Being a designer in the plastic manufacturing industry teaches me the importance of reducing defects such as fusion marks. Reducing these defects is essential. Adjusting melt temperature plays a big role in this task. I feel very thrilled to share my knowledge and experiences!
To minimize fusion marks in injection molding, adjust melt temperature within the optimal range for each material, and consider the effects of injection speed and pressure.
I’ll share my journey of finding the best steps for adjusting melt temperature. I have faced many challenges with fusion marks. Understanding material properties changed everything for me. Each plastic type has its perfect melt temperature range. For instance, polystyrene needs 180 – 280°C. Polypropylene requires 200 – 280°C. Knowing the material and its quirks is key.
Raising melt temperature is helpful, too. I recall increasing polycarbonate’s temperature from 280 – 300°C to 300 – 320°C. This change greatly reduced those annoying fusion marks. However, too high a temperature really damages your product. Balancing quality with efficiency is crucial for me. Mold structure is important as well. Optimizing cooling channels has prevented many problems from uneven temperatures. I found that adjusting melt temperature with other factors like injection speed is vital. It really helps achieve the best results.
Proper melt temperature adjustment reduces fusion marks.True
Adjusting the melt temperature correctly can minimize defects like fusion marks in injection molding, leading to higher quality components.
Higher melt temperatures always eliminate fusion marks.False
While higher melt temperatures can help reduce fusion marks, they may also lead to other defects, making this claim false.
- 1. Why Does Melt Temperature Matter in Injection Molding?
- 2. How Does Material Choice Affect Melt Temperature Adjustment?
- 3. What Are the Risks of High Melt Temperatures?
- 4. How Can Mold Design Influence Melt Temperature Management?
- 5. What Additional Parameters Should Be Considered Alongside Melt Temperature?
- 6. Conclusion
Why Does Melt Temperature Matter in Injection Molding?
Ever felt confused about melt temperature’s role in injection molding? Really, I understand! Melt temperature is very important in injection molding. It helps in getting the best product quality. Let’s explore why knowing melt temperature is crucial for perfect results.
Melt temperature is crucial in injection molding, determining material flow and product quality. Proper temperature control within specific ranges reduces manufacturing defects and ensures consistent, high-quality outputs for different plastics.
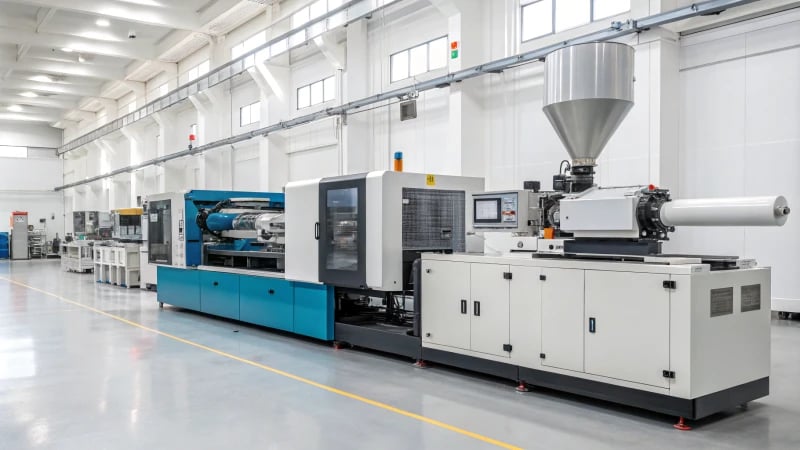
Understanding Material Properties
Melt temperature is more than a number on a machine; it’s key to injection molding. Each plastic type has its own unique melt temperature range that must be respected to avoid material degradation. It’s like they have their comfort zones. For example:
Material | Melt Temperature Range (°C) |
---|---|
Polystyrene (PS) | 180 – 280 |
Polypropylene (PP) | 200 – 280 |
Polyvinyl Chloride (PVC) | 160 – 220 |
Understanding this factor is crucial as it influences material behavior and the final product’s quality. Just like a chef needs the right temperature to bake a cake, we need the right melt temperature for perfect molded parts.
Heat-sensitive materials, such as PVC, are tricky. I learned this during a project when I increased the temperature too much. The PVC broke down and released harmful gases like hydrogen chloride. It messed up the product and my equipment, teaching me how careful I must be with melt temperatures.
Appropriately Increase the Temperature of the Melt
Increasing melt temperature is about balance. Higher temperatures reduce viscosity, allowing smoother mold flow. Once, I increased polycarbonate (PC) melt temperature from 280 – 300°C to 300 – 320°C. It was like switching from a trickle to a steady stream; the reduction in fusion marks was incredible, improving product looks and function.
However, too high a melt temperature risks thermal degradation, which can compromise mechanical properties and extend cooling times. Thus, balancing melt temperature with product quality and efficiency is critical.
Consider the Mold Structure and Cooling System
The design of both mold structure and cooling systems significantly impacts melt temperature management. Once, I had issues with badly designed cooling channels that caused local melt temperatures to drop quickly, leading to ugly fusion marks.
To achieve uniform temperature distribution, optimizing cooling channel layouts is essential. For example, using conformal cooling channels can better match mold cavity shapes, allowing for precise cooling control and reducing defects.
With Other Process Parameters Adjustment
Melt temperature changes work with other parameters like injection pressure and speed. When I raise melt temperature, I often lower injection pressure and speed. For example, during an ABS material project, increasing the melt temperature let me cut injection pressure by 10 – 15% and speed by 20 – 30%. The outcome? Fewer fusion marks with quality intact—a real win!
As melt temperatures go up, I adjust holding time and pressure since shrinkage changes need attention to avoid defects while ensuring accuracy.
Melt temperature is not just a detail; it’s crucial for making great products. By sharing my challenges and learning, I hope to inspire you to explore the interesting world of injection molding with me!
Melt temperature affects plastic viscosity in injection molding.True
Higher melt temperatures reduce viscosity, improving flow within molds and enhancing product quality.
Low melt temperature can lead to fusion marks in products.True
Insufficient melt temperature increases viscosity, causing poor flow and resulting in visible defects like fusion marks.
How Does Material Choice Affect Melt Temperature Adjustment?
Did you ever think about how the materials we pick change the melt temperature during production? The right choice really increases efficiency and improves the quality of the finished product. Let’s explore this complex connection together!
Material choice significantly influences melt temperature adjustments in injection molding. Each plastic type has specific melt temperature ranges affecting viscosity and flow, essential for preventing defects and enhancing production efficiency.
Raise the Melt Temperature Carefully
A higher melt temperature usually lowers viscosity. This lets plastic flow smoothly into the mold cavity. I remember increasing the melt temperature for polycarbonate (PC) from 280 – 300°C to 300 – 320°C. This change reduced fusion marks. Watching how a simple change really improved product quality was rewarding. However, setting the temperature too high might cause thermal degradation. This weakens the final product. Balancing quality and efficiency can be tricky, but it is very necessary.
Mold Structure and Cooling System Matter
Mold structure and cooling systems are very important for melt temperature. Early in my career, I ignored this and faced problems with uneven temperature distribution. These caused defects like fusion marks. I optimized the cooling channels with follow-shape designs. This change was thrilling. It improved fits within mold cavities. Accurate cooling control really reduced temperature variations and defects. What a relief!
Coordinate With Other Process Settings
Adjusting melt temperature should match with other injection settings like pressure and speed. Increasing the melt temperature lets me lower injection pressure and speed due to better fluidity. For instance, with ABS material, I increased the melt temperature and reduced injection pressure by 10 – 15%. Speed decreased by 20 – 30%. This adjustment minimized fusion marks and stopped defects like flying edges. It was definitely a win!
Adjustment of Holding Time and Pressure: At hotter temperatures, material shrinkage changes, needing pressure adjustments for accurate size.
Understanding these complex relationships helped me pick materials and set processing parameters wisely. Product quality and production efficiency improved as a result.
For more on optimizing temperature in injection molding, read our articles on material properties and mold design techniques. Happy reading!
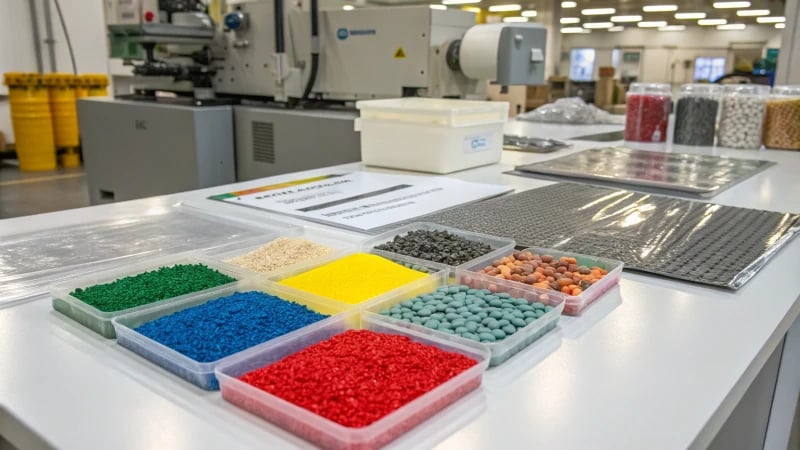
Understanding Material Properties
Material choice significantly influences melt temperature adjustments. Different plastics exhibit unique melt temperature ranges. For example:
Material | Melt Temperature Range (°C) |
---|---|
Polystyrene (PS) | 180 – 280 |
Polypropylene (PP) | 200 – 280 |
Polyvinyl Chloride (PVC) | Narrow range, sensitive to temperature |
In the beginning, I worked with various plastics and felt amazed by how much their properties differed. For example, polystyrene (PS) melts between 180 – 280°C, while polypropylene (PP) melts around 200 – 280°C. This difference showed me that knowing these ranges is really important. It is crucial to adjust melt temperatures correctly. Ignoring these limits could damage the material or alter its unique features. Very essential to respect them!
One eye-opening experience involved polyvinyl chloride (PVC). I found out that PVC is heat-sensitive and melts in a narrow range. During a project, I set the temperature too high by mistake. This caused PVC to break down and release hydrogen chloride gas. Unfortunately, this mistake harmed the product quality. It even corroded some equipment. A hard lesson indeed!
For heat-sensitive materials like PVC, precise temperature control is critical. Excessive heat can lead to decomposition, releasing harmful gases such as hydrogen chloride. Conversely, too low a temperature results in high viscosity, impeding flow and leading to defects.
Appropriately Increase the Melt Temperature
Increasing melt temperature generally reduces viscosity, allowing smoother flow within the mold cavity. For instance, raising the melt temperature for polycarbonate (PC) from 280 – 300°C to 300 – 320°C can effectively reduce fusion marks. However, caution is essential; overly high temperatures can cause thermal degradation, compromising the mechanical properties of the final product. Factors to consider include:
- Product Quality: Maintaining integrity without thermal damage.
- Production Efficiency: Balancing cooling times and cycle durations.
Consider the Mold Structure and Cooling System
The design of the mold and its cooling system profoundly affects melt temperature. If cooling channels are improperly designed, they may lead to uneven temperature distribution, causing defects like fusion marks. Optimizing cooling channels can achieve uniform temperature control throughout the mold.
For example, using follow-shape cooling channels allows:
- Improved fit within the mold cavities.
- Accurate control over cooling rates, thus minimizing local temperature variations that lead to defects.
With Other Process Parameters Adjustment
Melt temperature adjustments should align with other injection parameters such as pressure and speed. Increasing melt temperature enables a reduction in injection pressure and speed due to enhanced fluidity. For example, when raising the melt temperature of ABS material, reducing injection pressure by 10 – 15% and speed by 20 – 30% can effectively minimize fusion marks while preventing defects like flying edges.
- Adjustment of Holding Time and Pressure: Higher temperatures may alter material shrinkage, necessitating adjustments in holding pressure for dimensional accuracy.
Consider this table summarizing recommended adjustments:
Parameter | Recommended Change |
---|---|
Injection Pressure | Reduce by 10 – 15% |
Injection Speed | Reduce by 20 – 30% |
Holding Pressure | Adjust based on material shrinkage |
By understanding these relationships, manufacturers can make informed decisions on material selection and processing parameters, improving both product quality and production efficiency.
For further insights into optimizing melt temperature adjustments in injection molding, check out our related articles on material properties1 and mold design techniques2.
Different plastics have unique melt temperature ranges.True
Each type of plastic has a specific melt temperature range, affecting how they behave during processing.
Higher melt temperatures always improve product quality.False
While higher melt temperatures can enhance flow, they may also lead to thermal degradation and compromise quality if excessive.
What Are the Risks of High Melt Temperatures?
Ever been in a manufacturing process and felt worried about the melt temperatures? I know that feeling. Understanding these risks proves crucial. It changes product quality and efficiency significantly.
High melt temperatures can cause thermal damage in plastics, affecting strength and creating flaws. It’s crucial to understand specific melt ranges and adjust processing settings to maintain product quality.
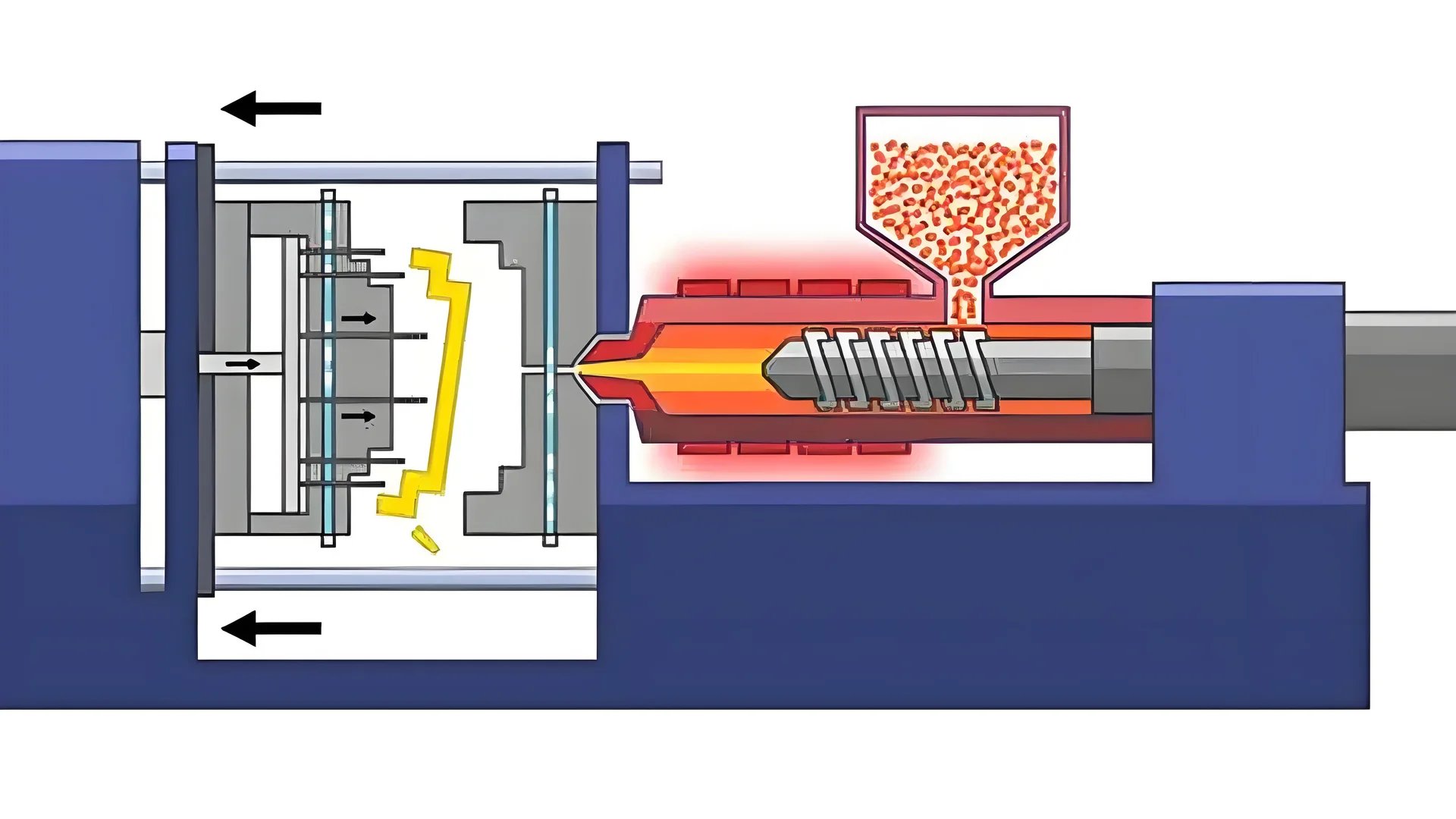
Understanding Material Properties
I remember my early days in product design. I felt overwhelmed by the many types of plastic materials and their unique melting temperatures. Different plastic materials come with specific melt temperature ranges that are crucial to their processing. For instance, polystyrene (PS) typically melts between 180 – 280°C, while polypropylene (PP) ranges from 200 – 280°C.
Each type has its own quirks. In the beginning, I learned to adjust melt temperatures. I quickly understood how important it is to stay within these limits. If you go too high, the material might degrade. Polyvinyl chloride (PVC) is an example. Its narrow melt range means high temperatures can break it down, releasing hydrogen chloride gas which can not only affect product quality but also corrode machinery. Conversely, too low a temperature results in high melt viscosity and poor fluidity, leading to fusion marks.
Thermal Degradation Risks
Raising melt temperature might help the plastic flow more easily; however, it comes with risks of thermal degradation that can significantly affect the mechanical properties of the final product. Here are some potential outcomes:
Risk | Effect |
---|---|
Reduced Mechanical Strength | Lower resistance to stress and strain |
Increased Cycle Times | Longer cooling times due to thermal retention |
Poor Surface Finish | Increased likelihood of defects like fusion marks |
For instance, I increased the melt temperature of polycarbonate (PC) from 280 – 300°C to 300 – 320°C. I noticed fewer fusion marks; however, that small win came with the risk of material degradation.
Cooling System Considerations
The mold structure and cooling system are very important for managing melt temperatures. Poorly designed cooling channels may lead to overheating or rapid cooling—both can cause unwanted fusion marks.
To ensure uniform temperature distribution, consider optimizing cooling channel layouts. Using follow-shape cooling channels allows for better temperature control which is vital in maintaining product quality.
Process Parameter Adjustments
Adjusting melt temperatures should not happen alone; it is crucial to coordinate it with other process parameters like injection pressure and speed. Raising the melt temperature can reduce injection pressures and speeds which helps with fluidity and reduces fusion marks.
For example, when raising the melt temperature of ABS material, this allowed me to decrease injection pressure by 10 – 15%, while injection speed decreased by 20 – 30%. It’s like dancing—get each step right to avoid defects such as flying edges.
Conclusion: Balancing Risks and Benefits
Working with high melt temperatures in plastic processing sometimes feels like walking a tightrope. It requires balancing temperature settings and material properties. My advice? Assess the specific traits of your materials and adjust your processing parameters carefully. By keeping these details in mind, I’ve optimized production processes effectively—you probably can too!
High melt temperatures can degrade PVC material properties.True
Excessive heating of PVC can lead to decomposition, affecting quality and releasing harmful gases.
Increasing melt temperature always improves product flow.False
While higher temperatures enhance flow, they also risk thermal degradation of materials, impacting mechanical properties.
How Can Mold Design Influence Melt Temperature Management?
Have you ever thought about how mold design affects the control of melt temperatures in manufacturing? It’s a very interesting subject that greatly affects product quality. Let’s explore the important aspects that influence this process!
Mold design impacts melt temperature management by utilizing material properties, optimizing heating, and implementing efficient cooling systems. Coordinating with injection parameters is vital for enhancing product quality and manufacturing efficiency.
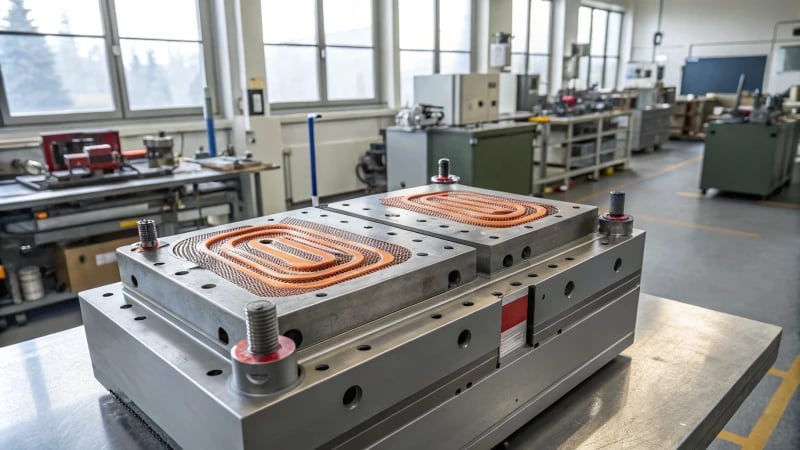
Understanding Mold Design and Material Properties
Mold design involves more than just appearance; it significantly influences melt temperature management by necessitating an understanding of the material properties involved. This impacts product quality and production efficiency. When I began working in mold design, I was surprised to learn how the choice of material and its properties can really change the final product. It is similar to cooking—picking the right ingredients is vital to avoid a bad dish!
Different plastic materials come with unique melt temperature ranges. For example, polystyrene (PS) typically melts between 180 – 280°C, while polypropylene (PP) ranges from 200 – 280°C.
When adjusting the melt temperature, it’s crucial to ensure that it remains within the permissible range to prevent any degradation of material properties. Heat-sensitive materials like polyvinyl chloride (PVC) require careful monitoring; exceeding its narrow melt range can lead to decomposition and the production of harmful gases such as hydrogen chloride. This not only compromises product quality but can also corrode equipment.
Material | Melt Temperature Range (°C) | Notes |
---|---|---|
Polystyrene | 180 – 280 | Ensure to maintain within range to avoid issues |
Polypropylene | 200 – 280 | Adjustments affect flow and quality |
Polyvinyl Chloride | Narrow range | High risk of degradation if overheated |
Polycarbonate | 280 – 320 | Higher temperatures reduce fusion marks |
Appropriately Increase the Melt Temperature
Increasing the melt temperature can reduce the viscosity of plastics, allowing the melt to flow smoothly into the mold cavity. For instance, raising the melt temperature of polycarbonate (PC) from 280 – 300°C to 300 – 320°C effectively minimizes fusion marks. However, one must be cautious—excessively high melt temperatures may lead to thermal degradation, which negatively impacts mechanical properties and increases cooling times.
It’s essential to balance this increase with product quality and production efficiency to prevent defects while ensuring optimal flow.
Consider the Mold Structure and Cooling System
The design of the mold and its cooling system plays a pivotal role in managing melt temperatures. Improperly designed cooling channels can lead to rapid local temperature drops, which in turn create fusion marks on the final product.
Optimizing the cooling channel layout is crucial for ensuring uniform temperature distribution throughout the mold. For example, using follow-shape cooling channels can enhance heat transfer efficiency by fitting closely to mold cavity shapes, thereby controlling cooling rates more accurately.
Coordination with Other Process Parameters
Melt temperature adjustments should always be coordinated with other process parameters such as injection pressure and speed. For example, increasing melt temperature allows for a reduction in injection pressure by 10 – 15% and injection speed by 20 – 30% for materials like ABS. This reduction helps mitigate fusion marks caused by excessive pressure or speed during injection.
Additionally, holding time and pressure may need adjustment; higher melt temperatures can change material shrinkage rates, necessitating careful control of holding pressure to maintain dimensional accuracy and reduce potential defects.
For further insights on optimizing these parameters, consider exploring resources that discuss melt temperature management3 in detail.
Mold design affects melt temperature management significantly.True
The design of the mold directly influences how melt temperatures are managed, impacting material properties and product quality.
Higher melt temperatures always improve product quality.False
Excessively high melt temperatures can lead to thermal degradation, negatively affecting product quality.
What Additional Parameters Should Be Considered Alongside Melt Temperature?
Diving into the world of plastics can be confusing. People often focus on melt temperature details. But there is so much more to discover! Other factors also affect product quality. Some factors really improve the final product.
In plastics processing, optimize melt temperature by considering material properties, mold design, cooling systems, and coordinating with injection speed and pressure.
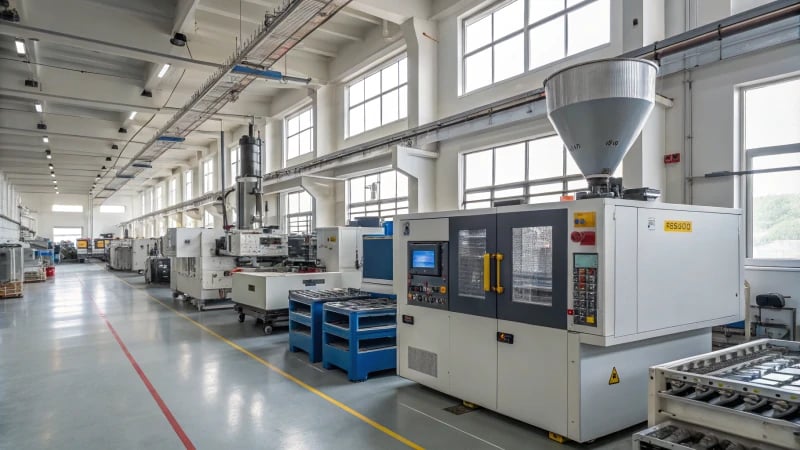
Understanding Material Properties
Each type of plastic has its own personality, especially regarding melt temperature. For example, polystyrene (PS) generally melts between 180 – 280°C, while polypropylene (PP) usually ranges from 200 – 280°C. When I first adjusted melt temperatures without these specific ranges, I faced challenges. Material degradation was a real problem. I remember a project using polyvinyl chloride (PVC). Its narrow melt temperature range required careful management to avoid issues such as decomposition that can produce harmful gases like hydrogen chloride. Proper management ensures the melt viscosity is optimal to avoid defects like fusion marks.
Temperature Range | Material Type | Effect of Increase |
---|---|---|
180 – 280°C | Polystyrene | Flow improvement |
200 – 280°C | Polypropylene | Flow improvement |
Narrow Range | Polyvinyl Chloride (PVC) | Avoids decomposition |
Effect of Increasing Melt Temperature
Raising the melt temperature feels like giving the plastic extra energy. This increase lowers viscosity, allowing it to flow smoothly into mold cavities. I recall a project where we increased the melt temperature of polycarbonate (PC) from 280 – 300°C to 300 – 320°C. The result was impressive; there was a significant decrease in fusion marks and our final product appeared cleaner and very professional.
However, too high a melt temperature can lead to thermal degradation. Balancing quality and efficiency is crucial; it’s a delicate dance.
Mold Structure and Cooling System Considerations
Mold design is critical. I remember a time with poorly designed cooling channels that caused rapid local temperature drops and defects like fusion marks. Optimizing these channels changed everything; uniform temperature distribution across the mold has saved countless hours of rework.
Coordination with Other Process Parameters
Adjusting melt temperature isn’t a solo task; it needs coordination with parameters like injection pressure and speed. In my experience, raising the melt temperature of ABS material required reducing injection pressure by 10 – 15% and lowering speed by 20 – 30%. This careful calibration avoided pesky fusion marks and prevented defects like flying edges.
Parameter Change | Action Required | Effect on Product Quality |
---|---|---|
Melt Temperature Up | Reduce Injection Pressure | Prevents fusion marks |
Melt Temperature Up | Reduce Injection Speed | Avoids defects |
Adjust Holding Time | Ensure Dimensional Accuracy | Reduces shrinkage issues |
Plus, holding time and pressure adjustments are equally important since higher melt temperatures change material shrinkage behavior. Correct adjustments keep dimensional accuracy while minimizing defects from temperature changes.
Polystyrene melts between 180 - 280°C.True
This claim is true as polystyrene's melt temperature range is specifically stated in the context.
Increasing melt temperature always improves product quality.False
This claim is false; excessively high temperatures can lead to thermal degradation and affect quality negatively.
Conclusion
Learn how to adjust melt temperature in injection molding effectively to reduce fusion marks by understanding material properties, optimizing mold design, and coordinating with other processing parameters.
-
Discover how material properties influence melting processes for better production outcomes. ↩
-
Explore the latest mold design techniques that optimize melt temperatures for various materials. ↩
-
Discover comprehensive strategies for optimizing melt temperature management in injection molding processes to enhance product quality. ↩