Being a product designer, I understand the importance of selecting the correct molding process. This decision is crucial. It might determine whether your product succeeds or fails.
Blow molding has several limits compared to injection molding. It allows only simple shapes. Accuracy in dimensions remains low. The appearance quality is poor. These issues affect design options. Precision and looks are very important.
Today, I want to share my thoughts on blow molding and injection molding. I’ve noticed the frustrations that arise from blow molding’s limits. For example, when designing a complex bottle, I learned blow molding struggled with complex shapes. This taught me how these processes affect our designs. Low dimensional accuracy and poor surface quality have also troubled me in projects. Precision is really important. Let’s explore these challenges together!
Blow molding offers higher shape complexity than injection molding.False
This claim is false; blow molding has restricted shape complexity compared to injection molding, limiting design options.
Injection molding provides better dimensional accuracy than blow molding.True
This claim is true; injection molding typically offers superior dimensional accuracy compared to blow molding, making it suitable for precision applications.
What are the common applications of blow molding?
Do you ever think about how plastic things you use every day are created? Blow molding plays an important role in forming these products. This fascinating process really shapes many items we use daily. Let’s look at the most common uses of blow molding together!
Blow molding is often used in packaging, like bottles. It is frequently found in consumer goods, such as toys. This method is also utilized for industrial parts, including fuel tanks. Blow molding shapes hollow objects rapidly. This makes it very important in these areas.
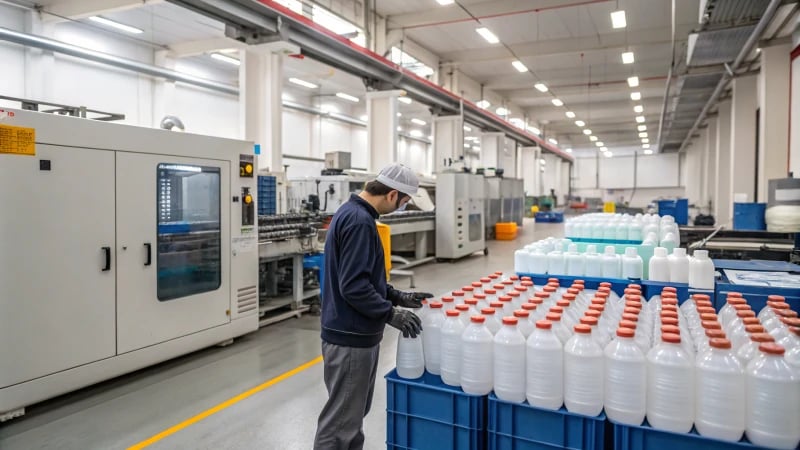
Blow molding is a versatile manufacturing process widely used across various industries, primarily for creating hollow plastic products. Here, we will explore some of the common applications of blow molding in detail.
Packaging Industry
One of the most prominent applications of blow molding is in the packaging industry. This includes:
Product Type | Examples | Description |
---|---|---|
Bottles | Soda and shampoo bottles | Used for beverages and liquids |
Jars | Cosmetic and food jars | For storage of various products |
Containers | Chemical and industrial drums | Safe storage and transportation |
Blow molding allows for the production of lightweight yet sturdy containers that can hold a variety of substances. The process is particularly advantageous because it offers high production rates with consistent quality, making it ideal for large-scale manufacturing. Learn more about packaging1.
Consumer Goods
Another significant application lies in the consumer goods sector. Examples include:
Product Type | Examples | Description |
---|---|---|
Toys | Hollow toys | Lightweight and safe for children |
Household items | Storage bins | Durable and easy to stack |
Sporting goods | Kayaks and inflatable items | Designed for recreational use |
Products made through blow molding in this sector are often designed to be both functional and appealing. The manufacturing process allows for a variety of colors and finishes, catering to consumer preferences. Explore consumer goods2.
Industrial Components
Blow molding also finds its place in the industrial sector. Here are some applications:
Product Type | Examples | Description |
---|---|---|
Fuel tanks | Automotive fuel tanks | Lightweight and resistant to corrosion |
Pipes | Plumbing pipes | Used in various plumbing applications |
Housings | Electronic equipment housings | Provides protection for sensitive components |
In these applications, the process is utilized to create robust parts that can withstand harsh environments and chemical exposure. The ability to produce complex shapes, although limited compared to injection molding, still meets specific industrial requirements effectively. Check out industrial components3.
Limitations and Considerations
While blow molding offers many advantages, it does come with certain limitations that should be noted:
- Limited Shape Complexity: The external shapes are usually regular; complex shapes may be hard to achieve.
- Low Dimensional Accuracy: Wall thickness control can be challenging, leading to variances in product dimensions.
- Poor Appearance Quality: Surface imperfections such as marks and unevenness may occur during production.
These factors can affect the choice of blow molding for specific applications. Understanding these limitations is crucial for designers like Jacky, who aim to meet both aesthetic and functional requirements in their products. Discover more about limitations4.
Blow molding is primarily used for hollow plastic products.True
This process is specifically designed to create hollow shapes, making it ideal for various applications like bottles and containers.
Blow molding is unsuitable for producing complex shapes.True
The blow molding process has limitations in creating intricate designs, focusing instead on more regular external shapes.
How does the cost of blow molding compare to injection molding?
Ever thought about the difference in costs between blow molding and injection molding? Let’s explore the details of these two popular manufacturing methods. These methods really influence a product’s success.
When you compare blow molding and injection molding, consider expenses for materials, tooling, production size, labor and maintenance. Understanding these factors helps you pick the best method for your needs. I learned this in my early product design days.
Understanding Cost Factors in Blow Molding and Injection Molding
As I dug deeper into manufacturing, I saw how crucial it was to grasp the costs in blow molding and injection molding. Both have unique benefits and drawbacks that affect expenses significantly.
Material Costs:
Blow molding usually uses less material than injection molding, especially for hollow items. This often leads to savings, particularly for high-volume production of simple shapes. However, intricate designs might need more tools or redesigns, which quickly increase costs!
Tooling Costs:
Tooling costs heavily influence expenses for both methods. Injection molds frequently cost more due to their complexity and precision requirements. I remember a project where these costs were overwhelming! Blow molding molds, although simpler, can also be pricey with large production volumes. Here’s a quick comparison:
Production Volume Considerations
Production volume really impacts cost-effectiveness. Blow molding often excels in large production runs. Injection molding fits smaller runs with fewer units due to initial tooling investment.
High Volume:
In large quantities, like bottles or containers, blow molding becomes very efficient. The unit cost drops via reduced waste and faster cycles.
Low Volume:
Injection molding works well in low to medium volumes, especially if the design complexity justifies its higher tooling costs.
Labor and Operational Costs
Labor expenses differ too. Blow molding machines typically need less manual handling and have faster cycles. This results in lower labor costs per unit. Injection molding, however, often involves complex setups and maintenance, raising labor demands considerably.
Maintenance and Downtime
Machinery maintenance is another point. Injection molds require frequent adjustments due to complexity. Blow molds, being less complex, might lead to lower maintenance costs. When budgeting, include regular maintenance and potential unexpected downtime.
Conclusion
In conclusion, blow molding might seem cheaper for large runs regarding material use and labor. However, injection molding offers higher quality and precision for complex designs despite greater initial expenses. If you’re like me starting out, exploring the cost analysis of each process supports well-informed decisions.
For those curious about comparisons, looking at case studies from industry experts provides useful insights into real-world uses and their financial effects. Trust me, diving into these resources is very worthwhile!
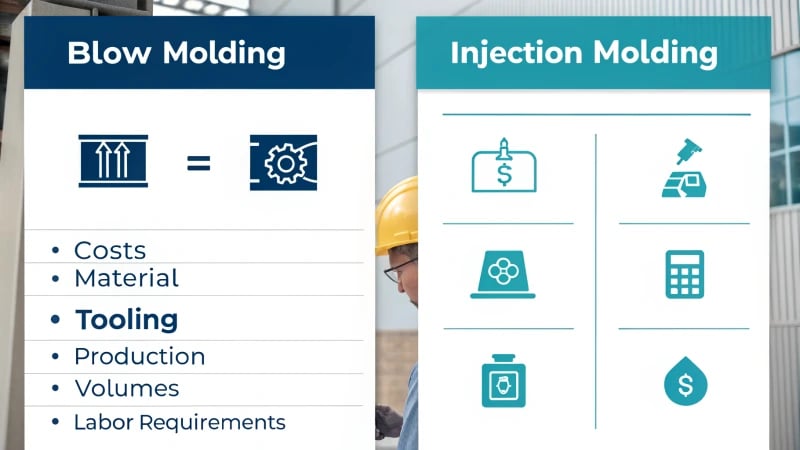
Understanding Cost Factors in Blow Molding and Injection Molding
Knowing the costs of blow molding and injection molding is very important for people in manufacturing. I recall my early days in product design. The technical terms and cost considerations seemed confusing. However, once I understood them, things became clear. Let’s explore this topic together!
When comparing the costs of blow molding and injection molding, several factors come into play. Each method has its own set of advantages and disadvantages that can significantly affect production expenses.
Material Costs:
Blow molding generally utilizes less material compared to injection molding, especially for hollow products. This can lead to lower raw material costs, making it an attractive option for high-volume production of simple shapes. However, the limitations in shape complexity might require additional tooling or redesigns for more intricate designs, thus increasing costs.
Tooling Costs:
The tooling cost is a significant aspect of both processes. Injection molds tend to be more expensive due to their complexity and the precision required for high-quality output. Blow molding molds are simpler but still can have considerable costs, particularly when producing high volumes. The following table summarizes the typical tooling costs:
Process Type | Typical Tooling Cost Range | Complexity |
---|---|---|
Blow Molding | $500 – $2,500 | Low |
Injection Molding | $1,000 – $10,000 | High |
Production Volume Considerations
Production volume plays a crucial role in determining cost-effectiveness. Blow molding is often more cost-effective for large-scale production runs, while injection molding can be more beneficial for smaller runs where the initial tooling investment is amortized over fewer units.
- High Volume: For products like bottles or containers, blow molding becomes increasingly efficient as production scales up. High volume reduces the unit cost significantly due to lower material waste and faster cycle times.
- Low Volume: Injection molding shines in low to medium volume production where design complexity justifies the higher tooling costs.
Labor and Operational Costs
Labor costs can also differ between the two methods. Blow molding machines typically require less manual intervention and have faster cycle times, which can lead to lower labor costs per unit produced. On the other hand, injection molding processes might involve more intricate setups and maintenance which can increase labor requirements.
Maintenance and Downtime
The maintenance of machinery is another factor that can influence overall costs. Injection molds can require frequent adjustments and maintenance due to their complexity. In contrast, blow molds tend to be less complex and may incur lower maintenance costs over time. Regular maintenance schedules and unexpected downtime should also be factored into the overall cost evaluation.
Conclusion
In summary, while blow molding generally appears cheaper in terms of material usage and labor for large runs, injection molding may provide better quality and precision for complex designs at a higher initial investment. To make an informed decision, consider exploring more about cost analysis5 of each process.
For those interested in detailed comparisons, reviewing case studies6 from industry experts can shed light on real-world applications and their financial implications.
Blow molding generally has lower material costs than injection molding.True
Blow molding uses less material for hollow products, reducing raw material expenses in high-volume production.
Injection molding is always cheaper than blow molding.False
This claim is false; blow molding can be more cost-effective for large-scale production despite higher tooling costs for complex designs.
What factors should I consider when choosing a molding process?
Selecting the right molding process resembles standing at a crossroads. Each path leads to a different result for your product. Several important factors influence your decision. These factors determine your project’s success. Your project depends on these decisions.
When you choose a molding process, think about the material type. Look at the production volume too. Know the desired product characteristics. Consider the cost implications carefully. Each factor is very important. Every one of these factors contributes to the success of your manufacturing project.
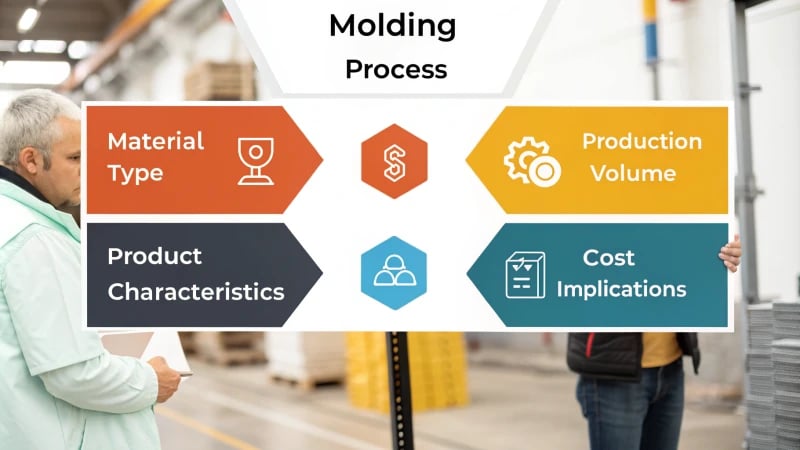
When choosing a molding process, several critical factors should be evaluated to ensure the right fit for your specific needs. Let’s break these down further:
Material Type
The material is the backbone of your product. It decides many things. Every material has a different character. For example, thermoplastics are very flexible for injection molding. You melt and reshape them many times, which is perfect for repeated designs. But thermosetting plastics in compression molding harden permanently. If you choose wrong, the product might not work.
Understanding how materials interact with processes is vital. It probably decides if production runs smoothly or faces setbacks. If you want more information, see material properties in molding7.
Production Volume
Production volume is also important. I remember choosing between a large launch and a limited edition. Different processes work better for different needs:
Molding Process | Ideal Production Volume | Notes |
---|---|---|
Injection Molding | High | Best for mass production |
Blow Molding | Medium to High | Suitable for hollow products |
Compression Molding | Low to Medium | Good for smaller batches |
High-volume production often uses injection molding due to its speed and efficiency. However, for unique or smaller projects, compression molding might save money without losing quality. Learn more about production efficiency8.
Desired Product Characteristics
What do you want in your finished product? Here is where the magic is! Factors like shape and finish affect your choice:
- Shape Complexity: I once designed with complex patterns. Blow molding couldn’t achieve those details; injection molding did.
- Dimensional Accuracy: Precise parts like mechanical ones demand injection molding as it provides the tight fit that blow molding does not.
- Surface Finish: Injection-molded products usually have smooth and polished surfaces while blow molded might have marks or uneven surfaces.
Matching these traits with your project’s goals is essential. Find more at product characteristics9.
Cost Considerations
Face it – budget is vital. Understand costs clearly:
- Initial Setup Costs: Injection molding has high upfront costs for mold creation but pays off in large runs.
- Operational Costs: Consider the cost per unit produced; while injection molding seems expensive initially, the lower cost per unit can be worth it at scale.
- Material Costs: The materials chosen affect total costs; some need special inputs raising expenses.
Knowing these cost factors helps you budget well. Explore molding process costs10 to learn more.
Choosing a molding process need not be daunting. Understand your needs and use the right method. This journey of considerations guided me, and I hope it helps guide you too.
Injection molding is ideal for high-volume production.True
Due to its speed and efficiency, injection molding is best suited for producing large quantities of parts quickly.
Blow molding is suitable for complex shapes.False
Blow molding is generally limited to simpler shapes, making it less ideal for intricate designs compared to other methods.
How Can We Improve Blow Molding to Overcome Its Limitations?
I have experienced the ups and downs of blow molding. I have observed its advantages and disadvantages clearly. Blow molding is a fascinating process. New technology and materials may truly change its abilities. Let’s explore this topic together.
Blow molding probably gets better! Use advanced materials for smoother flow. Optimize mold designs to handle complexity. Control process parameters very precisely. These strategies significantly expand capabilities. Surface treatments also really increase product quality.
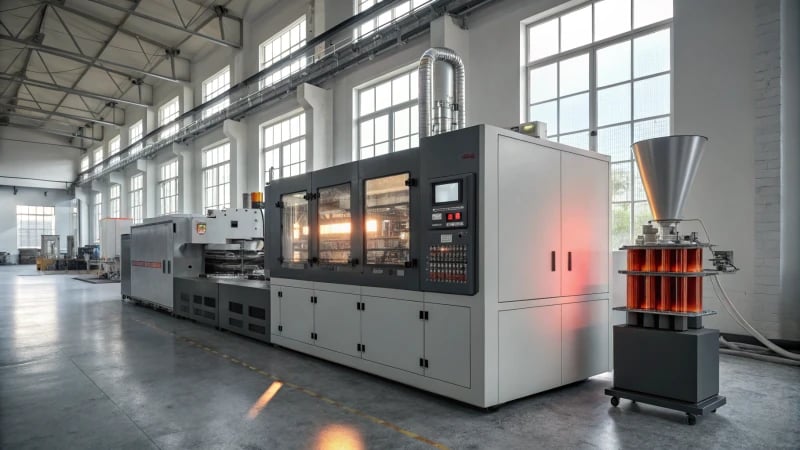
Understanding Blow Molding Limitations
On my journey as a product designer, I often used blow molding to create hollow products like bottles and containers. Though this method is a favorite, it has limitations, including:
- Limited Shape Complexity: I worked on a project needing intricate designs. Blow molding handles simple shapes well. However, when I tried complex buckles or fine patterns, I faced problems with uneven wall thickness and my designs did not come out as planned.
- Low Dimensional Accuracy: Getting precise wall thickness felt like balancing on a tightrope. Many factors like blow ratio and air pressure influenced this. I found it hard to keep the consistency needed for precise products, which was a big issue for mechanical parts where every millimeter is vital.
- Poor Appearance Quality: I noticed the frustration on my team’s faces with blow-molded products due to surface imperfections. Marks and uneven surfaces often ruined the final product. Injection molding offered much smoother finishes by comparison.
Innovations to Improve Blow Molding
To tackle these issues head-on, I explored some innovations that might transform the blow molding process:
- Advanced Materials: I am very excited by new polymer blends with better flow characteristics. These materials could help reproduce complex shapes more effectively; improved elasticity might lead to better mold filling.
- Optimized Mold Designs: Adjustable cavity molds spark my imagination; innovative designs may allow complex shapes with dimensional accuracy. There is plenty of potential in advanced mold-making technologies11.
- Process Parameter Control: Sophisticated monitoring of parameters like temperature and pressure could be a big change; real-time data could help maintain better wall thickness and dimensions, boosting production efficiency.
Strategies for Enhancing Surface Quality
Improving surface quality is key to market success; here are strategies I find very useful:
- Surface Treatment Techniques: Post-production treatments like polishing and coating can significantly elevate product appearance. Utilizing surface treatment methods tailored for blow-molded products could help minimize initial imperfections.
- Flow Simulation Software: Using simulation tools changed my approach; they help predict and resolve surface quality issues before production, ensuring the final product meets high standards.
Conclusion and Future Directions
The future of blow molding really excites me! Continuous improvement through innovative technology and advanced practices could elevate this industry. Research and development are crucial; exploring new possibilities in material science and process engineering will help overcome existing limitations effectively.
Blow molding is limited in producing complex shapes.True
Blow molding excels at simple shapes but struggles with intricate designs, leading to uneven wall thickness and potential product failure.
Advanced materials can enhance blow molding capabilities.True
Utilizing new polymer blends improves flow characteristics, allowing for better reproduction of complex shapes in blow molding processes.
Conclusion
Blow molding has limitations like simple shapes, low accuracy, and poor surface quality compared to injection molding, impacting design choices for product designers.
-
Clicking this link will provide you with deeper insights into how blow molding is utilized in the packaging industry, enhancing your understanding of its importance. ↩
-
This link offers a comprehensive overview of consumer goods produced through blow molding, illustrating its versatility in everyday products. ↩
-
Exploring this link will reveal various industrial applications of blow molding, showcasing its role in producing robust components. ↩
-
By following this link, you will learn about the limitations of blow molding, which is crucial for making informed design choices. ↩
-
Discover insightful cost comparisons between blow molding and injection molding that can guide your manufacturing decisions effectively. ↩
-
Explore case studies that highlight financial outcomes from using blow molding versus injection molding in different manufacturing contexts. ↩
-
This link provides a comprehensive overview of material properties relevant to different molding processes, helping you make informed decisions. ↩
-
Explore production efficiency insights that can guide your choice of molding techniques based on anticipated volume. ↩
-
Learn about various product characteristics and how they influence the selection of an appropriate molding method. ↩
-
Find detailed information on costs associated with different molding processes to aid in your budgeting. ↩
-
Discover new techniques that can enhance blow molding processes and address its common limitations effectively. ↩