Picking the correct material for mold-making seems difficult, but it’s an important step for your project’s success. Let’s look at the choices together!
The best materials for molds include carbon, alloy, high-speed steel, cast iron, non-ferrous metals, hard alloys, and composites. Suitable material choices depend on the mold’s complexity and load requirements.
I remember my first mold project. I felt overwhelmed by the choices! Different materials offer distinct qualities. These qualities help or hurt your design. For example, carbon tool steel suits simpler molds. However, it gives trouble with precision. Aluminum is another option. It feels light and cools well. Yet, it lacks strength. Learning about these materials changed my approach. My creativity flourished. The process became fun. It became rewarding.
Steel is a top choice for mold-making materials.True
Steel, including carbon and alloy types, is favored for its strength and durability in mold applications.
Non-ferrous metals are unsuitable for molds.False
Non-ferrous metals can be effective for specific mold applications, contrary to this claim.
- 1. What Are the Properties of Carbon Tool Steels for Mold Making?
- 2. How Do Alloying Elements Enhance Mold Steel Performance?
- 3. What Role Do Non-Ferrous Metals Play in Mold Fabrication?
- 4. Why Are Hard Alloys So Important for High-Precision Molds?
- 5. How Can Composite Materials Improve Mold Efficiency?
- 6. What Factors Should You Consider When Choosing Mold Materials?
- 7. Conclusion
What Are the Properties of Carbon Tool Steels for Mold Making?
I work as a designer in the world of mold crafting. I really value the special qualities of carbon tool steels. These materials are more than just steel. They serve as the foundation for my projects. Let’s discuss their interesting features!
Carbon tool steels, essential for mold making, include high carbon, low alloy, high alloy, and hot working die steels. Each type offers unique properties suitable for specific applications, highlighting their importance and limitations in manufacturing processes.
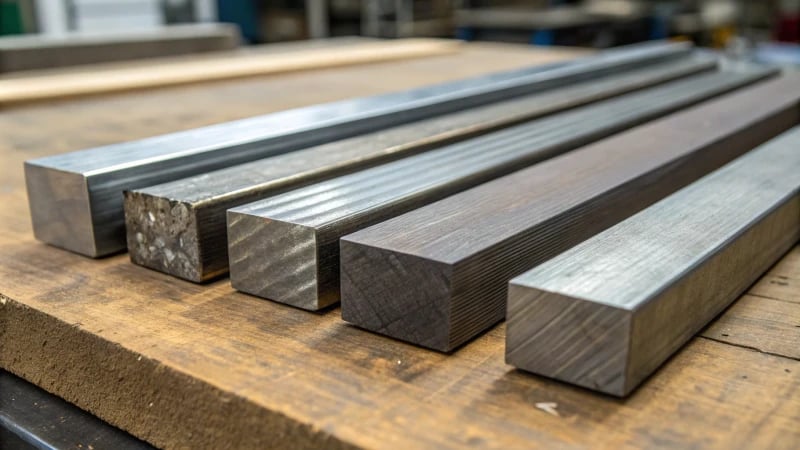
Understanding Carbon Tool Steels for Mold Making
Carbon tool steels are important for mold creation due to their unique properties that cater to various applications. They fall into categories like high carbon, low alloy, high alloy, and hot working die steels. Each has specific uses and limits in manufacturing, which significantly impacts a project’s success.
Low carbon steels remind me of gentle giants; they have great ductility but lower hardness. High carbon steels, on the other hand, resemble tough warriors: hard and resilient but less flexible. It’s a delicate balance reflecting design challenges.
Types of Carbon Tool Steels
-
High Carbon Tool Steels
- Examples: T7A – T12A
- Characteristics: Very hard after quenching; ideal for simple molds without heavy loads.
- Applications: I use them often for small stamping molds, ideal for thin metal sheets.
- Limitations: Like me after a tiring day, they can be tricky with low hardenability and high quenching deformation.
-
Low Alloy Tool Steels
- Examples: CrWMn, 9Mn2V
- Characteristics: Good hardenability and wear resistance because of alloying elements.
- Applications: Perfect for cold stamping and extrusion molds due to stable dimensions.
-
High Alloy Tool Steels (High-Speed Steel)
- Examples: W18Cr4V, W6Mo5Cr4V2
- Characteristics: High hardness and wear resistance; great for complex molds and heavy impacts.
- Applications: I choose these when working with plastics containing hard fillers like glass fiber.
-
Hot Working Die Steel
- Examples: 5CrNiMo, 5CrMnMo
- Characteristics: Excellent performance at high temperatures; resisting thermal fatigue.
- Applications: Crucial for aluminum die-casting molds; they endure high pressures and heat well.
Comparison Table of Carbon Tool Steels for Mold Making
Type of Steel | Examples | Hardness Level | Applications | Limitations |
---|---|---|---|---|
High Carbon Tool Steel | T7A – T12A | High | Simple molds, stamping molds | Poor hardenability, large deformation |
Low Alloy Tool Steel | CrWMn, 9Mn2V | Medium-High | Cold stamping, high precision molds | Moderate wear resistance |
High Alloy Tool Steel | W18Cr4V | Very High | High-speed tools, complex molds | Expensive |
Hot Working Die Steel | 5CrNiMo | High | Die-casting molds; withstands high temps | Limited availability |
Key Considerations When Selecting Carbon Tool Steels
When selecting the appropriate carbon tool steel for mold making, consider factors such as:
- Load Requirements: Knowing the mold’s load is key; it helps me pick steel that withstands the pressure.
- Complexity of Mold Design: Complex designs often need more alloys for top performance—designing is like creating a masterpiece where every detail matters!
- Thermal Resistance: For high temperatures, I trust hot working die steels due to their superior thermal fatigue resistance—true workhorses!
For further reading on mold materials and their applications in various industries, check out these resources: material properties1, mold making processes2.
High carbon tool steels are suitable for simple molds only.True
High carbon tool steels like T7A - T12A are designed for simple molds, providing high hardness but limited hardenability.
Low alloy tool steels offer poor wear resistance.False
Low alloy tool steels enhance wear resistance due to their alloying elements, making them suitable for cold stamping molds.
How Do Alloying Elements Enhance Mold Steel Performance?
Have you ever wondered how alloy elements turn mold steel from good to extraordinary? I want to tell you about my journey into the interesting world of mold steel and how these elements really change everything.
Alloying elements enhance mold steel by boosting hardness, toughness, wear resistance, and thermal stability, enabling complex molds to endure high-stress applications effectively.
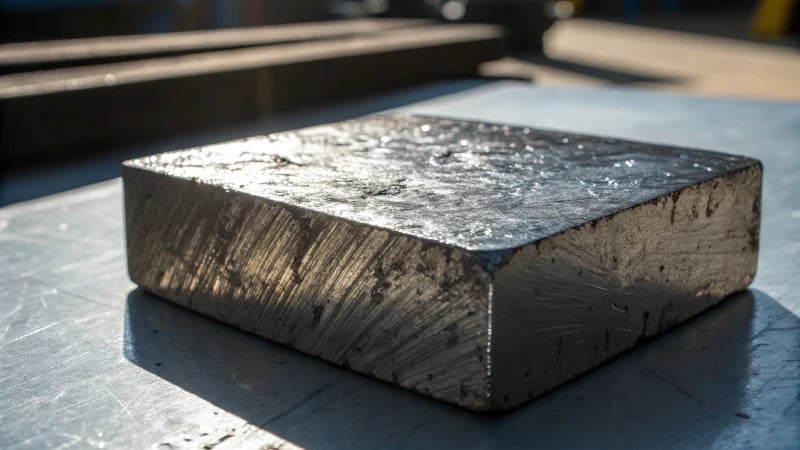
Understanding Alloying Elements
I explored mold steel and discovered alloying elements as hidden champions. These elements join base metals and tirelessly improve features like hardness, toughness, wear resistance, and machinability. They change ordinary steel into something extraordinary.
Look at low alloy tool steels. Adding chromium and manganese transformed my understanding. These elements really improve hardenability and toughness. They allow creating molds with complex shapes that endure high operational stresses. I recall working on a project with detailed designs for a new product. These improvements helped us achieve precision beyond our expectations.
Types of Mold Steel and Their Alloying Elements
Type of Mold Steel | Common Alloying Elements | Key Properties Enhanced |
---|---|---|
Carbon Tool Steel | Carbon | High hardness after quenching |
Low Alloy Tool Steel | Chromium, Manganese | Improved hardenability, toughness |
High Alloy Tool Steel | Tungsten, Molybdenum | High hardness, wear resistance |
Hot Working Die Steel | Nickel, Molybdenum | High strength and toughness at elevated temperatures |
Plastic Mold Steel | Nickel, Chromium | Good processing performance and minimal deformation |
Ductile Cast Iron | Silicon | Increased toughness and strength |
I studied high-speed steels like W18Cr4V and was amazed by tungsten. It really improves red hardness. This feature is invaluable for molds facing high-speed cutting or abrasive materials, such as glass fiber in plastic injection. It highlights the careful planning needed to select the right steel for specific tasks.
The Role of Alloying Elements in Performance
-
Hardness: My first lesson was the power of alloying elements in increasing mold steel hardness. Vanadium addition leads to fine carbide formation, resulting in fantastic hardness and wear resistance. I remember a project where achieving a specific hardness was crucial for success.
-
Toughness: Toughness is vital for mold steels facing impact loads. Nickel stands out as it improves toughness and prevents cracking under stress. I recall applying this knowledge in design talks aiming for durability.
-
Hardenability: Learning about hardenability was eye-opening. Chromium improves this trait, allowing steel to achieve desired hardness throughout during quenching. This is beneficial for complex shapes I often work with.
-
Wear Resistance: Molybdenum addition can greatly improve wear resistance in molds facing abrasive materials in production.
-
Thermal Stability: Consistency at different temperatures is important. Thanks to alloying elements, enhancing thermal stability and preventing heat-caused deformation is possible. This is something I frequently consider.
These improvements empower designers to select the best steel for applications, ensuring longevity and reliability.
Practical Implications for Product Designers
Being a product designer, understanding alloying elements’ specific benefits changed my process in choosing mold materials. For example, in consumer electronics design – demanding both precision and durability – I find high alloy or low alloy tool steels with specific elements often give better results than simple carbon steels.
To explore more about types of mold steels and their uses, consider resources on mold steel characteristics3 or alloying elements’ effects4. These insights have been very helpful in improving my designs and optimizing production processes.
Alloying elements improve mold steel toughness and hardness.True
Adding alloying elements enhances toughness and hardness, crucial for mold steel used in high-stress applications, preventing failure during operation.
High-speed steels retain hardness at elevated temperatures.True
High-speed steels like W18Cr4V maintain their hardness under heat, making them ideal for high-speed cutting tools and molds in demanding conditions.
What Role Do Non-Ferrous Metals Play in Mold Fabrication?
Do you ever think about how the materials we select influence the efficiency and performance of mold creation? Let’s dive into the interesting role of non-ferrous metals and discover how they leave a notable mark on our projects. Non-ferrous metals really matter.
Non-ferrous metals like copper and aluminum are crucial in mold fabrication due to their non-rusting and lightweight properties, enhancing mold efficiency and overall factory performance.
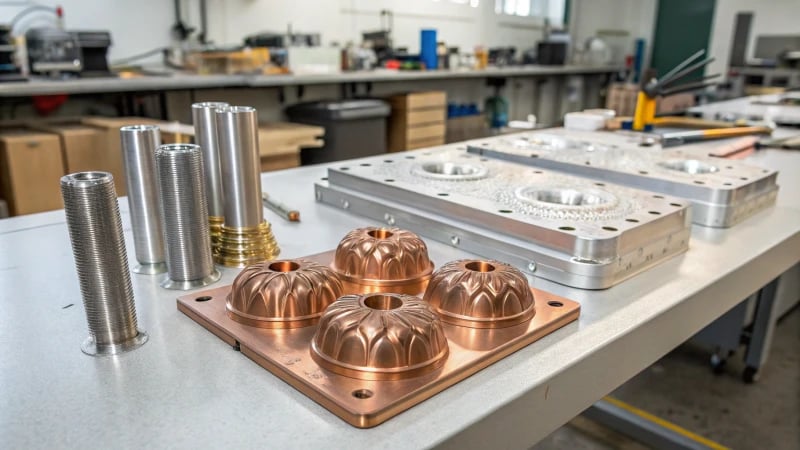
Importance of Non-Ferrous Metals in Mold Making
Non-ferrous metals play a key role in mold making due to their special traits. They do not contain iron like ferrous metals. Non-ferrous metals offer advantages such as resisting rust, being lighter and conducting electricity well.
1. Copper Alloys
Beryllium bronze is one material I really like. It is not only strong, but it also has amazing heat conductivity. I once worked on a project needing molds that cooled quickly during injection molding. Beryllium bronze inserts efficiently removed heat from the hot plastic, greatly cutting down the time for each cycle. This alloy’s flexibility is very useful in parts needing elastic reset mechanisms.
2. Aluminum Alloys
Aluminum alloys change the game. They weigh less and conduct heat well, making them ideal for molds that we often handle or move. They are great for reducing weight.
Type | Key Features | Applications |
---|---|---|
Cast Aluminum | Low density, good thermal conductivity | Auxiliary structural parts |
Aluminum Alloy | Lightweight, easy to machine | Molds with lower load requirements |
However, these alloys have lower strength, so they are best for less demanding uses.
3. Hard Alloys
Hard alloys like tungsten carbide are the superheroes of mold making. They resist wear and are incredibly hard, which is vital for very precise molds and fast stamping jobs. I use hard alloys for critical components like punches; this really extends the life of molds.
Composite Materials in Mold Fabrication
The arrival of composite materials in mold making excites me. Reinforced plastics, such as glass fiber reinforced plastic (GFRP) and carbon fiber reinforced plastic (CFRP), have become my top choices for light but strong solutions.
Material Type | Benefits | Typical Use Cases |
---|---|---|
GFRP | High corrosion resistance, lightweight | Small injection mold prototypes |
CFRP | Exceptional strength-to-weight ratio | Rapid mold manufacturing |
These materials greatly speed up prototyping and cut down mold development time a lot.
Applications of Non-Ferrous Metals in Mold Making
Exploring the applications more, I find non-ferrous metals everywhere in mold making:
- Injection Molds: Using copper alloys for inserts improves cooling efficiency; I have seen this success in many projects.
- Die-Casting Molds: Aluminum alloys create lighter designs while keeping functionality; this is crucial when we need efficiency.
- Precision Molds: Hard alloys provide strength under high stress; seeing a mold perform perfectly over time is truly satisfying.
Conclusion on Non-Ferrous Metals’ Role
Learning the special features of non-ferrous metals changed my work. They not only boost mold performance but also increase manufacturing efficiency. I urge you to learn more about the role of metal alloys5 or composite materials in manufacturing6. The right material choices can really take your designs to new heights!
Non-ferrous metals improve mold performance in fabrication.True
Non-ferrous metals enhance mold efficiency and performance due to their unique properties, making them essential in various fabrication applications.
Aluminum alloys are the strongest non-ferrous metals available.False
While aluminum alloys are lightweight, they generally have lower strength compared to other non-ferrous options like hard alloys and copper alloys.
Why Are Hard Alloys So Important for High-Precision Molds?
Do you ever think about why hard alloys are so important for high-precision molds? Hard alloys are essential in the manufacturing world. They really help shape the industry.
Hard alloys are crucial for high-precision molds due to their exceptional hardness, wear resistance, and thermal stability. These attributes enhance mold performance and longevity, making them essential for demanding manufacturing processes.
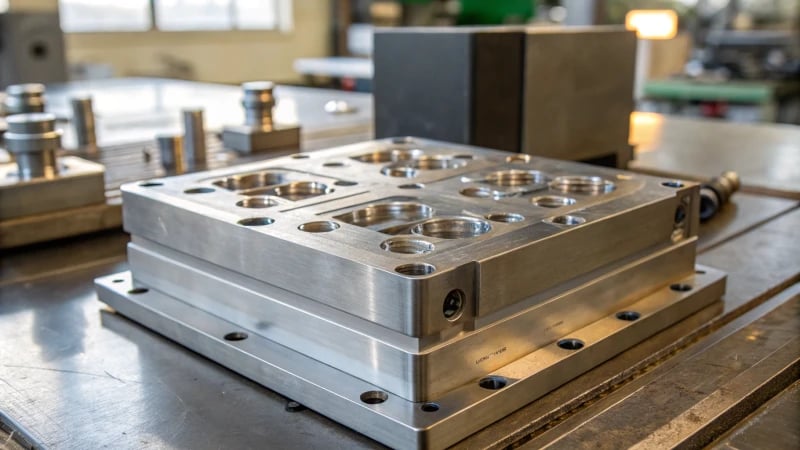
Understanding Hard Alloys
In the mold industry, hard alloys show amazing properties. Composed of strong compounds like tungsten carbide and titanium carbide, they play a crucial role in high-precision molds. Their features not only help molds last longer but also improve performance in many applications.
The critical characteristics of hard alloys include:
- High Hardness: A mold can keep its shape and precision even in tough conditions. This is the strength of hardness. Like a dependable friend, it never disappoints.
- Good Wear Resistance: Hard alloys fight abrasion from materials inside the mold. This increases the mold’s lifespan and decreases downtime.
- High Red Hardness: These alloys remain strong at high temperatures. This makes them perfect for fast and precise tasks, similar to an expert working under pressure.
- Chemical Stability: Hard alloys perform well when exposed to various chemicals, keeping mold integrity intact during production.
Applications in High-Precision Molds
Hard alloys are vital in complex molded products. They are important for essential parts in high-precision molds. Here’s a breakdown of their applications:
Component | Function | Material Used |
---|---|---|
Punches | Used in stamping operations to shape materials under high pressure. | Tungsten carbide |
Concave Molds | Essential for achieving intricate designs and shapes in molded products. | Titanium carbide |
Inserts | Improve thermal conductivity and enhance cooling during injection molding. | Beryllium bronze |
In ultra-precision molds, hard alloys help meet strict product standards like those needed for electronics components. They increase product quality and cut down on waste.
Challenges in Using Hard Alloys
Using hard alloys poses some challenges:
- Brittleness: Their extreme hardness might cause them to crack under stress. Even the strongest have their limits.
- Difficult Processing: Machining these alloys needs special techniques and tools, which often raises production costs. It’s similar to finding your way through a difficult road; the right tools are necessary.
- Cost: The price of hard alloys is often higher than other materials, which can be intimidating when planning costs for manufacturing projects.
Conclusion on the Role of Hard Alloys
As a mold designer, choosing materials for high-precision molds requires thoughtfulness. Hard alloys offer great benefits, but their challenges must also be considered. Understanding these factors is key for experts like us aiming for better performance while controlling costs. For more details on material selection, explore advanced materials7.
Hard alloys enhance mold durability and precision.True
The unique properties of hard alloys, such as high hardness and wear resistance, significantly improve the durability and precision of high-precision molds.
Hard alloys are inexpensive compared to other materials.False
Despite their advantages, hard alloys are generally more expensive than alternative materials, impacting manufacturing budgets.
How Can Composite Materials Improve Mold Efficiency?
Ever wondered how composite materials transform mold manufacturing? I have! Composites bring new efficiency and performance levels. These materials improve processes in unexpected ways.
Composite materials enhance mold efficiency due to their lightweight, high strength, and excellent thermal properties, enabling faster production and easier handling, making them ideal for modern mold design and processes.
Understanding Composite Materials in Mold Manufacturing
Composite materials truly transform mold manufacturing. They provide a fantastic mix of durability, reduced weight and withstand higher temperatures. Not like traditional options.
Reinforced plastic mold materials are amazing. Glass fiber reinforced plastic (GFRP) and carbon fiber reinforced plastic (CFRP) serve as fantastic choices. When I worked on a small injection mold prototype, using these composites changed everything. The molds became lighter and more resilient. Projects finished faster than before.
Composite materials are easy to process and modify. I remember when quick design changes were needed. Flexible materials saved the day! This flexibility is vital for designers like Jacky. Molds must not only look good but also function well in large-scale production.
Advantages of Composite Materials
Lightweight
Composites reduce mold weight. They are much easier to handle and transport. No more lifting struggles!
High Specific Strength
They provide excellent strength-to-weight ratios. Design intricate shapes without adding extra pounds.
Corrosion Resistance
Composites resist chemical attacks. Perfect for harsh production environments. A real relief for anyone involved!
Applications of Composite Materials
I’ve seen how composites work in various molds:
Injection Molds: In high-volume productions, composites shorten cooling times. Every second counts under tight deadlines.
Ceramic-Based Composites: These work well for high-temperature tasks like ceramic injection molding. Silicon carbide fiber reinforced ceramics (SiC/SiC) hold up under extremely tough conditions. I marvel at how they endure intense environments.
In tasks requiring rapid heating and cooling, composites improve cycle times. For example, beryllium bronze in mold inserts excels in heat dissipation. High thermal conductivity keeps things efficient!
The Future of Mold Efficiency with Composites
Reflecting on manufacturing’s future, composite materials will probably play a bigger role. Their lightweight nature and excellent performance decrease energy costs and emissions. This benefits both the environment and finances!
In summary, understanding how composites improve mold efficiency is crucial for manufacturers and engineers. Curious about specific applications or benefits? Explore advanced composite techniques . Let’s embrace these innovative materials together!
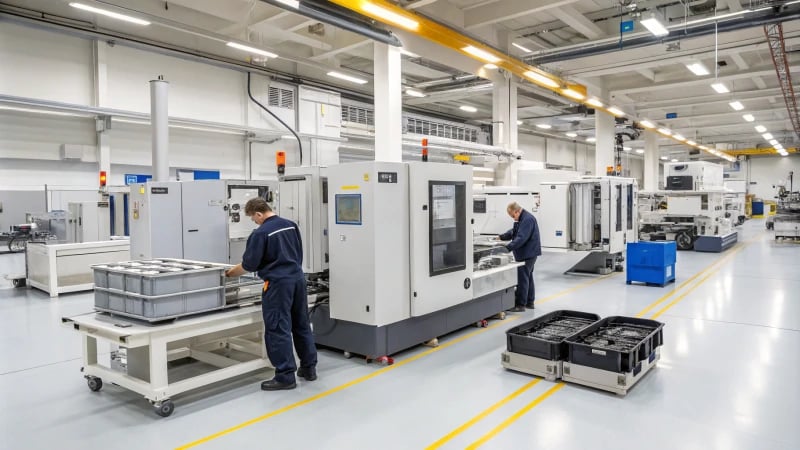
Understanding Composite Materials in Mold Manufacturing
Composite materials stand as unsung heroes in mold manufacturing. I really feel excited about their potential. When I first learned about these materials, it surprised me. They offer a unique mix of lightness, incredible strength and remarkable heat resistance. Traditional materials really struggle to compete with this combination. This mix helps achieve quicker production cycles. It probably makes life easier for designers like me.
Advantages of Composite Materials
- Lightweight: Composites reduce the overall weight of molds, making them easier to handle and transport.
- High Specific Strength: They provide greater strength-to-weight ratios compared to traditional materials, allowing for the design of more complex shapes without added weight.
- Corrosion Resistance: Composites resist chemical attacks, which is particularly beneficial in environments where molds might be exposed to harsh materials or conditions.
Property | Composite Materials | Traditional Materials |
---|---|---|
Weight | Lightweight | Heavier |
Strength | High Specific Strength | Variable |
Corrosion Resistance | Excellent | Limited |
Processing Flexibility | High | Moderate to Low |
Applications of Composite Materials
Composite materials find applications in various mold types:
- Injection Molds: Especially in high-volume production where rapid cycle times are crucial, composites can enhance efficiency by reducing cooling times due to their thermal conductivity properties.
- Ceramic-Based Composites: Silicon carbide fiber reinforced ceramics (SiC/SiC) are suitable for high-temperature applications like ceramic injection molding. They maintain integrity under extreme conditions and resist wear and chemical erosion effectively.
In applications requiring rapid heating and cooling cycles, the thermal properties of composites can lead to improved cycle times, thereby enhancing productivity. For example, beryllium bronze has been used in mold inserts where heat dissipation is critical due to its high thermal conductivity.
The Future of Mold Efficiency with Composites
As industries evolve towards more sustainable practices, the role of composite materials in mold manufacturing will likely expand. Their lightweight nature and superior performance characteristics not only contribute to reduced energy costs during production but also lower emissions during transport and handling.
In conclusion, understanding how composite materials can improve mold efficiency is vital for professionals in manufacturing and engineering. For further insights into specific applications or benefits of composites in mold design, consider exploring advanced composite techniques8 or case studies on mold efficiency improvements9.
Composite materials are heavier than traditional mold materials.False
This claim is false; composite materials are lightweight, making molds easier to handle.
Composites improve mold cooling times due to high thermal conductivity.True
This claim is true; composites enhance cooling efficiency, leading to improved production cycles.
What Factors Should You Consider When Choosing Mold Materials?
Selecting the correct mold materials greatly transforms manufacturing. Manufacturers focus on more than just efficiency. They aim to create durable products. Sharing knowledge from my experiences might be helpful.
Consider strength, toughness, cost, production volume, finish, tolerances, environmental factors, and ease of fabrication when choosing mold materials, as these aspects influence mold performance and longevity.
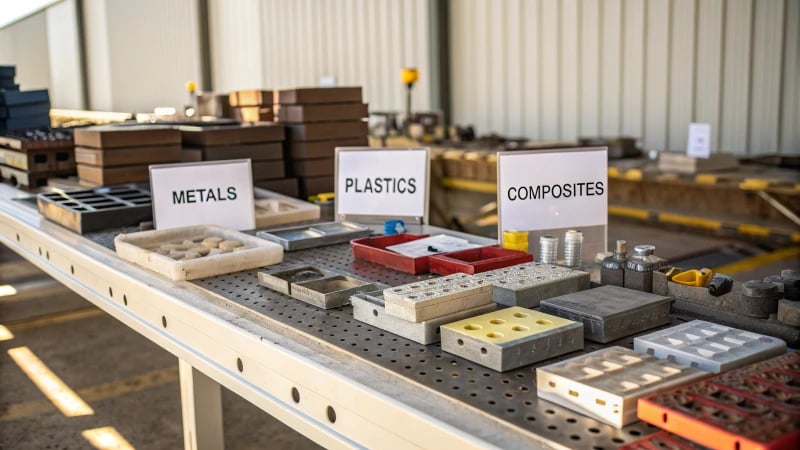
Understanding the Role of Mold Materials
When I first started my journey in product design, I quickly saw that picking the right mold materials was not just a technical decision. It felt almost like choosing ingredients for a recipe. Each factor plays a big role in how successful the final dish – or the product – becomes. Here’s what I’ve learned over the years:
1. Mechanical Properties
Strength, hardness, and toughness are basic mechanical qualities that decide how well a material can handle the stresses of molding. For example, in one project with plastic injection molding and glass fiber fillers, I learned about high-speed steels like W18Cr4V. They worked well because of their great wear resistance.
Property | Material Type | Example | Application |
---|---|---|---|
Hardness | High Alloy Tool Steel | W6Mo5Cr4V2 | Complex molds |
Toughness | Ductile Cast Iron | QT500-7 | Impact load molds |
Thermal Resistance | Hot Working Die Steel | 5CrNiMo | Die-casting molds |
Learn more about mechanical properties in material strength considerations10.
2. Cost Considerations
When managing budgets, cost became a big factor in my decisions. While high alloy steels delivered great performance, they proved expensive compared to materials like gray cast iron. I remember a time when choosing cheaper materials saved us a lot of money without much drop in quality.
3. Production Volume
Expected production volume affects material choice. For low-volume runs, reinforced plastics provided a fast and cost-effective solution. But, for high-volume production, choosing high-speed steel or hot working steels was wise due to their strength and long life.
4. Required Finish and Tolerances
Every application needs different levels of finish and precision. I worked with plastic mold steels, like P20, which offered great surface finish ability for detailed designs. Understanding what my final product needed helped me choose materials wisely.
Discover more about finishing in achieving mold precision11.
5. Environmental Factors
The operating environment is really crucial. If molds contact corrosive substances, materials with good corrosion resistance – such as copper alloys or composite materials – become essential. These choices greatly affect the mold’s life.
6. Fabrication and Processing
Ease of fabrication is another important aspect. Some materials are tougher to machine than others and finding the right balance between machinability and performance is tricky. I’ve dealt with hard alloys that performed well but were difficult to work with.
Explore more on processing challenges in fabrication techniques12.
By considering these factors based on my experiences, I’ve managed to make smart decisions that improve productivity and product quality in my molding processes.
High-speed steels are ideal for high-impact mold applications.True
High-speed steels like W18Cr4V offer excellent wear resistance, making them suitable for molds subjected to high impact loads, particularly in plastic injection molding.
Cost is the only factor when choosing mold materials.False
While cost is important, it is not the sole factor; mechanical properties, production volume, and environmental conditions also significantly influence material selection.
Conclusion
Explore essential materials for mold-making, including carbon tool steels, non-ferrous metals, hard alloys, and composites. Each material offers unique benefits tailored to specific applications.
-
Discover the detailed characteristics and applications of carbon tool steels for effective mold making decisions. ↩
-
Explore the differences between high carbon and low alloy tool steels for mold applications. ↩
-
Understanding these insights can help optimize your mold designs for better performance and durability. ↩
-
Gain deeper knowledge about material properties and their implications in manufacturing processes. ↩
-
Explore this link to discover detailed insights into the benefits of using non-ferrous metals in mold fabrication processes. ↩
-
Click here to learn more about specific applications of aluminum alloys in mold making. ↩
-
Explore this link for in-depth material selection strategies that enhance mold performance and durability. ↩
-
This link provides in-depth insights into advanced composite techniques that can help you enhance your mold designs. ↩
-
Discover case studies that demonstrate how composites have improved mold efficiency in real-world applications. ↩
-
This link offers detailed insights into material selection for molds, ensuring you choose wisely based on your project’s needs. ↩
-
Learn about the latest advancements in mold materials and techniques that can enhance your manufacturing processes. ↩
-
Explore efficient fabrication techniques that can help streamline your mold production process. ↩