Have you ever held a plastic product only to find rough edges or unexpected flaws? Those annoying burrs might be more than just a cosmetic issue; they can impact functionality too!
Burrs in injection molded products are primarily caused by issues with the mold’s parting surface precision, excessive injection pressure, high material temperature, and insufficient clamping force. Addressing these factors can significantly reduce the occurrence of burrs.
But hold on! Before we dive deeper, let’s explore why understanding these factors is not just beneficial—it’s essential for enhancing your manufacturing process.
Excessive injection pressure causes burrs in molded products.True
High pressure exceeds mold's sealing capacity, leading to burrs.
How Does Mold Design Influence Burr Formation?
Burr formation in injection molding can often be traced back to the intricacies of mold design, significantly impacting product quality.
Mold design plays a critical role in burr formation during injection molding. Key factors include the precision of the mold’s parting surface, the alignment of mold components, and the overall integrity of the mold structure. Addressing these elements can help minimize burr occurrence.
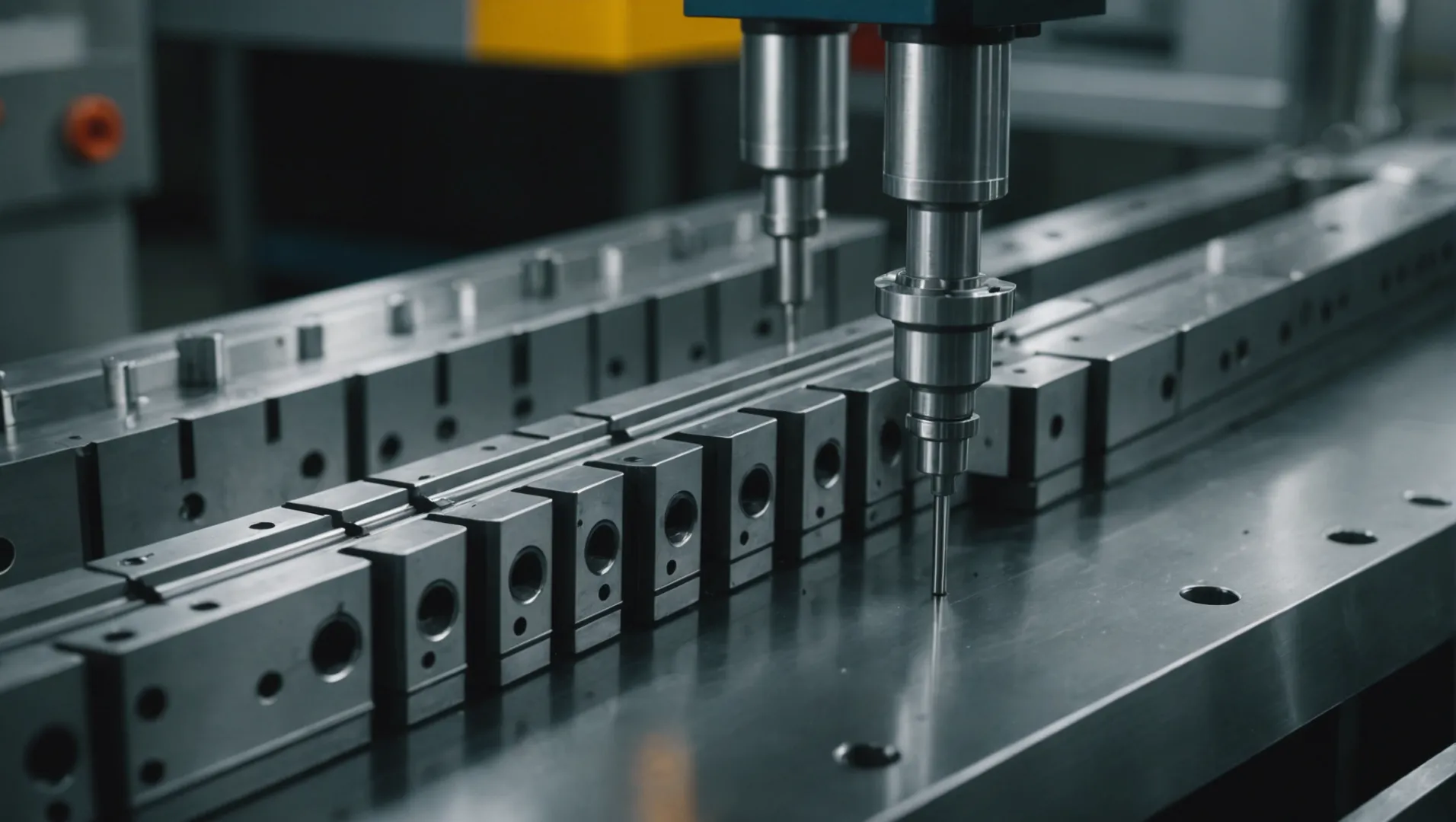
Precision of the Mold Parting Surface
The precision of the mold’s parting surface1 is pivotal in preventing burrs. A rough or damaged surface allows molten plastic to escape during injection, creating unwanted burrs. Over time, wear and tear can increase this gap, exacerbating the issue. Regular inspection and maintenance of the parting surfaces are crucial to maintain their integrity.
Importance of Mold Assembly
Improper mold assembly2 is another significant contributor to burr formation. If there’s a lack of parallelism between templates or if screws are not adequately tightened, gaps appear. These gaps become pathways for plastic under high pressure, leading to burr formation. Ensuring precise assembly of all components, including inserts and sliders, helps in mitigating this risk.
Role of Mold Material and Design
The choice of materials used for mold construction can also influence burr formation. Molds made from materials prone to deformation under stress can lead to increased gaps at parting lines. Additionally, complex designs with numerous movable parts like slides and lifters may introduce more opportunities for misalignment and potential burrs.
Mold Design Factor | Influence on Burr Formation |
---|---|
Parting Surface | Rough surfaces increase burr risk |
Mold Assembly | Misalignment creates gaps |
Mold Material | Deformation under stress increases gap |
Long-Term Use and Maintenance
Over time, molds can degrade due to repeated use. This degradation can manifest as increased gap size or surface roughness, both contributing to burr formation. Regular maintenance, including resurfacing or replacing worn components, is vital to prolonging mold life and maintaining product quality.
By addressing these key elements in mold design, manufacturers can significantly reduce the incidence of burrs, ensuring higher quality products and more efficient production processes.
Rough parting surfaces increase burr risk.True
Rough surfaces allow molten plastic to escape, causing burrs.
Mold material choice doesn't affect burr formation.False
Materials prone to deformation can lead to increased gaps.
What Role Does the Injection Molding Process Play in Creating Burrs?
The injection molding process can significantly impact the formation of burrs, a prevalent issue that can compromise product quality and functionality.
Burrs during injection molding arise mainly from excessive injection pressure, fast injection speed, high material temperature, and prolonged holding time. By optimizing these parameters, manufacturers can effectively minimize burr formation.
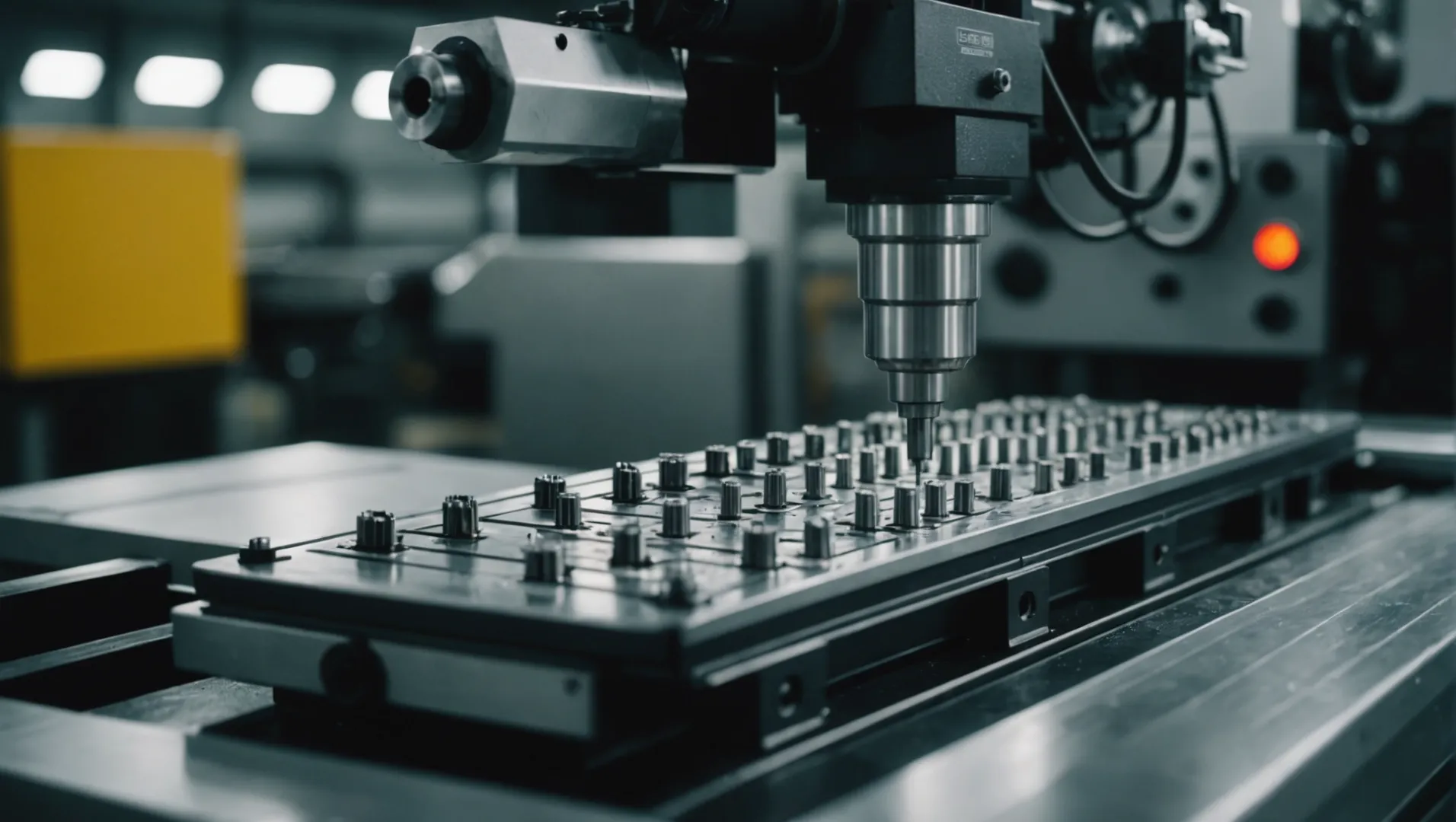
Excessive Injection Pressure
Excessive injection pressure is a leading cause of burr formation during the injection molding process3. When the molten plastic is injected with too much force, it may surpass the mold’s sealing capacity, leading to overflow and burrs. Additionally, high pressure can deform the mold, further widening gaps at the parting surfaces.
- Impact: Increased extrusion force of molten plastic.
- Solution: Adjust injection pressure to match mold capacity.
Too Fast Injection Speed
A rapid injection speed can cause the molten plastic to flow too quickly, increasing the impact force within the mold. This scenario may lead to high instantaneous pressures, pushing plastic through any available gaps and creating burrs.
- Impact: Increased flow speed and impact force.
- Solution: Reduce injection speed for controlled flow.
High Material Temperature
When the plastic’s melting temperature is too high, its fluidity increases while viscosity decreases. This makes it easier for the plastic to seep through any mold gaps. Moreover, elevated temperatures can cause plastic decomposition, generating gas and increasing internal pressure.
- Impact: Enhanced fluidity and reduced viscosity.
- Solution: Maintain optimal melting temperatures.
Parameter | Effect on Burr Formation |
---|---|
High Injection Pressure | Causes overflow and mold deformation |
Fast Injection Speed | Elevates flow speed and impact force |
High Material Temperature | Increases fluidity and gas formation |
Prolonged Holding Time or High Holding Pressure
The holding stage compensates for cooling shrinkage by maintaining pressure within the mold. However, excessively long holding times or high pressures can sustain high internal pressures, facilitating burr creation.
- Impact: Sustained high pressure within the mold.
- Solution: Optimize holding time and pressure levels.
By understanding and optimizing these aspects of the injection molding process, manufacturers can better control burr formation and enhance product quality. Further exploration into effective injection molding strategies4 can provide deeper insights into achieving superior outcomes.
Excessive injection pressure causes burrs.True
High pressure exceeds mold capacity, causing overflow and burrs.
Low material temperature increases burr formation.False
High, not low, material temperature enhances fluidity, causing burrs.
How Do Plastic Material Properties Affect Burr Development?
Understanding how plastic material properties influence burr development can transform your manufacturing process, leading to smoother, defect-free products.
Plastic material properties affect burr development primarily through fluidity and the presence of impurities or moisture. High fluidity allows plastic to seep through mold gaps, causing burrs, while impurities can lead to gas formation, increasing pressure and promoting burrs.
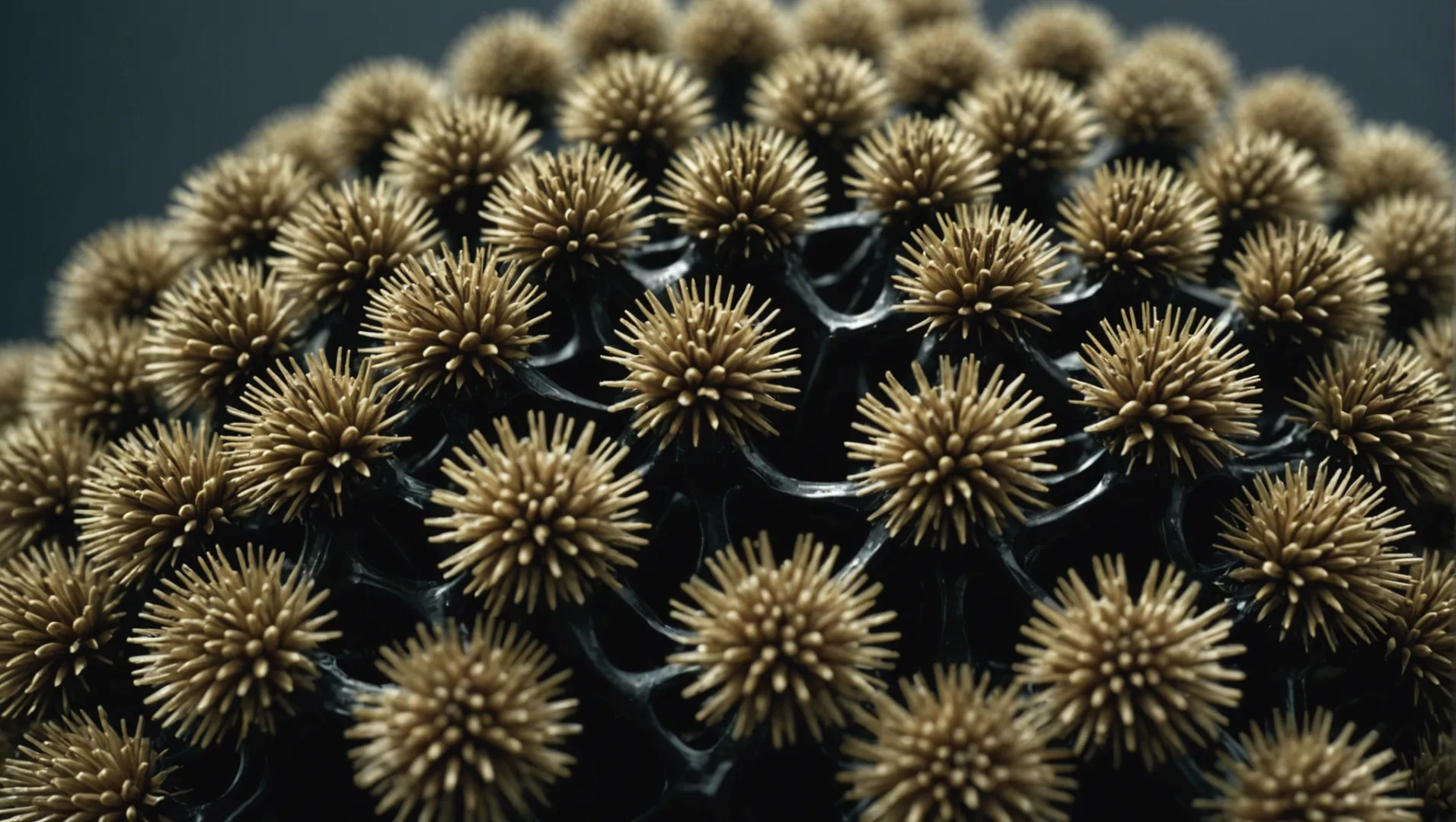
The Role of Fluidity in Burr Formation
Plastic fluidity significantly impacts burr development. High fluidity plastics can more easily flow through gaps in the mold, which are inevitable due to design or wear. This can lead to excessive overflow and burr formation. For instance, plastics with low viscosity, such as polyamide, are more prone to creating burrs when not carefully managed.
Plastic Type | Fluidity Level | Burr Risk |
---|---|---|
Polyamide | High | High |
Polyethylene | Medium | Moderate |
PVC | Low | Low |
Selecting materials with appropriate fluidity levels is crucial in minimizing burr occurrence. It’s also essential to consider the specific application needs, as different products may require varying material properties.
Impurities and Moisture Impact
Another critical factor is the presence of impurities or moisture in plastic materials. These contaminants can cause gas generation during the injection molding process, leading to increased internal pressure and eventual burrs.
For example, improperly dried plastics can retain moisture that vaporizes during molding, creating pressure spikes that cause molten plastic to escape through tiny mold gaps.
Material Selection Strategies
To mitigate burr development, it’s important to select materials with suitable properties. Understanding the material’s characteristics, such as melting temperature and viscosity, is essential. For example, choosing grades of plastic that suit the product’s complexity and design can help minimize defects.
When selecting materials, consider:
- The product’s required durability and flexibility.
- Environmental conditions the product will be exposed to.
- The dimensional accuracy needed for the final product.
By focusing on these factors, manufacturers can reduce burr formation and improve product quality. Implementing stringent material selection criteria and quality checks can lead to significant improvements in the manufacturing process.
The Role of Testing and Quality Assurance
Regular testing for fluidity and impurity levels is crucial in maintaining quality control. Implementing a robust QA process helps in identifying problematic batches before they cause issues on the production line.
Learn more about quality testing for plastics5
Moreover, conducting trials with different plastic grades can provide insights into optimal material choices for specific applications, reducing long-term costs associated with rework and scrap losses.
Explore advanced testing methods for plastic material properties6
High fluidity plastics increase burr risk.True
High fluidity allows plastic to seep through mold gaps, forming burrs.
Impurities in plastic reduce burr formation.False
Impurities cause gas formation, increasing pressure and promoting burrs.
Can Equipment Maintenance Reduce Burr Occurrence?
Equipment maintenance plays a crucial role in minimizing burrs in injection molded products, ensuring higher quality and efficiency.
Regular maintenance of injection molding equipment can prevent burrs by ensuring optimal clamping force, maintaining precision, and avoiding machine wear. This proactive approach minimizes downtime and enhances product quality.
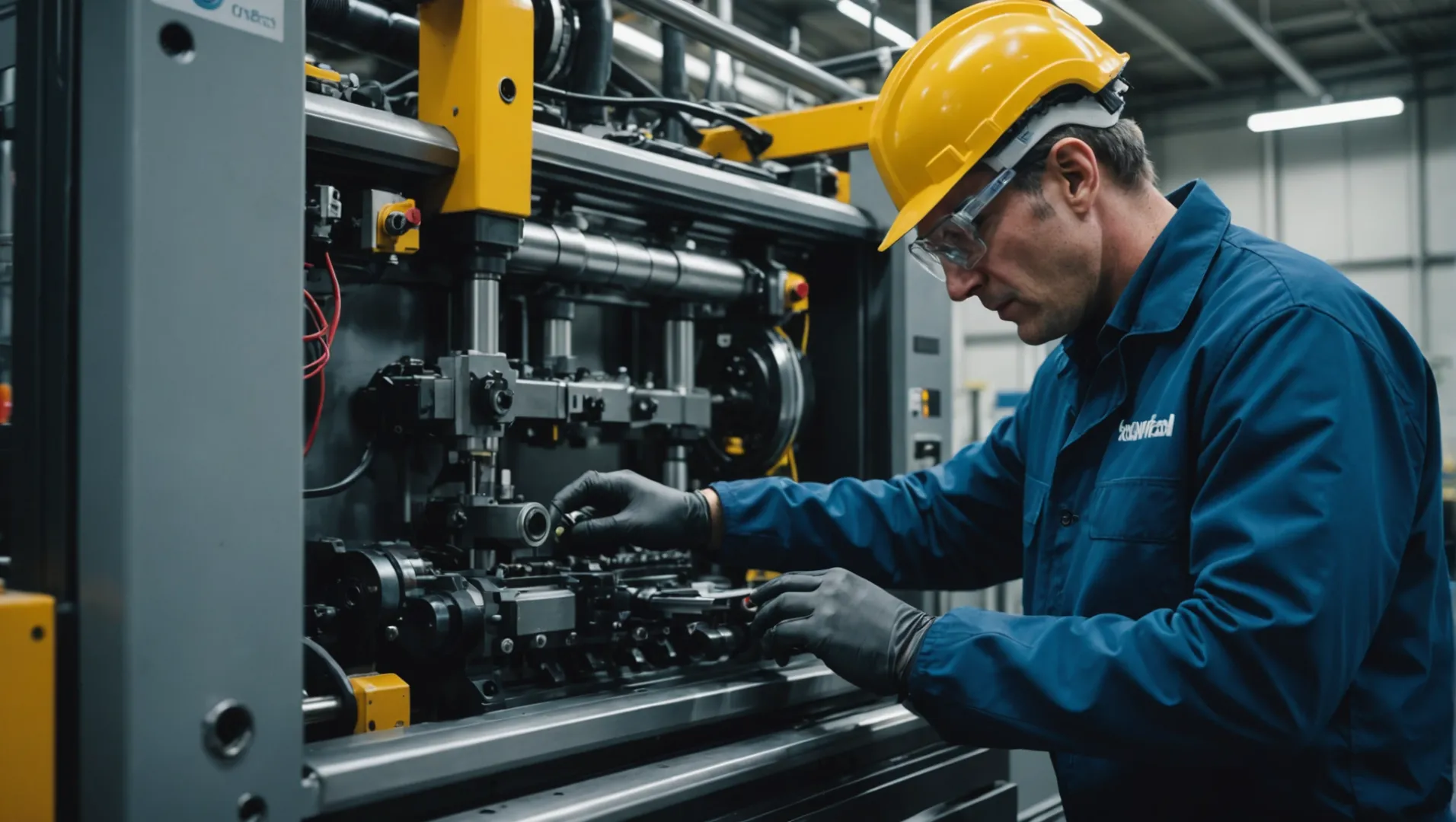
The Importance of Clamping Force
One of the primary responsibilities of equipment maintenance is to ensure that the injection molding machine provides sufficient clamping force. When the clamping force is inadequate, molds can stretch open under injection pressure, leading to gaps at the parting surfaces and resultant burrs.
Routine checks should be performed to ensure the machine’s clamping unit operates efficiently. Adjustments based on the projected area of the product and the injection pressure are vital to maintain optimal clamping force.
Precision in Machine Components
Precision problems with parts such as pull rods and templates can lead to non-parallel mold alignment, increasing burr formation risks. Regular calibration and precision checks help maintain component accuracy.
Investing in high-precision components and conducting periodic assessments can prevent misalignment issues. This practice reduces wear and maintains consistent quality across production runs.
Addressing Wear and Tear
Injection molding machines undergo significant stress during production, resulting in wear over time. Regular maintenance helps identify worn-out parts, like seals or hydraulic systems, that may compromise machine performance.
A comprehensive maintenance schedule should include inspections of movable parts like inserts and sliders. This approach ensures these components function correctly without introducing additional gaps that could cause burrs.
Implementing a Maintenance Schedule
Developing a structured maintenance plan tailored to the specific needs of your machinery is crucial. The plan should include:
- Daily Inspections: Checking for visible wear or damage in key components.
- Weekly Reviews: Verifying clamping force and machine calibration.
- Monthly Audits: Comprehensive checks on alignment and precision.
- Bi-Annual Overhaul: In-depth maintenance involving disassembly and part replacement if necessary.
By following these guidelines, manufacturers can effectively reduce burr occurrence. This strategy not only improves product quality but also extends machine lifespan, offering long-term cost savings.
To further understand how regular maintenance impacts manufacturing processes, explore maintenance strategies for injection molding7 or common equipment failures8.
Regular maintenance prevents burrs in injection molding.True
Maintenance ensures optimal clamping force and precision, reducing burrs.
Inadequate clamping force causes more burrs in molded products.True
Insufficient force allows molds to open, leading to gaps and burrs.
Conclusion
By tackling mold precision, process parameters, and equipment functionality, we can significantly reduce burr occurrences, enhancing overall product quality.
-
Learn why precision is crucial for reducing burrs in molding.: The parting surfaces provide support to the mold during the injection process and help to distribute the molten plastic evenly. It is important … ↩
-
Explore how precise assembly reduces burrs during molding.: The quality of your injection-molded product can be influenced by the design of the mold, the wall thickness of the end-product, type of runner, and even the … ↩
-
Learn how excessive pressure affects product quality and causes burrs.: Three, high injection pressure can force the mold open at the parting line. This creates flashing on the part, but more importantly, it can … ↩
-
Discover strategies to optimize molding processes and minimize burr formation.: Reducing injection pressure or increasing clamping force can eliminate this defect. It is sometimes very effective to switch to low-pressure … ↩
-
Discover effective methods for ensuring plastic quality control.: Ultrasonic inspection is a way to detect flaws in the material. This is a more intensive test, requiring a source of high-frequency sound waves. ↩
-
Learn about innovative testing techniques to enhance material selection.: Tensile Testing · Compression Testing · Flexural Testing · Impact Testing · Hardness Testing · Melt Flow Index (MFI) Testing · Differential Scanning … ↩
-
Discover effective maintenance plans that reduce equipment-related burrs.: 1. Keep Molds and Components Clean and Dry 2. Perform Safety Checks 3. Ensure Your Machine Is Level and Parallel 4. Check Your Oil 5. Check Electrical … ↩
-
Learn about frequent issues and preventative measures for your machines.: 11 Injection Molding Defects and Troubleshooting · Short Shot · Flash · Sink Marks · Splay Marks · Warpage · Burn Marks · Voids · Bubbles. ↩