Curious about how injection molding machines create hollow parts? You’re in the right place! Let’s dive into this fascinating world together!
Injection molding machines produce hollow parts primarily through blow molding, gas-assisted injection molding, and foaming injection molding. Each method is chosen based on the design, material, and manufacturing requirements of the part, offering versatility and efficiency.
Understanding these basic methods is just the beginning. Let’s delve deeper into each technique to see how they cater to diverse industrial needs!
Injection molding machines can produce hollow parts.True
Injection molding machines use methods like blow molding to create hollow parts.
What is Blow Molding and How Does It Work?
Curious about blow molding and its impact on modern manufacturing? Discover the magic behind creating hollow parts.
Blow molding is a manufacturing process used to create hollow plastic products by expanding a preform in a mold using air pressure. This technique is ideal for producing items like bottles and containers efficiently and consistently.
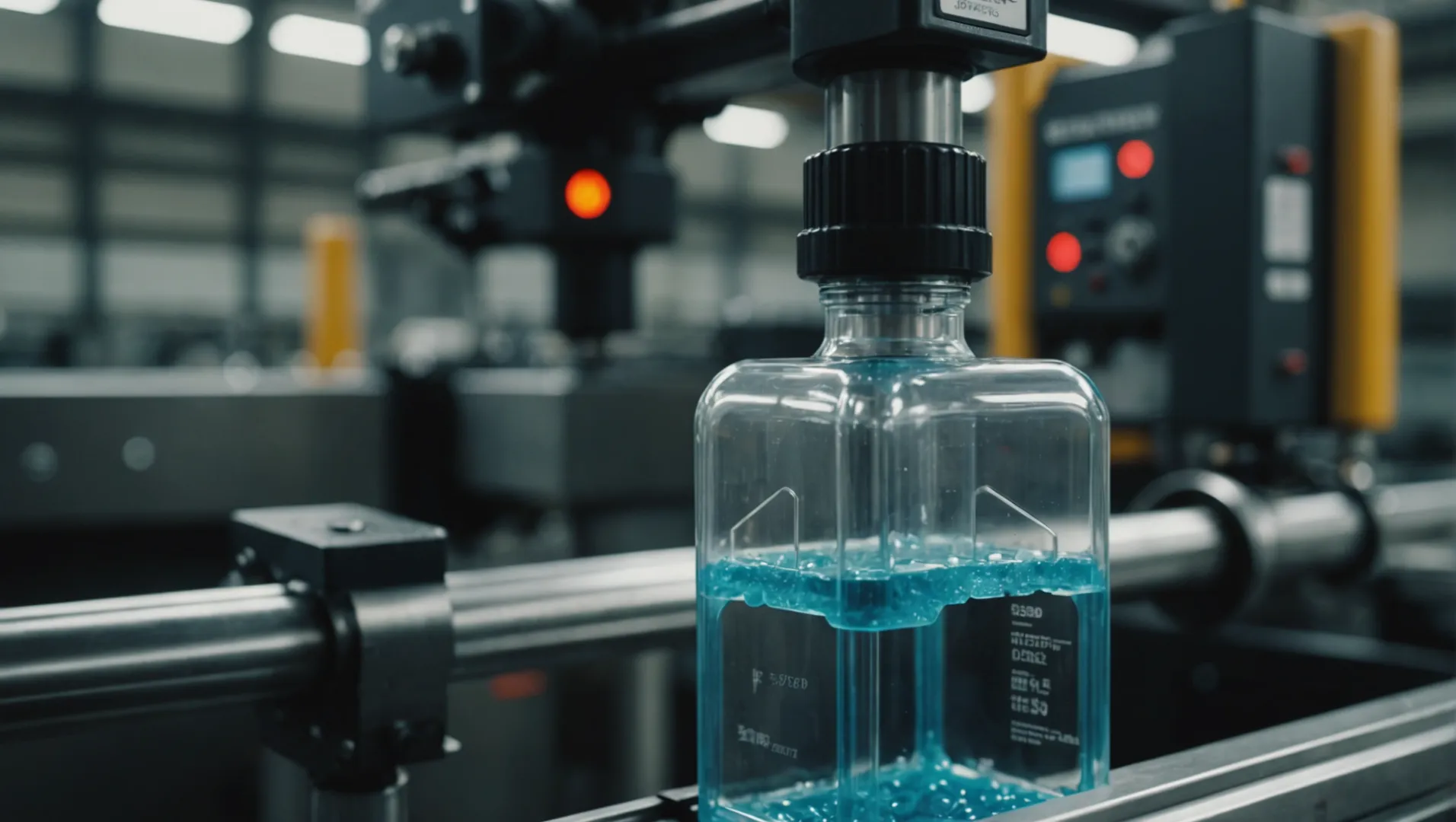
Understanding Blow Molding Process
Blow molding begins with the creation of a preform, typically produced through injection molding. This preform resembles a test tube and is made of plastic. Once the preform is ready, it is heated and placed inside a mold.
Air pressure is then applied, forcing the preform to expand and take the shape of the mold’s inner cavity. The result is a hollow part with uniform wall thickness. This method’s precision makes it highly suitable for producing items such as plastic bottles, fuel tanks, and other containers.
Types of Blow Molding
-
Extrusion Blow Molding
This is the most common type of blow molding used in industries. A plastic tube, known as a parison, is extruded into a mold. The mold closes, cutting off the parison, and air is blown into it to create the hollow product.
-
Injection Blow Molding
Used primarily for small, precision items like medicine bottles, this method involves injecting molten plastic into a preform cavity before blowing.
-
Stretch Blow Molding
Often used for making PET bottles, this process involves stretching the plastic before blowing, which improves the material’s strength and clarity.
Benefits of Blow Molding
- Efficiency in Production: Blow molding allows for rapid production cycles, significantly reducing lead times.
- Versatility in Design: The ability to create complex shapes and sizes meets various industry demands.
- Cost-Effectiveness: By optimizing material usage and minimizing waste, blow molding reduces production costs.
Industrial Applications of Blow Molding
Blow molding’s versatility extends its use across numerous industries:
Industry | Application |
---|---|
Automotive | Fuel tanks, ducts |
Packaging | Bottles, containers |
Consumer Goods | Toys, household items |
Medical | IV bags, medical bottles |
In conclusion, understanding blow molding techniques1 provides insight into how various sectors benefit from efficient and innovative manufacturing processes. Each type of blow molding offers unique advantages tailored to specific production needs.
Blow molding creates solid plastic products.False
Blow molding creates hollow, not solid, plastic products.
Stretch blow molding improves material strength.True
Stretching before blowing enhances the material's strength and clarity.
How Does Gas-Assisted Injection Molding Improve Part Production?
Gas-assisted injection molding is revolutionizing part production. But how exactly does it make a difference?
Gas-assisted injection molding enhances part production by reducing material use, minimizing cycle times, and improving structural integrity. This technique introduces high-pressure gas into molten plastic, creating hollow sections that maintain strength while using less material.
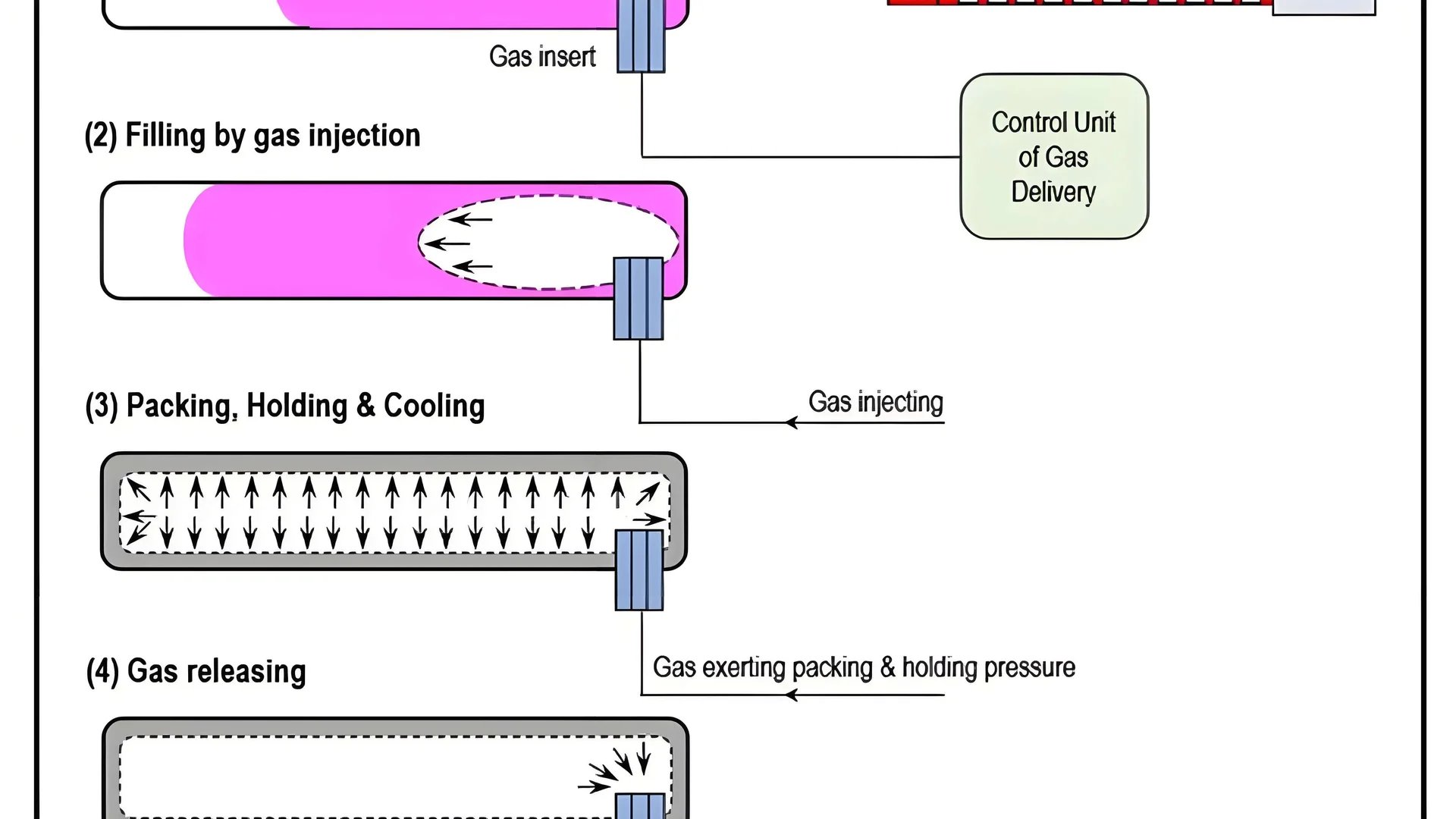
The Gas-Assisted Injection Molding Process
Gas-assisted injection molding involves injecting high-pressure gas into the molten plastic inside the mold. This process creates hollow sections within the part, which significantly reduces the amount of plastic required. The gas moves through the molten plastic, pushing it against the mold walls and forming a thin, hollow section that retains strength and rigidity.
This method is particularly effective for large parts with complex geometries that require consistent wall thickness and structural integrity. By creating a uniform distribution of material, this process minimizes sink marks and warpage, enhancing the overall quality of the final product.
Advantages Over Traditional Methods
Compared to traditional injection molding, gas-assisted methods offer several key advantages:
- Material Efficiency: By creating hollow sections, this technique uses significantly less plastic, leading to cost savings and reduced waste.
- Reduced Cycle Times: Faster cooling times are achieved due to the thinner walls, speeding up the entire production process.
- Enhanced Part Quality: Improved surface finish and reduced defects such as sink marks result from uniform pressure distribution during molding.
Applications and Examples
Gas-assisted injection molding is widely used in industries requiring large and complex parts, such as automotive and consumer goods. For example, automotive manufacturers use this process to create lightweight yet sturdy components like handles and panels. Consumer products like furniture and appliance parts also benefit from the strength and cost-effectiveness offered by gas-assisted methods.
Incorporating these elements into your production can lead to substantial improvements in efficiency and quality. By understanding how gas-assisted injection molding works, you can better assess its potential benefits for your specific applications. Explore more about injection molding innovations2 to stay ahead in part production advancements.
Gas-assisted molding reduces material use in part production.True
The process creates hollow sections, using less plastic.
Gas-assisted injection molding increases cycle times.False
It actually reduces cycle times by speeding up cooling.
Why Choose Foaming Injection Molding for Lightweight Parts?
When it comes to manufacturing lightweight parts, foaming injection molding stands out as an innovative solution.
Foaming injection molding is ideal for lightweight parts due to its ability to create hollow structures, reduce material usage, and enhance thermal insulation. This method involves incorporating a foaming agent into the plastic, which decomposes to generate gas during molding, forming a lightweight yet robust component.
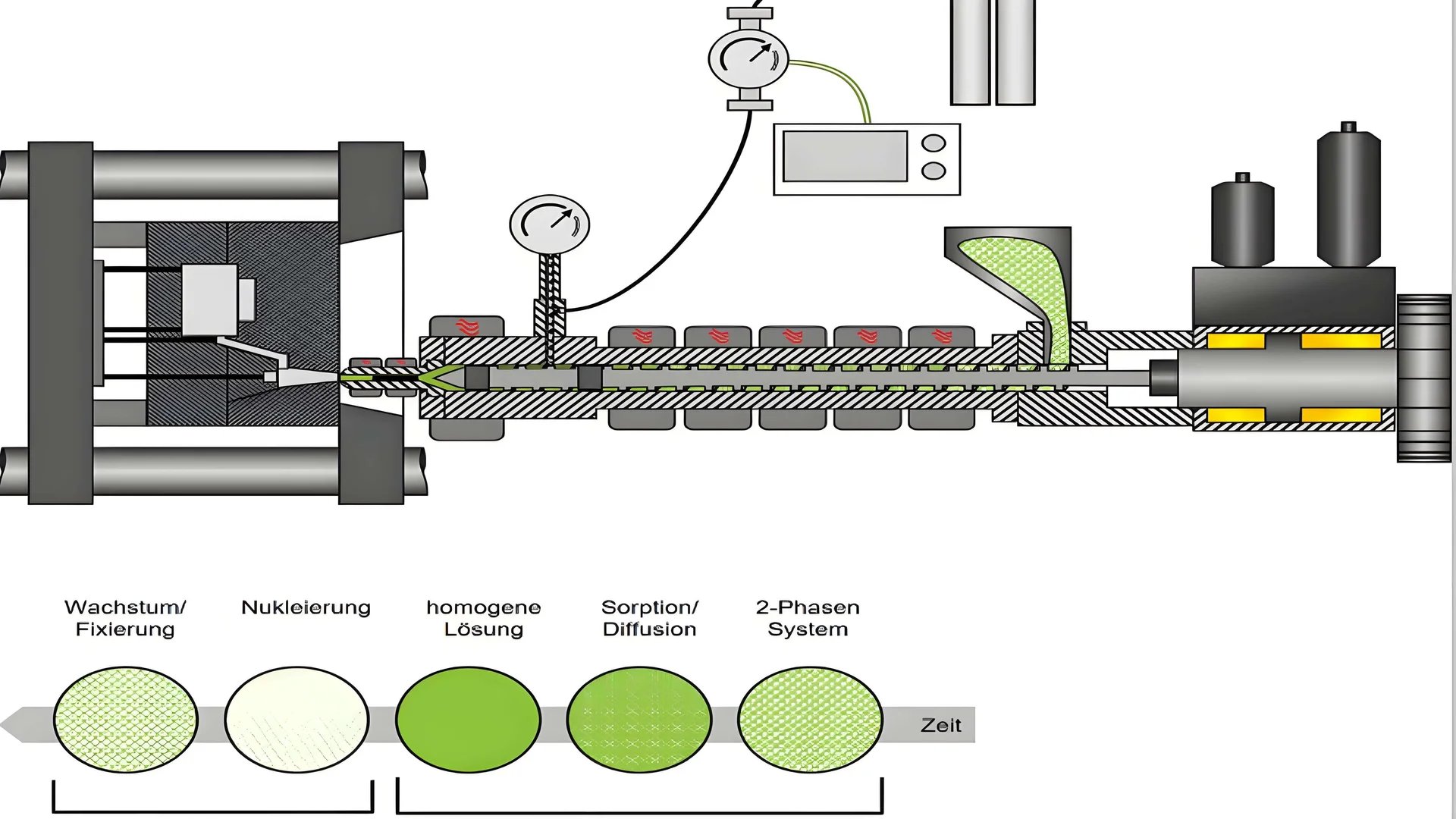
Understanding Foaming Injection Molding
Foaming injection molding integrates a foaming agent into the plastic material. During the molding process, the foaming agent decomposes, releasing gas that forms bubbles within the plastic. This results in a cellular structure that is lighter than solid plastics while maintaining structural integrity.
Benefits of Foaming Injection Molding
-
Material Efficiency: By reducing the amount of plastic used, manufacturers can achieve significant cost savings. The internal cellular structure provides volume without the weight, making it a cost-effective alternative for producing large parts.
-
Enhanced Insulation: The foam structure offers excellent thermal and sound insulation properties, which is beneficial for applications such as automotive and aerospace components.
-
Improved Mechanical Properties: Despite being lightweight, foamed parts often exhibit enhanced strength-to-weight ratios and rigidity. This makes them suitable for applications where strength is critical but weight reduction is desired.
Applications of Foaming Injection Molding
-
Automotive Industry: The demand for lightweight materials in automotive applications is rising. Foaming injection molding is used to manufacture components such as dashboards and bumpers, where reduced weight contributes to fuel efficiency.
-
Consumer Electronics: In gadgets where space and weight are premium, such as laptops and smartphones, foamed parts provide structural support without adding unnecessary bulk.
-
Construction Materials: Lightweight panels and insulation materials benefit from the properties of foamed plastics, offering durability and thermal resistance.
Comparing Foaming Injection Molding with Other Methods
Aspect | Foaming Injection Molding | Gas-Assisted Injection Molding | Blow Molding |
---|---|---|---|
Weight Reduction | High | Moderate | Moderate |
Cost Efficiency | High | Moderate | Low |
Insulation | Excellent | Poor | Moderate |
Complexity | Moderate | High | High |
Understanding these aspects helps industries choose foaming injection molding3 for its unique advantages, especially when aiming to achieve both lightweight and strong components.
Foaming injection molding uses less material than solid molding.True
The cellular structure reduces plastic usage, saving costs.
Gas-assisted molding offers better insulation than foaming molding.False
Foaming provides excellent thermal insulation, unlike gas-assisted.
What Factors Influence the Choice of Hollow Part Production Method?
Choosing the right method for producing hollow parts can greatly impact efficiency and product quality.
The choice of a hollow part production method is influenced by factors such as part geometry, material properties, cost considerations, and production volume. Understanding these factors helps in selecting the most appropriate technique, ensuring optimal performance and efficiency in manufacturing processes.
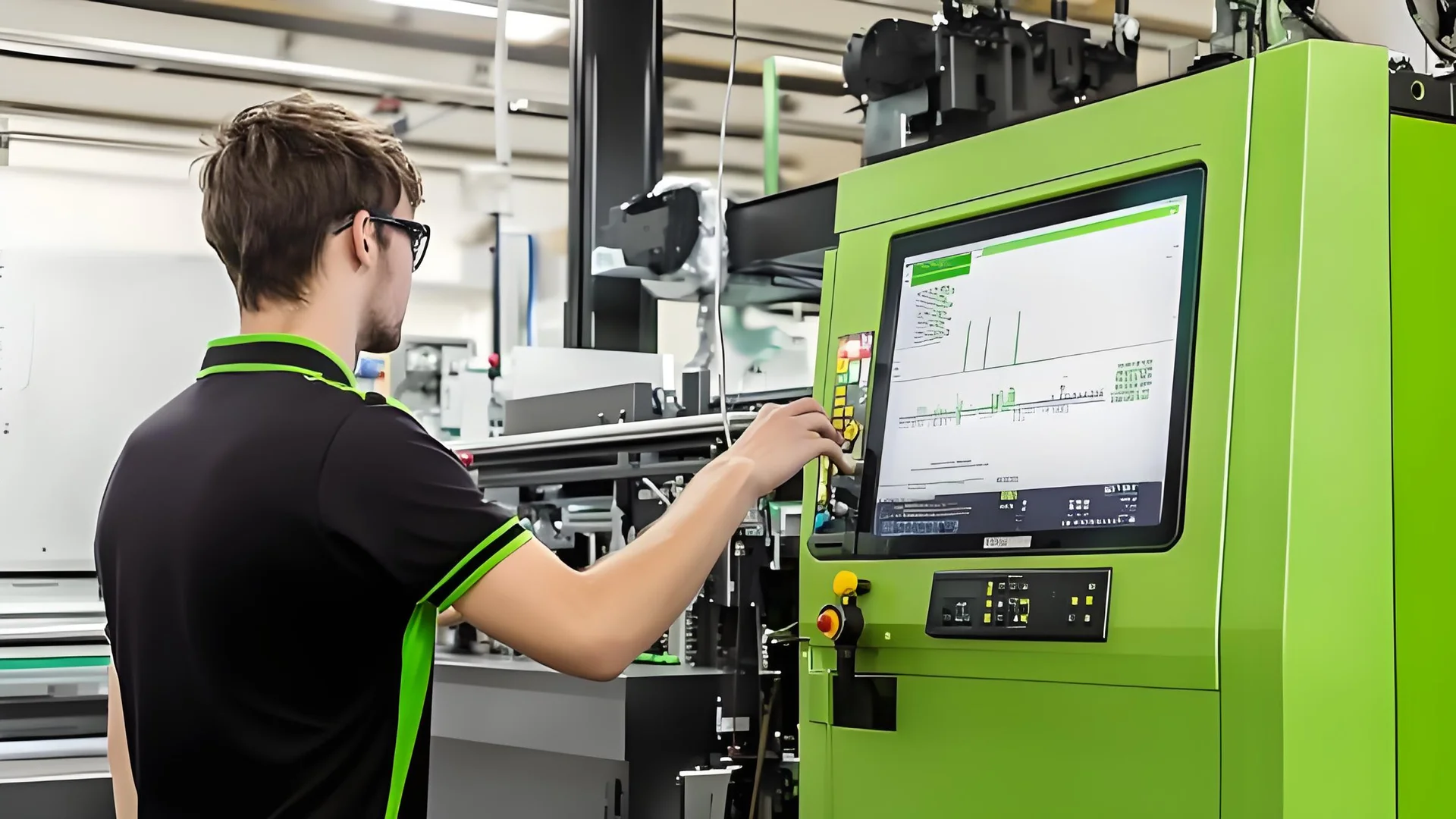
Part Geometry and Design Requirements
The shape and complexity of a part play a crucial role in determining the appropriate production method. For instance, blow molding4 is ideal for producing simple, symmetrical shapes like bottles and containers due to its efficiency in creating uniform walls. In contrast, gas-assisted injection molding excels in producing complex geometries with intricate hollow sections because it allows for precise control of material flow and gas pressure.
Material Properties and Compatibility
Different materials respond uniquely to each production method. If you’re working with thermoplastics that require high rigidity and strength, gas-assisted injection molding5 might be preferable. On the other hand, foaming injection molding is better suited for lightweight materials needing additional insulation properties. It’s crucial to match the material’s thermal and mechanical properties with the method to ensure the final product meets desired specifications.
Cost Efficiency and Resource Optimization
Budget constraints and cost-effectiveness are major considerations. Blow molding generally offers lower initial costs for large volume production runs due to its rapid cycle times and minimal material waste. However, if minimizing plastic usage is a priority, gas-assisted injection molding could prove more cost-effective despite higher upfront tooling expenses.
Production Volume and Lead Time
The scale of production significantly influences method selection. High-volume production often benefits from blow molding due to its speed and efficiency. For smaller batches or prototyping, gas-assisted injection molding might be more suitable as it offers flexibility in design changes without incurring significant retooling costs.
Method | Best For | Key Considerations |
---|---|---|
Blow Molding | Simple shapes, high volume | Uniform wall thickness, speed |
Gas-Assisted Injection | Complex designs, reduced material usage | Precision, tooling costs |
Foaming Injection | Lightweight, insulated parts | Insulation properties, material choices |
Understanding these factors is crucial for making an informed decision that balances quality, cost, and efficiency. Selecting the right method can lead to superior product performance and significant competitive advantages in the marketplace.
Blow molding is best for complex part geometries.False
Blow molding is ideal for simple, symmetrical shapes due to efficiency.
Gas-assisted injection reduces material usage in production.True
This method allows precise control, reducing material waste.
Conclusion
In understanding these methods, I feel empowered to choose the right techniques for my projects. Let’s explore further to enhance our manufacturing endeavors!
-
Explore diverse blow molding types and their industrial applications.: There are three primary types of blow molding: extrusion blow molding (EBM), injection blow molding (IBM), and injection stretch blow molding (ISBM). The … ↩
-
Stay updated with cutting-edge techniques for enhanced production efficiency.: A great innovation for injection molding is structural foam molding. This process combines injection molding and gas-assisted injection molding … ↩
-
Explore in-depth benefits and industrial applications of foaming injection molding.: Can replace many types of materials · Lighter in weight · Many available resins · High dimensional stability · Environmentally friendly · Saves … ↩
-
Explore blow molding applications for creating diverse hollow products.: Blow molding (or moulding) is a manufacturing process for forming hollow plastic parts. It is also used for forming glass bottles or other hollow shapes. ↩
-
Learn how gas-assisted techniques enhance manufacturing efficiency.: Gas assist uses pressurized gas to improve the plastic injection molding process. This Miles … ↩