Do you want to improve your factory processes? I remember when I began exploring plastic molding. I felt both excited and unsure. I want to share what I have discovered during my journey.
Plastic molding services, including injection and extrusion, offer efficient, precise, and cost-effective production of high-quality plastic products, benefiting businesses through enhanced manufacturing processes.
This blog post guides you through different types of plastic molding services. These services probably transform business operations. Injection molding and blow molding are examples. Each method has unique benefits. Mold design and material selection are important. Extra services lift product quality. Designers like me see these services improve efficiency. Precision in production remains very high.
Plastic molding services improve manufacturing efficiency.True
Utilizing various molding techniques enhances production speed and reduces waste, thus improving overall manufacturing efficiency.
Injection molding is the only type of plastic molding available.False
There are multiple plastic molding techniques, including extrusion and blow molding, not just injection molding.

- 1. What Are the Different Types of Plastic Molding Techniques?
- 2. How Does Mold Design Impact Product Quality?
- 3. What Materials Are Best for Plastic Molding?
- 4. How Can Value-Added Services Transform Your Molding Process?
- 5. How Can Plastic Molding Services Reduce Manufacturing Costs?
- 6. Conclusion
What Are the Different Types of Plastic Molding Techniques?
In my journey through manufacturing, I discovered that knowing plastic molding techniques is vital. These skills are crucial for developing products that connect with users. Let’s explore these methods and uncover their special features together!
Plastic molding techniques include injection, extrusion, blow, and compression molding, each offering unique benefits and catering to various manufacturing needs.
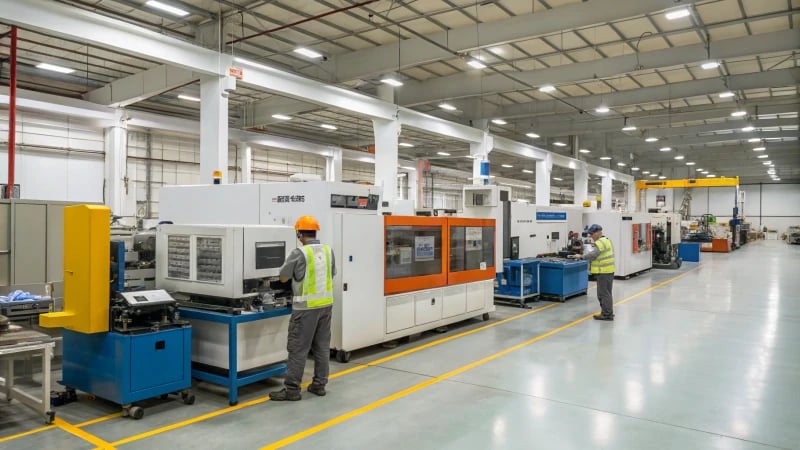
Injection Molding Service
Injection molding works like magic in the plastic world. Imagine plastic granules heated until they melt. Then, they go into a mold created with care. This technique is perfect for detailed shapes, like high-quality plastic shells or children’s toys. Yes, it creates those toys that make kids happy.
For more details on this process, check out injection molding insights1.
Extrusion Molding Service
Extrusion molding has its own charm, especially for long products. Think of a giant toothpaste tube, but with plastic being pushed to form pipes and films. Industries often choose this method for consistent shapes over long distances.
Learn more about extrusion processes in our extrusion molding guide2.
Blow Molding Service
Blow molding works like inflating a balloon. But here, it forms hollow plastic items. This technique is crucial for products like bottles and barrels. For further details on blow molding methods, visit blow molding explained3.
Compression Molding Service
Compression molding involves raw materials meeting heat and pressure. This method brings big, sturdy items to life and creates dense and durable objects. If you want to know more about this process, our compression molding overview4 offers deep insights.
Mold Design and Manufacturing
I deeply appreciate mold design; it’s not just about shapes but creating a mold that fits customer needs precisely. A well-designed mold greatly affects production efficiency and product quality. For more on mold design principles, check mold design essentials5.
Aspect | Considerations |
---|---|
Mold Structure | Shape, size, precision requirements |
Cooling System | Efficiency in cooling to enhance production speed |
Gate Location | Affects filling and quality of molded parts |
Material Selection and Processing
Choosing the right material feels like picking the best paint color for a masterpiece; it’s very important for any plastic molding project. Selecting the right material is crucial as it impacts performance requirements significantly.
Here’s a quick table to visualize:
Material Type | Application | Recommended Treatment |
---|---|---|
Polyimide (PI) | High-temperature applications | Drying |
Polyethylene (PE) | General packaging | Color matching |
Discover best practices for material selection at material processing tips6.
Value-Added Services
After molding, value-added services really improve the final product’s quality through surface treatments like polishing or electroplating that transform an ordinary piece into something extraordinary.
For insights into post-processing techniques, visit post-processing methods7.
Injection molding produces complex parts with high accuracy.True
Injection molding allows for precise shapes and dimensions, making it ideal for intricate designs in various industries.
Blow molding is used for solid plastic products only.False
Blow molding is specifically designed for hollow items like bottles, not solid products, making this claim false.
How Does Mold Design Impact Product Quality?
Ever wonder why some products feel better and last longer? Mold design is often the reason. This important factor shapes the quality of items we use daily.
Mold design crucially impacts product quality by controlling material movement, cooling rate, and distribution during molding processes, reducing errors, and enhancing functionality for superior products.

The Role of Mold Design in Manufacturing
Mold design is critical in the manufacturing process, particularly in injection molding. The design influences various factors such as material flow, cooling rates, and overall product uniformity.
Material Flow: A well-designed mold facilitates the smooth flow of molten plastic into the mold cavity, ensuring that every part of the product is filled uniformly. This can significantly reduce the risk of defects such as voids or incomplete fills. I recall a project where wrong gating systems led to defects. It was a tough lesson. This taught me how essential correct material flow is in avoiding empty spaces and incomplete fills. For instance, proper gating systems8 ensure that the material enters the mold at the right velocity and pressure.
Impact on Cooling Rates
Cooling is crucial, not secondary! A good mold uses an effective cooling system to deliver even cooling across the product. Molds that incorporate an efficient cooling system can help achieve uniform cooling rates across the entire product, which is essential for maintaining dimensional accuracy.
Cooling Method | Advantages | Disadvantages |
---|---|---|
Water Cooling | Fast and efficient | Risk of warping if not managed properly |
Air Cooling | Simplifies the cooling process | Slower than water cooling |
Temperature Control | Precise control over cooling rates | More expensive setup |
I’ve personally observed how cooling inconsistencies can cause size errors. Here are cooling methods I’ve experienced:
- Adding features like cooling channels9 was like solving a puzzle!
Achieving Product Uniformity
Uniformity holds great importance in mold design. It provides consistent wall thickness, key for looks and function. Mold design directly affects product uniformity. Uniform designs lead to consistent wall thickness, which is crucial for both aesthetic and functional purposes. Variability in wall thickness can lead to weak points in the product, making it prone to failure under stress. For example, advanced CAD tools I’ve used enable designers to see how mold changes impact wall thickness, affecting product strength.
Customization for Specific Products
Each product has its own story, needing different designs based on their intended use and material characteristics. Different products require different mold designs based on their intended use and material characteristics. A mold designed for a sleek plastic bottle requires a different approach than one for a complex electronic case. Customization ensures that molds meet specific product requirements while optimizing production efficiency.
This customization process involves selecting appropriate materials for the mold itself, which can influence durability and longevity. High-quality materials can withstand the rigors of repeated use, leading to higher production yields.
Conclusion without Conclusion
I hope this journey explains why mold design significantly affects product quality. While we won’t conclude here, understanding how mold design impacts product quality is essential for manufacturers looking to enhance their production processes. By focusing on these factors—material flow, cooling rates, and product uniformity—designers can significantly influence the overall effectiveness of their manufacturing operations.
For those interested in diving deeper into this topic, exploring advanced mold design techniques10 could probably provide more understanding of improving production quality.
Effective mold design reduces manufacturing defects.True
A well-designed mold ensures uniform material flow and cooling, minimizing defects like voids or incomplete fills during production.
Cooling methods have no impact on product quality.False
Cooling methods significantly affect dimensional accuracy and uniformity, directly influencing the overall quality of the final product.
What Materials Are Best for Plastic Molding?
Have you ever thought about which materials work best for plastic molding? This is a very important decision. It could really make or ruin your manufacturing project. Let’s explore the interesting world of plastics and their qualities!
The best materials for plastic molding include Polyethylene and Polypropylene for common use, and Polyimide and Nylon for high-performance needs, considering temperature resistance and mechanical properties for optimal performance.
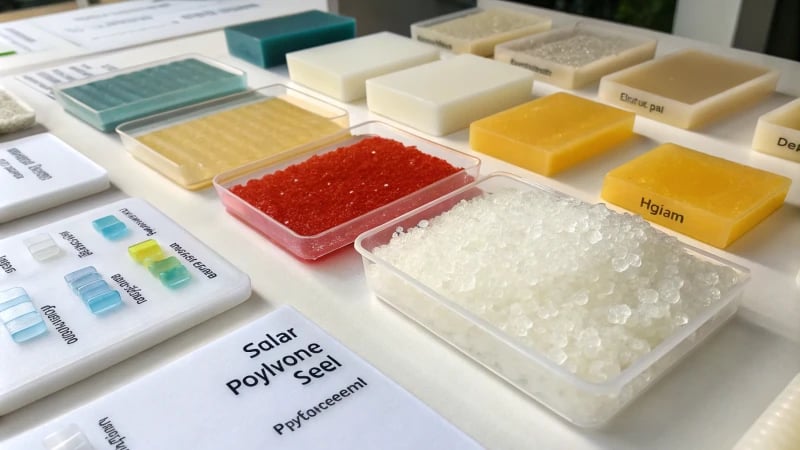
Understanding Plastic Materials for Molding
Choosing the right material for plastic molding is very important. It affects performance and the cost of the final product. Many factors, such as application needs, manufacturing methods and budgets, influence this choice.
Types of Plastics Used in Molding
Different types of plastics suit various molding needs. Below is a table summarizing some commonly used plastics along with their properties:
Plastic Type | Properties | Common Applications |
---|---|---|
Polyethylene (PE) | Good chemical resistance, flexible | Packaging, bottles, toys |
Polypropylene (PP) | High fatigue resistance, lightweight | Automotive parts, containers |
Polyvinyl Chloride (PVC) | Durable, low cost | Pipes, fittings, flooring |
Polystyrene (PS) | Rigid, good insulation properties | Packaging materials, toys |
Polycarbonate (PC) | High impact resistance, transparent | Lenses, safety glasses |
Nylon (PA) | Strong, good abrasion resistance | Gears, bearings, automotive parts |
I recall choosing between Polypropylene and Nylon for a project. Nylon’s strength was tempting, but budget and the product’s purpose mattered too. These decisions teach you to truly understand your materials.
For more detailed insights on these materials, you can explore available plastic types11.
Factors Influencing Material Selection
Several factors affect material choice for molding:
- Temperature Resistance: Some uses need plastics that handle high heat. For example,
polyimide (PI) and polyphenylene sulfide (PPS) are perfect for high-temperature uses. - Chemical Compatibility: Materials must withstand any chemicals they may face. This is vital in fields like food packaging and automotive.
- Mechanical Properties: Strength and flexibility matter based on the plastic part’s purpose. For example, Nylon provides excellent strength for mechanical parts.
In one project involving food packaging, selecting a material with proper chemical compatibility was essential. Real-world projects remind us how important material choice is.
Cost Considerations
Cost always impacts material selection. High-performance plastics offer better qualities but cost more. Balancing performance and budget might mean selecting cheaper options like polyethylene or polypropylene for less crucial uses.
To learn more about cost-effective materials for certain needs, look at material cost analysis.
The Role of Additives
Additives improve the qualities of base plastics:
- Reinforcing Agents: Improve strength and durability. For instance,
adding glass fibers to polypropylene enhances its mechanical properties. - Flame Retardants: Necessary where fire safety is vital.
- Colorants: Used to achieve aesthetic goals in consumer products.
Effectively using additives can lead to very improved product performance. For a comprehensive guide on additives in plastics, check out additive applications. Experience has shown me that the right additive elevates a product from good to excellent!
Polyethylene is ideal for high-temperature applications.False
Polyethylene (PE) is not suitable for high temperatures; materials like polyimide are better.
Nylon offers excellent abrasion resistance for mechanical parts.True
Nylon (PA) is known for its strong abrasion resistance, making it perfect for gears and bearings.
How Can Value-Added Services Transform Your Molding Process?
Have you ever felt like something was missing in your molding process? Let’s explore how extra services really improve product quality. These services also bring a sense of fulfillment to your manufacturing journey.
Value-added services enhance molding by improving product quality and operational efficiency through post-processing, assembly, quality checks, and custom material recommendations.
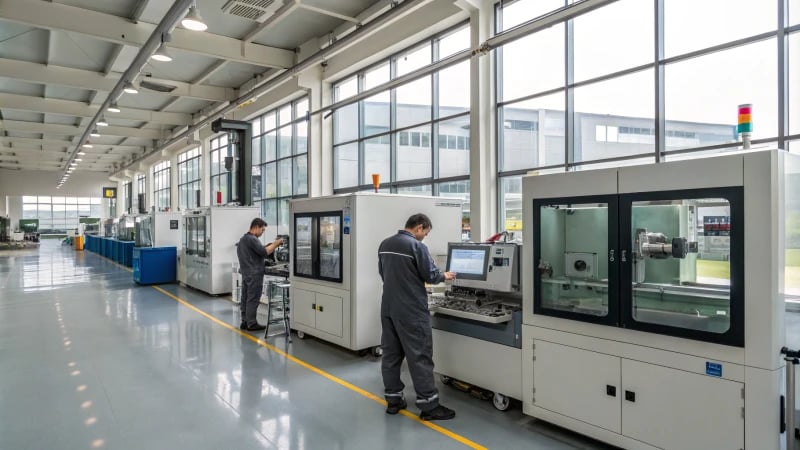
Understanding Value-Added Services
Value-added services play a crucial role in enhancing the molding process by improving product quality, efficiency, and customer satisfaction. In the highly competitive plastics industry, incorporating these services can be a game-changer.
Imagine standing in your workshop. Machines hum around you and the air smells of fresh plastic. I remember my early days in mold making. I felt excited but also frustrated when products did not meet expectations. That is when I discovered value-added services. They changed how I approached molding.
Value-added services are like secret ingredients in a recipe. Post-processing services, for example, turn simple molded parts into eye-catching pieces. Once, I worked on a project that used surface treatments like polishing and painting. Clients felt ecstatic when they saw the shimmering final product under the light. It was a very proud moment for my team and me.
Moreover, assembly services12 allow multiple components to be efficiently combined into a final product, streamlining the manufacturing process. This means that businesses can reduce production time and costs while maintaining high quality.
Types of Value-Added Services
The following table summarizes various value-added services available for molding processes:
Service Type | Description | Benefits |
---|---|---|
Post-Processing | Enhancements to the product’s surface such as polishing or painting. | Improves appearance and marketability |
Assembly | Combining different parts into a final product. | Reduces assembly time and costs |
Packaging | Protective packaging solutions to safeguard products during transport and storage. | Minimizes damage and loss |
Quality Inspection | Rigorous testing of products to ensure compliance with standards. | Guarantees product reliability |
Certification Assistance | Support in obtaining necessary certifications for specific industries like medical or food packaging. | Facilitates market entry and consumer trust |
Importance of Quality Inspection
Quality inspection acts as a safety net in production. Rigorous testing saves a brand’s reputation. Advanced technologies help find defects early. Products meet customer expectations and industry standards. It is a win-win; we reduce waste and save costs in the long term.
Implementing quality control measures13 not only safeguards the reputation of a brand but also contributes to long-term cost savings by reducing waste and rework.
Tailored Material Recommendations
Choosing materials feels overwhelming sometimes; I once felt lost until I learned about tailored material recommendations. For high-temperature applications, using polyimide (PI) or polyphenylene sulfide (PPS) improved performance and durability. Recommending such materials to clients increased their satisfaction—it felt like guiding them to success.
Here are some tailored recommendations based on performance needs:
- High-temperature resistance: Polyimide (PI) or polyphenylene sulfide (PPS) is ideal under heat.
- General packaging: Polyethylene (PE) or polypropylene (PP) suits everyday applications.
Understanding material properties is crucial for end products; they must perform well under different conditions. Explore material selection strategies14 to improve production outcomes.
Post-processing services improve product aesthetics.True
Post-processing services like polishing and painting enhance the visual appeal of molded products, increasing their market value and meeting consumer expectations.
Quality inspection ensures compliance with standards.True
Implementing quality inspection in molding processes guarantees that products meet regulatory standards, enhancing reliability and customer trust.
How Can Plastic Molding Services Reduce Manufacturing Costs?
Have you ever thought about how plastic molding services might lower manufacturing costs? Let me explain how these methods and materials might change your production line. These processes often reduce costs.
Plastic molding services cut manufacturing costs by optimizing processes like injection and extrusion, improving mold design, selecting suitable materials, reducing waste, and enhancing production efficiency.
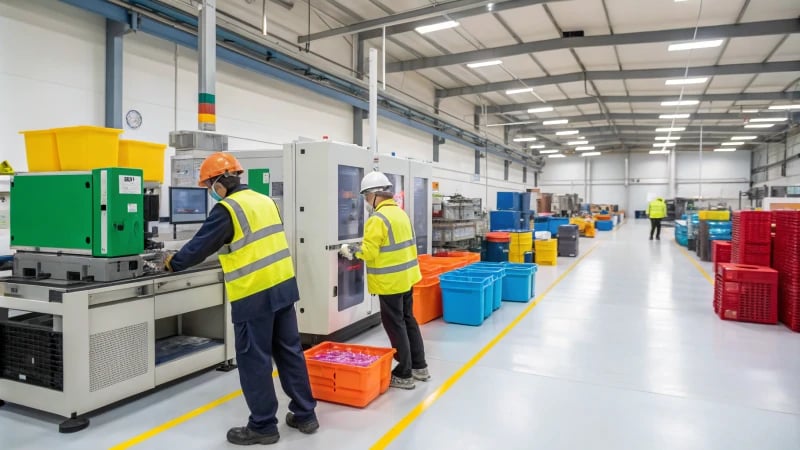
Understanding Plastic Molding Services
Plastic molding services really lower manufacturing costs. They do this by improving production processes such as injection, extrusion, and blow molding. Better mold design reduces waste. Choosing suitable materials is essential. Quality checks are also important. They probably increase efficiency. These steps really save money. Maintaining product quality is also possible. I have seen it myself. These strategies help a business save money.
Injection Molding: Efficiency in Production
Injection molding is a highly efficient process where plastic granules are heated, melted, and injected into molds under high pressure. This technique is especially suitable for producing complex shapes with high dimensional accuracy.
Benefits of Injection Molding:
- Reduced Waste: This method minimizes scrap material due to precise material usage.
- High Production Rates: Capable of producing thousands of identical parts quickly.
- Lower Labor Costs: Automated processes reduce the need for manual labor.
For more details on injection molding advantages, check out injection molding benefits15.
Extrusion Molding: Cost-Effective for Long Products
Extrusion molding allows for the continuous production of long plastic items, such as pipes and sheets. This method is particularly cost-effective when producing high volumes of standardized products.
Advantages of Extrusion Molding:
- Low Material Costs: Continuous production helps in utilizing raw materials efficiently.
- Simplified Process: Fewer steps mean lower operational costs.
To explore how extrusion can benefit your production, visit extrusion molding insights16.
Blow Molding: Ideal for Hollow Products
Blow molding is another essential service for creating hollow plastic products, such as bottles and barrels. This process can reduce material costs by using less plastic while maintaining structural integrity.
Key Advantages of Blow Molding:
- Material Efficiency: Uses less material compared to other methods for hollow products.
- High Speed Production: Fast cycle times increase output.
Learn more about the efficiency of blow molding at blow molding efficiency17.
Compression Molding: Strength Meets Cost-Effectiveness
Compression molding is suitable for large, thick-walled items and offers significant cost savings on heavy-duty products.
Benefits of Compression Molding:
- Lower Raw Material Costs: Suitable for bulk production with less waste.
- Durability: Creates strong components ideal for high-stress applications.
For further reading on compression molding benefits, see compression molding advantages18.
Effective Mold Design: The Backbone of Cost Reduction
a well-designed mold can drastically affect the overall cost and quality of production. Factors include: | Factor | Impact on Cost |
---|---|---|
Mold Structure | Affects precision and waste levels | |
Gate Location | Influences cycle time and efficiency | |
Cooling System | Determines production speed |
By investing in quality mold design, manufacturers can ensure consistent product quality and minimize defects, leading to cost savings over time.
For more on mold design impact, check mold design impact19.
Injection molding minimizes waste and lowers manufacturing costs.True
Injection molding's precision reduces scrap material, making it a cost-effective choice for manufacturers.
Blow molding is inefficient for producing hollow plastic products.False
Contrary to the claim, blow molding is efficient, using less material while maintaining quality in hollow products.
Conclusion
Explore how plastic molding services improve manufacturing processes through various techniques while emphasizing the importance of mold design and material selection for cost reduction.
-
This link provides detailed insights into various molding techniques that can enhance your understanding of the industry. ↩
-
This resource offers comprehensive information on extrusion processes used in manufacturing plastic products. ↩
-
Learn more about blow molding processes and their applications in this informative link. ↩
-
Explore compression molding techniques that are vital for producing durable plastic parts. ↩
-
Dive deeper into mold design essentials to optimize your manufacturing process with this valuable resource. ↩
-
This link covers best practices for material selection in plastic molding that could be beneficial for your projects. ↩
-
Get insights into post-processing methods to improve the quality of your molded products with this link. ↩
-
Discover best practices in mold design that can enhance your product quality through this comprehensive guide. ↩
-
Explore advanced cooling techniques in mold design that optimize manufacturing efficiency. ↩
-
Gain knowledge on selecting materials for mold designs to improve durability and efficiency. ↩
-
Discover the top plastic materials suited for your molding projects and how to choose them wisely. ↩
-
Discovering innovative value-added services can help optimize your molding process and improve product outcomes. ↩
-
Learn how quality inspections can ensure product standards and reduce defects in your molding operations. ↩
-
Explore tailored material selection for enhanced performance and cost-effectiveness in your products. ↩
-
This link provides an in-depth look at various plastic molding techniques that can lead to significant cost savings in manufacturing. ↩
-
Find out how extrusion molding can save you money in your manufacturing process with this comprehensive guide. ↩
-
Explore the advantages of blow molding in reducing material costs and increasing efficiency through this detailed article. ↩
-
Learn how compression molding can offer a balance between strength and cost-effectiveness in this insightful post. ↩
-
This resource outlines how effective mold design can contribute to lower production costs significantly. ↩