Navigating the maze of manufacturing choices is like finding the perfect recipe for success.
Injection molding and die casting both inject molten material into molds but differ in materials, suitability, and costs. Understanding these distinctions is crucial for optimizing production efficiency and product quality.
I remember the first time I had to choose between injection molding and die casting. It was like deciding between two equally delicious desserts. Each method had its own appeal and unique set of challenges. Injection molding seemed perfect for plastics, like crafting those sleek smartphone cases I often worked on, where precision and detail were non-negotiable. Meanwhile, die casting felt like the go-to choice for robust, metal components, offering strength where it mattered most.
As I delved deeper into these processes, I realized how they could complement each other, especially in hybrid designs where plastic meets metal. Balancing cost with quality, while meeting design goals, often requires blending techniques for the best results. Let’s explore how these methods can uniquely benefit your projects.
Injection molding is ideal for metal components.False
Injection molding is primarily used for plastics, not metals.
Die casting uses high-pressure to shape metal.True
Die casting involves injecting molten metal into molds under high pressure.
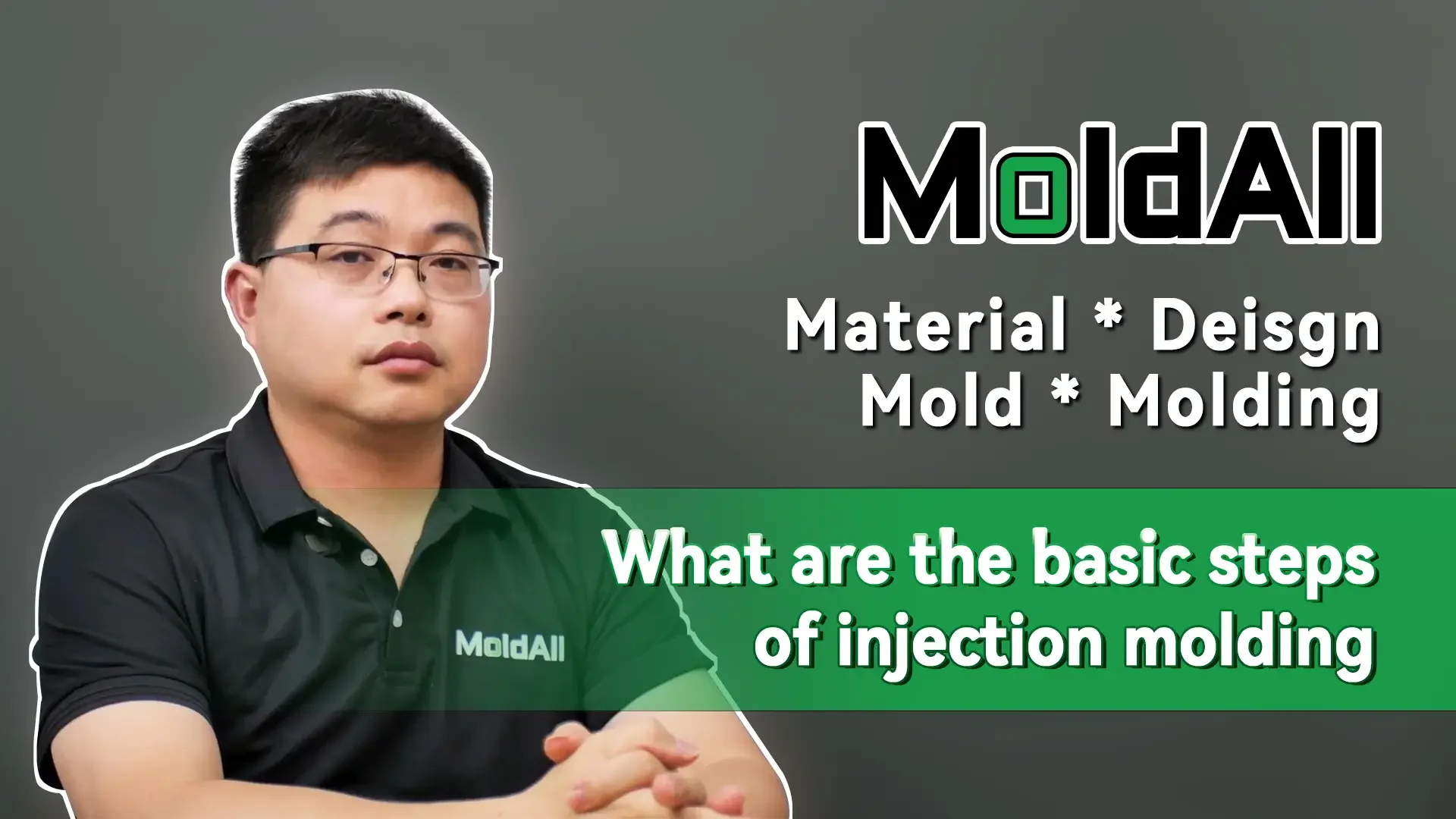
- 1. What Materials Are Used in Injection Molding vs. Die Casting?
- 2. How Can I Find the Most Cost-Effective Manufacturing Process?
- 3. How Do Cycle Times Compare Between These Methods?
- 4. How do different manufacturing techniques fit into various industries?
- 5. Can Injection Molding and Die Casting Be Used Together?
- 6. Conclusion
What Materials Are Used in Injection Molding vs. Die Casting?
Have you ever wondered what makes injection molding and die casting so different? Let’s explore the unique materials that define these manufacturing marvels.
Injection molding uses thermoplastics like polypropylene for flexibility, while die casting uses metals like aluminum for strength. Material choice depends on project needs, including cost and durability.
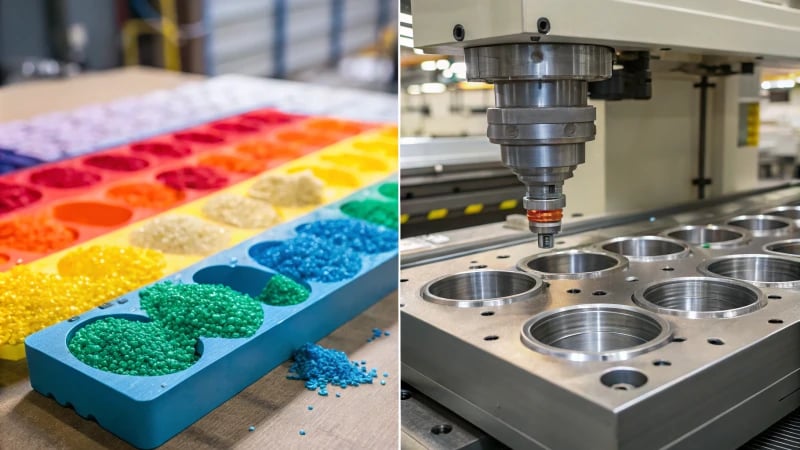
Injection Molding Materials
When I first started designing, I was amazed by how versatile injection molding could be. You see, this process uses thermoplastics, which are pretty much like the chameleons of the manufacturing1 world—they can be melted down and reshaped over and over again.
Common Thermoplastics
- Polypropylene (PP): This is the go-to for anything that needs to bend a bit without snapping. Think of it as the yoga instructor of plastics.
- Polyethylene (PE): If you’ve ever dropped your phone and heard that horrifying thud, you’ll appreciate polyethylene’s impact resistance.
- Acrylonitrile Butadiene Styrene (ABS): Remember those hard-shell suitcases? Yep, ABS is what gives them their tough-as-nails exterior.
These thermoplastics have their own charm, making them perfect for creating intricate designs with precision and a smooth finish. They’re staples in things like consumer electronics and automotive parts.
Material | Key Properties |
---|---|
Polypropylene | Flexible, fatigue-resistant |
Polyethylene | Impact-resistant |
ABS | Strong, rigid |
Die Casting Materials
On the flip side, die casting is like the heavyweight champion of manufacturing. It uses non-ferrous metals—those that won’t rust away at the first sign of moisture—by forcing them into molds at high pressure.
Common Metals
- Aluminum: Light as a feather and doesn’t mind getting wet—perfect for when you need something lightweight yet sturdy.
- Zinc: Think of zinc as that dependable friend who always shows up on time. It’s got excellent dimensional stability.
- Magnesium: The athlete of metals, boasting a fantastic strength-to-weight ratio.
These metals are all about strength and thermal conductivity, making them ideal for automotive parts and electronic housings.
Material | Key Properties |
---|---|
Aluminum | Lightweight, corrosion-resistant |
Zinc | Dimensionally stable |
Magnesium | High strength-to-weight ratio |
Comparison of Material Properties
So, how do you choose between these two? Here’s where it gets interesting:
- Durability: If you need something to last a lifetime, die-cast metals might be your best bet.
- Weight: For projects where every gram counts, thermoplastics could be your hero.
- Cost: Planning for a large production run? Thermoplastics often win the cost battle.
Ultimately, matching these properties with your project goals2 and constraints can drastically affect the performance and cost-efficiency of your final product. It’s all about finding that sweet spot between what’s needed and what’s practical. For even more tailored insights into material selection3, consider diving into industry-specific requirements—you’d be surprised how much they can vary across fields like automotive versus consumer electronics.
Injection molding uses thermoplastics like ABS.True
ABS is a common thermoplastic used in injection molding for its strength.
Die casting primarily uses ferrous metals.False
Die casting uses non-ferrous metals like aluminum, zinc, and magnesium.
How Can I Find the Most Cost-Effective Manufacturing Process?
Navigating the maze of manufacturing costs can be daunting, but finding the right process is like uncovering hidden treasure. Let’s explore how to maximize efficiency while keeping expenses in check.
To find the most cost-effective manufacturing process, evaluate material costs, labor, production volume, and quality standards. Compare various methods to identify the optimal choice for each project.
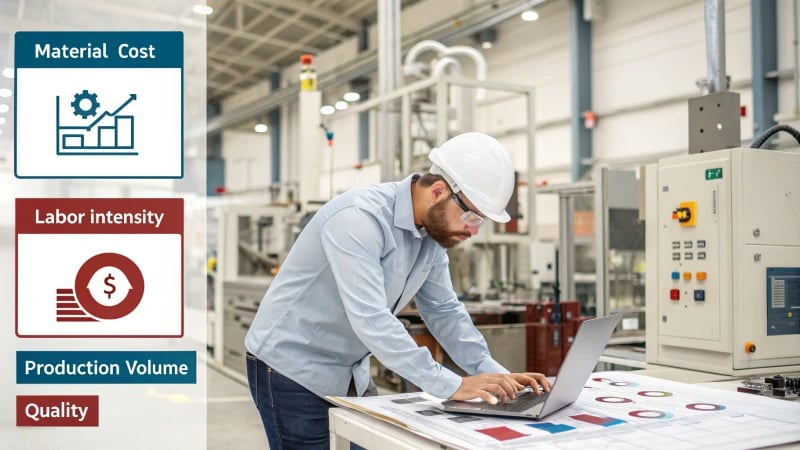
Evaluating Cost-Effectiveness in Manufacturing
When it comes to manufacturing, balancing cost with quality isn’t just a task—it’s an art form. I’ve learned that what might seem like a minor tweak can make a world of difference in the long run. For instance, injection molding4 often shines when we’re talking big numbers due to its lower cost per unit.
Comparing Manufacturing Processes
I’ve spent countless hours weighing the pros and cons of various manufacturing processes. Here’s a little cheat sheet I’ve put together over the years:
Process | Material Costs | Labor Costs | Speed | Quality |
---|---|---|---|---|
Injection Molding | Low | Medium | Fast | High |
CNC Machining | Medium | High | Slow | Very High |
3D Printing | High | Low | Medium | Medium |
Each of these processes has its unique charm. For instance, CNC machining5 is my go-to when precision is key, especially for those projects where quality can’t be compromised.
Real-World Examples
In my work with consumer electronics, I’ve seen firsthand how the right process choice can drastically affect our bottom line. Imagine discovering that blending injection molding with CNC machining for plastic component production6 offers the sweet spot of cost and quality. These are the kinds of insights that make all the late nights at the drawing board worth it.
So, whenever I dive into evaluating these aspects, I try to keep my project’s specific needs at heart. By doing so, I can tailor my approach to ensure I’m not just saving money but achieving the best possible results.
Injection molding is the fastest manufacturing process.True
Injection molding offers fast production speeds, suitable for large volumes.
3D printing has the lowest material costs in manufacturing.False
3D printing typically incurs high material costs compared to other methods.
How Do Cycle Times Compare Between These Methods?
I remember the first time I truly grasped how cycle times could transform a production line. It was like seeing an intricate puzzle fall into place.
Cycle times vary by method complexity, materials, and processes. Analyzing each method’s efficiency helps manufacturers optimize production and reduce costs.
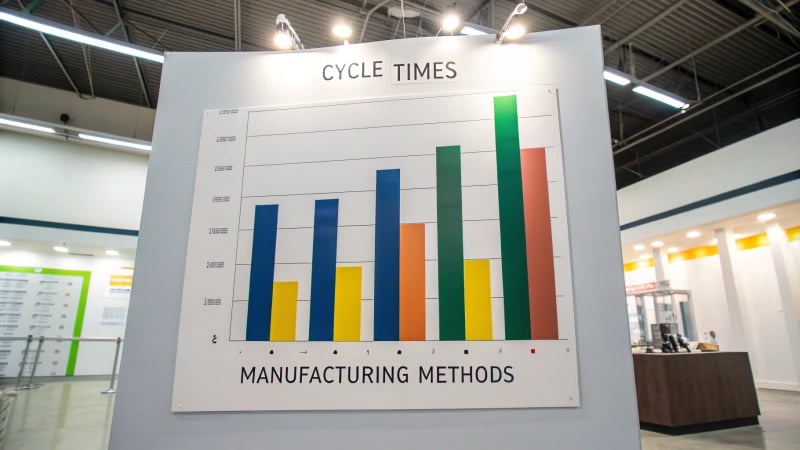
Methodology Overview
When it comes to manufacturing, I’ve found that cycle time is a key player. It refers to how long it takes to finish a single production cycle. Each manufacturing method7 comes with its own quirks—different steps, materials, and efficiencies—and these all impact cycle time.
Injection Molding vs. CNC Machining
- Injection Molding: Typically faster due to simultaneous multi-part production and less manual intervention. Perfect for when you need to produce a lot of items quickly.
- CNC Machining: More precise but usually slower, as it involves sequential processing of individual components.
Method | Average Cycle Time | Best Use Scenario |
---|---|---|
Injection Molding | 30-60 seconds | High-volume production |
CNC Machining | 5-15 minutes | Precision components |
Factors Influencing Cycle Time
- Material Type: The type of material you’re working with can really change the game. Some materials need extra time for heating or cooling, or they might require different cutting speeds.
- Complexity: Complex designs often mean more processing steps, which can slow things down.
- Automation Level: Let’s not forget automation; machines have a knack for speeding things up compared to manual labor.
Cycle Time Optimization Techniques
I’ve spent countless hours analyzing cycle time data to spot bottlenecks and improve workflows. Tools like data analytics8 are incredibly helpful in pinpointing where things get bogged down.
Real-World Applications
Let me share a real-world scenario: a company I worked with was producing plastic enclosures for electronics:
- By switching from CNC machining to injection molding, we cut cycle times by more than half and ramped up production significantly.
- We also brought in automation solutions9, like robotic arms, to handle loading and unloading parts, which further shaved off precious minutes.
Understanding these nuances empowers manufacturers to choose the best method for their needs, striking a balance between speed, cost, and quality.
Injection molding is faster than CNC machining.True
Injection molding produces multiple parts simultaneously, reducing cycle time.
CNC machining is ideal for high-volume production.False
CNC machining is slower and better suited for precision components.
How do different manufacturing techniques fit into various industries?
Ever wondered how different manufacturing techniques fit into the puzzle of product design?
Manufacturing techniques like welding and CNC machining are integral to industries such as automotive and electronics, enhancing product functionality and aesthetics.
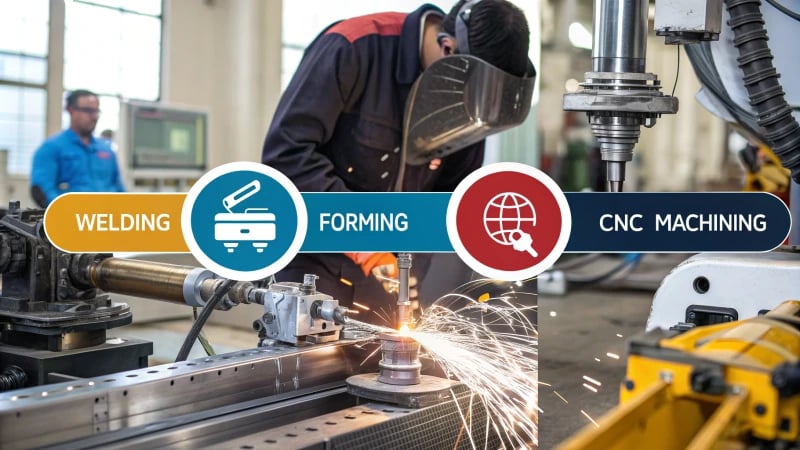
As a designer, I’ve always been fascinated by how different techniques fit seamlessly into the world of product creation. It’s like piecing together a puzzle where each method brings its own flair and function to the table. Let me take you through some personal insights into how these techniques find their sweet spots in diverse industries.
Welding Applications
Welding is like the unsung hero of the manufacturing world. I remember the first time I saw a car being put together on an assembly line; it was mesmerizing to watch the sparks fly as metal parts joined to form something robust and reliable. In the automotive industry, welding is key to building vehicle bodies that can withstand the test of time—and road conditions.
In aerospace, welding takes on a whole new level of precision and importance. Imagine crafting lightweight yet durable structures that need to endure the harshest environments. It’s no small feat, and yet, welding makes it possible10.
Forming Techniques
When it comes to forming, my mind often drifts back to my early days as a designer, experimenting with bending and shaping metal into something useful. These techniques are vital in metal fabrication, creating everything from appliance parts to HVAC components.
In consumer electronics, forming isn’t just about shaping metal; it’s about crafting ergonomic designs that feel right in your hands. Think of your favorite gadget—chances are, forming played a role11 in making it both functional and comfortable to use.
CNC Machining
CNC machining was a game-changer for me. The precision it offers is unparalleled, especially in industries where accuracy is non-negotiable. I still get a thrill from watching CNC machines carve out intricate parts for medical devices or electronics. It’s like watching an artist at work, but with laser-focused precision.
The electronics industry relies heavily on CNC machining, especially when producing high-quality circuit boards12. It’s fascinating how this technique ensures each component fits perfectly into the larger picture of a device’s functionality.
Comparison Table
Technique | Industry Application | Key Benefit |
---|---|---|
Welding | Automotive, Aerospace | Structural integrity |
Forming | Metal Fabrication, Electronics | Shape customization |
CNC Machining | Medical Devices, Electronics | Precision and repeatability |
Each technique is like a tool in my designer’s toolkit, each with its own unique benefits and applications. By understanding these methods, I’ve been able to choose the right approach for my projects, ensuring both aesthetic appeal and functional prowess.
Welding is crucial for constructing vehicle bodies.True
Welding ensures strength and durability in automotive manufacturing.
CNC machining is rarely used in medical device production.False
CNC machining is vital for producing precise medical devices.
Can Injection Molding and Die Casting Be Used Together?
Ever wonder if combining injection molding and die casting could revolutionize your production process? Let’s dive into the possibilities and see how these two powerhouse techniques might just be the dynamic duo you’ve been looking for.
Yes, injection molding and die casting can be combined to improve production efficiency and quality, effectively creating hybrid assemblies that integrate plastic and metal components.
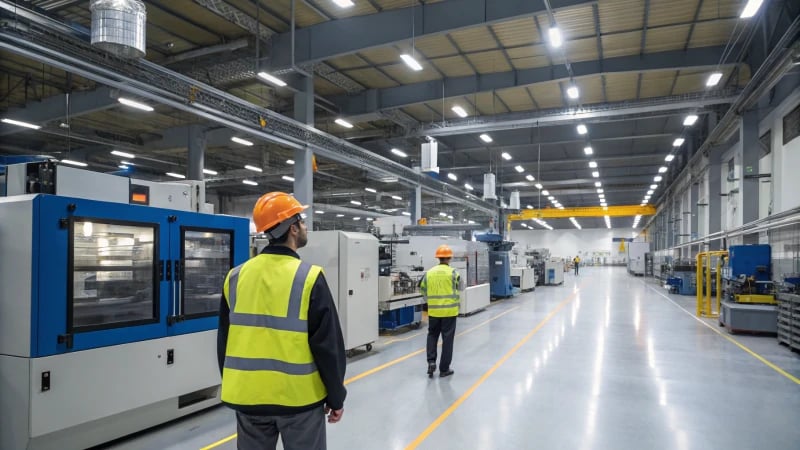
Understanding Injection Molding and Die Casting
I remember my first encounter with injection molding during a summer internship at a bustling factory. Watching molten plastic being injected into molds to create all sorts of products was like witnessing magic unfold. This process is perfect for producing high-volume, complex plastic parts. Meanwhile, die casting—a technique I saw in action during a project for automotive components—uses molten metal to craft sturdy parts with intricate details.
Process | Material Type | Common Uses |
---|---|---|
Injection Molding | Plastic | Consumer electronics, toys |
Die Casting | Metal | Automotive parts, hardware |
Potential Synergies
Combining these techniques can lead to some pretty exciting innovations. Imagine crafting a car part where a metal structure provides strength, while the surrounding plastic enhances flexibility and reduces weight. This is not just theoretical; it’s happening right now in industries like automotive, where both materials are essential for optimal performance. Injection molding13 enables the creation of detailed plastic parts that mesh perfectly with metal structures from die casting.
Design Considerations
Of course, mixing processes isn’t without its challenges. During a collaborative project, I learned that thermal expansion differences between plastic and metal can be a tricky hurdle. To tackle this, selecting materials that complement each other and designing flexible joints is crucial. The initial costs of using both methods might raise eyebrows, but trust me—the long-term gains in production efficiency14 and product quality often make it worthwhile.
Practical Applications
In my own experience working on electronics, we’ve often used plastic housings with metal reinforcements. This seamless integration of injection molding with die casting doesn’t just boost product durability; it also allows for creative design flexibility. Diving into case studies15 from industries like aerospace or consumer goods can offer valuable insights into these successful applications.
Whether you’re considering these techniques for a new project or exploring them out of curiosity, it ultimately comes down to your specific requirements. By exploring various examples16, designers like myself can make informed decisions about whether to embrace this integrated approach.
Injection molding produces metal parts.False
Injection molding is used for plastic, not metal parts.
Die casting is suitable for complex geometries.True
Die casting can create detailed and durable metal parts.
Conclusion
Injection molding and die casting are distinct manufacturing processes, each with unique materials and applications. Their combination can enhance production efficiency and product quality in various industries.
-
Learn the fundamentals of injection molding to understand its application scope and benefits. ↩
-
Setting clear goals can streamline your design process and enhance product quality. ↩
-
Explore how to choose the right material based on specific criteria like cost, durability, and application. ↩
-
Learn why injection molding is often chosen for large-scale production due to its cost efficiency and scalability. ↩
-
Discover how CNC machining ensures high precision, making it essential for producing intricate components. ↩
-
Explore strategies for producing plastic components effectively by understanding various manufacturing processes. ↩
-
Explore various manufacturing methods to understand their unique processes and how they impact cycle times. ↩
-
Discover how data analytics tools can help identify inefficiencies and improve cycle time in production. ↩
-
Learn how automation solutions can reduce cycle times and increase efficiency in manufacturing. ↩
-
Explore how welding techniques enhance safety and performance in aerospace structures. ↩
-
Learn how forming techniques contribute to ergonomic designs in consumer electronics. ↩
-
Understand the role of CNC machines in producing high-quality electronic components. ↩
-
Discover how injection molding excels in creating complex shapes efficiently, making it suitable for intricate plastic components. ↩
-
Learn about the benefits of integrating different manufacturing methods to enhance overall production efficiency. ↩
-
Explore successful examples where both processes were used together to achieve superior product design. ↩
-
See real-world applications where hybrid assemblies have been successfully implemented. ↩