Exploring plastic manufacturing feels overwhelming, right? I remember my first time. Understanding the differences between molding processes seemed like learning a new language!
Blow molding usually forms hollow shapes like bottles and containers. Injection molding, on the other hand, produces both solid and intricate structures. Knowing these differences is important. This knowledge really helps in choosing the right method for your design needs.
In this article, I explore the fascinating world of blow molding and injection molding. These processes have unique characteristics. Each has its own advantages. Both methods find use in many applications. I reveal insights into their special features. This information may greatly influence your design decisions.
Blow molding is used for solid plastic shapes.False
This claim is false; blow molding primarily produces hollow shapes like bottles.
Injection molding can create complex structures.True
This claim is true; injection molding is capable of producing both solid and intricate designs.
- 1. What Makes Blow Molding a Better Choice Than Injection Molding?
- 2. When Should You Choose Injection Molding for Your Projects?
- 3. What Are the Key Differences in Production Costs Between Blow Molding and Injection Molding?
- 4. What Materials Are Commonly Used in Each Molding Process?
- 5. How Do Design Considerations Affect the Choice of Molding Technique?
- 6. Conclusion
What Makes Blow Molding a Better Choice Than Injection Molding?
Join me on a journey into the exciting world of manufacturing methods. We focus on blow molding and injection molding. Blow molding really impresses in many situations. This process is truly remarkable.
Blow molding is very efficient for making hollow shapes like bottles and containers. It reduces costs by using faster cycle times and creating minimal waste. This method is excellent for mass production of simple designs. In contrast, injection molding is better for creating complex structures.
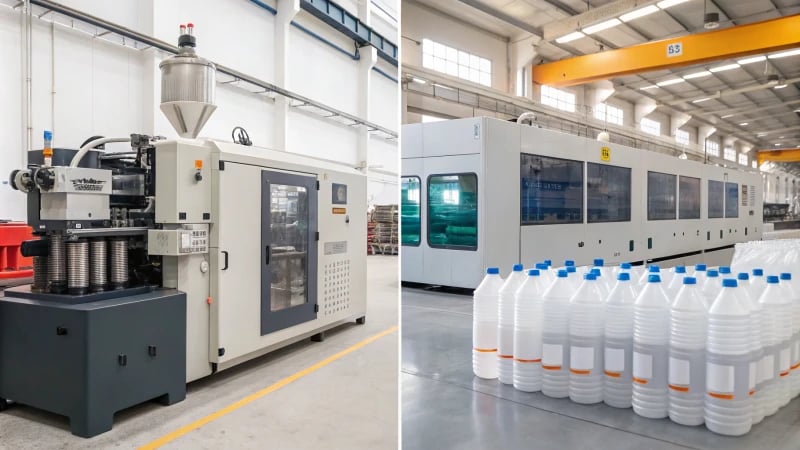
Main Content
When I first learned about blow molding, I was amazed by how it creates hollow shapes. This was something I hadn’t noticed before. Imagine blowing air into hot plastic and watching it expand into the mold. It feels magical. This method produces perfect items like bottles and containers. It’s incredible how a simple process can create products with big spaces inside while keeping thin, even walls.
Injection molding is very different. I often marvel at how flexible it is. This technique creates both solid and complex items. It forms everything from delicate gears to smooth casings for electronic devices. Designers like me find understanding these shape features crucial. It helps in picking the right method for a product’s needs.
Shape Characteristics of Blow Molding
Blow molding is mainly for hollow plastic items. It works best with basic, regular shapes. Picture plastic bottles or even barrels. These are classic examples of blow molding. These shapes make me remember my early design days. Back then, I focused more on function than complexity.
Blow molding excels with simple shapes like cylinders or spheres. Special methods allow slightly more complex shapes, but I often weigh them against injection molding’s clarity. The capabilities’ contrast is stark. Blow molding is great for mass-producing simple designs. Injection molding leads in creating detailed products with different inner structures.
Efficiency and Production Speed
Blow molding’s speed really excites me. Projects with tight deadlines benefit from its speed. A typical blow molding cycle finishes in just seconds.
Molding Type | Cycle Time | Production Volume |
---|---|---|
Blow Molding | Short (Seconds) | High (Ideal for mass production) |
Injection Molding | Longer (Seconds to Minutes) | Varies (Depending on complexity) |
Efficiency becomes essential in such situations.
Cost-Effectiveness
Cost is always on our minds as designers. I recall working on a beverage bottle project where blow molding was incredibly cheap for the large quantities we needed. The lower tooling costs for blow molds helped keep our budget balanced.
On the opposite side, detailed designs needing precision become pricey with injection molding due to higher tooling costs that are the reason behind this increase in expense.
Material Utilization
Blow molding uses material very efficiently; it’s nice to know minimal waste occurs since a single plastic piece fills the mold completely! I’ve felt frustrated with wasted materials in injection molding, but blow molding reduces costs and supports sustainability—a value I hold dearly as a designer.
Flexibility in Production
Today’s fast market demands flexibility, and blow molding allows quick production changes if a design needs tweaking—altering the mold is simple and low-cost! This flexibility has been invaluable in my projects; it’s perfect for meeting market demands or changing consumer tastes quickly compared to altering injection molds, which can be complex and time-intensive.
Conclusion: Tailoring Manufacturing Processes
The choice between blow molding and injection molding depends on product needs: think of shape complexity, production amount, and budget limits! As someone deeply invested in product design, understanding these differences helps align design goals with capabilities.
For more about how these methods shape product design and manufacturing efficiency, explore our resources on molding techniques1 and cost analysis in production.
Blow molding is faster than injection molding for simple shapes.True
Blow molding has shorter cycle times, making it ideal for producing large volumes of simple hollow items quickly.
Injection molding is more cost-effective for large runs of simple shapes.False
Blow molding typically offers lower tooling costs, making it more economical for mass production of simple shapes than injection molding.
When Should You Choose Injection Molding for Your Projects?
Do you ever struggle with choosing a manufacturing method? I do! Injection molding usually stands out for good reasons. Let’s look into the situations where it really excels. It might even be the perfect match for your next project.
Injection molding is the top pick for manufacturers needing high volumes. They choose it for complex shapes, material variety, low cost, quick production and design flexibility. This method creates precise and detailed parts. It is perfect for many uses. Probably, it suits diverse applications well.
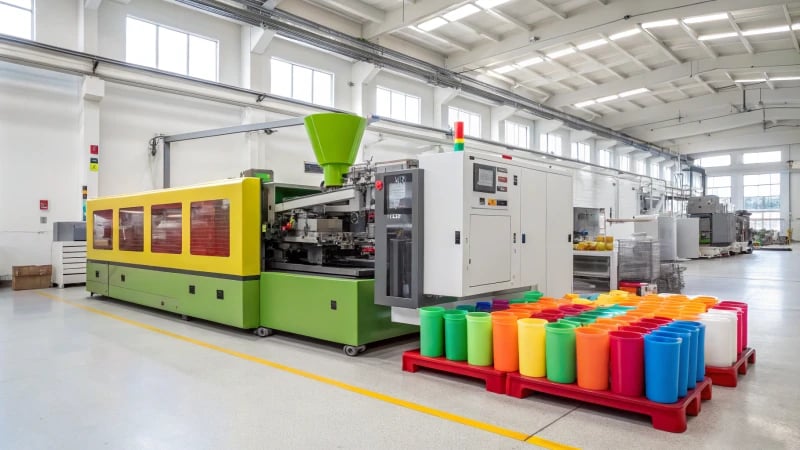
High Volume Production Needs
Injection molding is often chosen by designers and engineers when manufacturers need to produce large quantities of identical parts. This method focuses on being fast and precise in crucial situations, allowing for rapid cycle times. For example, when I worked on a project with plastic parts for electronics, injection molding became essential for making many items quickly. The speed and efficiency are unmatched; I remember the thrill of watching hundreds of identical parts coming from the machine in just hours. The setup costs might be high initially, yet as you produce more, those costs drop significantly, making each item cheaper. For those needing fast production, this method is tough to compete with.
Complex Shapes and Designs
I get excited about injection molding because it creates complex shapes with high accuracy that other manufacturing methods struggle with. On a project needing detailed designs, I was impressed by how smoothly it managed intricate designs with high precision. From car parts to stylish electronic cases, injection molding allows for fine details that make a product truly stand out. If you’re curious about specific design capabilities, explore this resource on mold design2.
Material Versatility
The wide range of materials used in injection molding always amazes me. Injection molding accommodates various plastics tailored for specific applications. Strong thermoplastics suit car parts well, while softer plastics fit perfectly for everyday products. This adaptability is very important where performance depends on material properties and is crucial in industries like electronics and automotive. Discover more about material selection here3.
Cost-Effectiveness in Mass Production
While the initial cost for injection molding may seem large, think long-term; it becomes cost-effective when producing large volumes. Once producing many items, the cost per piece significantly decreases due to the ability to reuse molds and reduce waste during production. Understanding these savings is key for mass production scenarios; companies can expect reduced costs per unit when scaling up production. To understand more about cost analysis in manufacturing, see this detailed article4.
Rapid Turnaround Times
Today, time is extremely valuable; I recall a project where quick delivery was vital and injection molding helped us a lot. With proper setup, we produced quality items very fast without sacrificing quality—this speed is vital in industries like electronics and fashion where trends shift rapidly. To learn about strategies for speeding up production, refer to this overview on efficient manufacturing5.
Design Flexibility for Custom Projects
I really enjoy injection molding for its flexibility with design changes; if you like innovating, you will appreciate how easy it is to adjust or create new molds without significant downtime in production. This adaptability is critical for meeting changing consumer needs or starting new projects—insights on managing design changes can be found in this guide on product lifecycle management6.
Injection molding is ideal for high-volume production.True
This claim is true as injection molding efficiently produces large quantities of identical parts, reducing per-unit costs significantly with increased volume.
Injection molding cannot create complex shapes.False
This claim is false; injection molding excels at producing intricate designs and complex shapes with high precision, which other methods struggle to achieve.
What Are the Key Differences in Production Costs Between Blow Molding and Injection Molding?
Have you ever felt confused about two manufacturing methods and wondered which one is cheaper? I have experienced that too! Let’s dive into blow molding and injection molding to compare their production costs. This way, you probably choose the best option for your project.
Comparison of production costs between blow molding and injection molding involves several factors. Initial tooling costs are important to consider. Material expenses also play a major role. Production speed often varies between the two methods. Blow molding is usually more economical for hollow products. Injection molding excels in creating precise complex shapes.
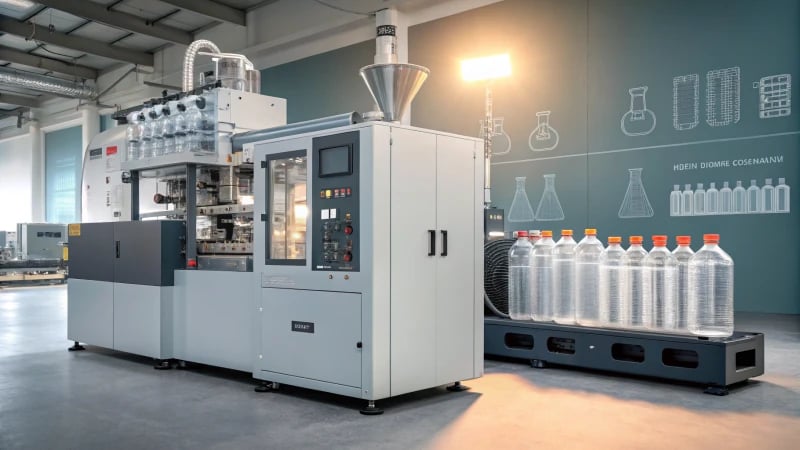
Understanding Production Costs
When comparing production costs between blow molding and injection molding, it’s not just numbers. Understanding these numbers is crucial for your project. I remember my first experience with these options – confusing doesn’t even begin to describe it! Let’s break it down so it’s clear.
-
Initial Tooling Costs
Blow molding generally needs simpler tooling than injection molding. I remember seeing blow molds that were easier and cheaper, which made my starting production runs smoother. Meanwhile, injection molds are usually intricate and costly, especially for detailed shapes. If you produce many simple, hollow products, blow molding7 might be the right choice for you! -
Material Costs
The plastic type greatly affects your production expenses. I’ve often observed that blow molding uses thermoplastics, which are typically less expensive when bought in large amounts. Plus, blow molding is efficient – less waste is created as it forms hollow products directly. This really could lead to more savings. In contrast, injection molding sometimes results in additional scrap due to its complexity. These factors can really add up! -
Production Speed and Volume
Once the mold is prepared, injection molding produces items faster, reducing costs per unit for large-scale production. This method works well if you need to create many small parts quickly. However, blow molding might be slower but excels in making larger items like bottles and containers. Knowing your production needs helps you choose the most cost-effective method.
Cost Breakdown Table
Cost Factor | Blow Molding | Injection Molding |
---|---|---|
Initial Tooling | Lower initial investment | Higher initial investment |
Material Costs | Generally lower | Can be higher due to complexity |
Production Speed | Slower for complex shapes | Faster overall production |
Waste | Less waste | More scrap material |
Best Use Cases | Hollow products | Complex shapes and precision |
Efficiency Considerations
As I studied this topic further, efficiency became just as important as direct costs. Blow molding is excellent for making many similar hollow products, while injection molding is great for creating detailed designs with precision. This difference can impact long-term profits. It’s essential to consider how each method suits your production requirements.
Don’t forget about maintenance! Injection molds often need more care due to their complexity, affecting your budget over time.
Final Thoughts
In summary, comparing blow molding and injection molding is not only about initial costs; it’s about understanding total expenses over time. Thinking about how each method fits your production needs leads to a wise and confident decision. My journey through these options showed me that clarity leads to better outcomes – and I hope this explanation helps you as much as it helped me!
Blow molding has lower initial tooling costs than injection molding.True
Blow molding requires simpler molds, making it more economical for initial production runs compared to the complex molds needed for injection molding.
Injection molding produces less waste than blow molding.False
Injection molding often has more scrap material due to excess material in complex molds, whereas blow molding has less waste from hollow product design.
What Materials Are Commonly Used in Each Molding Process?
Have you ever thought about how people create everyday plastic items? Learning about the materials used in molding is not only for engineers. It’s very interesting to see how our favorite products actually come to life!
In molding processes such as blow molding and injection molding, people often use certain materials. Polyethylene (PE) is common for blow molding. ABS or nylon is typical in injection molding. Each material has unique qualities. These qualities fit them for different uses. They impact everything from how long a product lasts to how efficiently it is manufactured. Each material affects manufacturing efficiency.
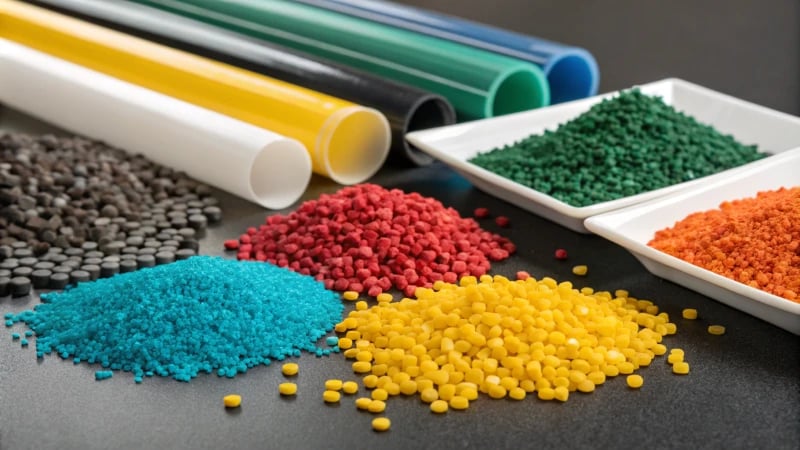
Common Materials in Blow Molding
Blow molding looks magical when you watch it. It creates hollow plastic items. The primary material used in this process is polyethylene (PE), known for its excellent flexibility and strength. Common examples include:
- HDPE (High-Density Polyethylene): This material is tough. It’s ideal for milk jugs and detergent bottles due to its rigidity and chemical resistance.
- LDPE (Low-Density Polyethylene): People use this in squeeze bottles and grocery bags, offering flexibility and ease of processing. I made a squeeze bottle prototype with it, which was really successful!
- Polypropylene (PP): This material melts at a higher temperature, making it suitable for containers that may be exposed to heat. Many designers often choose PP.
Manufacturers like these materials because they create lightweight yet strong products. They balance essential qualities, which is key when designing items with large internal spaces, like beverage bottles.
Common Materials in Injection Molding
Injection molding offers many possibilities. It does more than create solid shapes; it also handles complex forms using materials such as:
- ABS (Acrylonitrile Butadiene Styrene): ABS is tough and resists impacts, commonly used in automotive parts and consumer goods.
- PS (Polystyrene): This rigid material is used for plastic cutlery due to its clarity and ease of molding.
- PVC (Polyvinyl Chloride): PVC is durable and versatile, commonly found in pipes, fittings, and other construction materials.
- Nylon (Polyamide): Nylon is very strong; it resists heat and is widely used in automotive components.
Injection molding allows us to create intricate designs with precise dimensions. Understanding these materials helps me choose what meets functional and aesthetic needs while enabling the production of both small precision parts and large complex assemblies.
Comparison of Materials Used in Different Processes
Molding Process | Common Materials | Key Properties | Typical Products |
---|---|---|---|
Blow Molding | HDPE, LDPE, PP | Lightweight, strong, chemical resistance | Bottles, barrels, containers |
Injection Molding | ABS, PS, PVC, Nylon | Toughness, precision, versatility | Automotive parts, toys, housings |
Each molding method takes advantage of specific material traits. Picking the right material affects product quality and manufacturing efficiency. Knowing these materials deeply empowers designers to align choices with project goals. If you’re interested in specific materials in manufacturing processes, explore the molding materials guide8. Let’s continue this exciting discovery together!
Blow molding primarily uses polyethylene materials.True
Blow molding predominantly utilizes polyethylene, including HDPE and LDPE, for creating hollow plastic products due to their flexibility and strength.
Injection molding exclusively uses ABS and PVC materials.False
Injection molding employs a variety of materials, including ABS, PVC, Nylon, and others, not limited to just ABS and PVC.
How Do Design Considerations Affect the Choice of Molding Technique?
Did you ever think about how complex design choices impact the ways we mold things? Join me. Discover how materials and shapes affect our choices.
Design choices really affect which molding method is chosen. Factors like material, wall thickness and shape complexity are very important. Tolerances and production efficiency also matter a lot. Each factor helps in getting the best performance. Every factor is important for saving money.
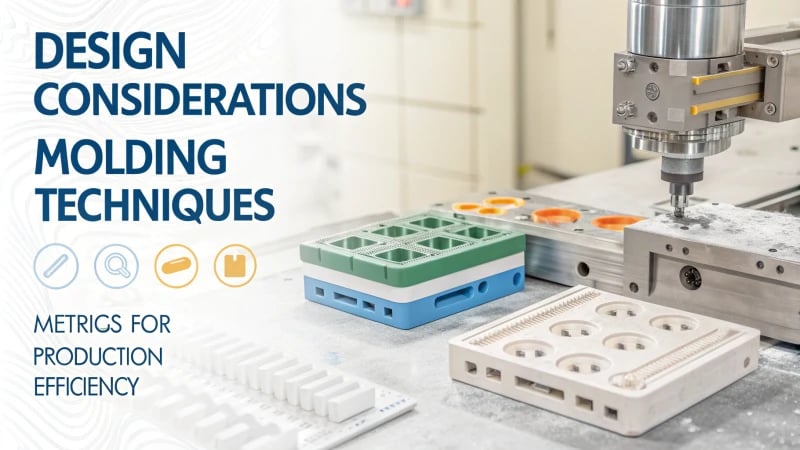
Understanding Design Considerations
Design considerations mean much more than simple technical details; they reveal how ideas come alive. My experiences in product design taught me that every tiny decision affects the molding technique. Let’s explore this idea.
When choosing a molding technique, design considerations play a crucial role. These factors can influence everything from the molding process to the final product’s performance. Some key considerations include:
-
Material Choice: Every material has unique qualities. Working with thermoplastics, for example, makes injection molding ideal for detailed and complex shapes. The right material transforms any design from ordinary to amazing.
-
Wall Thickness: Wall thickness often decides the molding technique. I remember designing a lightweight bottle. Blow molding worked because it allowed thin, even walls. This technique made the product both useful and attractive.
Shape Characteristics
Shape plays a crucial role in choosing a molding technique. Different shapes mean different techniques. Below is a comparison table outlining the shape characteristics of both techniques:
Molding Technique | Shape Characteristics | Examples |
---|---|---|
Blow Molding | Mainly hollow shapes; simple and regular forms | Plastic bottles, barrels |
Injection Molding | Solid or complex structures; unlimited shape possibilities | Gears, automotive parts |
Complex internal structures, like intricate gears, need injection molding. This choice affects both the function and look of the product.
Tolerances and Surface Finish
Tolerances resemble fine print in design; they dictate possibilities. Injection molding works well for high-precision parts, crucial in electronics. Keeping tight tolerances is vital.
Moreover, surface finish matters in design. Some projects prioritize appearance as much as function. Injection molding creates smooth surfaces while blow molded items often feature more texture.
Production Efficiency
Production efficiency is important. Blow molding excels at producing many hollow items quickly; it really saved time! A fast-paced project once relied on blow molding due to its speed and cost-effectiveness.
Injection molding may involve higher initial costs but offers precision and versatility that can justify the investment.
The world of design combines creativity and technical skill, each essential in molding choices. For further insights on optimizing design choices for molding techniques, check out design optimization strategies9. This journey emphasizes the strong connection between creativity and expertise.
Injection molding is ideal for complex geometries.True
Injection molding excels in producing intricate designs due to its precision and ability to handle varying wall thicknesses.
Blow molding produces thicker walls than injection molding.False
Blow molding typically results in thinner, uniform walls, making it unsuitable for thicker structures compared to injection molding.
Conclusion
Discover the essential differences between blow molding and injection molding processes, focusing on shape characteristics, efficiency, cost-effectiveness, and material selection for optimal product design.
-
Discover detailed comparisons between blow and injection molding processes that can enhance your manufacturing decisions. ↩
-
Explore this resource to delve into the complexities of mold design and how it relates to injection molding capabilities. ↩
-
Understanding material selection is crucial; this link discusses how various materials impact injection molding processes. ↩
-
Learn about cost efficiency in manufacturing through this article, which explains the economic advantages of injection molding. ↩
-
This overview provides strategies on speeding up production processes, relevant for quick market responses in injection molding. ↩
-
Gain insights into managing design changes effectively with this guide, critical for adapting to new project requirements. ↩
-
Discover insights on how production costs differ between these two molding techniques to make an informed decision for your project. ↩
-
Explore this resource to gain insights into how material selection impacts production efficiency and product quality in molding processes. ↩
-
Explore detailed insights on optimizing design choices for different molding techniques and improve your product’s performance. ↩