Injection molding is a marvel of modern manufacturing—but it’s not without its pitfalls. Debonding and cracks can jeopardize the integrity of your products, leaving you with costly defects.
Debonding and cracks in injection molded products are primarily caused by insufficient injection pressure, improper mold temperature, material issues, and design flaws. These defects can be prevented by optimizing processing conditions, selecting suitable materials, and improving mold design.
While these initial insights provide a quick overview, understanding the intricate details of these defects and their countermeasures is essential for anyone in product design or manufacturing. Read on to explore deeper insights that can significantly enhance your production processes.
Insufficient injection pressure causes debonding.True
Low pressure fails to fill mold cavity fully, weakening bond.
How Does Injection Pressure Affect Product Integrity?
Injection pressure in molding is crucial for maintaining product integrity and quality.
Injection pressure directly impacts product integrity by influencing the fill quality of the mold, affecting bonding strength, and contributing to defects such as cracks or debonding. By adjusting injection pressure appropriately, manufacturers can ensure better product performance and longevity.
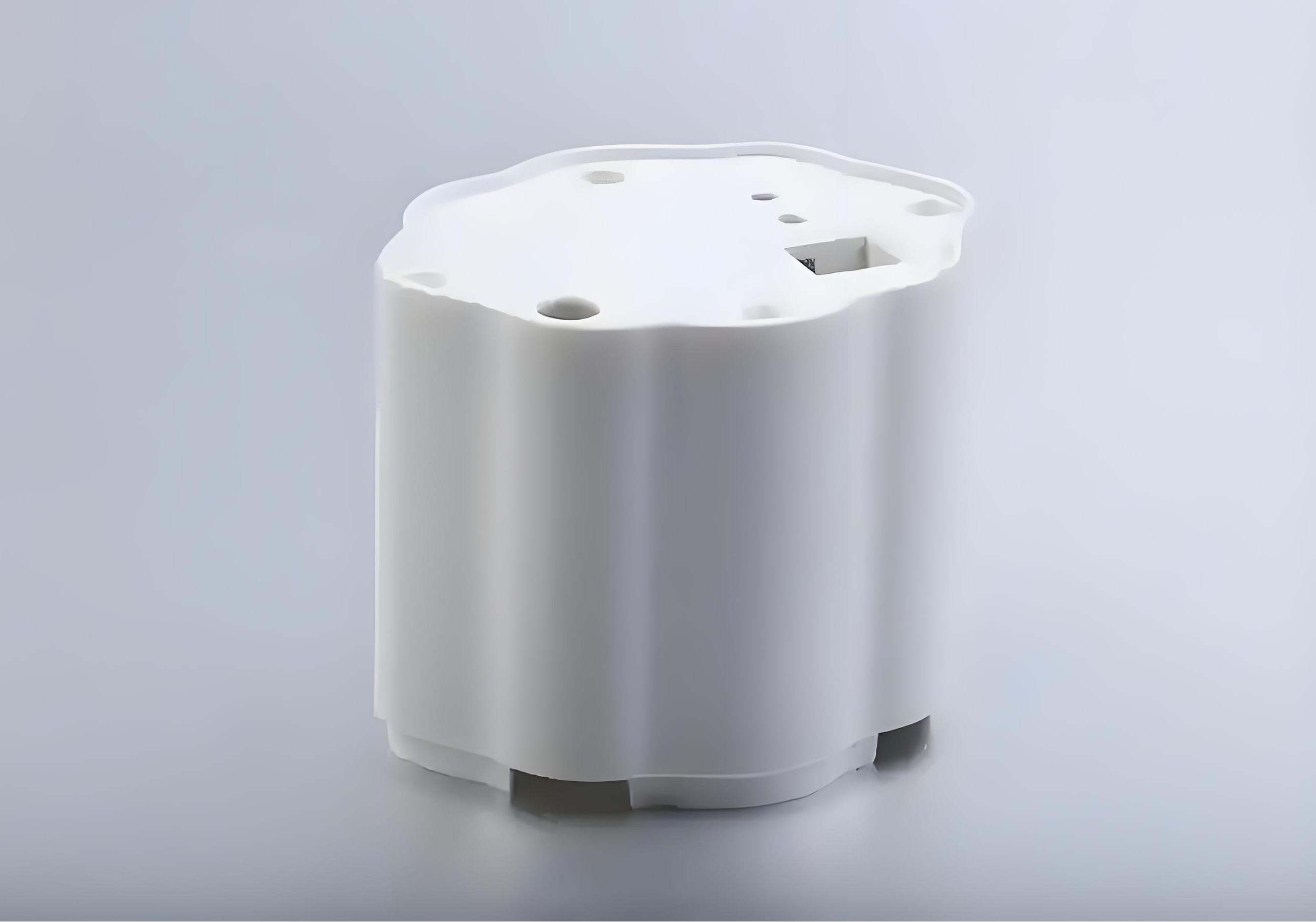
The Role of Injection Pressure in Molding
Injection pressure is a critical parameter in the injection molding process. It determines how well the plastic melt fills the mold cavity. If the injection pressure is insufficient, the melt may not fully occupy the cavity, leading to incomplete parts or weak bonding with the mold surface. This results in debonding, where parts separate from the mold improperly, compromising product integrity.
Conversely, excessive injection pressure can lead to internal stresses within the mold, causing deformation or cracks in the product. Balancing injection pressure is essential to achieve optimal mold filling without introducing stress-related defects.
Common Defects Caused by Improper Injection Pressure
- Debonding: Insufficient pressure fails to press the melt against the mold walls tightly, leading to weak bonding.
- Cracks: High pressure can overstress the material or the mold, resulting in cracks.
Defect Type | Cause | Recommended Countermeasure |
---|---|---|
Debonding | Low injection pressure | Increase injection pressure |
Cracks | High injection pressure | Reduce injection pressure |
Optimizing Injection Pressure for Better Product Integrity
Manufacturers can take several measures to optimize injection pressure:
- Adjust Process Parameters: Carefully calibrate the injection speed and pressure1 to suit specific material and product requirements.
- Monitor Mold Fill Quality: Use sensors to detect underfilled areas in real-time.
- Regular Maintenance: Ensure molds are free from obstructions that could alter pressure distribution.
Case Studies: Real-World Applications
A case study in the automotive industry highlighted how optimizing injection pressure reduced debonding incidents by 30% and improved overall part consistency.
In another instance, a consumer electronics manufacturer adjusted their injection parameters based on real-time monitoring data. They achieved a significant reduction in stress-induced cracks, leading to enhanced product durability.
Understanding how injection pressure affects product integrity allows manufacturers to make informed decisions that improve quality and reduce defects. These insights are vital for anyone involved in product design2 or manufacturing. By exploring these aspects, businesses can enhance their production processes and deliver superior products to market.
High injection pressure causes cracks in products.True
Excessive pressure leads to internal stresses, resulting in cracks.
Low injection pressure prevents debonding.False
Insufficient pressure leads to weak bonding and debonding issues.
What Role Does Mold Temperature Play in Defect Prevention?
Mold temperature is a pivotal factor in injection molding, influencing both product quality and defect prevention.
Mold temperature significantly impacts defect prevention by affecting the demolding performance and internal stress of molded products. Proper temperature management can mitigate issues such as debonding and cracking, ensuring higher quality and durability.
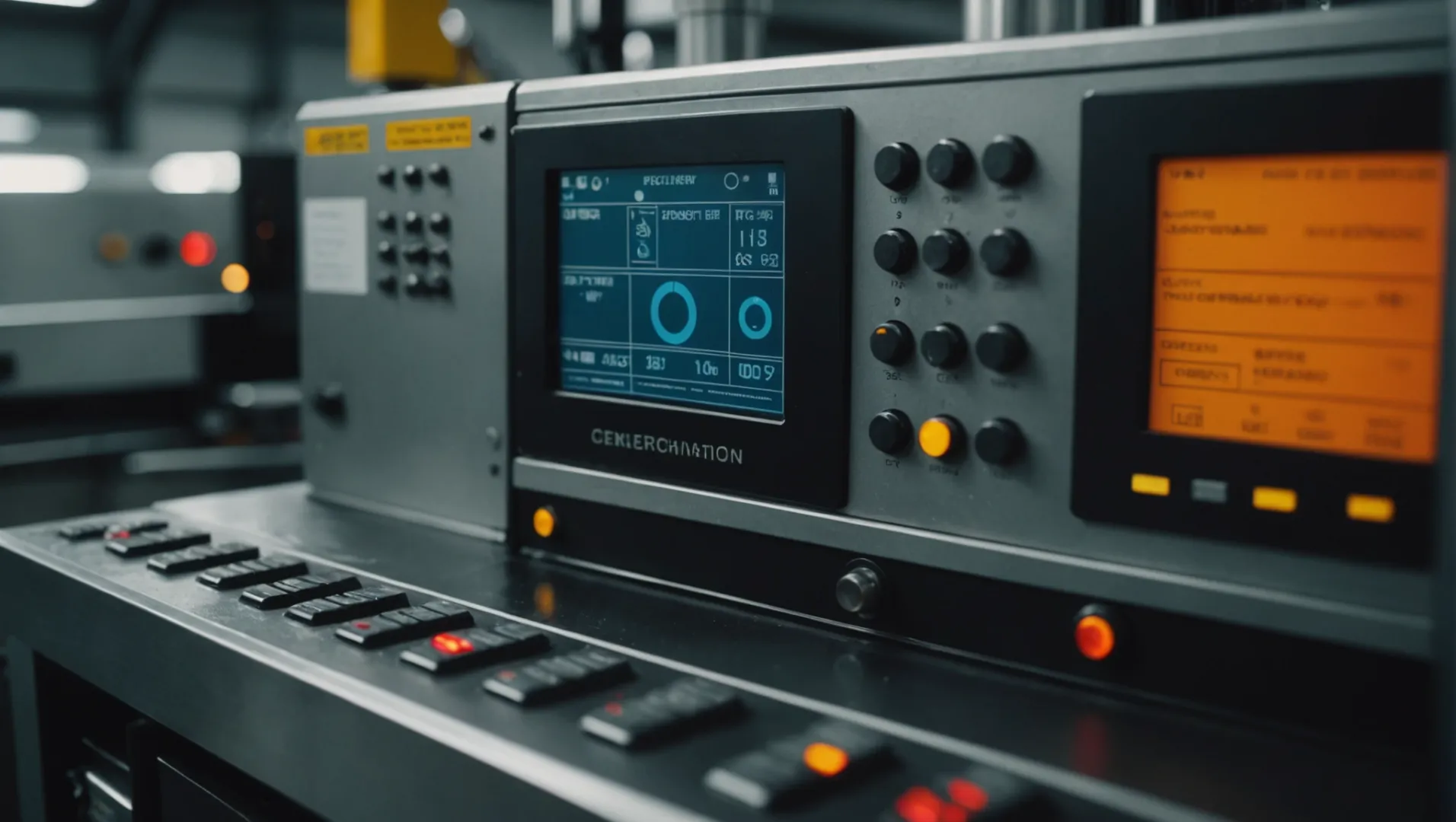
The Impact of Mold Temperature on Demolding Performance
Mold temperature plays a crucial role in the demolding process of injection molded products. A temperature that is too high can cause the molten plastic to stick to the mold, leading to difficulties in releasing the product. Conversely, a temperature that is too low results in the plastic cooling too quickly, causing uneven shrinkage and potential debonding. By optimizing mold temperature, manufacturers can improve the ease of demolding and reduce instances of defects.
Example: Consider a scenario where the mold temperature is excessively high. The plastic may adhere to the mold surface, making it challenging to remove without damaging the product. On the other hand, if the mold temperature is too low, rapid cooling might lead to uneven contraction, causing the product to pull away from the mold surface prematurely.
Ensuring Uniform Mold Temperature
Uniform mold temperature is critical in preventing defects like cracks. Variations in temperature across the mold can lead to uneven shrinkage, creating internal stresses that exceed the material’s strength, resulting in cracks. Techniques such as utilizing heating rods or oil temperature machines can help maintain consistent temperatures throughout the mold.
Example: A manufacturing setup employing uneven heating can cause different parts of the product to cool at varying rates, inducing stress and potential cracking. By implementing uniform heating methods, these risks are minimized.
Strategies for Temperature Optimization
To optimize mold temperature effectively, it is essential to consider several factors:
- Material Characteristics: Different materials require specific temperature settings for optimal flow and solidification.
- Product Design: Complex designs might need tailored temperature control to ensure even cooling.
- External Factors: Ambient conditions and equipment efficiency can also affect mold temperature control.
Example: Utilizing a mold temperature control unit3 can help maintain precise temperature settings tailored to material and design specifications, reducing defect rates significantly.
In summary, proper mold temperature control is indispensable for preventing defects in injection molded products. By understanding and implementing optimal temperature strategies, manufacturers can enhance product quality and longevity.
High mold temperature can cause product sticking.True
Excessive heat causes plastic to adhere to the mold, complicating demolding.
Low mold temperature prevents debonding issues.False
Low temperatures cause rapid cooling, leading to uneven shrinkage and debonding.
Why Is Material Selection Critical in Injection Molding?
Choosing the right material for injection molding is crucial for ensuring product performance, longevity, and cost-efficiency.
Material selection in injection molding affects product strength, durability, and manufacturability. The wrong material can lead to defects like debonding and cracks. Considerations include material flow properties, moisture content, and compatibility with the mold design to ensure a high-quality product.
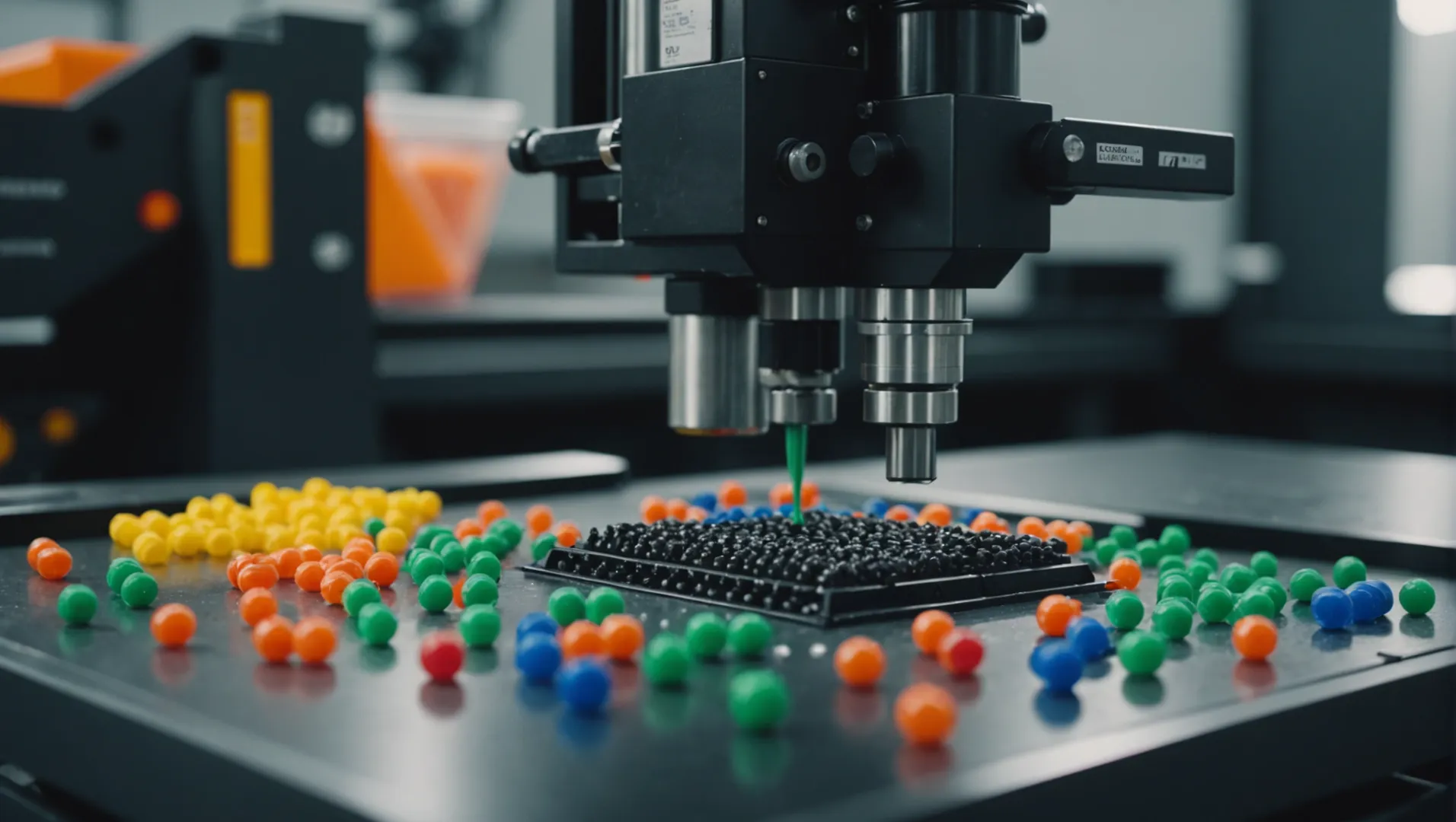
Understanding Material Properties
The choice of material in injection molding is paramount because it directly influences the mechanical properties4 of the final product. This includes tensile strength, flexibility, and resistance to various environmental factors such as temperature and chemicals. Selecting a material that aligns with the product’s intended application ensures that it performs effectively under expected conditions.
Material Flow and Molding Process
Materials with poor flow characteristics can lead to incomplete filling of the mold, resulting in defects like debonding. To prevent this, it’s important to choose a material with appropriate flow properties that suit the specific mold design and injection parameters. For instance, materials like nylon and polyethylene have different flow behaviors; understanding these can help in making an informed decision.
Moisture Content Management
Moisture content in materials can significantly affect the molding process. High moisture levels can lead to issues like bubbling or voids within the product, while dry materials ensure smooth operation. Therefore, pre-treatment processes such as drying are essential before the material is used in molding. This step ensures that the end product is free from imperfections caused by moisture.
Compatibility with Mold Design
The design of the mold itself should complement the chosen material. Materials react differently under stress and temperature variations, which necessitates a design that accommodates these characteristics. For example, a material prone to high shrinkage might require a mold designed with extra allowances to compensate for this factor.
Balancing Cost and Performance
Finally, balancing cost-effectiveness with performance is crucial. While some high-performance materials might offer excellent attributes, they may also drive up costs significantly. Analyzing the cost-benefit ratio for each potential material is necessary to ensure that both production costs and product quality remain within desired parameters.
In conclusion, careful consideration of material properties and compatibility with design and processing conditions can prevent defects like debonding and cracks, ensuring a successful injection molding project.
Material flow affects injection molding quality.True
Poor flow can cause incomplete mold filling and defects.
High moisture content improves material strength.False
High moisture causes defects like bubbling, weakening the product.
How Can Mold Design Minimize Stress and Cracking?
Effective mold design is pivotal in preventing stress and cracking in injection molded products, ensuring durability and quality.
Mold design minimizes stress and cracking by focusing on uniform wall thickness, smooth transitions, and optimized cooling systems. These design elements help in distributing stress evenly and reducing weak points in the final product.
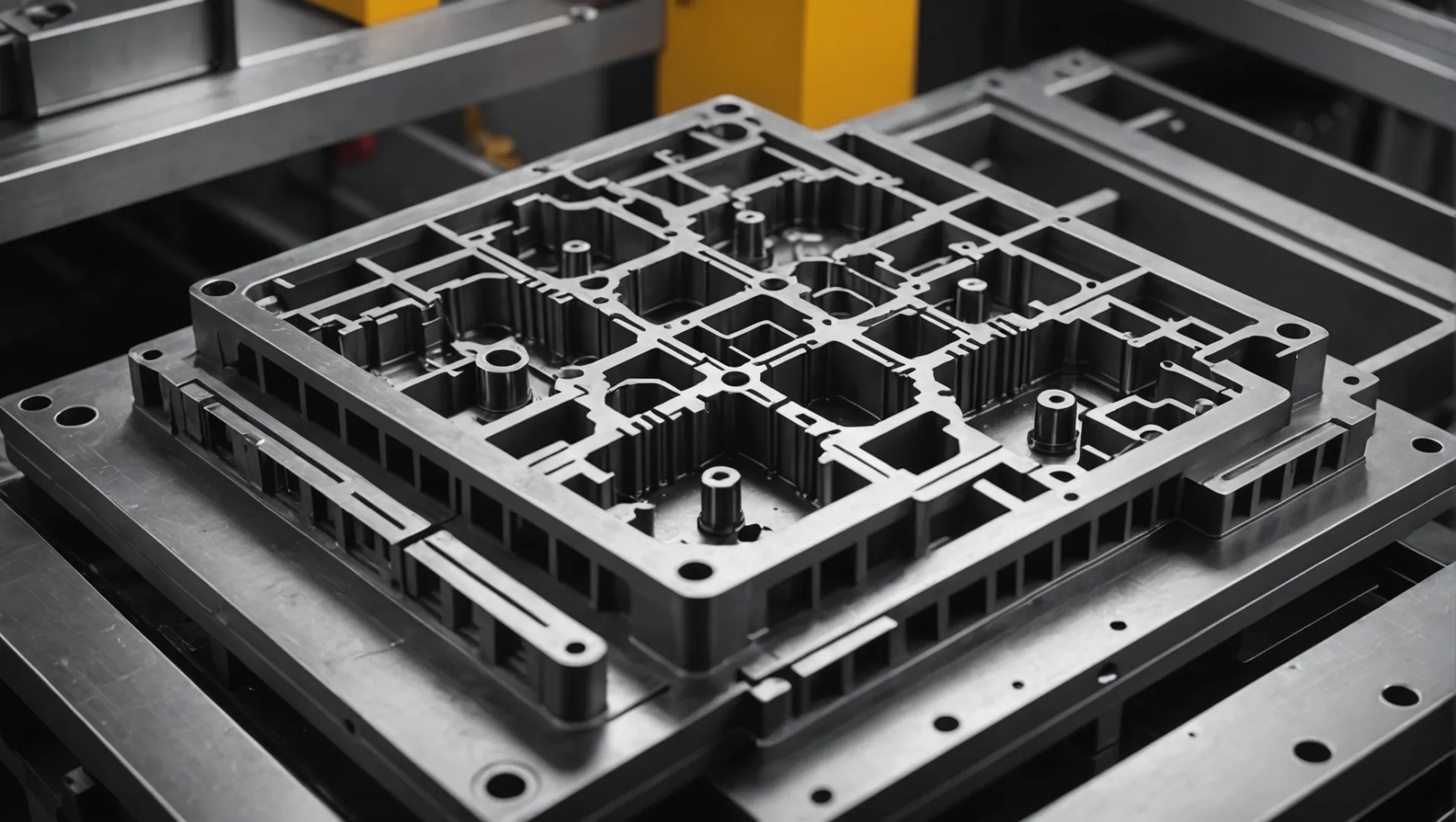
Key Elements in Mold Design
Proper mold design5 is crucial for minimizing defects in injection molded products. By focusing on the following elements, manufacturers can significantly reduce stress and cracking:
- Uniform Wall Thickness: Ensuring uniform wall thickness helps distribute stress evenly throughout the product, avoiding areas where stress may concentrate and cause cracks.
- Smooth Transitions: Sharp corners can act as stress concentrators. By designing smooth transitions, such as rounded corners, stress can be distributed more evenly, thereby minimizing the risk of cracking.
- Reinforcing Ribs: Adding ribs can enhance the strength of a product without increasing wall thickness excessively, thus balancing strength and weight efficiently.
Cooling System Optimization
A well-designed cooling system is essential to prevent internal stresses that lead to cracking:
- Balanced Cooling Channels: Distribute cooling channels uniformly to ensure even cooling across the mold. Uneven cooling can result in differential shrinkage, leading to cracks.
- Advanced Cooling Techniques: Utilize techniques such as conformal cooling, where cooling lines are designed in complex shapes to fit the mold geometry better, ensuring efficient heat removal.
Case Study: Optimizing Mold Structure
Consider a manufacturer facing frequent product cracking issues. By redesigning the mold with:
- Uniform Wall Thickness
- Reinforced Ribs
- Optimized Cooling Systems
The manufacturer reduced defect rates significantly, demonstrating the power of thoughtful mold design.
By understanding these principles, manufacturers can refine their processes to produce high-quality, durable products. For further insights into mold design strategies, exploring innovative cooling systems6 can offer new perspectives.
Uniform wall thickness reduces stress concentration.True
Even distribution of material prevents localized stress, reducing cracking risk.
Sharp corners enhance product durability in molds.False
Sharp corners concentrate stress, increasing the likelihood of cracks.
Conclusion
By understanding the causes of debonding and cracks, you can implement effective strategies to enhance product quality and reliability.
-
Learn techniques for adjusting injection parameters for various materials.: By fine-tuning temperature, pressure, speed, and other key factors, you can achieve consistent, high-quality results while minimizing defects … ↩
-
Discover how thoughtful design influences injection molding outcomes.: Before you can manufacture a plastic part you need to have a solid design in place. Once done, you can build an injection mold to meet the product … ↩
-
Discover how precise control units enhance molding efficiency and product quality.: These benefits include precise temperature regulation, which in turn results in improved product quality and productivity. ↩
-
Understand how different materials affect product performance in injection molding.: Tough, stiff, hard, and strong. Good lubricity and resistance to hydrocarbons and organic solvents. Good elasticity, slippery. Low creep. Great fatigue … ↩
-
Discover how mold design impacts product quality and defect reduction.: Mike Baranoski, a Design Engineer at Rodon, discusses how his role and having a solid design are critical to the plastic injection molding process. ↩
-
Learn about cutting-edge cooling methods that improve mold efficiency.: The most representative ones are: pulse cooling technology, CO2 gas cooling technology and nano fluid cooling technology. This article will … ↩