Ever looked at a sleek car interior or your favorite gadget and wondered how it got that perfect finish?
Common surface finishing techniques for injection molded parts are painting, electroplating, hot stamping, silk screening, pad printing, laser engraving, frosting, and polishing, each improving appearance and performance through unique processes.
Every time I see a well-designed product, I think about the intricate surface finishing techniques that bring it to life. From painting to electroplating, each method has its own unique charm and application. Let’s explore these fascinating techniques that make our everyday items not only functional but also visually appealing.
Painting enhances UV resistance of molded parts.True
Painting provides a protective layer that can enhance UV resistance.
Laser engraving weakens the structural integrity of parts.False
Laser engraving is a surface process and doesn't affect structural integrity.
- 1. How Does Painting Treatment Enhance Injection Molded Parts?
- 2. Why Should You Consider Electroplating for Plastic Components?
- 3. When Should You Use Hot Stamping in Product Design?
- 4. How Can Silk Screen Processing Improve Product Branding?
- 5. Why is Laser Processing Ideal for Customization?
- 6. What Are the Functional Advantages of Frosted Treatments?
- 7. Conclusion
How Does Painting Treatment Enhance Injection Molded Parts?
Imagine transforming a simple plastic part into something that not only looks stunning but also stands the test of time. That’s what painting treatment can do for injection molded parts.
Painting treatment enhances injection molded parts by boosting aesthetics and durability, offering various colors and textures, and providing protection against environmental damage.
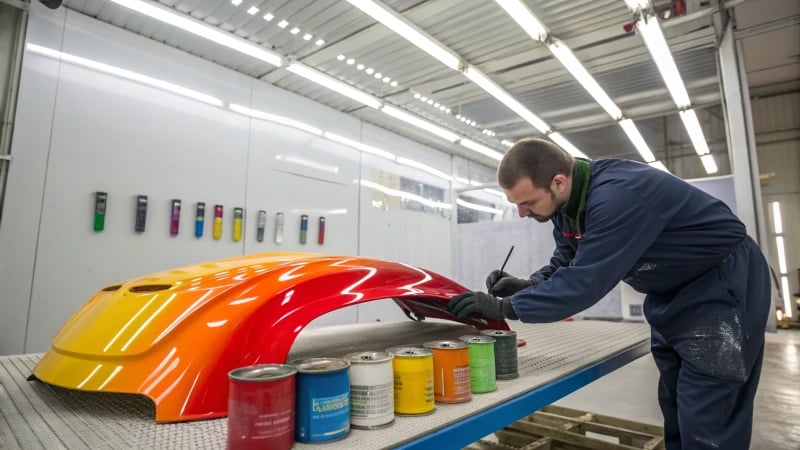
The Principles of Painting Treatment
Remember the first time you painted a room and felt that rush of satisfaction seeing the transformation? Well, painting injection molded parts is a bit like that, but with a scientific twist. By applying a paint layer, we not only change the part’s color and texture but also enhance its durability. Just as the pigment brings vibrant hues, the resin ensures the paint sticks and protects.
Application Scenarios
Application Area | Effects |
---|---|
Car Interiors | Matches car style with various colors |
Electronic Shells | Achieves metallic appearance |
Outdoor Plastics | Enhances corrosion resistance |
Enhanced Appearance and Functionality
-
Rich Color Selection
Have you ever walked into a car showroom and marveled at how the interior just "fit" with the car’s vibe? That’s the magic of a well-thought-out color scheme. Painting gives us that flexibility, letting products resonate with consumer tastes or brand identities. -
Special Appearance Effects
Think of those sleek electronic gadgets with surfaces that gleam like metal. They’re not metal, but with special paints, they achieve that premium look without the extra cost or weight.
-
Improved Durability
Remember that time your outdoor furniture faded in the sun? A good weather-resistant paint can prevent that, giving outdoor plastics longer life by shielding them from UV rays and harsh chemicals.
Exploring Other Surface Treatments
While painting is a versatile champion, I often explore other treatments like electroplating1, hot stamping, and silk screen processing. Each method has its own perks, offering unique benefits from metallic finishes to intricate pattern prints.
Comparative Overview
Treatment Method | Key Benefit |
---|---|
Electroplating | Metallic appearance and shielding |
Hot Stamping | Decorative and high-end looks |
Silk Screen | High-precision colorful patterns |
Each method finds its niche, tailored to specific design needs or performance goals. Like when I needed to make a logo pop on an electronic device, silk screen processing2 was my go-to for its precision and vibrant results. Understanding these techniques lets me choose just the right one to elevate my designs to meet both aesthetic desires and industrial demands.
Painting treatment increases the durability of outdoor plastics.True
Weather-resistant paints enhance lifespan by protecting against UV and chemicals.
Electroplating is preferred for high-precision pattern printing.False
Silk screen processing, not electroplating, is used for detailed patterns.
Why Should You Consider Electroplating for Plastic Components?
Have you ever wondered how a plastic component can suddenly transform into something that looks like shiny metal?
Electroplating plastic components increases durability, corrosion resistance, and aesthetics by applying a metallic layer. It extends product life and offers a lightweight metallic finish, making it valuable in manufacturing.
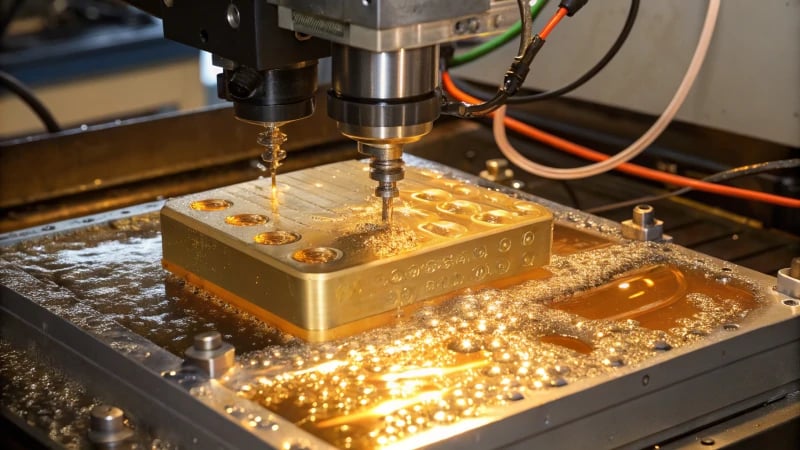
Understanding Electroplating
When I first stumbled upon electroplating, it felt like witnessing magic—turning a basic plastic piece into something that gleams like metal. Electroplating uses electrolysis to deposit a metal coating on plastic parts, boosting their durability and aesthetic value. Typically, metals like copper, nickel, and chromium are involved.
Here’s a simple table showing some of their magic properties:
Metal | Attributes |
---|---|
Copper | Conductivity, corrosion resistance |
Nickel | Hardness, wear resistance |
Chrome | Brightness, anti-tarnish properties |
Enhanced Durability and Corrosion Resistance
In my experience, plastic components often lack the resilience3 needed for demanding applications. Electroplating comes in handy by forming a hard protective barrier against wear and environmental damage. Take bathroom fixtures, for example—they’re constantly exposed to moisture. Chrome-plated plastic handles thrive in such conditions, resisting corrosion effortlessly.
Aesthetic Improvements with Electroplating
There’s something incredibly satisfying about seeing a mundane plastic component transformed with electroplating. It bestows a metallic finish without the extra heft. Nickel or chrome layers create shiny, reflective surfaces that make products like electronic casings visually appealing and premium-looking.
Applications in Various Industries
Electroplating is the unsung hero across multiple industries:
- Automotive: Where it adds durable, decorative finishes to interior parts.
- Electronics: Enhancing electromagnetic shielding capabilities.
- Consumer Goods: Giving everyday items that coveted premium look.
Comparative Surface Treatment Techniques
While electroplating is powerful, exploring other methods like painting treatment4 and hot stamping is beneficial too:
Treatment | Advantages |
---|---|
Painting | Rich color selection, enhanced texture |
Hot Stamping | High-end appearance, branding enhancement |
These alternatives let designers tailor surface treatments to meet specific needs. Yet, electroplating still stands out for its functional and aesthetic enhancements for plastic components.
Considering Limitations and Innovations
Despite its many advantages, electroplating has its limitations—especially concerning environmental impacts due to chemical use. It’s heartening to see innovators working on eco-friendly options like physical vapor deposition (PVD) that offer similar benefits minus the harmful by-products.
Staying updated on these advancements ensures electroplating remains a sustainable choice in manufacturing. For those eager to delve deeper into cutting-edge techniques, resources on cutting-edge surface treatments5 are invaluable.
Electroplating improves plastic durability.True
Electroplating adds a protective metal layer, enhancing durability.
Electroplating adds weight to plastic components.False
The metal layer is thin, providing aesthetics without added weight.
When Should You Use Hot Stamping in Product Design?
Remember the thrill of unboxing a beautiful package? Hot stamping can bring that magic to your product design.
Use hot stamping in product design for luxury branding and packaging, where differentiation is crucial. It adds vivid colors and metallic finishes, enhancing visual appeal and uniqueness.
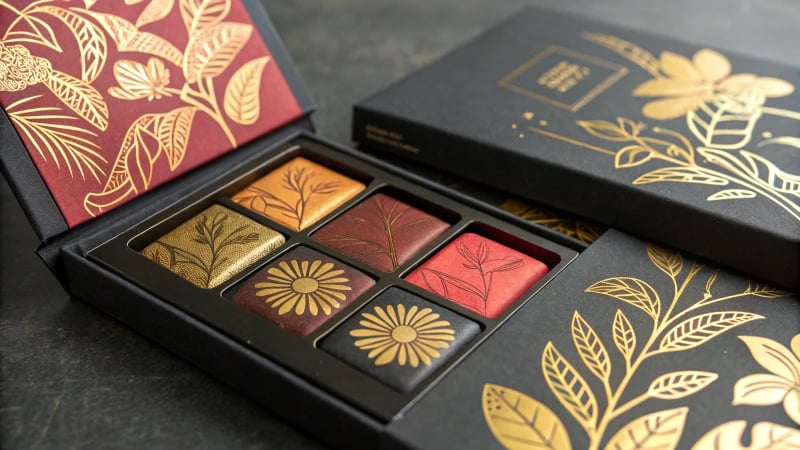
Exploring the Ideal Applications of Hot Stamping
Hot stamping is like the secret sauce that adds that irresistible appeal to a product. It’s something I’ve come to appreciate deeply in my design journey. Imagine you’re holding a beautifully packaged product, and it just screams elegance and luxury—more often than not, hot stamping is behind that magic.
-
Branding and Packaging: One of my favorite applications is in luxury packaging, especially for cosmetics. There’s something incredibly satisfying about seeing a brand logo6 come to life with hot stamping, transforming it into a high-end masterpiece that demands attention. It’s like giving the product a shiny new suit, instantly upping its allure.
-
Decorative Elements: For special occasions or gifts, hot stamping can turn ordinary boxes into keepsakes. I remember working on a project where we designed gift boxes with intricate foil patterns. The end product looked so exclusive, it was as if each box whispered stories of craftsmanship and care.
-
Unique Identification: In the fast-paced world of electronics, where standing out is everything, hot stamping can be a game-changer. It’s not just about aesthetics but also about adding unique identifiers that boost brand recognition and safeguard against counterfeits.
Comparing with Other Surface Treatments
Treatment | Principle | Best Used For |
---|---|---|
Painting | Uses paint to change color/texture | Wide color selection & special effects |
Electroplating | Deposits metal on surfaces | Metallic appearance & corrosion resistance |
Silk Screen | Transfers ink through a screen | High-precision pattern printing |
Pad Printing | Transfers ink using silicone head | Irregular surfaces with high detail |
Each method has its own charm and utility. Painting, for example, offers a rainbow of colors perfect for car interiors7—like choosing the right mood for a road trip playlist. On the flip side, electroplating adds a durable metallic touch, ideal for bathroom hardware.
Understanding these nuances helps me decide when hot stamping is the way to go, ensuring my designs stand out in the best possible way.
Technical Considerations
Before diving into hot stamping, there are a few important things to consider:
- Material Compatibility: Not all materials play well with heat and pressure, so it’s crucial to ensure compatibility to avoid any mishaps.
- Design Complexity: Sometimes, achieving those jaw-dropping designs requires special foils or techniques.
- Production Volume: For large-scale production, hot stamping offers efficiency and consistency, making it a favorite choice when crafting decorative elements across numerous items.
By weighing these factors carefully, designers like Jacky8 can use hot stamping to create products that not only look stunning but also deliver exceptional consumer experiences. Whether it’s adding that touch of elegance or ensuring brand recognition, hot stamping is an invaluable tool in my design arsenal.
Hot stamping is ideal for luxurious packaging.True
Hot stamping creates an elegant finish, perfect for high-end packaging.
Silk screen is better than hot stamping for metallic effects.False
Hot stamping excels in metallic finishes, unlike silk screen printing.
How Can Silk Screen Processing Improve Product Branding?
Ever wondered how a simple print can elevate your brand’s presence? Dive into the world of silk screen processing and discover its transformative power.
Silk screen processing enhances branding by providing vibrant, precise prints on products, boosting brand visibility and appeal with high-quality, durable visuals.
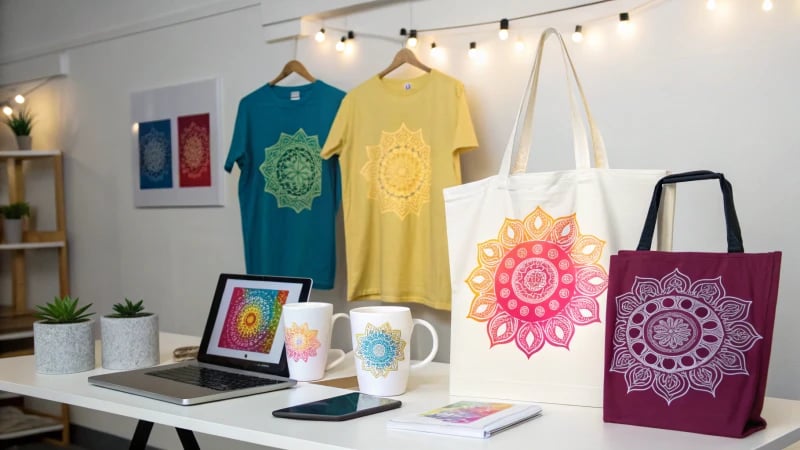
The Art of Precision and Versatility
You know that feeling when you stumble upon something that just clicks? That’s exactly what I experienced with silk screen processing. It’s not just about slapping a logo on a product; it’s about bringing your brand’s essence to life with precision and versatility. This technique uses a screen printing plate9 to transfer ink through a fine mesh onto surfaces, creating detailed images and text that speak volumes.
Application Across Industries
What really fascinates me is how silk screen processing isn’t confined to one industry. In the electronics world, for instance, I’ve seen how it creates those crisp, functional logos on device casings that not only look great but also withstand daily wear and tear. The fashion industry, on the other hand, uses it to craft intricate fabric designs that can turn heads and spark conversations.
Industry | Application Example |
---|---|
Electronics | Device casing logos |
Fashion | Detailed fabric designs |
Toys | Vibrant patterns on plastics |
Enhancing Brand Identity
Let’s talk about brand identity—something near and dear to my heart. Silk screen processing ensures logos and patterns remain consistent and high-quality across all products. By using multiple colors and gradients, it allows brands to stay true to their signature look. Imagine a toy company printing colorful characters on plastic toys; it’s these vivid images that capture kids’ imaginations and make parents remember the brand.
Durability Meets Aesthetic Appeal
Of course, visual appeal is crucial, but durability is what seals the deal for me. The ink in silk screen printing adheres strongly, making it resistant to wear and tear—perfect for products that face tough conditions. Think about outdoor equipment that needs to brave the elements. With silk screen processing, branding elements remain intact no matter what nature throws their way.
- Long-lasting: Withstands environmental factors
- Vibrant colors: Maintains visual appeal over time
Integrating with Other Techniques
But here’s where things get even more interesting: silk screen processing can be integrated with other treatments like painting10 or electroplating. It’s like combining your favorite ingredients to make a dish that’s both unique and memorable. These methods work together to create textures and finishes that elevate a product’s aesthetic and help it shine in a crowded market.
Whether it’s the bright chrome-like finish from electroplating or the rich color palette achieved through painting, these enhancements ensure that your brand stands out while still delivering quality and consistency.
Silk screen printing is used in the toy industry.True
The technique is used for vibrant patterns on plastic toys.
Silk screen processing lacks durability for outdoor products.False
It offers durability, withstanding environmental factors.
Why is Laser Processing Ideal for Customization?
Ever marveled at how a perfectly engraved design can transform a product? Laser processing is revolutionizing customization, bringing precision and flexibility to the forefront of manufacturing. Let’s delve into why it’s becoming the go-to for personalized designs.
Laser processing is perfect for customization due to its precision, speed, and versatility, enabling detailed designs on various materials to produce unique, high-quality products efficiently.
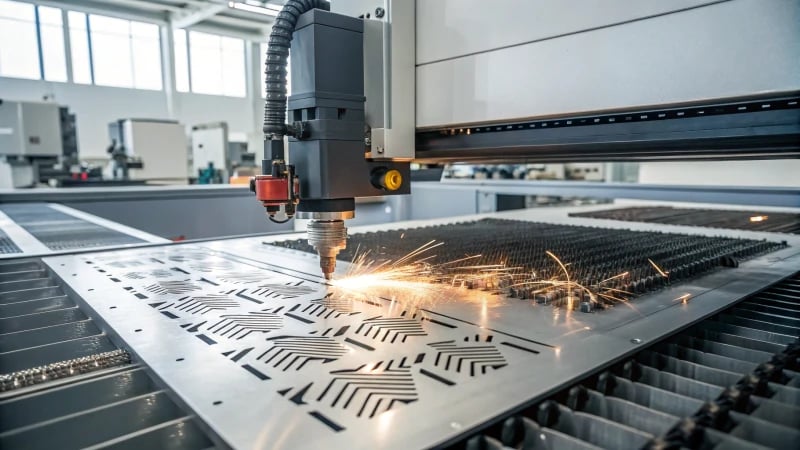
Precision and Accuracy
I remember the first time I witnessed laser processing in action—watching a laser beam carve out intricate designs with breathtaking precision felt almost like watching an artist at work. The ability to create such detailed patterns with minimal error is what makes laser processing indispensable for custom designs11. It’s reassuring to know that each piece will meet exact specifications, which not only reduces waste but also elevates the quality of the final product.
Versatility Across Materials
The versatility of laser processing is something that never ceases to amaze me. Whether it’s metal, plastic, or even wood, lasers adapt seamlessly without compromising the material’s properties. I once worked on a project that involved customizing both metallic and plastic components, and the ease with which laser processing handled these diverse materials was nothing short of impressive. This flexibility is crucial for industries like automotive and electronics, where materials can vary widely.
Speed and Efficiency
In my line of work, deadlines are tight, and there’s little room for error. Laser processing has been a game-changer in this regard. The rapid production speeds paired with consistent quality mean that I can meet those deadlines without sacrificing the integrity of the product. It’s this balance of speed and precision that gives laser processing an edge in competitive markets.
Permanent Markings and Textures
The permanence of laser engravings is another standout feature. I recall engraving an identification mark on a high-end electronic device—a task that required durability to withstand everyday wear and tear. The result was a crisp, long-lasting mark that could endure the test of time. Additionally, laser texturing offers a creative avenue to enhance product aesthetics with unique patterns that are as functional as they are decorative.
Treatment Type | Principle & Effects | Application Scenarios |
---|---|---|
Laser Processing | Uses laser beams for precise engraving | Anti-counterfeiting IDs on products |
Painting | Applies paint layers for color/texture | Car interior customization |
Electroplating | Deposits metal layers via electrolysis | Adds metallic look to products |
Comparison with Traditional Methods
Reflecting on traditional methods like screen printing12 or pad printing13, I’ve noticed that laser processing consistently outperforms them in detail and durability. Traditional techniques often struggle with complex surfaces or require additional steps, which lasers bypass altogether, making the customization process smoother and more efficient.
Environmental Impact
As someone who values sustainability, the environmental benefits of laser processing resonate deeply with me. It eliminates the need for inks or solvents, significantly reducing chemical waste. This eco-friendly approach aligns well with modern manufacturing’s shift towards greener processes, making laser processing not just a practical choice but also a responsible one.
Laser processing provides unmatched detail compared to screen printing.True
Laser processing achieves higher precision, making it superior for intricate designs.
Laser processing alters the inherent properties of materials.False
Laser processing customizes without changing material properties, unlike other methods.
What Are the Functional Advantages of Frosted Treatments?
You know that moment when you find the perfect solution that checks all the boxes? That’s what frosted treatments feel like—style, privacy, and efficiency all in one.
Frosted treatments provide privacy while allowing natural light, reduce glare, improve energy efficiency through insulation, and offer anti-slip surfaces, making them versatile for diverse uses.
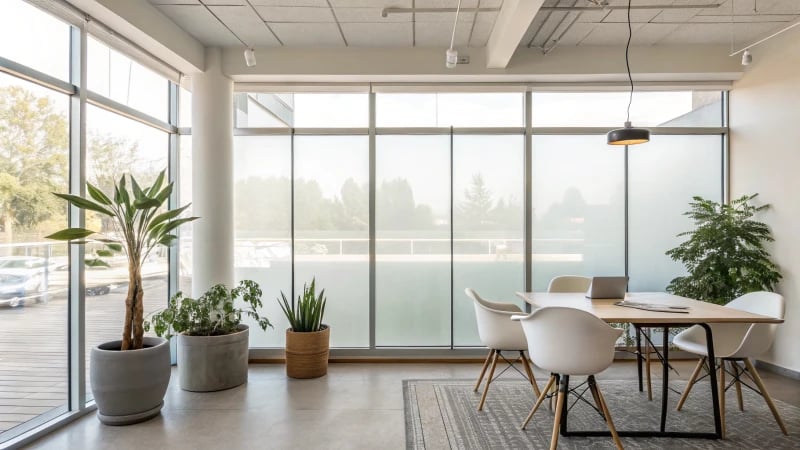
Enhancing Privacy and Aesthetic Appeal
I remember the first time I installed frosted window films in my office. It was like hitting two birds with one stone—privacy without sacrificing the beautiful, natural light streaming through the windows. The frosted effect is brilliant; it scatters light just enough to obscure visibility but still lets in the sunshine. This was especially useful in spaces where I wanted to keep prying eyes out while maintaining a bright and inviting atmosphere. Whether you’re looking at home or work, these films blend seamlessly with any interior design.
For those seeking both form and function, frosted window films14 provide a modern solution that complements any interior design.
Improving Energy Efficiency
One of the best parts about these treatments is their contribution to energy efficiency. When I had them installed, I noticed a significant change in how the space retained temperature. The films cut down on heat transfer through the windows, which meant I could keep my heating and cooling costs in check. For anyone like me who cares about energy usage and costs, these treatments are a no-brainer.
This makes them an excellent choice for eco-conscious individuals looking to optimize energy usage15 in their homes or offices.
Light Control and Anti-Glare Benefits
I’ve always had trouble with glare on my computer screen, which was frustrating during those sunny days when I had to squint to see my work. The frosted surface changed everything—it diffused incoming light perfectly, reducing glare without darkening the room. This improvement made my workspace much more comfortable and functional.
Feature | Benefit |
---|---|
Privacy Enhancement | Obscures visibility without blocking light |
Energy Efficiency | Reduces heat transfer, lowers costs |
Glare Reduction | Improves screen visibility |
Versatile Applications and Anti-Slip Features
Beyond just windows, these treatments are fantastic on other products too. I’ve used frosted textures on electronic device covers to provide anti-slip benefits while reducing fingerprints. It’s been a game-changer for handheld gadgets and tools where grip and cleanliness are key.
Explore more examples16 of how frosted finishes are applied across different industries.
Maintenance and Durability
Maintenance has always been a concern for me, but frosted films are surprisingly easy to keep clean. Their surfaces resist fingerprints and smudges, maintaining a pristine look with minimal effort. Plus, they hold up well against wear and tear, proving to be a durable solution for both home and office settings.
For more insights on maintaining frosted treatments, check this guide17.
In essence, frosted treatments provide an outstanding mix of privacy, aesthetic enhancement, and functional benefits like energy efficiency and glare reduction. They are truly a versatile addition to modern spaces.
Frosted treatments improve energy efficiency by reducing heat transfer.True
They reduce heat transfer, maintaining indoor temperatures.
Frosted window films block all natural light from entering a room.False
They scatter light, allowing it to pass through while obscuring visibility.
Conclusion
Explore common surface finishing techniques for injection molded parts, including painting, electroplating, hot stamping, and more, enhancing aesthetics and functionality across various industries.
-
Explore the advantages of electroplating for achieving metallic finishes and improving plastic part durability. ↩
-
Discover how silk screen processing achieves detailed and colorful patterns on plastic surfaces. ↩
-
Explore how electroplating strengthens plastics against wear and tear. ↩
-
Understand how painting treatments can change aesthetics and enhance durability. ↩
-
Stay updated on eco-friendly alternatives to traditional electroplating methods. ↩
-
Explores how hot stamping enhances brand appeal in cosmetic packaging with luxurious finishes. ↩
-
Provides insights into how painting treatments offer diverse color options for automotive design. ↩
-
Guides designers on effectively using hot stamping for enhanced product aesthetics and functionality. ↩
-
Explore how screen printing plates create detailed designs crucial for high-quality branding. ↩
-
Discover how combining techniques enhances product aesthetics and branding impact. ↩
-
Discover how laser technology maintains superior precision and accuracy in manufacturing processes. ↩
-
Understand why screen printing may fall short compared to laser processing for customization needs. ↩
-
Explore the differences between pad printing and laser processing to see which suits your customization needs better. ↩
-
Explore how frosted films enhance privacy while maintaining style. ↩
-
Learn how frosted films can contribute to reducing energy costs. ↩
-
Discover various industrial uses of frosted finishes beyond windows. ↩
-
Find easy maintenance tips to keep frosted films clean and durable. ↩