Have you ever asked why those annoying sprue marks appear on your neatly shaped products?
Sprue marks on injection molded products are caused by improper gate design, incorrect process settings, and material properties. Optimizing gate characteristics and adjusting injection speeds and pressures can help reduce these marks.
Understanding why sprue marks happen is just the beginning. I felt like a detective when I first saw these marks. I tried to solve a mystery. I realized the picture became clearer after looking into design and process mistakes. For example, I adjusted the gate location on a project for an electronics company. This simple change improved the product’s appearance a lot. Small changes lead to big improvements. Sharing these insights helps others improve their work. Product quality really improves this way.
Sprue marks result from incorrect gate design.True
Improper gate design can lead to sprue marks by affecting material flow.
Adjusting injection speed increases sprue marks.False
Optimizing injection speed helps reduce sprue marks by ensuring proper flow.
How Does Gate Design Affect Sprue Marks?
Look at a plastic part. See the sprue mark? The mark stands out a lot. Gate design causes this. Learn how these designs affect the marks.
Gate design really impacts sprue marks because it controls how molten plastic flows and cools. Issues with gate size, shape or location probably result in visible marks. These marks affect the product’s appearance and function.
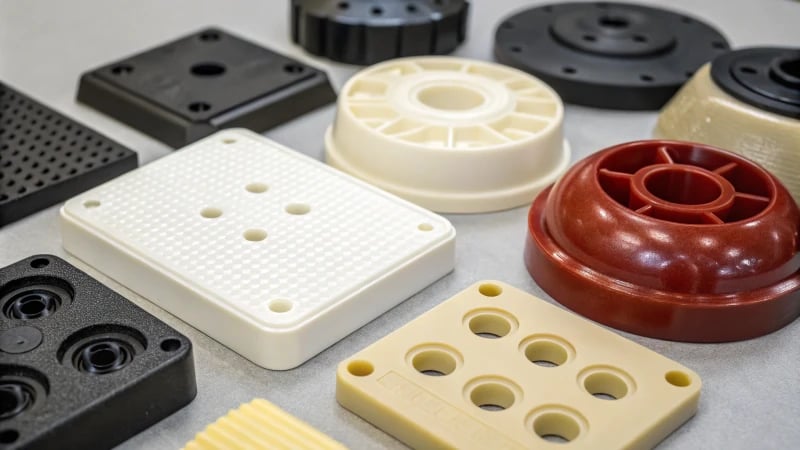
The Impact of Gate Size
The size of the gate plays a crucial role in sprue mark formation. Think of pouring a thick milkshake through a straw. If the straw is too big, you spill it everywhere. If it’s too small, it barely flows. A large gate causes the plastic to move slowly, creating thick marks near the gate. Conversely, a small gate pushes the plastic too fast, leading to irregular patterns.
Gate Size | Impact on Sprue Marks |
---|---|
Too Large | Thick, pronounced marks due to stagnation |
Too Small | Jetting and irregular patterns |
I recall a project where we adjusted the gate size for weeks before finding the right size.
Gate Shape and Its Consequences
In my early career, I designed a part with a pin point gate and soon learned why shape matters a lot. During demolding, plastic stuck to the gate pin, leaving rough marks. The wrong gate shape1 can ruin things; for example, a side gate at an incorrect angle stops smooth flow and results in ugly fusion marks.
Strategic Gate Location
Placing gates needs careful planning. Gates positioned too near a visible surface become unattractive. Once, we placed a gate by a thin-walled section which caused short shots and left clear traces.
Gate Location | Effect on Sprue Marks |
---|---|
Near Surface | Affects appearance negatively |
Thin-Walled Area | Short shots and visible traces |
The strategic location2 of gates must always be planned carefully to solve these problems.
Injection Molding Parameters
Adjusting injection settings is like tuning an instrument. High pressure causes swirling around the gate while high speed causes shear heat; both leave more visible marks.
I spent days adjusting these settings with the goal of perfecting our output.
Material Properties
The fluidity of plastic matters significantly as well. Materials that don’t flow easily might fill the mold poorly, resulting in visible sprue marks. When materials flow too easily without proper control of parameters, jetting effects are evident.
Understanding these parts helps in crafting successful gates that reduce sprue marks and improve product quality. Each project teaches me something new that shapes my approach to making better designs.
A large gate reduces sprue marks by slowing flow rate.False
A large gate causes stagnation, leading to thicker sprue marks.
High injection speed decreases sprue marks.False
Excessive speed increases shear heat, worsening sprue marks.
How Do Injection Molding Parameters Affect Sprue Marks?
Do you ever think about why sprue marks always show up on your molded parts? The answer is in the injection molding settings.
Pressure, speed and temperature are important in injection molding. These factors affect sprue mark formation. Setting them properly helps reduce defects a lot. This improvement really changes how plastic parts look and work.
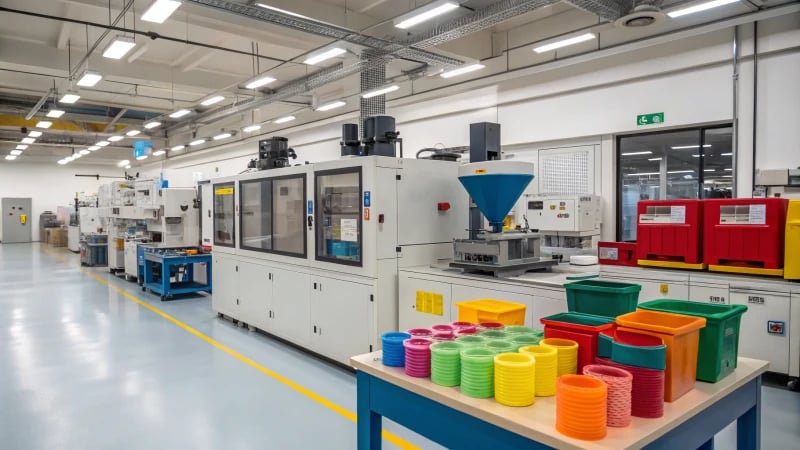
Key Injection Molding Parameters Influencing Sprue Marks
When I began studying injection molding, I discovered how parameters like pressure and speed greatly affect sprue marks. It’s similar to balancing a recipe. Too much of one element and the result is flawed.
Injection Pressure and Speed
I quickly noticed excessive pressure as a common issue. Imagine swirling the melt too much at the gate, like whipping cream too hard. Visible marks become noticeable. High speed, on the other hand, resembles driving a race car too fast. It leads to decomposition and those unwanted burnt marks.
Parameter | Effect |
---|---|
High Pressure | Swirling flow, visible marks |
High Speed | Decomposition, burnt marks3 |
Mold Temperature
Seeing how mold temperature alters cooling was truly enlightening. Higher temperatures slow cooling, leaving thick gate marks. It’s like a pot simmering too long. If it’s too cold, underfilled spots with clear marks might appear.
Material Properties and Their Effects
Choosing the right plastic is similar to picking pasta for your sauce. Poorly flowing plastics might struggle at the gate. This results in stagnation and noticeable marks. Thermosensitive plastics face problems with high temperatures or shear rates, causing discoloration4 and burnt gate marks.
Gate Design Considerations
Gate Size and Shape
I remember designing gates that were either too large or too small. Large gates act like funnels, causing stagnation. Small gates jet through like a power hose, resulting in irregular patterns. The shape of the gate matters a lot too; pin-point gates can leave rough marks due to adhesion.
Gate Design Factor | Impact on Sprue Marks |
---|---|
Large Diameter | Stagnation near gate |
Small Diameter | Jetting, irregular patterns |
Inappropriate Shape | Rough or pronounced marks |
Location of the Gate
The gate’s placement is crucial, much like arranging a view in a gallery. Placing a gate too close to visible surfaces hurts product aesthetics. Poor location may also cause short-shooting in thin-walled areas because of insufficient pressure.
Learning more about injection molding defects5 could really improve your production process.
High injection pressure causes swirling flow.True
Excessive pressure leads to melt swirling at the gate, forming marks.
Low mold temperature causes thicker gate marks.False
Low temperatures hinder flow, causing underfilling and visible marks.
How Do Plastic Material Properties Influence Sprue Marks?
Have you ever thought about why some plastic items have those annoying small marks?
The properties of plastic materials include fluidity and heat sensitivity. These properties directly affect sprue mark formation. Highly fluid plastics probably fill molds easily. Yet, they risk creating jetting marks. Highly fluid plastics risk this problem. Heat-sensitive plastics decompose at high temperatures. This decomposition leads to distinct sprue marks. Sprue marks become noticeable.
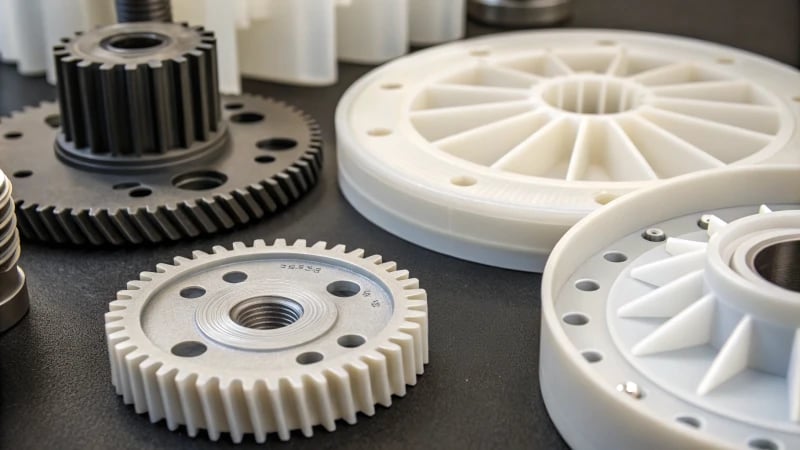
Fluidity of Plastic Materials
Plastic fluidity is similar to pouring a thick milkshake into a narrow glass. Poor flowing plastics encounter problems smoothly filling the mold. Imagine a highly filled composite6 pushing through, leaving clear sprue marks behind. In contrast, more fluid plastics flow too fast, like a milkshake splashing everywhere. This is called jetting. Finding the right balance is delicate. Mold designs and injection settings often need adjustments.
Plastic Type | Fluidity | Sprue Mark Impact |
---|---|---|
Poor Flow | High Resistance | Prominent Marks |
Good Flow | Easy Fill, Risk Jet | Irregular Traces if Uncontrolled |
Thermal Sensitivity of Plastics
Plastics’ thermal sensitivity is unforgiving. I once used PVC that decomposed at higher temperatures. It left very noticeable burnt marks. Changing temperature and shear rate becomes crucial to prevent these issues.
For example, PVC may decompose, producing burnt and discolored marks7 due to changes in melt flow rate and pressure near the gate. To mitigate this, optimizing the injection molding process parameters8, such as adjusting temperature and shear rate, is essential.
Influence of Irrational Gate Design
Once, I ignored the gate design for a project. Using a large gate slowed the flow, leading to stagnation and thicker traces. A small gate caused fast-flowing jetting, forming irregular patterns.
An irrational gate design can exacerbate sprue marks significantly. The shape and location of the gate also matter significantly; for instance, pin point gates9 might leave rough marks if the plastic adheres to the pin during demolding.
Understanding these small details in plastic materials has really shaped my path as a designer. Each type of plastic has its quirks and personality traits. Careful handling is necessary to achieve the best quality in molded parts.
Highly fluid plastics always prevent sprue marks.False
While they fill molds easily, they risk jetting if speed isn't controlled.
Thermal sensitivity affects sprue mark visibility.True
Sensitive plastics may decompose, causing burnt marks near the gate.
Can Advanced Technologies Help Reduce Sprue Marks?
Have you ever thought about how to say farewell to unwanted sprue marks in injection molding?
Advanced technologies include precision molding and smart sensors. These technologies change the game for reducing sprue marks. They offer precise control over molding parameters. This precision improves product quality. It also reduces visible defects.
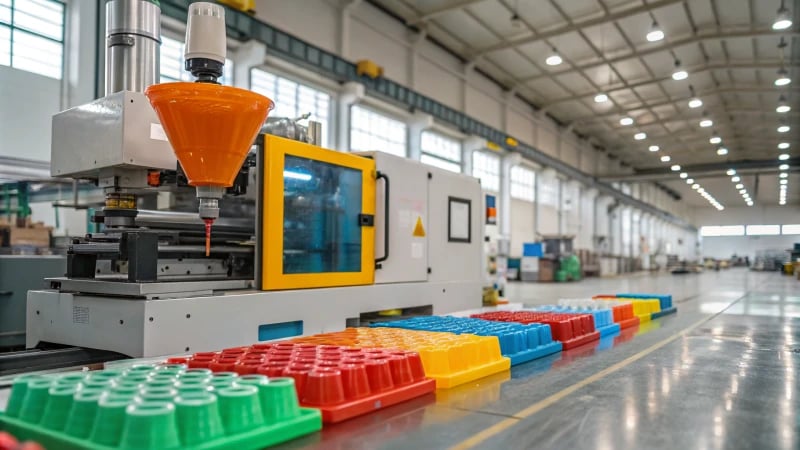
Exploring Precision Molding Techniques
Precision molding techniques solve sprue mark problems directly. I remember when I first saw how a well-designed gate transformed things. Advanced computer-aided design10 software helps us adjust gate designs to perfect them. This prevents issues from bad gate sizes or shapes. The software does more than design; it simulates fluid dynamics, ensuring the molten plastic spreads evenly into every small space, reducing ugly defects.
Smart Sensor Integration
Think of a guard that never sleeps, always watching the injection molding process. Smart sensors do just that. They monitor things like injection pressure and speed. I recall a project where sensors detected an issue during production, saving us from faulty parts. These small heroes let us fix problems immediately and prevent issues like high shear rates, which can cause burnt marks at the gate.
Parameter | Traditional Method | Advanced Tech Approach |
---|---|---|
Injection Speed | Manual Calibration | Automated Adjustment |
Mold Temperature | Fixed Settings | Dynamic Control |
Materials and Innovations
Choosing the right material is like picking the perfect partner; it can really decide your project’s success. Improved fluidity polymers are a game changer as they flow better and solve problems like stagnation and uneven filling. Control over mold temperatures stops heat-sensitive plastics from decomposing, preserving our products’ quality.
I remember testing new composites for tough conditions; the results were amazing, showing that learning about material properties is valuable.
The Role of Artificial Intelligence
AI goes beyond being just a buzzword; it acts as our crystal ball for possible molding problems. Machine learning examines past data to foresee issues such as bad gate locations before they happen. It’s like adding extra eyes to our designs, helping us proactively adjust settings to improve efficiency and reduce defects.
These technologies have great potential but need ongoing development and testing for smooth integration into regular manufacturing processes. Knowing the limits and possibilities of each technology is crucial for those of us hoping to improve product quality and efficiency.
Learn more about AI applications in manufacturing11. Discover how they may predict and solve complex issues before they arise.
AI predicts unsuitable gate locations in molding.True
AI uses past data to forecast potential issues, like gate locations.
Manual calibration is used for dynamic mold temperature control.False
Advanced tech uses automated systems for dynamic mold temperature control.
Conclusion
Sprue marks on injection molded products arise from improper gate design, incorrect process settings, and material properties. Adjustments in these areas can significantly enhance product quality.
-
Learn how different gate sizes influence plastic flow and cooling, impacting sprue mark visibility. ↩
-
Discover how side gate angles impact plastic flow and fusion marks during molding. ↩
-
Learn how controlling injection speed can prevent common defects such as burnt or discolored sprue marks. ↩
-
Discover how the thermal properties of plastics influence the formation of sprue marks during molding. ↩
-
Gain insights into various injection molding defects and effective strategies to mitigate them. ↩
-
Learn how fillers in composites affect plastic flowability and impact sprue marks. ↩
-
Understand the effects of PVC decomposition on injection molding quality. ↩
-
Find strategies to optimize parameters for minimizing sprue marks. ↩
-
Explore challenges and solutions associated with pin point gate designs. ↩
-
Discover how CAD software enhances precision in injection molding by optimizing gate designs and reducing defects. ↩
-
Explore how AI is transforming manufacturing processes by predicting issues, enhancing efficiency, and reducing defects. ↩