Ever wondered why those pesky cold slugs keep showing up in your injection molding process?
Cold slugs in injection molding are due to material temperature inconsistencies, poor nozzle design, or improper mold cooling, leading to solidified material and affecting product quality.
I remember my early days in the mold industry, staring at a defective batch wondering where it all went wrong. Addressing cold slugs seems simple on paper, but in practice, it’s a tangled web of factors. Dive in with me as we explore the intricate causes, effective preventive strategies, and valuable tips to boost your injection molding process.
Cold slugs are caused by inadequate nozzle design.True
Inadequate nozzle design can lead to uneven material flow, causing cold slugs.
Cold slugs improve the quality of molded products.False
Cold slugs result in defects that degrade the quality of molded products.
- 1. How Does Material Temperature Affect Cold Slug Formation?
- 2. Why is Nozzle Design Crucial in Preventing Cold Slugs?
- 3. How Do Mold Cooling Systems Affect Cold Slug Issues?
- 4. How Do Process Parameters Impact Cold Slug Development?
- 5. What Material Choices Can Reduce Cold Slug Occurrence?
- 6. How Can I Effectively Tackle Cold Slugs in Production?
- 7. Conclusion
How Does Material Temperature Affect Cold Slug Formation?
Ever wondered how a tiny detail like material temperature can make or break your molding project? It might sound trivial, but it’s the unsung hero in crafting flawless plastic components.
Material temperature is crucial in injection molding, impacting the viscosity and flow of molten plastic. Lower temperatures boost viscosity, causing incomplete filling and cold slugs, while optimal temperatures improve flow and minimize defects.
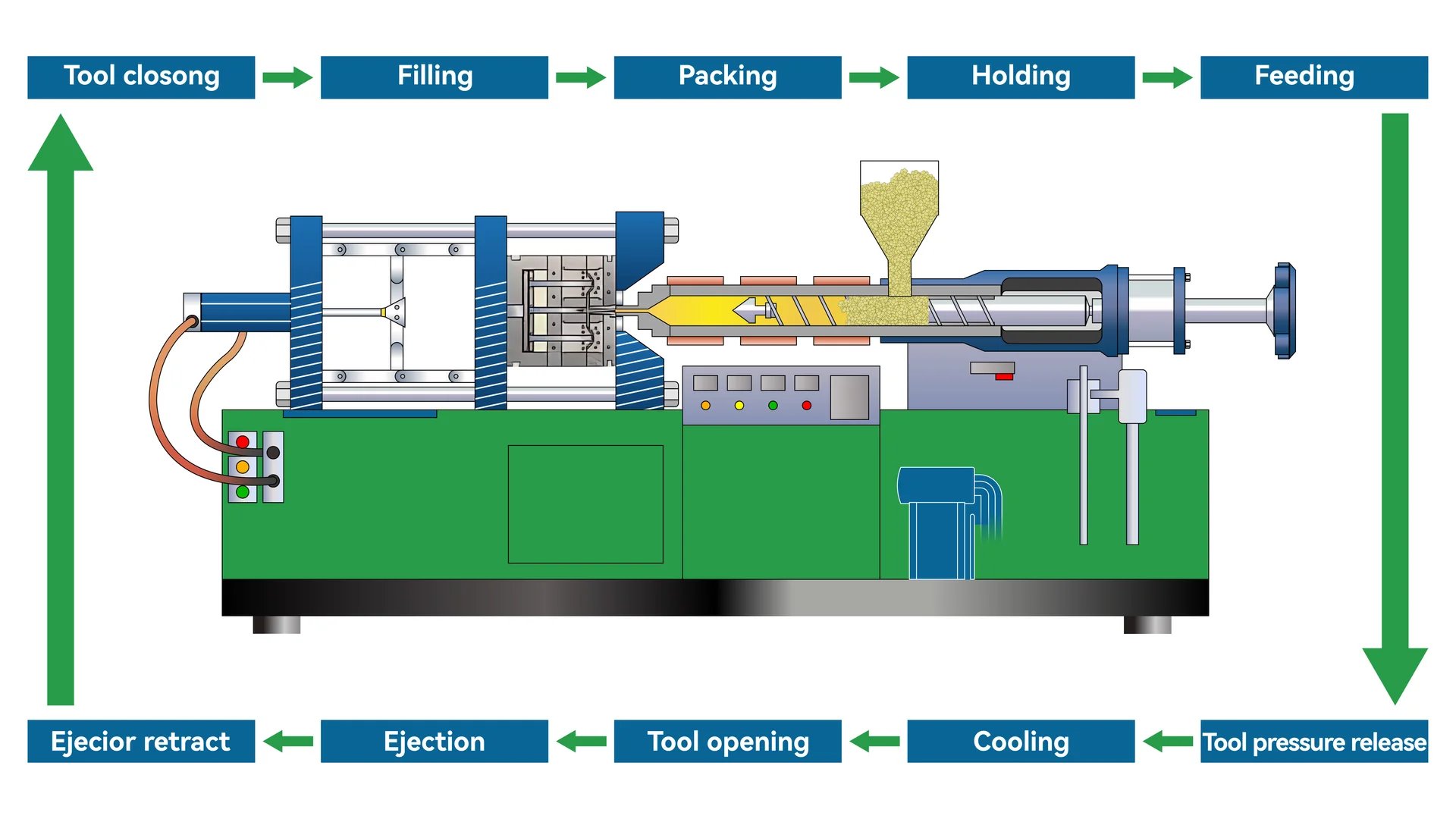
Understanding Cold Slug Formation
Picture this: you’ve meticulously designed a product, spent countless hours perfecting every curve, and then—bam! You’re faced with cold slugs disrupting your masterpiece. Cold slugs are those pesky solidified bits that sneak into the nozzle area, creating defects and ruining your day. They don’t just mess with the aesthetics; they can lead to significant issues in the mold cavity, affecting the overall quality of your product.
The Role of Material Temperature
Let’s dive deeper into this. You know how when you’re cooking, the right temperature can make or break a dish? Well, it’s similar here. Material temperature plays a starring role in injection molding by dictating the viscosity of the plastic1. When the temperature is too low, viscosity skyrockets, making the plastic thick and sluggish—like trying to pour molasses on a cold day. This results in incomplete filling of intricate mold parts, inevitably leading to cold slug formation. On the flip side, if it’s too hot, you’re looking at material degradation.
Temperature Range | Viscosity Effect |
---|---|
Low | High (Thicker Flow) |
Optimal | Balanced |
High | Low (Thinner Flow) |
Mitigating Cold Slug Formation
So, what’s the solution? It’s all about striking that perfect balance. Keeping an optimal temperature range is vital to mitigate cold slug formation. I often rely on temperature control systems2 to ensure consistency throughout the process. This not only reduces defects but also fortifies the structural integrity of our molded products.
Practical Adjustments for Designers
For those like me who live and breathe design, tools like simulation software3 are game-changers. These tools allow us to foresee how temperature changes affect slug formation before we even hit production, saving both time and precious resources.
Moreover, it’s crucial to understand how different materials with varying thermal properties behave under certain conditions. Selecting plastics that are less prone to forming cold slugs can be a real lifesaver in maintaining quality.
Lower material temperatures increase plastic viscosity.True
Lower temperatures cause plastic to thicken, increasing its resistance to flow.
High material temperature prevents cold slug formation.False
Excessive heat can degrade material properties, not necessarily preventing slugs.
Why is Nozzle Design Crucial in Preventing Cold Slugs?
Ever wondered how a tiny piece of plastic could throw off your whole design? Let’s dive into how nozzle design can be a game-changer in injection molding.
Nozzle design plays a pivotal role in preventing cold slugs by maintaining a consistent temperature and flow during injection molding, thereby reducing defects and enhancing part quality.
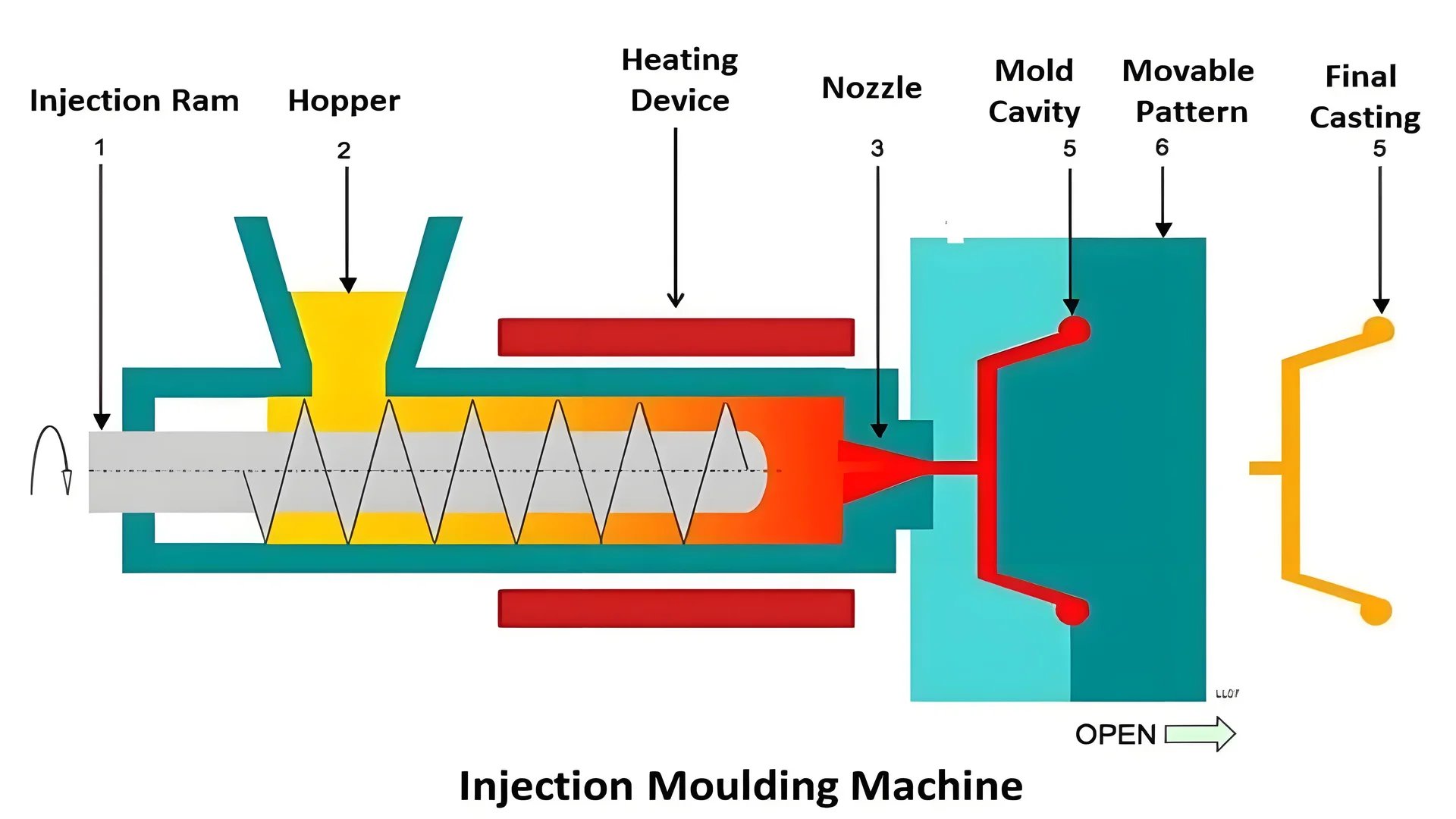
Understanding Cold Slugs
I remember the first time I encountered a cold slug; it was like finding a rogue puzzle piece in the perfect jigsaw of my design process. These hardened bits of plastic form when the material cools and solidifies too early in the nozzle. Not only do they create defects, but they can also derail the quality of the final product. That’s why nozzle design isn’t just a technical detail—it’s a critical element that manages both the flow and temperature of the plastic.
Key Features of Nozzle Design
The secret sauce to an effective nozzle is all about maintaining consistent heating and ensuring smooth flow. Imagine trying to pour syrup on your pancakes only to find it frozen halfway through—that’s what happens when there’s a cold spot in the nozzle. A heated nozzle tip or a streamlined internal structure can prevent such cold spots, keeping the plastic flowing like it should and minimizing the risk of cold slugs.
Nozzle Types and Their Impact
Choosing the right nozzle type is like selecting the perfect tool for a DIY project—each has its perks:
Nozzle Type | Benefits |
---|---|
Open Nozzle | Simplicity and ease of maintenance |
Shut-off Nozzle | Controls material flow precisely |
Hot Runner Nozzle | Maintains consistent temperature |
Each type is tailored for different needs, whether it’s the complexity of the mold design or the properties of the material you’re working with.
Factors Influencing Nozzle Performance
In my experience, getting nozzle performance right is like crafting a symphony where every instrument must play its part. It’s not just about design but also how well it integrates with the entire system. Here are some crucial considerations:
- Material Compatibility: Just like how some people need hypoallergenic products, certain plastics need specific nozzle materials to avoid degradation.
- Temperature Control: Imagine trying to bake without an oven thermometer—accurate temperature control is vital to prevent cold spots.
- Flow Rate: The speed of injection is key; think of it like driving a car—too fast or too slow, and you could end up in trouble.
Balancing these factors ensures your injection molding process hits all the right notes.
Exploring Real-world Applications
In one of the projects I worked on, switching to a hot runner nozzle system made all the difference. We were manufacturing automotive parts, and by ensuring better temperature consistency, we cut down defects significantly. This case study4 shows how thoughtful changes in nozzle design can lead to major boosts in product quality.
By exploring different nozzle designs and understanding their impact on cold slug prevention, I’ve found that it’s possible to achieve not just good but outstanding manufacturing results, especially in high-precision industries.
Heated nozzle tips prevent cold slugs effectively.True
Heated nozzle tips maintain consistent temperature, reducing solidification.
Open nozzles are best for controlling material flow.False
Shut-off nozzles are better suited for precise material flow control.
How Do Mold Cooling Systems Affect Cold Slug Issues?
Ever wondered if the cooling system in your mold could be the unsung hero or villain behind cold slug issues?
Yes, mold cooling systems can significantly influence cold slug issues by maintaining optimal temperature control. Proper cooling helps prevent cold slugs, which occur when molten plastic solidifies prematurely.
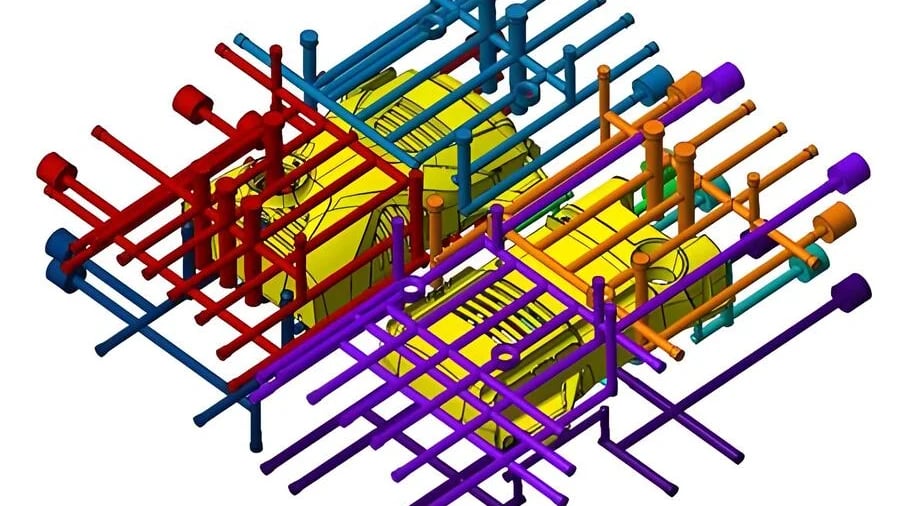
Understanding Cold Slugs and Their Formation
I remember the first time I encountered a cold slug issue in my mold design. It was frustrating. These defects form when molten plastic solidifies too soon during the injection process, often due to uneven or rapid cooling. I learned this the hard way while troubleshooting a batch of faulty components.
How Mold Cooling Systems Work
Mold cooling systems are like the thermostat of your home, circulating coolant through channels to regulate temperature. This helps in maintaining optimal temperature distribution5, crucial for reducing cold slug formation. I realized the importance of this when we upgraded our system and saw a noticeable improvement.
Factors Affecting Cooling Efficiency
- Channel Design: Imagine trying to cool a pie fresh out of the oven—efficient channel design works similarly, ensuring uniform cooling.
- Coolant Type: Whether you use water or oil as a coolant affects how quickly heat is transferred. It’s like choosing between a fan and an air conditioner on a hot day.
- Flow Rate: Just like increasing the water flow in your shower for a quicker rinse, higher flow rates improve cooling efficiency, preventing uneven cooling6.
Cooling System Aspect | Influence on Cold Slugs |
---|---|
Channel Layout | Uniformity in cooling |
Coolant Temperature | Rate of heat removal |
Material Conductivity | Heat distribution efficiency |
Impact of Cooling on Cold Slugs
Think of a well-designed cooling system as a master chef ensuring every part of your dish is cooked to perfection. It minimizes cold slugs by keeping the mold temperature consistent, preventing premature solidification and leading to smoother surfaces and stronger structures.
By focusing on these factors, designers like me can optimize mold designs and significantly reduce defects like cold slugs, enhancing product quality.
Innovative Cooling Techniques
I’ve been amazed by new technologies like conformal cooling, which allows for custom channels adapting to complex mold shapes. This innovation enhances heat dissipation7 and cooling efficiency, offering promising solutions to persistent cold slug issues.
Staying updated on these advancements is crucial for improving manufacturing processes and outcomes. Regularly reviewing technical resources and experimenting can lead to optimal solutions8 for maintaining product quality in injection molding.
Uneven cooling causes cold slug formation.True
Uneven cooling leads to premature solidification of plastic, forming cold slugs.
Faster coolant flow rates decrease cold slug risk.True
Higher flow rates improve cooling efficiency, reducing uneven temperature distribution.
How Do Process Parameters Impact Cold Slug Development?
Ever wondered why some molded parts just don’t turn out right? It’s often about those pesky cold slugs and the magic of process parameters.
Adjusting melt temperature, injection speed, and cooling time in injection molding can reduce cold slug defects and enhance product quality.
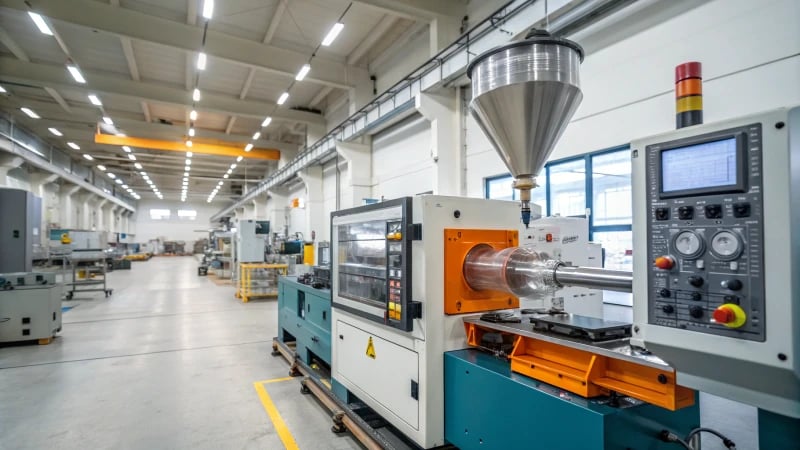
You know, there was a time when I first started working with injection molds, and everything seemed like a puzzle. I remember facing issues with cold slugs that felt like trying to solve a Rubik’s cube blindfolded. But over time, I learned that the key to success lay in understanding and controlling the process parameters. It’s not just about setting numbers; it’s about feeling the rhythm of the process.
The Role of Melt Temperature
Imagine you’re baking a cake, and the oven temperature is all over the place. That cake would be a disaster, right? The same goes for melt temperature in molding. If it’s too low, the material just sits there, refusing to flow properly, leading to unfilled cavities and those unwanted cold slugs. On the flip side, crank it up too high, and you risk burning the material. The sweet spot is where the magic happens—keeping the polymer at an ideal viscosity.
To achieve optimal results, monitor the melt temperature9 closely. Keeping it within recommended ranges ensures that the polymer maintains its ideal viscosity for proper filling.
Injection Speed Considerations
Think of injection speed like driving a car. Go too slow, and you might not reach your destination in time (in this case, filling the mold properly). But hit the pedal too hard, and you risk skidding off course with defects like flashing or burn marks.
Balancing injection speed is crucial. Refer to optimal speed guidelines10 for specific materials to find a sweet spot where flow meets quality requirements.
Cooling Time Adjustments
It’s a bit like waiting for your coffee to cool down before taking a sip. If you rush it, you’re bound to get burned or end up with cold slugs because the material hasn’t solidified enough. But wait too long, and you’re just wasting time.
Utilize a cooling time calculator11 to determine precise durations based on mold and material properties.
A Simple Parameter Table
Parameter | Effect on Cold Slugs |
---|---|
Melt Temperature | Low temps: increase |
High temps: degrade | |
Injection Speed | Too fast: defects |
Balanced: reduces | |
Cooling Time | Too short: increases |
Optimal: balances |
Understanding these nuances felt like unlocking a new level in my career. Addressing them meticulously can transform the injection molding process12 from frustrating to seamless. It’s like finding that missing piece of the puzzle that makes everything come together beautifully. This knowledge not only enhances product outcomes but also significantly cuts down on material waste.
High injection speed reduces cold slug formation.True
High speeds ensure quick mold filling, reducing cold slug risks.
Excessive cooling time increases cold slug defects.False
Excessive cooling prolongs cycles but does not increase cold slugs.
What Material Choices Can Reduce Cold Slug Occurrence?
Ever felt the frustration of a perfect design marred by cold slugs in injection molding? I know I have. Let’s explore how choosing the right materials can be a game-changer for quality and efficiency.
Using high-flow materials like polycarbonate and additives to reduce viscosity minimizes cold slug occurrence in injection molding, improving product quality and efficiency.
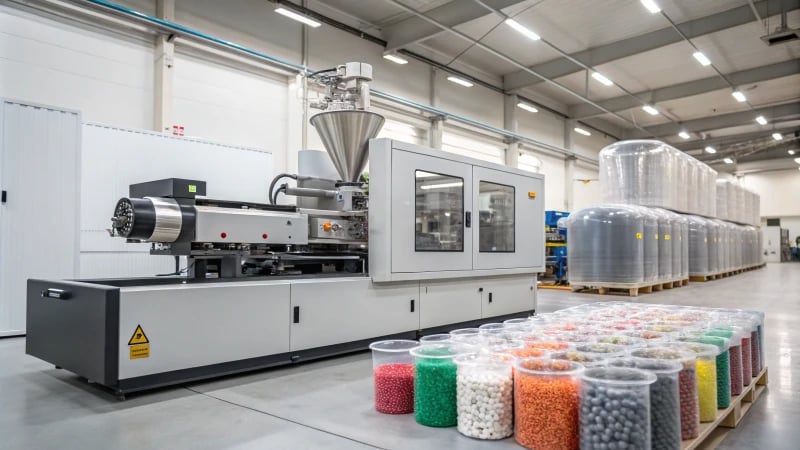
Understanding Cold Slugs
I still remember the first time I encountered cold slugs in my designs—those pesky solidified plastic residues ruining an otherwise flawless mold. Cold slugs form in the sprue or runner system during the injection molding13 process when the plastic cools too fast. The material’s flow characteristics are crucial in determining whether these defects will rear their ugly heads.
High-Flow Materials
From my experience, selecting high-flow materials like polycarbonate or certain grades of polypropylene can be a lifesaver. These materials allow the plastic to flow smoothly into every nook and cranny of the mold before solidifying. Here’s a table highlighting some high-flow options I’ve found effective:
Material | Flow Rate | Application |
---|---|---|
Polycarbonate | High | Electronics |
Polypropylene | Moderate | Packaging |
Choosing a high-flow material is like having a trusty sidekick that ensures your molten plastic fills even the most complex molds without leaving slugs behind.
Using Additives
Over the years, I’ve discovered that additives, especially plasticizers, can be the unsung heroes in this fight against cold slugs. They decrease the viscosity of plastics, making the flow smoother. This is particularly beneficial for molds with intricate designs or long flow paths. For example, adding plasticizers to PVC enhances its fluidity, reducing those annoying cold slug issues.
Material Optimization Techniques
But it’s not just about the materials; tweaking the molding conditions14 is just as critical. By adjusting temperature and pressure settings to suit specific materials, I’ve managed to further cut down on cold slug formation. For instance, increasing mold temperature for certain polymers has helped me achieve better flow and reduced solidification rates.
Exploring Innovative Material Solutions
I’m particularly excited about the potential of emerging materials like biodegradable plastics. Not only do they align with sustainability goals, but they might also offer unique flow properties that combat slug formation. Although research is ongoing, early findings are promising for both performance and environmental impact.
If you’re keen to see how these material choices could boost your production efficiency15, chatting with a materials scientist might provide some tailored insights. They can help align your design requirements with production goals, paving the way for more efficient manufacturing processes.
High-flow materials reduce cold slug formation.True
Materials with high flow rates reach all mold parts before solidifying.
Additives increase the viscosity of plastics.False
Additives like plasticizers decrease viscosity, aiding smoother flow.
How Can I Effectively Tackle Cold Slugs in Production?
Cold slugs in injection molding can be as pesky as that one mosquito that just won’t quit buzzing around your ear on a summer night.
To tackle cold slugs in production, optimize temperature controls, adjust injection speeds, ensure precise mold designs, and conduct regular maintenance.
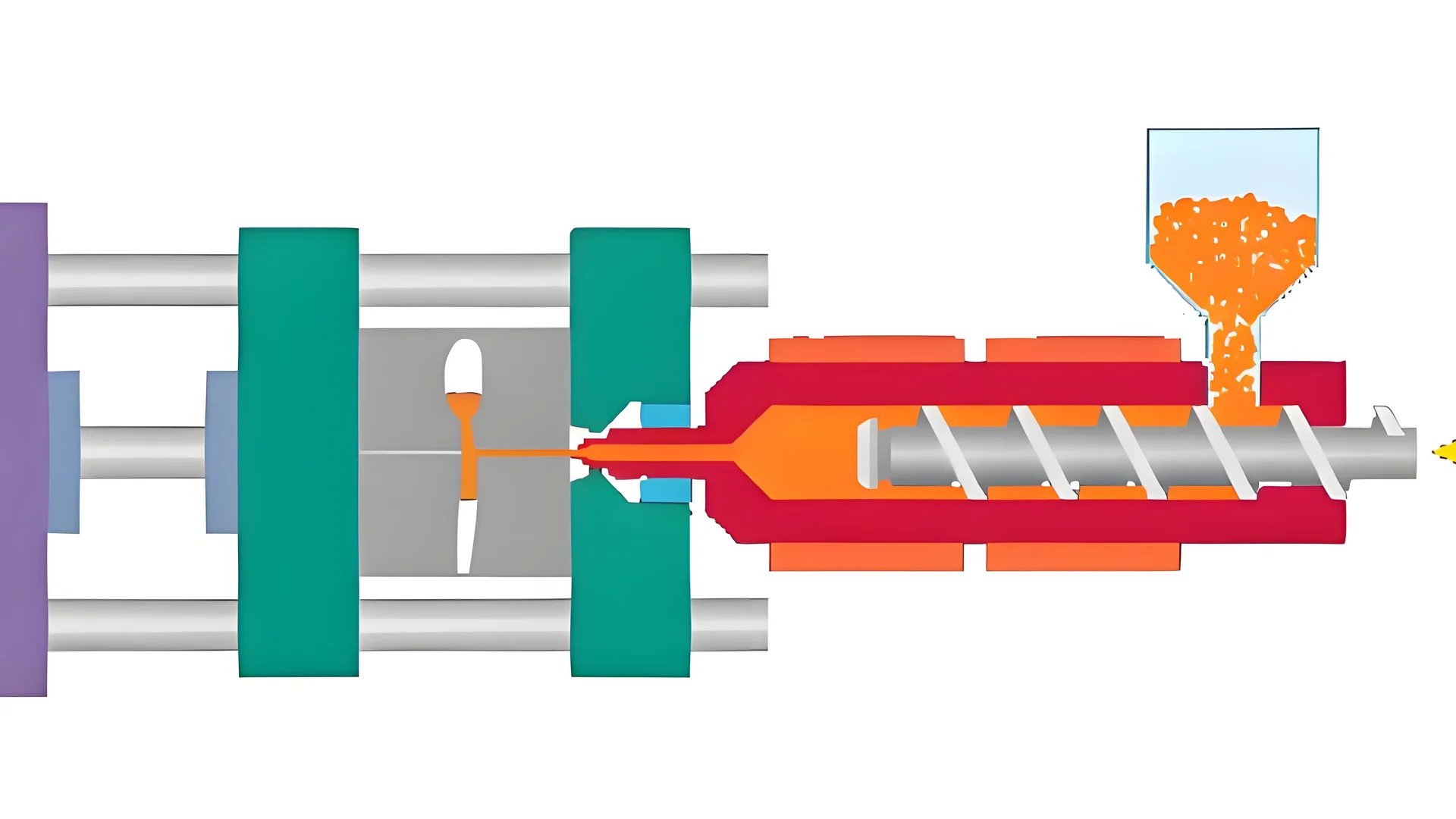
Understanding Cold Slugs
Let me paint you a picture: you’re in the middle of a production run, and everything seems to be going smoothly. Then, out of nowhere, those dreaded cold slugs pop up, leaving defects in their wake. It’s like planning a perfect road trip only to hit traffic at every turn. Cold slugs happen when cooled plastic sneaks into the mold cavity, causing those annoying voids and blemishes that mess with both the aesthetic16 and functional aspects of your product.
Temperature Control
Managing Mold and Barrel Temperatures
Here’s where I had an epiphany: keeping consistent temperatures is non-negotiable. I once thought I could wing it, but I learned the hard way that even minor fluctuations could lead to quality dips. Now, I’m all about using advanced temperature monitoring systems to keep things steady.
Table: Temperature Settings Guide
Component | Optimal Temperature Range |
---|---|
Mold | 20°C – 60°C |
Barrel | 180°C – 240°C |
Injection Speed Adjustment
I’ve found that dialing up the injection speed can be a game-changer. Imagine trying to keep a hot cup of coffee warm while standing outside in the cold—moving faster helps keep the temperature just right.
Mold Design Considerations
Incorporating Cold Wells
Picture this: cold wells are like little bouncers at a club, catching those unwanted cold slugs before they crash the party. A well-thought-out design can prevent these gatecrashers from marring the finish of your products.
Table: Cold Well Effectiveness
Mold Feature | Impact on Quality |
---|---|
Cold Wells | Significant |
No Cold Wells | Minimal |
Regular Maintenance and Inspection
Remember when I thought skipping regular maintenance was no biggie? Yeah, I paid for that mistake. Routine check-ups are like going to the dentist—painful if avoided too long. Regular inspections17 can catch wear and tear before they spiral into bigger issues.
Conclusion Placeholder (Avoid adding here)
Through trial and error, I’ve learned that mastering these strategies takes more than just understanding machinery—it’s about knowing the materials and process inside out. With a focus on temperature control, mold design, and maintenance, I’ve seen firsthand how production quality can soar.
Cold slugs can cause surface blemishes in plastic parts.True
Cold slugs occur when cooled plastic enters the mold, causing defects.
Adjusting injection speed has no effect on cold slugs.False
Faster injection speeds help maintain plastic temperature, reducing cold slugs.
Conclusion
Cold slugs in injection molding arise from temperature inconsistencies, poor nozzle design, and mold cooling issues. Effective strategies include optimizing temperatures, adjusting speeds, and maintaining equipment.
-
Understanding how viscosity affects defects can help optimize mold design and material choice. ↩
-
Temperature control systems enhance product quality by maintaining consistent temperatures. ↩
-
Simulation software helps foresee potential issues and allows for pre-production adjustments. ↩
-
Read about real-world examples where hot runner systems improved production efficiency and reduced defects. ↩
-
Discover how temperature distribution impacts the cooling efficiency and quality of molded products. ↩
-
Learn about the consequences of uneven cooling on molded parts and how to address them. ↩
-
Explore recent innovations that enhance heat dissipation in mold designs. ↩
-
Uncover effective strategies and solutions for preventing cold slug issues in injection molding. ↩
-
Discover recommended melt temperature ranges for different polymers to ensure proper material flow. ↩
-
Find guidelines on setting appropriate injection speeds to reduce defects and enhance mold filling efficiency. ↩
-
Learn how to calculate precise cooling times to ensure optimal solidification without prolonging cycle durations. ↩
-
Explore methods for optimizing injection molding processes to improve efficiency and product quality. ↩
-
Learn about the injection molding process, which is crucial for understanding cold slug formation and prevention strategies. ↩
-
Find out how adjusting molding conditions can reduce defects and improve product quality. ↩
-
Explore how selecting the right materials can enhance production efficiency and reduce defects. ↩
-
Discover how aesthetic considerations impact product design and user satisfaction in injection molding. ↩
-
Learn why regular inspections are vital for maintaining equipment efficiency and preventing defects in production. ↩