Finding the dividing line in injection molding reveals secrets to improving design and making manufacturing more efficient. This knowledge really benefits production. It is very important.
In injection molding, the parting line is the junction where mold sections join together. This spot shapes both the appearance and performance of the product. Careful placement of this line holds great importance for reaching high-quality results.
The parting line really affects many parts of product design. I recall my surprise when I first understood its impact. Something small changes a lot. It affects looks by leaving marks on surfaces and also influences strength. Incorrect placement might cause stress in important parts. Stress weakens products. Learning these details is very important for all designers. Designs need to be both beautiful and strong.
Parting lines only affect the appearance of products.False
Parting lines affect both appearance and structural integrity.
Flash at parting lines indicates poor mold design.True
Flash occurs due to mold design or manufacturing inaccuracies.
How Does the Parting Line Form in Injection Molding?
Have you ever thought about the mysterious line on your molded items? It’s named the parting line. It plays an interesting role in injection molding.
The parting line appears in injection molding where the moving and still mold parts connect. This line impacts the look and strength of the final item because it divides when the mold opens. The parting line dictates both style and durability.
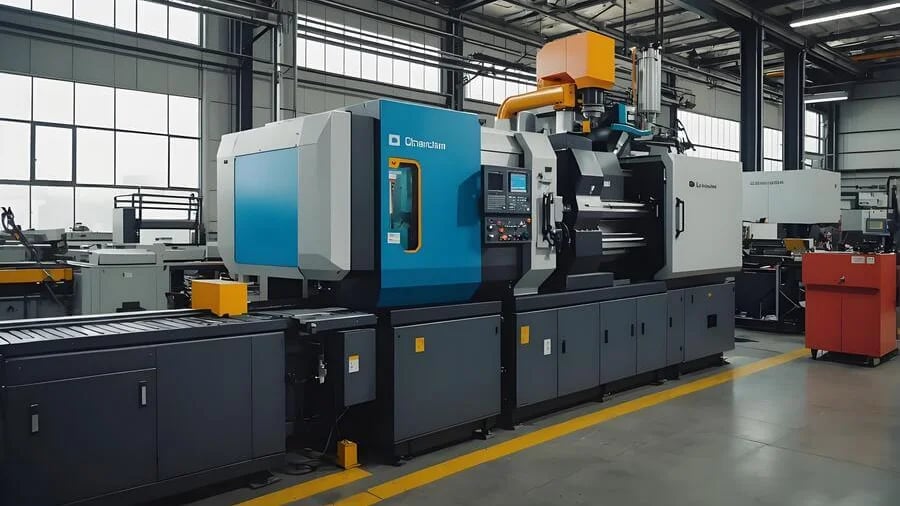
Understanding the Parting Line
When I began working in mold design, I saw small lines on plastic parts and wondered how they appeared. These lines are called parting lines, important in injection molding1. They mark where moving parts, like sliders and ejectors, meet the fixed mold. You see them clearly when the mold opens to release a new product.
Formation Process
The process starts with mold design. Imagine hot plastic flowing into the mold, creating a shape. As it cools and the mold opens, the product comes out, following this line. It feels like witnessing a magic trick but relies entirely on engineering.
Factors Influencing Parting Line | Impact |
---|---|
Mold design precision | Surface finish and flash |
Injection pressure | Structural integrity |
Impact on Product Design
Appearance Impact
A poorly placed parting line can leave unattractive marks on a product. If the design lacks precision, flash – thin plastic overflow sheets – may occur. This is not ideal for smooth electronic devices.
Structural Impact
Structurally, a wrong parting line can cause issues. Stress points weaken the product and poor alignment makes assembly difficult. It’s like forcing a square peg into a round hole—frustrating.
Uneven lines might impede assembly performance2.
Managing Parting Lines
I’ve learned it is vital to consider these lines early to make strong and good-looking products. Modern CAD tools now help predict and reduce these issues much easier.
- Select good mold materials
- Use precise machining methods
- Conduct routine maintenance
Using these strategies helps achieve both beauty and functionality in products, keeping customers satisfied.
To learn more about improving mold designs, check out related techniques3.
The parting line affects product aesthetics in injection molding.True
Visible marks from the parting line can reduce visual appeal.
Poor mold design does not impact the parting line formation.False
Design accuracy is crucial to avoid flash and ensure quality.
What Are the Visual Effects of a Parting Line on Products?
Parting lines might seem like a minor detail. They play an important role in product design, especially in injection molding. Parting lines affect both looks and usefulness.
A parting line forms where mold halves join in injection molding. This line affects how a product looks and how strong it is. Good design reduces these lines. It really improves the look. It also increases durability.
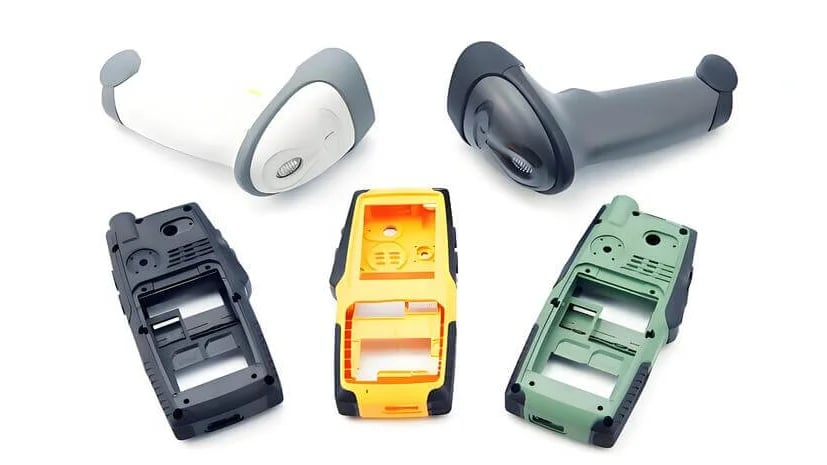
Defining the Parting Line
My path through the complex world of injection molding4 shows parting lines as both a problem and a chance. These lines are where the mold’s moving and still parts meet. When plastic hardens, it often leaves a small line – a clear sign of the mold’s shape.
Causes and Formation
During injection, hot plastic fills every corner of the space made by the molds. As the mold separates, this spot is where the item detaches, marking the parting line. Understanding this is like knowing where a seam on your jacket will be.
Aesthetic Implications
Aesthetic problems cause worry! I once worked on an electronic case where a bad parting line looked like a scratch on a new car. Such lines or thin plastic sheets – called flashes – can really damage how a product looks.
Factor | Impact |
---|---|
Precision in Mold Design | Reduces visibility of parting line |
Mold Manufacturing Accuracy | Prevents flash formation |
Structural Considerations
Parting lines affect more than looks; they can change a product’s strength. Placing a line at a stress point is like putting a crack in a dam. Stress here creates weak spots, hurting the product’s strength.
Examples and Best Practices
Over time, I learned the importance of placing the parting line in safe areas or using advanced mold design methods5. These ways increase product strength. They keep the beauty we want in our designs, too. This is very crucial.
Considerations in Design
Designers, be it experienced ones like Jacky or novices, need to mix visual and practical thoughts about parting lines. Using CAD tools well can shift a design from normal to amazing by perfect line placement. Learning about injection molding methods6 offers many benefits for reducing flaws and improving quality. It’s a trip worth taking for anyone who seeks the best in manufacturing.
Parting lines always enhance product appearance.False
Parting lines can leave marks, reducing the product's aesthetic quality.
Parting line placement affects product strength.True
Improper parting line placement can cause stress concentration, weakening the product.
Can Parting Lines Affect Structural Integrity?
Think back to a time when selecting between appearance and strength was necessary for your new project. Parting lines in injection molding probably offer a way to combine both aspects.
Parting lines affect structural strength by adding stress points. These lines weaken the machine parts’ characteristics. Assembly precision may suffer if these lines are not in the correct place. Proper placement is really important.
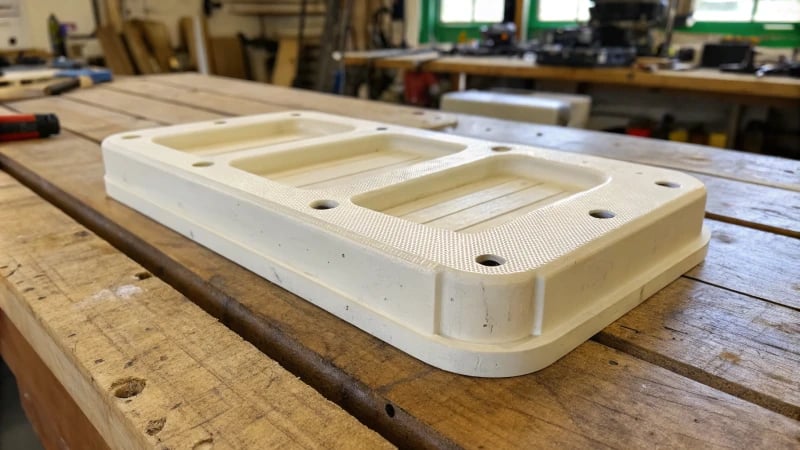
Understanding Parting Lines in Injection Molding
The parting line is a small but important divide in injection molding. Picture it like the seam on your favorite jacket. This line is where two sides meet to become one. In injection molding, it separates the parts of a mold that move and those that stay still. It shows where the magic happens when the mold closes and the liquid plastic flows in. It’s very much like stitching your jacket to stop it from falling apart.
Formation and Implications of Parting Lines
When the mold opens, parting lines show on the finished product. It’s like turning the pages of a book; you see where everything splits to reveal the story. These lines always appear, but placing them carefully can really change everything.
Aspect | Impact on Product |
---|---|
Appearance | Parting lines can leave visible marks, affecting aesthetic quality, especially in consumer electronics. |
Structure | Incorrect placement can lead to stress concentration, reducing strength and impacting assembly accuracy. |
Mitigating Structural Impact
I spent many hours at my desk, with CAD software7 lights on, making sure each parting line is in the best spot. If a line falls in a high-stress area, it could lead to trouble – like your favorite chair breaking beneath you. Careful planning really helps. It truly does.
Strategies for Optimizing Parting Line Placement
- Material Choice: Some materials handle parting line problems easily, like a hero deflects bullets.
- Mold Design Precision: Precision here is like a finely tuned musical instrument – everything is perfectly in place.
- Stress Analysis: Think of a stress test as a magic crystal ball showing where problems might hide.
Through these strategies, parting lines support rather than weaken designs. They keep both looks and function strong. For more tips on improving your manufacturing skills, dive into mold design techniques8.
Parting lines affect product aesthetics.True
Visible marks from parting lines can affect the aesthetic quality of products.
Incorrect parting line placement reduces strength.True
Stress concentration from poorly placed parting lines can weaken structural integrity.
How can I optimize mold design to reduce parting lines?
Do those annoying lines on new molded products ever frustrate you? Smart mold design strategies offer a way to completely remove them.
I focus on placing lines thoughtfully to reduce parting lines in injection molding. Precision matters in mold design, which results in smoother surfaces. Right materials improve strength. This leads to better products.
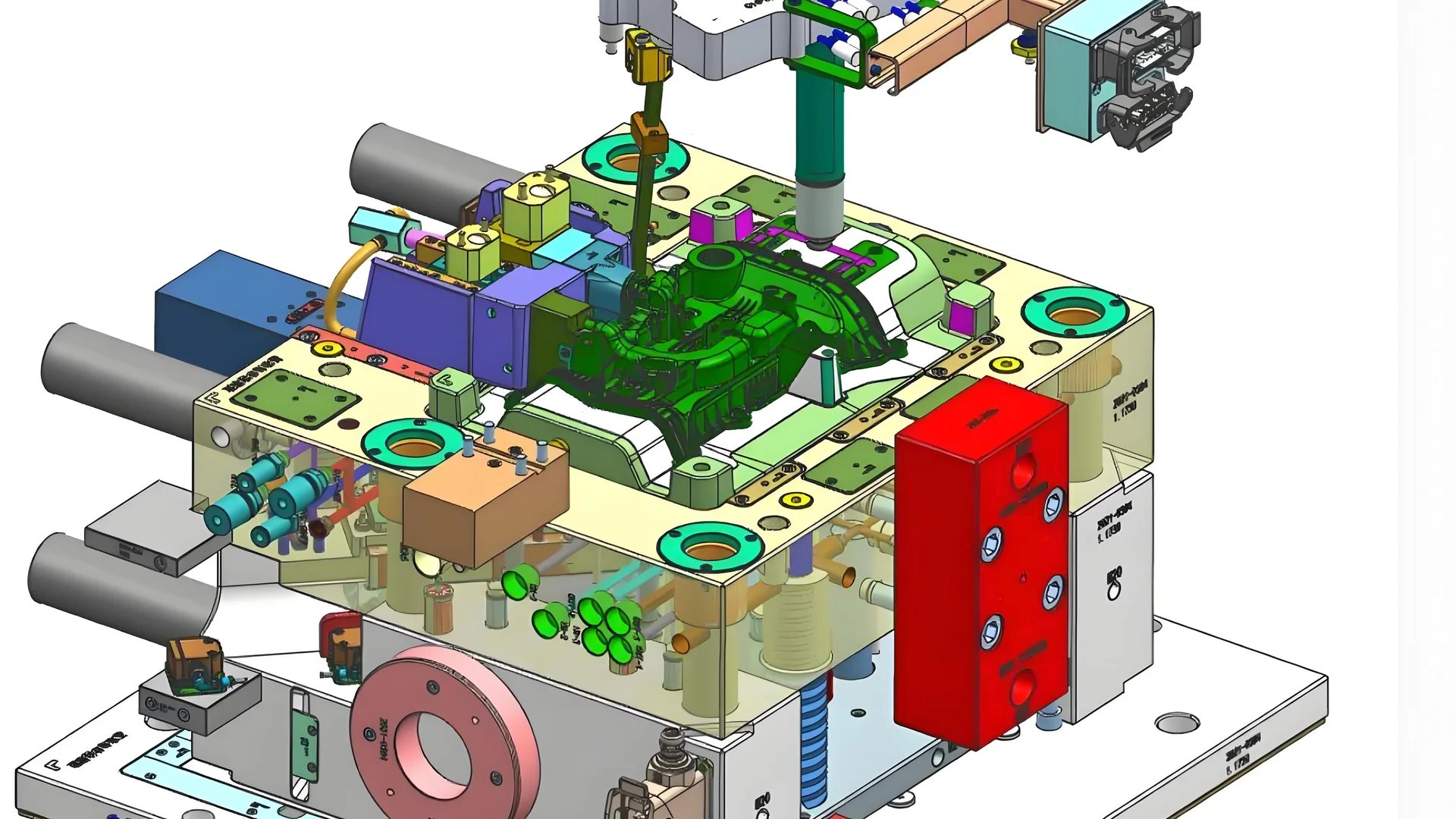
Understanding Parting Lines in Injection Molding
The parting line is where mold pieces join. It’s like a seam on clothes. Sometimes it’s easy to see; other times, it’s hidden. In injection molding, this line appears when the mold closes on the hot plastic and becomes visible when the mold opens. If not placed right, it might leave ugly marks or make the product weak.
Cause of Parting Line Formation
Think about putting too much jam in a sandwich—it spills out the sides. This is similar to how it works here. The plastic fills the space inside the mold, and as it cools, the parting line forms where the mold parts meet. Good design changes how visible this line is; it really matters. Sometimes it can almost disappear.
Impact on Product Quality
Impact Type | Description |
---|---|
Appearance | Visible lines or flash may form, impacting visual quality, especially in products like electronics. |
Structural | Incorrect line placement can weaken structural integrity or affect assembly precision. |
Strategies to Optimize Mold Design
Strategic Positioning of Parting Lines
Parting lines in hidden places can be helpful. If designing a phone case, place lines where fingers don’t notice them. Consider product use and aesthetic requirements9 when determining line placement to reduce visual interruptions on the product surface.
Enhancing Mold Precision
Precision is crucial for reducing flash formation by ensuring tighter fits between mold parts. Advanced CAD tools help create detailed designs—it’s like a perfectly tailored suit—and benefit from technologies that enhance mold accuracy10.
Material Selection Considerations
Good materials are crucial too. Selecting materials with appropriate shrinkage and flow characteristics helps keep lines less visible and maintain better mold integrity while minimizing defect risks.
Materials resisting bending keep the shape stable, reducing flaws.
These strategies help products look good and stay strong; they really matter for manufacturing efficiency as well as aligning product needs with what factories do best. New ideas appear often, offering exciting ways to solve old issues with skill and charm.
Parting lines are only an aesthetic concern.False
Parting lines affect both aesthetics and structural integrity.
Material choice affects parting line prominence.True
Materials with suitable shrinkage reduce warping and minimize lines.
Conclusion
The parting line in injection molding is crucial for product aesthetics and strength, influencing design quality by affecting appearance and structural integrity during manufacturing.
-
Understanding injection molding fundamentals helps grasp how parting lines are formed in molds. ↩
-
Exploring parting line impact on assembly aids in designing better-fitting products. ↩
-
Enhancing mold design techniques can reduce negative effects of parting lines. ↩
-
Understand what injection molding is to grasp how parting lines are formed in this process. ↩
-
Explore advanced techniques to manage parting lines effectively and improve product quality. ↩
-
Learn techniques to reduce defects and enhance product quality in injection molding. ↩
-
Discover CAD tools that help optimize parting line placement for improved structural integrity. ↩
-
Uncover mold design methods that ensure structural integrity and quality in plastic products. ↩
-
This link provides insights into balancing function and aesthetics in design. ↩
-
Explore how modern CAD tools improve mold precision and reduce defects. ↩