Picking the right injection speed really improves your plastic molding process. Precision and efficiency work together perfectly.
Ideal injection speed in plastic molding depends on factors like how fluid the material is, the mold’s structure and what the product requires. For instance, materials such as polypropylene allow quicker speeds due to their easy flow. In contrast, heat-sensitive materials like PVC need slower speeds. The gate’s size and type, along with specific product needs, also affect speed settings.
I remember when I first needed to find the right injection speed for a new job. The material was polypropylene. This material moves very smoothly. This smoothness let us raise the speed to 300 mm/s with no problems. PVC presented a different challenge. PVC heats up quickly. We had to slow down to stop it from breaking down. Materials convey their unique nature through how they flow. Getting this right is vital.
Then there is the mold. Once, I worked on something with a big gate. This size let us keep a higher speed and really improved production. But with tiny gates, like pinpoint ones, slowing down was necessary to avoid mistakes. Each choice felt like solving a puzzle. Puzzle-solving is crucial for producing efficiently.
These parts combine in interesting ways, forming the final product’s quality. Understanding and adjusting these details have become natural to me over time. Skills grow with each task.
Polypropylene allows faster injection speeds.True
Polypropylene's good fluidity supports higher injection speeds.
PVC requires faster injection speeds than polypropylene.False
PVC is heat-sensitive, necessitating slower injection speeds.
How Do Material Characteristics Affect Injection Speed?
Ever experienced a moment when a tiny detail leads to a huge change? That’s the wonder of injection speed in molding. Everything revolves around the material’s unique character!
Material traits such as flow, heat sensitivity and molecule arrangement influence how quickly injection happens. Materials that flow easily probably cope well with faster speeds. Very sensitive to heat or thick materials often require slower speeds to prevent problems.
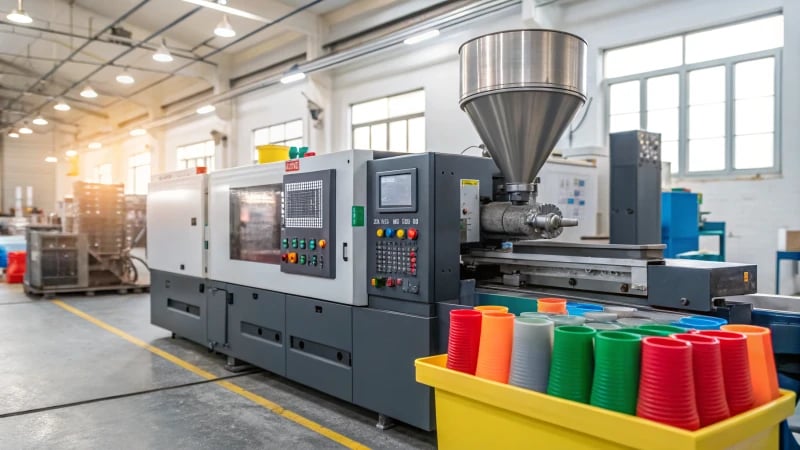
Fluidity of Materials
Let me take you back to when I started working with various plastics. Watching polyethylene (PE) and polypropylene (PP) rush into molds at super-fast speeds, between 100 to 300 mm/s, felt thrilling. It was like a speedy race where quickness didn’t just win – it meant molds filled perfectly every time.
But some were tricky – engineering plastics like polycarbonate (PC) and polyphenylene ether (PPO). Their challenging nature required slowing things down to 30 to 100 mm/s to prevent heat build-up that could ruin everything. I learned when a batch of optical lenses developed stress marks because of my impatience. Rushing them didn’t help. Patience with these materials is really important.
Heat Sensitivity Considerations
I still remember my experience with polyvinyl chloride (PVC). Dealing with it was like handling a moody artist. If the temperature was off, it decomposed. Keeping the speed between 20-60 mm/s was crucial. Continuous monitoring felt like walking on a tightrope.
Influence of Mold Structure
The mold’s design also plays a big role in determining the optimal injection speed1. In one project with large gates, speed could go up to 200 mm/s, which was very exciting! But with small gates? Slow and steady was the way to go, between 30-80 mm/s to avoid surprises like surface blemishes.
Product-Specific Requirements
Every product presents its own challenge. For high-quality finishes, keeping speeds at 50-150 mm/s means no flow marks appear. Precision parts demand careful speed control to ensure perfection without stress marks.
Working with these materials taught me that knowing their quirks isn’t just about preventing defects; it’s about mastering the art of molding.
Material Type | Typical Injection Speed (mm/s) |
---|---|
Polyethylene (PE) | 100-300 |
Polypropylene (PP) | 100-300 |
Polycarbonate (PC) | 30-100 |
Polyphenylene Ether (PPO) | 30-100 |
Polyvinyl Chloride (PVC) | Heat Sensitive: 20-60 |
Polyethylene can be injected at speeds up to 300 mm/s.True
Polyethylene has high fluidity, allowing fast injection speeds between 100-300 mm/s.
PVC requires an injection speed of over 100 mm/s.False
PVC is heat sensitive, requiring slower speeds between 20-60 mm/s to prevent decomposition.
How Does Mold Structure Impact Injection Speed?
Have you ever thought about how changing mold designs might improve your injection molding process a lot?
Mold structure is very important in deciding injection speed. Gate size, runner design and material properties influence it. Adjusting these details improves flow efficiency. Defects decrease and production quality increases. This really matters. Quality becomes better overall.
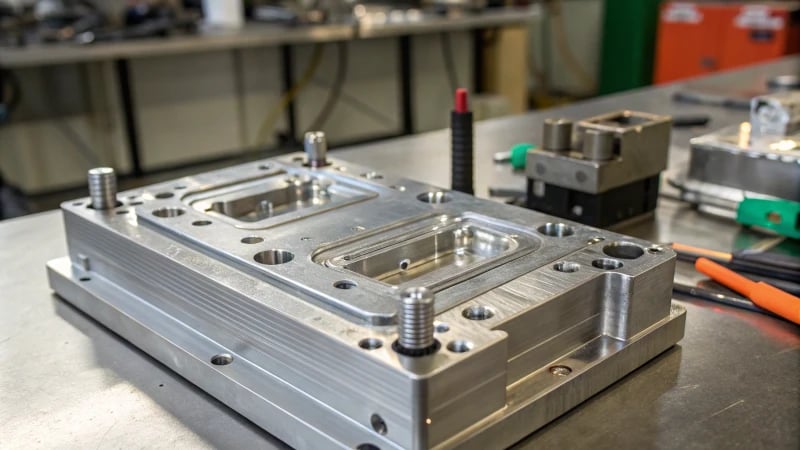
When I began working with molds, how they shaped injection speed puzzled me. My first major project involved molding a complex plastic part for a gadget. I soon discovered that small tweaks in mold design hugely impacted production speed and quality.
Gate Size and Type
Gates matter. Imagine selecting the right door for your house. Big gates, like direct or side gates, handle fast flows well, usually allowing speeds of 80-200 mm/s. Picture water shooting through a firehose – fast and effective! Conversely, small gates like pin-point ones need slower handling at 30-80 mm/s to prevent messy surface issues. Balance is key here.
Runner System Design
Consider the runner system design. I once adjusted a runner design for a tricky plastic. Large, smooth runners are like a speedy highway for molten plastic, allowing it to travel at 100-300 mm/s with little resistance. Narrow or rough runners move slower at 40-120 mm/s to avoid pressure issues and uneven filling. Think of a winding country road – slow and steady wins here.
Runner Type | Speed Range (mm/s) |
---|---|
Large, Smooth | 100-300 |
Narrow, Rough | 40-120 |
Material Characteristics
Materials are crucial! Compare pouring honey to pouring water. Plastics like polyethylene (PE) flow like water, managing fast speeds of 100-300 mm/s smoothly. Others, like polycarbonate (PC), act like honey – thicker and requiring slower speeds of 30-100 mm/s to prevent overheating and damage.
Product Requirements
Product needs also play a role. Achieving a perfect finish demands moderate speeds (50-150 mm/s) to prevent marks, while precise parts need controlled speeds (40-100 mm/s) for accuracy.
Together, these factors fit like puzzle pieces, optimally setting speeds and improving production effectiveness. If curiosity strikes about these elements, explore more about mold design and injection molding2.
Large gates allow higher injection speeds.True
Large gates handle high melt flow rates efficiently, allowing 80-200 mm/s.
Narrow runners permit faster injection speeds.False
Narrow runners require reduced speeds (40-120 mm/s) to avoid pressure buildup.
Why Are Product Requirements Critical in Determining Injection Speed?
Have you ever thought about how speed alone affects the whole injection molding process? Speed is very important.
Product requirements are key in deciding injection speed. They affect the choice of materials, mold design and how the final product looks. Matching injection speed with these needs may really increase production efficiency. Top product quality probably depends on this alignment. Quality is important.
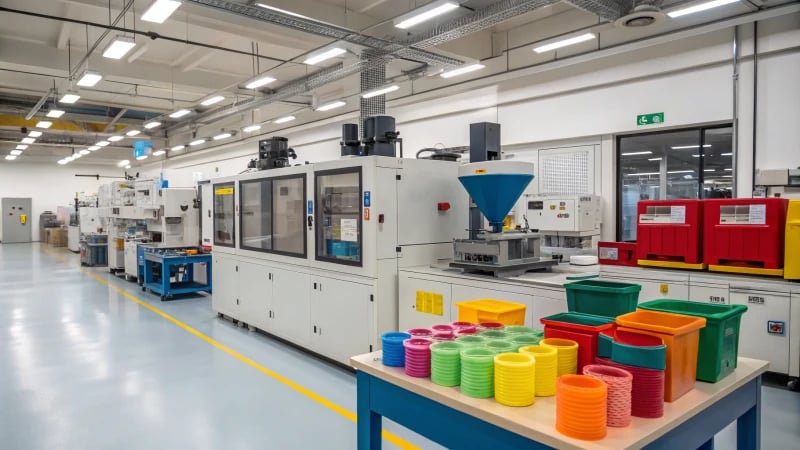
The Role of Material Characteristics
In the world of mold work, material and speed perform a delicate dance. Early days with polyethylene (PE) and polypropylene (PP) were a learning journey. These materials are very fluid. We increased speed between 100 and 300 mm/s. Watching the molds fill without problems felt magical. These plastics let us go a little faster, keeping quality high.
Material Type | Fluidity | Recommended Speed (mm/s) |
---|---|---|
Polyethylene (PE) | Good | 100-300 |
Polypropylene (PP) | Good | 100-300 |
However, polycarbonate (PC) and polyphenylene ether (PPO) told a different story. They flow poorly, so we slowed down to avoid problems like shear heat. Rushing wasn’t an option. Patience became very important.
Material Type | Fluidity | Recommended Speed (mm/s) |
---|---|---|
Polycarbonate (PC) | Poor | 30-100 |
Polyphenylene ether (PPO) | Poor | 30-100 |
Mold Structure Considerations
The mold itself plays a silent role in speed. Bigger gates such as direct or side gates support speeds from 80 to 200 mm/s. It unlocked new levels, like a game! But small gates needed gentleness. Slower speeds prevented surface problems.
Designing the runner system was an interesting puzzle. A good system works like a smooth highway for the melt, allowing faster speeds because resistance is low. Well-designed runner systems shape your speed approach.
Optimizing runner systems3 plays a critical role in managing injection speed effectively.
Importance of Product Specifications
Product needs guide each of my choices. For example, automotive interiors need high beauty; moderate speeds between 50 and 150 mm/s avoid flow marks.
In precision work, like medical devices, careful speed and pressure adjustment becomes vital to maintain exact shapes for product strength.
Product Requirement | Critical Speed Range (mm/s) |
---|---|
Aesthetic Quality | 50-150 |
Dimensional Accuracy | Careful Adjustment Needed |
Navigating injection molding involves a mix of art and science. Each decision affects the outcome, leading to excellent processes and top-quality results.
Polyethylene can be injected at 100-300 mm/s.True
Polyethylene has good fluidity, allowing high-speed injection.
Small gates allow higher injection speeds than large gates.False
Small gates require reduced speeds to prevent surface defects.
How Can Optimizing Injection Speed Improve Production Efficiency?
Do you ever think how a tiny change in injection speed might completely change your production line?
Improving injection speed in plastic manufacturing matches with the material’s nature, mold design and what the product needs. This increases efficiency and keeps quality high. Quick speeds increase production. Slow speeds help avoid defects in tricky materials.
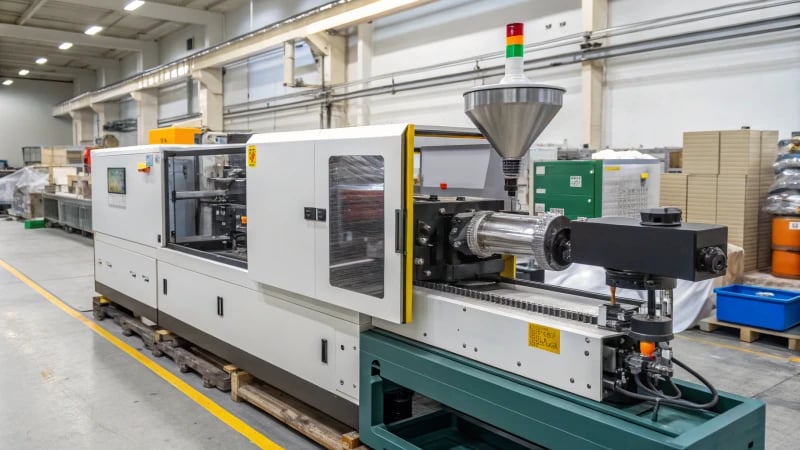
Material Characteristics Impact
I remember when I first understood how important it was to know the material’s nature. Working with polyethylene (PE) and polypropylene (PP)4, which flow well, taught me that increasing speed improves efficiency without losing quality. Filling a mold quickly is like pouring syrup on pancakes neatly. This happens at speeds between 100 and 300 mm/s.
However, working with engineering plastics like polycarbonate (PC) is a slower process. It’s like getting honey into a narrow jar, where patience helps. Slowing down to about 30 to 100 mm/s keeps everything clear and strong for delicate uses like lenses.
Mold Structure Factors
Mold design is quite interesting. Large gates act like wide doors, letting the melt move quickly at speeds up to 200 mm/s with ease. It’s similar to a river flowing through a valley. With smaller gates, caution is necessary. It’s like threading a needle, where slow speeds prevent surface marks.
Example Table: Gate Types and Recommended Speeds
Gate Type | Recommended Speed (mm/s) |
---|---|
Direct/Side Gate | 80-200 |
Pinpoint Gate | 30-80 |
A good runner system really matters. When it is smooth and well-planned, it’s like driving on a newly paved road – travel faster with no problems.
Product Requirements and Quality Control
Sometimes, the final product must look perfect, like with car interiors5. Medium speeds (50-150 mm/s) help achieve smooth finishes, avoiding ugly marks.
For precise parts, like those in medical tools, adjusting speed is important to keep accuracy and avoid stressing the material. This balance keeps products both functional and attractive.
Perfecting these details, I have observed how adjusting injection speed changes efficiency and quality in production. For more advice on improving your injection molding, look at modern manufacturing ideas and mold design advances.
Polyethylene requires injection speeds of 100-300 mm/s.True
Polyethylene's excellent fluidity allows for faster injection speeds.
Small gates can handle speeds of 80-200 mm/s.False
Small gates require slower speeds to prevent surface defects.
Conclusion
Injection speed in plastic molding is determined by material fluidity, mold structure, and product requirements, balancing efficiency and quality to prevent defects during production.
-
Understand how mold features impact the choice of injection speed for optimal product quality. ↩
-
This link offers detailed information on mold design principles, essential for optimizing injection molding processes. ↩
-
Understanding the impact of runner design can help optimize speed settings and improve molding outcomes. ↩
-
Explore how these materials’ fluidity allows for faster injection speeds, enhancing production efficiency. ↩
-
Understand how moderate injection speeds help achieve high-quality finishes for automotive parts. ↩