Ever found yourself puzzling over the exact amount of material to use in injection molding? You’re not alone, and that’s why understanding shot weight is crucial.
Calculate shot weight in injection molding by determining the volume of the part, runner, and gate, and multiplying by material density. Use the formula W=(V{part}+V{runner}+V{gate})×ρ. Alternatively, use metering systems or weigh molded parts for accuracy.
When I first started working with injection molding, calculating shot weight seemed like deciphering a complex puzzle. But once I got the hang of it, it transformed how I approached each project. Theoretical methods, like using geometric formulas to determine part volume and considering the material’s density, were invaluable. It was like unlocking a new level of precision.
The practical side of things, like using the injection molding machine’s metering system or weighing the parts after molding, provided that tangible feedback I craved. These methods not only ensured that I was using materials efficiently but also improved the quality of the products I was creating. Whether you’re a seasoned pro or just getting started, mastering these techniques can make a world of difference.
Shot weight is calculated using volume and material density.True
Shot weight is determined by multiplying the total volume by material density.
Machine metering systems cannot calculate shot weight.False
Machine metering systems can indeed be used to calculate shot weight.
How Do You Calculate Part Volume in Injection Molding?
Ever wondered how to precisely calculate part volume in injection molding? It’s a bit like baking—measurements are key! Dive into this guide for practical tips.
Calculate injection molding part volume using geometric formulas or 3D modeling software. Include runner and gate volume, and use material density for accurate shot weight estimation.
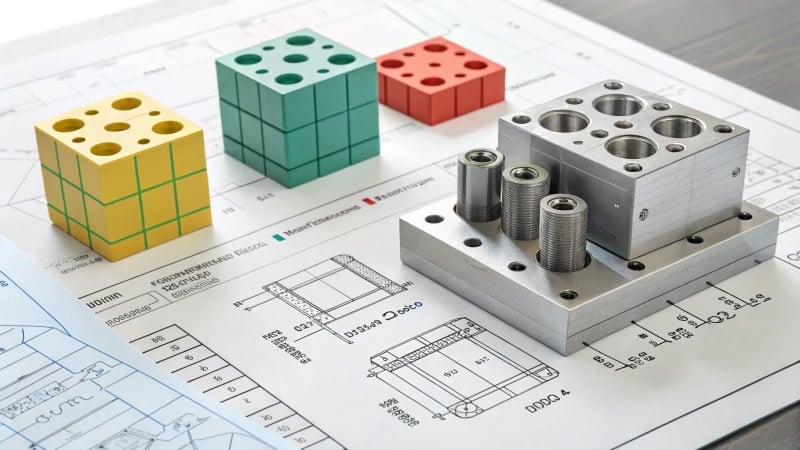
I remember the first time I had to calculate part volume for an injection molding project. It felt daunting, almost like solving a puzzle. You see, whether you’re working with a simple cube or a complex piece of art, getting the volume right is crucial.
Theoretical Approach to Part Volume Calculation
Starting with the basics, if your part is shaped like a cube, just use the formula V = l × w × h . But when things get more complicated, that’s when 3D modeling software1 becomes your best friend. Breaking down a design into simpler components can make the whole process less intimidating.
Accounting for Runner and Gate Volume
Don’t forget about the runner system—the unsung hero that delivers molten plastic to your mold cavity. I once overlooked this in a project and let me tell you, it was a lesson learned! Calculate its volume with Vrunner = πr² × L, and remember, every little bit counts toward the total shot weight.
Understanding Material Density
Knowing the density of your material is like knowing the secret ingredient in your recipe. Different plastics have unique densities that can impact your calculations significantly. For example:
Material | Density (g/cm³) |
---|---|
Polypropylene | 0.90 – 0.91 |
ABS | 1.04 – 1.06 |
These numbers are essential when converting volume to weight.
Practical Measurement Approaches
Modern injection molding machines2 often come with metering systems that feel like having a built-in assistant. They measure shot weight directly, helping you verify those theoretical calculations. And if you’re anything like me, you’ll appreciate the reassurance of weighing molded parts post-production.
Weighing Molded Parts
Weighing involves sampling molded parts with runners and gates to determine an empirical shot weight. Average multiple samples to account for any variability in the process.
So next time you’re at your workstation, calculator (or software) in hand, remember that each step of this process is like piecing together a mystery where precision and accuracy lead to success.
Volume of a cube is calculated using V = l × w × h.True
The formula V = l × w × h is the standard calculation for a cube's volume.
Material density does not affect shot weight calculations.False
Material density is crucial for converting volume to weight, impacting shot weight.
How Does Material Density Impact Shot Weight Calculation?
Have you ever wondered why some injection-molded products feel just right, while others seem off? It’s all about density and shot weight.
Material density affects shot weight calculation by determining the mass of plastic per unit volume, influencing the material required for consistent injection molding quality.
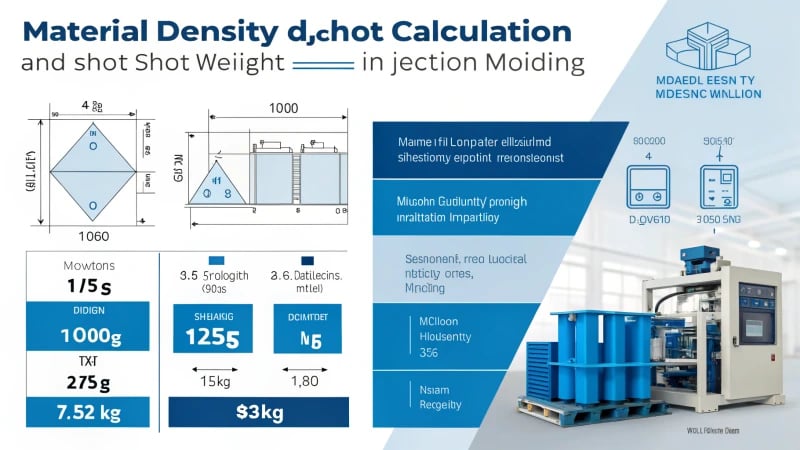
Theoretical Approach to Shot Weight Calculation
I remember my first big project in injection molding—it was a whirlwind of calculations, geometry, and plenty of learning curves. I quickly realized that material density wasn’t just a number; it was the backbone of getting shot weight right.
Calculating Part Volume
One late night, staring at a CAD model of a complex gadget part, I realized that calculating volume isn’t always straightforward. For simpler shapes like cubes, it’s a breeze with V = l × w × h. But when things got complicated, I turned to 3D modeling software3 to break it down.
Including Runner and Gate Volume
I once overlooked the runner system’s volume in a project—let me tell you, that was a lesson learned the hard way! Calculating something like a circular runner’s volume, Vrunner = πr² × L, is crucial to nail down those precise measurements.
Knowing Material Density
I still recall the first time I learned about the diverse densities of plastics. Whether it’s polypropylene with a density of (0.9 – 0.91 g/cm³) or ABS at (1.04 – 1.06g/cm³), knowing these values meant I could calculate shot weight with surgical precision.
Material | Density (g/cm³) |
---|---|
PP | 0.9 – 0.91 |
ABS | 1.04 – 1.06 |
It’s all about piecing together the formula:
W = (V{part} + V{runner} + V{gate})×ρ
Practical Measurement Approach
Modern tech has been a game-changer in my career. Using the metering systems in advanced injection molding machines, I’ve seen how we can measure material use in real-time—like having an extra pair of eyes on the process.
Using Metering Systems
Calibrating machines as per the manual is something I can’t stress enough. It provides real-time data and has saved me more than once from using too much material.
Weighing Molded Parts
Back in the day, before tech took over, weighing parts after molding was my go-to method. Taking multiple samples helped me ensure accuracy, catching any process variabilities.
These experiences taught me that understanding and applying these concepts optimizes production processes, maintaining efficiency and quality. If you’re eager to dive deeper into injection molding machines, check out this resource4.
Material density affects shot weight in injection molding.True
Material density determines the mass per unit volume, impacting shot weight.
Runner and gate volumes are irrelevant to shot weight.False
Including runner and gate volumes is essential for accurate shot weight.
Why Should You Care About Runner and Gate Volume?
Ever wondered why runner and gate volume is a big deal in injection molding? It’s the secret to cutting costs and improving quality.
Understanding runner and gate volume is vital in injection molding as it affects material usage, efficiency, and product quality, leading to optimal performance and cost savings.
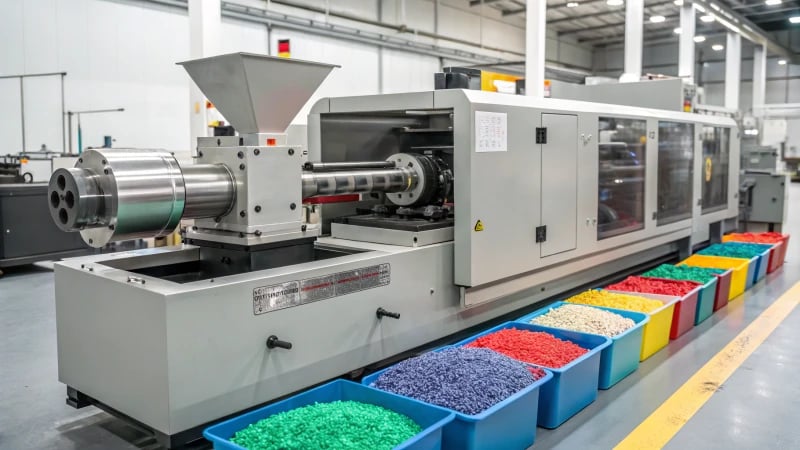
Theoretical Approach: Understanding the Basics
When I first delved into the world of injection molding, I realized that the volume of the runner and gate system5 is as critical as the part itself. Imagine these components as highways for molten plastic, guiding it from the machine to the mold cavity. Misjudging their volume can feel like being stuck in a traffic jam of waste and inefficiency.
Part Volume and Material Density
One of my aha moments was understanding how to determine the volume of a molded part. For simple shapes, I relied on basic geometry—like using V = l × w × h. But for more intricate designs, breaking them down or turning to 3D modeling was my go-to.
Next, account for the runner system’s volume6. Picture calculating the volume of a circular runner using V{runner}=πr² × L. Each gate has its unique design requiring careful calculation.
Knowing the material density is akin to knowing your ingredients when cooking. With plastics, this varies—take polypropylene, for example, with a density of (0.9 – 0.91g/cm³), whereas ABS stands around (1.04 – 1.06g/cm³).
Calculating Shot Weight
Shot weight was another puzzle piece that fell into place once I combined volumes of the part, runner, and gate with material density: W=(V{part}+V{runner}+V{gate})× ρ). Accurate measurements became my allies in saving costs and materials.
Component | Formula | Example |
---|---|---|
Part Volume | V = l × w × h | Complex Shapes: Use 3D modeling |
Runner Volume | Vrunner=πr² × L | Circular runner |
Gate Volume | Geometric shapes | Depends on design |
Shot Weight | W=Vpart+Vrunner+Vgate × ρ) | Combine all volumes |
Practical Measurement Approach: On-the-Spot Techniques
Modern machines often come equipped with metering systems. Once calibrated, they can measure material dispensed during each shot, providing direct insight into shot weight.
Weighing molded parts7 post-molding was a game-changer for me, offering an empirical shot weight value that factors in process variability. By taking multiple samples, I could ensure accuracy, helping to validate theoretical calculations.
Understanding these concepts has allowed designers like myself to optimize manufacturing processes. Precise runner and gate sizing not only enhances product quality but also plays a crucial role in reducing production costs8.
Runner volume affects shot weight in injection molding.True
The runner's volume contributes to the total shot weight calculation.
Ignoring gate volume leads to improved production efficiency.False
Ignoring gate volume can cause defects and inefficiencies in production.
How can practical measurement improve shot weight accuracy?
Imagine a world where every shot weight in injection molding was as precise as a Swiss watch. It’s not just a dream—practical measurement makes it possible.
Practical measurement improves shot weight accuracy through metering systems and direct weighing, adapting to changes for precise injection molding.
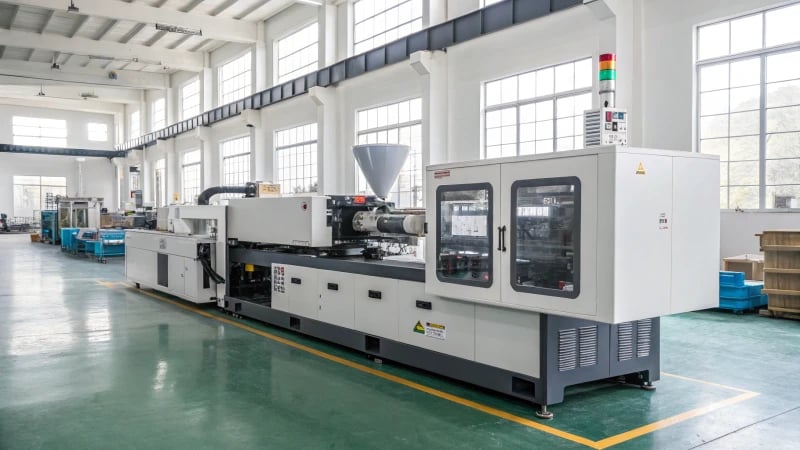
Leveraging Injection Molding Machine’s Metering System
Back when I was starting out in the world of injection molding, I quickly realized that relying solely on theoretical calculations was a bit like trying to predict the weather by looking at the sky. Enter the magic of modern machines with their metering systems. These machines are like the wise elders of the molding world, whispering secrets about precise measurements directly to you.
By calibrating the system9 according to the manufacturer’s guidelines, I found that I could measure exactly how much material was being dispensed with each shot. It’s like having a digital scale that accounts for those tricky real-time variations in material flow or density. This method became particularly indispensable when dealing with diverse materials10, where each type seemed to have its own personality.
Weighing Molded Parts for Empirical Accuracy
After the initial molding process, there’s something quite satisfying about physically weighing the molded parts. It’s a bit like baking—when you weigh your ingredients to ensure everything turns out just right. This hands-on approach gives me an empirical basis for shot weight calculation, complementing the theoretical methods.
I remember once, after meticulously weighing a series of parts, including runners and gates, I discovered a slight but crucial discrepancy in the calculated shot weight. Taking multiple samples and calculating an average helped smooth out those anomalies caused by fluctuations in material properties or machine settings. It was a lesson in patience and precision that paid off in spades.
Practical Approach vs Theoretical Calculations
Theoretical methods certainly have their place. Calculating part volume and applying material density is a solid starting point. I once had to calculate the volume of a complex shape using 3D modeling software—it felt like solving a puzzle! But these methods often assume conditions are uniform, which we know is rarely the case.
In contrast, practical measurement adapts beautifully to in-process changes, enhancing precision. For example, while calculating volume11 theoretically requires assumptions about geometry and density, practical methods can step in to validate or correct these assumptions.
Method | Pros | Cons |
---|---|---|
Theoretical Calculation | Provides initial estimates | May overlook real-time variations |
Practical Measurement | Accurate, accounts for real-time discrepancies | Requires equipment and repeated manual effort |
Understanding Material Variability
Different plastics are like different characters in a story—they each bring something unique. For instance, polypropylene might range from 0.9 to 0.91 g/cm³, while ABS is around 1.04 to 1.06 g/cm³. Understanding these differences has been crucial in my journey to reduce waste and optimize production costs12.
Practical measurement methods provide real-time data that lets me adjust on the fly rather than relying on static figures. It’s an approach that aligns perfectly with my goals of delivering quality while minimizing waste—a balance that’s not just good for business but also for peace of mind.
Practical measurement enhances shot weight accuracy.True
It adapts to real-time changes, improving precision over theoretical methods.
Theoretical calculations are always more accurate than practical methods.False
They assume uniform conditions, which may not reflect real-world variations.
Conclusion
Learn how to calculate shot weight in injection molding by determining part, runner, and gate volumes, factoring in material density for precise measurements and improved production efficiency.
-
Learn about software tools that assist in accurate volume calculation for complex part designs. ↩
-
Explore advanced features of modern injection molding machines that aid in precise material measurement. ↩
-
Explore how 3D modeling software aids in precise volume calculations for complex part geometries. ↩
-
Discover detailed insights into the functionality of injection molding machines and their role in manufacturing. ↩
-
This link provides a comprehensive understanding of the role runner and gate systems play in enhancing mold efficiency. ↩
-
Learn detailed methods to calculate runner system volumes for various shapes, crucial for precise molding. ↩
-
Discover techniques for weighing molded parts to ensure shot weight accuracy, enhancing production reliability. ↩
-
Explore how correctly sized runners can lead to significant reductions in production costs and waste. ↩
-
Discover how to calibrate metering systems for precise shot weight calculations in molding. ↩
-
Explore how different materials affect shot weight and measurement techniques. ↩
-
Learn methods to calculate volume for complex shapes in injection molding. ↩
-
Find strategies to minimize costs through accurate shot weight calculations. ↩