Quality Inspection
blog & article
read our latest newsletter
Whether you’re curious about material selection, product design, mold design, mold making and injection molding, feel free to ask us anything. Our team is ready to provide the guidance and insights you need.
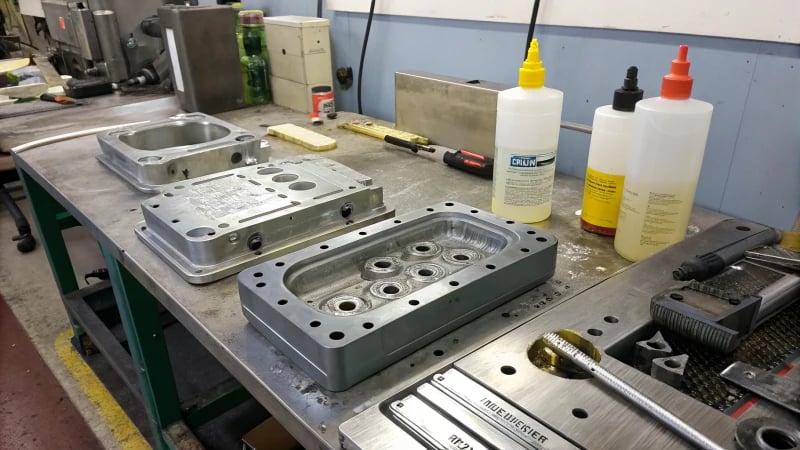
What Are the Steps to Successfully Plate Injection Molded Parts?
Plating injection molded parts involves several critical steps to ensure a successful outcome. Start with thorough cleaning using solvents like ethanol to remove contaminants. Next, enhance surface roughness through mechanical or chemical methods for better adhesion. Sensitization and activation treatments ...
Quality Inspection
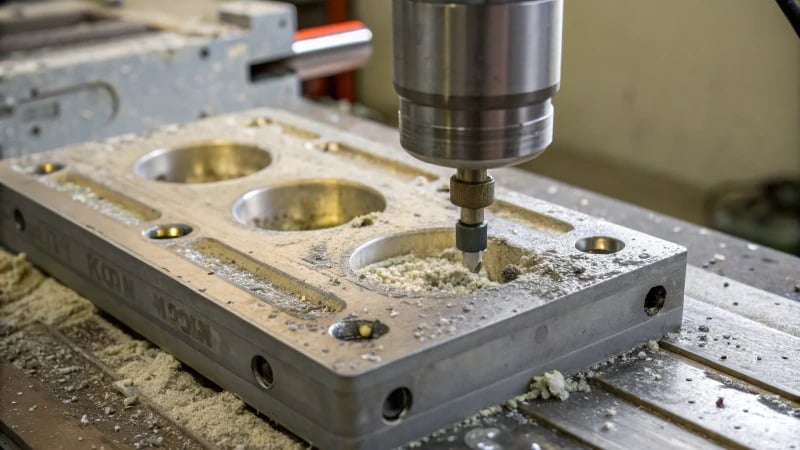
How Can You Identify Signs of Wear and Tear in Injection Molds?
This article discusses how to identify signs of wear and tear in injection molds that can affect product quality. Key indicators include dimensional deviations, surface quality deterioration, and increased filling pressure. Recognizing these early signs can prevent costly repairs and ...
Quality Inspection
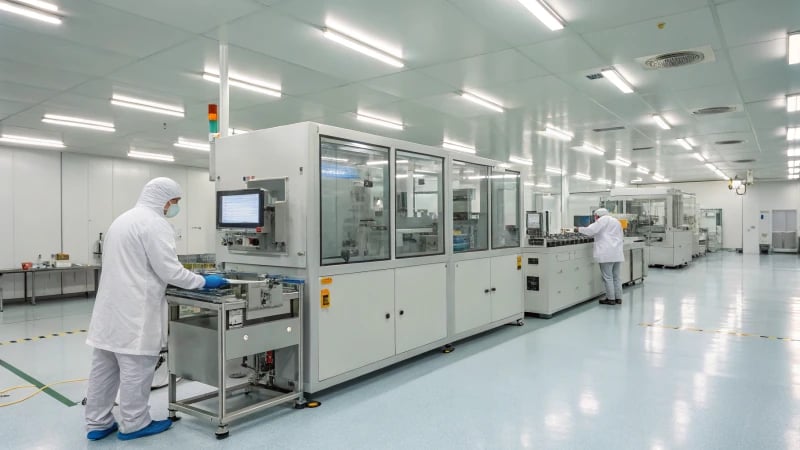
When Should You Use Clean Room Injection Molding?
Clean room injection molding is essential in various industries such as medical devices, pharmaceuticals, electronics, and aerospace. This process ensures that products are free from contaminants like dust and bacteria, which can compromise safety and functionality. In medical device manufacturing, ...
Quality Inspection
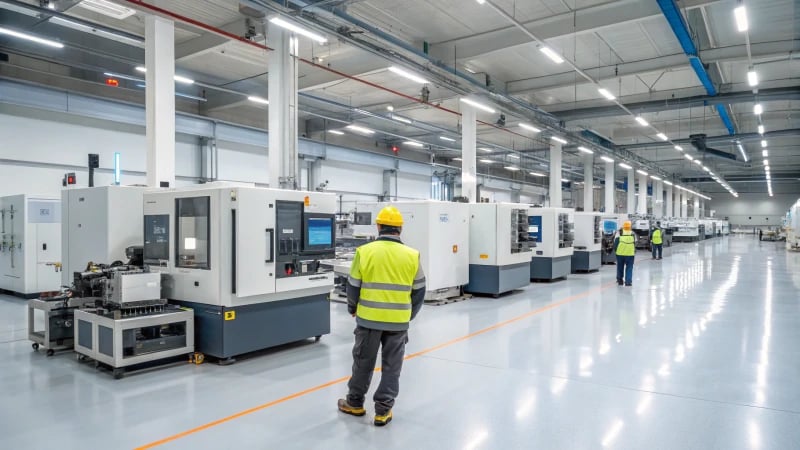
How Can You Ensure Quality Consistency from Suppliers in Injection Molding?
This article explores strategies for ensuring quality consistency from suppliers in injection molding. It emphasizes the importance of thorough supplier evaluations, clear contract agreements detailing quality standards, vigilant production oversight, and ongoing quality improvement measures. By implementing a structured approach ...
Quality Inspection
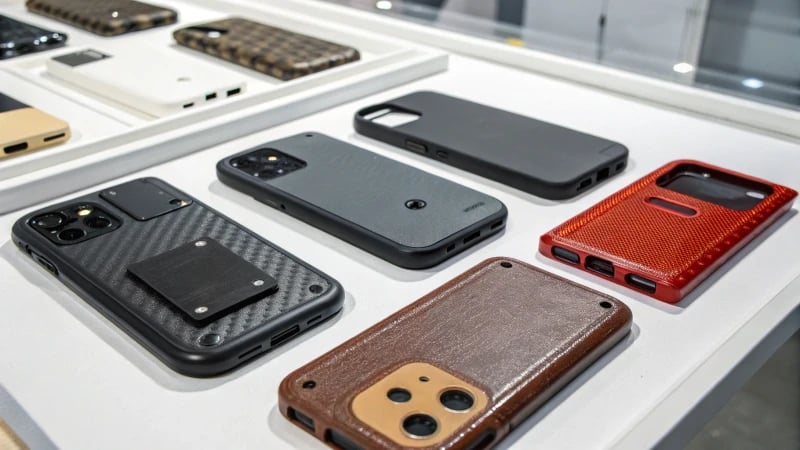
What Are the Key Standards for Injection Molded Electronic Casings?
This article explores the essential standards for designing injection molded electronic casings. It covers critical aspects such as dimension and tolerance controls, material performance requirements, appearance quality considerations, functionality standards like electromagnetic compatibility (EMC), waterproofing ratings, and rigorous quality inspection ...
Quality Inspection
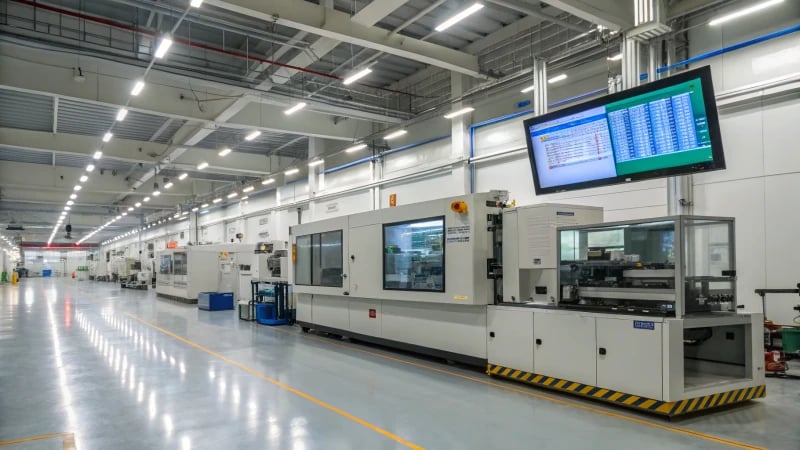
How Can You Effectively Monitor and Control the Qualified Rate After Injection Molding?
Effective monitoring and control of qualified rates in injection molding hinge on implementing strong quality assurance protocols, utilizing real-time data analytics for process oversight, and fostering a culture of continuous improvement. Key checks such as dimensional verification, visual inspections, mechanical ...
Quality Inspection
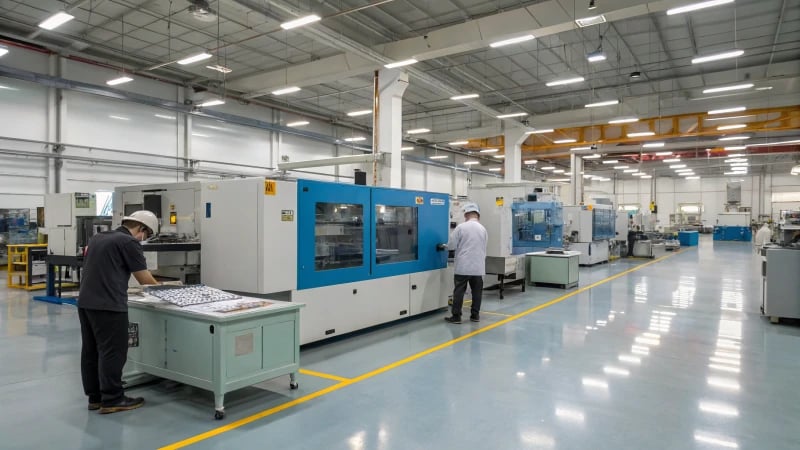
What Are the Key Benefits of ISO 9001 Certification for Injection Molding Operations?
ISO 9001 certification provides significant advantages for injection molding operations. It boosts efficiency, enhances product quality, and improves customer satisfaction. By standardizing processes and focusing on continuous improvement, companies can reduce waste and optimize resource management. This leads to consistent ...
Quality Inspection
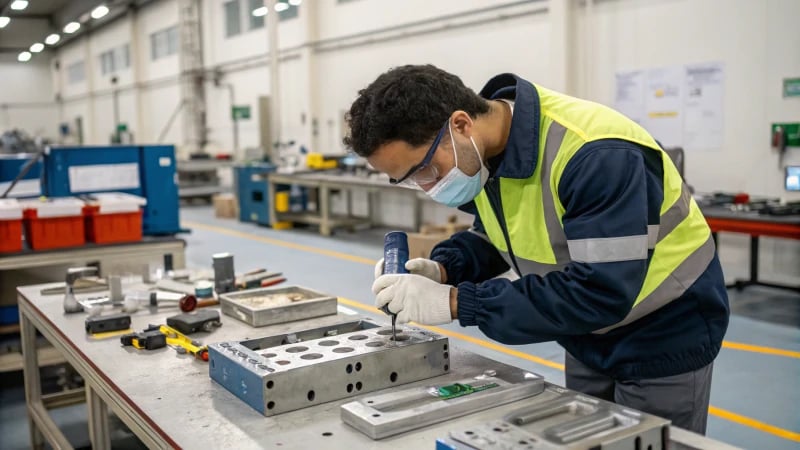
How Can You Troubleshoot and Repair Injection Molds Effectively?
Troubleshooting and repairing injection molds is essential for maintaining product quality and efficiency. This guide covers key diagnostic methods such as appearance inspection, dimensional measurement, action checks, and cooling/heating system evaluations. It emphasizes the importance of regular maintenance practices like ...
Quality Inspection
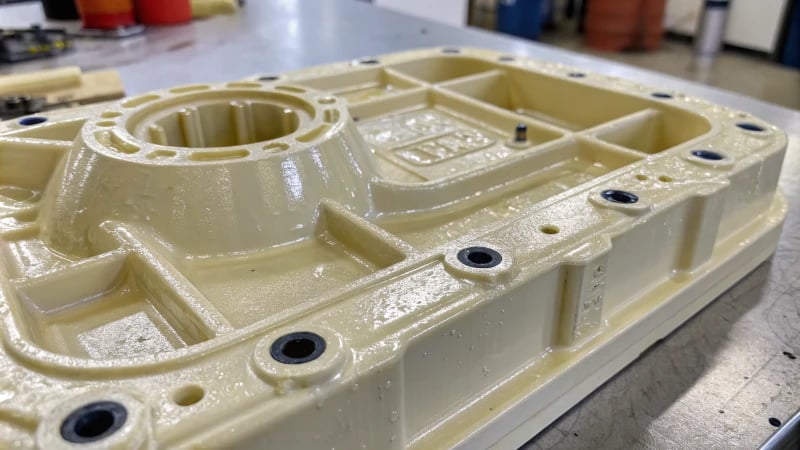
How Do Gas Marks Affect the Injection Molding Process?
Gas marks in injection molding occur when trapped gases create surface blemishes, compromising both aesthetics and structural integrity. This article explores the causes of gas marks, including material degradation, poor venting, and high injection speeds. It emphasizes the importance of ...
Quality Inspection
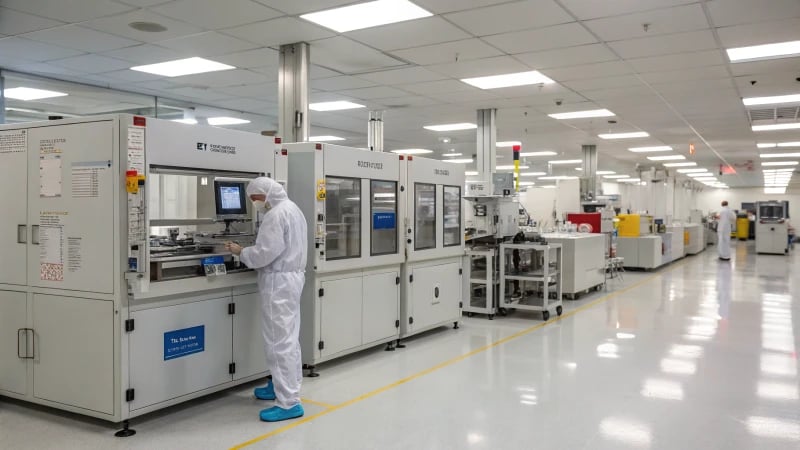
How Do Injection Molding Companies Achieve FDA Compliance?
Achieving FDA compliance is crucial for injection molding companies, especially in medical and food sectors. This involves selecting compliant materials from certified suppliers, conducting rigorous inspections using techniques like FTIR, maintaining a robust Quality Management System (QMS), and ensuring continuous ...
Quality Inspection
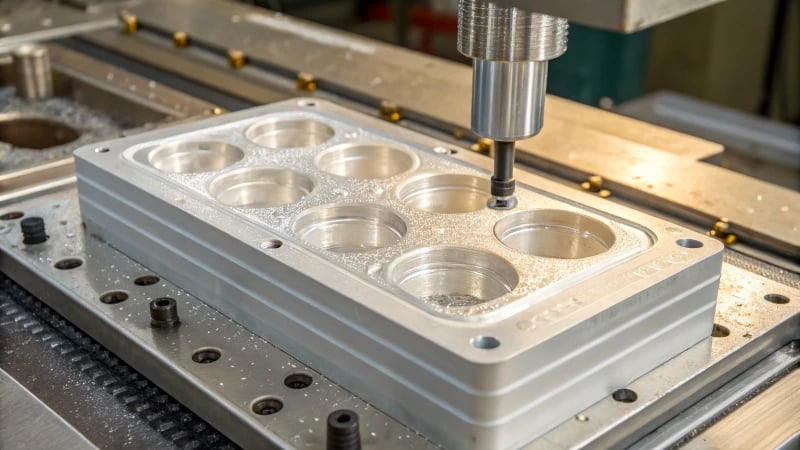
Why Do Injection Molds Need Vents?
Venting is a critical aspect of injection mold design that allows trapped air and gases to escape during the molding process. Proper venting prevents common defects such as burn marks, short shots, and poor surface finishes. This article explores the ...
Quality Inspection
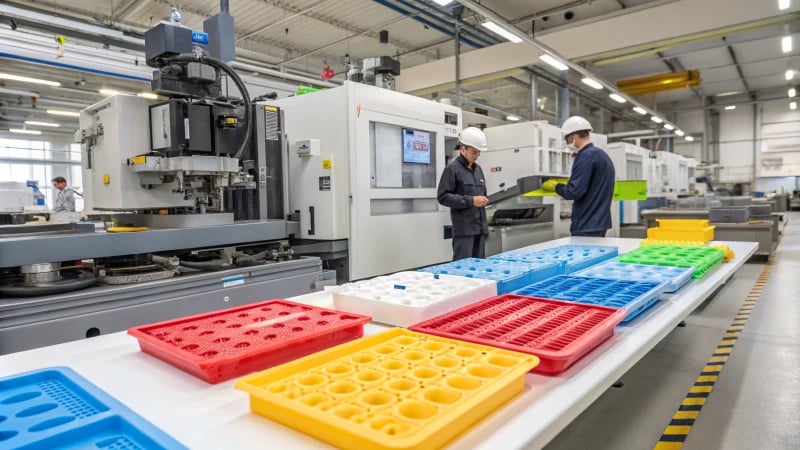
What Are the Essential Quality Control Considerations for Overmolding?
Overmolding enhances product strength and aesthetics, but requires strict quality control. Key considerations include material compatibility, surface preparation, dimensional stability, and effective bonding techniques to ensure high-quality outcomes.
Quality Inspection
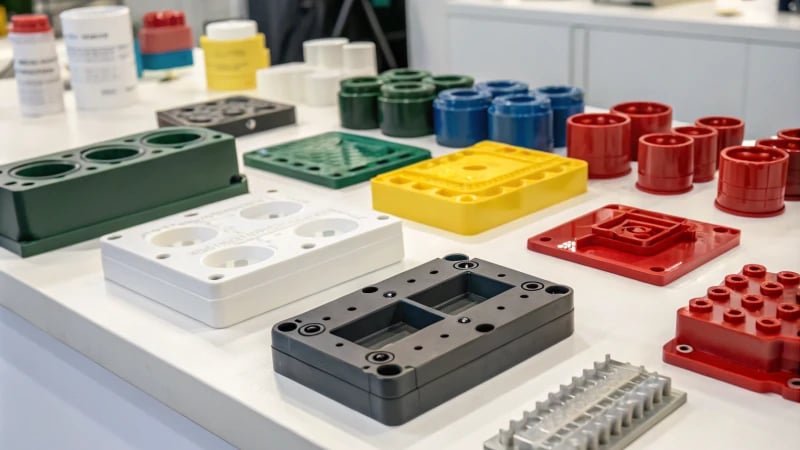
What Common Defects Occur in Extrusion and Injection Molding, and How Can They Be Prevented?
This article explores common defects in extrusion and injection molding, their causes, and preventive measures to enhance product quality. Key insights include material purity, mold design, and process monitoring.
Quality Inspection
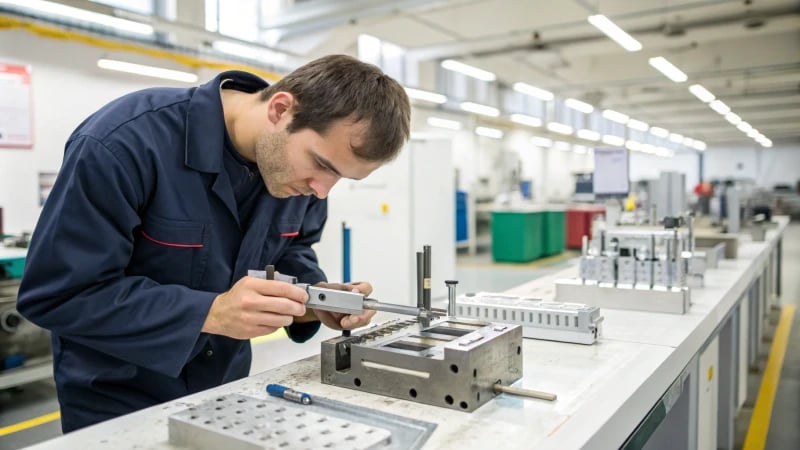
How Can You Test and Ensure the Accuracy of Injection Molds?
Ensuring the accuracy of injection molds is crucial in manufacturing. This article discusses various testing methods such as appearance inspection, surface roughness detection, linear dimension measurement, and assembly accuracy checks. Techniques like using roughness meters for surface quality assessment and ...
Quality Inspection
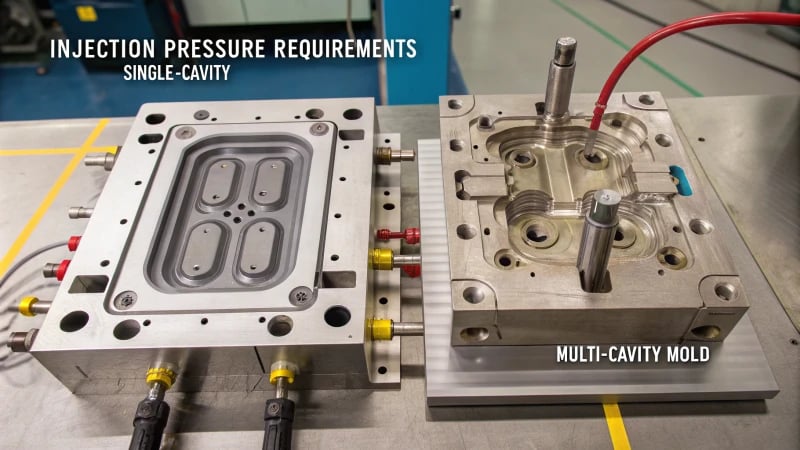
How Does the Number of Mold Cavities Impact Injection Pressure?
This article explores how the number of mold cavities impacts injection pressure in the molding process. Single-cavity molds utilize lower pressures due to their straightforward flow paths, allowing for consistent quality and energy efficiency. In contrast, multi-cavity molds face increased ...
Quality Inspection
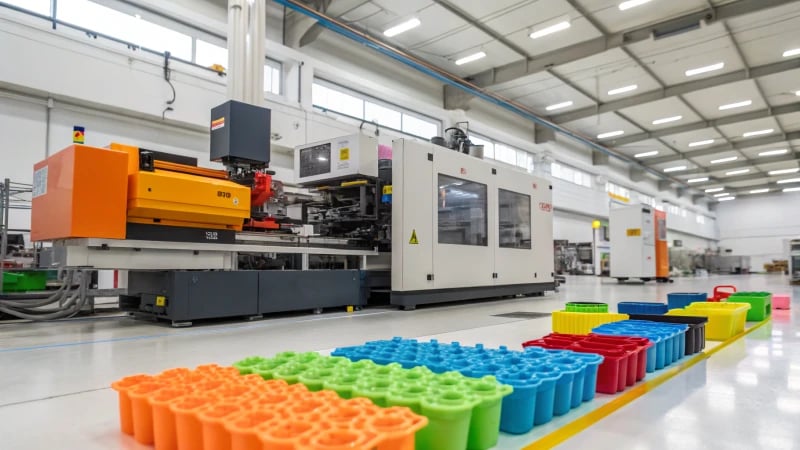
How Can You Effectively Manage Shrinkage Problems in Injection Molded Products?
Shrinkage in injection molded products can significantly impact quality and dimensions. To effectively manage this issue, manufacturers should adjust key process parameters such as holding pressure, injection speed, melt temperature, and mold temperature. Additionally, modifying mold structures by increasing gate ...
Quality Inspection
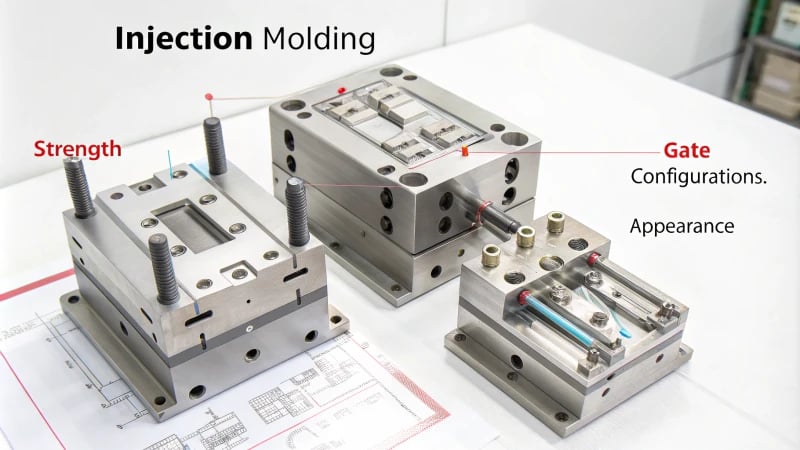
How Does Gate Location and Size Impact Product Properties?
In injection molding, the placement and size of gates are critical factors that impact both the aesthetic and functional qualities of a product. Proper gate positioning can minimize visible defects such as gate marks and flow lines, which can detract ...
Quality Inspection
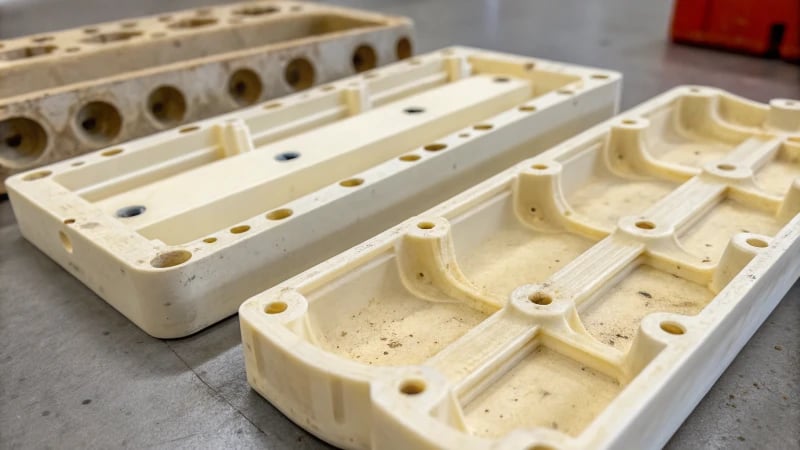
What Causes Product Warpage Defects?
This article explores the causes of product warpage in injection molding, focusing on key factors such as mold design, cooling systems, injection pressures, and material properties. Uneven cooling is a primary contributor to warpage, often exacerbated by irrational cooling system ...
Quality Inspection
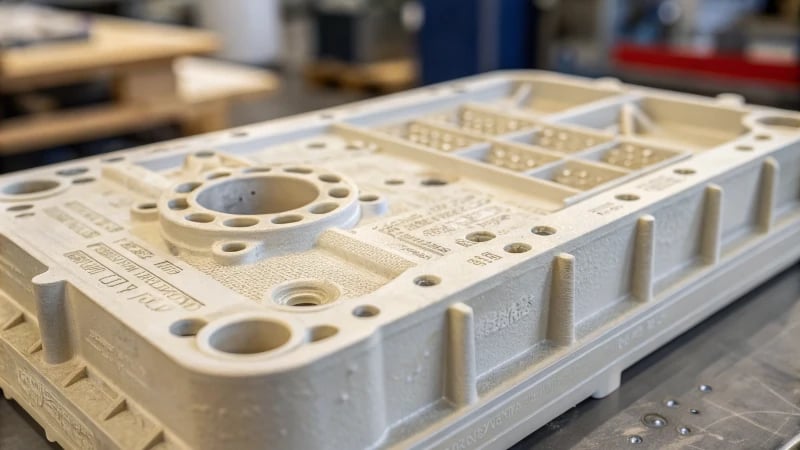
What Causes Sprue Marks on Injection Molded Products?
Sprue marks are common defects in injection molded products caused by various factors including gate design, process parameters, and material properties. Properly designed gates with appropriate sizes, shapes, and locations are crucial to minimize these marks. Additionally, adjusting injection speeds ...
Quality Inspection
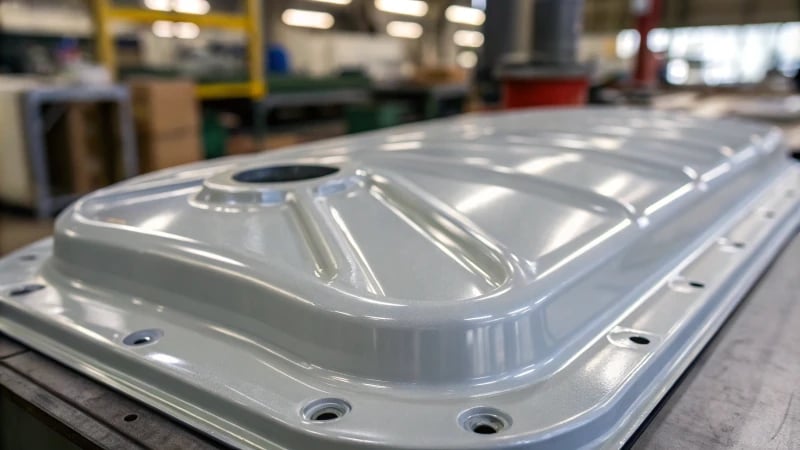
What Are the Key Factors That Influence the Quality of a Parting Line?
This article explores the key factors influencing the quality of parting lines in injection molding. It emphasizes the importance of mold accuracy, design considerations, material selection, and precise control over injection parameters such as pressure and temperature. Each aspect plays ...
Quality Inspection
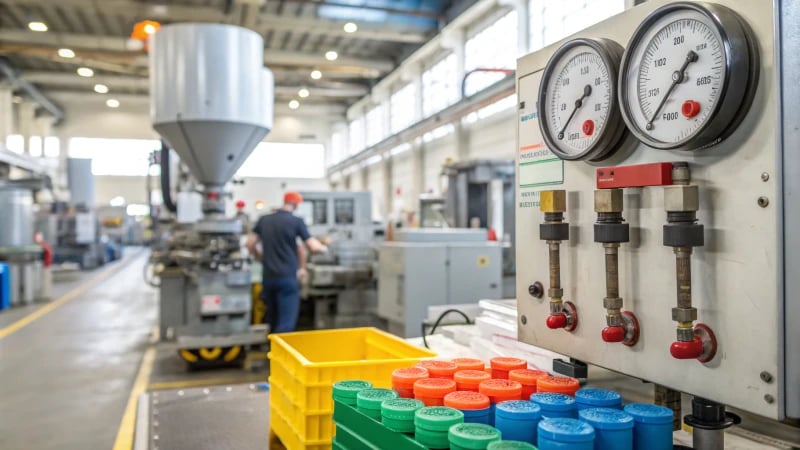
How Do Injection Molding Process Parameters Impact Product Weight?
The injection molding process is a delicate balance of various parameters that directly impact the weight of the final product. Key factors include screw stroke, injection pressure and speed, holding pressure and time, as well as melt and mold temperatures. ...
Quality Inspection
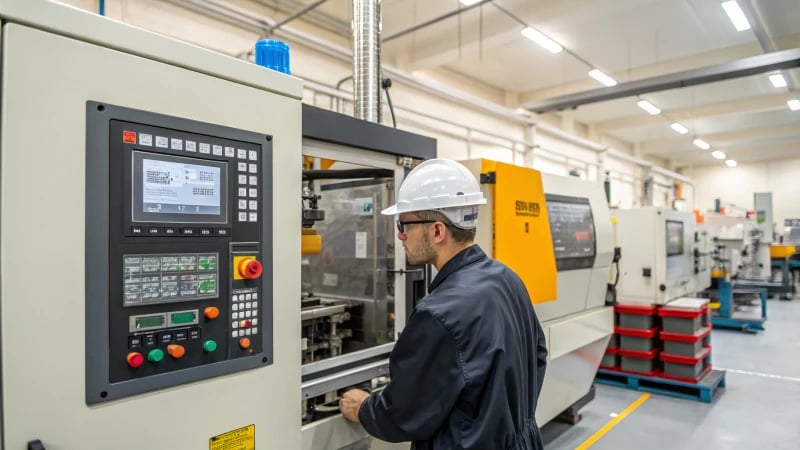
How Does Injection Speed Impact the Quality of Plastic Products?
This article explores how injection speed influences the quality of plastic products in terms of both appearance and internal integrity. Fast injection speeds can lead to surface defects such as flow marks, weld lines, and air entrapment, while slow speeds ...
Quality Inspection
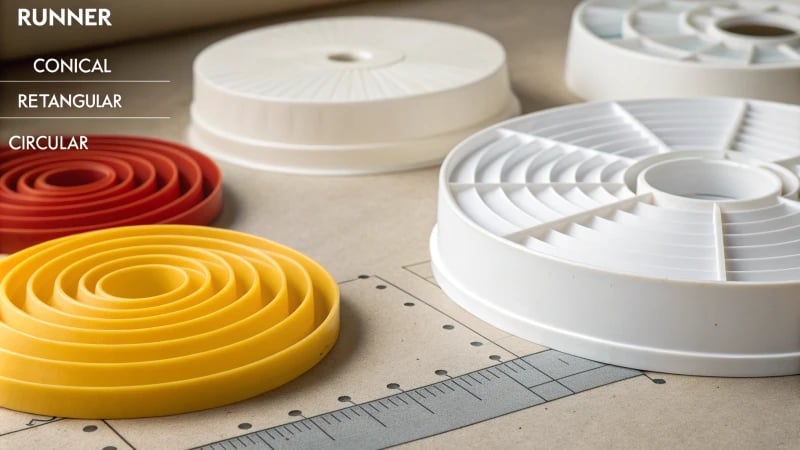
Why Do Injection Molded Products Lack Sufficient Strength?
Injection molded products frequently fail to meet strength expectations due to various factors including high impurity content, inadequate material drying, incorrect injection parameters, and flawed mold designs. Impurities such as dust or metal chips create weak points in the material, ...
Quality Inspection
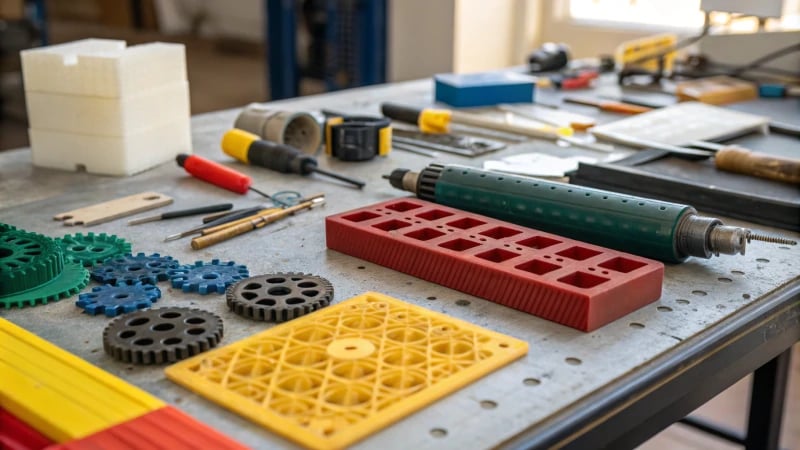
How Does Injection Pressure Affect the Performance of Plastic Products?
This article explores how injection pressure affects the mechanical properties, dimensional stability, and physical traits of plastic products. It highlights the importance of proper pressure settings in enhancing strength, toughness, and accuracy in manufacturing processes. Through personal experiences and examples ...
Quality Inspection
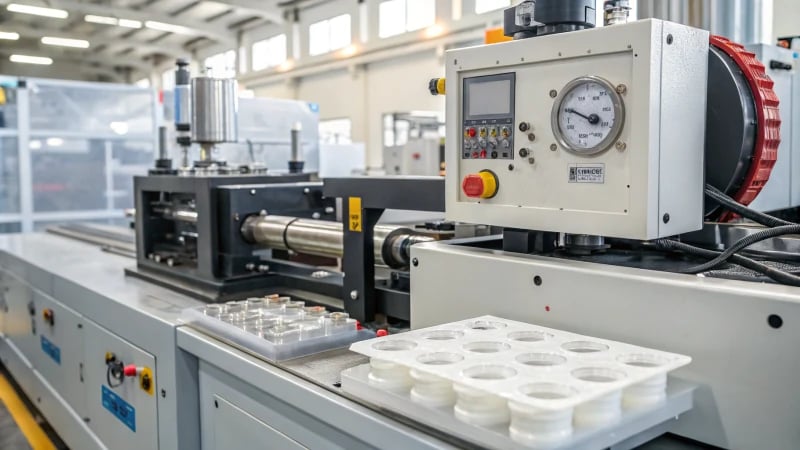
How Does Injection Pressure Impact the Dimensional Stability of Plastic Products?
This article explores how injection pressure influences the dimensional stability of plastic products. It highlights the consequences of both excessive and insufficient pressure during molding processes, emphasizing that high pressure can lead to product shrinkage and warping due to internal ...
Quality Inspection
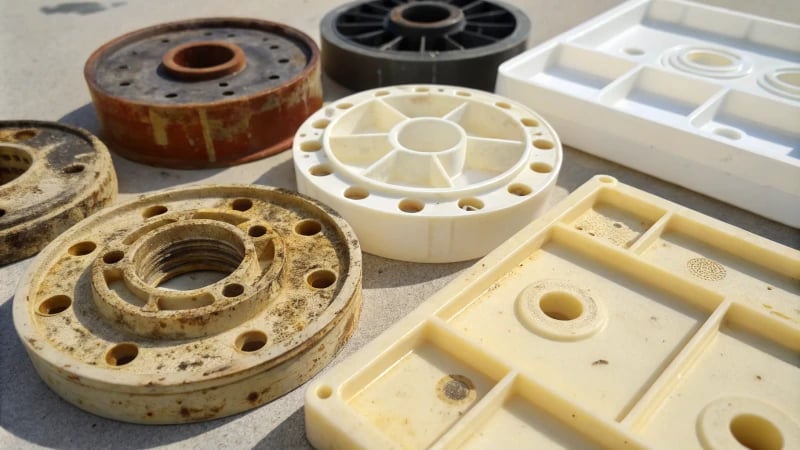
How Does Improper Pretreatment Affect Injection Molded Product Properties?
This article explores the critical impact of improper pretreatment on injection molded products. It highlights how inadequate drying, mixing, and preheating can lead to significant issues such as reduced mechanical strength, deteriorated toughness, uneven hardness distribution, and poor surface quality. ...
Quality Inspection
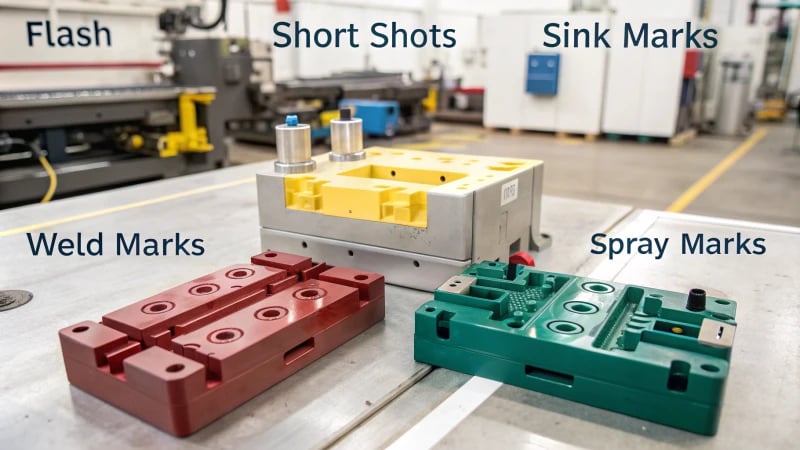
What Defects Arise from Improper Injection Pressure in Molding?
This article explores how improper injection pressure during the molding process can lead to various defects such as flash, short shots, sink marks, weld marks, and spray marks. Each defect arises from either too high or too low injection pressure ...
Quality Inspection
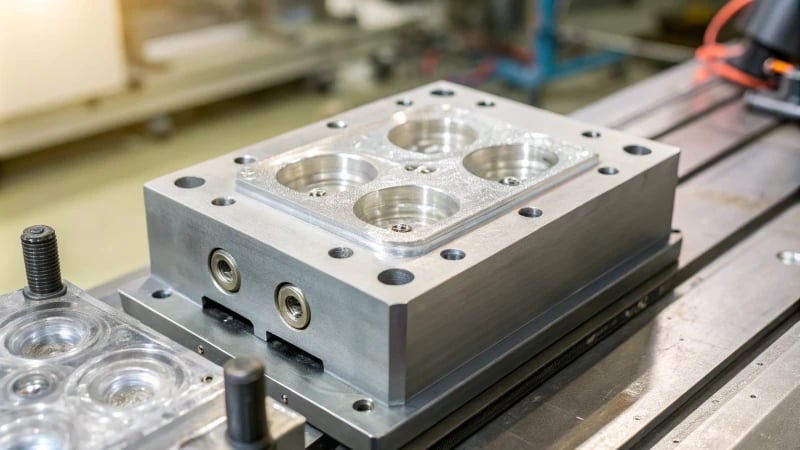
How Does Insufficient Mold Filling Affect the Quality of Injection Molded Products?
This article explores how insufficient mold filling negatively impacts the quality of injection molded products. It discusses various defects such as short shots, increased surface roughness, and dimensional deviations that arise from incomplete filling. These issues not only affect the ...
Quality Inspection
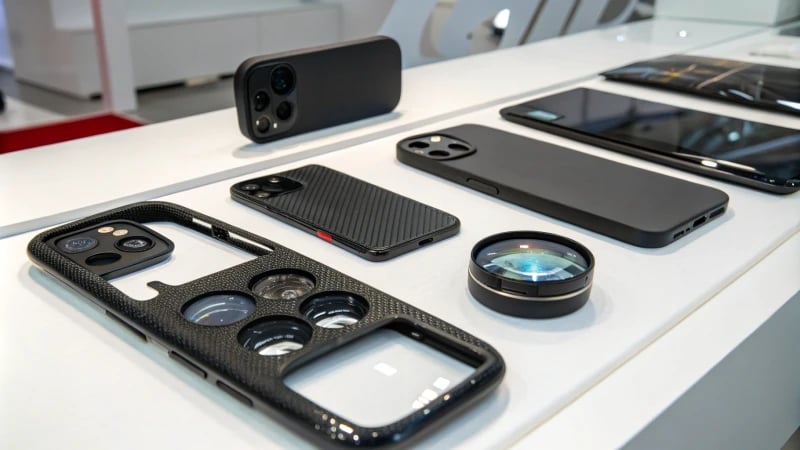
What Injection Molding Products Require High Surface Flatness?
This article explores the critical importance of high surface flatness in injection molding products such as optical lenses, smartphone cases, car dashboards, and household items. It discusses how precise flat surfaces enhance clarity in optical devices, improve aesthetics and functionality ...
Quality Inspection

What Are the Key Steps to Examine the Production Management Process of a Mold Manufacturer?
Understanding the production management process is crucial for mold manufacturers to ensure quality and efficiency. This article details key areas to examine during evaluations: raw material management, production planning, machining processes, assembly operations, and quality inspections. Each step is vital ...
Quality Inspection