries
I remember my first encounter with multi-material 3D printing in the aerospace sector. It was like witnessing magic—components that were both lightweight and robust enough to enhance fuel efficiency while reducing emissions. It’s not just aerospace; even in the medical field13, I’ve seen how these technologies create custom implants that mimic human tissue more closely than ever before. This isn’t just technology; it’s a revolution.
And let’s talk about consumer electronics! Every time I hold a device that seamlessly integrates electronic components and casings, all made in one go, I’m reminded of how far we’ve come. This approach cuts down on production time and costs, changing the game for designers like me.
Challenges and Future Directions
Of course, it’s not all smooth sailing. There are still hurdles to overcome, such as ensuring consistent quality across different materials and scaling up production for industrial applications. But every challenge is a new opportunity, right? I find myself eagerly following the research into new materials and improved printing methods that are pushing the boundaries even further.
The future is brimming with exciting potential. Imagine working with self-healing materials14 or smart materials that adapt to environmental changes—it’s like science fiction coming to life! Staying updated with these developments isn’t just necessary; it’s exhilarating. For professionals like Jacky, keeping up with these advancements ensures we’re ready to tackle future challenges and seize new opportunities in this competitive landscape.
Voxel-based printing controls material properties microscopically.True
Voxel-based printing allows precise control at a microscopic level.
Self-healing materials are currently used in multi-material 3D printing.False
Self-healing materials are a future innovation, not yet widely used.
How Can I Enhance Quality Control in Multi-Material Molding?
Ever found yourself wrestling with the complexities of multi-material molding? Let’s explore some game-changing strategies that ensure top-notch quality control in this intricate process.
Enhance quality control in multi-material molding by implementing real-time monitoring, precision process control, and advanced material analysis, supported by regular equipment maintenance and thorough staff training for consistent product quality.
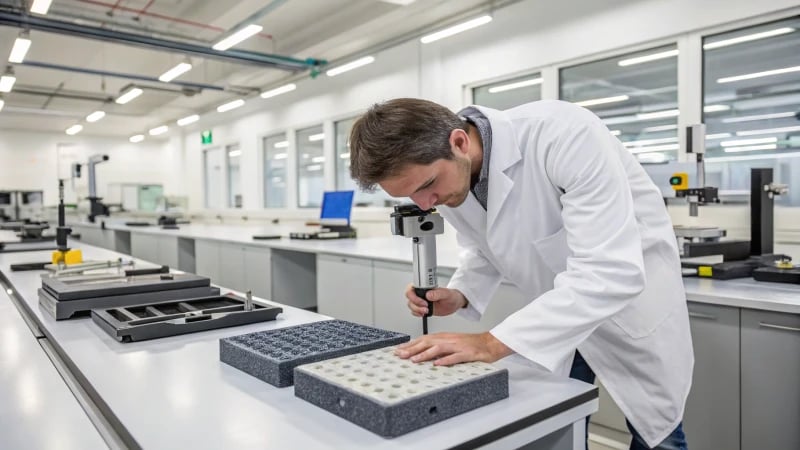
Real-Time Monitoring Systems
One of the most transformative steps I’ve taken is implementing real-time monitoring15 systems. Imagine having sensors and software that instantly alert you to any hiccups in pressure, temperature, or fill time. It’s like having a guardian angel for your manufacturing process, catching defects before they become costly issues.
- Advantages: This approach has significantly reduced waste for me and boosted overall efficiency.
- Tools: I’ve found that integrating software solutions seamlessly with existing setups can be a game changer.
Precision in Process Control
Precision isn’t just a buzzword; it’s the cornerstone of quality. Techniques like precision machining16 and CAD have been instrumental in my journey to achieve impeccable results.
Aspect | Importance |
---|---|
Dimensional Accuracy | High |
Cycle Time | Moderate |
Material Consistency | Very High |
Advanced Material Analysis
Before diving into production, I always emphasize the importance of analyzing materials for compatibility and performance. Using spectroscopic analysis17 ensures I avoid unexpected reactions during molding, helping me to select the best materials—be it thermoplastics or elastomers—to minimize defects.
- Materials: Thermoplastics, elastomers.
- Benefits: Improved material selection reduces defects.
Equipment Maintenance and Calibration
I can’t stress enough how crucial regular maintenance and calibration are. Skipping these steps once led to unforeseen variations in product quality, a lesson I learned the hard way. Now, I stick to a rigorous maintenance schedule—monthly for high-use machines and quarterly calibrations.
- Routine Check: Monthly for high-use equipment.
- Calibration: Quarterly to ensure precision.
Staff Training Programs
Finally, training is key. I’ve invested heavily in workshops and online courses for my team, focusing on safety, new technologies, and troubleshooting. Investing in training18 has not only improved quality but also boosted employee morale and reduced turnover rates. It’s all about fostering a culture of continuous learning to keep us ahead of the curve.
Real-time monitoring reduces waste in molding.True
Real-time monitoring detects defects early, reducing waste and improving efficiency.
Monthly calibration is recommended for all equipment.False
Calibration is recommended quarterly, not monthly, for precision maintenance.
Conclusion
Multi-material molding presents challenges like material compatibility, intricate mold design, and production efficiency. Strategies include careful material selection, advanced design techniques, and real-time monitoring for quality control.
-
Understand the basics of multi-material molding and its applications in various industries. ↩
-
Learn about methods for testing material compatibility to prevent molding defects. ↩
-
Discover cutting-edge techniques in multi-material injection molding for improved product outcomes. ↩
-
Aluminum molds offer superior thermal conductivity, which can significantly reduce cycle times in production. ↩
-
Steel molds are highly durable, making them ideal for high-volume production runs where longevity is crucial. ↩
-
Conformal cooling improves heat management in complex mold designs, leading to better quality and reduced warpage. ↩
-
Advanced CAD tools help identify and address complex features like undercuts early in the design process. ↩
-
Explore polymers that improve thermal stability to reduce defects and enhance product longevity. ↩
-
Learn how conformal cooling techniques can reduce cycle times and enhance mold cooling efficiency. ↩
-
Understand how MES can streamline operations by providing real-time data on production status. ↩
-
Discover frameworks for continuous improvement that help maintain optimized production lines. ↩
-
Explore how voxel-based printing allows for customizable material properties at a microscopic level. ↩
-
Discover how multi-material 3D printing is revolutionizing medical implants. ↩
-
Learn about innovative self-healing materials and their potential applications. ↩
-
Real-time monitoring systems provide immediate feedback, helping to identify defects early and improve overall efficiency. ↩
-
Precision machining ensures high-quality molds, crucial for maintaining dimensional accuracy and reducing waste. ↩
-
Spectroscopic analysis helps identify material compatibility, preventing unwanted reactions during the molding process. ↩
-
Investing in staff training improves skills, enhances quality control measures, and increases employee satisfaction. ↩