Air bubbles in injection molding can be a manufacturer’s nightmare, affecting the quality and integrity of plastic parts. Understanding their causes is essential to improving production efficiency.
Air bubbles in injection molding are primarily caused by excessive moisture in raw materials, poor plastic fluidity, rapid injection speed, low pressure, and improper equipment settings. Addressing these issues can significantly enhance the quality of molded products.
While understanding these causes is a significant first step, effectively addressing each one requires a deeper dive into the specifics of materials, processes, and equipment involved in injection molding. Let’s explore how each factor contributes to air bubble formation and discover actionable solutions.
Excessive moisture in raw materials causes air bubbles.True
Moisture in materials vaporizes during molding, forming bubbles.
How Do Raw Materials Affect Bubble Formation?
Understanding how raw materials contribute to bubble formation in injection molding is crucial for quality control.
Raw materials can affect bubble formation due to moisture absorption and volatile components. Materials like polyamide and polycarbonate, if not adequately dried, introduce moisture that turns into gas during molding, forming bubbles. Additionally, poor plastic fluidity leads to uneven flow and encapsulation of air, increasing bubble occurrence.

Moisture and Volatiles: The Silent Culprits
In the world of injection molding1, raw materials play a pivotal role in determining the final product’s quality. One major issue is excessive moisture or volatile components present in these materials. Polymers like polyamide (PA) and polycarbonate (PC) are known for their high water absorption rates. If these materials are not thoroughly dried before the molding process, the absorbed moisture will vaporize under the high temperatures used in molding. This vaporization results in gas pockets, which manifest as bubbles in the final product.
For instance, consider a scenario where polycarbonate is stored in a humid environment before use. Upon heating, the absorbed moisture turns into steam, leading to bubble formation within the melt. This problem highlights the need for stringent storage conditions and pre-processing drying.
Fluidity and Flow Dynamics
Another critical factor affecting bubble formation is the plastic’s fluidity. High-viscosity materials or those processed at lower temperatures exhibit reduced fluidity. This reduction causes uneven flow patterns, leading to localized turbulence or eddy currents within the mold cavity.
Imagine injecting high-viscosity plastic into a complex mold. As the material struggles to fill intricate sections uniformly, it traps air in certain areas, forming bubbles. This scenario underscores the importance of selecting appropriate materials and adjusting processing parameters to enhance flow characteristics.
Influence of Material Selection on Flow
When choosing raw materials for injection molding, considering their flow properties is essential. The table below illustrates how different materials respond to varying temperatures and their typical fluidity levels:
Material | Temperature Range (°C) | Fluidity Level |
---|---|---|
Polyamide (PA) | 220-280 | Moderate |
Polycarbonate | 230-300 | Moderate |
Polyethylene | 180-240 | High |
Polystyrene | 190-250 | High |
Selecting materials with high fluidity can minimize the risk of air entrapment during the molding process. However, it’s also crucial to balance other properties such as mechanical strength and thermal stability.
Practical Solutions for Reducing Bubbles
To mitigate bubble formation due to raw material issues, several strategies can be employed:
- Pre-drying: Implementing thorough drying procedures for moisture-sensitive materials like PA and PC before processing.
- Material Selection: Choosing polymers with inherently better fluidity or modifying process temperatures to enhance flow.
- Environmental Control: Storing raw materials in controlled environments to prevent moisture absorption.
By focusing on these strategies, manufacturers can significantly reduce the incidence of bubbles, thereby improving product quality and reducing waste.
Polyamide absorbs moisture, causing bubbles in molding.True
Polyamide's high water absorption leads to vaporization and bubble formation.
High fluidity materials increase bubble occurrence in molds.False
High fluidity reduces air entrapment, decreasing bubble formation.
What Role Does Injection Speed Play in Air Bubble Generation?
Injection speed is a critical factor in the molding process, influencing the formation of air bubbles. Understanding its role can help in optimizing product quality.
Injection speed affects air bubble generation by influencing how the melt fills the mold cavity. Too fast or too slow speeds can trap air, leading to bubble formation. Adjusting speed appropriately can minimize defects.
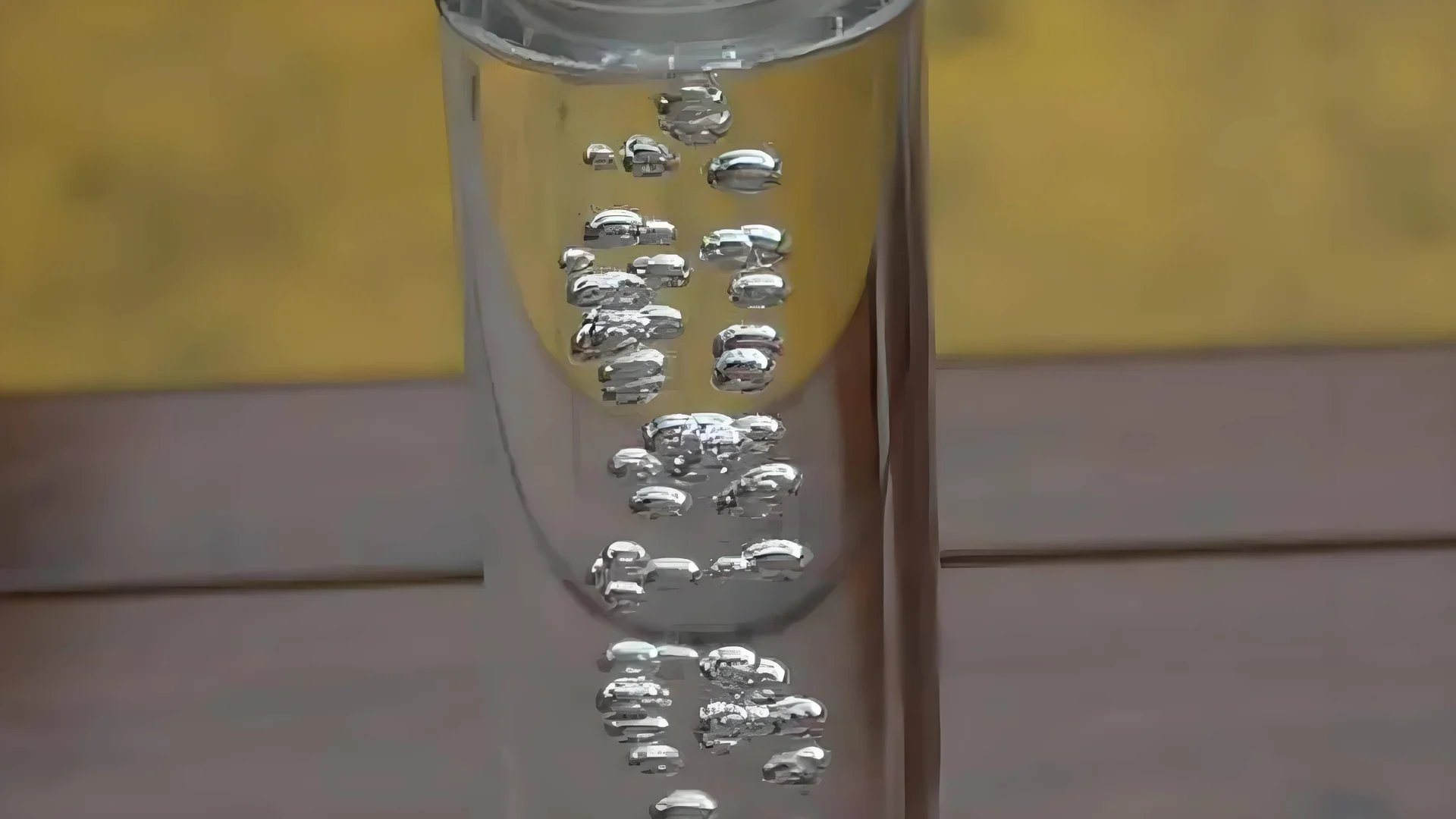
The Impact of High Injection Speed
High injection speed is often used to quickly fill molds, especially for thin-walled products. However, this rapid filling can lead to air entrapment within the melt, resulting in bubble formation. When the injection speed is too fast, the material rushes into the mold cavity, trapping air pockets that fail to escape before solidification occurs.
Example Scenario: In high-speed injection molding of thin-walled components, the quick filling process does not allow adequate time for air evacuation, causing bubbles. This is particularly problematic when producing parts that require transparency or a flawless finish.
Balancing Speed with Mold Design
The design of the mold, including venting systems, plays a crucial role in how well it can accommodate various injection speeds. Proper venting helps in releasing trapped air effectively. However, even with a well-designed mold, excessive speed can overwhelm the system.
Example Insight: When molds have insufficient vents or improperly designed exhaust systems, increasing injection speed exacerbates the issue by trapping more air than can be vented out efficiently.
To explore effective mold venting strategies, check out mold venting techniques2.
Influence of Material Properties
Material properties, such as viscosity, also interact with injection speed to influence bubble formation. High-viscosity materials are less forgiving at high speeds as they do not flow as smoothly, increasing the likelihood of encapsulating air.
Expert Tip: For materials with poor fluidity, consider reducing injection speed to enhance flow consistency and minimize bubble formation.
For detailed insights on material selection and fluidity impact, see material viscosity and flow3.
Optimizing Injection Speed: A Key Consideration
Finding the optimal injection speed requires balancing several factors: material characteristics, mold design, and desired product attributes. Adjusting these variables helps in minimizing defects like bubbles while maintaining production efficiency.
A well-adjusted injection speed not only enhances product quality but also reduces waste and rework efforts. For specific adjustments and optimization techniques, refer to injection speed optimization4.
High injection speed can trap air, causing bubbles.True
Rapid filling doesn't allow air to escape, leading to entrapment.
Proper mold design negates the need for speed adjustments.False
Even with good design, excessive speed can still trap air.
How Can Equipment Design Lead to Defects?
The design of injection molding equipment plays a crucial role in the quality of molded products. Poorly designed equipment can lead to various defects, including air bubbles, which compromise product integrity.
Defects in injection molding are often linked to equipment design flaws, such as inadequate screw parameters or insufficient clamping force. These issues can cause air entrapment, leading to defects like bubbles in the final product. Proper equipment calibration is key to minimizing these defects.
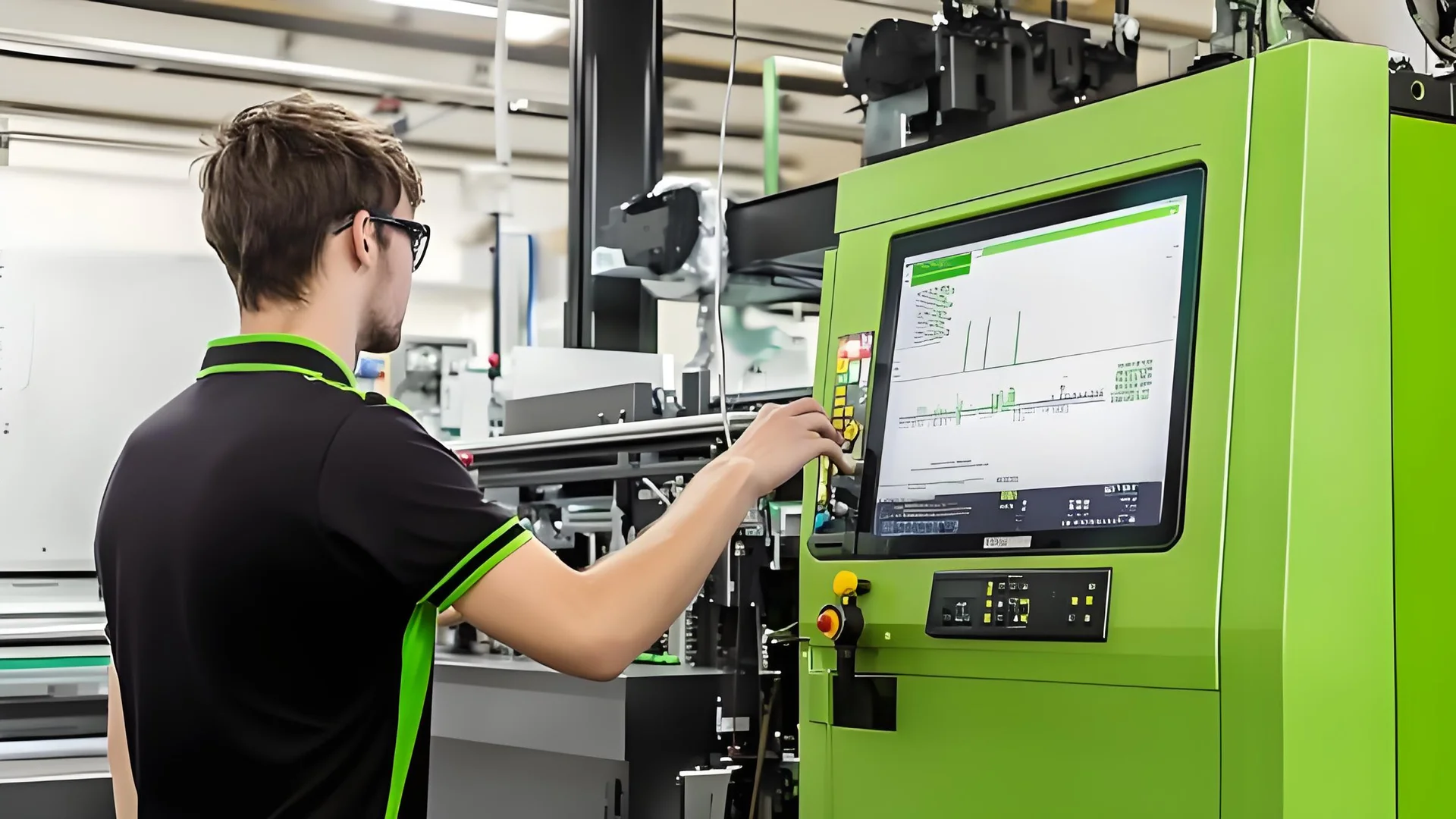
The Impact of Screw Design
The screw design5 within an injection molding machine is paramount for ensuring proper plasticization and mixing of raw materials. A poorly designed screw may not adequately melt the plastic, causing air to become trapped and forming bubbles. For example, plastics with high additives require screws with specific compression ratios to avoid uneven melting.
- Compression Ratio: Affects how tightly the plastic is compressed, influencing melt uniformity.
- Aspect Ratio: Determines the screw’s ability to mix and convey the plastic effectively.
A well-designed screw will ensure a homogeneous melt, reducing the risk of air entrapment.
Clamping Force and Mold Integrity
Insufficient clamping force6 can lead to mold defects. During the injection process, if the clamping force isn’t strong enough, the mold may slightly open, allowing air to be trapped in the cavity. This is particularly problematic for large or complex molds.
- Mold Bulging: Occurs when clamping is inadequate, leading to poor part quality.
- High Injection Pressure: Requires robust clamping to maintain mold integrity.
Ensuring sufficient clamping force aligns the mold halves perfectly, preventing air pockets and associated defects.
Exhaust System Efficiency
The efficiency of the mold’s exhaust system can significantly affect defect formation. Poorly designed or blocked exhaust channels mean that air cannot escape the mold cavity efficiently, leading to bubble formation.
- Exhaust Grooves and Holes: Need precise placement to facilitate air escape at strategic points.
- Maintenance: Regular cleaning and inspection of exhaust systems prevent blockages that cause defects.
By optimizing these aspects of equipment design, manufacturers can greatly reduce the incidence of air bubbles and other injection molding defects.
Screw design affects air bubble formation.True
Proper screw design ensures uniform plastic melting, reducing air entrapment.
Inadequate clamping force prevents mold integrity.True
Insufficient clamping force allows molds to open, trapping air inside.
What Preventative Measures Can Be Taken to Avoid Air Bubbles?
Preventing air bubbles in injection molding is crucial for producing high-quality plastic parts. By focusing on material preparation, process optimization, and equipment maintenance, manufacturers can significantly reduce the occurrence of these defects.
To avoid air bubbles in injection molding, ensure materials are properly dried, optimize injection speed and pressure, maintain precise mold temperatures, and regularly inspect equipment. These measures can drastically improve the quality of molded products by minimizing bubble formation.
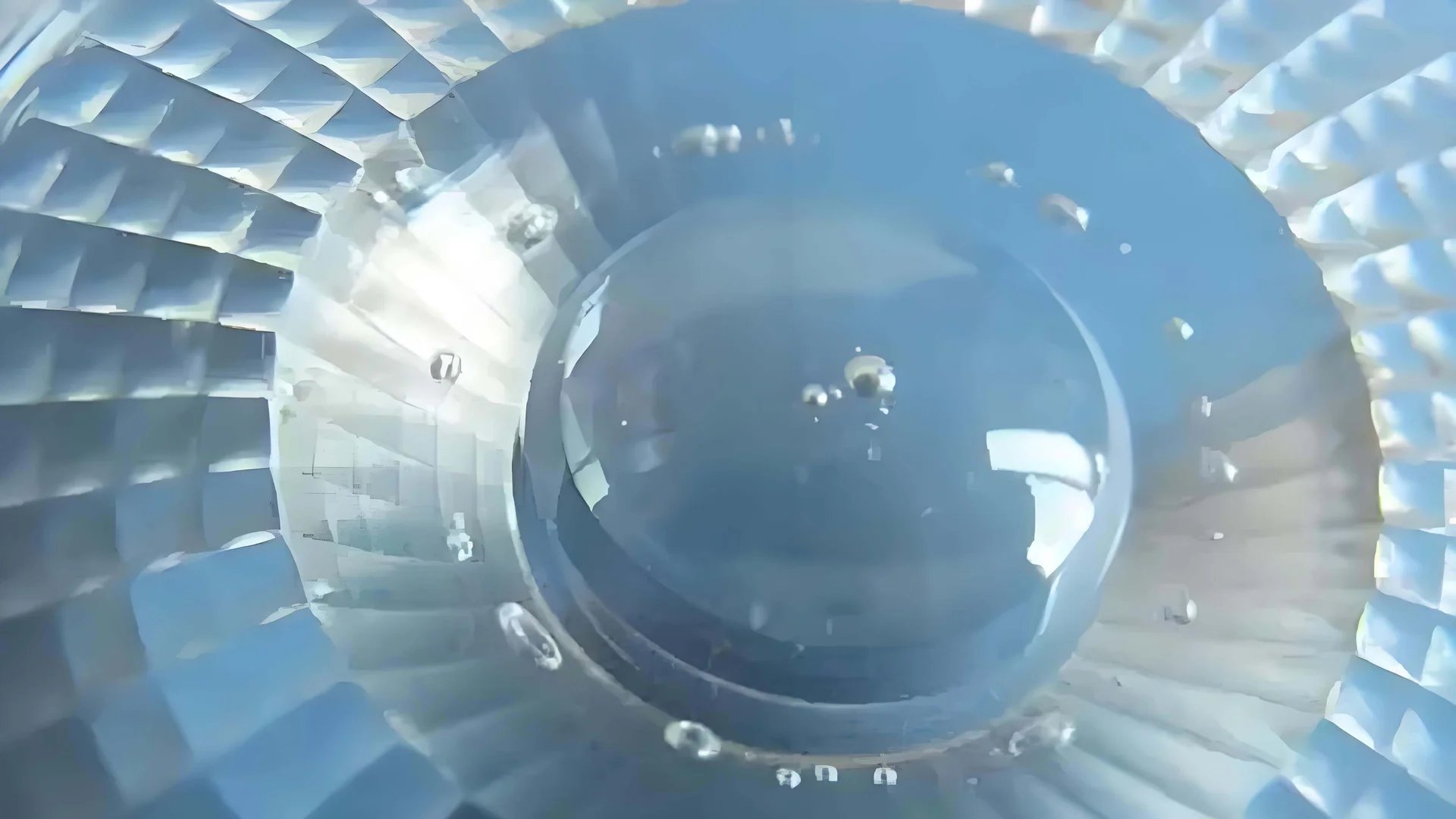
Material Preparation
The first line of defense against air bubbles starts with the materials. Ensuring raw materials are well-prepared can significantly mitigate the risk of bubble formation.
- Drying Raw Materials: Plastics prone to moisture absorption, such as polyamide (PA) and polycarbonate (PC), should be thoroughly dried before use. Investing in a reliable drying system can help maintain consistent material conditions.
- Controlling Volatiles: Regularly monitor and manage volatile content in materials. Use additives or processing aids that can reduce gas formation during melting.
Process Optimization
The injection molding process itself offers several avenues for preventing air bubbles:
- Adjusting Injection Speed: Modulate the injection speed to allow for adequate mold filling without trapping air. Slower speeds can facilitate better air evacuation, particularly for thin-walled parts.
- Setting Optimal Injection Pressure: Use sufficient injection pressure to compact the melt fully. Tailoring the pressure settings based on part geometry and thickness can ensure complete air expulsion.
Process Step | Recommended Action |
---|---|
Injection Speed | Adjust to prevent rapid cavity filling |
Injection Pressure | Set higher for complex or thick-walled parts |
Holding Time | Extend for large or uneven parts |
Mold and Equipment Maintenance
Ensuring that the mold and equipment are in prime condition is essential:
-
Temperature Control: Maintain precise mold temperatures. This can prevent cavitation and ensure uniform cooling. Utilize temperature control units to stabilize conditions.
-
Effective Exhaust Design: Regularly inspect and clean mold vents to guarantee effective air evacuation. Design molds with appropriate exhaust grooves and holes.
-
Equipment Checks: Regular maintenance of the injection molding machine, including screw design and clamping force, can prevent operational issues that lead to bubbles. Ensure all settings are optimized for the specific materials and product requirements.
By systematically addressing these areas, manufacturers can significantly reduce the occurrence of air bubbles in their products. This not only enhances product quality but also improves overall production efficiency.
Drying raw materials reduces air bubbles in molding.True
Properly dried materials prevent moisture-related bubble formation.
Higher injection pressure increases air bubble formation.False
Higher pressure compacts melt, reducing trapped air and bubbles.
Conclusion
To mitigate air bubbles in injection molding, focus on drying materials, optimizing injection parameters, and ensuring proper equipment maintenance. These steps will improve product quality and manufacturing efficiency.
-
Learn about material factors influencing injection molding quality.: 5 Factors that Affect Injection Molding Quality · Design of the Mold · Thickness of the Product Walls · Runner Presence · Surface Finishing · Raw Materials. ↩
-
Discover efficient techniques to enhance mold ventilation and reduce air entrapment.: Alternative venting valves can help overcome standard mold venting limitations and improve mold performance. ↩
-
Learn how material viscosity influences flow and defect formation in molds.: Materials that are low viscosity flow thinly and quickly, while high viscosity materials flow thickly and slowly. For instance, nylon flows … ↩
-
Find strategies to adjust injection speed for improved molding results.: Injection Speed: The rate at which molten plastic is injected into the mold affects the filling pattern, part density, and overall quality. ↩
-
Understand how screw design affects plastic melting and defect formation.: Screws allow for for these fluids to flow smoother by exert the force required over a longer time than a piston. Upvote ↩
-
Learn why adequate clamping force is critical for mold integrity.: Well, applying too much clamping force in injection molding leads to its own host of issues. Too much pressure leads to defects on the finished … ↩