Finding the sweet spot between rigidity and toughness in plastic parts is no small feat!
To achieve the perfect balance of rigidity and toughness in plastic injection molded parts, one must carefully consider material selection, optimize the injection molding process, and implement strategic structural design features.
But this is just the beginning! The path to mastering this balance is filled with fascinating insights on materials, processes, and innovative designs that can truly elevate your manufacturing game.
Polycarbonate is ideal for high rigidity and toughness.True
Polycarbonate offers excellent rigidity and impact strength, suitable for demanding applications.
- 1. What Role Does Material Selection Play in Balancing Rigidity and Toughness?
- 2. How Does Injection Molding Process Optimization Impact Part Performance?
- 3. What Structural Design Techniques Enhance Rigidity Without Compromising Toughness?
- 4. Why Is Post-Processing Critical in Achieving Desired Mechanical Properties?
- 5. Conclusion
What Role Does Material Selection Play in Balancing Rigidity and Toughness?
Choosing the right material is crucial in balancing rigidity and toughness for plastic injection molded parts, influencing durability and performance.
Material selection is vital in achieving the right balance between rigidity and toughness in plastic parts. Choosing appropriate plastic matrices, using alloys or blends, and adding reinforcement materials are effective strategies to enhance both properties.

Selecting Suitable Plastic Matrices
When aiming to balance rigidity and toughness, the choice of plastic matrix1 plays a pivotal role. For instance, polycarbonate (PC) is known for its high rigidity and impact strength, making it ideal for applications demanding these properties. On the other hand, polypropylene (PP) offers better toughness at a lower cost but lacks rigidity. It’s crucial to align the choice of plastic with specific application requirements.
Leveraging Alloys and Blends
Alloying or blending plastics can effectively combine the strengths of different materials to achieve a balance. A common example is the PC/ABS alloy, which merges the rigidity of PC with the toughness of ABS. This combination finds widespread use in electronics housing due to its ability to maintain integrity under stress while being resilient to impacts.
Adding Reinforcement Materials
Fiber Reinforcement
Fiber reinforcement significantly enhances the rigidity of plastics. Materials like glass fiber and carbon fiber are often used to boost strength. Control over fiber length, content, and orientation is essential to maintain an optimal level of toughness.
Mineral Filling
Mineral fillers such as talcum powder and calcium carbonate increase hardness and stability. However, excessive filler amounts can diminish toughness, necessitating careful selection based on application needs.
Table 1: Examples of Plastics with Reinforcement
Type | Reinforcement | Effect on Rigidity | Effect on Toughness |
---|---|---|---|
Polycarbonate | Glass Fiber | High | Moderate |
Polypropylene | Talcum Powder | Moderate | Low |
ABS/PC Alloy | Carbon Fiber | High | High |
Considerations for Specific Applications
Each application demands a unique balance of these properties. For example, automotive parts require materials that can withstand both force and impact, making PC/ABS blends with fiber reinforcement an excellent choice. In contrast, consumer electronics might prioritize a lighter weight without sacrificing structural integrity.
Understanding the nuances of material selection not only aids in achieving the desired mechanical properties but also influences factors like cost-effectiveness and manufacturability. The interplay between rigidity and toughness2 is complex, requiring a nuanced approach to material science to meet diverse industrial needs.
Polycarbonate offers high rigidity and impact strength.True
Polycarbonate is known for its excellent rigidity and impact resistance.
Excessive mineral fillers enhance toughness in plastics.False
Too much mineral filler reduces toughness, making plastics more brittle.
How Does Injection Molding Process Optimization Impact Part Performance?
Injection molding process optimization can significantly enhance the performance of plastic parts, improving both their rigidity and toughness.
By optimizing temperature, pressure, speed, and cooling time during injection molding, manufacturers can achieve superior part performance through enhanced rigidity and controlled toughness.
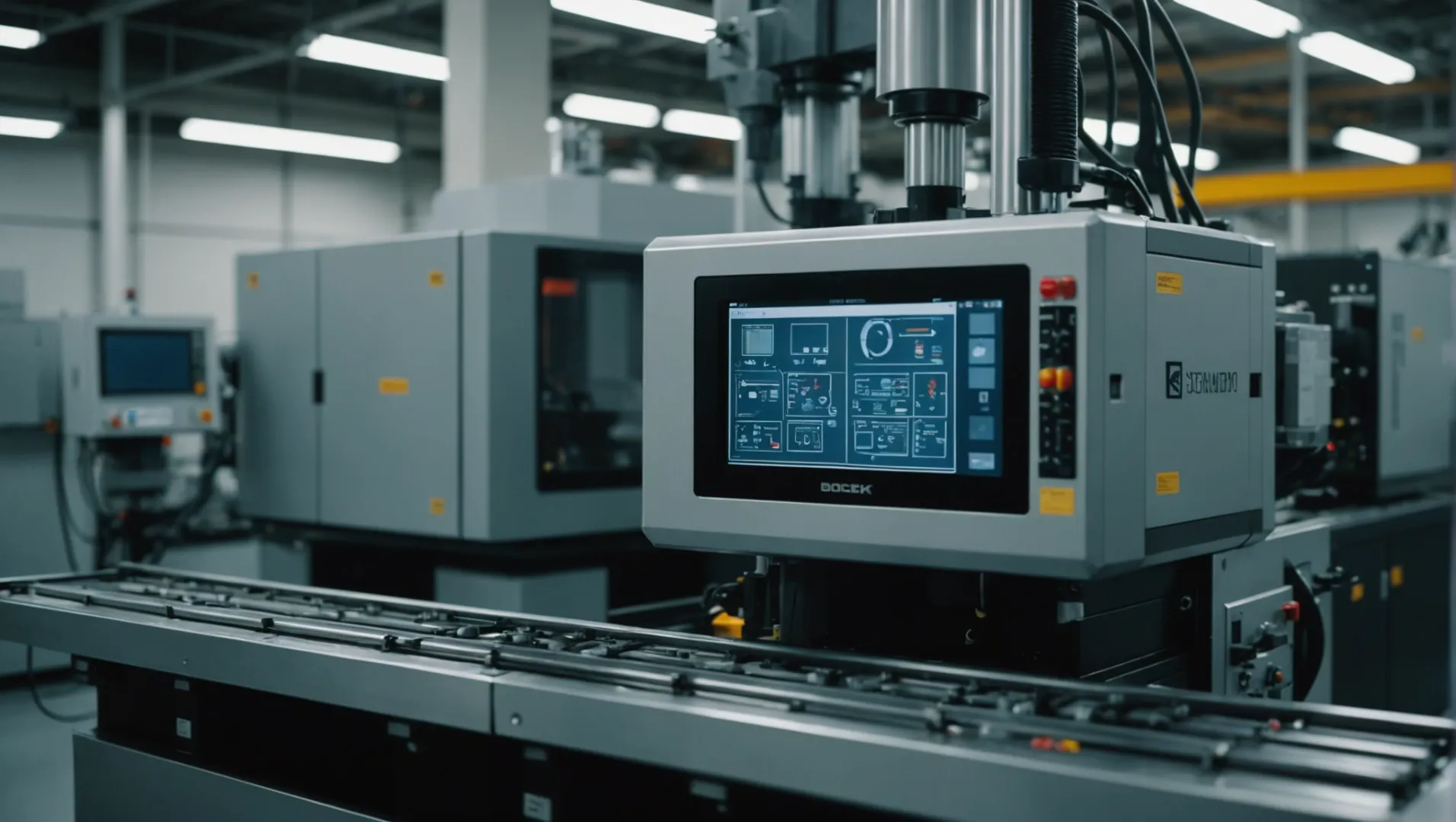
The Influence of Temperature Control
Temperature is a pivotal factor in the injection molding process3. By fine-tuning the injection and mold temperatures, manufacturers can enhance the molecular orientation and crystallization of plastics, leading to improved rigidity. However, excessive temperatures might degrade plastics, compromising their performance.
Key Considerations:
- Injection Temperature: Increasing it reduces viscosity, enhancing flow but risking degradation.
- Mold Temperature: Higher settings improve crystallization but extend cycle time.
Pressure and Speed Adjustments
Adjusting injection pressure and speed affects the compaction of the plastic material. Higher pressure typically enhances rigidity by ensuring thorough packing of the material, yet it may induce internal stress that diminishes toughness.
Pressure Insights:
- Holding Pressure: Helps compensate for shrinkage but excessive levels lead to over-compaction.
- Speed Variations: Faster speeds improve production efficiency but can exacerbate internal stresses.
Cooling Time Management
The cooling phase is crucial for controlling crystallinity and stress distribution. By extending cooling time, manufacturers allow for full crystallization, thus improving rigidity. However, this can slow down production cycles.
Cooling Time | Impact |
---|---|
Longer | Enhanced crystallinity, better rigidity |
Shorter | Increased production speed, potential stress issues |
Integrating Process Adjustments into Design
Integrating these process optimizations with strategic design considerations4 such as wall thickness and rib design can further enhance part performance. This holistic approach ensures that each component of the injection molding process works in synergy to produce parts that meet specific application demands for both strength and resilience.
Higher mold temperature improves part crystallization.True
Higher mold temperatures enhance crystallization, improving rigidity.
Faster injection speeds reduce internal stress in parts.False
Faster speeds can increase internal stresses, affecting toughness.
What Structural Design Techniques Enhance Rigidity Without Compromising Toughness?
Designing for rigidity and toughness in plastic parts demands strategic choices that ensure optimal performance without sacrificing flexibility.
Employing techniques like optimized wall thickness, strategic rib placement, and fillet design can enhance rigidity without compromising toughness in plastic injection molded parts.
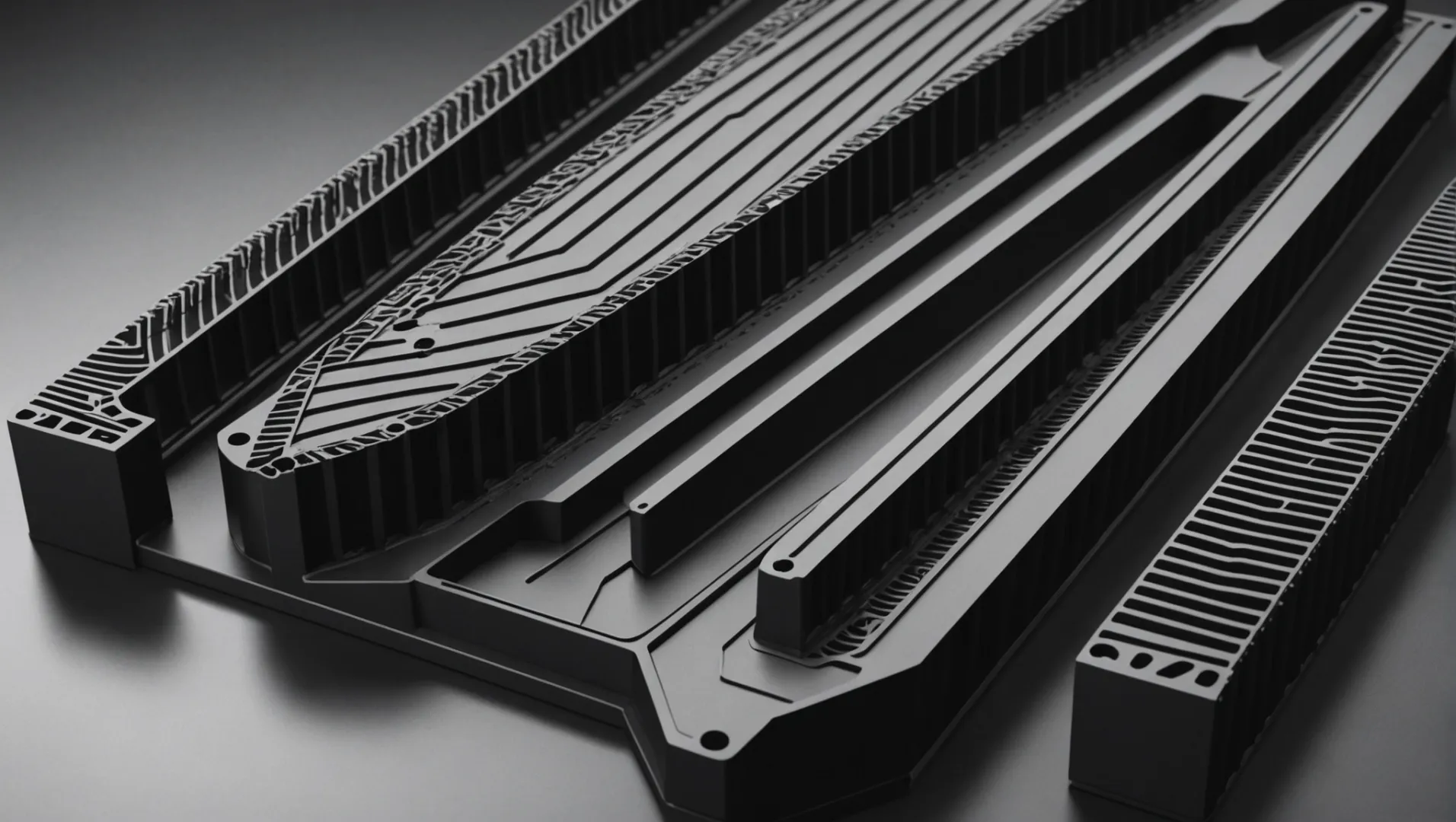
Wall Thickness Optimization
The thickness of the walls in plastic parts plays a crucial role in determining both rigidity and toughness. Gradient wall thickness is a design technique where the thickness varies depending on the stress distribution across the part. For example, areas expected to bear more load can have thicker walls, while less stressed regions can be thinner. This method reduces weight and material costs while ensuring structural integrity.
Moreover, uniform wall thickness helps avoid stress concentration and uneven cooling, which can lead to warping or cracking. When designing, consider that too thin walls may reduce rigidity, while overly thick walls can affect toughness due to internal stress5 during cooling.
Rib Design Considerations
Ribs are essential in enhancing the rigidity of plastic parts. They provide additional support without substantially increasing weight or material usage. However, the placement, shape, and size of ribs must be carefully planned. Avoid excessive rib height or width as it can lead to stress concentration points, potentially compromising toughness.
Proper bonding between ribs and the main body of the part is vital. Integrating ribs with smooth transitions rather than sharp edges helps distribute stress evenly. This practice reduces the risk of cracks and improves the overall toughness of the component.
Fillet Design for Stress Distribution
Fillets, or rounded corners, significantly reduce stress concentration at joints and intersections within plastic parts. By increasing the fillet radius, stress is more evenly distributed across surfaces, enhancing toughness. However, one must balance this with the potential decrease in rigidity due to material redistribution.
Choosing the right fillet radius depends on the specific application requirements and should be determined based on comprehensive stress analysis. A larger radius usually implies greater toughness but may compromise rigidity if not appropriately managed.
Implementing These Techniques
To achieve an optimal balance of rigidity and toughness, integrate these structural design techniques early in the development process. Computer-aided design (CAD) software can simulate stress distribution and predict potential failure points, enabling designers to refine their approaches before manufacturing begins. This proactive approach ensures that adjustments can be made to rib configurations or wall thicknesses efficiently.
Incorporating these strategies6 effectively requires a thorough understanding of material properties and performance expectations. By leveraging advanced design tools and methodologies, manufacturers can produce high-performing plastic parts tailored to specific demands.
Gradient wall thickness optimizes rigidity and toughness.True
Gradient wall thickness varies stress distribution, enhancing structural integrity.
Excessive rib height increases toughness in plastic parts.False
Excessive rib height can cause stress concentration, reducing toughness.
Why Is Post-Processing Critical in Achieving Desired Mechanical Properties?
Post-processing is pivotal in ensuring plastic parts meet specific mechanical requirements, often overlooked but vital in enhancing performance.
Post-processing in plastic manufacturing, including annealing and surface treatments, is crucial for optimizing mechanical properties by eliminating residual stresses and enhancing surface characteristics.
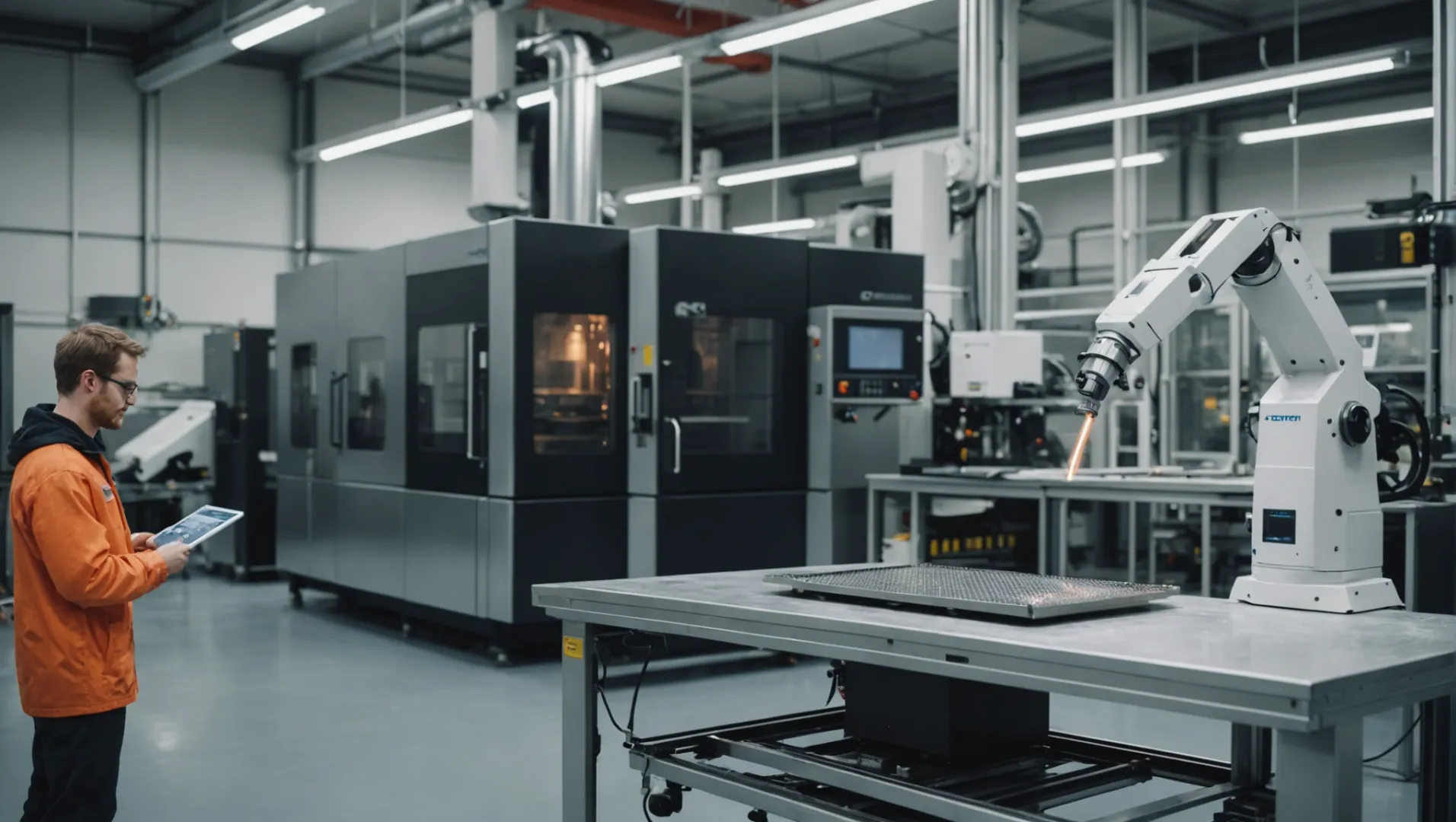
The Importance of Annealing
Annealing plays a significant role in post-processing by relieving internal stresses within plastic parts, which can arise during the injection molding process. These stresses, if not addressed, may lead to warping or cracking under load. Through controlled heating and cooling, annealing allows the molecular chains to relax, resulting in improved toughness. For example, polycarbonate parts, often used for their high impact strength, benefit greatly from annealing to ensure dimensional stability and prevent long-term deformation.
Annealing temperatures and times must be tailored to each plastic type and part size. A case study on annealing polycarbonate7 demonstrates how precise temperature control can enhance performance.
Surface Treatments for Enhanced Properties
Surface treatments such as spraying or electroplating can significantly impact the mechanical properties of plastic parts. These treatments improve surface hardness and wear resistance, which are crucial for components exposed to abrasive environments. However, while they increase rigidity, they can also inadvertently affect the material’s toughness. This trade-off needs careful consideration during the design phase.
For instance, a comparison of electroplated vs. non-plated plastics8 reveals differences in wear resistance and mechanical stability.
Balancing Act: The Trade-offs in Post-Processing
The challenge in post-processing lies in achieving a balance between improving rigidity without compromising toughness. This involves selecting appropriate methods and conditions tailored to the specific application of the part. For example, a part requiring high surface durability might prioritize harder coatings, whereas components exposed to impact might focus more on annealing.
Moreover, post-processing doesn’t operate in isolation; it complements material selection and molding processes. A holistic approach, considering comprehensive post-processing strategies9, is essential for optimizing final product performance.
In conclusion, post-processing is indispensable in refining the mechanical properties of plastic injection molded parts. By meticulously choosing post-processing techniques, manufacturers can tailor parts to meet specific performance criteria, thereby enhancing product longevity and reliability.
Annealing improves polycarbonate toughness.True
Annealing relieves internal stresses in polycarbonate, enhancing toughness.
Surface treatments reduce plastic wear resistance.False
Surface treatments increase plastic wear resistance by hardening surfaces.
Conclusion
Achieving the ideal balance requires a thoughtful approach to material choice, process control, and design. Embrace these strategies to enhance your plastic parts’ performance.
-
Explore various plastic matrices ideal for different manufacturing needs.: The Top 10 Plastic Injection Molding Materials These are the most common plastic materials for injection molding: acrylic (PMMA) acrylonitrile butadiene … ↩
-
Gain insights into the relationship between material properties for design.: A material’s toughness or stiffness (almost two opposite things) come from how its components interact with each other. ↩
-
Explores temperature’s role in enhancing rigidity during molding.: A too hot mold causes the part to warp or blister the plastic. This leads to raised sections on the surface. Inappropriate temperature levels … ↩
-
Highlights the synergy between design and process optimization.: What is the importance of mold design in injection molding? · Ensure high tolerance · Eliminate defects · Determine project feasibility · Choose the right raw … ↩
-
Explore how wall thickness affects rigidity and toughness.: Non-uniform wall thickness can also impact shear stress in the flowing plastic. At a constant fill rate, thin areas force the flow to move faster, increasing … ↩
-
Discover key strategies for optimizing plastic part design.: Most plastic product’s structural design have reinforcing ribs because ribs can increase strength without adding to the overall wall thickness. ↩
-
Explore how annealing enhances polycarbonate’s stability and durability.: BENEFITS OF POST-MACHINING ANNEALING. Improved Chemical Resistance Polycarbonate, polysulfone, and Ultem® PEI, like many amorphous (transparent) plastics may … ↩
-
Understand how surface treatments affect plastic wear resistance.: Using electroless plating can enhance results when plating onto plastics and can promote better adhesion of the metal topcoat. Electroless plating entails … ↩
-
Learn about holistic approaches to optimize plastic post-processing.: Learn new technologies and best practices for assembly, decoration, packaging, labeling, in-mold labeling, printing, ultrasonic welding, laser welding, … ↩