Ever wondered how multi-stage injection transforms everyday products from cars to toys?
Multi-stage injection in molding machines provides precise control over speed and pressure. This control significantly improves the quality of products. Many industries, like automotive, electronics and medical devices, use this technology. Dimensional accuracy benefits from this system. Defects become fewer. Overall efficiency grows as a result.
That feeling when a puzzle piece finally clicks into place is familiar. Multi-stage injection in manufacturing brings that satisfaction to me. This technology truly supports my design work. Every curve and edge of a product turns out perfect.
In the car industry, dashboards and bumpers demand precision. Multi-stage injection allows exact control of the molding process. This lowers defects and raises assembly quality. It really helps.
In electronics, creating slim and flawless parts is possible. Each setting is carefully adjusted for perfect results. Important details, for sure. For medical devices, where safety is very crucial, this method makes precise and pure parts. No impurities.
Not merely about productivity, these examples illustrate how multi-stage injection sets new design and innovation goals. From household items to detailed toys with complex and colorful forms, this technology allows creative exploration. Quality stays intact, no compromise.
Multi-stage injection improves product dimensional accuracy.True
Multi-stage injection allows for precise control, enhancing accuracy.
Multi-stage injection is rarely used in the automotive industry.False
It is widely used due to its benefits in precision and efficiency.
- 1. How Does Multi-Stage Injection Enhance Automotive Manufacturing?
- 2. How Does Multi-Stage Injection Enhance Electronics Production?
- 3. Why Is Multi-Stage Injection Crucial for Medical Device Manufacturing?
- 4. How is Multi-Stage Injection Revolutionizing Packaging?
- 5. What Advantages Does Multi-Stage Injection Offer in Toy Manufacturing?
- 6. Conclusion
How Does Multi-Stage Injection Enhance Automotive Manufacturing?
Picture creating car parts with the accuracy of a master artist’s touch.
Multi-stage injection controls injection speed and pressure in automotive manufacturing. This process very carefully creates perfect parts like dashboards and bumpers. High precision in assembly improves overall quality. Quality is very important.
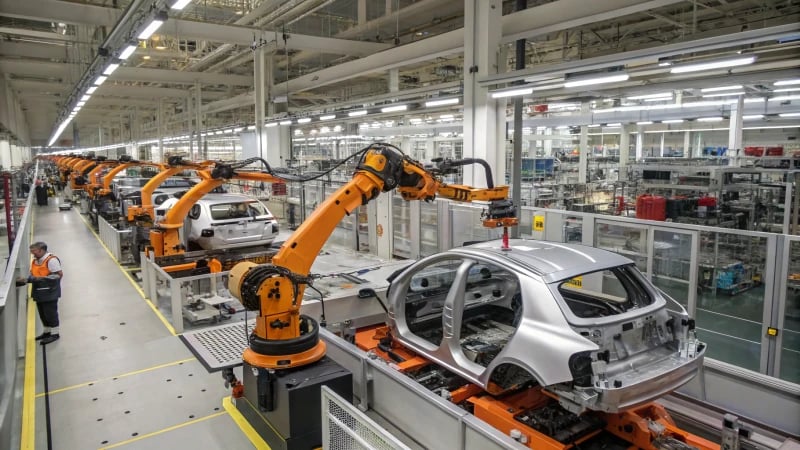
The Role of Multi-Stage Injection in Automobiles
I recall entering a busy car factory for the first time. It felt like entering a completely different realm. Machines moved with a rhythm, and every step needed precision. This was truly an engineering wonder. The technique that impressed me most was multi-stage injection molding. This process creates car parts with very complex shapes and accurate details.
Imagine fitting pieces of a puzzle perfectly together. Car dashboards and bumpers have perfect forms thanks to this method. By controlling the speed and pressure of injection carefully, manufacturers can ensure dimensional accuracy1 and prevent problems like warping or shrinking marks.
Benefits for Quality and Efficiency
Reflecting on my time in the industry, I observed many benefits from multi-stage injection:
Benefits | Description |
---|---|
Dimensional Accuracy | Precise control leads to exact dimensions, reducing post-production work |
Defect Reduction | Minimizes warping and shrinkage marks, enhancing aesthetic appeal |
Enhanced Durability | Improved mechanical properties ensure long-lasting components |
Cost Efficiency | Reduces scrap rates and increases production efficiency |
The parts have very reliable mechanical properties. A well-made dashboard not only looks good but fits exactly in the car’s structure. This precision reduces issues during assembly, really improving the car’s safety and performance.
Comparing with Traditional Methods
I often think about how things changed from old single-stage methods to multi-stage ones. It’s like comparing old black-and-white pictures to color ones—both work, but color adds more detail and depth. Old single-stage methods struggle with detailed shapes or thin parts common in cars. Multi-stage molding handles these well by using different pressures and speeds at each step, ensuring a uniform fill of complex cavities2.
Industry Applications Beyond Automotive
Interestingly, while car production gains a lot from multi-stage injection, other fields also benefit from it:
- Electronics: Needs tiny components with great precision.
- Medicine: High safety standards require accurate device production.
Multi-stage injection is truly amazing; it shows its power in raising product quality across many areas.
For those curious about its impact in other industries, there is a detailed guide3 about its use in medical devices, packaging, and more. Different sectors highlight the flexibility and potential of this technology to change production processes.
Multi-stage injection reduces automotive defects.True
It minimizes warping and shrinkage marks, enhancing component quality.
Single-stage injection is more precise than multi-stage.False
Multi-stage allows better control over speed and pressure for precision.
How Does Multi-Stage Injection Enhance Electronics Production?
Do you ever think about how the small parts in your devices are created with high accuracy?
Multi-stage injection plays a key role in electronics production. It gives precise control over how fast and hard materials are injected. This control leads to high-quality parts with complex designs. It reduces defects. Parts with fewer flaws last longer. Good control also improves both how products work and look.
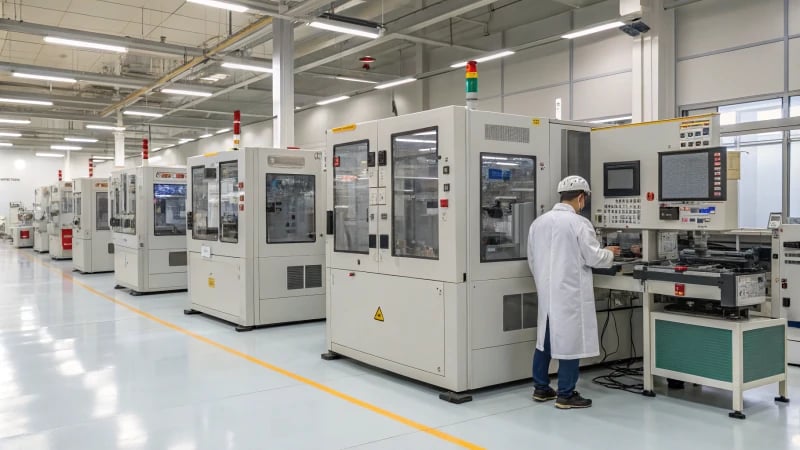
Understanding Multi-Stage Injection
Multi-stage injection is a sophisticated molding process where the injection speed and pressure are carefully controlled in stages. This technique is crucial for producing electronic parts with thin walls, intricate structures, and stringent quality demands. It’s primarily used to avoid common defects such as flash and weld marks.
My first experience with multi-stage injection was during a project for electronics connectors. We had to design tiny and detailed parts. I saw then how important it is to control injection speed and pressure precisely. This method became our secret tool. It helped us make electronic parts with thin walls and complex shapes while keeping top-notch quality.
Benefits in Electronics Manufacturing
In electronics, every tiny bit matters. Components like shells, connectors, and buttons demand precision. Multi-stage injection enables the melt to fill molds evenly, reducing material shortages and ensuring superior electrical performance.
Key Advantages
Advantage | Description |
---|---|
Precision Control | Adjusts parameters dynamically for optimal mold filling and solidification. |
Quality Assurance | Minimizes defects like warping and shrinkage, enhancing product reliability. |
Cost Efficiency | Reduces waste and production costs by minimizing errors and rejects. |
I recall when even a small mistake meant long hours fixing designs. Multi-stage injection changed that. This process allowed the melted material to spread evenly in molds, preventing flaws like flash and weld marks. It felt like having a dependable partner that ensures the product meets strict electric performance and looks perfect.
Applications Across Industries
Automobile Manufacturing
In the automotive sector, multi-stage injection creates parts like dashboards and bumpers that require high precision. I once collaborated on a car dashboard project where this technique ensured dimensional accuracy4 and mechanical properties were met, crucial for automotive safety and performance.
Medical Devices
The medical field benefits from this method by producing high-precision, impurity-free products such as syringes. In another project for medical devices, we faced strict rules for precision and safety; multi-stage injection was important here to meet the exacting standards of medical device manufacturing5, ensuring safety and reliability.
Household Goods
For household items like plastic furniture, this process meets diverse design needs while producing durable products with smooth surfaces, enhancing aesthetic appeal6 and functionality.
The Future of Multi-Stage Injection in Electronics
As electronics continue to evolve towards miniaturization yet more powerful capabilities, I see multi-stage injection becoming even more important in meeting these demands. By enabling precise molding of complex shapes,
it will support innovations in cutting-edge electronic designs7. Imagine the creations possible as we push the limits! Fascinating.
Multi-stage injection reduces material shortages.True
This technique ensures even mold filling, minimizing shortages.
Multi-stage injection is not used in medical devices.False
It produces high-precision, impurity-free products like syringes.
Why Is Multi-Stage Injection Crucial for Medical Device Manufacturing?
I remember when I first discovered the magic of multi-stage injection molding. It felt like finding a hidden ingredient in a favorite family recipe.
Multi-stage injection plays a big role in making medical devices. This process allows precise control over molding. It gives high-quality results. Products have no bubbles or impurities. Medical devices meet strict safety and reliability rules. This is very important.
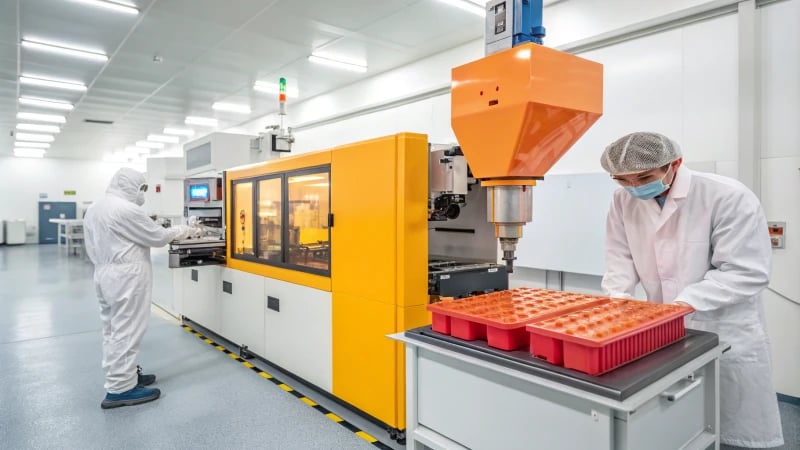
The Role of Precision in Medical Devices
Precision in medical devices is essential, not just optional. I remember a project where our team designed syringes. Syringes seem simple but need high accuracy. The multi-stage injection8 process was very helpful. It let us control speed and pressure during molding, ensuring that products like syringes were perfect, without bubbles or impurities. Safety depended on it.
Key Benefits | Description |
---|---|
Quality Assurance | Ensures consistency and reliability in product batches. |
Defect Reduction | Minimizes issues like warping and shrinkage. |
Regulatory Compliance | Meets stringent industry regulations effectively. |
Enhancing Product Quality
Quality in medical devices matters a lot. In a difficult project, multi-stage injection helped us make high-precision parts needed for reliable medical equipment. By achieving a consistent fill in the mold cavity, we avoided problems like material shortages and weld lines, ensuring every finish was perfect.
Cost Efficiency in Manufacturing
A surprising benefit of multi-stage injection is cost efficiency. Lower defect rates reduced material costs and labor spent on rework or waste. This process also sped up production without losing quality—very much a win-win in manufacturing.
Meeting Industry Standards
Making medical devices means meeting industry standards is essential. Multi-stage injection gave us control to meet every requirement, which is crucial for devices used directly on patients where safety always comes first. Advanced molding not only improved quality; it kept us competitive by aligning with evolving standards9 in the medical field, thereby maintaining our reputation (公司保持信誉).
Multi-stage injection reduces manufacturing costs.True
By minimizing defects, it saves on material and labor costs.
Multi-stage injection increases defect rates in products.False
It actually reduces defects like warping and shrinkage.
How is Multi-Stage Injection Revolutionizing Packaging?
Multi-stage injection molding reshapes the packaging world. This process really transforms efficiency and reduces environmental impact. The packaging industry becomes better and greener.
Multi-stage injection molding increases the packaging industry’s effectiveness. The process improves container quality. Wall thickness control becomes better. Pressure resistance also becomes higher. Waste decreases. As a result, costs drop. This leads to really affordable solutions.
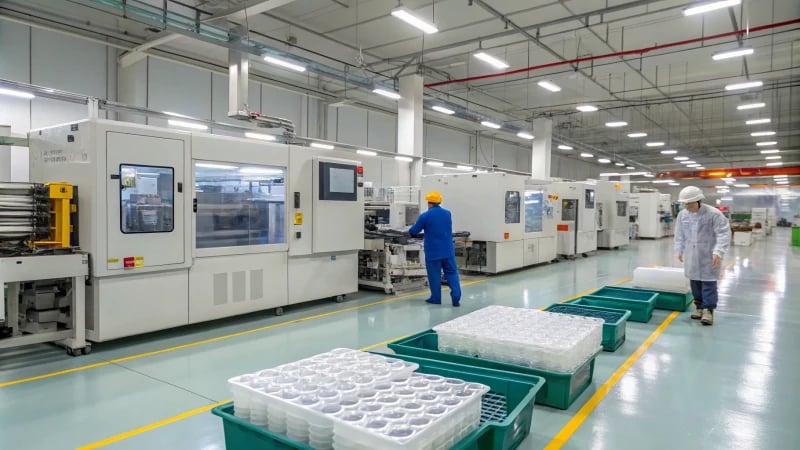
Improving Molding Quality
Multi-stage injection has revolutionized the production of plastic packaging, such as bottles and barrels. By offering precise control over settings, manufacturers can achieve even wall thickness10 and create strong products with less wasted material. It’s akin to discovering the perfect recipe after many attempts.
Benefits | Description |
---|---|
Wall Thickness | Ensures consistent product quality, minimizing defects. |
Material Efficiency | Reduces waste and enhances sustainability efforts. |
Cost Savings and Less Waste
I recall a project plagued by high scrap rates—what a headache it was! Multi-stage injection refined the process, greatly reducing waste. This approach not only saves money but also aligns with our planet-friendly goals11. It feels satisfying to help the Earth while controlling expenses.
Design Flexibility
The excitement of having design freedom is wonderful! Multi-stage injection allows for creative exploration of different shapes and looks. We achieve precise control over12 material movement, making complex designs possible. Our products become both functional and eye-catching.
Feature | Impact |
---|---|
Complex Shapes | Supports branding and product differentiation on busy store shelves. |
Material Flow Control | Ensures high-quality finishes and intricate designs that stand out in a crowded marketplace. |
In a field where precision and trust are necessary, multi-stage injection offers more than just technical progress—it’s a path to success. Whether for drink containers or beauty packaging, this method delivers top-quality production.
Multi-stage injection reduces plastic waste.True
Optimizing the injection process minimizes scrap rate, cutting waste.
Multi-stage injection limits design creativity.False
It allows for complex shapes and precise material flow control.
What Advantages Does Multi-Stage Injection Offer in Toy Manufacturing?
Picture designing toys that bring happiness, focusing on every detail carefully shaped. Multi-stage injection molding truly brings this vision to life, offering accuracy and bright colors.
Multi-stage injection in toy production provides exact control over the injection steps. This method allows for complex designs and bright colors. It decreases flaws. It also increases safety. High-quality demands of consumers are met. The demands are very high.
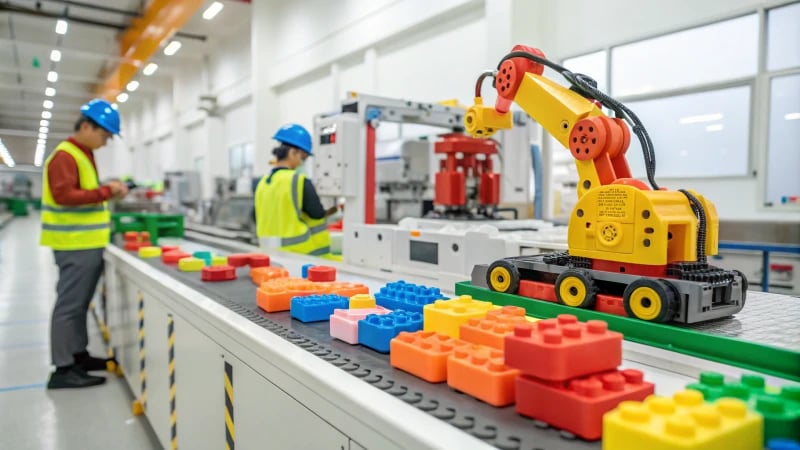
Greater Accuracy and Complexity
I remember seeing multi-stage injection13 work for the first time. It felt like watching an artist paint with skill and style. This technique provides careful control over how fast and hard materials are injected. Such control is vital for creating complex toy designs. This method allows for crafting toys with amazing detail and bright colors, achieving impressive results in one step. Less time for assembly and stronger toys are extra benefits.
Fewer Mistakes
At the start of my work with molds, flaws like warps and shrinkages were common headaches. Multi-stage injection changed everything. Problems like weld lines and defects are no longer issues. Adjusting settings during the process produces toys that are smooth and flawless. This saves time and resources since there is no need for rework.
Defect | Impact on Toy | Solution via Multi-Stage Injection |
---|---|---|
Warping | Distorted shapes | Controlled cooling phase to prevent warping |
Shrinkage | Size inconsistencies | Adjusted pressure to maintain uniformity |
Weld Lines | Weak structural integrity | Optimized flow to avoid weld line formation |
Better Safety
Safety is important and not just a task to check off; it’s a promise to our young users. Multi-stage injection keeps the melt flow stable. Weak spots and breakages are now past concerns. Toys created this way meet strict safety standards—no impurities, no sharp edges.
Fulfilling Consumer Needs
Consumers today look for everything – safety, beauty, durability. Multi-stage injection provides these all. It lets us design toys that exceed expectations while remaining efficient. We personalize toys without losing quality, matching what modern consumers really expect.
For more information on how injection molding innovations14 are revolutionizing toy making, see how companies use advanced methods to stay strong in a changing market.
Flexibility and Cost Savings
Multi-stage injection offers flexibility, like a trusty tool always ready for use. Mixing different materials and colors in one mold reduces extra steps and waste, leading to lower costs—very beneficial for manufacturers needing to stay competitive while keeping quality high.
Find out more about cost-efficient toy production15 and how multi-stage injection helps improve toy manufacture and profitability.
Multi-stage injection reduces toy assembly time.True
It molds multiple components in one process, reducing assembly.
Multi-stage injection increases toy defect rates.False
It minimizes defects by allowing flexible adjustments during molding.
Conclusion
Multi-stage injection molding enhances precision and quality across various industries, including automotive, electronics, medical devices, packaging, household goods, and toys by reducing defects and improving efficiency.
-
Understanding how multi-stage injection ensures precision helps optimize component quality. ↩
-
This link explains why multi-stage injection offers superior quality control over traditional methods. ↩
-
Discover how different sectors utilize multi-stage injection to enhance product quality. ↩
-
Discover how multi-stage injection ensures precise dimensions, crucial for automotive safety and performance. ↩
-
Learn about standards ensuring the safety and reliability of medical devices through precise molding techniques. ↩
-
Explore how multi-stage injection improves the aesthetic appeal of household goods through precise molding. ↩
-
See how multi-stage injection supports innovations in complex electronic designs. ↩
-
Explore how multi-stage injection enhances precision in molding processes, crucial for manufacturing defect-free medical devices. ↩
-
Discover how manufacturers meet stringent industry standards using advanced molding techniques. ↩
-
Learn how precise control over wall thickness contributes to high-quality and durable packaging solutions. ↩
-
Discover how this technology helps in reducing waste and promoting sustainability in manufacturing. ↩
-
Explore how control over material flow enables intricate and innovative packaging designs. ↩
-
Discover how multi-stage injection enhances design precision and reduces defects in toy production. ↩
-
Learn about cutting-edge advancements in injection molding that are transforming toy manufacturing. ↩
-
Find strategies for reducing costs while maintaining quality in toy production using advanced techniques. ↩