Understanding plastic mold shrinkage is vital for producing precise molded parts that fit specifications.
Plastic mold shrinkage is calculated by measuring the difference between the mold cavity size and the cooled part size, expressed as a percentage. Use precise tools to measure both sizes and apply the formula: Shrinkage rate = (mold cavity size – actual part size) / mold cavity size × 100%.
While this formula provides a basic approach, achieving accuracy requires considering various factors like material properties and process conditions. Delve into the nuances of plastic shrinkage to master this complex calculation and ensure optimal results.
Calipers measure mold cavity dimensions accurately.True
Calipers provide precise measurements necessary for accurate mold shrinkage calculations.
What Tools Can Enhance Measurement Accuracy?
Precision is key in measuring plastic mold shrinkage to ensure quality and fit.
Calipers and micrometers are essential for precise measurement in plastic mold shrinkage calculations. They provide accurate dimensions of both the mold cavity and the cooled part, ensuring data reliability. Additionally, using digital measuring tools can enhance precision through automated readings and data recording, minimizing human error.
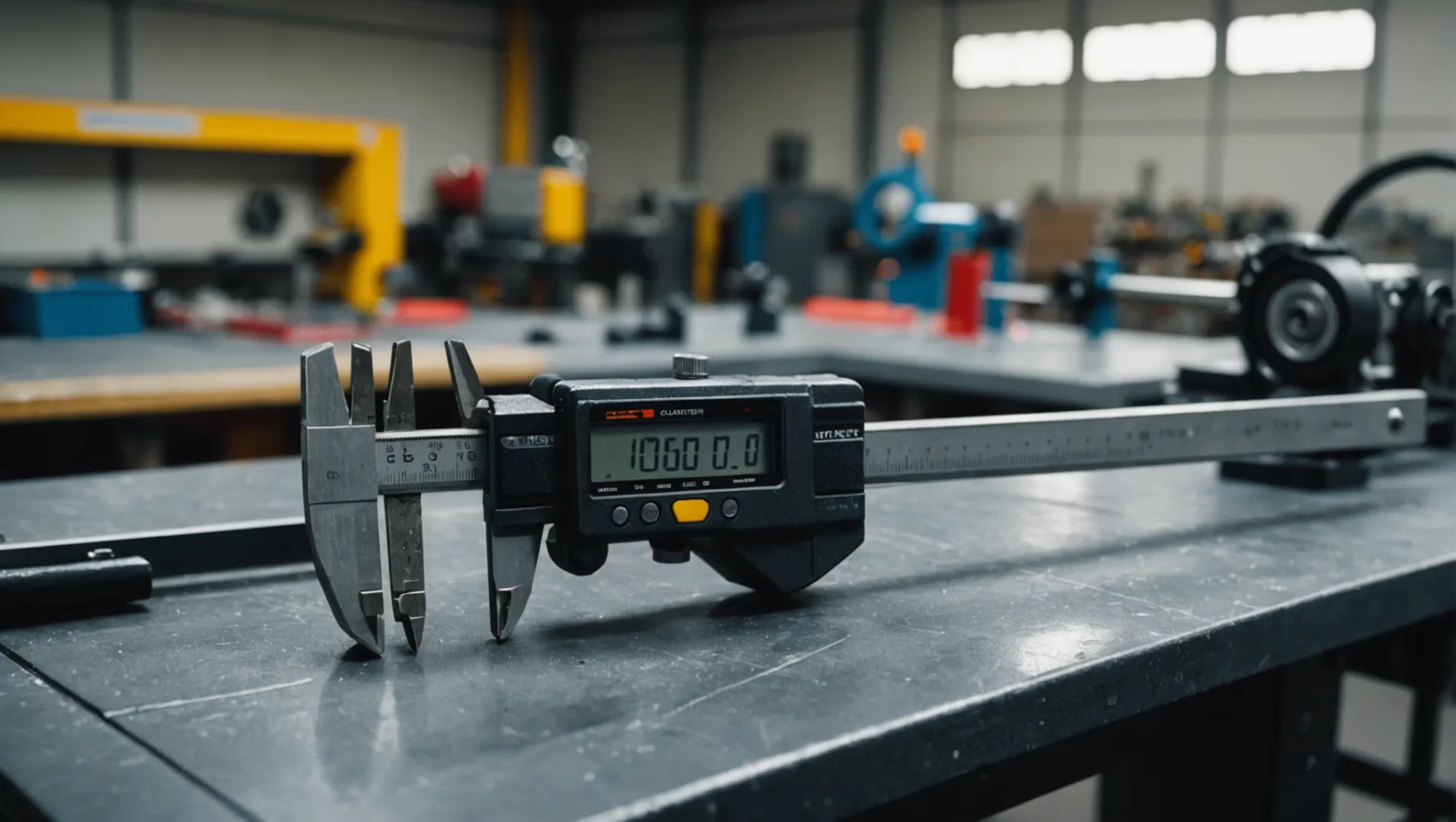
The Role of Precision Tools in Measurement
Accurate measurement is fundamental in determining the shrinkage of plastic molds1. Calipers and micrometers are widely used due to their high precision and ease of use. These tools allow for fine measurements, often down to the micrometer scale, which is crucial for evaluating the minute differences in size that indicate shrinkage.
Digital calipers, in particular, offer enhanced accuracy with their ability to provide digital readouts. This minimizes human error associated with reading analog scales. Furthermore, some advanced models even allow data to be directly transferred to computers, facilitating easy analysis and record-keeping.
Benefits of Automated Measurement Systems
Incorporating automated systems can greatly improve measurement accuracy. Coordinate Measuring Machines (CMMs) are increasingly popular in manufacturing settings for their ability to automatically measure complex geometries with high precision. These machines use probes to capture coordinates of an object’s surface, creating a detailed map of its dimensions.
For example, when measuring the shrinkage of a molded part, a CMM can quickly provide highly accurate data points across various axes, enabling a comprehensive understanding of the shrinkage pattern.
Importance of Repeated Measurements
To ensure consistency and accuracy, it is crucial to perform multiple measurements and average the results. This approach helps account for any variations that may occur due to slight discrepancies in measuring technique or tool calibration.
Moreover, using a combination of tools, such as verifying caliper readings with micrometer data, can further enhance measurement reliability.
Employing these practices not only aids in calculating the shrinkage rate more accurately but also enhances the overall quality assurance process for manufactured parts. For more insights into advanced measurement techniques, explore our guide on using CMMs for precise measurements2.
Calipers are essential for measuring mold shrinkage.True
Calipers provide precise measurements crucial for determining mold shrinkage.
CMMs cannot measure complex geometries accurately.False
CMMs are known for their precision in measuring complex geometries.
How Do Different Plastics Affect Shrinkage Rates?
Understanding how various plastics affect shrinkage rates is crucial for precision molding.
Different plastics exhibit distinct shrinkage rates due to their unique material properties. Polypropylene and polyethylene generally have higher shrinkage rates compared to ABS or polycarbonate. To calculate these rates accurately, it’s essential to consider each plastic’s inherent characteristics alongside external factors like temperature and pressure.
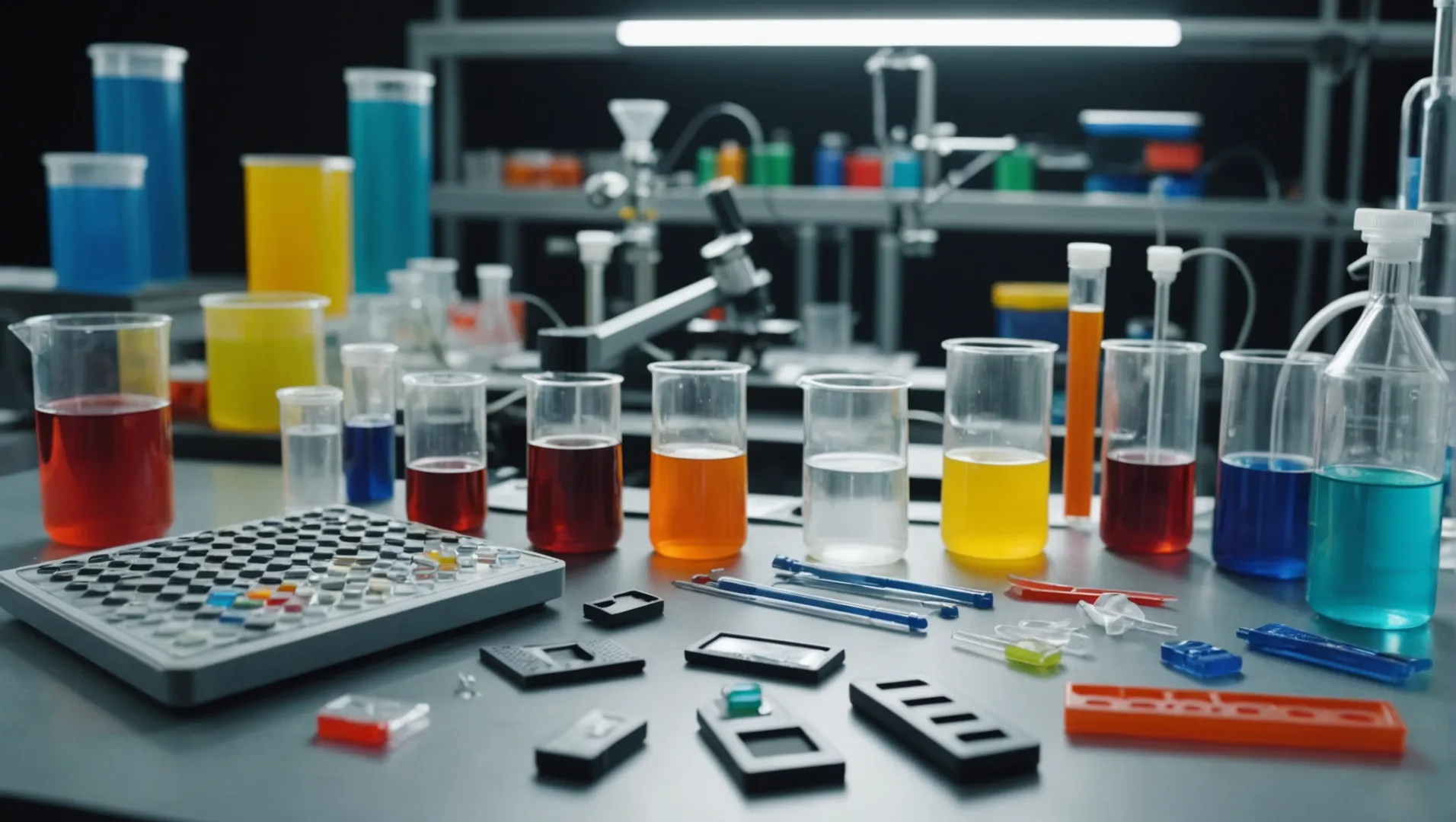
Material Properties Impact
The type of plastic used in molding significantly influences shrinkage rates. This is because each plastic has unique properties, such as crystallinity3, thermal expansion, and viscosity, which dictate how it behaves during cooling.
-
Amorphous Plastics: Materials like ABS and polycarbonate are amorphous, meaning they lack a crystalline structure. They tend to shrink less because their molecular chains are more entangled, offering resistance against contraction.
-
Semi-crystalline Plastics: Polypropylene and polyethylene fall into this category. These materials have a structured arrangement, leading to higher shrinkage rates as they crystallize during cooling.
Influence of Additives and Fillers
Additives and fillers can alter the shrinkage characteristics of a plastic. For example, adding glass fibers to a polymer can significantly reduce shrinkage by reinforcing the material structure.
Material Type | Shrinkage Rate (%) |
---|---|
Polypropylene | 1.5 – 2.5 |
Polyethylene | 1.5 – 3.0 |
ABS | 0.4 – 0.8 |
Polycarbonate | 0.5 – 0.7 |
External Factors and Their Role
Besides intrinsic material properties, external factors such as mold design and process conditions4 heavily influence shrinkage rates.
-
Temperature: Higher mold temperatures typically increase shrinkage by allowing more crystalline structures to form in semi-crystalline plastics.
-
Pressure: Increasing the injection pressure can compact the material more effectively, potentially reducing the overall shrinkage.
Understanding Shrinkage Ranges
Each plastic type has an estimated shrinkage range, but actual outcomes can vary based on processing conditions. For instance, within polypropylene’s range of 1.5% to 2.5%, different batches may show variations due to slight changes in melt temperature or cooling time.
In conclusion, knowing the interplay between material types and external factors is key to predicting and managing shrinkage rates effectively.
Polypropylene has a higher shrinkage rate than ABS.True
Polypropylene's semi-crystalline structure leads to higher shrinkage.
Amorphous plastics like ABS shrink more than semi-crystalline ones.False
Amorphous plastics have lower shrinkage due to entangled molecular chains.
What Role Does Injection Molding Play in Shrinkage?
Injection molding is a crucial step in determining the final shrinkage of a plastic part.
Injection molding significantly impacts shrinkage by influencing material behavior through process parameters like temperature, pressure, and speed. These parameters dictate the cooling rate and material orientation, which directly affect the shrinkage characteristics of the molded part.
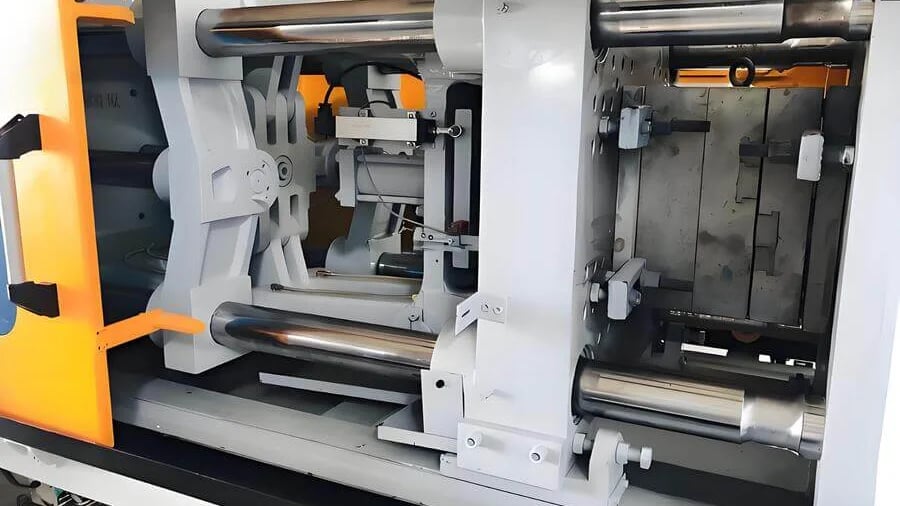
Understanding the Injection Molding Process
Injection molding is a manufacturing process used for producing parts by injecting molten material into a mold. This process is pivotal in determining the final properties of the plastic part, including its shrinkage rate.
-
Injection Pressure and Speed: The pressure at which the molten plastic is injected into the mold can influence shrinkage. High pressure tends to fill the mold cavity more thoroughly, reducing voids and minimizing shrinkage. Similarly, injection speed affects how quickly the mold is filled, impacting the material’s orientation and its eventual shrinkage rate.
-
Mold Temperature: A higher mold temperature generally increases the mobility of polymer chains, allowing them to pack more densely as they cool. This can lead to greater shrinkage. Conversely, lower mold temperatures might reduce shrinkage but can also affect the surface finish and mechanical properties of the part.
-
Cooling Rate: The cooling rate is crucial in controlling shrinkage. Faster cooling typically results in less shrinkage because it restricts the movement of polymer chains. However, uneven cooling can lead to warping or residual stresses.
Material and Structural Influences
-
Material Properties: Different plastics have inherent shrinkage rates due to their molecular structure. For instance, semi-crystalline polymers like polyethylene tend to shrink more than amorphous polymers such as polystyrene.
-
Part Geometry: The design of the part can influence shrinkage. Features like ribs or varying wall thickness can result in uneven cooling and differential shrinkage, leading to warping or dimensional inaccuracies.
Parameter | Influence on Shrinkage |
---|---|
Injection Pressure | Higher pressure reduces shrinkage by thorough cavity filling |
Mold Temperature | Higher temperature increases shrinkage via polymer mobility |
Cooling Rate | Faster cooling reduces shrinkage, affects part quality |
Process Optimization
To minimize shrinkage and achieve consistent quality, it is crucial to optimize injection molding parameters. This involves a delicate balance between pressure, temperature, and cooling time. Learn more about optimizing injection molding5 to ensure precise control over part dimensions and properties.
Understanding how each aspect of injection molding influences shrinkage enables manufacturers to predict and control dimensional changes effectively. Dive into advanced strategies6 for managing shrinkage through process adjustments and material selection.
Higher mold temperature increases shrinkage.True
High mold temperatures increase polymer mobility, leading to more shrinkage.
Faster cooling results in more shrinkage.False
Faster cooling restricts polymer chain movement, reducing shrinkage.
Why Is Consistent Measurement Critical for Accurate Results?
Accurate measurements are fundamental in manufacturing, ensuring each product meets the stringent quality standards required for success.
Consistent measurement is crucial because it minimizes variability, ensures reliability, and enhances the accuracy of results, particularly in calculating plastic mold shrinkage.
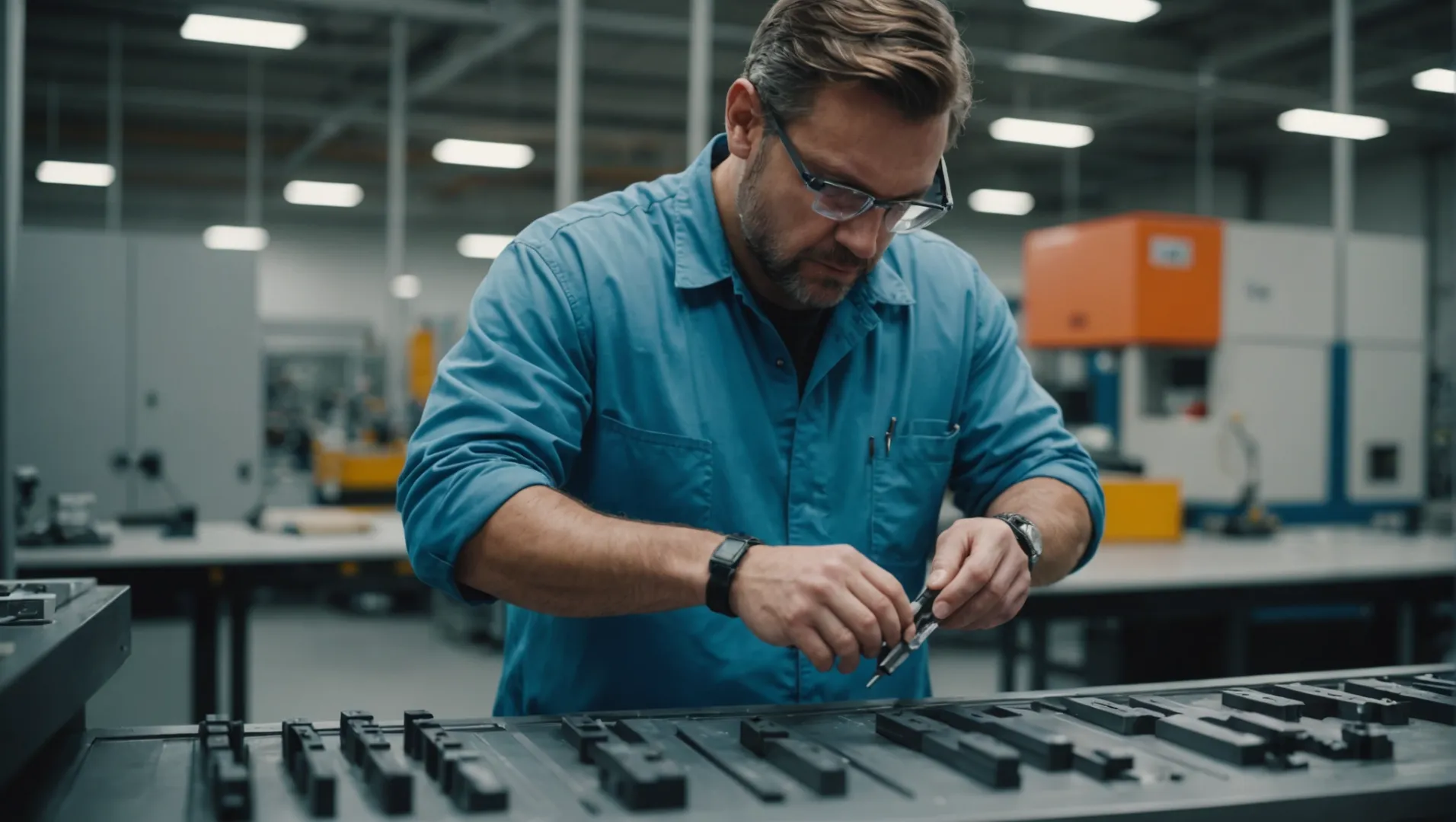
The Importance of Consistency in Measurements
Consistency in measurement is paramount in maintaining the reliability of data across production processes. When measuring plastic mold shrinkage7, the precision of each measurement directly impacts the quality and accuracy of the final product.
Tools and Techniques
Using advanced tools such as calipers and micrometers ensures precision when measuring both the mold cavity and the final part dimensions. However, even the most advanced tools can yield inconsistent results if not used systematically. Thus, adopting a standardized method across all measurements is vital. Regular calibration of tools is also essential to maintain accuracy.
Impact on Plastic Mold Shrinkage
The calculation of mold shrinkage relies on accurate measurements. Variability can arise from different sources, such as tool wear, operator error, or environmental factors like temperature and humidity. By maintaining consistent measurement practices, you can minimize these variables.
Example Calculation:
Mold Cavity Size (mm) | Actual Part Size (mm) | Shrinkage Rate (%) |
---|---|---|
100 | 98 | 2 |
This table illustrates how precise and consistent measurements lead to accurate shrinkage calculations, ensuring that every batch meets the desired specifications.
Minimizing Human Error
Human error is a common source of inconsistency. Implementing training programs and developing standard operating procedures8 can significantly reduce errors. Furthermore, using digital tools to automate certain aspects of measurement can enhance consistency and accuracy.
Environmental Considerations
Environmental factors such as temperature changes can affect measurement accuracy. Using temperature-controlled environments for measurements or compensating for temperature variations through calibrated adjustments can help maintain consistency.
Consistency is not just a matter of using the right tools but involves a holistic approach incorporating tool use, human factors, and environmental conditions. Ensuring consistent measurement practices will lead to more reliable outcomes, enhancing the overall production quality.
Consistent measurement minimizes variability.True
Consistent measurements reduce variability, ensuring reliable data.
Human error is the primary source of measurement inconsistency.True
Human error often causes inconsistency, which SOPs help mitigate.
Conclusion
Mastering plastic mold shrinkage calculations empowers you to produce parts with precision. Consider material properties, process parameters, and structural influences for accurate results.
-
Discover detailed methods for measuring plastic mold shrinkage accurately.: Plastic injection molded part shrinkage units are expressed as thousandths of an inch per linear inch (0.00X /in/in). Typical shrink rates vary between 0.001/ … ↩
-
Learn how CMMs enhance measurement precision in manufacturing.: Improved Efficiency · Repeatability and Reliability · Accuracy · Verifying Geometric Dimensioning & Tolerancing (GD&T) · Efficient Labor Use … ↩
-
Learn how crystallinity affects the physical properties of different plastics.: The crystallinity is important as it affects material selection, part design, processing, and the ultimate anticipated service properties. ↩
-
Discover how process parameters like temperature and pressure impact shrinkage rates.: The extent of plastic shrinkage depends on factors such as material type, composition, moisture absorption, and mold temperature. For instance, … ↩
-
Discover tips for balancing injection molding parameters for best results.: The 8 Key Parameters in Injection Molding Process Optimization to Avoid Defects · 1. Temperature Control: · 2. Injection Speed: · 3. Cooling … ↩
-
Explore techniques for precise control over injection molding shrinkage.: How to Avoid the Shrinkage in Plastic Moulding? · Optimize the Cooling Effects · Reduce Wall Thickness Reasonably · Reduce the Plasticizing Temperature · Enhance … ↩
-
Learn why consistent measurement is key in reducing variability.: Because viscosity is a variable, keeping fill time constant minimizes the influence of these variations and provides a more stable process, and … ↩
-
Discover how SOPs enhance measurement reliability.: Check standards that represent the standard and/or the items to be calibrated. Check standards must be stable, and their values should be established with … ↩