Do you want to improve the weight and efficiency of your product designs? Let us discover this together!
Blow molding is ideal for lightweight, hollow products with thin walls, while injection molding excels in crafting precise, complex shapes but may result in heavier items.
I have worked in product design and know how vital it is to pick the right manufacturing process. Blow molding and injection molding each bring their unique benefits. Understanding these can change how you design products.
I once worked on a project needing lightweight plastic bottles. We chose blow molding and the outcome was impressive. The material spread evenly and created a thin but strong wall. This kept the bottle light while staying durable. This method allowed us to reduce material costs and still meet design goals.
In another case, precision became very important. Injection molding excelled when I needed a complex electronic casing. The detailed design needed high accuracy. Injection molding handled this well. Yet, it posed challenges with material use and weight control, which required careful handling.
So, choose blow molding for flexibility and lightweight features or injection molding for precision. The key is finding what fits your specific needs. Let’s look closely at how these methods affect your designs!
Blow molding is ideal for creating hollow lightweight products.True
Blow molding is specifically designed for producing hollow items with thin walls, making it suitable for lightweight product manufacturing.
Injection molding cannot produce complex shapes efficiently.False
Injection molding excels in creating intricate designs and complex shapes with high precision, contrary to the claim.
What Are the Key Differences Between Blow Molding and Injection Molding?
Recognizing the differences between blow molding and injection molding is significant for designers like me in manufacturing. Each method has unique advantages suited for different products. Exploring this topic seems like uncovering the layers of an interesting puzzle.
Blow molding and injection molding have different processes. Blow molding is perfect for creating lightweight, hollow items with thin walls. Injection molding is suitable for more complex shapes. It allows for higher precision in forming intricate designs.
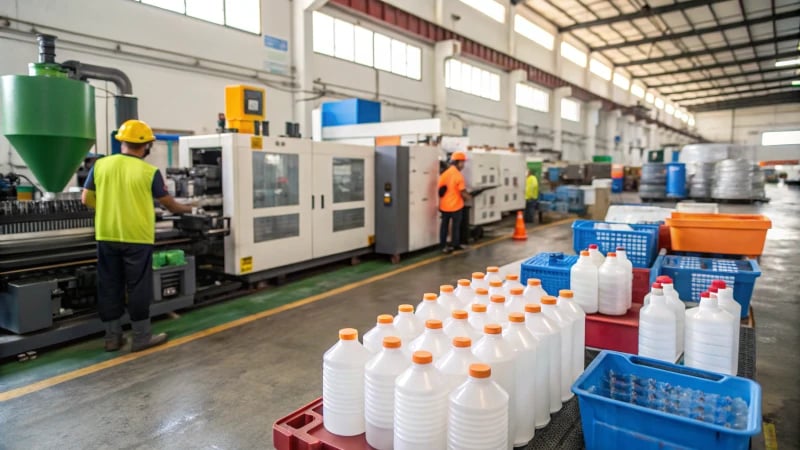
Understanding Blow Molding
Blow molding shows the beauty of simple manufacturing. When I first saw this process, it surprised me. It creates hollow plastic products skillfully. Imagine inflating a molten plastic parison. It feels like blowing up a balloon, but instead, you are making stable, lightweight items. This technique lets the walls be really thin. Products become light and strong.
For instance, in the case of plastic bottles, blow molding can produce containers with very thin walls without sacrificing integrity. This results in reduced material usage and contributes to lower transportation costs due to lighter weight.
Additionally, blow molding offers significant process flexibility. Manufacturers can easily adjust the inflation size and pressure to create products that meet specific design requirements. This is particularly beneficial for items such as toys1, where weight precision is crucial.
Features of Injection Molding
Injection molding holds a special place for its precise and intricate designs. Visualize molten plastic injected into a mold cavity, which solidifies into detailed shapes. It’s nearly magical to see a complex device housing form.
This method can also produce lightweight products; however, it excels at making complex geometries. One of the key advantages of injection molding lies in its capability to produce intricate designs with fine details. For example, small electronic device housings are often made via injection molding to ensure both durability and aesthetic appeal.
However, complexity comes with downsides. Waste is a common issue due to gates and runners, lowering material use. I faced frustration balancing intricate designs while reducing waste.
Comparative Analysis
The differences between blow molding and injection molding can be summarized in the table below:
Feature | Blow Molding | Injection Molding |
---|---|---|
Process Type | Inflates molten plastic | Injects molten plastic |
Material Distribution | Thin and even wall distribution | Thicker walls, potential waste |
Product Shape | Best for hollow, lightweight items | Ideal for complex shapes |
Precision | Moderate | High |
Material Utilization | Efficient, less waste | Less efficient due to waste |
Cost Implications | Lower for large volumes | Higher due to complexity |
Overall, while blow molding is advantageous for producing lightweight and hollow products with minimal material waste, injection molding shines when detailed design and high precision are required. As a designer, knowing these differences helps me choose the right method for my needs.
Blow molding produces hollow plastic products efficiently.True
Blow molding is designed for creating lightweight, hollow items, ensuring efficient material distribution and reduced waste.
Injection molding is better for complex geometries than blow molding.True
Injection molding excels in producing intricate shapes and high precision, making it suitable for detailed designs.
How Does Material Utilization Impact Production Costs?
Have you ever thought about how using different materials changes the financial world of manufacturing? Let us explore the interesting realm of material use and its big effects on production expenses.
Material use greatly affects production costs. It measures how well raw materials are used in manufacturing. Efficient use of materials lowers waste. It also decreases expenses. This is important in processes such as blow molding and injection molding.
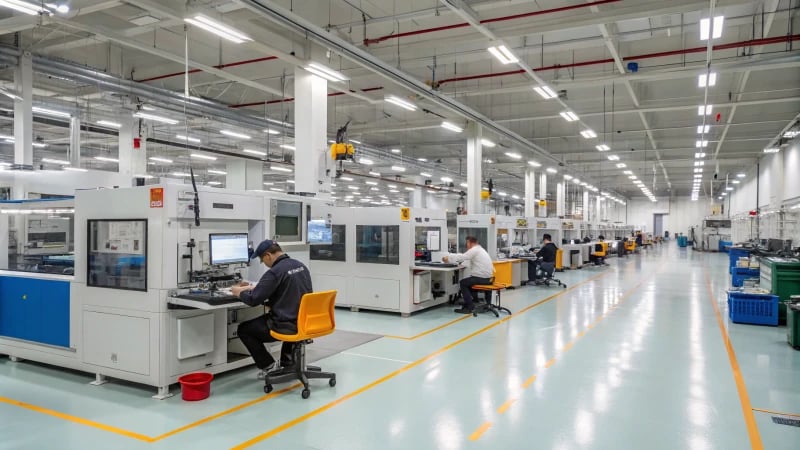
Understanding Material Utilization in Manufacturing
Material utilization involves more than a technical term. It is a significant change in manufacturing. Throughout my career, I saw how using raw materials wisely led to great cost savings and improved efficiency in operations. In some projects, like creating a new line of plastic bottles, the impact of good material use was clear. Reducing waste not only saved money but also increased our profit margins.
Material utilization strongly influences the choice of manufacturing processes. Blow molding and injection molding both offer different advantages that affect costs. Knowing these differences helps us make smart decisions aligned with our goals.
Blow Molding: A Cost-Effective Approach for Lightweight Products
Material Distribution Characteristics
On a project to create lightweight plastic bottles, we chose blow molding. This method allows precise material distribution by blowing a molten plastic parison into a mold, creating thin, even walls that greatly reduce the material used.
Process Type | Material Usage | Typical Products |
---|---|---|
Blow Molding | Lower | Plastic bottles, containers |
Injection Molding | Higher | Small electronic housings |
During bottle production, we achieved thin walls while keeping strength. This made the bottles lighter and reduced the material needed. It felt good knowing we were benefiting both the environment and our financial gains.
Process Flexibility
Blow molding offers great flexibility, allowing us to make various hollow shapes with control over wall thickness. I remember creating lightweight toys with specific weight needs; by adjusting pressure and timing in blow molding, we met those requirements efficiently. This process saved significantly on raw materials.
Injection Molding: Precision Comes at a Cost
Advantages in Precision and Complex Shapes
Injection molding allows for detailed designs but comes at a cost—especially for lightweight items. While working on small electronic housings, maintaining wall thickness for strength made them heavier compared to blow-molded items.
Advantages | Drawbacks |
---|---|
High precision | Higher material costs |
Complex designs | More waste from gates and runners |
Although injection molding provides detailed designs, it might increase costs due to material waste from gates and runners. We always consider if the precision justifies higher expenses.
Difficulty in Material Utilization and Weight Control
Controlling weight and reducing waste in injection molding is challenging as product shape and wall thickness greatly affect material use. Often, I wished for blow molding’s simpler approach which simplifies weight control and waste reduction.
Overall, my journey in material utilization revealed its vital role for manufacturers. Selecting the right method for products allows us to improve material usage which cuts production costs significantly; thus, material efficiency is crucial.
For more insights on optimizing material usage, check out material efficiency strategies2.
Blow molding reduces material waste compared to injection molding.True
Blow molding allows for thinner walls and precise control, leading to less material waste and lower production costs compared to injection molding's thicker walls.
Injection molding is always more cost-effective than blow molding.False
Injection molding may offer precision but often results in higher material costs and waste, making it less cost-effective than blow molding in many scenarios.
When Should You Choose Blow Molding or Injection Molding?
Exploring the world of manufacturing often feels confusing. This is especially true when deciding between blow molding and injection molding. Let’s simplify this process together. Find the best option for your product needs.
Decide between blow molding and injection molding by looking at product design complexity, weight and material efficiency. Blow molding works well for lightweight products. Injection molding suits complex designs better. Select according to your project needs.
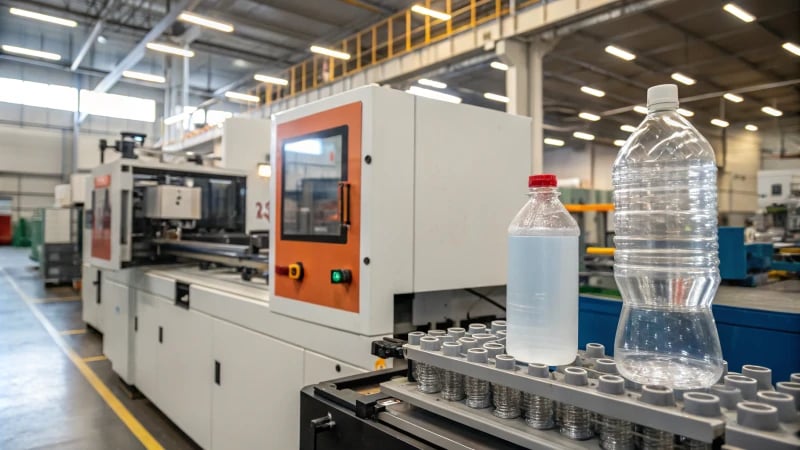
Understanding Blow Molding vs. Injection Molding
In my early days of working in product design, I often had to decide between blow molding and injection molding for each project. Both techniques have their own strengths. Knowing these strengths is important for selecting the right method.
Advantages of Blow Molding
I remember my first time using blow molding for a project. It involved creating a simple but iconic lightweight plastic bottle. Watching the molten plastic expand inside a mold to form thin, strong walls was truly amazing. This method is great for making lightweight products:
-
Material Distribution Characteristics: Blow molding lets you create very thin and evenly spread walls. When designing plastic bottles, this ability to use less material while keeping strength was revolutionary for me. It reduced costs and helped the environment. Low costs and eco-friendliness matter to me.
-
Process Flexibility: What I admire about blow molding is its adaptability. When working on small toys with strict weight limits, this method allowed control over wall thickness. This adaptability supports creative designs. It lets me reach the desired weight while maintaining quality.
When to Choose Injection Molding
On the other hand, injection molding also has special benefits:
-
Precision and Complex Shapes: For a project with electronic devices, I needed a housing with intricate internal details. Injection molding was vital here. It provided high precision and kept the design appealing. These products may not be as light as blow-molded ones; however, they offer strong structure.
-
Challenges with Material Utilization: A challenge with injection molding is managing waste from gates and runners. It affects efficiency. To reduce waste, blow molding might be better; but with complex designs, injection molding is essential even if it adds some weight.
Decision-Making Framework
When choosing between these methods, I use a decision-making framework that helps clarify my choices:
Factor | Blow Molding | Injection Molding |
---|---|---|
Material Utilization | High efficiency, less waste | Generates material waste |
Product Weight | Lightweight, thin walls | Heavier due to thicker walls |
Design Complexity | Simpler shapes | Highly complex designs |
Production Speed | Fast for large quantities | Moderate speed with setup time |
Cost-Effectiveness | Lower material costs | Higher tooling costs |
This table can help you evaluate which process aligns best with your project’s specific needs. Use this as a starting point for deeper analysis by considering your product’s functional and aesthetic requirements.
Practical Considerations
From experience, it’s key to closely assess your product needs:
- Are lightweight features or complex shapes more important?
- What about production volume? Blow molding is more cost-effective for high-volume simple shapes; injection molding suits smaller complex designs.
- Consider long-term aspects like design changes or scaling production.
By analyzing these factors carefully, I’ve made better choices aligned with my project goals. If you’re curious about refining your design process, look into advanced techniques3 that can enhance both methods.
Blow molding is ideal for lightweight product manufacturing.True
Blow molding produces thin-walled, lightweight products, making it suitable for items like plastic bottles where material conservation is crucial.
Injection molding is more wasteful than blow molding.True
Injection molding generates material waste through gates and runners, unlike blow molding which has higher efficiency and less waste.
What Innovations Are Shaping the Future of Molding Processes?
Let’s explore the exciting world of molding processes. Innovative technologies reshape industries. Production becomes more efficient. Industries become more sustainable. Quality improves greatly. This journey is really fascinating!
Innovations shaping the future of molding involve advanced technologies. IoT provides real-time monitoring. 3D printing allows fast prototyping. New methods use recyclable materials. These advancements increase efficiency. They also lower waste. Product quality also improves across various industries.
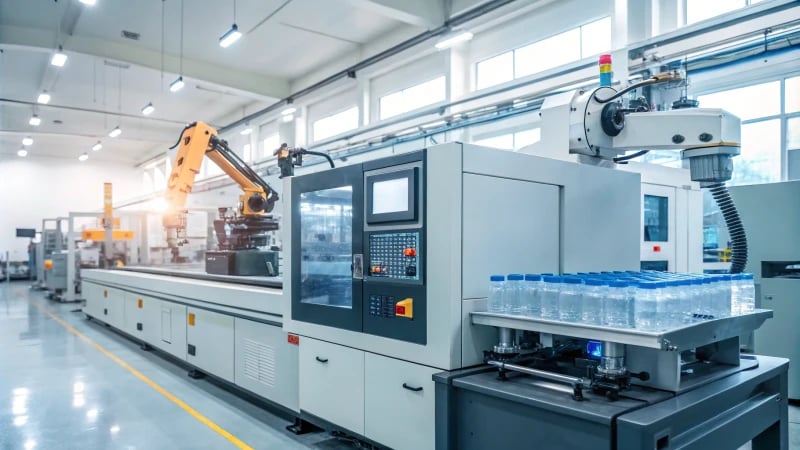
The Rise of Advanced Technologies in Molding Processes
Thinking about how molding processes have evolved fills me with awe. Technology has advanced so much that the possibilities seem endless now. One major breakthrough is the use of Industry 4.0 technologies. Smart sensors and IoT connectivity come together to keep an eye on molding processes in real time. It feels like having a helpful assistant who makes sure everything goes smoothly! This technology allows changes that improve product quality and cut down on waste.
Long ago, downtime was a big issue. Predictive maintenance now helps us avoid those dreaded production halts. Additionally, the rise of 3D printing in mold creation has changed the game. Designers, like me, use this method to create and test different versions quickly. It’s thrilling to make complex designs that traditional methods can’t achieve. During a medical device project, customization became crucial. 3D printing let us try out unique shapes, making our design process efficient and creatively satisfying.
Blow Molding: A Game Changer for Lightweight Products
Blow molding stands out for producing lightweight goods due to its unique material distribution characteristics. By utilizing a molten plastic parison, the blow molding process can create thin-walled structures while maintaining integrity. This method not only reduces material usage but also results in lighter products, crucial for industries focused on sustainability.
Aspect | Blow Molding | Injection Molding |
---|---|---|
Material Distribution | Even and thin-walled | More challenging to achieve thin walls |
Product Types | Hollow lightweight products | Complex shapes with precision |
Material Waste | Less waste due to direct shaping | Higher waste due to runners and gates |
Flexibility | Adjustable inflation for designs | Limited by mold complexity |
Flexibility in creating hollow, variously shaped products is another fascinating feature of blow molding. Weight was key when making small toys. Precise parison inflation enabled extremely light items with thin walls. This process meets specific design needs creatively.
Injection Molding: Precision Meets Complexity
While blow molding excels in lightweight production, injection molding captivates for creating precise items with complex designs. Many projects, like small electronic casings, need both durability and visual appeal. Wall thickness control is vital in this process, as thin walls risk strength.
Innovations like multi-material injection molding shine as they allow combining different materials in one process. I designed a part requiring both flexibility and stiffness; this method was ideal as it added functionality without extra weight.
Sustainability in Molding Processes
Sustainability now plays a big role in our industry. Many manufacturers use recyclable materials and bio-based plastics which address environmental concerns while meeting consumer demands for sustainable goods. Working with firms cutting their carbon footprint is impressive; exploring energy-efficient molding machines showed they work well without losing power.
Recycled materials are also making a splash—minimizing waste and saving on raw material costs is a win-win! Meeting the same quality standards as new materials with these recycled ones remains a challenge we must solve.
Conclusion: The Future Ahead
Looking to the future, innovations in molding processes clearly shape our industry from IoT advancements to sustainable practices; staying informed about trends is really important for everyone in the field. Embracing these changes not only improves our design and production strategies but also positively impacts the environment.
Curious about specific innovations or trends? Check out latest technologies in molding4 or explore sustainable practices in manufacturing5. Let’s keep exploring and pushing boundaries together!
Industry 4.0 technologies improve molding process efficiency.True
The integration of Industry 4.0 technologies enhances real-time monitoring, leading to better efficiency and product quality in molding processes.
Blow molding is unsuitable for lightweight product manufacturing.False
Contrary to this claim, blow molding is ideal for creating lightweight products due to its unique material distribution capabilities.
Conclusion
Blow molding is ideal for lightweight, hollow products, while injection molding excels in precision and complex shapes. Understanding these methods aids product design decisions.
-
Discover more about the practical applications of both methods to choose the right one for your project. ↩
-
Learn about innovative methods to optimize raw material usage and reduce costs. ↩
-
Discover detailed insights that will guide you in making informed decisions between blow molding and injection molding processes. ↩
-
Exploring these topics can provide you with valuable insights into current trends that can enhance your design strategies. ↩
-
Understanding sustainable practices can help you align your designs with market demands for eco-friendly solutions. ↩