Struggling with uneven distribution in your multi-cavity molds? You’re not alone.
Efficiently balance runners in multi-cavity molds by using simulation software to predict flow patterns and adjust design for even molten material distribution, improving part quality and reducing defects.
While simulation is a powerful tool, it’s just the beginning. I remember the first time I faced this issue; it felt like trying to solve a puzzle without all the pieces. But diving deeper into runner design nuances revealed so much more. By experimenting with different strategies and seeking advice from industry veterans, I discovered innovative solutions that significantly improved our process. Join me as I share some of these insights that could transform your manufacturing outcomes too.
Simulation software predicts flow patterns in molds.True
Simulation software helps in forecasting how molten material flows.
Runner design has no impact on mold efficiency.False
Proper runner design is crucial for efficient and balanced molding.
What Are the Basics of Runner Systems in Injection Molding?
I remember my first encounter with injection molding—a mesmerizing dance of plastic and machinery that felt like magic.
Runner systems in injection molding direct molten plastic to mold cavities. They impact efficiency, cost, and quality, with cold and hot runners providing unique benefits.
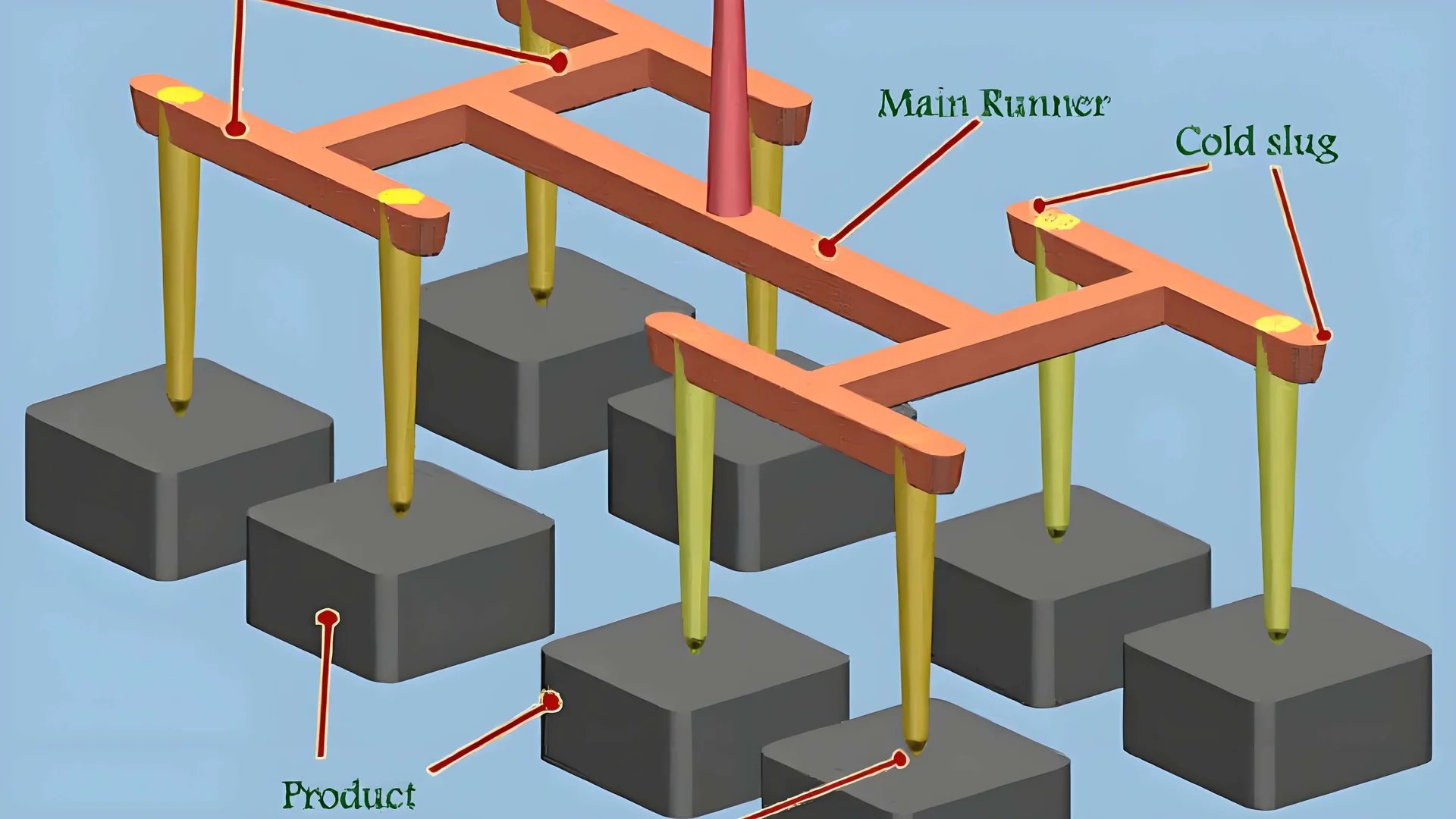
I remember my first encounter with injection molding—a mesmerizing dance of plastic and machinery that felt like magic. Understanding runner systems became my key to unlocking this mystery. These systems are like the circulatory system of the injection molding world, channeling molten plastic where it needs to go to shape the final product.
Understanding Runner Systems
Runner systems in injection molding are like the veins of the process, ensuring that every part of the mold receives its fair share of molten plastic. I learned that without these, achieving precise, uniform products would be nearly impossible. Imagine trying to fill a complex mold without a clear path—chaos!
Types of Runner Systems
Cold Runner Systems
My first project involved a cold runner system. I remember the satisfying clunk as we removed solidified plastic after each cycle. It’s straightforward and cost-effective, but I quickly realized the trade-offs with material waste and longer cycle times.
Advantages | Disadvantages |
---|---|
Lower initial cost | Material waste |
Flexibility in materials | Longer cycle times |
Hot Runner Systems
Then came hot runners—game-changers for high-volume production. No more waste and faster cycle times, but they came with a hefty upfront cost and maintenance complexity. It was a steep learning curve, but seeing the efficiency gains made it worthwhile.
Advantages | Disadvantages |
---|---|
Reduced material waste | Higher initial cost |
Faster cycle times | More complex maintenance |
Key Components of Runner Systems
- Sprue: The starting point—the main artery. It’s where everything begins.
- Runners: These are the distribution network, guiding molten plastic to various destinations.
- Gates: The traffic lights of the system, controlling flow into each cavity.
Each component must be meticulously crafted to maintain efficiency and quality—a lesson I learned after countless tweaks and adjustments.
Factors Influencing Runner System Design
Designing runner systems isn’t just about technical specs; it’s a blend of science and art. The type of plastic1, production speed, and part complexity all influence choices.
- Material Type: Some plastics are picky about their temperatures—I’ve had a few meltdowns (literally) when this wasn’t considered.
- Part Design Complexity: Intricate designs demand smarter runner layouts. I remember a particularly tricky project that required advanced configurations to get right.
- Production Volume: Hot runners start to make sense when you’re cranking out thousands of units—they pay for themselves over time.
Understanding these basics can transform your approach to injection molding, whether you’re just starting out or refining your expertise. Every mold is a new challenge, and mastering runner systems is your ticket to success.
Cold runner systems require removal of solidified plastic.True
Cold runner systems solidify the plastic, needing removal after each cycle.
Hot runner systems are ideal for low-cost production environments.False
Hot runner systems have higher initial costs, suited for high-volume production.
Why is balancing runners crucial in multi-cavity molds?
I remember the first time I realized how crucial balancing runners in multi-cavity molds truly is. It’s the key to ensuring every part we produce meets the high standards we set.
Balancing runners in multi-cavity molds ensures even material flow, crucial for consistent part quality and minimizing defects, enhancing the efficiency and reliability of injection molding.
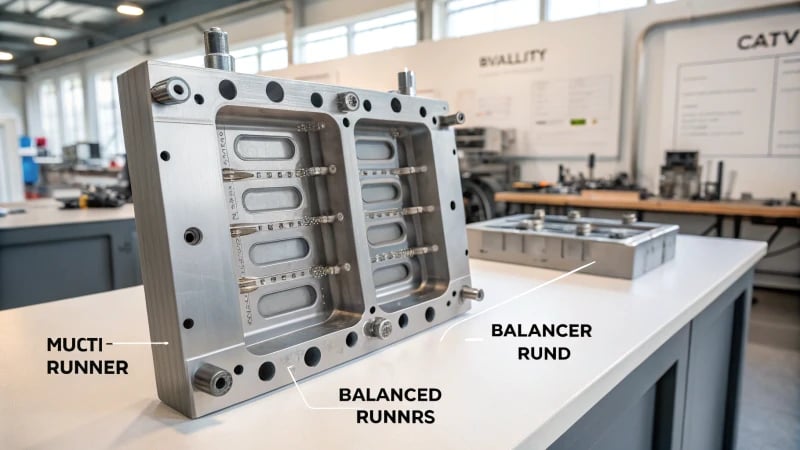
Understanding Multi-Cavity Molds
Back when I first started working with multi-cavity molds, it was like orchestrating a symphony of molten material. These molds are designed to churn out multiple parts in a single cycle, which is fantastic for boosting production efficiency. But here’s the catch: every cavity needs an equal share of molten material. That’s where the magic of balancing runners comes in. If the balance is off, you’ll end up with parts that are inconsistent in quality.
Importance of Runner Balance
-
Consistency in Part Quality
I can’t stress enough how runner balance impacts the final product. Imagine trying to fill multiple glasses of water from a single jug without spilling or shorting any glass—that’s what balancing runners does for molds. It ensures each cavity fills simultaneously, resulting in uniform part dimensions and properties. Without this balance, some cavities might come up short, leading to those pesky short shots or dimensional inaccuracies.
-
Reducing Defects
I’ve seen unbalanced flow create defects like flash—where excess material oozes out of the mold. It’s a nightmare that not only wastes materials but also tarnishes the part’s quality. Balancing helps keep the flow under precise control, reducing waste and boosting overall part quality.
-
Optimizing Production Efficiency
Efficient runner balance can cut down cycle times and make production processes repeatable. This is huge for keeping production costs2 in check, making it a pivotal consideration for manufacturers like us.
Techniques for Achieving Runner Balance
- Design Symmetry: Remember when you learned about symmetry in art class? It’s just as important here. Ensuring the mold design is symmetrical can naturally help balance the runners.
- Flow Simulation Software: Tools like Moldflow are lifesavers. They let us predict and tweak runner designs to achieve balance before we even create a physical mold.
- Gate Sizing: Proper gate sizing is another trick up our sleeves, helping us control the flow rate into each cavity and achieve that perfect balance.
Technique | Benefit |
---|---|
Design Symmetry | Natural balance |
Flow Simulation Software | Predictive adjustments pre-production |
Gate Sizing | Control over flow rate |
Understanding these techniques and their benefits has been transformative for me and can be for you too. Exploring advanced simulation tools3 can offer insights into how they revolutionize the manufacturing landscape.
Balanced runners prevent short shots in multi-cavity molds.True
Balanced runners ensure equal material distribution, preventing short shots.
Gate sizing is irrelevant to runner balance in molds.False
Proper gate sizing controls flow rate, aiding runner balance.
How Can Simulation Software Aid in Runner Balancing?
Ever wondered how to perfect that intricate runner system in your mold design?
Simulation software helps balance runners in injection molding by modeling material flow, identifying imbalances, and suggesting design adjustments, thus cutting costs and production time.
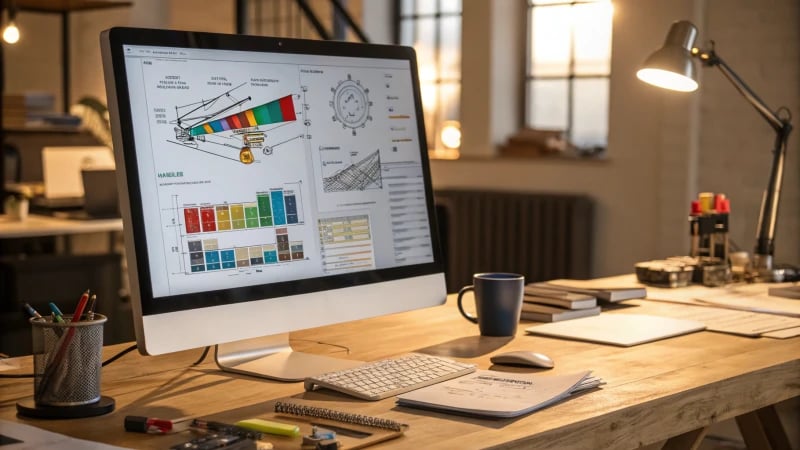
The Role of Simulation Software in Runner Balancing
As someone who’s spent a decade immersed in the world of product and mold design, I’ve seen firsthand the magic simulation software like Autodesk Moldflow or SIGMASOFT can weave. Imagine having a crystal ball for your designs, one that shows you exactly how plastic flows through your runner system. It’s like being able to spot potential pitfalls before they even happen. I remember when I first used these tools; it felt like a revelation. Suddenly, I could tweak designs with confidence, avoiding costly trial and error.
Key Features of Runner Balancing Software
- Flow Analysis: This feature is a game-changer. With flow analysis tools4, I could predict the exact path materials would take, much like plotting a course on a map before setting out on a journey. It’s all about foresight—knowing where potential delays or incomplete fillings might trip you up.
- Visualizing Imbalances: There’s something incredibly powerful about seeing a visual representation of imbalances. It’s like having a spotlight on problem areas, allowing me to make precise modifications that save both time and resources.
Feature | Benefit |
---|---|
Flow Analysis | Predicts material distribution |
Visualization | Identifies imbalance areas |
Benefits of Using Simulation Software
The benefits of these tools go beyond just saving money. They transform how we design:
- Reduced Costs: Less trial and error means fewer prototypes and less waste—a win-win for the budget and the environment.
- Time Efficiency: Faster iterations bring products to market quicker. I’ve seen projects cut weeks off their timelines thanks to these insights.
- Enhanced Product Quality: Consistency is key, and a balanced runner system ensures each part meets the highest standards without unnecessary defects.
I’ve seen companies like mine embrace simulation technology5 and revolutionize their design processes, optimizing outcomes without blowing the budget.
Practical Applications and Case Studies
I’ve read about companies making substantial strides thanks to simulation software. One standout was an electronics manufacturer that shaved 30% off their development time by integrating runner balancing simulations into their workflow6. These real-world successes underscore just how transformative this technology can be.
In my experience, simulation software doesn’t just streamline runner balancing—it can redefine our approach to injection molding, offering insights that were previously out of reach.
Simulation software reduces physical prototypes needed.True
Virtual optimization with simulation software cuts down on material costs.
Runner balancing software increases development time by 30%.False
Simulation reduces development time, improving efficiency and speed.
How Does Runner Design Impact Part Quality and Production Speed?
Runner design in injection molding is like the unsung hero, quietly ensuring our parts are top-notch and produced at lightning speed. It’s a bit like the GPS of manufacturing, guiding every move with precision and efficiency.
Runner design in injection molding influences part quality and production speed by controlling material flow, with the choice between hot or cold runner systems being crucial for optimizing manufacturing efficiency and results.
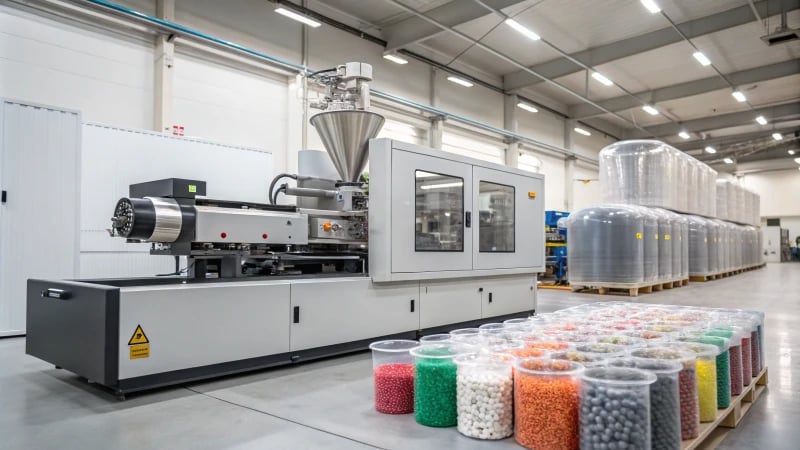
Key Factors Influencing Runner Design
I remember my first major project involving runner design; it felt like solving a complex puzzle. The runner system determines how molten plastic travels through a mold, which directly impacts both quality and speed. A well-designed runner is like a well-oiled machine, ensuring uniform flow and reducing defects.
- Balance: Ensures even material distribution across all cavities.
- Size and Length: Affects pressure drop and cooling time.
Hot Runner Systems
Switching to hot runner systems was a game-changer for me. Hot runners keep the plastic molten, eliminating sprues and runners. This significantly enhanced our production speed7 thanks to reduced cycle times.
Advantage | Explanation |
---|---|
Reduced Waste | No need for runner removal, minimizing scrap. |
Improved Aesthetics | Fewer weld lines and gates, enhancing appearance. |
Cold Runner Systems
On the flip side, cold runner systems have their charm too. They solidify the material in the runner, requiring trimming post-molding. I found them particularly cost-effective for low-volume production due to the lower initial investment.
- Cost-Effectiveness: Ideal for low-volume production due to lower initial investment.
- Material Versatility: Suitable for thermoset and thermoplastic materials.
Considerations for Optimizing Design
Optimizing runner design feels like walking a tightrope—balancing cost, material usage, and production speed. It’s essential to consider:
- Material Type: Different materials behave uniquely under heat and pressure.
- Product Complexity: Complex designs may require advanced runner systems.
Exploring innovative techniques8 for enhancing runner design can cater to specific product requirements and manufacturing conditions. This includes simulations that predict flow behavior to refine design choices.
Ultimately, understanding these variables can guide designers like me towards creating efficient, high-quality molds that align with production goals without compromising on part integrity or speed of manufacture. Remember, choosing the right system—hot or cold—depends on your specific application needs and long-term production plans.
Hot runners reduce cycle times significantly.True
Hot runners keep plastic molten, eliminating sprues and reducing cycle time.
Cold runner systems are more cost-effective for high-volume production.False
Cold runners are ideal for low-volume due to lower initial investment.
Conclusion
Efficiently balancing runners in multi-cavity molds enhances material flow, reduces defects, and optimizes production. Simulation software aids in achieving this balance for improved part quality and manufacturing efficiency.
-
Discovering how different materials behave can guide you in choosing the right runner system, impacting efficiency and product quality. ↩
-
Explore how balanced runners can reduce cycle times and waste, significantly impacting production costs. ↩
-
Discover how advanced simulation tools like Moldflow optimize runner designs, enhancing efficiency and precision. ↩
-
Explore how flow analysis predicts material distribution, helping to identify imbalances for better mold design. ↩
-
Discover how simulation technology enhances design processes, reducing time and cost while improving product quality. ↩
-
Learn from real-world examples how companies improved efficiency and quality using simulation tools. ↩
-
Hot runners eliminate runner solidification, reducing cycle times and boosting production efficiency. Explore further to understand their benefits. ↩
-
Discover cutting-edge methods for improving runner systems to achieve superior part quality and efficiency. ↩