I still recall my first experience with flow marks. It felt like looking at a puzzle that seemed unsolvable. Then, the mystery unraveled. Gate position design revealed the secret.
To avoid flow marks on products during injection molding, place the gate in the right position. Smooth melt flow is important. It prevents eddy currents. Product shape and wall thickness should be considered. Correct gate placement reduces surface imperfections significantly. Very important.
Putting the gate in the right place is crucial. But I’ve realized that knowing how the melt moves really changes everything. Thinking about the shape and how thick the walls are helps a lot. I have turned problems into amazing pieces. Let’s look at how these details can change your molding work.
Gate position affects flow marks in injection molding.True
Proper gate placement ensures smooth melt flow, reducing flow marks.
Multiple gates should always be used in injection molding.False
Use multiple gates only if they ensure balanced melt distribution.
How Does Melt Flow Direction Affect Flow Marks?
Picture shaping the ideal plastic part without annoying flow marks. Success depends on knowing how the plastic moves inside the mold.
Melt flow direction is very important to stop flow marks by letting the molten material fill the mold without problems. Correct gate placement is crucial to control this flow well.
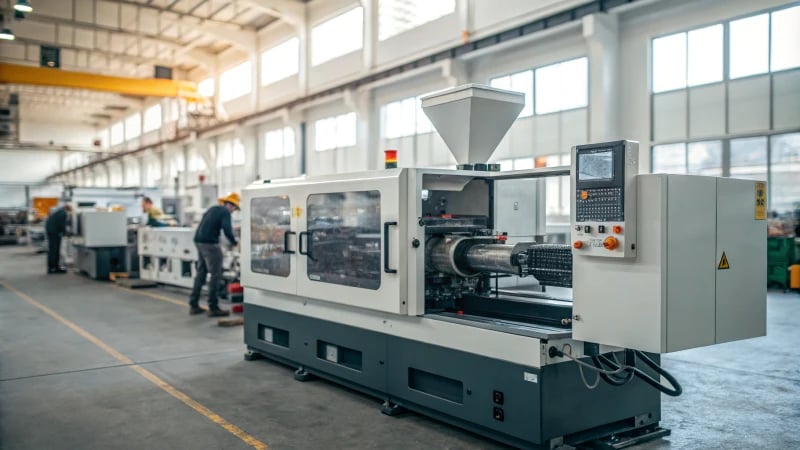
Understanding Melt Flow Dynamics
I remember when I first saw a perfect plastic piece. No flow marks, just smooth and flawless. The secret? Mastering melt flow dynamics holds the answer. Molten material moving through the mold decides the surface quality of the product. A smooth transition of melt flow helps manufacturers avoid ugly flow marks1. Think of melt entering through a gate that leads it gently along the product’s shape, much like water flowing along a riverbed.
Importance of Gate Position
Gate position really changes things. I worked on a part with many ribs and curves once. Placing the gate at an easy point seemed tempting, but it would have gone wrong! Instead, we put it along a curve. This allowed the melt to slide smoothly without marks. Many ribs involved? Strategic placement stops annoying eddy currents, which maybe cause imperfections.
Product Type | Recommended Gate Placement | Potential Issues if Ignored |
---|---|---|
Curved Surface | Along a curve | Impact marks |
Multiple Ribs | Near uniform thickness | Eddy currents |
Designing for Uniformity
Designing for uniformity has probably saved me from sleepless nights. For example, when working on a flat plastic product, gates in areas with even wall thickness keep consistent cooling rates. This avoids flow marks2. "Let thick areas take the heat first!" I often say. Doing this leads to a gentle change into thinner sections, reducing temperature changes and preventing flow marks.
Effective Use of Multiple Gates
In larger molds, using multiple gates resembles an orchestra. I recall coordinating them on a big round product. Their balanced distribution was key. The melt flowed evenly, reducing chaotic interactions that cause defects. The order in which these gates opened was our secret—starting with specific gates filled crucial areas first before others joined—a very significant improvement resulted in product beauty3.
Gate position affects melt flow direction.True
Proper gate placement ensures smooth melt flow, preventing flow marks.
Eddy currents improve product quality.False
Eddy currents cause chaotic flow, leading to defects in the product.
How Do Product Shape and Wall Thickness Affect Gate Design?
Have you ever thought about how the shape and thickness of a product control the complex details of gate design in injection molding? Let me guide you through the mix of skill and science that drives these choices.
Product shape and wall thickness play a key role in gate design for injection molding. These factors influence how the melt flows and help stop defects. Gate positioning allows for smooth melt flow. It avoids locations with thin walls. Gates should be placed in areas with even thickness to reduce defects. Uniform thickness is very important.
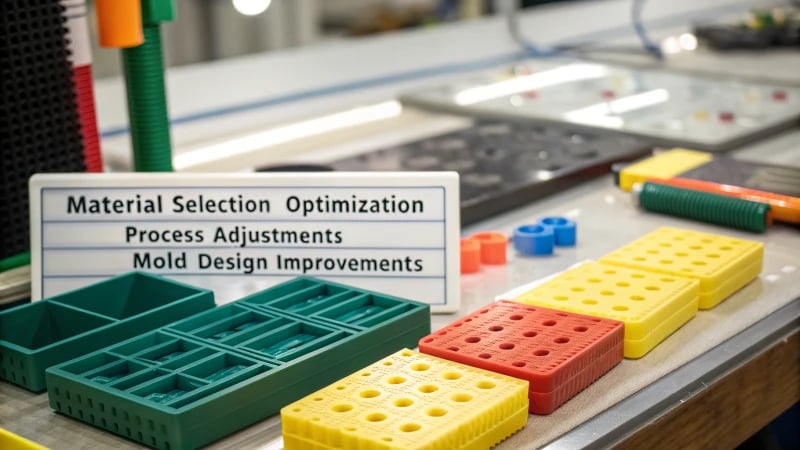
The Role of Product Shape
Imagine the shape of your product. Suppose you’re creating a smooth, curved remote. The way melted plastic moves during the process must follow the curves, similar to how I ease into my favorite chair after work. If the gate sits right – tangentially, then – the melt follows the shape naturally, avoiding any ugly marks or flaws. It’s like that perfect cup of coffee in the morning – smooth and just right.
For example, when dealing with a curved surface4, ensure that the gate is positioned tangentially to enable a natural flow, minimizing flow marks and defects.
Importance of Wall Thickness
Now, wall thickness is different. Picture holding a tablet with even thickness. You need the gate right in the middle or along the edge to stay consistent. This stops any uneven results, just like how I want my morning pancakes cooked evenly.
Wall Thickness | Recommended Gate Position |
---|---|
Uniform | Center/Edge |
Thin-walled | Away from direct impact |
In thinner areas, it’s key to fill the thicker parts first, like pouring syrup into the pancake center before it spreads to the sides.
Preventing Eddy Currents
Imagine a busy kitchen where everything spins out of control. That’s like eddy currents in complex shapes. In multi-compartment designs such as multi-room organizers5, careful gate planning keeps the melt moving smoothly, stopping those wild swirls that cause defects.
Multiple Gates Strategy
For large items like big storage bins I often organize, multiple gates really help. Placing them symmetrically allows even melt spread, like spreading cake toppings evenly.
Sequence control can also play a role; opening specific gates first helps manage initial melt distribution effectively.
Avoiding Thin-Wall Impacts
Hits on thin walls can shock you like biting into a sour lemon. Place gates to hit thicker sections first, letting a gentle flow to thinner areas. Imagine filling a bowl with cereal before adding milk – it keeps everything clean.
This approach is beneficial when designing items like plastic boxes with thin edges where gradual filling prevents defects.
Considerations for Multiple Gates
In situations needing many gates, such as in big car dashboard designs6, balance matters. A balanced layout around your product fills things evenly, cutting defect risk.
Use sequence control strategies to enhance melt flow orderliness and reduce defect likelihood—like orchestrating a symphony where every part fits just right.
Using these smart strategies improves product quality and raises manufacturing efficiency. These ideas are just the start—explore more to perfect your designs and create a masterpiece every time.
Melt flow should avoid directly impacting cavity walls.True
Direct impact can cause flow marks; a smooth transition is essential.
Multiple gates should be unevenly distributed around the product.False
Even distribution ensures balanced melt flow, reducing local flow marks.
Why is Gate Layout Crucial in Multi-Gate Molding?
Do you ever think about why arranging gates is so important in multi-gate molding?
Gate layout in multi-gate molding is crucial. It helps melt flow evenly and reduces defects like flow marks. The cooling times get better. Correct gate placement improves product quality. It really increases manufacturing efficiency.
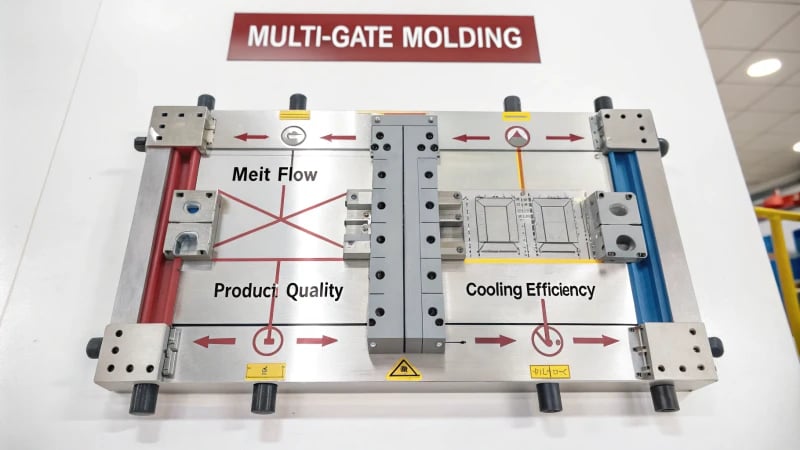
Understanding the Melt Flow Direction
There was a time when I worked on a project with a very tricky curved surface. Imagine trying to get hot melted plastic to move along a curve smoothly without any problems. The secret lies in gate layout7. Putting the gate at the tangent of the curve allows the melt to flow smoothly without defects. It feels like setting up a roller coaster ride that glides easily.
Designing for Product Shape and Wall Thickness
I remember designing flat plastic items and facing the challenge of placing gates where the walls were the same thickness. The trick is to get consistent cooling and avoid flow marks. Think of it like baking a cake so it cooks evenly, not burning on one side. Placing gates either in the center or at the edges can influence the outcome.
Product Type | Ideal Gate Position |
---|---|
Curved Surface | Tangent to the curve |
Flat Product | Center or edge in uniform area |
Thin-Walled Part | Away from direct impact areas |
The Role of Multiple Gates
There was a time we needed multiple gates on a big round item. Balancing them was necessary for even flow and fewer surface problems. It was like arranging a music performance where each instrument had to play in harmony. We controlled which gate released the flow first to focus on critical areas, enhancing our product’s appearance.
Additionally, controlling the injection sequence of these gates can further enhance product quality by strategically opening certain gates first, directing initial melt flow to critical areas before merging other flows.
Avoiding Common Pitfalls
Poorly designed gate layouts sometimes produced chaotic flows, like little whirlpools inside the mold. Planning gate positions with care is very important, especially in complex designs. Each choice about where to place a gate impacts the final quality of molded items.
Mastering gate layout involves knowing melt behavior and product shape while considering production goals. This knowledge is essential for anyone trying to optimize molding processes. Dive deeper into subjects like melt flow dynamics8 and injection sequence strategies9 to learn more about improving gate layouts.
Gate position affects melt flow smoothness.True
Correct gate placement ensures melt flows without impacting walls, reducing marks.
Multiple gates should be randomly placed.False
Gates must be evenly distributed for balanced melt flow and minimal marks.
How Can Sequence Control in Gate Operation Reduce Flow Marks?
Do you ever think about whether the method used to handle gates during molding could be the key to perfect plastic surfaces?
Sequence control in gate operations lowers flow marks by carefully directing melt flow during injection molding. Timing helps decide when each gate starts and stops. This timing leads to a smooth mold fill. It reduces imperfections. This is very effective.
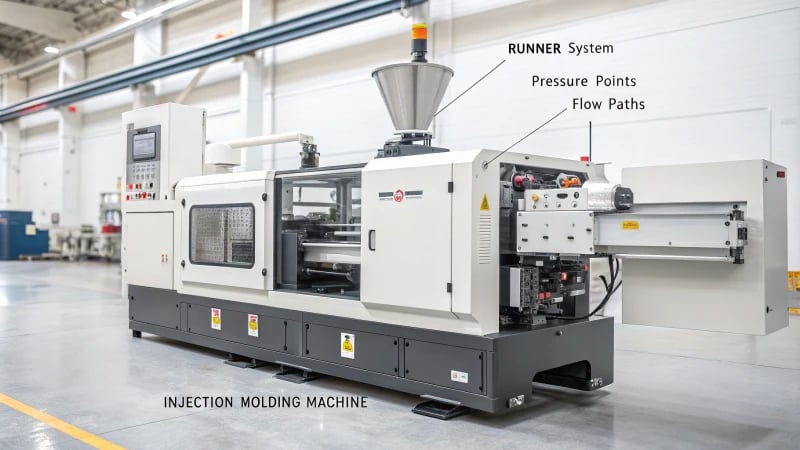
Understanding Sequence Control
Imagine a conductor leading a symphony. Every instrument, like a gate in molding, must join in at the right moment for harmony. Sequence control focuses on this timing during injection molding. By choosing which gates open and when10, manufacturers can really change how the liquid fills the cavity. This precision helps with even spread and a smooth surface.
The Role of Melt Flow Direction
Think of pouring syrup on pancakes. You want even spreading, right? The direction in which melt flows must be spot-on for smooth surfaces. The gate needs a perfect position so the melt enters smoothly. For plastic products with curved surfaces, place the gate along the curve11. This allows natural flow and stops sudden impacts or ugly marks.
Designing Gate Positions
Design gate spots thoughtfully, like planning a trip. Consider your route and wheel thickness—or here, the product’s shape and wall thickness. It is essential to place gates where wall thickness stays the same for steady melt flow and cooling rates.
Product Type | Recommended Gate Position |
---|---|
Curved Surface | Tangent to the curve |
Flat Product | Center or edge |
Thin-walled | Bottom or thick side |
Placing gates centrally on flat areas keeps distribution even, lowering the chance of cooling mishaps.
Balanced Distribution for Multiple Gates
Imagine decorating a big cake with several frosting bags; you want each bag to do its part equally. Similarly, balanced gate setup achieves this for multiple gates. Open gates one after another to fill certain spots first, creating a foundation before adding more melt. This methodical approach minimizes flow marks by promoting orderly melt flow.
Practical Examples
Picture molding a plastic box with thin walls. Positioning the gate at the bottom allows it to fill thick parts first, then move to thin edges—cutting down temperature changes that cause flaws. For large round products, space gates equally to allow melt to flow evenly from all sides.
These tips show how designers use sequence control to cut down flow marks in injection molding. To explore further on this topic, consider searching for advanced sequence control techniques12 or attending specialized workshops to see practical applications firsthand.
Gate position affects melt flow direction.True
Proper gate positioning ensures smooth melt flow, reducing flow marks.
Eddy currents improve product aesthetics.False
Eddy currents cause chaotic flow, leading to undesirable flow marks.
Conclusion
Proper gate positioning in injection molding is essential to avoid flow marks, ensuring smooth melt flow and uniform cooling by considering product shape and wall thickness.
-
Explore how controlling melt flow direction minimizes defects in plastic products. ↩
-
Learn about design principles that ensure consistent cooling and reduce defects. ↩
-
Discover how strategic gate use enhances product quality and appearance. ↩
-
Discover detailed techniques for positioning gates on curved surfaces to optimize melt flow and reduce defects. ↩
-
Learn about effective design strategies for molds with multiple compartments to ensure smooth melt flow. ↩
-
Explore best practices in gate design for improving product quality and manufacturing efficiency. ↩
-
Learn why strategic gate layout is vital for reducing defects in injection molding. ↩
-
Discover how melt flow dynamics influence gate placement decisions. ↩
-
Understand how controlling injection sequences can optimize multi-gate systems. ↩
-
Learn about sequence control’s role in optimizing melt flow for quality finishes in injection molding. ↩
-
Learn about sequence control’s role in optimizing melt flow for quality finishes in injection molding. ↩
-
Discover cutting-edge methods to implement sequence control effectively in your manufacturing processes. ↩