The smallest details often hold great importance. In injection molding, the parting line greatly affects a product’s precision. It seems small but matters a lot.
The parting line changes the size accuracy, shape quality and fit of injection molded products. Poor handling of the parting line leads to problems like extra material, uneven surfaces or misalignment. It harms the product’s quality and function.
Looking back at my time in mold design, I have observed how a small detail like the parting line really impacts a product’s success. It can help or hurt the product. Challenges with keeping dimensions stable or surfaces flat remind me of the delicate balance in this work. Parting lines truly affect the quality of products.
Dimensional deviation can cause flash in molded parts.True
Flash occurs when plastic overflows at the parting line due to poor fit.
Poor parting line placement affects assembly position accuracy.True
Incorrect parting lines can cause misalignment in assembled components.
What is Dimensional Accuracy in Injection Molding?
Do you ever think about the way those perfectly shaped plastic pieces are created?
Dimensional accuracy in injection molding means that every part produced closely matches the planned design. This precision is very important for the parts to work correctly and perform well. Many factors impact this accuracy, such as the mold’s quality, the precision where the mold halves meet and good process control.
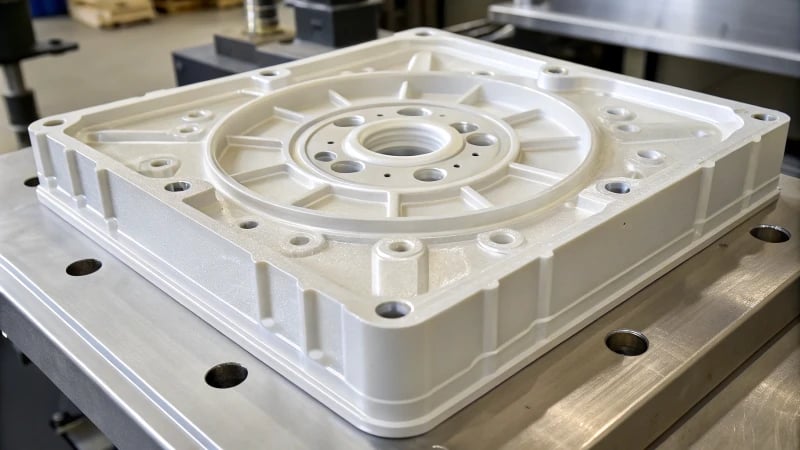
Understanding Dimensional Accuracy
I remember when I started with a project that depended on exact measurements. It was for a small piece inside an electronic device. This part had to fit exactly with others. I realized how important it was for the final product to match the designed size perfectly. This includes things like measurement mistakes, steadiness, and precise placement.
Factors Affecting Dimensional Accuracy
-
Dimensional Deviation: Picture a seam on your favorite shirt. If it’s sewn badly, the whole look gets spoiled. The same goes for a parting line not done well; extra material spills over and trimming it might leave the part smaller than needed. This happened to me once with gears. Just a tiny reduction in tooth thickness messed up their work.
-
Dimensional Stability: Molds wear out over time, which changes product size during production. It’s like a favorite sneaker losing shape after much use. If the mold doesn’t close right each time, the sizes can vary. I discovered this while making parts with different sizes in one batch.
Factor | Impact on Dimensional Accuracy |
---|---|
Parting Line Quality | Affects dimensional deviation and stability |
Mold Fit | Causes flash formation and size reduction |
Mold Wear | Leads to size changes over repeated cycles |
Shape and Position Accuracy
-
Shape Integrity: Creating complicated shapes takes skill. But if a mold’s line isn’t just right, things can mess up. I’ve noticed thin parts bending under pressure, failing to meet design needs.
-
Position Accuracy: It’s crucial for putting parts together. Any mistake here can mess up assembly. This is like facing uneven gaps in car interiors, something I dealt with many times in car projects.
Improving Dimensional Accuracy
We need advanced CAD software1 for precise mold designs and strong quality checks to improve accuracy. Regular mold care is a lesson I learned – it’s key for keeping output quality steady.
By grasping these aspects, we better our production methods, create better products, and make clients happy.
Parting line quality affects dimensional accuracy.True
Poor parting line quality can lead to flash formation, altering dimensions.
Mold wear does not impact product size.False
Mold wear can cause size changes over repeated cycles, affecting accuracy.
How Do Parting Lines Influence Shape Integrity?
Ever think about how a small line, like a parting line, affects the whole design?
Parting lines influence the shape’s strength. They affect how accurate the dimensions are. Surface smoothness also changes. Assembly precision suffers too. Bad design or wear leads to mistakes. Products might not work correctly. Fit could be problematic.
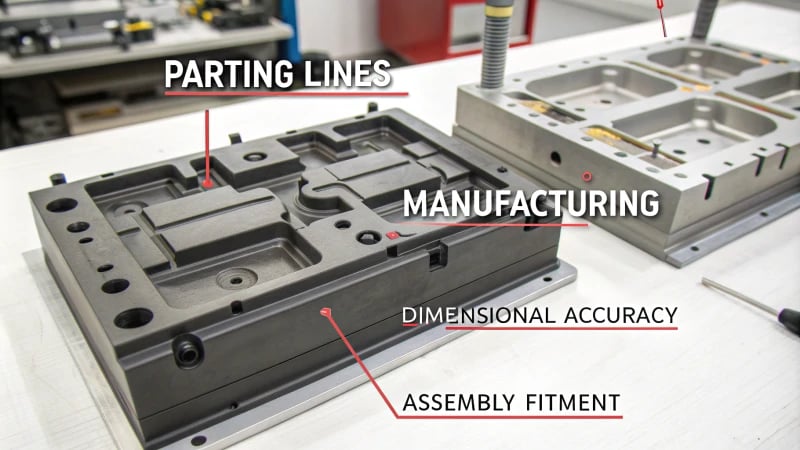
The Role of Parting Lines in Dimensional Accuracy
Once, I worked late at night, trying to understand why our plastic gears didn’t fit together right. Parting lines caused the problem. If the mold isn’t sealed perfectly, small unwanted pieces appear when you take out the product. I had a big "aha" moment when I saw this could really reduce gear tooth thickness and hurt their accuracy2. Important fact: it affects gear performance.
Dimensional stability also faced challenges. On one project, the mold wore down at the parting line over time. Each injection cycle caused tiny size changes, creating major problems for our precise parts. Mold integrity is absolutely necessary to keep size consistent. Yes, it’s that important.
Challenge | Impact |
---|---|
Dimensional Deviation | Reduced tooth thickness |
Dimensional Stability | Size fluctuations over cycles |
Influence on Shape Accuracy
Parting lines can silently ruin shape accuracy. Projects sometimes failed because molds didn’t close tightly, resulting in uneven surfaces. This is a nightmare for products like optical lens brackets, where high precision is really vital, influencing overall performance3. For real, it’s crucial.
Complex shapes offer additional challenges. Once, I placed a parting line on a thin-walled area without considering molding pressure. Walls deformed and we had to start over. I learned that careful placement is essential.
Assembly Position Accuracy Concerns
Precision in assembling composite products also depends on parting lines. During an automotive interior project, an irregular parting line caused uneven gaps and poor assembly quality. This highlighted how important precision is for the right fitment4 and functionality. Designers have to definitely consider these factors to maintain shape integrity through production cycles. It’s a careful balance, yet vital to meet the highest standards.
Parting lines cause dimensional deviation.True
Improperly fitted molds at parting lines can lead to size deviations.
Surface flatness is unaffected by parting lines.False
Poor mold closure at parting lines can compromise surface flatness.
Why Is Position Accuracy Crucial for Assembly?
Struggling with a puzzle where pieces don’t fit together? Assembling something feels like that without exact position accuracy.
Position accuracy in assembly is crucial. Components fit perfectly, reducing errors and increasing efficiency. Precision matters. It stops shape and dimension mistakes. High-quality assemblies are the result.
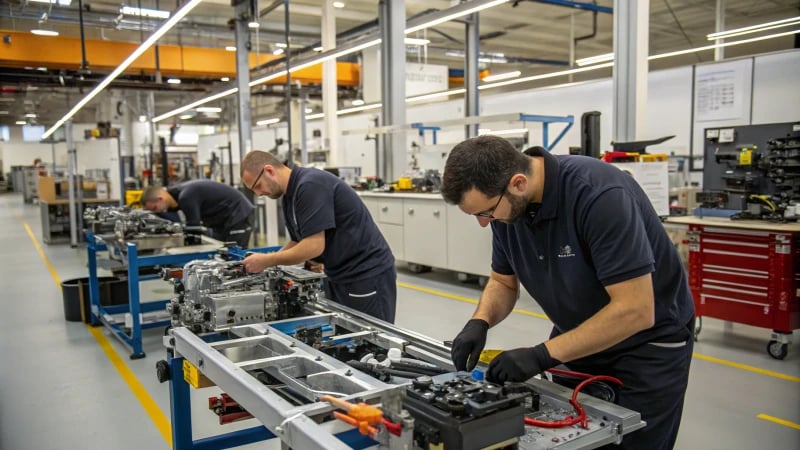
The Role of Position Accuracy in Assemblies
Years of working with molds taught me that even tiny misalignments create big problems later. Once, a small error of less than a millimeter caused parts not to fit well, resulting in a whole batch being thrown away. Accurate positioning lays the groundwork for manufacturing. Each piece must fit perfectly into the whole to avoid issues.
For example, dimensional accuracy5 is crucial for maintaining precise alignments between parts. When parts are incorrectly aligned, the resulting assemblies can suffer from increased wear or even failure.
Impact on Dimensional Stability
There was a project involving precise plastic gears. Some gears turned out slightly smaller after removing excess material. This small change prevented the gears from working together smoothly. Extra wear resulted from this misalignment.
Aspect | Impact of Inaccuracy |
---|---|
Dimensional Deviation | Causes irregular sizes |
Surface Flatness | Results in uneven surfaces |
Shape Integrity | Leads to incomplete forms |
Dimensional stability really matters for keeping product quality high over time. It does.
Guaranteeing Shape Integrity
I remember when we made plastic brackets for optical lenses. The surface had to be very flat for proper function. Any small error could ruin lens performance. This taught me how important precise shape is.
In assembly, maintaining shape integrity6 is key. Poor positioning damages shape integrity easily and leads to gaps or misalignments.
Importance of Assembly Position Accuracy
In the car industry, even small component misalignments ruin both look and function. I worked on a car interior project where uneven gaps were ugly and caused noise and weakened structure.
Properly aligned parts enhance the longevity and performance of assemblies. By focusing on accurate positioning, manufacturers can achieve higher quality products, reduce waste, and improve overall efficiency.
Understanding these aspects encourages professionals to prioritize precise positioning in their manufacturing processes7. Precision in manufacturing is crucial; it saves time, raises reliability, and ensures final products meet all promises.
Position accuracy prevents assembly failures.True
Accurate positioning ensures components fit correctly, preventing wear or failure.
Dimensional deviation has no impact on assemblies.False
Deviations cause irregular sizes, affecting the assembly's performance.
How Can I Master Parting Lines in Injection Molding?
Ever been puzzled by those annoying lines in your plastic designs? You’re not alone! Problems often bring new chances for precision and perfection.
To master parting lines, focus on mold alignment, careful maintenance and strategic line placement. These steps help avoid visible defects. Products will maybe achieve their dimensional and shape accuracy goals.
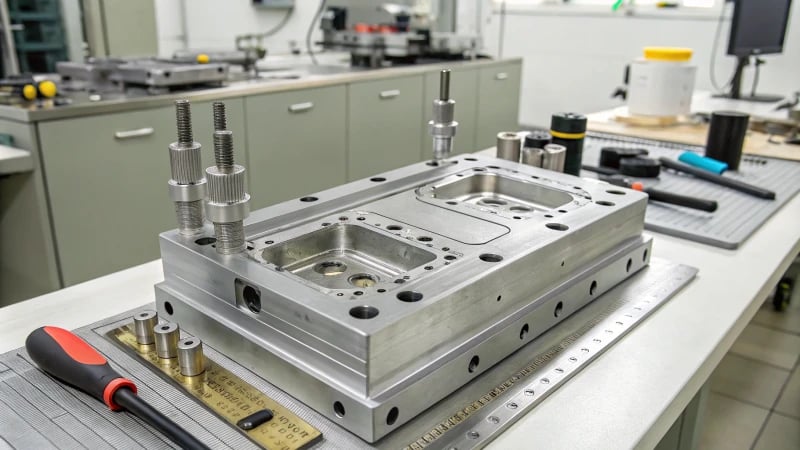
Embracing Mold Alignment
I remember my early days in mold design. I realized how important mold alignment truly was. It’s like creating a perfect sandwich. If bread slices don’t match, you get a mess. Accurate alignment means mold halves fit together well, preventing issues like dimensional deviation8. Misalignment brings material leaks and unwanted extra bits, turning an exciting project into repair work. Regular check-ups are my preferred strategy to keep everything working smoothly.
The Lifesaver: Regular Maintenance
I ignored maintenance on a project once, thinking molds could last longer—big mistake! This situation taught me that worn or damaged molds hurt the quality of the parting line. A strict maintenance plan now keeps my molds in excellent condition, preventing defects before they start. I use smart monitoring systems to catch early signs of problems; these systems are my safety net.
Crafting the Perfect Line Placement
Smart placement of parting lines changed my approach. I avoid placing them on important surfaces or thin areas where they might risk shape integrity9. In complex designs, working with mold makers is crucial to find the best places for these lines. Teaming up like this reduces visual issues and really benefits product performance.
Keeping Surface Defects at Bay
Surface flatness can suffer if parting lines aren’t managed correctly. I’ve discovered that improving mold closing pressure and using surface treatments preserve a product’s smooth finish. During design, I always consider how parting line locations affect surface quality.
Aspect | Consideration |
---|---|
Dimensional Accuracy | Prevent flash by ensuring tight mold fitting |
Shape Integrity | Avoid placing lines on thin or complex surfaces |
Position Accuracy | Critical for components requiring precise assembly |
Teaming Up with Mold Designers
Communication with mold designers is like sharing a favorite recipe—it is essential for good results. I ensure we discuss assembly position accuracy10 and any specific needs early on. This collaboration often leads to creative ideas that really improve product quality.
Leveraging Advanced Technologies
Tech tools like 3D scanning and CAD software have improved my methods for managing parting lines by providing precise simulations and adjustments before production begins, reducing trial-and-error phases significantly.
Using these practices in your work helps maintain high standards in injection molding projects, achieving both visual appeal and excellent functionality in your finished products.
Mold alignment prevents flash and size alteration.True
Proper mold alignment ensures tight fitting, preventing material leakage.
Ignoring parting line placement affects shape integrity.True
Strategically placing parting lines avoids defects on critical surfaces.
Conclusion
The parting line in injection molding significantly impacts dimensional accuracy, shape integrity, and assembly precision, affecting product quality and functionality if not managed properly.
-
Learning about CAD tools aids in creating accurate molds, improving product quality. ↩
-
Learn about the impact of parting lines on gear functionality and meshing precision. ↩
-
Discover how surface flatness influences the performance of optical components. ↩
-
Understand the role of parting line precision in ensuring proper automotive interior fitment. ↩
-
This link provides insights into why maintaining precise dimensions is crucial for effective manufacturing processes. ↩
-
Learn more about strategies to ensure components maintain their intended shapes during assembly. ↩
-
Explore methods to enhance manufacturing efficiency and product quality through optimized processes. ↩
-
Discover techniques to maintain mold alignment and reduce dimensional deviation, ensuring precise product sizes. ↩
-
Learn about the impact of parting line placement on shape integrity, particularly in complex molded parts. ↩
-
Explore why assembly position accuracy is crucial for high-quality plastic components and their assemblies. ↩