Design relies on exactness when choosing the right film gate size.
Measure the film gate size by considering the product’s width, wall thickness and how the material behaves. Gate width usually varies from 25% to the full product width. Meanwhile, gate thickness often falls between 0.5 and 0.8 times the wall thickness. Short gate length is important. It often stays between 0.5 and 2mm. This helps to lessen pressure and heat loss. Pressure and heat loss need to be low.
I know this sounds a little complex. Let me explain it easily. Think about putting together a jigsaw puzzle. Each piece should fit exactly, just like how the film gate’s size should match your design. It’s more than just about numbers. It’s about building something smooth and effective. In this post, I’ll show you the details that could really turn your project into something not just good, but truly outstanding.
Gate width is always 50% of product width.False
The gate width varies from 25% to 100% of the product width.
Gate length should be kept between 0.5-2mm.True
Short gate lengths minimize pressure and heat loss effectively.
What Factors Influence the Determination of Gate Width?
Have you ever thought about choosing the right gate width in mold design?
Gate width depends on product size, mold cavity arrangement and material characteristics. It balances melt flow. This ensures quality output.
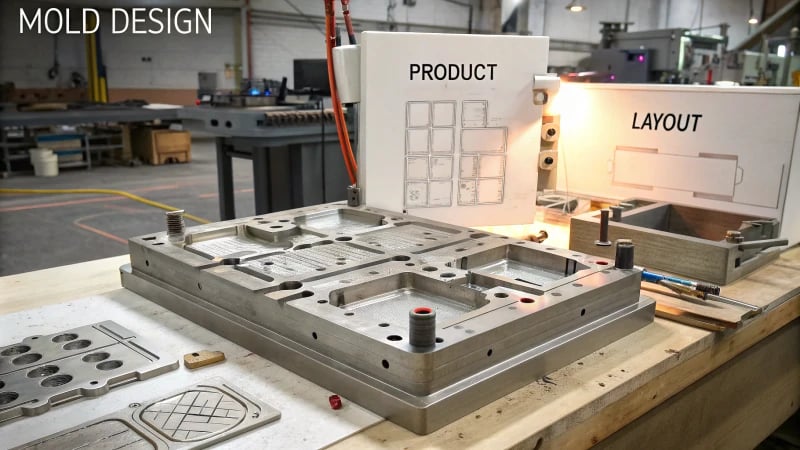
Product Width Considerations
When I first began exploring mold design, figuring out gate width felt like cracking a secret code. It required technical knowledge and a kind of intuition that grows with practice. Here are some important things I’ve learned to think about.
The gate width often correlates with the product’s width. Typically, it’s designed to be 25% – 100% of the product width. For instance, a flat product with a width of 100mm might have a gate width ranging from 25mm to 100mm. If a product demands high aesthetic quality, a wider gate close to the product’s width may be selected for even melt distribution.
Product Width | Gate Width Range |
---|---|
100mm | 25mm – 100mm |
Mold Cavity Layout Influence
The arrangement of cavities in molds is similar to playing Tetris. The gate width must not disturb nearby cavities. Imagine the smallest gap between cavities is 30mm; the gate width must stay within this limit or the molten material could overflow.
In molds with multiple cavities, spacing and layout are pivotal. The gate width must not interfere with adjacent cavities’ filling.
Material Properties
The type of material really plays a big role. For polystyrene (PS), thinner gates might work because the material flows easily. But with glass fiber-reinforced plastics, a thicker gate helps manage thicker flow.
Material fluidity influences gate thickness and potentially its width. For materials like polystyrene (PS) with good fluidity, gates can be thinner, whereas glass fiber-reinforced plastics require thicker gates.
Material | Recommended Gate Thickness |
---|---|
Polystyrene (PS) | 0.5x Product Wall Thickness |
Glass Fiber Reinforced | 0.7 – 0.8x Product Wall Thickness |
This adjustment helps manage melt flow resistance, ensuring smooth cavity filling.
Understanding these factors not only aids in effective mold design1 but also enhances the production process by minimizing defects and maximizing output quality.
Real-World Examples
Picture using both PS and reinforced plastic: With PS, a narrower gate works due to its easy flow, while reinforced plastic needs a wider gate to pass through smoothly.
Consider a scenario where two materials are used: PS might allow for a narrower and thinner gate due to its fluidity, while reinforced plastic might necessitate a wider gate to accommodate its increased viscosity.
Gate width is always 50% of product width.False
Gate width can range from 25% to 100% of the product's width.
Material fluidity affects gate thickness.True
Materials with good fluidity, like PS, allow for thinner gates.
How Does Material Choice Affect Gate Thickness?
Do you ever think about how the material you select really impacts the thickness of gates in mold design?
Material choice directly affects gate thickness because different materials have different fluidity and pressure needs. Polystyrene, for instance, often requires thinner gates compared to glass fiber reinforced plastics. This happens for optimal flow. Optimal flow is important.
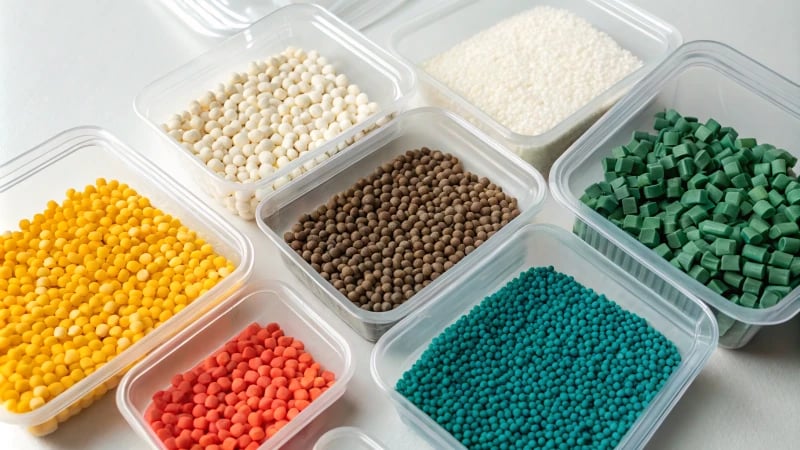
Role of Material Fluidity
I recall my first encounter with polystyrene in a mold. Its very high fluidity felt like a dream, allowing thinner gates2 and smoother flow. Less pressure was needed. In contrast, glass fiber reinforced plastics presented a challenge. Lower fluidity required thicker gates to reduce resistance for proper filling. It was important. Very important.
Material Type | Recommended Gate Thickness |
---|---|
Polystyrene (PS) | 0.5 times wall thickness |
Glass Fiber Reinforced | 0.7 – 0.8 times wall thickness |
Impact on Pressure Drop
Gate thickness mattered for pressure drop during injection. Thinner gates could lead to higher pressure drop, which works well for materials like polystyrene, where melt flow control is crucial.
Conversely, thicker gates suit glass fiber reinforced plastics as they help maintain a steady flow and minimize defects.
Quality Considerations
Balance is everything. Product quality demands also influence gate thickness. Delivering products with high appearance standards required larger gate width3. This ensured even filling and fewer defects like flow lines or weld marks.
Choosing the right gate thickness kept both structure and appearance in line. It was essential. It mattered a lot.
Practical Examples and Recommendations
My experience with designing molds for consumer electronics offered insights:
- For polystyrene, a gate thickness of about 1mm suits a 2mm wall thickness.
- Switching to glass fiber reinforced materials benefits from increasing it to 1.4mm.
These adjustments were crucial; they were key to achieving top production efficiency, quality, and reducing material waste and cost.
Polystyrene requires thicker gates than glass fiber plastics.False
Polystyrene requires thinner gates due to higher fluidity.
Thinner gates result in higher pressure drops.True
Thinner gates increase pressure drop, aiding flow control in fluid materials.
Why Is Gate Length Critical in Mold Design?
Do you ever think about how even a tiny change in gate length greatly changes mold design? It’s like finding the special spice in your favorite meal.
Gate length is important in mold design. It changes pressure loss, melt flow and the chance of blockages. A short gate lowers pressure and heat loss. But it maybe causes blockages. This needs careful material choice and upkeep.
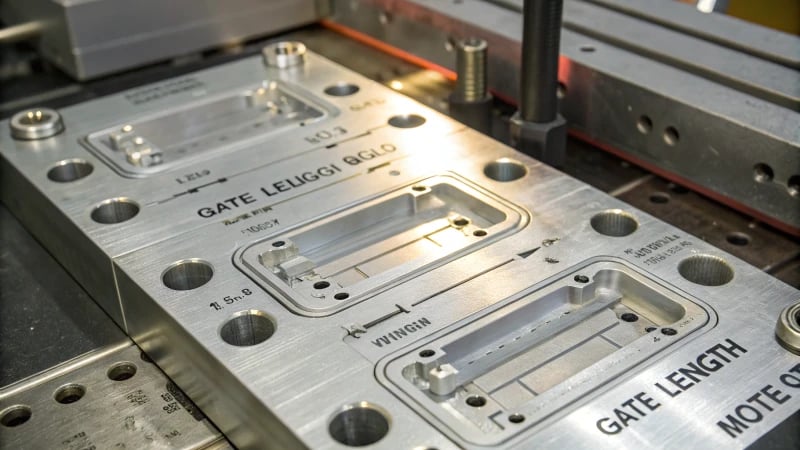
Why Gate Length Matters
Gate length plays a pivotal role in injection molding4 by dictating how efficiently the molten material fills the mold cavity. A well-designed gate ensures minimal pressure and heat loss, which is crucial for maintaining part integrity.
Balancing Gate Length and Pressure Loss
On my first project with a thin-walled item, I saw that shorter gates helped reduce pressure loss. These gates, about 0.5 to 2mm, allowed the material to flow quickly into the mold. However, this also meant more risk of blockage, especially if there were impurities or if the mold isn’t regularly maintained.
Gate Length | Advantages | Disadvantages |
---|---|---|
Short (0.5-1mm) | Fast melt entry, reduced pressure | Higher risk of blockage |
Long (1.5-2mm) | Lower blockage risk | Potential for increased pressure loss |
Effects on Look and Strength
In a project about consumer electronics, I learned that gate length influences both strength and appearance. Proper gate length filled molds evenly and reduced visible flaws such as weld lines or warping. A balanced design made it look good and work well.
Considering Material Types
Each material reacts differently to gate length due to their unique flow characteristics:
- Polystyrene (PS): Short gates enhance flow due to excellent fluidity.
- Glass Fiber Reinforced Plastics: Longer gates help reduce flow resistance.
For further insights into material-specific requirements, consider reviewing material properties5.
Maintenance and Design Changes
Routine maintenance impacts short gate designs significantly. More frequent cleaning helps shorter gates by lowering blockage risks; whereas less frequent cleaning might require slightly longer gates.
It’s essential to adjust gate design6 according to these factors to optimize both productivity and product quality. Recognizing these aspects aids mold designers in customizing gate lengths for specific needs by considering materials, upkeep, and product requirements.
Short gates reduce pressure loss in molding.True
Short gates allow faster melt entry, minimizing pressure loss in the cavity.
Longer gates increase blockage risk in molds.False
Longer gates reduce blockage risk by accommodating impurities and flow resistance.
How Do Different Industries Approach Film Gate Sizing?
Have you ever thought about how choosing the right film gate size affects a project? Different industries use unique methods, each designed for specific needs.
Industries like filmmaking, photography and manufacturing rely on specific criteria. People evaluate product dimensions and material properties. This helps them decide on the correct film gate size. Optimal performance and quality result from such careful analysis.
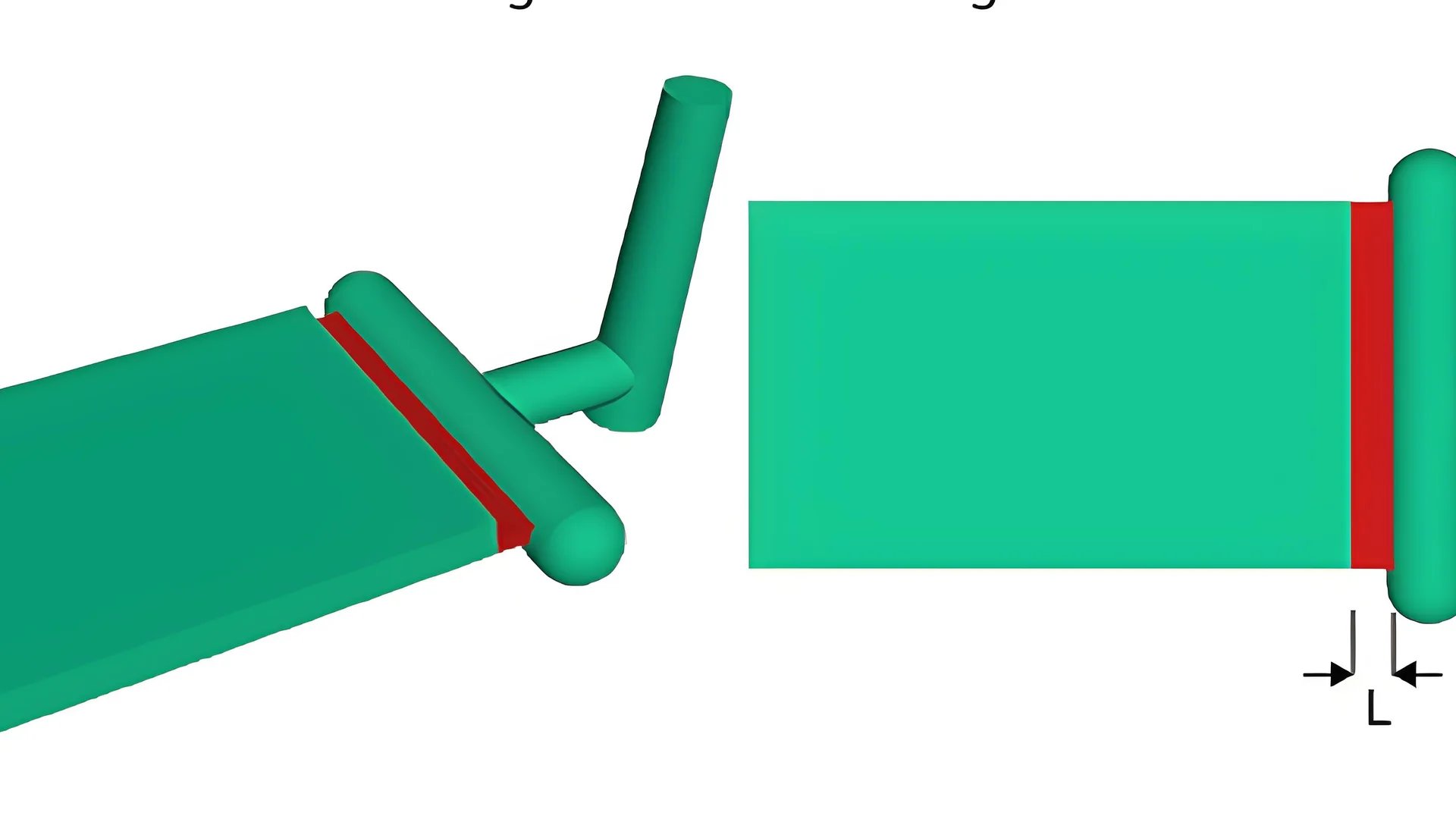
Cinematography and Photography
In cinematography7 and photography, the huge impact of film gate size on image sharpness really surprised me. It’s like choosing the perfect picture frame – everything relies on that decision. Think about 35mm or IMAX formats. Each needs specific gate sizes to capture that beautiful picture shape. I watched cinematographers struggle to choose the right gate size, balancing creativity with technical skill.
Film Formats and Gate Sizes
Format | Standard Gate Size (mm) | Aspect Ratio |
---|---|---|
35mm | 24 x 18 | 4:3 |
IMAX | 70 x 48.5 | 1.43:1 |
Manufacturing Industries
In manufacturing, especially in areas like plastic molding, film gate size plays a key role in product quality. Imagine designing a flat object; the gate width might vary from a small part to the full width of the product. During a visit to a plastics factory, I saw how important it was to get this right for even material spread.
The determination of gate width8 is often based on product width, with a typical range from 25% to 100% of the product’s total width. This is crucial in ensuring even material distribution during production.
Considerations for Gate Sizing:
- Gate Thickness: Often 0.5 – 0.8 times the product wall’s thickness to control flow pressure.
- Material Properties: Like adjusting a recipe with available ingredients, changes here depend on material flow – PS generally uses thinner gates compared to glass fiber-reinforced plastics.
Technical Considerations
There’s also the technical side – mold cavity designs and blockage challenges feel like solving a tough puzzle. With multi-cavity molds, stopping one gate from messing with another is necessary.
For example, in multi-cavity molds, the gate width must not affect adjacent cavities, maintaining an ideal balance to prevent manufacturing errors.
Gate Length Design: Short gates (0.5-2mm) are useful for cutting pressure loss but need careful handling to avoid blockages from dirt.
Short gate design principle9 is very important for fast material flow in thin-walled products.
Understanding these details in film gate sizing means more than just following rules. It involves knowing what each industry needs. It’s about finding the perfect mix of efficiency and quality – whether creating amazing images or precise plastic parts.
35mm film gate size affects image aspect ratio.True
35mm film has a standard gate size of 24x18mm, impacting aspect ratio.
Manufacturing uses a fixed gate size for all products.False
Gate size in manufacturing varies based on product width and material properties.
Conclusion
This article explains how to determine the appropriate size of a film gate in mold design, focusing on product dimensions, material properties, and optimal flow for quality output.
-
Discover strategies for effective mold design that enhance production efficiency and product quality. ↩
-
Learn how different materials’ fluidity affects their required gate thickness for optimal molding. ↩
-
Understand how adjusting gate width can enhance product quality and consistency. ↩
-
Explore why gate length impacts injection molding efficiency and part quality. ↩
-
Compare how different materials affect optimal gate design in molds. ↩
-
Learn how maintenance frequency influences mold design choices. ↩
-
Explore how different film gate sizes affect cinematic image quality and creative possibilities. ↩
-
Learn how industries determine gate width for optimal production quality in molding processes. ↩
-
Understand the principles behind designing short gates for efficient material flow in manufacturing. ↩