I remember the first time I encountered a stubborn injection mold issue. It was frustrating, but with some patience and persistence, I learned the ropes of troubleshooting.
To troubleshoot and repair injection molds, inspect appearance, measure dimensions, and check actions. Perform targeted maintenance, including part repairs or replacements and system recalibration, to ensure optimal mold performance.
When it comes to injection molds, I’ve found that diagnosing problems is only half the battle. The real challenge—and satisfaction—comes from applying the right maintenance techniques. Whether it’s repairing a worn part or adjusting the clamping force, having a clear plan makes all the difference. Let me walk you through my process for tackling these issues efficiently.
Injection molds never develop faults over time.False
Injection molds can indeed develop faults due to wear and tear.
Appearance inspection helps diagnose mold faults.True
Visual checks can identify surface defects or damage in molds.
- 1. What Are Common Faults in Injection Molds?
- 2. How Do Appearance Inspections Help Diagnose Mold Issues?
- 3. Why Is Dimensional Accuracy Crucial in Mold Maintenance?
- 4. How do cooling and heating systems impact mold efficiency?
- 5. How Can Regular Cleaning and Lubrication Extend Mold Life?
- 6. Conclusion
What Are Common Faults in Injection Molds?
Ever faced unexpected issues with injection molds? You’re not alone! As someone who’s been knee-deep in the world of molds, I’ve seen my fair share of common faults and learned a few tricks along the way to keep things running smoothly.
Common faults in injection molds include flash, dimensional deviations, surface scratches, and cooling system failures, diagnosed through appearance inspection, dimension measurement, and checking mold actions and systems.
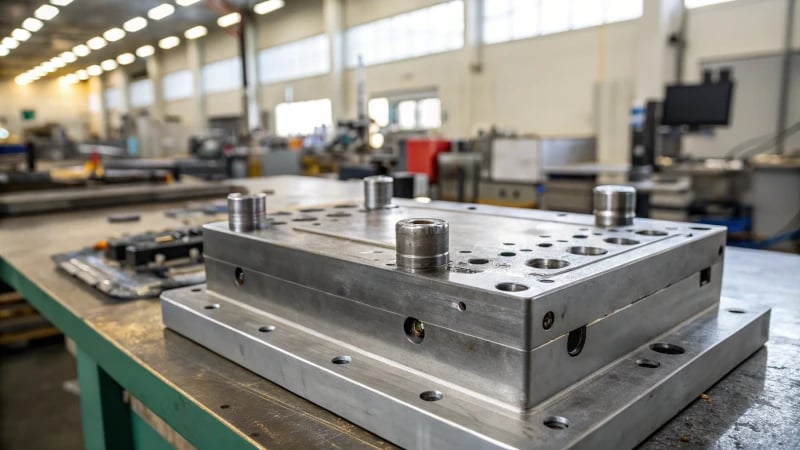
Appearance Inspection
I remember the first time I noticed flash on a molded product. It was a small plastic shell, and that pesky extra bit of plastic on the edges drove me nuts! Turns out, it was due to some looseness in the clamping mechanism. So now, during an appearance inspection1, I make sure to thoroughly check the surface for defects like flash or scratches, which could indicate damage to the cavity or core surfaces. It’s also crucial to inspect for any loose, deformed, or cracked parts.
Dimension Measurement and Precision Inspection
Measuring product dimensions is like having a reality check on your mold’s health. I once found that a product was consistently thinner than its design. After some head-scratching and measuring, it turned out to be cavity wear. Using precision tools like three-dimensional coordinate measuring machines has since become a staple in my inspection process to ensure everything is up to par.
Fault Type | Possible Causes |
---|---|
Dimensional deviation | Cavity wear |
Increased aperture | Core size reduction |
Action Inspection
Opening and closing molds is more than just part of the job; it’s an art form. I once heard a sharp friction sound that screamed for attention. It was a sign that lubrication was desperately needed between the guide pin and guide sleeve. Manually controlling the mold while listening for abnormal noises has saved me from bigger headaches down the line.
Cooling and Heating System Check
Cooling system failures can sneak up on you, leading to defects like shrinkage marks. I remember spending hours trying to figure out why the product kept warping, only to find a blocked cooling water pipeline was the culprit. Since then, checking for obstructions or leaks has been a non-negotiable step in my process.
System Type | Check Required |
---|---|
Cooling | Water leakage, flow tests |
Heating | Temperature sensor accuracy |
The heating system also requires regular checks to ensure accurate temperature readings—trust me, it saves a lot of trouble with poor plastic melt fluidity.
Diagnosing these faults efficiently is essential for high-quality production output in injection molding processes. With a keen eye and precision tools, maintaining these molds becomes less of a chore and more of an art, ultimately extending their life and improving product quality.
Flash on product edges indicates poor clamping.True
Flash occurs due to looseness in the clamping mechanism, leading to defects.
Cooling system leaks don't affect product quality.False
Leaks can cause shrinkage marks, impacting the final product's appearance.
How Do Appearance Inspections Help Diagnose Mold Issues?
Ever wondered why appearance inspections are so crucial in spotting mold issues?
Appearance inspections help diagnose mold issues by identifying visible signs like discoloration, water stains, and musty odors. Inspectors also examine structural damage and moisture levels, key for early mold detection and prevention.
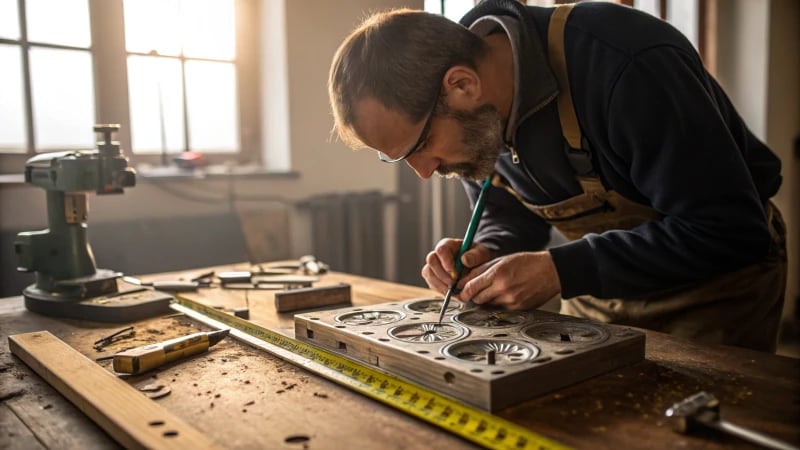
I remember the first time I noticed something off about my home. It was a faint musty smell that lingered no matter how much I aired out the rooms. That’s when I learned the power of an appearance inspection. These inspections are like having a detective on your side, hunting down mold before it becomes a nightmare.
Identifying Visible Signs of Mold
During an appearance inspection, experts look for visible signs such as discoloration2 on walls or ceilings, peeling paint, and water stains. These indicators can often hint at hidden mold growth behind surfaces. For instance, a musty odor is a telltale sign of potential mold presence.
Signs | Implications |
---|---|
Water Stains | Possible leak, potential mold growth |
Peeling Paint | Moisture intrusion, possible mold |
Musty Odor | Hidden mold growth |
Cracks in Walls | Structural issues, potential for mold |
Checking Structural Damage and Moisture Accumulation
Structural damage like cracks in walls or warped floors can indicate underlying moisture issues. Inspectors assess these areas to determine if they contribute to mold problems. A moisture meter is often used to gauge the level of moisture in materials.
Observing Environmental Conditions
Inspectors evaluate environmental conditions that promote mold growth, such as humidity levels. High humidity can create an ideal environment for mold. They might suggest using a dehumidifier or improving ventilation.
Tools Used in Appearance Inspections
Tools like flashlights, moisture meters, and thermal cameras help inspectors see beyond the naked eye. A thermal camera3 can detect temperature variations that may indicate moisture presence behind walls or under floors.
Understanding the critical role of appearance inspections in diagnosing mold issues enables you to take early action and prevent extensive damage. This knowledge is invaluable for maintaining a healthy living environment and safeguarding property value.
Musty odors always indicate mold presence.False
Musty odors suggest possible mold but can also result from other sources.
Moisture meters are used in mold inspections.True
Moisture meters assess moisture levels, crucial for identifying mold risks.
Why Is Dimensional Accuracy Crucial in Mold Maintenance?
Ever wondered why precision is such a big deal in mold maintenance? Imagine crafting a perfect key for a lock—it’s that level of accuracy that keeps things running smoothly.
Dimensional accuracy in mold maintenance is vital for defect-free production, involving regular checks to uphold mold integrity, minimize errors, and prolong mold lifespan.
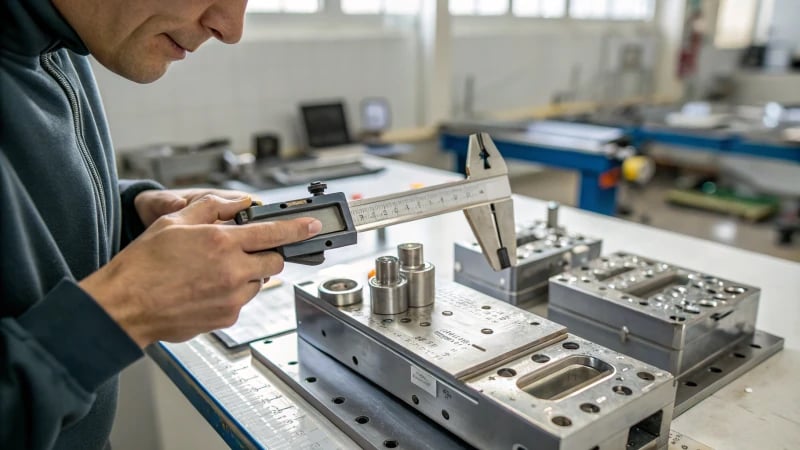
The Role of Dimensional Accuracy in Mold Functionality
Let me take you back to my early days working in a bustling mold shop. I learned firsthand how critical precision is. Picture this: you’re assembling a puzzle, but one piece doesn’t quite fit. Frustrating, right? That’s what happens when mold components are out of sync. Keeping dimensional accuracy ensures every part fits just right, avoiding gaps or misalignments that lead to production defects4. I’ve seen molds that weren’t precisely maintained produce warped or misshaped items, causing production to halt—an experience no manufacturer wants.
For instance, during the injection molding process, even slight deviations in cavity dimensions can result in products with thin walls or odd shapes. This often means higher rejection rates and spiraling costs.
Common Issues Due to Poor Dimensional Accuracy | Potential Consequences |
---|---|
Flash on products | Increased scrap rate |
Misalignment of parts | Assembly difficulties |
Warped products | Quality complaints |
Methods for Ensuring Dimensional Accuracy
Over the years, I’ve gathered some reliable methods to keep molds in top shape:
-
Regular Inspection:
I can’t stress enough the importance of frequent checks using precise tools like calipers and coordinate measuring machines (CMMs) to catch deviations early. -
Calibration and Adjustment:
Keeping things calibrated is key. Regular adjustments help molds remain within tolerance levels, avoiding nasty surprises during production. -
Surface Treatment:
Techniques such as grinding and polishing can restore slightly worn surfaces, maintaining their original dimensions. -
Replacement of Worn Parts:
When parts are beyond repair, replacing them promptly can save time and prevent bigger headaches down the line.
The Impact on Product Quality and Efficiency
Ensuring dimensional accuracy isn’t just about preserving the mold; it directly affects product quality and efficiency. Precise molds churn out products that align perfectly with design specs, ensuring customers are happy and returns are minimized.
Efficiency-wise, precise molds reduce unexpected downtime for repairs or adjustments, making production runs smoother and cost savings5 more achievable.
Troubleshooting Dimensional Deviations
When deviations sneak in, here’s how I tackle them:
- Re-measure: Double-check dimensions with advanced equipment to confirm issues.
- Inspect for Wear: Spot worn parts that might need repair or replacement.
- Analyze Process Parameters: Ensure injection molding settings aren’t causing dimensional changes.
Keeping a keen eye on dimensional accuracy isn’t just about making things work; it’s about making them work better. This focus enhances product quality and operational efficiency, leading to more reliable and cost-effective production processes.
Dimensional accuracy prevents mold misalignment.True
Accurate dimensions ensure mold components fit perfectly, avoiding misalignment.
Regular inspection is unnecessary for mold maintenance.False
Frequent inspections detect deviations, ensuring molds stay within tolerance levels.
How do cooling and heating systems impact mold efficiency?
Ever wondered how a simple tweak in your heating or cooling system could revolutionize your mold efficiency?
Cooling and heating systems maintain optimal mold temperature, crucial for injection molding efficiency. Proper management ensures consistent product quality and minimizes defects.
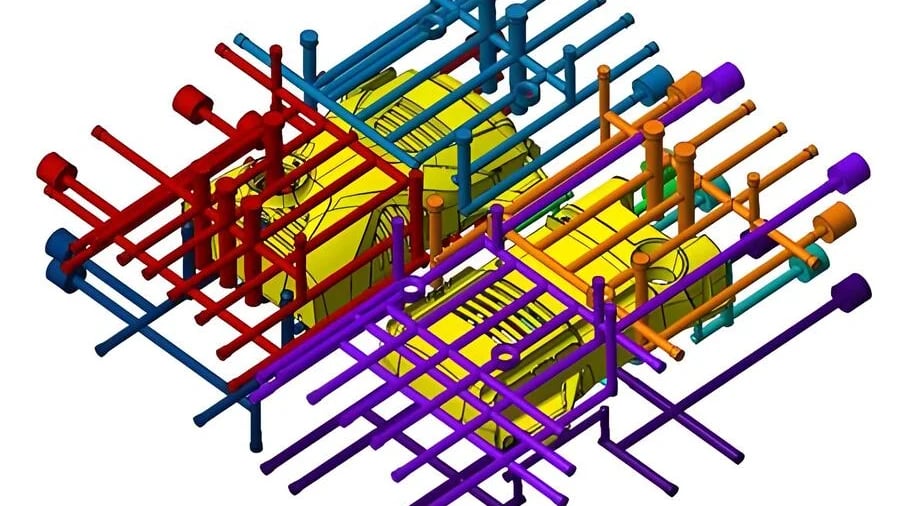
The Importance of Temperature Control
I remember the first time I realized how vital temperature control was in the injection molding process. It was during a hectic week at work when one of our major clients needed a rush order. The cooling system in our plant wasn’t up to par, and it led to products that were slightly warped. After a frantic period of adjustments and testing, I learned just how much these systems affect every little detail of the final product.
- Cooling Systems: These guys are like the unsung heroes of the injection process, managing heat to prevent warping or shrinkage. For example, during that hectic week, we found out that a blocked pipeline was causing our issues, leading to uneven cooling and warped products.
Cooling System Components | Function |
---|---|
Water Pipelines | Regulate temperature through flow |
Water Pumps | Ensure constant circulation |
Heat Exchangers | Transfer heat away from mold |
- Heating Systems: Equally important, especially in hot runner molds6, these systems ensure plastic flows smoothly by maintaining the right viscosity. I can’t count the number of times a malfunctioning heater has caused delays until we figured out the root cause.
Heating System Components | Function |
---|---|
Heating Rods | Provide uniform heat distribution |
Temperature Sensors | Monitor and adjust heat levels |
Insulation Materials | Minimize heat loss |
Diagnosing System Faults
Diagnosing faults is like being a detective. During my early days, there was this one time I spent an entire afternoon figuring out why our ejection system kept failing. Turns out, it was just a bent ejector pin! Now I know to regularly check for water seepage in cooling systems and ensure heating elements are in top shape.
- Cooling System Check: Watch out for blockages that lead to uneven cooling; they can sneak up on you and affect product quality.
- Heating System Check: Make sure heating elements are functioning properly to avoid uneven temperature distribution.
Maintenance Practices
I’ve learned that regular maintenance isn’t just a good practice—it’s essential. Cleaning, lubricating, and system checks save us from unexpected downtime more times than I can count.
- Cooling System Maintenance: Address leaks pronto by replacing faulty joints and cleaning blockages with high-pressure tools.
- Heating System Maintenance: Replace damaged heating rods or sensors without delay. Calibration is key to keeping temperatures accurate.
I’ve found that incorporating efficient maintenance practices7 into our routine not only keeps everything running smoothly but also prolongs the life of our molds. It’s a small investment for a big payoff in efficiency.
Cooling systems reduce cycle time in injection molding.True
Efficient cooling solidifies molten material quickly, reducing cycle time.
Heating systems are irrelevant in hot runner molds.False
Heating systems maintain plastic viscosity, crucial for hot runner molds.
How Can Regular Cleaning and Lubrication Extend Mold Life?
Ever wondered how keeping molds clean and well-lubricated can save time and money in manufacturing?
Regular cleaning and lubrication reduce wear, prevent damage, and enhance mold lifespan, efficiency, and product quality, while minimizing repair needs.
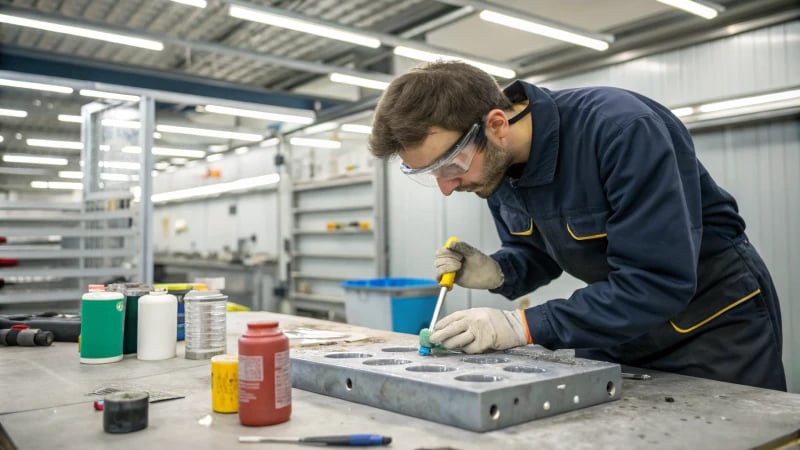
Understanding Mold Wear and Tear
Imagine you’ve invested time and resources into designing a perfect mold, only to see it wear out prematurely due to neglect. Molds endure a lot of stress from friction and residue buildup. It’s like not cleaning out the crumb tray in your toaster—eventually, it just won’t work right anymore. Regular cleaning is essential to remove stubborn plastic residues, oil stains, and other impurities that could compromise the mold’s performance. This not only prevents defects in the products but also keeps the molds running smoothly, saving you from unnecessary headaches down the line.
The Importance of Lubrication
I remember one time I skipped lubricating a mold thinking I’d save a few minutes—big mistake! Lubrication minimizes friction between moving parts, such as guide pins and sliders, reducing the risk of damage. Applying lubricants like grease or oil can make operations smoother and extend the mold’s life considerably. For example, properly lubricating guide sleeves can prevent them from wearing out quickly, thus avoiding costly replacements.
Mold Maintenance Tasks | Frequency | Tools Required |
---|---|---|
Cleaning plastic residues | After each production run | Brushes, air guns |
Lubricating guide pins | Every maintenance cycle | Lubricating oil or grease |
Checking cooling systems | Monthly | Thermometers, pressure testers |
Actionable Steps for Effective Maintenance
- Appearance Inspection: Regularly check the mold for any visible damages or defects. Spotting issues like flash8 or scratches early on can save you a lot of trouble.
- Dimension Measurement: Use precision tools to measure product dimensions against design specs. Deviations might hint at wear in the mold’s cavity or core.
- Action Inspection: Ensure smooth opening and closing of the mold by inspecting guide pins and other movable parts for signs of wear.
- Cooling System Check: Make sure cooling water pipelines are clear to prevent abnormal mold temperatures that could affect product quality.
- Lubrication: Don’t skip this step! Apply the right lubricants to reduce friction between moving parts for smoother operations.
By implementing these practices, not only do you extend the life of your molds, but you also enhance the overall efficiency of your production process. Take it from someone who learned these lessons firsthand—consistent maintenance is worth every second spent!
Explore more on proper lubrication techniques9 to ensure your molds last longer and function optimally.
Regular cleaning prevents mold defects.True
Cleaning removes residues and impurities, preventing defects in products.
Lubrication is unnecessary for mold longevity.False
Lubrication reduces friction, preventing wear and extending mold lifespan.
Conclusion
This article outlines effective troubleshooting and repair techniques for injection molds, focusing on diagnosis, maintenance practices, and the importance of precision in ensuring optimal mold performance.
-
Learn about detailed inspection techniques that help identify surface defects early, improving product quality. ↩
-
Learn how discoloration on surfaces can indicate mold presence and what steps to take next. ↩
-
Discover how thermal cameras identify hidden moisture areas, preventing potential mold issues. ↩
-
Learn about specific defects caused by inaccurate mold dimensions and how they impact production quality. ↩
-
Explore how maintaining accurate molds can lead to significant cost reductions. ↩
-
Understand how heating systems maintain plastic flow consistency, essential for high-quality production in hot runner molds. ↩
-
Discover comprehensive maintenance techniques to extend mold lifespan and enhance performance. ↩
-
Identify defects to diagnose potential mold issues early. ↩
-
Find effective lubrication methods to extend mold life. ↩