As a manufacturer, I know how vital it is to ensure that our injection molded products are durable and free from defects. Let’s dive into how we can achieve this together.
To prevent cracks and breakage in injection molded products, focus on selecting appropriate materials, designing effective molds, optimizing the injection molding process, and implementing post-processing techniques like annealing and humidity adjustments.
While these initial steps provide a solid framework for preventing defects, exploring each aspect in depth can significantly enhance product durability. Join me as we delve into these strategies to see how they can be effectively implemented in your production processes.
Material selection prevents cracks in injection molded products.True
Choosing materials with good toughness and impact resistance reduces cracking.
What Role Does Material Selection Play in Preventing Cracks?
Material selection is crucial in ensuring the strength and durability of molded products.
Choosing the right material is vital to prevent cracks in injection molded products. Select plastic raw materials with excellent toughness, strength, and impact resistance that meet quality standards. Ensure proper drying to remove moisture, preventing defects like bubbles and cracks.
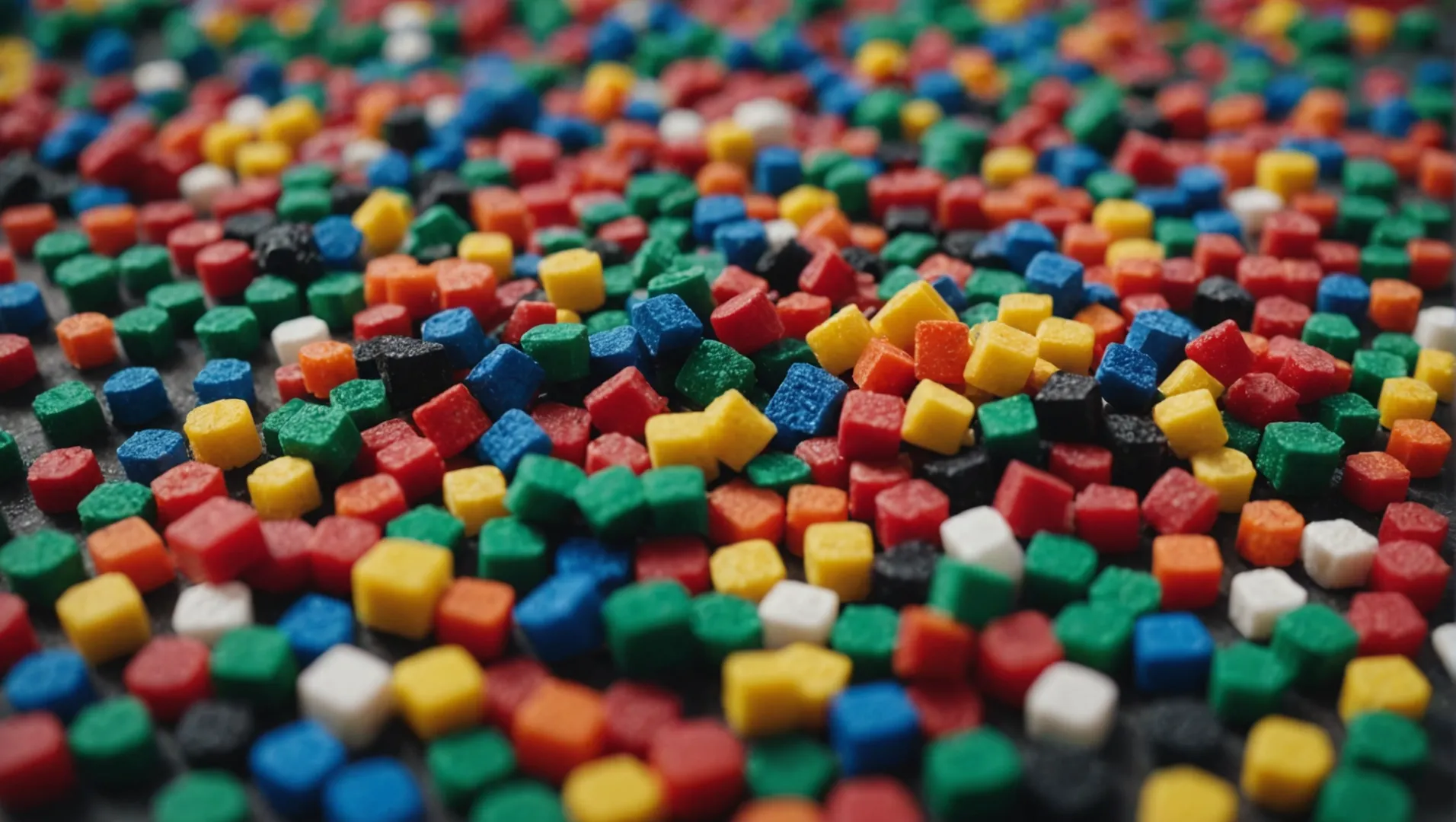
The Importance of Material Characteristics
In the world of injection molding, selecting the appropriate material can make the difference between a robust product and one prone to cracking. The performance characteristics of different plastics are vital in determining their suitability for specific applications. For instance, ABS materials1 offer a balance of strength and toughness, making them ideal for general applications. On the other hand, PC materials2 provide superior impact resistance, crucial for products exposed to dynamic stresses.
Ensuring Material Quality
The quality of raw materials cannot be overstated. Impurities or degradation products within the plastic can lead to structural weaknesses and eventual cracking. Implementing a rigorous inspection process for raw materials helps in maintaining quality. This includes screening for impurities and ensuring consistent material properties across batches. Such practices guarantee that only the highest quality materials are used in production.
Drying: A Critical Step
Moisture within plastic raw materials is a common issue that can result in surface defects like bubbles, which can lead to cracks. The drying process3 plays a pivotal role here. Each plastic type requires specific drying conditions—both temperature and time must be carefully controlled. For instance, nylon, known for its water absorption properties, needs thorough drying to ensure optimal performance.
Material Type | Typical Drying Temperature (°C) | Typical Drying Time (hours) |
---|---|---|
ABS | 80-85 | 2-4 |
PC | 120-130 | 2-3 |
Nylon | 70-80 | 4-5 |
Customizing Material Selection for Application Needs
Understanding the end-use requirements of the product guides the choice of material. Products subjected to mechanical stress or temperature variations need plastics with enhanced characteristics. By aligning material properties with product demands, manufacturers can significantly reduce the risk of cracks.
To sum up, selecting the right material involves understanding both the intrinsic properties of plastics and the specific demands of the product’s application environment.
ABS materials are ideal for high-impact applications.False
PC materials, not ABS, are known for superior impact resistance.
Nylon requires thorough drying to prevent cracks.True
Nylon's water absorption properties necessitate careful drying to avoid defects.
How Does Mold Design Influence Product Durability?
Mold design is a pivotal factor that directly affects the durability of injection molded products.
Mold design influences product durability through structural integrity, cooling efficiency, and stress distribution, ensuring high-quality, long-lasting products.
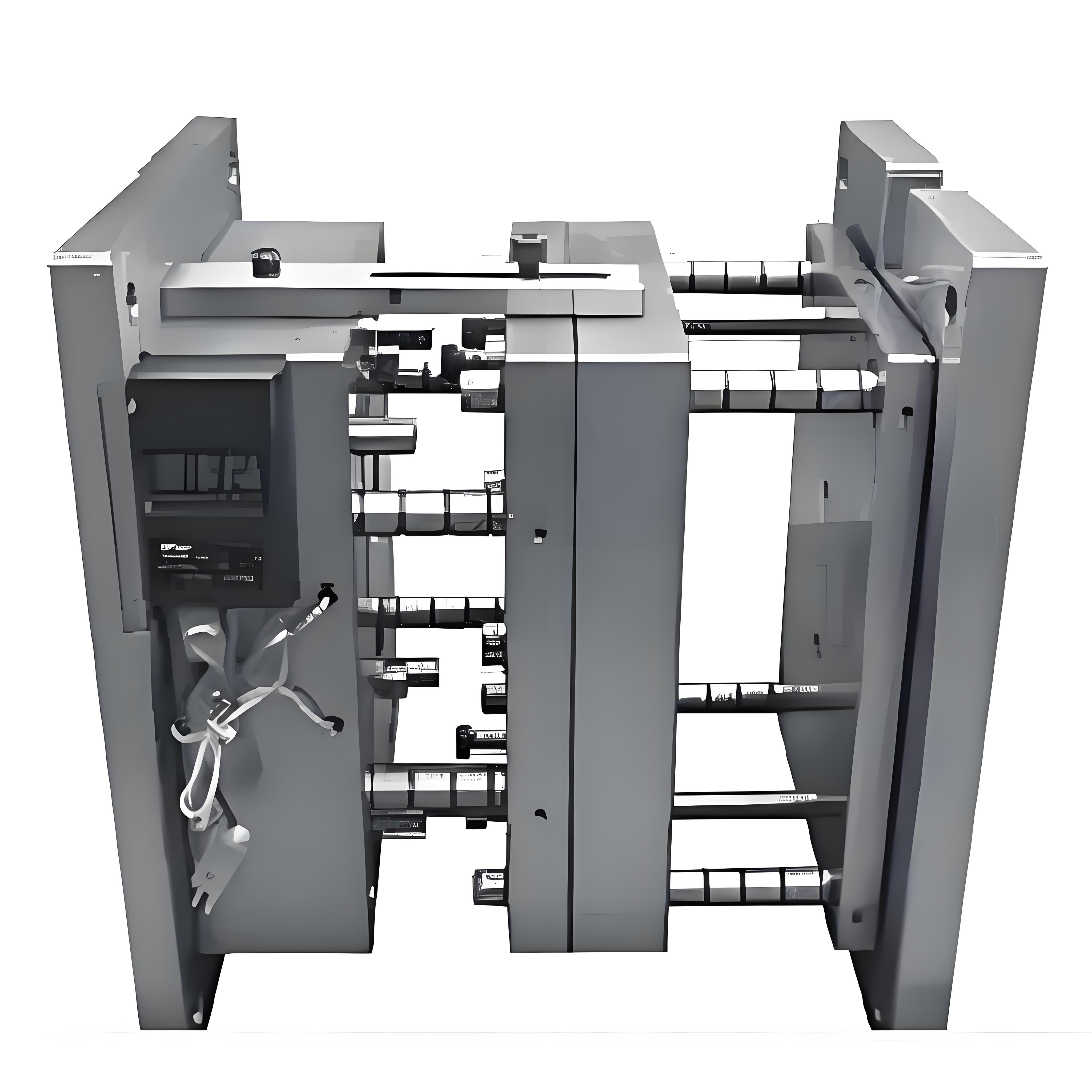
Structural Integrity in Mold Design
The structure of a mold dictates how stress is distributed across the product. A well-designed mold avoids stress concentrations by incorporating rounded corners and avoiding thin walls. For example, choosing materials4 like PC for their high impact resistance can complement such designs, enhancing product durability.
-
Rounded Corners: Sharp edges can lead to stress fractures. Incorporating fillets or radii can disperse stress evenly.
-
Wall Thickness: Uniform wall thickness prevents weak spots where stress could accumulate, thus reducing the risk of cracks.
Cooling Efficiency
A mold’s cooling system plays a crucial role in maintaining product integrity by controlling shrinkage and preventing defects.
-
Cooling Channel Design: Strategic placement of cooling channels ensures uniform cooling. Considerations include the number of channels and their proximity to critical areas.
-
Cooling Rate Control: By optimizing the cooling rate, manufacturers can avoid internal stresses. Too fast cooling can cause warping, while too slow may affect cycle times.
Stress Distribution and Reduction
Stress distribution within a molded product is paramount to its longevity. Mold design can minimize potential failure points.
-
Parting Line Placement: Proper placement of parting lines helps avoid defects such as flash, which can weaken structural integrity.
-
Ejection System Design: A well-designed ejection system ensures that products are removed from molds without excessive force, reducing the chance of cracking or deforming.
In conclusion, focusing on mold design elements such as structural integrity, efficient cooling systems, and effective stress distribution is crucial for producing durable injection molded products. By paying attention to these factors, manufacturers can significantly improve the quality and lifespan of their products.
Rounded corners in mold design prevent stress fractures.True
Rounded corners help distribute stress evenly, avoiding fractures.
Uniform wall thickness leads to weaker product durability.False
Uniform wall thickness prevents weak spots, enhancing durability.
Why Is Process Optimization Critical in Injection Molding?
Optimizing the injection molding process is crucial to ensure product quality and efficiency.
Process optimization in injection molding is vital as it ensures consistency, reduces defects, and improves production efficiency by fine-tuning parameters like temperature, pressure, and speed.

The Importance of Temperature Control
Temperature plays a pivotal role in the injection molding process. Maintaining the right temperature ensures that the plastic material flows adequately into the mold, preventing issues such as insufficient filling or material degradation. Too high a temperature can lead to material degradation5, while too low a temperature may cause incomplete filling.
Managing Pressure and Speed
Pressure and speed must be meticulously controlled during the injection molding process. High pressure can lead to internal stress within the product, while low pressure may result in defects like shrinkage holes. Similarly, the speed of injection affects the distribution of material within the mold. Rapid injection can lead to defects such as flash and bubbles, whereas slow injection may reduce production efficiency.
Holding Time Considerations
Controlling holding time is essential to avoid cracks and breakages. Excessive holding time may induce stress, while insufficient time can lead to depressions in the product. Adjusting holding time according to product size and material type ensures optimal performance and durability.
Parameter | Optimal Control Method |
---|---|
Temperature | Balance between flow and degradation |
Pressure | Avoid high internal stress |
Speed | Prevent defects, maintain efficiency |
Holding Time | Tailor to product size and material |
Cooling and Demolding
The cooling system’s design significantly impacts product quality. A well-designed cooling system prevents local overheating or overcooling, reducing stress and deformation. Proper control of demolding temperature is also crucial. If too high, it can cause deformation; if too low, it might damage the mold or make demolding difficult.
Continuous Improvement Through Optimization
By continuously optimizing these parameters, manufacturers can achieve higher quality standards and reduce waste. This iterative approach leads to improvements in production efficiency6 and cost-effectiveness, ultimately resulting in better product quality and reliability.
High pressure in molding causes internal stress.True
Excessive pressure can induce stress, leading to defects.
Cooling systems have no impact on product quality.False
Proper cooling prevents deformation and ensures quality.
What Are Effective Post-Processing Techniques to Enhance Product Quality?
Enhancing product quality post-production is crucial for ensuring longevity and customer satisfaction.
Effective post-processing techniques, such as annealing and humidity adjustment, enhance product quality by reducing internal stress and improving dimensional stability.
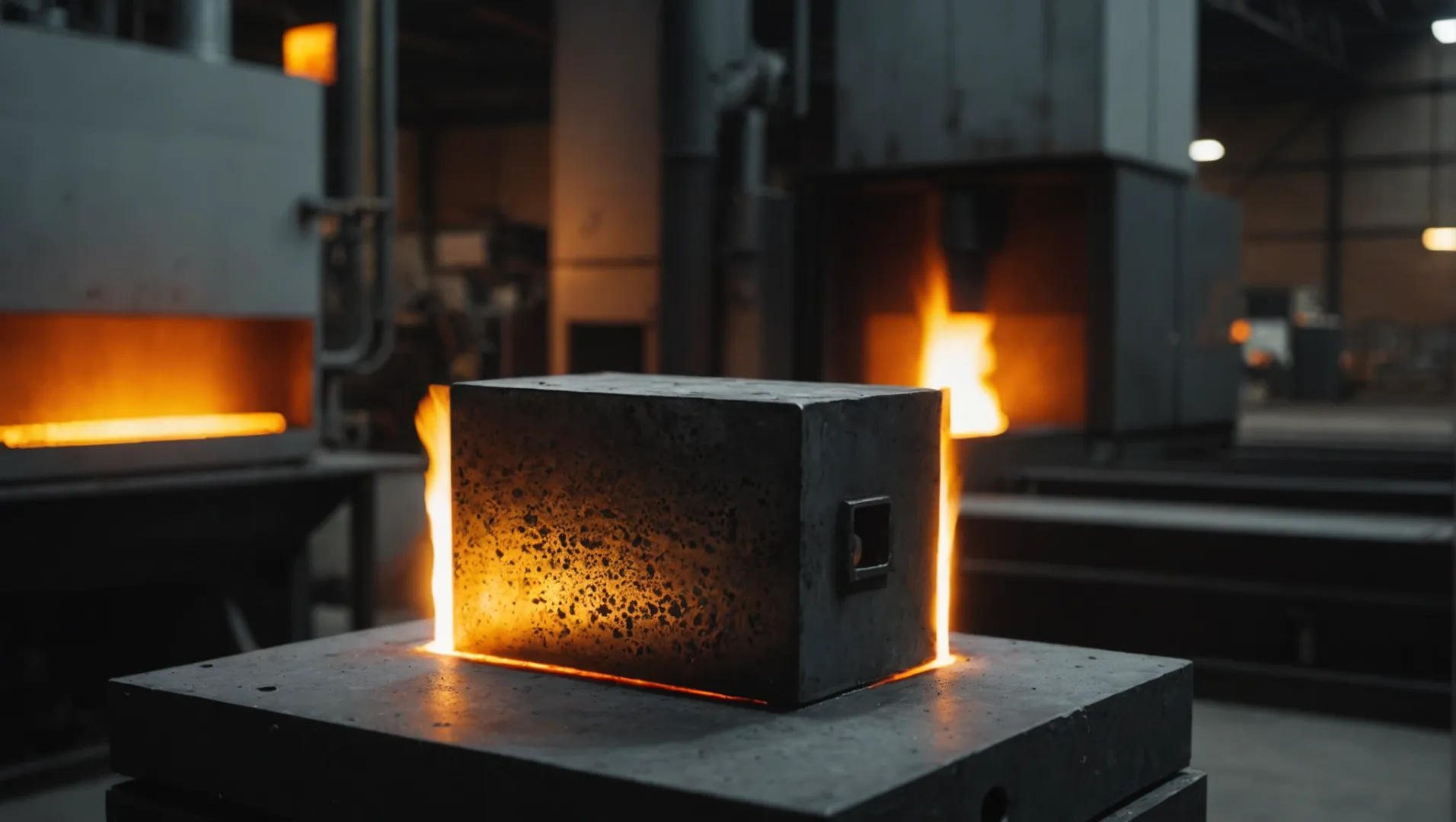
Annealing for Stress Reduction
Annealing is a critical post-processing technique used to eliminate internal stresses in injection molded products. Internal stresses can lead to cracks and breakage over time, compromising the product’s structural integrity. By carefully controlling the annealing temperature and time7, manufacturers can relieve these stresses without degrading the material.
How Annealing Works:
- Temperature Control: The product is heated to a specific temperature, which is below its melting point but sufficient to allow molecular rearrangement.
- Time Management: Maintaining the product at this temperature for a set duration allows the stress to dissipate, thereby enhancing toughness.
- Cooling Process: Gradually cooling the product prevents the introduction of new stresses.
For instance, polycarbonate products are often annealed to improve their impact resistance, making them ideal for high-stress applications.
Humidity Adjustment for Dimensional Stability
Certain plastics, such as nylon, are hygroscopic, meaning they absorb moisture from the environment. This can lead to dimensional changes that affect product performance. Humidity adjustment treatments involve conditioning the product in a controlled environment to achieve optimal moisture content.
Process Steps:
- Water Soaking: The product is submerged in water at a specified temperature to allow moisture absorption.
- Controlled Environment: Maintaining the correct temperature and time ensures uniform moisture distribution.
- Benefits: Enhances the material’s flexibility and reduces brittleness.
A nylon component, for example, may be soaked at 60°C for several hours to achieve balanced moisture content, which enhances its toughness.
Combining Techniques for Optimal Results
Utilizing both annealing and humidity adjustment in tandem can produce superior outcomes for certain materials. By initially relieving stress through annealing and then stabilizing dimensions with humidity control, products achieve a higher quality standard and better performance.
Technique | Primary Benefit | Suitable Materials |
---|---|---|
Annealing | Stress reduction | Polycarbonate, ABS |
Humidity Adjustment | Dimensional stability | Nylon, PET |
By integrating these methods into your production process, you can significantly enhance product quality, reduce defects, and ensure customer satisfaction. It’s important to tailor these techniques to the specific requirements of your materials and products for best results. Learn more about tailored processing techniques8.
Annealing reduces internal stress in plastics.True
Annealing relieves internal stresses, preventing cracks and breakage.
Humidity adjustment increases brittleness in nylon.False
Humidity adjustment enhances flexibility, reducing brittleness in nylon.
Conclusion
By integrating these strategies, we can significantly reduce defects and ensure higher product quality. Let’s start implementing these best practices today to optimize our production process!
-
Learn about ABS’s balance of strength and toughness.: High rigidity, good weldability, and insulating properties · Good impact resistance, even at low temperatures · Good abrasion and strain resistance · High … ↩
-
Discover why PC is ideal for high-impact applications.: Polycarbonate is a tough, transparent plastic material with outstanding strength, stiffness, and impact resistance. Polycarbonate’s optical clarity makes it … ↩
-
Explore why proper drying prevents surface defects and cracks.: Almost every other polymer exhibits some level of polarity and therefore can absorb a certain amount of moisture from the atmosphere. ↩
-
PC materials offer excellent impact resistance for durable products.: Polycarbonate material is strong, tough, stiff, transparent with outstanding impact resistance. Research Polycarbonate properties and uses at Curbell … ↩
-
Explore how temperature affects plastic material properties during molding.: What is clear is that increasing melt temperature, residence time, and moisture content increases the risk of material degradation. ↩
-
Discover strategies for enhancing efficiency in injection molding processes.: 1. Streamline Processes and Workflow · 2. Optimize Machine Utilization · 3. Invest in Advanced Technology · 4. Implement Effective Production … ↩
-
Discover optimal temperatures and times for effective annealing.: Well it’s simply a process that involves heating a specific type of plastic below its glass transition temperature in order to ease all the internal pressures … ↩
-
Explore advanced strategies tailored to specific materials.: This can include processes like trimming, surface finishing, painting, and assembly. Why is post-processing necessary for plastic injection molding? ↩