Ever thought about how those reliable plastic bottles in your fridge are created? Let’s explore the interesting world of blow molding together!
Blow molding is ideal for producing bottles and containers due to its efficiency, cost-effectiveness, ability to create uniform hollow structures, flexible shape options, and high production efficiency, making it a preferred method in the plastics industry.
Blow molding fascinates me because it is efficient and versatile. This method creates bottles and containers. I remember seeing a parison turn into a perfectly formed bottle. It felt like watching magic. Blow molding helps form hollow structures. This is very important for storing drinks and cleaning products.
I value how blow molding keeps material even. Every bottle stays strong and reliable. Bottles can hold fizzy drinks or water. The process allows for easy changes in shape and size. There are really no limits to creative design. The technique is affordable and highly productive. Manufacturers, like me, often choose blow molding for these reasons.
Blow molding is the most efficient method for bottle production.True
Blow molding offers high production efficiency, making it ideal for manufacturing bottles and containers quickly and cost-effectively.
Blow molding can only produce rigid plastic containers.False
Contrary to this claim, blow molding can create both rigid and flexible hollow structures, expanding its application range.
What Are the Different Types of Blow Molding Processes?
Ever wonder how sleek plastic bottles and containers are produced? Understanding various blow molding processes probably helps in choosing the right method for projects. Let’s explore the intriguing world of blow molding!
Blow molding includes extrusion blow molding, injection blow molding and injection stretch blow molding. Each method offers different benefits and suits various applications for making hollow plastic products. Understanding these methods assists in selecting the best one for your project.
Extrusion Blow Molding
Extrusion blow molding is a common method for creating hollow plastic products. Imagine a long tube of melted plastic, called a parison, that is pushed out and pressed into a mold. Air is blown inside it, expanding to perfectly fill the mold’s shape. It works well for large containers like bottles and tanks because it easily forms hollow structures.
Advantages:
High production efficiency: This method operates continuously. It’s impressive.
Cost-effective: Simpler molds than injection methods add even more value.
Learn more about extrusion extrusion techniques.
Injection Blow Molding
Let’s consider injection blow molding. This combines injection molding and blow molding with precision. First, a preform is made using injection molding, then it moves to a blow mold. Air then shapes it into its final form.
Key Features:
High precision: Wall thickness remains very uniform.
Versatile shapes: Allows for intricate designs, like uniquely shaped bottles.
Discover more on injection blow molding injection methods.
Injection Stretch Blow Molding
Now, meet injection stretch blow molding. This method stretches the preform before blowing it into shape. The stretching aligns the polymer molecules, making the final product stronger and clearer.
Common Applications:
- Ideal for PET bottles for drinks due to their strong yet lightweight nature.
For details on this process, view stretch blow molding insights.
Comparison of Blow Molding Types
Understanding these processes is important for designers needing the right method for their needs. Explore further blow molding technologies. I remember Jacky, a designer, who deeply compared these methods for a new bottle line. This knowledge was crucial for him.
Whether you’re working on a project or just curious about how things are made, I hope this exploration into blow molding offers clarity! Let’s continue learning together!**
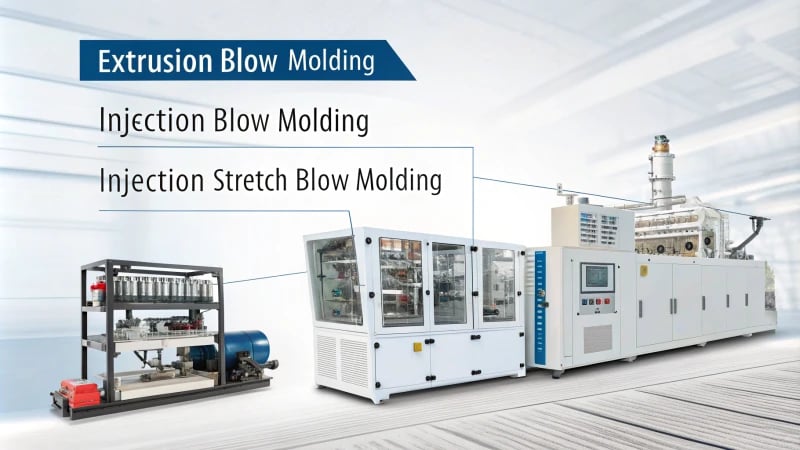
Blow molding is a fascinating process that creates hollow plastic shapes. Trust me, it’s more exciting than it sounds! This technique truly sparks interest. I recall seeing this process in action for the first time. It felt like watching a sculptor at work. However, instead of clay, molten plastic took center stage. There are different types of blow molding. Each type has its unique charm and use. Let’s explore them together, okay?
Extrusion Blow Molding
Extrusion blow molding is one of the most commonly used processes in the manufacturing of hollow plastic products.
In this method, a continuous tube of molten plastic, called a parison, is extruded and then clamped into a mold. Compressed air is blown into the parison, expanding it to fill the mold cavity. This process is ideal for creating large containers, such as bottles and tanks, due to its ability to form a hollow structure easily.
Advantages:
- High production efficiency allows for continuous operation.
- Cost-effective due to simpler mold design compared to injection methods.
For more information on extrusion methods, explore extrusion techniques1.
Injection Blow Molding
Injection blow molding combines the principles of injection molding and blow molding. In this method, a preform is first created using injection molding, which is then transferred to a blow mold. Here, air is blown into the preform to achieve the final shape.
Key Features:
- Provides high precision and uniformity in wall thickness.
- Suitable for producing complex shapes and designs.
Consider the benefits of injection blow molding by checking out injection methods2.
Injection Stretch Blow Molding
This process enhances the capabilities of injection blow molding by stretching the preform before blowing it into shape. This stretching aligns the polymer molecules, improving the strength and clarity of the final product.
Common Applications:
- Often used for manufacturing PET bottles for beverages, leveraging its ability to produce strong, lightweight containers.
For detailed insights into this process, view stretch blow molding insights3.
Comparison of Blow Molding Types
Type | Advantages | Disadvantages |
---|---|---|
Extrusion Blow Molding | High efficiency, simpler molds | Limited precision in complex shapes |
Injection Blow Molding | High precision, better wall uniformity | Higher mold costs |
Injection Stretch Blow Molding | Stronger products, great for thin walls | More complex process |
Understanding these processes is crucial for product designers like Jacky who need to choose the right method for their specific applications. For further exploration of blow molding technologies, visit blow molding technologies4.
Extrusion blow molding is ideal for large hollow containers.True
This method efficiently produces large containers like bottles and tanks due to its continuous operation and hollow structure capabilities.
Injection stretch blow molding enhances product strength.True
By stretching the preform, this process aligns polymer molecules, resulting in stronger and clearer final products, especially useful for PET bottles.
How Does Blow Molding Compare to Other Manufacturing Techniques?
Have you ever thought about how blow molding compares to other manufacturing methods like injection molding? Let’s look closely at their differences in efficiency, cost and design flexibility. The facts we discover might really surprise you!
Blow molding is a cheap way to create hollow objects like bottles and containers. It allows very fast and flexible production. Blow molding is really good for making different designs. Unlike blow molding, injection molding works best for solid parts. Blow molding is a great option for many uses.
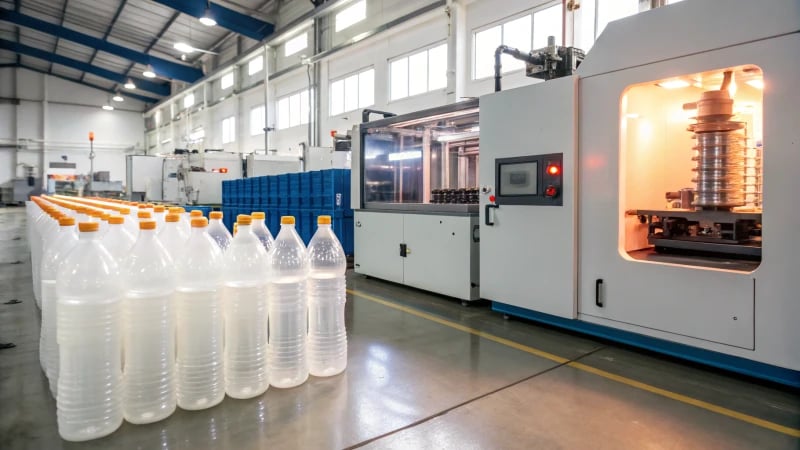
Understanding Blow Molding
I remember the first time I saw blow molding. It felt like entering a world full of possibilities. This special way of manufacturing mainly creates hollow plastic items. It is amazing to see how it works. You take a heated plastic tube called a parison and put it in a mold. Then, compressed air pushes it and the plastic expands. It fills the mold and becomes hollow. Watching this process feels almost magical.
Comparison with Injection Molding
When I first compared blow molding to injection molding, many differences stood out. Injection molding is fantastic for solid parts with intricate designs. However, blow molding is excellent for hollow items like bottles. This difference offers many uses in manufacturing.
For example, blow molding is perfect for products needing a hollow shape, while injection molding focuses on solid forms like those found in many goods. Each technique has its strengths and weaknesses:
Feature | Blow Molding | Injection Molding |
---|---|---|
Product Type | Hollow structures | Solid components |
Material Distribution | Good uniformity | Variable distribution |
Production Speed | Higher efficiency | Moderate speed |
Mold Complexity | Simpler molds | Complex molds |
Cost | Generally lower | Higher |
I realized how important the even spread of material is during blow molding. The plastic stretches under air pressure and spreads evenly inside the mold. This distribution is crucial for keeping the wall thickness consistent, which matters for strength—especially in bottles holding carbonated drinks. It’s indeed about durability.
Flexibility in Design
Blow molding offers great flexibility in shape and size, allowing manufacturers to express creativity. With some mold changes and blow ratio adjustments, you can create round, square or unique containers. This flexibility is great for companies wanting to innovate their products.
Adjusting designs in blow molds is simple and often cheaper than in injection molds. This flexibility reduces the time needed to develop products and cuts down costs, which attracts manufacturers aiming for mass production.
Cost-Effectiveness and Efficiency
Blow molding often proves more cost-effective than other methods due to the simplicity of its molds that reduce production expenses. The process minimizes material waste because the parison fills the mold without needing extra runners, unlike injection molding.
Blow molding usually offers higher efficiency levels as well; once set up, processes like extrusion blow molding maintain high outputs easily—manufacturers achieve impressive results for large batch demands.
Choosing between blow molding and techniques like injection molding requires considering factors like production needs, material specifications, and costs. Understanding these helps me make good decisions for my projects; hopefully, it helps you too.
Blow molding is primarily used for solid plastic parts.False
This claim is false; blow molding is specifically designed for creating hollow plastic parts, unlike injection molding which produces solid components.
Blow molding offers higher production efficiency than injection molding.True
This claim is true; blow molding processes typically maintain higher efficiency rates due to their continuous operation, benefiting large batch production.
Why is Material Selection So Important in Blow Molding?
Did you ever consider the materials in the products we use daily? In blow molding, choosing the right material is very important. It’s the backbone of quality and efficiency. Let’s explore why this is so crucial.
Material choice is very important in blow molding. It affects product strength, production speed and cost. Knowing different materials helps designers like me. Designers create customized solutions. These solutions meet specific needs. They also provide high-quality results.
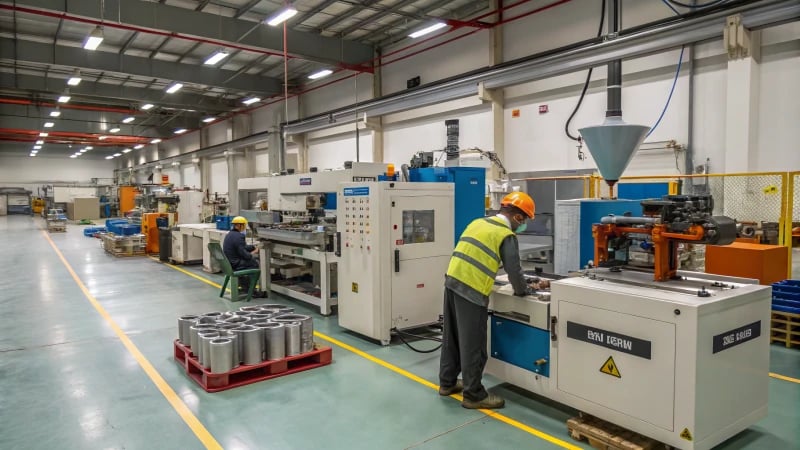
Importance of Material Choice in Blow Molding
Choosing materials is very important in blow molding. It affects not only product performance and durability but also production efficiency. Different materials can significantly affect how well the blow molding process can create products that meet specific design and functional requirements.
Types of Materials Used in Blow Molding
-
Polyethylene (PE)
- Acts as the reliable choice – flexible, strong and budget-friendly.
- Ideal for making containers like bottles and jugs.
-
Polypropylene (PP)
- Great for projects needing heat and chemical resistance. It’s very tough.
- Perfect for durable and impact-resistant items.
-
Polyvinyl Chloride (PVC)
- Stands out with good weather resistance and transparency.
- Useful for unique containers and packaging.
-
PET (Polyethylene Terephthalate)
- Popular for drink bottles due to strength and recyclability.
- Excellent at keeping moisture out, preserving freshness.
-
ABS (Acrylonitrile Butadiene Styrene)
- Known for toughness, used for rigid containers that won’t crack.
Choosing the right material from the above options can enhance the uniformity of material distribution5 during the blow molding process, leading to products with consistent wall thicknesses, essential for maintaining structural integrity under pressure.
The Role of Material Features in Design
Material properties are key for designing blow molded products. Using these features wisely helps create products that not only look good but also function well.
Property | Description | Importance in Blow Molding |
---|---|---|
Tensile Strength | Resistance to being pulled apart | Ensures durability under stress |
Flexibility | Ability to bend without breaking | Important for applications requiring deformation |
Impact Resistance | Ability to withstand sudden forces | Critical for products exposed to physical shock |
Temperature Resistance | Stability under heat | Essential for products used in high-temperature environments |
By selecting materials that align with these properties, designers can ensure that their blow molded products meet both aesthetic and functional requirements effectively.
Cost-Effectiveness Thoughts
Material choice often affects production costs greatly. For instance, materials like PE and PP generally cost less than PET or PVC, making them ideal for high-volume production where saving money is important. The high cost-effectiveness6 of blow molding can be maximized by choosing materials that minimize waste while meeting quality standards, especially when producing large quantities of containers.
Moreover, I also like the flexibility of blow molding; changing product shape and size is possible without major equipment changes, even with different materials.
Conclusion
Looking back at my work in product design, I see how vital material choice is in blow molding. It affects everything from production efficiency to product characteristics. Understanding material effects on performance and cost helps me make smart decisions that lead to better product quality and improved manufacturing processes.
Material selection impacts the durability of blow molded products.True
Choosing the right material enhances product durability, ensuring it withstands stress and environmental factors during use.
Polyethylene is the most expensive material for blow molding.False
Polyethylene is generally less expensive than other materials like PET or PVC, making it a cost-effective choice for production.
Which Industries Truly Thrive with Blow Molding Technology?
Do you ever think about how common things are created? Blow molding changes how hollow plastic products come into being. It’s a big shift across different industries. But which industries benefit the most? Let’s explore!
Industries benefiting most from blow molding technology include consumer goods, automotive, pharmaceuticals, agriculture and cosmetics. Each sector uses this technique for its efficiency. This process is also very cost-effective. It creates custom hollow structures. These structures meet specific needs. They are durable. They perform very well.
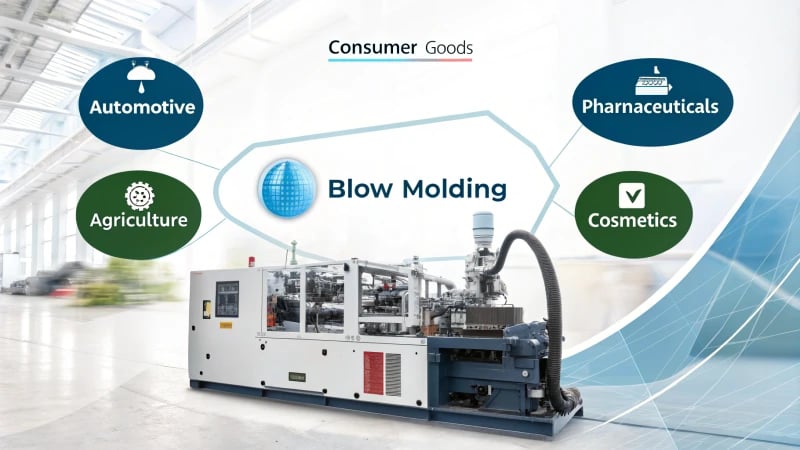
Consumer Goods
Blow molding technology works like magic in the consumer goods industry. It shapes hollow structures for many purposes, including the production of containers for household products such as detergents and personal care items. I first saw this technology and felt amazed. I learned how a simple bottle becomes precise and efficient.
Moreover, with the growing demand7 for sustainable packaging, manufacturers use blow molding to produce recyclable bottles that meet consumer values. It’s nice to see eco-friendly solutions becoming popular.
Automotive Industry
In the automotive sector, blow molding helps create key parts like fuel tanks and bumpers. I first learned how adaptable this technology is for specific vehicle parts. A lightbulb went off in my mind! Manufacturers can change shapes and sizes yet keep safety standards. This method offers a cost-effective way to produce parts in large numbers, supporting cost-effectiveness8 while automakers save money.
Pharmaceutical Sector
The pharmaceutical industry relies on blow molding for product safety. I found blow-molded containers protecting essential liquids and powders intriguing. They keep a tight seal and avoid contamination, making them ideal for storing medicines. Knowing a bottle is precisely made provides peace of mind, especially since these containers handle pressure while safeguarding quality—an important aspect of medication storage9.
Agricultural Applications
Blow molding greatly helps the agricultural sector by providing containers for fertilizers and pesticides. These lightweight yet durable containers suit outdoor conditions well. During busy times, factories produce many containers fast to meet seasonal demands, ensuring farmers receive supplies on time by leveraging efficiency in producing bulk quantities of agricultural containers10.
Cosmetics Industry
In the cosmetics industry, blow molding creates stunning yet practical packaging such as eye-catching shampoo bottles and elegant cream jars. Customizing shapes and sizes helps brands stand out in stores while ensuring product safety inside the container. Additionally, less material waste due to blow molding supports eco-friendly practices11, resonating with many modern consumers.
In summary, whether making durable consumer goods or protecting pharmaceutical products, blow molding technology impacts several industries significantly.
Blow molding is primarily used in the consumer goods industry.True
Consumer goods utilize blow molding for creating lightweight, durable containers for household products, enhancing safety and usability.
The automotive industry does not benefit from blow molding technology.False
Contrary to this claim, blow molding is essential in automotive for producing parts like fuel tanks and bumpers efficiently.
Conclusion
Blow molding efficiently produces hollow plastic products like bottles, offering flexible designs, uniform material distribution, and cost-effectiveness, making it ideal for various industries.
-
Discover essential details about extrusion blow molding processes and their applications in manufacturing. ↩
-
Learn how injection blow molding can enhance precision and efficiency in product design. ↩
-
Understand how injection stretch blow molding improves product strength and clarity. ↩
-
Gain insights into the various blow molding technologies available in modern manufacturing. ↩
-
Explore how material choice influences blow molding processes and product outcomes. Gain insights into optimizing material selection for better performance. ↩
-
Learn about various materials used in blow molding and their specific applications. This link will guide you through key properties and benefits. ↩
-
Explore how different industries utilize blow molding technology to gain insights into its applications and benefits. ↩
-
Discover the impact of blow molding on production costs and efficiency in various sectors. ↩
-
Learn more about the advantages of blow molding in packaging solutions across different fields. ↩
-
Find out how blow molding technology supports sustainability efforts in manufacturing. ↩
-
Uncover the role of blow molding in enhancing product design within the cosmetics industry. ↩