Imagine a world where every product coming off the assembly line meets the highest standards of quality. This is becoming a reality with real-time monitoring in injection molding.
Real-time monitoring in injection molding enhances quality by continuously tracking key parameters like temperature, pressure, speed, and position. This allows for immediate adjustments, ensuring consistent product quality and reducing defects.
But what does this really mean for manufacturers? Dive deeper with me as we explore how each monitored parameter plays a crucial role in achieving efficiency and cost savings.
Real-time monitoring reduces defects in injection molding.True
Continuous tracking of parameters allows immediate adjustments, enhancing quality.
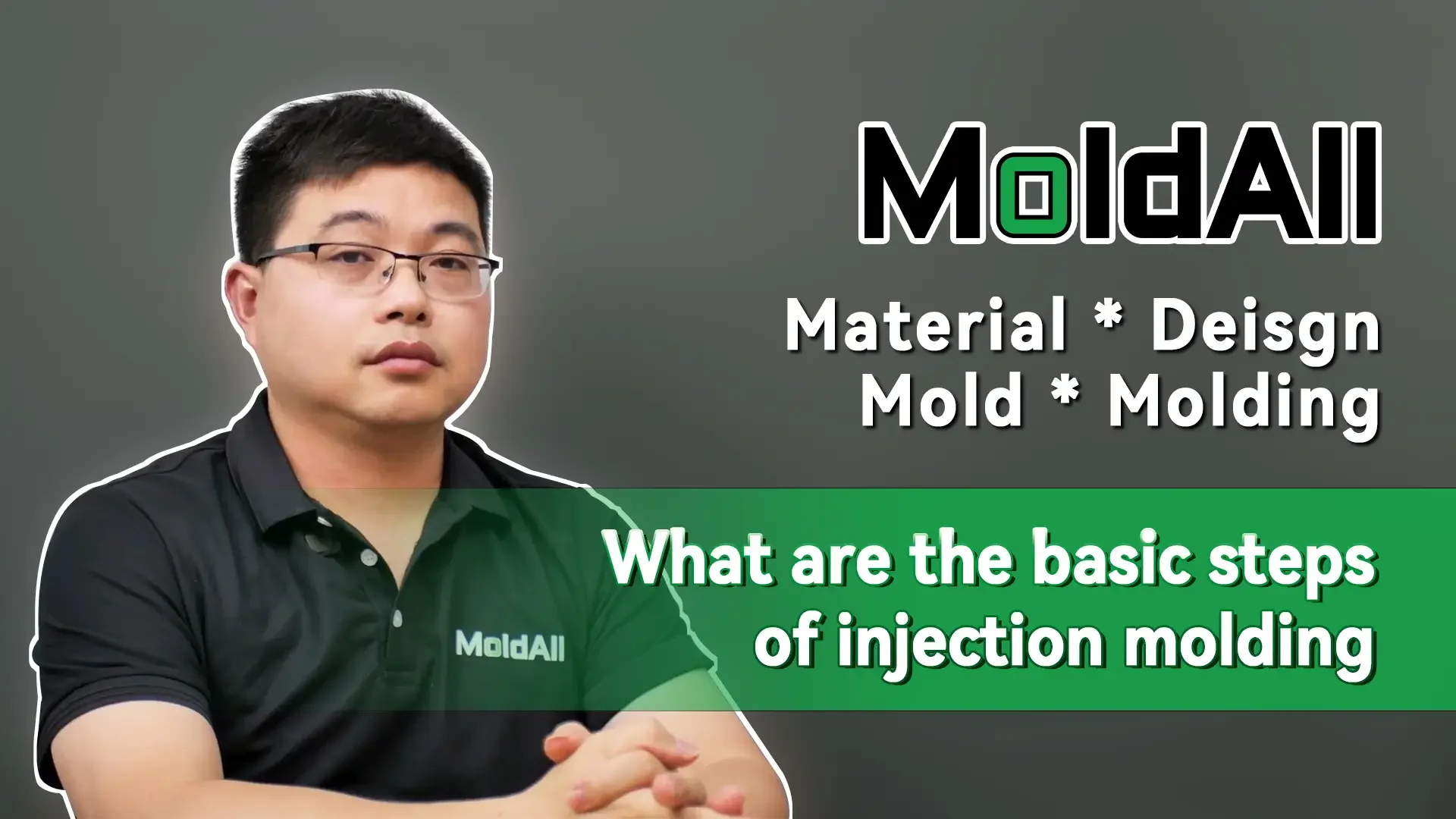
What Are the Key Temperature Parameters to Monitor?
Temperature parameters are crucial in injection molding, affecting the plasticization, fluidity, and quality of the final product. Real-time monitoring ensures these parameters stay within optimal ranges, minimizing defects and maximizing efficiency.
Key temperature parameters in injection molding include barrel, melt, and mold temperatures. Monitoring these parameters in real-time ensures optimal plasticization and cooling, improving product quality and reducing defects.
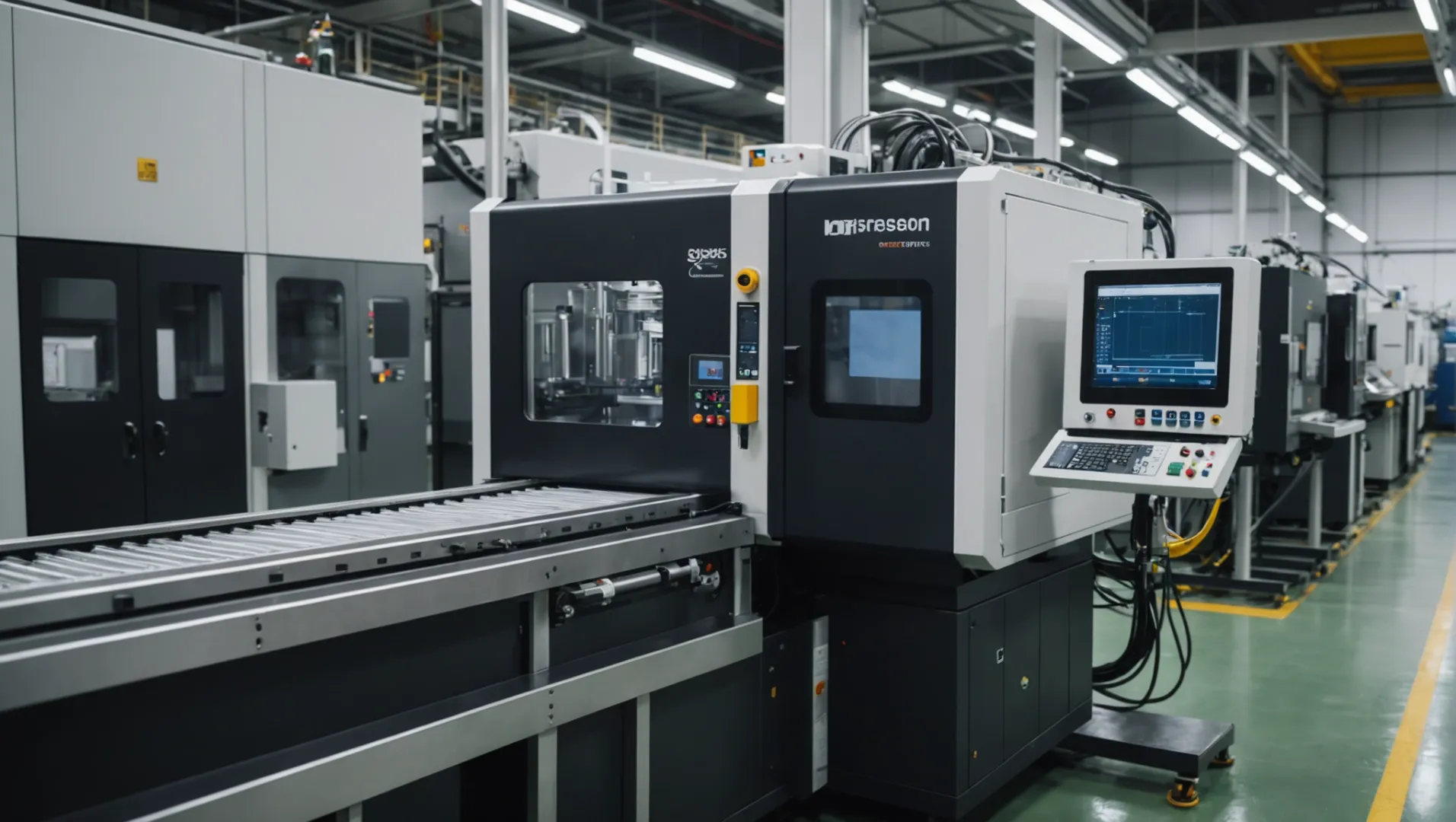
Barrel Temperature: The Backbone of Plasticization
In injection molding, barrel temperature is a critical factor that influences the plasticization process. The barrel is divided into zones, each requiring specific temperature settings:
- Feed Zone: A lower temperature prevents premature melting and feed port blockages.
- Plasticization Zone: Higher temperatures here ensure the plastic melts fully, promoting smooth flow.
By using thermocouples strategically placed along the barrel, operators can monitor temperature1 variations. If the temperature deviates from the set range, alarms notify operators to make necessary adjustments. This proactive approach prevents issues like plastic decomposition or reduced fluidity, which can compromise product quality.
Melt Temperature: Ensuring Product Integrity
The melt temperature is measured at the nozzle or near the mold gate. It is a pivotal parameter for guaranteeing the integrity of the molded product:
- High Melt Temperatures: May cause defects such as burning or bubbles.
- Low Melt Temperatures: Can lead to issues like inadequate filling or poor surface gloss.
Employing a professional melt temperature sensor allows precise measurement and control, ensuring each product meets quality standards. Real-time adjustments based on sensor readings help maintain optimal conditions, thereby enhancing product appearance and structural integrity.
Mold Temperature: Balancing Cooling and Crystallinity
Mold temperature affects several critical aspects of the product, including its cooling rate, crystallinity, and dimensional stability:
- High Mold Temperatures: Necessary for products requiring high crystallinity.
- Low Mold Temperatures: Suitable for thin-walled items to expedite cooling and boost production efficiency.
Temperature sensors placed inside or on the mold surface offer continuous monitoring. By analyzing this data, manufacturers can ensure consistent performance and quality across all products, adjusting mold temperatures as needed to meet specific production goals.
Temperature Parameter | Impact on Product |
---|---|
Barrel Temperature | Affects plasticization and fluidity |
Melt Temperature | Influences filling and surface quality |
Mold Temperature | Controls cooling rate and stability |
Understanding and controlling these temperature parameters enhances efficiency2 in injection molding. By leveraging real-time monitoring systems, manufacturers can optimize processes, leading to superior product quality and reduced waste.
Barrel temperature affects plasticization in injection molding.True
Barrel temperature impacts the melting and flow of plastic, crucial for product quality.
Low mold temperatures increase product crystallinity.False
High mold temperatures are needed for increased crystallinity, not low temperatures.
How Does Pressure Monitoring Affect Injection Molding Quality?
Pressure monitoring is pivotal in injection molding, directly impacting product quality and consistency.
Monitoring pressure in injection molding ensures optimal filling and holding, preventing defects like incomplete filling, internal stress, and flash.
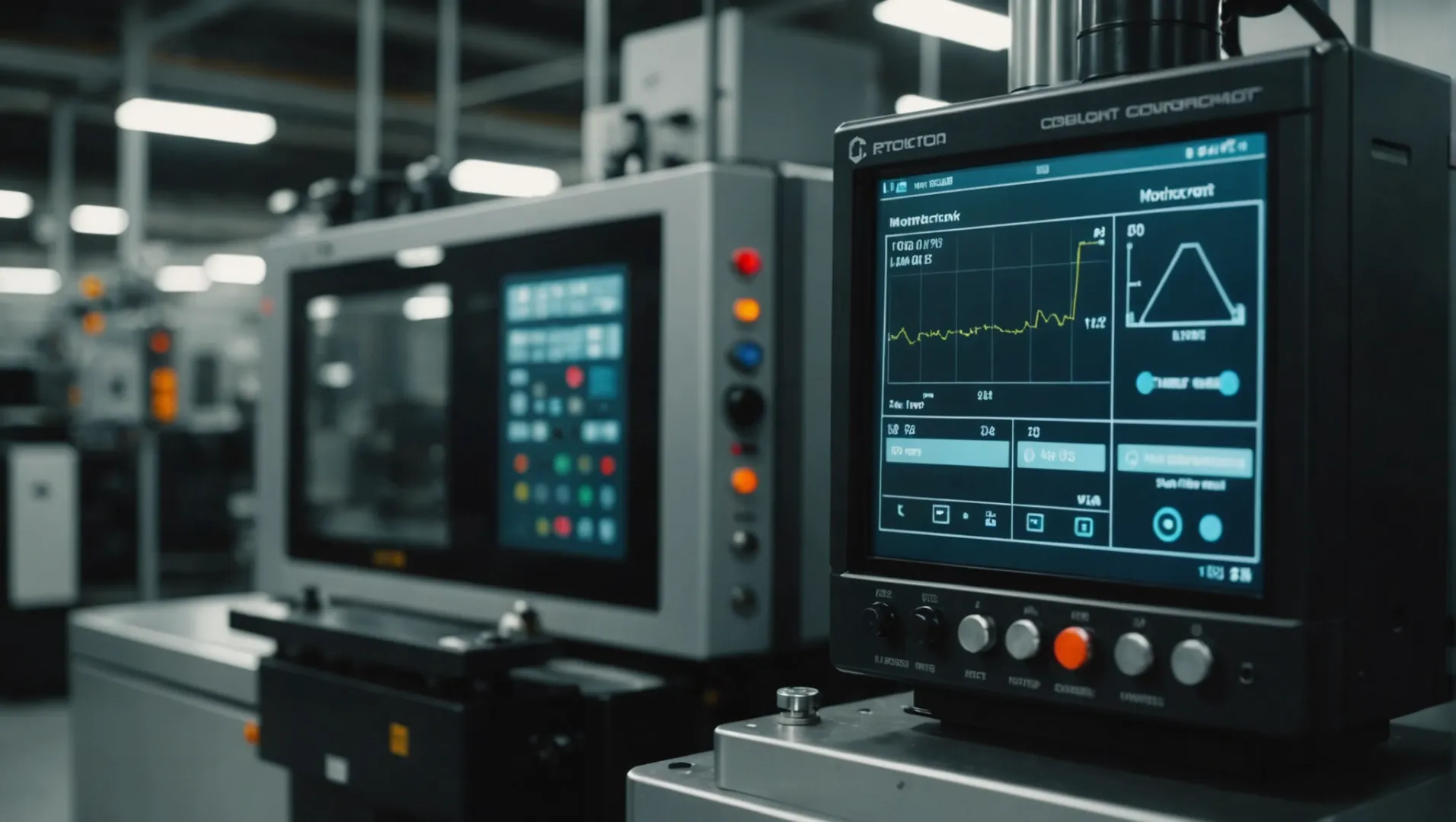
The Importance of Injection Pressure
Injection pressure directly influences how the plastic melt fills the mold cavity. High injection pressure ensures complete filling, crucial for producing defect-free products. However, excessive pressure can lead to internal stress and undesirable surface defects such as flash. By monitoring injection pressure3 in real-time, manufacturers can maintain it within an optimal range, enhancing the dimensional accuracy and surface quality of the final product.
Holding Pressure’s Role in Dimensional Stability
Once the mold cavity is filled, holding pressure is applied to compensate for plastic shrinkage. This is vital for maintaining the product’s dimensional stability and appearance. Insufficient holding pressure can lead to surface depressions and dimensional deviations, while excessive pressure can increase internal stress. Real-time monitoring allows for precise adjustments, ensuring products meet stringent quality standards.
Clamping Pressure: Ensuring Mold Integrity
Clamping pressure is essential for keeping the mold closed during the injection phase. An optimal clamping pressure prevents the mold from opening prematurely, which can cause flash defects. Monitoring this parameter helps prevent damage to both the mold and the product while optimizing energy consumption and extending mold life.
Real-World Applications and Benefits
Consider a scenario where an automotive part manufacturer uses advanced pressure sensors to monitor injection and holding pressures. By maintaining these parameters within ideal ranges, they achieve a 15% reduction in defect rates, significantly improving production efficiency. This not only enhances product reliability but also results in substantial cost savings over time.
Implementing a robust pressure monitoring system can also streamline operations by reducing machine downtime due to fewer rejected parts and less frequent mold maintenance. Additionally, integrating these systems with modern data analytics tools enables predictive maintenance, further enhancing overall production efficiency.
High injection pressure prevents incomplete filling.True
High pressure ensures the mold is fully filled, avoiding defects.
Excessive holding pressure reduces internal stress.False
Excessive pressure increases internal stress, affecting quality.
Why Is Speed Monitoring Crucial for Product Consistency?
Speed monitoring in manufacturing isn’t just about efficiency—it’s a linchpin for consistent product quality.
Speed monitoring ensures product consistency by regulating injection speed and screw speed, crucial for optimal plastic flow and uniformity.
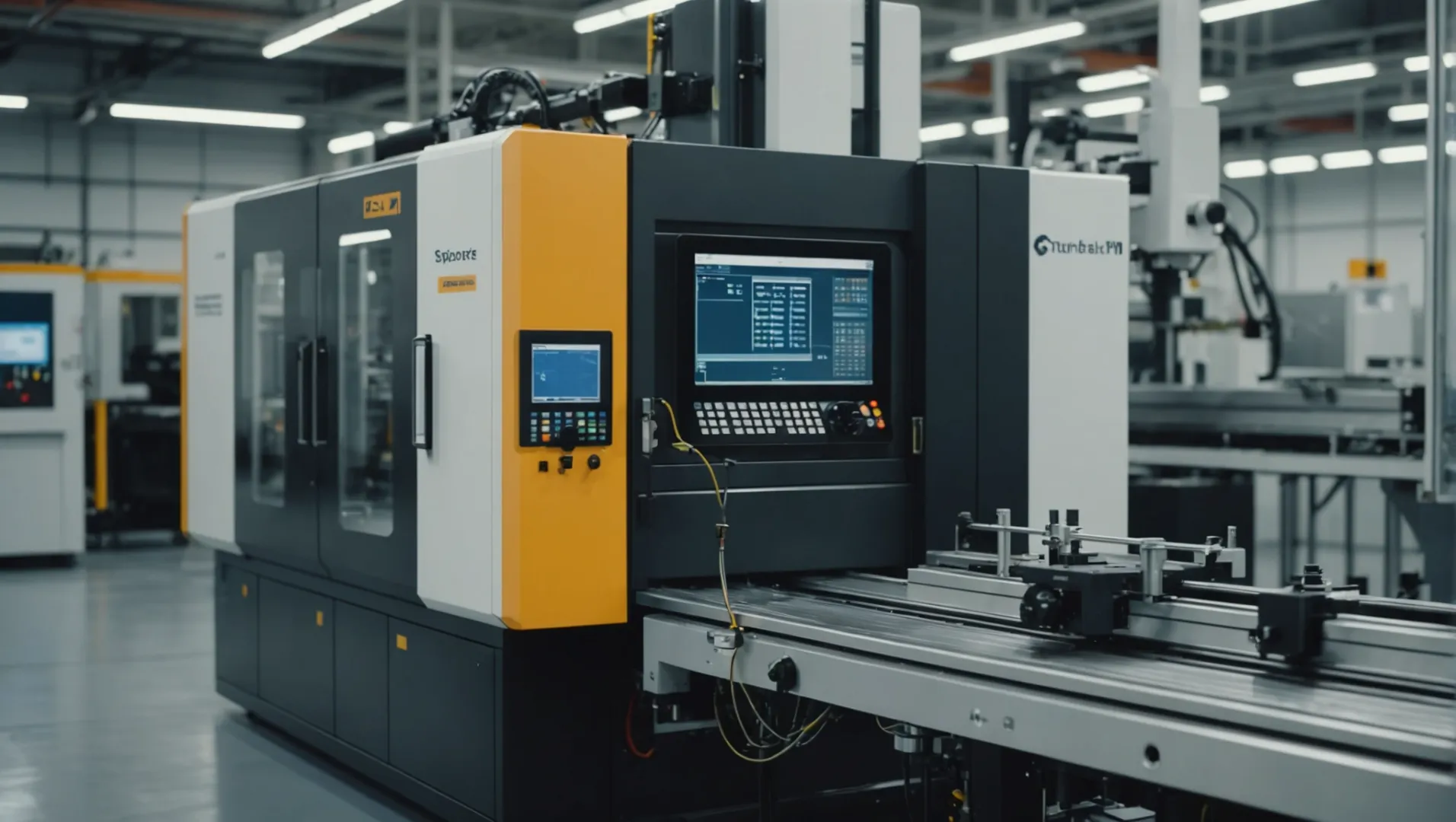
The Critical Role of Injection Speed
Injection speed refers to how quickly the plastic melt is injected into the mold cavity. This speed directly influences the quality and uniformity of the final product. For instance, a rapid injection speed might lead to surface defects like air marks or spray, while a slower pace can result in incomplete filling and flow marks. By deploying speed sensors within the injection system, real-time data allows operators to make necessary adjustments, thus maintaining the desired product quality.
Balancing Screw Speed for Optimal Results
Screw speed impacts both the plasticization process and overall cycle time. An overly fast screw speed can cause excessive shear, breaking down the plastic molecular chains and compromising product strength. Conversely, a slow screw speed extends plasticization time, negatively affecting production efficiency. Real-time monitoring enables precise control over screw speed, adapting to different plastics and process requirements.
Parameter | Optimal Range | Potential Issues if Mismanaged |
---|---|---|
Injection Speed | Moderate | Surface defects, incomplete fill |
Screw Speed | Balanced | Molecular breakdown, low efficiency |
Implementing Speed Sensors: A Pathway to Consistency
Integrating speed sensors into the injection molding machine empowers manufacturers to closely observe both injection and screw speeds. These sensors provide invaluable data that can be analyzed to ensure that each batch of products meets the same high standards of quality.
For example, companies using advanced speed sensor technology4 have reported significant reductions in defect rates and material waste. This not only boosts product consistency but also enhances overall operational efficiency.
In the broader scope of manufacturing, real-time speed monitoring dovetails with other key parameters such as temperature control5 and pressure management, creating a synergistic effect that elevates product quality across the board. As industries continue to push towards automation and precision, mastering speed control remains an indispensable part of maintaining competitive advantage.
Speed monitoring prevents surface defects in products.True
Monitoring injection speed avoids air marks and spray on product surfaces.
Screw speed does not affect plasticization time.False
Screw speed directly impacts the time needed for plasticization.
What Role Do Position Parameters Play in Ensuring Quality?
Understanding the role of position parameters can significantly boost product quality in injection molding.
Position parameters in injection molding ensure precise control over screw and mold positions, directly impacting product accuracy and quality. By monitoring these parameters in real-time, manufacturers can detect discrepancies early, allowing for timely adjustments that maintain high standards and minimize defects.
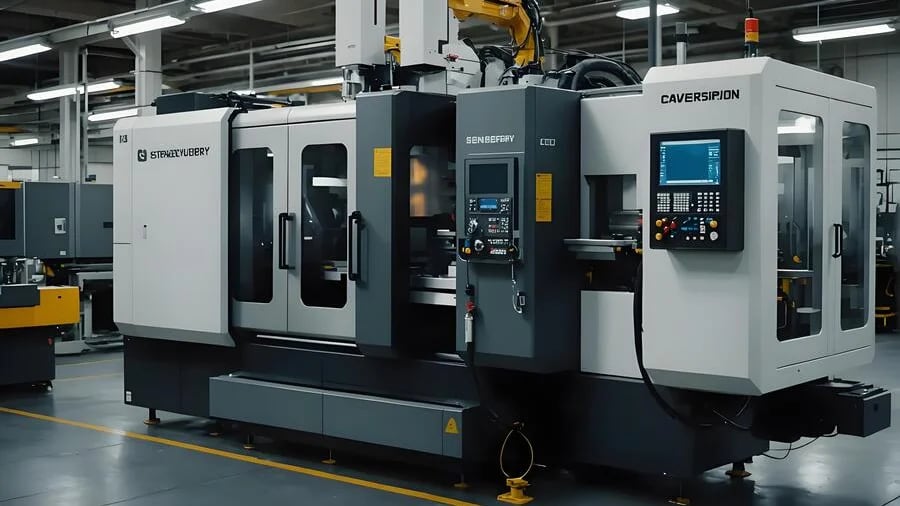
Importance of Screw Position Monitoring
The screw position in an injection molding machine is pivotal for controlling the injection volume6 and the degree of plasticization. Accurate monitoring through position sensors allows manufacturers to gauge whether the plasticization process is uniform and if the injection volume meets specifications. For instance, a deviation in screw position may indicate inconsistent plasticization, leading to product defects such as uneven wall thickness or voids.
Example:
Consider a scenario where a deviation in screw position causes under-filling. This could lead to parts with inadequate structural integrity, making them prone to failure under stress. By detecting this early, corrective measures such as adjusting the screw position can be made, ensuring the final product’s robustness.
Mold Opening and Closing Position
Monitoring the mold opening and closing positions is crucial for maintaining the integrity of both the mold and the product. Position sensors ensure that molds open and close accurately, preventing damage that could occur from misalignment.
For example, an improperly aligned mold during closure could result in flash, where excess material leaks out at the parting line, necessitating additional trimming and potentially leading to wasted material. By ensuring precise mold positioning, manufacturers can avoid these issues, thus enhancing the efficiency and quality of the molding process.
Table: Impact of Position Parameters on Product Quality
Parameter | Impact on Quality | Potential Issues if Misaligned |
---|---|---|
Screw Position | Controls injection volume and plasticization | Uneven walls, voids, under-filling |
Mold Position | Ensures proper opening/closing | Flash, mold damage, product misalignment |
Real-Time Adjustments and Benefits
Implementing real-time monitoring of position parameters enables manufacturers to make instant adjustments, reducing downtime and enhancing overall productivity. For instance, if a sensor detects an anomaly in the screw position during the injection cycle, operators can promptly rectify the issue before it affects subsequent production batches.
This proactive approach not only maintains quality but also fosters a culture of continuous improvement within manufacturing operations. By investing in advanced monitoring technologies, businesses can significantly enhance their production capabilities and achieve higher customer satisfaction.
Screw position affects injection volume accuracy.True
Screw position controls the volume injected, impacting product consistency.
Misaligned mold positions cause under-filling issues.False
Misalignment generally causes flash, not under-filling, in molds.
Conclusion
Real-time monitoring revolutionizes injection molding by ensuring consistent quality and operational efficiency. Embrace these technologies for a competitive edge.
-
Learn methods to effectively track barrel temperatures using advanced sensors.: The true melt temperature is difficult to measure during production. Most molders interrupt the cycle and purge plastic into the air to take a … ↩
-
Discover how precise temperature control boosts efficiency and product quality.: The plastics industry relies heavily on industrial temperature sensors to accurately monitor temperature stability. ↩
-
Understand why monitoring injection pressure is vital for defect-free production.: Slight fluctuation in one of these pressure values can impact the injection molding process and product quality. ↩
-
Explore how speed sensors reduce defects and waste in manufacturing.: Fill speed also has an effect on the packing phase of the molding process. Adjusting the injection speed helps prevent issues like flow lines … ↩
-
Learn how temperature control complements speed monitoring for better quality.: When the temperatures are too low during the injection-molding process, it can bring about wavy lines or flow marks that damage the surface of … ↩
-
Learn how screw positioning impacts injection volume and product consistency.: In addition, speed of screw is the first derivative of its position, injection molding machine monitors curve to select screw position and … ↩