Have you ever thought about how a bit of order changes mold creation completely?
Standardization in injection mold design means following common rules. Designers use these rules to simplify work and cut down on mistakes. This unified approach really helps. Consistent dimensions, structures and materials bring the same results each time. Manufacturing becomes easier and very precise. Every step gets smoother. Quality steps up, too.
Picture stepping into a workshop where tools rest exactly where they should be. Every tool in its place. Every measurement is exact. This order is what standardization creates in injection mold design – clean and precise. Exploring each standardized part, from mold sizes to cooling systems, helps us see their role. These practices make difficult processes simpler and strongly reduce costs. For instance, uniform gate sizes allow plastic melts to fill evenly, stopping flaws. Even, smooth filling of the material. Producing high-quality parts requires this level of consistency. Each part contributes to better manufacturing. Dive in to learn how each step plays a role in this enhanced production flow.
Standardized mold dimensions simplify design process.True
Standardized dimensions reduce complexity, aiding in efficient design.
Cooling channel diameter is always 10mm.False
Cooling channel diameter ranges from 6-16mm, not fixed at 10mm.
What Are the Key Dimensions in Mold Standardization?
Have you ever thought about how mold standardization affects your manufacturing? Understanding the basics helps production run smoothly and improves quality. Quality might even really increase.
Key dimensions in mold standardization include sizes of parts, gate and runner measurements and structural elements such as demolding mechanisms and cooling systems. These standards keep things compatible and efficient. This is very important for successful injection molding.
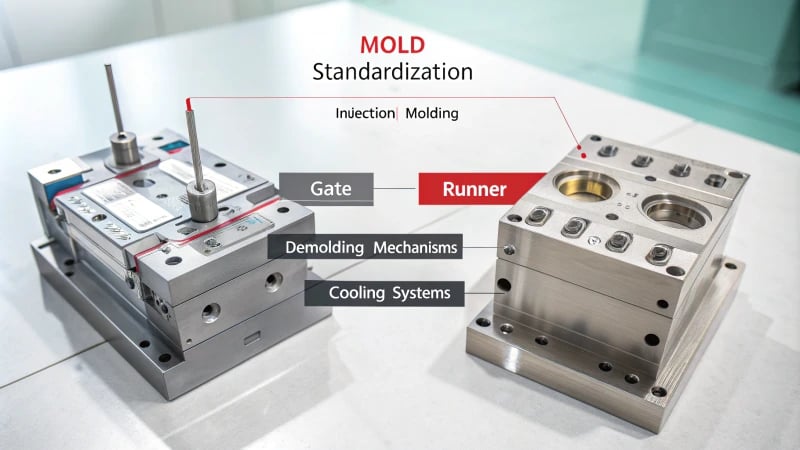
Mold Component Dimensions
The first time I chose mold parts, I felt like I was solving a big puzzle. Standard parts like fixed and moving templates made it simple. Detailed rules based on length, width, and height helped me pick the right ones for the injection machine. It became much less scary.
Table: Template Dimensions
Component | Standard Length | Standard Width | Standard Height |
---|---|---|---|
Fixed Template | 300 mm | 400 mm | 30 mm |
Movable Template | 250 mm | 350 mm | 25 mm |
Guide pins and sleeves play essential roles, following fixed sizes for diameter and length. Their standardization1 eases buying from different sellers. This is very helpful.
Gate and Runner Dimensions
Different gate types were confusing at first. Understanding their standard sizes really changed things for me. Side gates have fixed width and depth to improve plastic flow. This makes avoiding defects possible, not just a wish.
Table: Gate Types and Specifications
Gate Type | Width | Depth |
---|---|---|
Side Gate | 1 mm | 2 mm |
Point Gate | 0.5 mm | 1 mm |
Matching these sizes with the injection machine’s nozzle reduces pressure loss. I learned this the hard way when my first designs didn’t fit right.
Structural Elements: Demolding Mechanisms
Working with demolding mechanisms felt difficult at the start. Push rods and plate demolding became my preferred options for simple parts. Standard size rules for layout and diameter helped keep everything stable when removing parts.
Cooling System Dimensions
Cooling systems, those hidden channels in the mold, were once a mystery to me. Knowing that standard sizes (6-16mm) keep temperatures even was a turning point. Now, reducing shrinkage and improving part quality seems more like science than art.
These important sizes are more than just numbers; they are the backbone of good manufacturing. Using these standards has lowered mistakes in my designs, which has really improved product consistency2.
Standardized guide pins ensure precise mold guidance.True
Guide pins have standard dimensions to ensure accurate mold alignment.
Cooling channels are always 10mm in diameter.False
Cooling channels range from 6-16mm in diameter, not fixed at 10mm.
How Do Standard Structures Enhance Mold Reliability?
Do you ever think about how using the same parts for molds can really change how steady and quick things work?
Standard structures in mold design add reliability by creating consistency, precision and simple assembly. Unified standards and specifications probably decrease errors. Errors drop. Manufacturing time shrinks and product quality rises. Quality really improves.
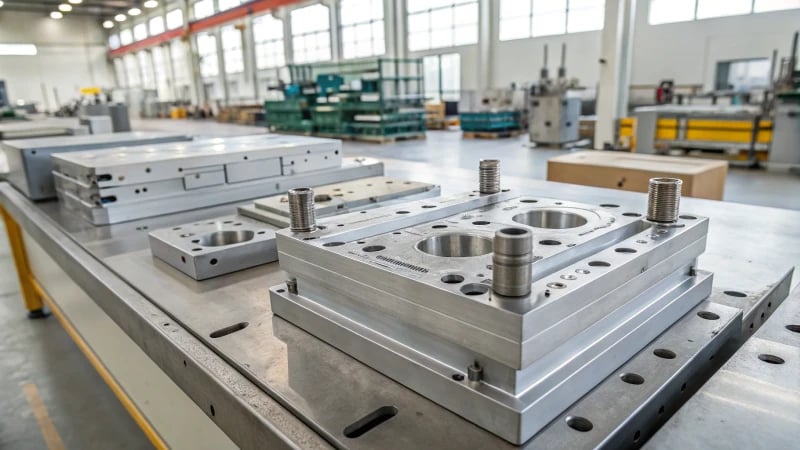
The Role of Standardization in Injection Mold Design
Let me take you back to when I began working with mold design. Complexity overwhelmed me with so many components involved. But as I learned more, I found that standardization saved me. Sticking to common guidelines for designing molds helped every part fit the needed sizes and details. It was like having a recipe that always gave a perfect dish.
By adhering to these standards, mold manufacturers can select components according to machine specifications, enhancing mold reliability3.
Component | Standard Dimensions |
---|---|
Template | Length, width, height |
Guide Pins & Sleeves | Diameter, length |
Structural Standardization
In those early days, demolding mechanisms felt challenging. Standard structures for mechanisms like push rod or plate made the process easier. Standards for where to place and size them made things smoother and less likely to go wrong.
Similarly, cooling systems got better too. Standard designs for channel sizes and spaces meant cooling happened evenly. This standardized approach4 reduced shrinkage and really improved part quality.
Standardized Design Process
Standardization is more than parts; it starts with the original design:
- Customer Demand Analysis: I find out what clients truly want, from product needs to materials.
- Conceptual Design: It feels like solving a puzzle based on client desires.
- Detailed Design: Everything gets carefully detailed with exact sizes and limits.
Following this order simplifies the work and probably increases mold efficiency5.
Material Standardization
Picking the right materials feels like choosing perfect ingredients for a dish. Mold materials must reach certain targets like hardness and strength. Using standard materials for different parts keeps costs stable without losing performance.
For key molded parts, I often pick high-quality mold steel because it’s strong and durable. For extra components, I go for cheaper options that work well and aren’t too costly.
Using these standard practices greatly improves mold reliability. Molds handle stress while keeping accuracy and quality during production. This careful approach not only enhances the final product but also refines the whole manufacturing process6.
Standard mold dimensions simplify design and processing.True
Standard dimensions allow for easier selection and reduce complexity.
Cooling channels in molds are always 6-16mm in diameter.True
The standard cooling channel diameter ensures effective heat dissipation.
How Do Cooling Systems Contribute to Standardization?
Have you ever thought about how cooling systems keep everything running well in mold design?
Cooling systems in mold design have a key role in standardization. These systems keep temperatures steady, cut down cycle times and improve part quality. Standard cooling rules help manufacturers work better. They lower defects. They help meet industry rules.
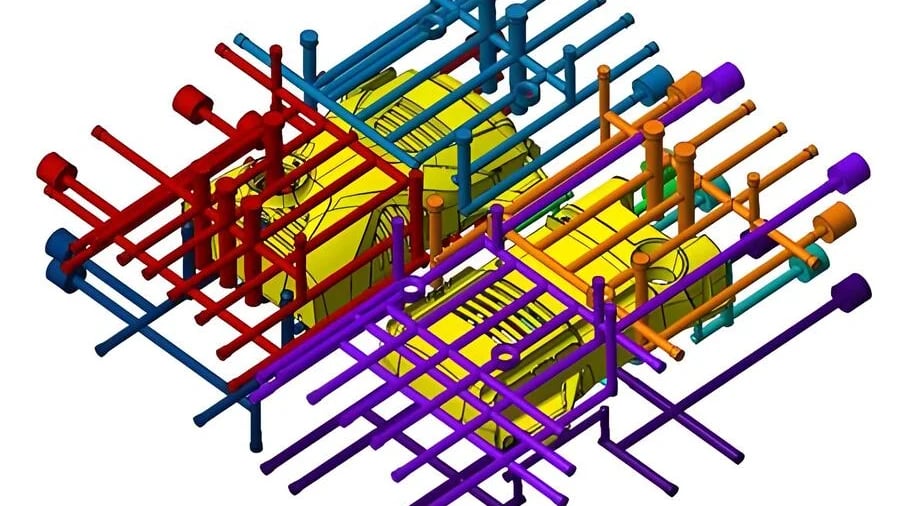
Understanding Cooling Systems in Mold Design
Think about working in a busy factory where everything must be perfect. A good cooling system is crucial in mold design. It’s like an unnoticed hero, impacting product quality and production speed. Following standard rules like channel size and distance is very important. These rules help achieve high-quality results by reducing shrinkage and deformation in plastic parts, which is very important for staying competitive in our industry.
Standard Cooling Parameters
- Channel Diameter: Typically ranges from 6-16mm. This detail is something I always check because it influences how well we cool our products.
- Channel Spacing: Usually 1-2 times the channel diameter from the cavity surface. Doing this makes cooling effective and consistent.
These parameters ensure that the cooling is effective and predictable.
Parameter | Standard Range |
---|---|
Diameter | 6-16mm |
Spacing | 1-2x diameter |
Impact on Production Quality
I remember past projects with warping problems. Standardized cooling systems have become my solution to control shrinkage and make sure every product meets high standards. By following these norms, manufacturers can achieve consistent7 results across different production runs, which clients value a lot.
Efficiency and Cycle Time Reduction
Time equals money. Efficient cooling lowers cycle times, directly impacting production speed and cost-effectiveness. I’ve noticed how standard cooling designs improve operations by cutting energy use and reducing machine wear—solving many problems at once.
Advantages of Standard Layouts
When starting a new project, I choose standard layouts such as series or parallel arrangements. These layouts spread coolant evenly, optimizing the entire cooling process by preventing hot spots and ensuring every mold part cools uniformly.
The standardization of these aspects not only aligns with industry norms but also facilitates easier maintenance and interchangeability of mold components, enhancing overall operational efficiency.
Standardized mold dimensions simplify design and processing.True
Standard dimensions reduce complexity by allowing easy selection and manufacturing.
Cooling channel diameter is standardized between 6-16mm.True
The cooling channel diameter follows standard ranges to ensure uniform cooling.
Why is material selection crucial in mold design?
Ever thought about how the right material changes your mold design from good to amazing? Let’s go on a journey to explore the crucial role of materials in creating molds.
Picking the right materials for mold design matters a lot. It greatly influences how long the mold lasts. Manufacturing becomes smooth and easy with good material choices. Materials have a big impact on product quality. Smart choices save money. Fewer defects occur with the right materials. Molding processes perform nicely with proper materials. Important fact꞉ materials matter.
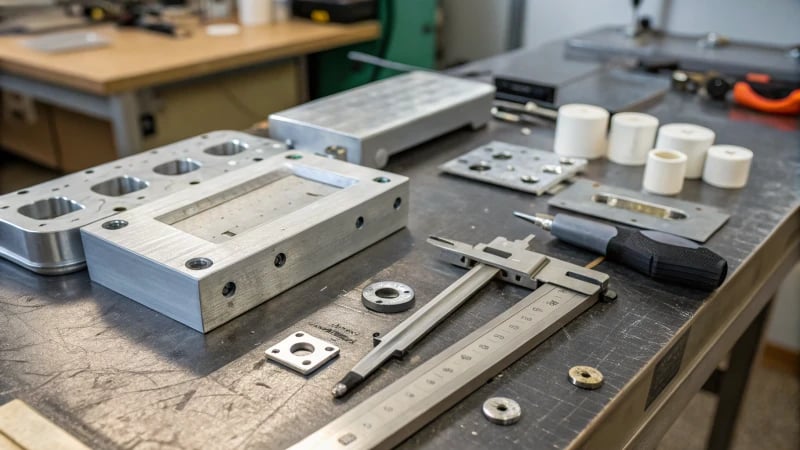
Impact of Material Properties
I remember my first time picking materials for a project at my old job. The pressure felt immense, as the mold’s durability8 depended on it. High-quality mold steels like P20 or H13, known for resisting wear, felt like armor for my mold. These steels offer long life even after many cycles. Reliable tools don’t let you down.
Material | Hardness (HRC) | Application |
---|---|---|
P20 | 30-50 | General molds |
H13 | 40-55 | High-precision molds |
Material hardness and toughness matter because they tell whether the mold handles intense pressure from the plastic melt. Imagine balancing strength and flexibility; too much of one may cause cracks or bends.
Standardization and Efficiency
Material standardization reminded me of a puzzle where every piece fits perfectly. Standardized guide pins and sleeves allowed precise guidance during mold operations9. This move simplified manufacturing and increased efficiency.
Influence on Product Quality
Material choice directly affects product quality. I learned this hard lesson when poor thermal conductivity caused warping in a client’s product. Materials with excellent thermal properties ensure even cooling, like a well-baked cake coming out evenly cooked.
Cost Implications
Balancing cost and quality is an art. Initially, high-quality steel seems costly, yet it cuts long-term costs by reducing maintenance and replacements. For less critical parts, choosing lower-grade materials can save money without losing performance. Minimizing downtime with wear-resistant materials also impacts production costs positively.
Material Selection for Different Mold Parts
Every mold component has unique needs. Core and cavity sections require high-strength materials due to contact with melted plastic, similar to how a chef’s knife needs a strong blade. Auxiliary parts may use cheaper options like carbon structural steel.
Understanding these details helps each component work best in its role, supporting efficient production cycles and steady product quality. Standardization of injection mold design10 helps with choosing materials for different mold parts.
In conclusion, selecting the right materials in mold design goes beyond a technical requirement—it’s a strategic choice affecting design efficiency, product quality, and cost control. It’s like an orchestra where every instrument plays its part beautifully.
Standard mold frame dimensions simplify design.True
Standard dimensions reduce complexity, aiding manufacturers in selecting appropriate components.
Cooling channels always have a fixed diameter.False
Cooling channel diameters vary between 6-16mm based on standard ranges.
How Does Standardization Influence the Design Process?
Have you ever thought about how common rules change the way we design, keeping both imagination and speed in harmony? Here are some thoughts from personal experience.
Standardization in design processes increases efficiency, reduces errors and keeps things consistent. Designers follow established rules to simplify their work. They also foster teamwork and maintain quality in different projects.
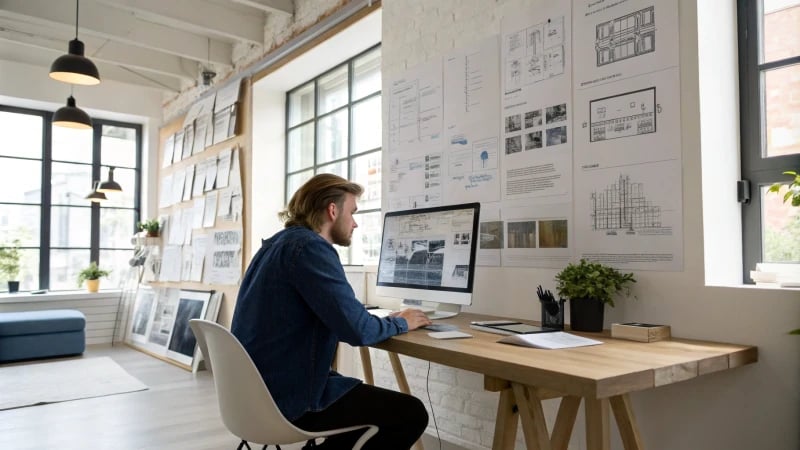
Increasing Efficiency through Standardization
In my early days of working on injection mold design11, I saw that standard sizes for mold parts like guide pins led to fewer problems. Think about a tidy room – standardization provides that kind of order. It works like a trusty map, letting you spend more time reaching your goal instead of figuring out the path.
Achieving Uniformity and Quality
Consistency is important. Using standard sizes and features for things like gates and runners led me to create products that are uniform in quality. In making plastic parts, where even tiny faults can cause big issues, uniformity is very important.
Component | Standard Dimension Range | Importance |
---|---|---|
Mold Frame | Length, width, height | Reduces complexity |
Guide Pins | Diameter and length | Ensures precise guidance |
Sparking Innovation within Limits
Standardization felt like it limited creativity until it became clear it acts like a jumping-off point. With a steady framework, focusing more on new ideas was easier. Consider the demolding mechanism: standardized push rod designs allow exploration of aesthetics without worrying about function.
Improving Teamwork
In my team at a mid-sized manufacturing company, I noticed how standardization encourages better teamwork. Everyone communicating in the same way leads to clear exchanges and fewer misunderstandings or delays.
Designers such as Jacky in mid-sized manufacturing companies12 use streamlined processes that align with industry standards to carry out projects more smoothly and effectively.
Harmonizing Creativity and Standard Methods
The creative design stage flourishes within standard limits. Deciding on structural things like parting surfaces with rules helps keep creativity and efficiency balanced.
- Two-plate mold for basic shapes
- Three-plate mold for difficult gates
These decisions, guided by standards, allow adjusting based on product needs while keeping creativity and efficiency in check.
Using standardization does not crush creativity; it forms a strong base for fresh ideas to bloom. This way not only improves design results but also refines workflow all over.
Standard dimensions simplify mold design.True
Using standard dimensions reduces complexity and aids in efficient design.
Custom gate sizes improve mold efficiency.False
Standardized gate sizes ensure even fill and reduce defects.
Conclusion
Standardization in injection mold design enhances efficiency, reduces errors, and improves product quality by adhering to unified dimensions, specifications, and materials throughout the manufacturing process.
-
Understand how standardized dimensions simplify manufacturing and reduce costs. ↩
-
Discover how consistent mold standards lead to reliable product quality. ↩
-
Explore how standard dimensions streamline mold manufacturing, improving consistency and reliability. ↩
-
Discover how structural standardization in molds ensures reliability and consistency in production. ↩
-
Learn how a standardized design process enhances efficiency in mold manufacturing. ↩
-
Understand how standardized material selection improves mold performance and cost-efficiency. ↩
-
Learn how standardization contributes to reliable and uniform product outcomes. ↩
-
Exploring this link provides insights into why specific steel properties are vital for effective mold design. ↩
-
This link elaborates on how standardization streamlines manufacturing processes, ensuring consistency and efficiency. ↩
-
Understanding standardization can enhance your knowledge of efficient practices in injection mold design. ↩
-
Learn about essential standards that guide injection mold design to improve precision and efficiency. ↩
-
Explore how standard practices enhance team collaboration in manufacturing design projects. ↩