I once believed injection molding was only about precision and speed. But I learned differently. Cooling times truly influence the process. They matter a lot.
Extended cooling periods during injection molding often cause problems. These issues include inefficiencies, increased expenses and defects such as warping. Mold dimensions might also become inaccurate, ultimately impacting its longevity.
I recall a period when longer cooling times really reduced our production speed. We used to produce five items every minute. It fell to three. This slower pace strained our finances with higher energy and equipment expenses. Quality decreased too. Parts struggled to fit properly because of shrinkage problems. Surface flaws became a common issue. Our molds, over time, also started to wear out from the extended heat. I needed to understand these challenges. I looked for ways to improve cooling times. Protecting both quality and our budget became essential.
Long cooling time reduces injection molding output.True
Extended cooling periods decrease the number of products produced per unit time.
Prolonged cooling improves mold life by reducing wear.False
Long cooling times increase thermal stress, leading to mold wear and reduced lifespan.
How Do Extended Cooling Times Affect Productivity?
Ever wonder why production often slows when cooling takes longer? I’ve experienced that too, just watching the clock and waiting. This situation really affects everything.
When cooling times are long, production decreases. Costs go up and quality suffers. The entire manufacturing process takes more time. Fewer products get created every hour. Machines wear out faster and finished items might have defects.
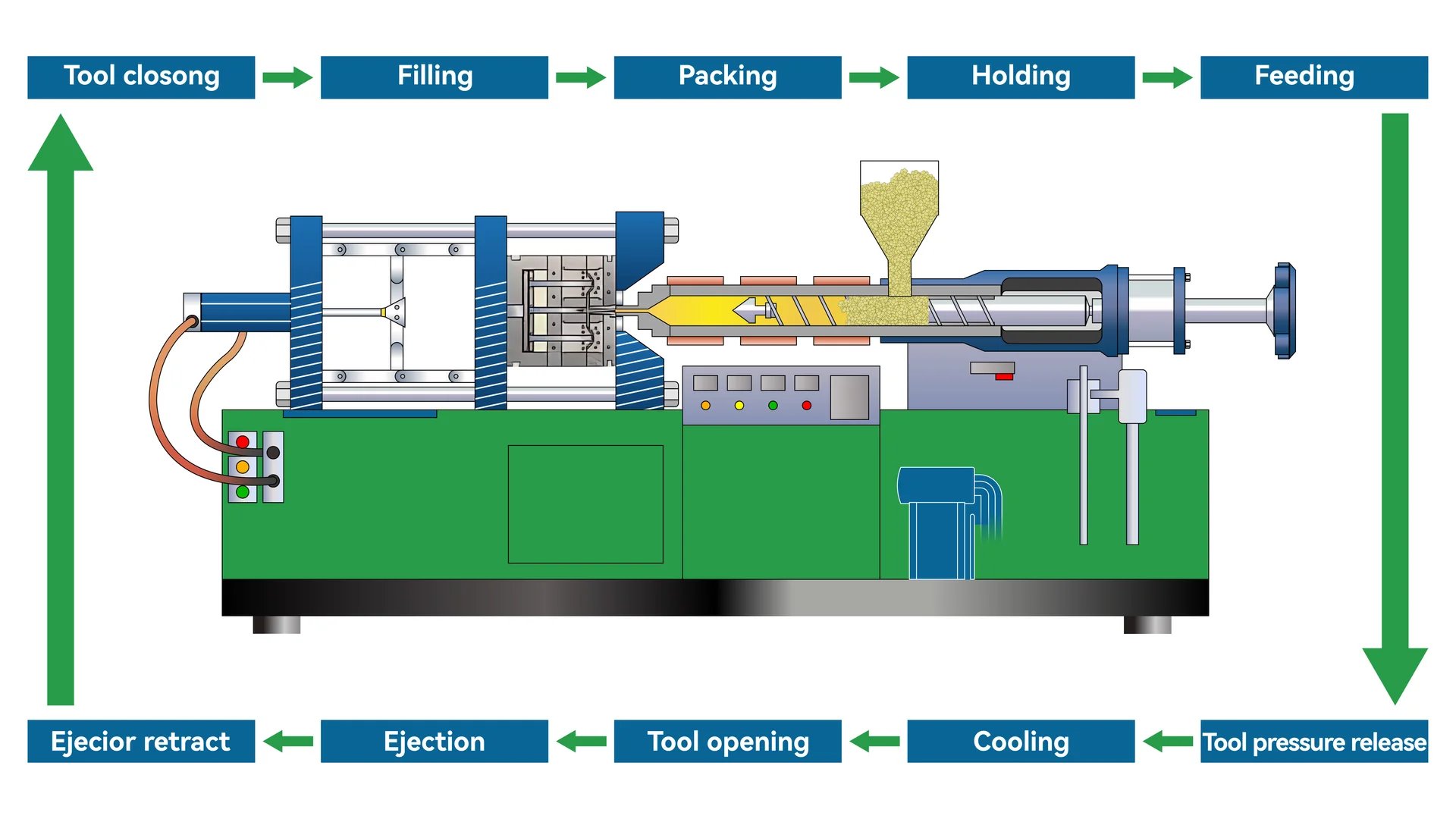
Impact on Production Output
The cooling phase is key in the injection molding cycle1, which includes injection, holding, cooling, and demolding times. I remember a project aiming for a cycle time of five units per minute. Extended cooling reduced this to just three units. Our efficiency dropped by nearly half.
Cost Implications
Longer cooling means machines stay busy longer. This increases costs like energy bills2 and labor hours. Each product costs more, as fixed expenses are spread over fewer units. I once calculated these costs. The results surprised me; our margins became tight.
Product Quality Concerns
Dimensional Accuracy Issues
Parts that cool too long and shrink badly feel like puzzle pieces that won’t click. This is bad for precision parts needing exact measurements.
Distortion and Warpage
Uneven cooling can twist products, especially large or thin ones. It’s like baking a cake that doesn’t rise evenly. It’s not just about looks; functionality suffers too.
Surface Defects
Surface defects from long cooling make products look bad. Cold marks3 and flow lines occur, which is unacceptable for high-end items.
Effects on Mold Life
Mold Wear and Tear
Long cooling times stress molds, leading to cracks. These small cracks can grow over time, reducing mold life.
Corrosion Risks
Moisture and metal do not mix well. Impurities in cooling fluids can cause corrosion, blocking cooling channels—a silent threat that might disrupt work if not handled.
Long cooling times reduce injection molding productivity.True
Extended cooling periods decrease the number of products made per minute.
Prolonged cooling improves the surface quality of products.False
Long cooling leads to defects like cold marks, reducing surface quality.
How Do Long Cooling Periods Impact Product Quality?
Have you ever thought about how a little extra cooling might affect your product’s quality? Extra cooling really changes things.
Long cooling times in manufacturing, such as injection molding, disrupt product quality. These periods lead to size errors and bending. Surface defects arise. Mold wear increases. Uneven cooling results in these problems. It also causes thermal stress. Product strength and appearance suffer.
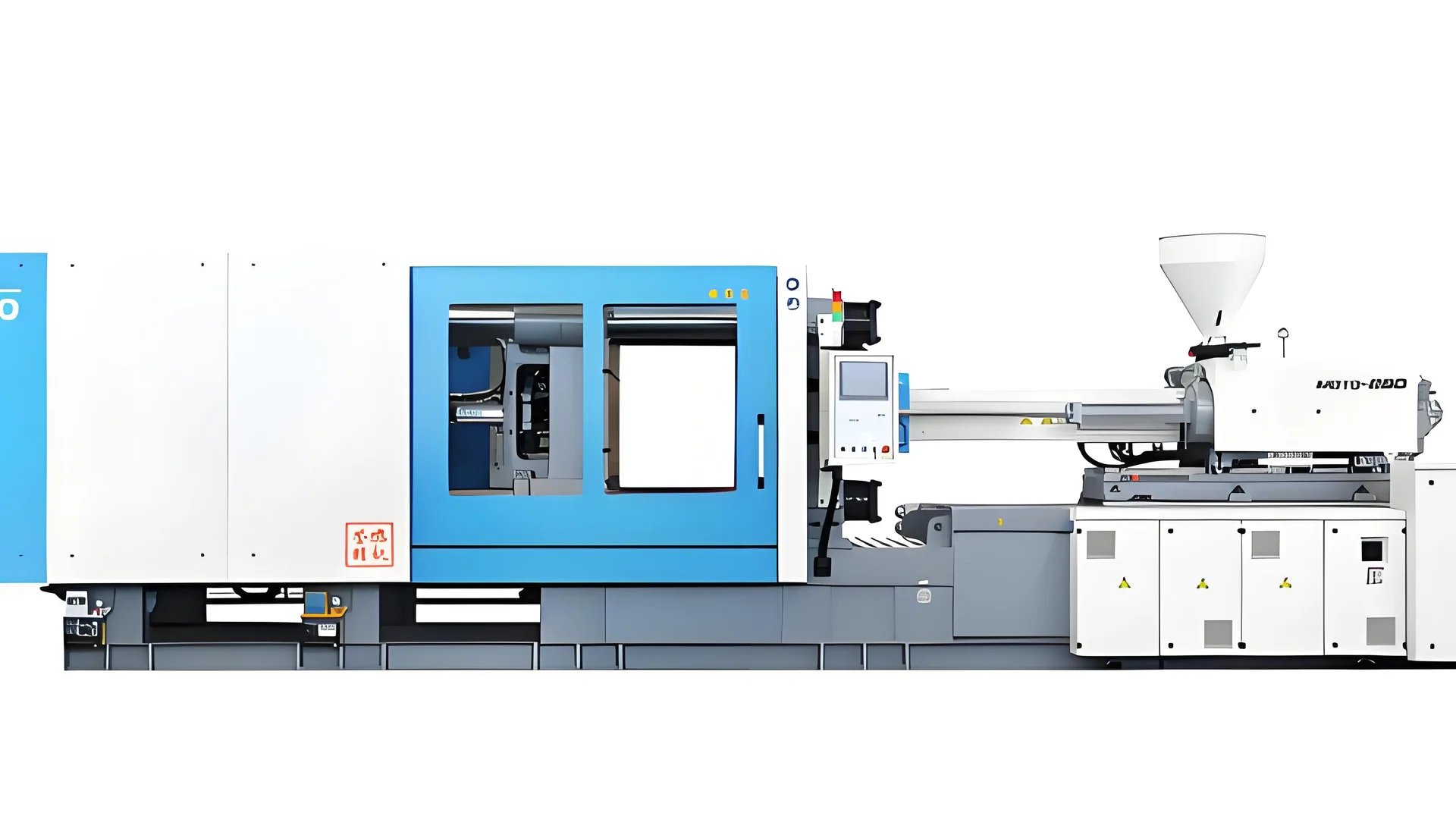
Dimensional Accuracy and Structural Integrity
Long cooling times change sizes. Products shrink more than needed, leading to significant dimensional accuracy problems4. This makes assembly hard as parts must fit perfectly. Warping happens when cooling is uneven, causing different parts to cool at different rates. This results in stress, leading to distortion. I have seen big shapes become puzzling when they should have been simple.
Surface Quality Concerns
Surface quality suffers with longer cooling periods. Defects like cold marks and flow marks appear due to significant temperature differences between the cooling medium and mold cavity surfaces. These are more than just looks; surface defects5 form with big temperature differences, reducing the aesthetic quality of products. Industries like electronics need a perfect finish, making these flaws serious problems for them.
Impact on Productivity and Costs
Long cooling slows productivity by extending the overall production cycle—meaning fewer products are manufactured in the same timeframe. I have felt the impact on production cycles; imagine expecting five units per minute but ending up with just three. Fewer products mean rising costs as equipment runs longer, increasing energy use. Fixed costs like mold expenses spread over fewer products, raising the cost per item significantly.
Effects on Mold Life
Molds wear out faster with long cooling times due to thermal stress creating micro-cracks from repeated expansion and contraction cycles. These cracks grow bigger over time, shortening the mold’s lifespan6. Corrosion becomes a risk if impurities enter the cooling system, leading to blockages and leaks that complicate maintenance and mold usage.
Long cooling time reduces injection molding output.True
Extended cooling prolongs the cycle, lowering production from 5 to 3 units/min.
Prolonged cooling enhances mold life by reducing stress.False
Long cooling increases thermal stress, causing micro-cracks and mold wear.
Why Does Prolonged Cooling Lead to Mold Wear and Corrosion?
Long cooling in injection molding often leads to hidden trouble like mold wear and corrosion. These problems might go unnoticed for a while. However, they steadily worsen. Why does this happen?
Long cooling in injection molding wears and corrodes molds. Molds face thermal stress and impurities in the cooling fluid. Repeated heat changes cause tiny cracks. These cracks grow over time. Corrosion happens more if the cooling fluid is harsh.
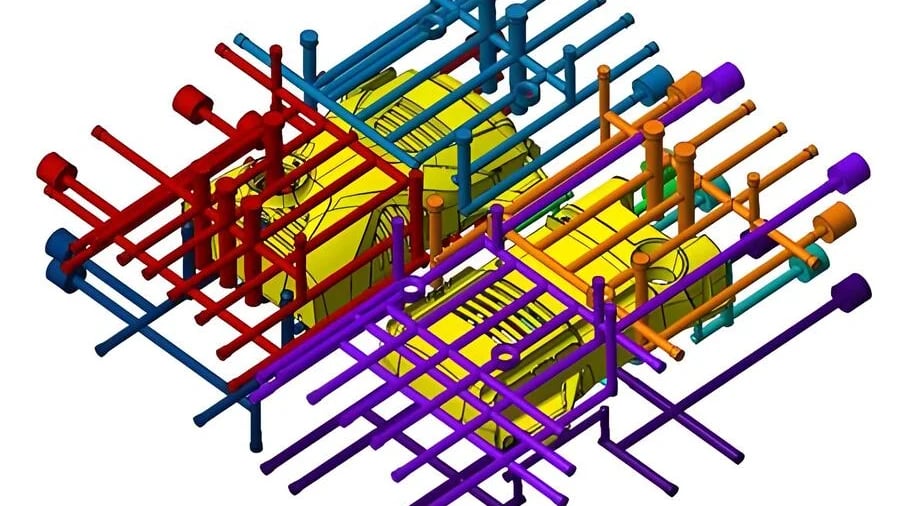
Productivity Impact
Cooling time is very important in injection molding. I didn’t realize this when I started. Imagine a machine creating five items a minute. Everything is fine. If cooling takes longer, output drops to three items. Productivity suffers greatly7. I felt this deeply when our numbers fell sharply. Fewer products meant costs really increased. Machines working longer meant more energy use. Parts wore out faster. Each item cost much more because we needed extra labor and had more overhead.
Quality Issues
Now let’s focus on quality. Have you ever tried to build something that just doesn’t fit? It’s like a puzzle with pieces that got smaller. Long cooling times cause this by ruining precise dimensions. Overcooling makes assembly really hard, especially for parts requiring precision assembly8. Nice designs come out bent or twisted from uneven cooling, which is particularly problematic for large parts.
Surface problems are also a big issue. I once got electronic shells with lots of marks on them; it was like scars on perfect surfaces. This happens from too much temperature difference between the mold and cooling medium, resulting in visible marks.
Mold Damage and Corrosion
Even molds suffer. We think molds are strong, but long cooling times wear them down. Tiny cracks form as molds expand and shrink due to thermal cycling stress, leading to bad wear over time as these cracks grow larger.
Corrosion is another danger; impure cooling media harms the molds like salt in a wound, increasing the risk of blocks or leaks in cooling pipes and putting efficiency at risk.
It’s really vital to know these problems in injection molding. Understanding them helps avoid trouble later on by adopting better practices and mitigating potential issues through resources like mold maintenance9, which has probably been helpful to me.
Long cooling time reduces product output.True
Extended cooling time decreases production rate from 5 to 3 units/min.
Prolonged cooling enhances mold life.False
Long cooling increases thermal stress, leading to mold wear and corrosion.
How Can You Optimize Cooling Times in Injection Molding?
Have you ever noticed how slow cooling times in injection molding delay everything? I know how annoying it is! Let’s look at ways that have really helped me.
Improving cooling times in injection molding requires changing mold design. Experts use new cooling methods and special software. These steps probably reduce cycle times. They really help improve dimensional accuracy. They also cut production costs.
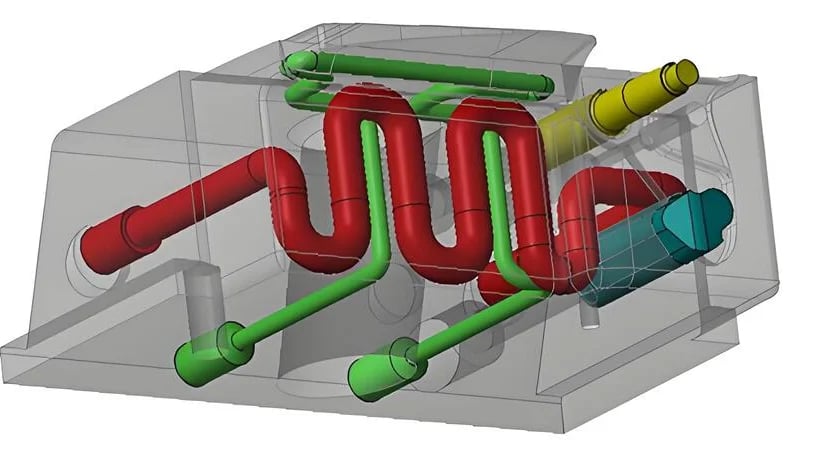
Optimizing Mold Design
When I started with injection molding, I saw that mold design was like the key to success. It surprised me how conformal cooling channels10, shaped around the mold, removed heat evenly. I remember watching them almost magically remove hotspots that cause warping. This amazing change with conformal cooling cut down cycle times a lot.
Advanced Cooling Techniques
As I explored injection molding, I found some advanced cooling ways that seemed very futuristic. Methods like using high-pressure air or liquid nitrogen cool the parts fast without ugly surface marks. When these advanced cooling techniques11 entered my routine, my productivity soared and cycle times shrunk.
Process Optimization Software
Technology really saved me. Using process optimization software12 gave me real-time control over cooling steps. It felt like having a digital helper that fixed things immediately to keep up quality and avoid delays. This software now helps me balance speed and precision perfectly.
Material Selection and Management
Picking the right materials is important. I learned that materials with low specific heat or those that cool fast help a lot. Managing these materials carefully also matters. Watching for contamination or moisture prevents issues during cooling. Finding the right materials13 can change your processes.
Monitoring and Maintenance Practices
Regular checks on cooling systems are crucial. It’s like taking your car for a regular service. This care stops inefficiencies from wear or corrosion. I plan preventive maintenance to keep cooling channels clear and running well, extending mold life and keeping production good. Good maintenance practices14 really help in holding high standards over time.
These methods truly changed how I approach injection molding. They improve efficiency and product quality. If you face similar problems, try these strategies—they might become your best friend.
Long cooling time reduces production output.True
Extended cooling time decreases the number of products produced per minute.
Prolonged cooling improves product dimensional accuracy.False
Excessive cooling can lead to shrinkage, reducing dimensional accuracy.
Conclusion
Long cooling times in injection molding reduce productivity, increase costs, and compromise product quality through dimensional inaccuracies, warping, and surface defects while also accelerating mold wear and corrosion risks.
-
Explore a detailed overview of the injection molding process. ↩
-
Understand how depreciation influences overall production expenses. ↩
-
Learn about factors leading to cold marks on product surfaces. ↩
-
Explore how cooling time affects precision in manufactured products. ↩
-
Understand why extended cooling causes visual defects on surfaces. ↩
-
Learn how extended cooling impacts mold durability. ↩
-
Learn how cooling time affects overall production efficiency. ↩
-
Discover how dimensional changes impact assembly processes. ↩
-
Find best practices for prolonging mold life and efficiency. ↩
-
Discover how conformal cooling enhances heat removal efficiency. ↩
-
Learn about innovative cooling techniques that cut cycle times. ↩
-
Explore software solutions for dynamic cooling control. ↩
-
Find out how materials affect cooling time efficiency. ↩
-
Understand how maintenance extends mold life and quality. ↩