Injection molding is a game changer in manufacturing, blending efficiency with precision in a way that transforms industries.
Injection molding plays a crucial role in producing everyday essentials like containers and automotive parts. Its high efficiency and precision make it vital for large-scale production, ensuring consistent quality in various sectors.
But this is just the tip of the iceberg! As we dive deeper into each sector, you’ll discover the true transformative power of injection molding. Let’s explore how it impacts our world!
Injection molding is used in automotive interior parts.True
It produces dashboards, door panels, and seat parts efficiently.
How Does Injection Molding Benefit the Electronics Industry?
Injection molding revolutionizes electronics manufacturing with precision, scalability, and design versatility.
Injection molding benefits the electronics industry by producing complex, high-precision components like device housings and intricate parts, ensuring durability and aesthetic appeal. This process supports scalability and innovation in electronic products.
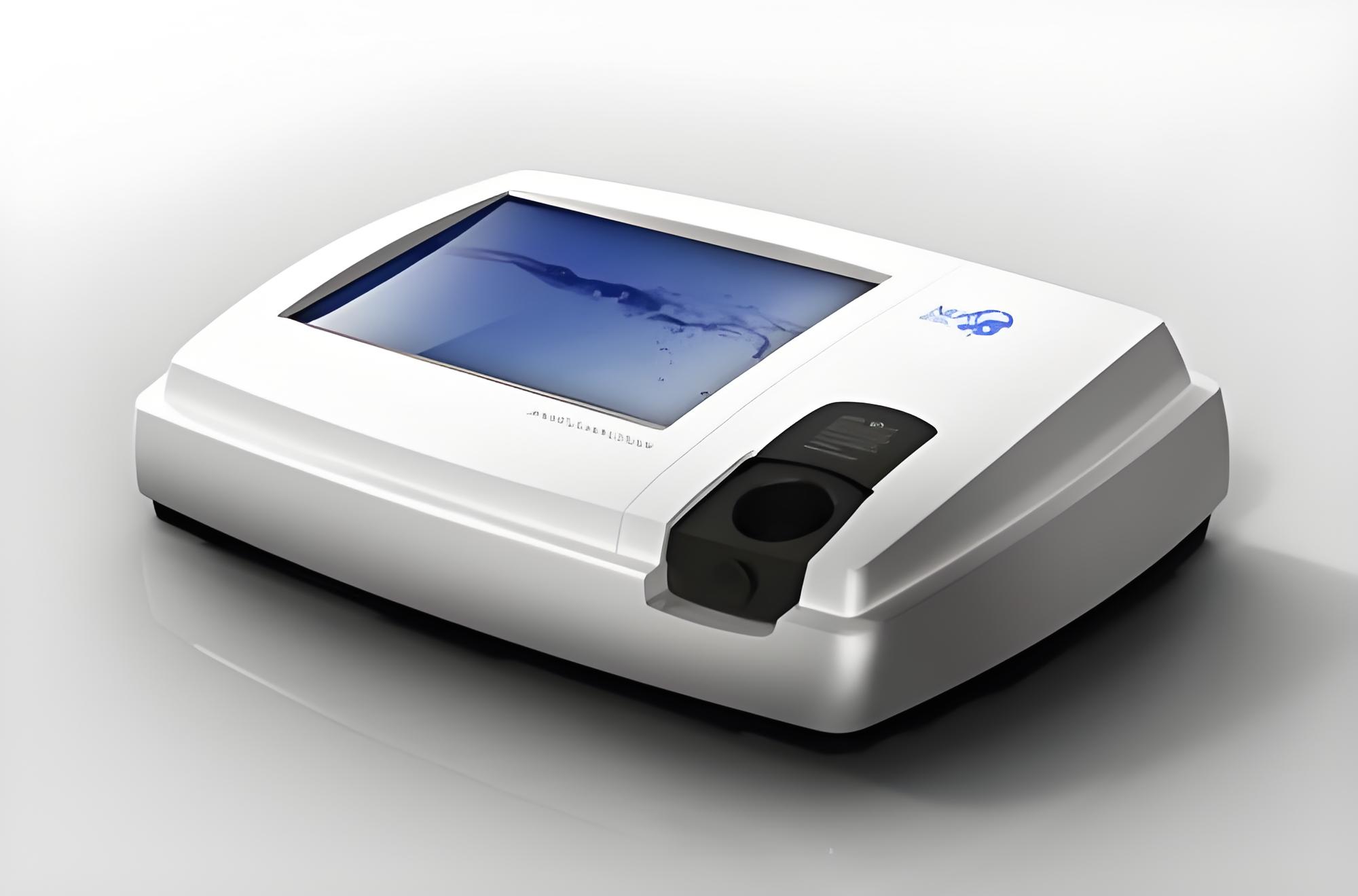
Injection Molding in Electronics
The Power of Injection Molding in Electronics
In the ever-evolving electronics industry, injection molding1 has become a cornerstone technology for producing both functional and aesthetically pleasing components. Its ability to handle complex designs with precision is unmatched, allowing manufacturers to create intricate electronic housings and parts that meet rigorous specifications. For instance, the sleek and robust shells of smartphones and laptops are often crafted using this method, ensuring both protection and visual appeal.
Versatility in Design and Function
The design flexibility of injection molding enables the production of electronic parts with varying degrees of complexity and functionality. Components such as connectors, buttons, and sockets benefit from this adaptability, allowing for custom shapes and sizes that adhere to specific performance requirements. Moreover, the process can accommodate diverse materials, including those offering enhanced conductivity or electromagnetic shielding, crucial for advanced electronic applications.
Efficiency and Scalability
One of the primary advantages of injection molding in electronics is its capacity for high-volume production without compromising on quality. This efficiency is particularly beneficial for producing small parts like microchips or connectors in large quantities. The speed and consistency of injection molding ensure that manufacturers can meet market demands swiftly, reducing lead times significantly.
Feature | Benefits |
---|---|
Precision | Consistent quality and fit |
High Volume Production | Meets large-scale demands |
Material Flexibility | Tailored properties for specific uses |
Enhancing Product Aesthetics and Durability
Beyond functionality, injection molding contributes significantly to the visual and tactile qualities of electronic products. Techniques such as texturing, coloring, and surface finishing can be integrated into the molding process to enhance appearance. Additionally, using durable plastics ensures longevity, making products more appealing to consumers who seek reliability alongside cutting-edge design.
Supporting Innovation in Electronics
The continuous advancements in injection molding technology foster innovation within the electronics sector. For example, as devices become smaller and more powerful, the need for compact yet efficient components grows. Injection molding supports this trend by enabling miniaturization without sacrificing performance or structural integrity. It also facilitates rapid prototyping, allowing designers to test new concepts quickly before committing to full-scale production.
Through these capabilities, injection molding not only meets current demands but also paves the way for future developments in electronic devices.
Injection molding ensures high precision in electronics.True
It produces complex components with precise specifications.
Injection molding cannot handle complex electronic designs.False
It excels at creating intricate designs with precision.
What Role Does Injection Molding Play in Automotive Manufacturing?
Injection molding revolutionizes automotive manufacturing by producing precise and durable components efficiently. It’s essential for both interior and exterior car parts.
Injection molding is pivotal in automotive manufacturing, producing both interior and exterior parts with precision, efficiency, and durability. It meets the industry’s high standards for safety, performance, and aesthetics, making it indispensable for mass production.
The Importance of Injection Molding in Automotive Interiors
Injection molding is integral to creating interior automotive components2 like dashboards, door panels, and seat parts. These elements not only define the aesthetic appeal of a vehicle but also meet stringent industry standards for durability and safety. The process allows for high customization, accommodating different textures, colors, and materials to suit various car models.
Efficiency and Precision
One of the standout features of injection molding is its efficiency. It enables the rapid production of complex shapes with consistent quality. Automotive interiors often require parts that can withstand extreme conditions such as fluctuating temperatures and impacts. Injection molding achieves this by using high-performance plastics that offer flame retardancy and resistance to wear and tear.
Crafting Durable Exterior Components
In the realm of automotive exteriors3, injection molding is crucial for manufacturing bumpers, headlight housings, and mirror caps. These components are exposed to the elements and must possess excellent weather resistance and impact strength.
Table: Benefits of Injection Molding for Exterior Parts
Component | Requirements | Injection Molding Advantages |
---|---|---|
Bumpers | Impact resistance, aesthetic appeal | Consistent quality, design flexibility |
Headlight Housings | Heat resistance, clarity | Precision in complex shapes |
Mirror Caps | Weather durability, lightweight | Cost-effective mass production |
Meeting Industry Standards
The automotive industry is characterized by its rigorous standards for safety and performance. Injection molding not only meets these demands but exceeds them by providing reliable solutions for mass production. It enables manufacturers to produce lightweight yet strong components that enhance fuel efficiency and overall vehicle performance.
Moreover, the use of advanced polymers in injection molding allows for innovative features such as scratch resistance and UV stability, further elevating the quality of automotive parts.
Innovation and Sustainability
Injection molding is also at the forefront of sustainable manufacturing practices. By minimizing waste through precise control over material usage and enabling the recycling of plastic scraps, it supports eco-friendly production processes. This approach aligns with the automotive industry’s growing commitment to sustainability, ensuring that production methods evolve alongside technological advancements.
Injection molding is used for automotive dashboards.True
Injection molding allows for the creation of customized dashboards with precision.
Injection molding cannot produce durable exterior car parts.False
It is crucial for making weather-resistant and impact-strong exterior components.
Why Is Injection Molding Crucial in the Medical Field?
Injection molding is pivotal in the medical field, ensuring precision and hygiene for critical equipment.
Injection molding is vital in the medical field for producing high-precision devices and consumables like syringes, infusion sets, and test tubes. This method allows for stringent hygiene standards, consistency, and large-scale production necessary for medical applications.
Precision and Hygiene in Medical Equipment
In the medical field, precision and hygiene are non-negotiable. Injection molding is a crucial method4 for producing intricate medical devices such as syringes, infusion sets, and medicine bottles. The method’s ability to maintain exact dimensions ensures that these devices meet strict safety standards. The process also supports manufacturing under sterile conditions, which is essential to prevent contamination.
Large-Scale Production Efficiency
Medical devices and consumables often require mass production to meet healthcare demands. Injection molding excels in this area by enabling rapid production of high-volume items like test tubes, culture dishes, and gloves. Its efficiency not only lowers production costs but also ensures a steady supply of critical medical items.
Medical Products | Application | Advantages of Injection Molding |
---|---|---|
Syringes | Drug delivery | Precision, hygiene, and sterility |
Infusion sets | Fluid transfer | Consistent quality and mass production |
Test tubes | Laboratory use | Large-scale production |
Versatility in Design and Material Use
Injection molding offers flexibility in material selection, allowing manufacturers to choose from a range of medical-grade plastics. This versatility means that products can be customized for specific applications, such as flexible tubing or rigid containers. The method’s adaptability enables innovation in medical design, ensuring that new products can be quickly brought to market to address emerging healthcare needs.
Meeting Regulatory Standards
Stringent regulatory standards govern the production of medical devices. Injection molding helps manufacturers comply with these standards by providing traceability and consistency in every batch produced. This capability is vital for gaining regulatory approvals and maintaining trust among healthcare providers.
The role of injection molding in the medical field is transformative, offering efficiency, precision, and compliance with regulatory requirements. It continues to be a cornerstone in the production of reliable and safe medical products.
Injection molding ensures sterility in medical devices.True
Sterility is maintained through controlled manufacturing environments.
Injection molding limits material choice for medical products.False
It allows diverse medical-grade plastics, enhancing design versatility.
How Are Toys Revolutionized by Injection Molding Techniques?
From intricate building blocks to vibrant dolls, injection molding has transformed toy manufacturing, ensuring creativity meets durability.
Injection molding revolutionizes toy manufacturing by enabling intricate designs, vibrant colors, and durable products. It allows for mass production while maintaining high precision and cost-effectiveness.
Intricate Designs and Creativity
One of the most significant advantages of injection molding in toys5 is the ability to create intricate and complex designs. This technique allows manufacturers to mold plastic into virtually any shape imaginable, giving designers the creative freedom to bring innovative toy concepts to life. For instance, the intricate interlocking systems found in popular building block sets are made possible by the precision of injection molding.
Vibrant Colors and Textures
Injection molding facilitates the use of a variety of colors and textures, resulting in toys that are visually appealing to children. By adding colorants during the molding process, manufacturers can create toys with vibrant hues and interesting textures without the need for additional painting or finishing. This not only enhances aesthetic appeal but also reduces production steps, making the process more efficient.
Durability and Safety
Safety is paramount in toy manufacturing, and injection molding plays a critical role in producing durable toys that withstand wear and tear. The use of high-quality polymers ensures that toys can endure rough handling without breaking. Additionally, the precision of injection molding guarantees that small parts fit together securely, reducing potential hazards for children.
Cost-Effectiveness in Mass Production
The efficiency of injection molding makes it ideal for mass production. Once the initial mold is created, it can be used repeatedly to produce large quantities of toys, significantly reducing unit costs. This efficiency is particularly beneficial for seasonal or trending toys that require quick turnaround times.
Feature | Benefit |
---|---|
Complex Designs | Enhances creativity and functionality |
Vibrant Colors | Improves visual appeal |
Durable Materials | Ensures safety and longevity |
Cost-Efficient Production | Supports affordable mass production |
Educational and Interactive Toys
Educational toys such as puzzles and Rubik’s cubes6 benefit greatly from injection molding. These toys require precise dimensions to function correctly and provide an engaging learning experience. The method ensures that each piece fits perfectly, offering a seamless user experience.
Overall, injection molding has not only revolutionized how toys are made but has also elevated the standards of safety, quality, and creativity in the industry.
Injection molding allows for intricate toy designs.True
The precision of injection molding enables complex, detailed toy designs.
Injection molding increases toy production costs.False
It reduces costs by enabling efficient mass production with reusable molds.
Conclusion
Injection molding revolutionizes production across industries by combining efficiency with precision. Its potential for innovative solutions is immense—explore its applications to stay ahead in the game.
-
Explore detailed benefits of injection molding in electronics manufacturing.: The Benefits of Plastic Injection Molding Electronic Products · Protect Products with Plastic Enclosures · Reduce Weight with Plastic · Create Less Waste. ↩
-
Discover how injection molding enhances car interiors’ quality and customization.: An injection molded design is easy to mass produce quickly thanks to the swiftness of the machinery and the fast process of molding the resin. ↩
-
Learn why injection molding is essential for durable automotive exteriors.: An injection molded design is easy to mass produce quickly thanks to the swiftness of the machinery and the fast process of molding the resin. ↩
-
Discover how injection molding meets medical industry’s precision and hygiene standards.: Plastic injection molding enables the production of medical components used in labware equipment and instrumentation, diagnostic disposables … ↩
-
Discover how injection molding enhances toy design and production efficiency.: Plastic injection molding is ideal for making these bricks, model kits, and similar items because it can scale up production and ensure precise shapes and sizes … ↩
-
Learn why injection molding is ideal for producing educational toys.: In summary, plastic injection molding offers an efficient, economical, precise, and versatile method of toy production. These advantages make injection molding … ↩