All Posts
blog & article
read our latest newsletter
Whether you’re curious about material selection, product design, mold design, mold making and injection molding, feel free to ask us anything. Our team is ready to provide the guidance and insights you need.
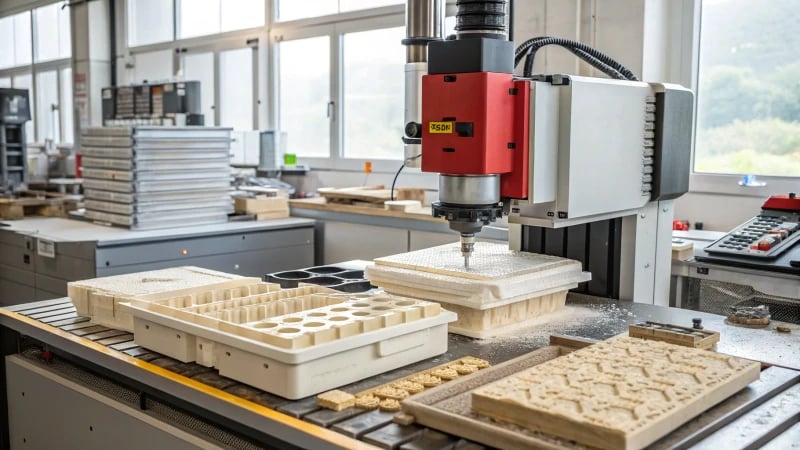
What Challenges Arise When Molding High-Impact Resistant Materials?
Molding high-impact resistant materials involves navigating various challenges such as selecting appropriate materials, designing effective molds, and preventing defects like warping and sink marks. Each challenge requires a blend of technical skill and creativity to ensure product durability and manufacturing ...
Materials Recommendations
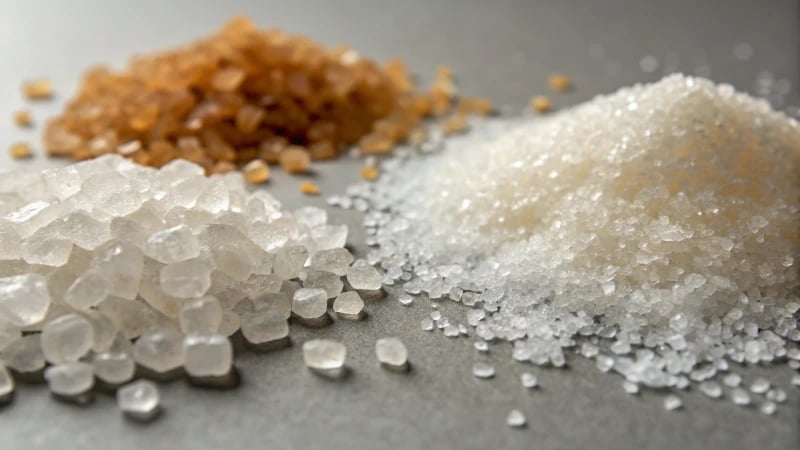
What Impact Do Crystallinity Levels in Polymers Have on Injection Molding Outcomes?
This article explores how crystallinity levels in polymers impact injection molding processes. It discusses the relationship between crystallinity and mechanical properties such as strength, brittleness, and thermal stability. Understanding these factors is essential for optimizing product designs in various applications, ...
MANUFACTURING
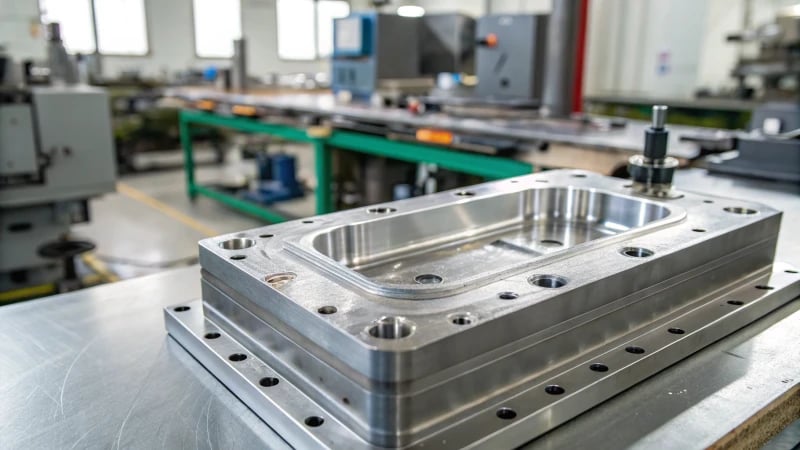
How Do You Design Molds for Achieving High-Gloss Surface Finishes?
Creating high-gloss finishes in molded parts is an intricate process that combines art and engineering. Key factors include choosing the right materials like stainless steel or aluminum, employing advanced polishing techniques, and adhering to industry standards such as SPI. Mold ...
DESIGN
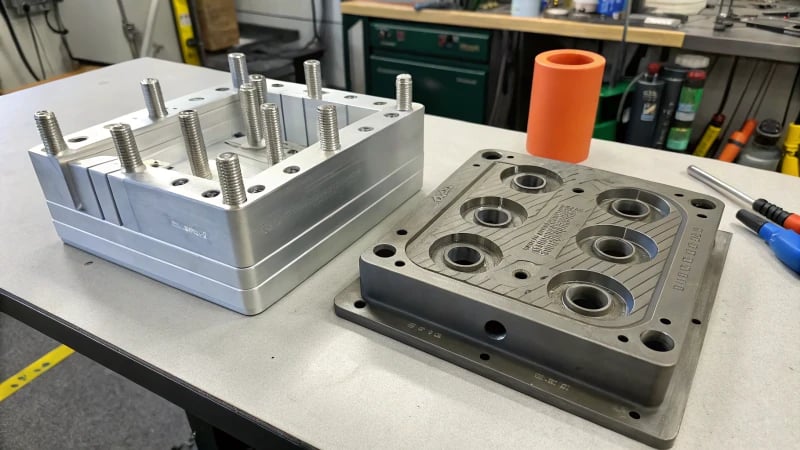
What Are the Differences in Injection Molding for Thin-Wall vs. Thick-Wall Parts?
This article explores the key differences between thin-wall and thick-wall injection molding processes. Thin-wall molding typically requires higher pressure and faster cooling times, enhancing production speed but potentially compromising structural integrity. In contrast, thick-wall molding allows for more leeway in ...
MANUFACTURING
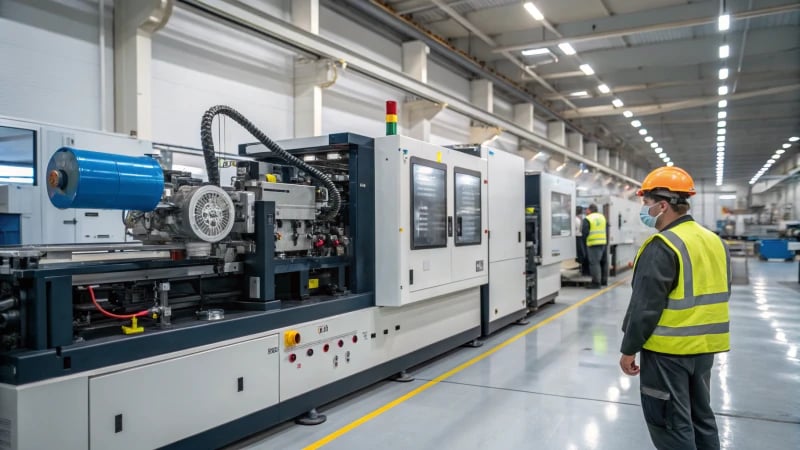
How Can Gas-Assisted Injection Molding Enhance Mold Design?
Gas-assisted injection molding revolutionizes traditional manufacturing by optimizing mold designs. This innovative technique reduces material usage, enhances surface finish, minimizes shrinkage, and allows for intricate geometries. It significantly improves production efficiency while maintaining product integrity. Designers can achieve lightweight components ...
DESIGN
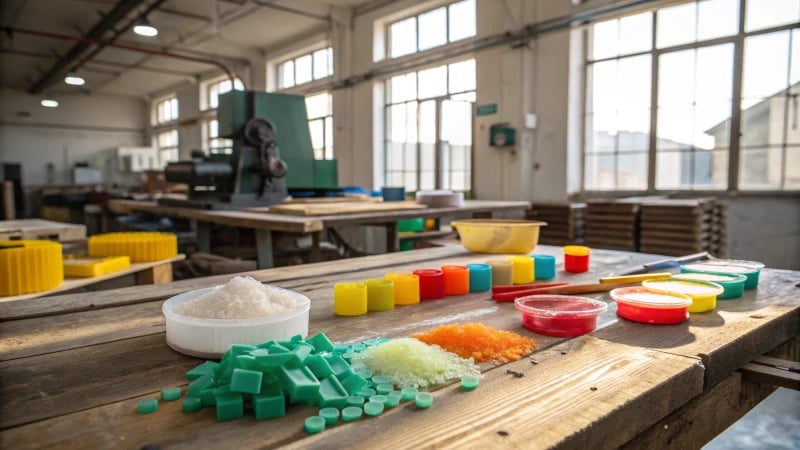
How Do Biopolymers Enhance the Sustainability of Injection Molding?
Biopolymers are revolutionizing the injection molding industry by providing eco-friendly, biodegradable alternatives to conventional plastics. Derived from renewable resources, they help reduce carbon footprints and align with sustainable production practices. However, integrating biopolymers into existing manufacturing processes presents challenges such ...
MANUFACTURING
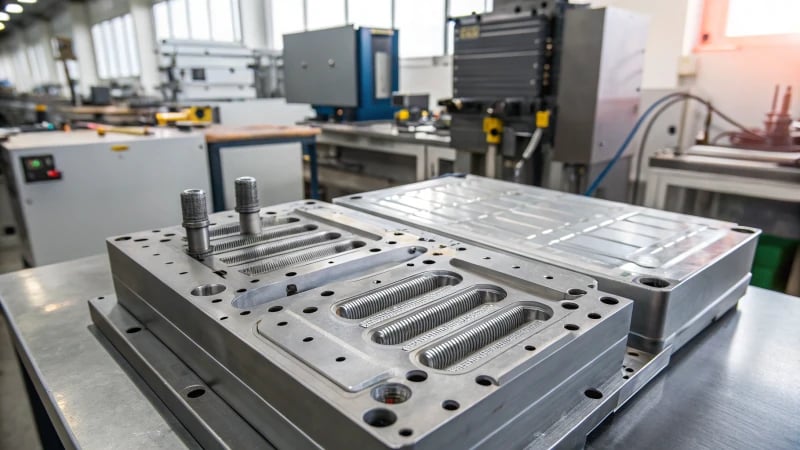
How Can Venting Enhance the Efficiency of Injection Mold Designs?
Venting plays a vital role in injection mold design by facilitating the escape of trapped air and gases during the injection process. This essential step helps reduce defects such as burn marks and voids, improves material flow, and optimizes cycle ...
DESIGN
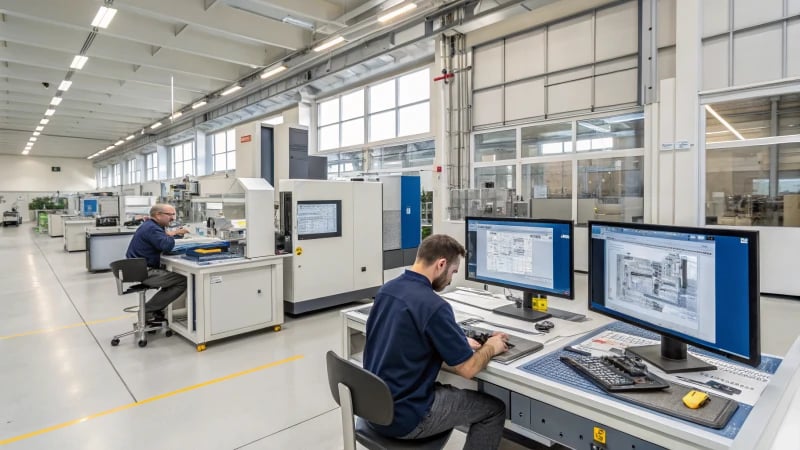
How Can Mold Design Strategies Effectively Minimize Material Waste?
This article explores how effective mold design strategies can minimize material waste in manufacturing. By focusing on techniques such as precise gate placement, optimizing runner systems, and utilizing advanced CAD tools, manufacturers can enhance production efficiency while promoting sustainability. The ...
DEVELOPMENT
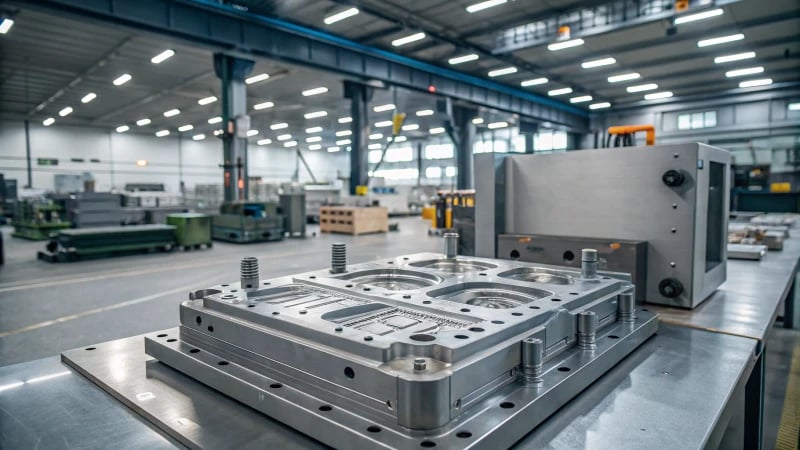
Why Choose Family Molds for Injection Molding: What Are the Benefits?
Family molds are a game-changer in injection molding, allowing manufacturers to produce various components in one cycle. This method significantly cuts production costs and time while optimizing material usage. Ideal for projects requiring diverse parts, family molds streamline operations and ...
MANUFACTURING
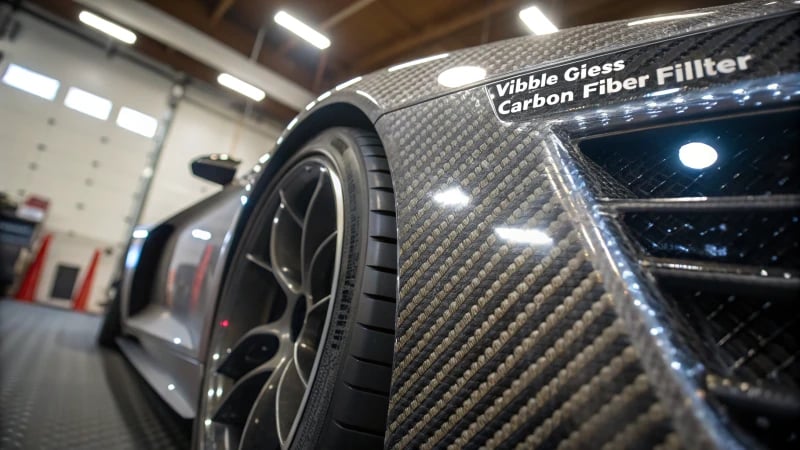
What Impact Do Glass Fiber and Carbon Fiber Fillers Have on the Mechanical Properties of Injection-Molded Parts?
This article explores the impact of glass fiber and carbon fiber fillers on the mechanical properties of injection-molded parts. It highlights how these materials enhance strength, stiffness, thermal stability, and weight reduction. Glass fibers improve durability and thermal resistance, while ...
Materials Recommendations
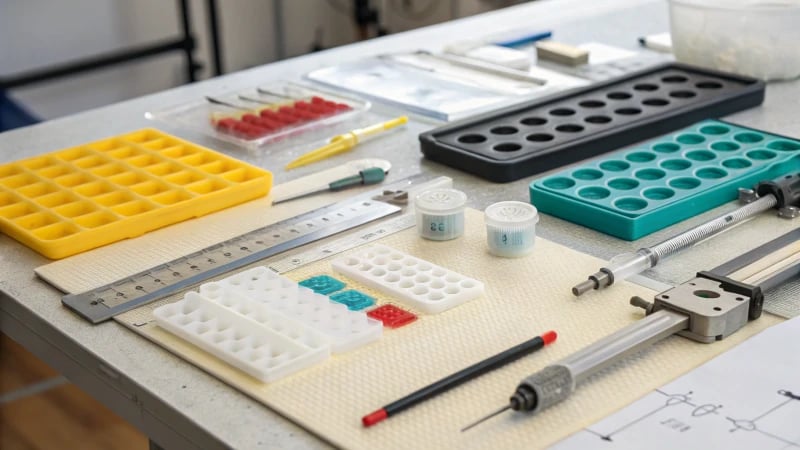
What Are the Best Practices for Choosing Materials in Medical-Grade Injection Molding?
Selecting the right materials for medical-grade injection molding is crucial for developing safe and reliable medical devices. Key factors include sterilization compatibility, mechanical properties like tensile strength and elasticity, biocompatibility to prevent adverse reactions, and adherence to regulatory standards. Understanding ...
Materials Recommendations
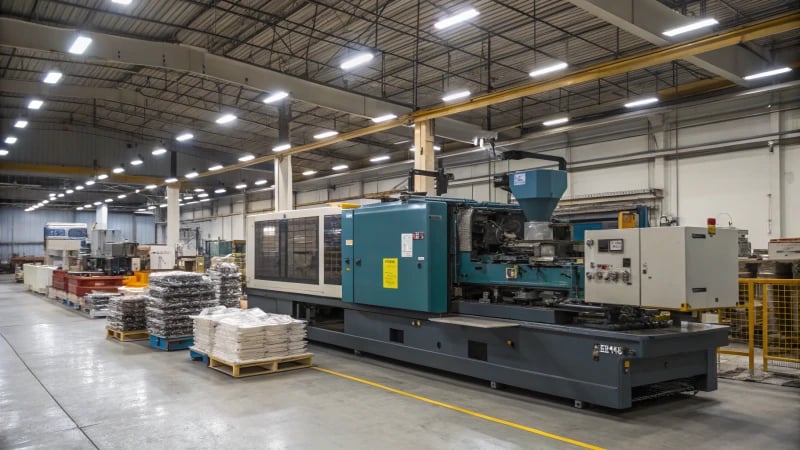
What Are the Challenges of Injection Molding Large-Scale Parts?
This blog explores the complexities of injection molding large-scale parts, highlighting challenges such as managing material volumes, ensuring consistent quality, and dealing with extended cooling times. It emphasizes the importance of selecting appropriate materials to balance cost and performance while ...
MANUFACTURING
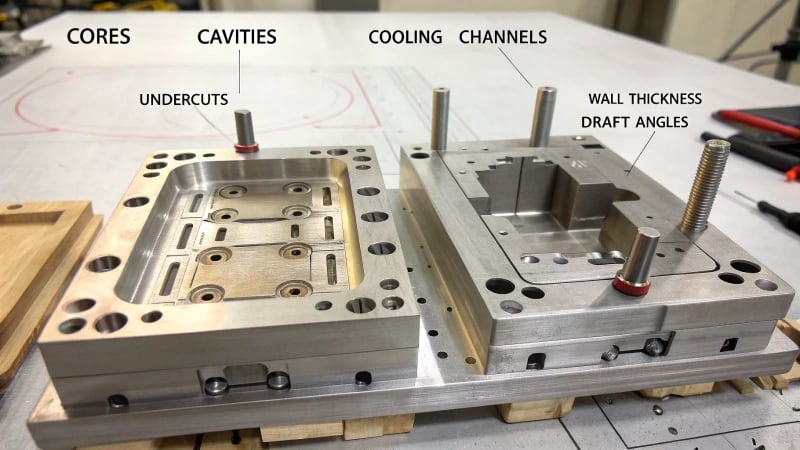
How Does Part Geometry Influence Mold Design in Injection Molding?
This article explores how part geometry affects mold design in injection molding. Key factors such as wall thickness, mold size, core shapes, and undercuts are discussed to highlight their influence on manufacturability and product quality. The importance of draft angles ...
MANUFACTURING
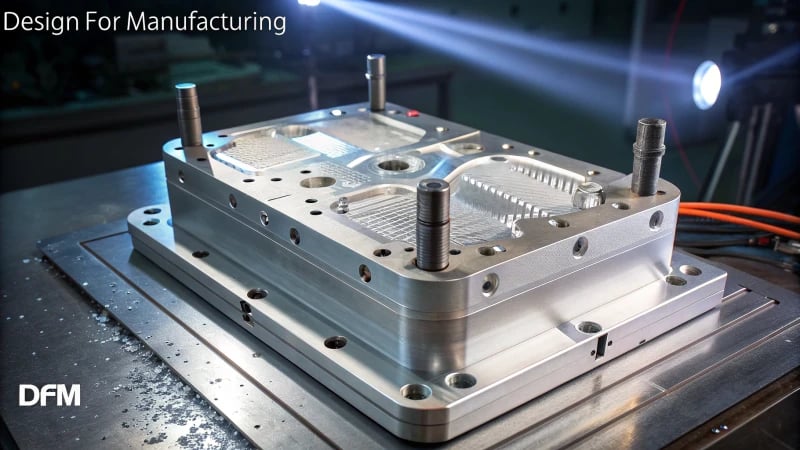
How Can DFM Principles Enhance Injection Mold Design?
Design for Manufacturing (DFM) principles significantly improve injection mold design by streamlining production processes, minimizing costs, and enhancing product quality. By focusing on simplicity, standardization, and ease of assembly, DFM helps designers create molds that are not only functional but ...
DESIGN
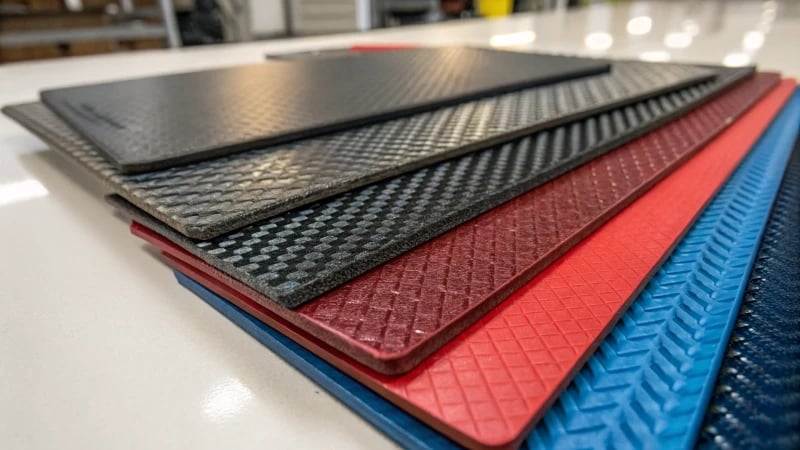
How Effectively Do Flame-Retardant Materials Perform in Injection Molding Applications?
This article explores the effectiveness of flame-retardant materials in injection molding applications, highlighting their crucial role in enhancing fire safety for consumer electronics. It discusses various types of flame-retardants, including halogenated compounds, phosphorous-based additives, and nitrogen-based synergists, each with unique ...
Materials Recommendations
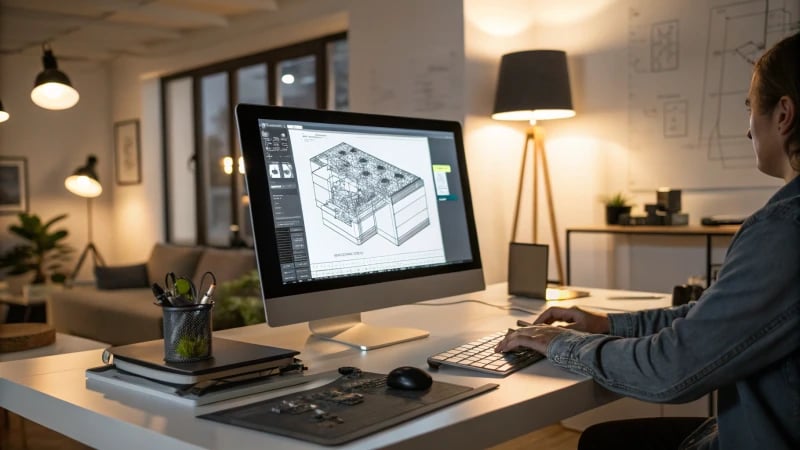
How Does CAD Software Enhance the Design of Injection Molds?
CAD software significantly enhances the design of injection molds by improving precision and efficiency. Key features include 3D modeling for accurate visualization, simulation tools to predict performance, and automated documentation that streamlines communication. These capabilities not only reduce design time ...
DESIGN
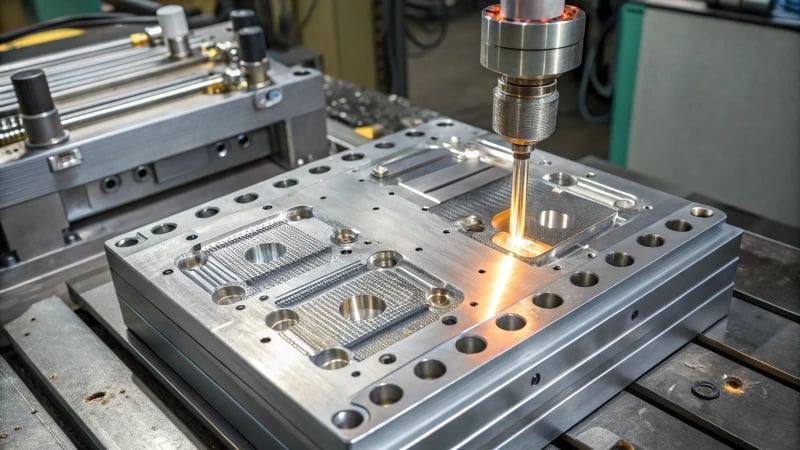
What Are the Essential Factors in Designing Injection Molds for High-Volume Production?
Designing injection molds for high-volume production involves a blend of art and science. Essential factors include careful material selection, optimizing cooling systems, ensuring uniform wall thickness, and precise construction. Utilizing advanced technologies like CAD software streamlines the design process by ...
DESIGN
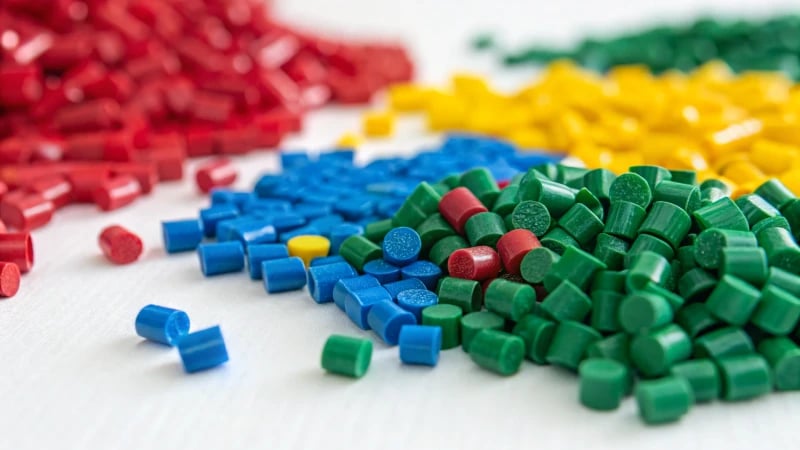
What Are the Latest Advancements in Thermoplastic Elastomers for Injection Molding?
Thermoplastic elastomers (TPEs) are transforming manufacturing with their unique blend of flexibility and durability. Recent advancements have led to enhanced material properties, new formulations, and innovative processing techniques that improve efficiency and reduce costs. TPEs allow for intricate designs, reduced ...
Materials Recommendations
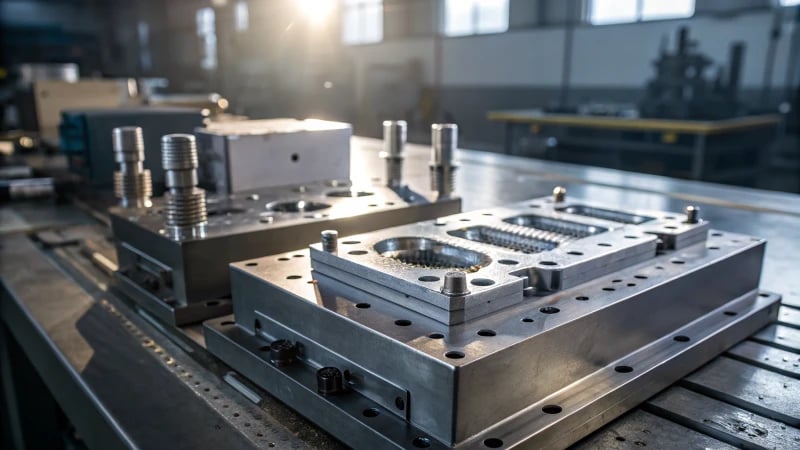
How Does the Choice of Mold Base Impact Your Overall Mold Design?
The choice of mold base significantly influences overall mold design by affecting structural integrity, thermal performance, and production costs. Different types of bases—standard, custom, hot runner, and stripper plate—serve specific needs in manufacturing. Material selection also plays a vital role; ...
MANUFACTURING
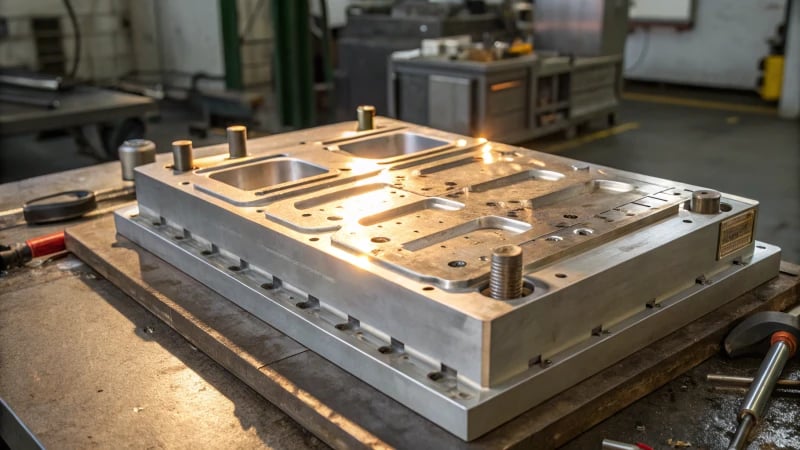
What Challenges Arise When Molding Multi-Material Components?
Navigating multi-material molding involves overcoming challenges such as ensuring material compatibility, designing complex molds, and maintaining efficient production processes. This post explores common hurdles faced in the industry and offers practical strategies to enhance product quality and reduce defects. Key ...
MANUFACTURING
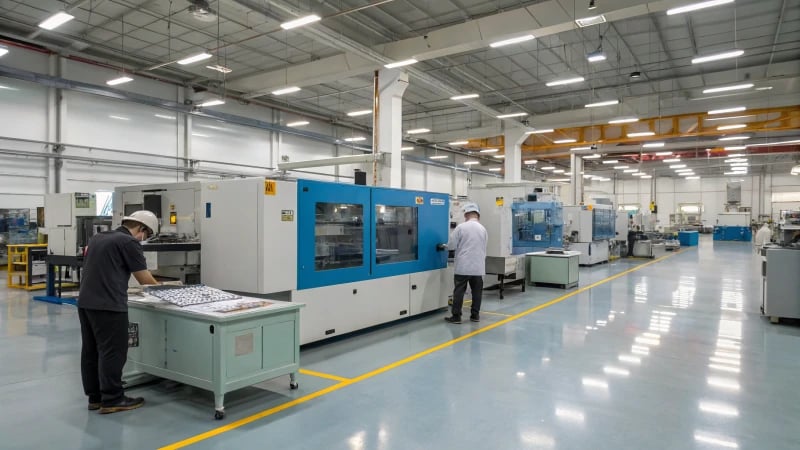
What Are the Key Benefits of ISO 9001 Certification for Injection Molding Operations?
ISO 9001 certification provides significant advantages for injection molding operations. It boosts efficiency, enhances product quality, and improves customer satisfaction. By standardizing processes and focusing on continuous improvement, companies can reduce waste and optimize resource management. This leads to consistent ...
Quality Inspection
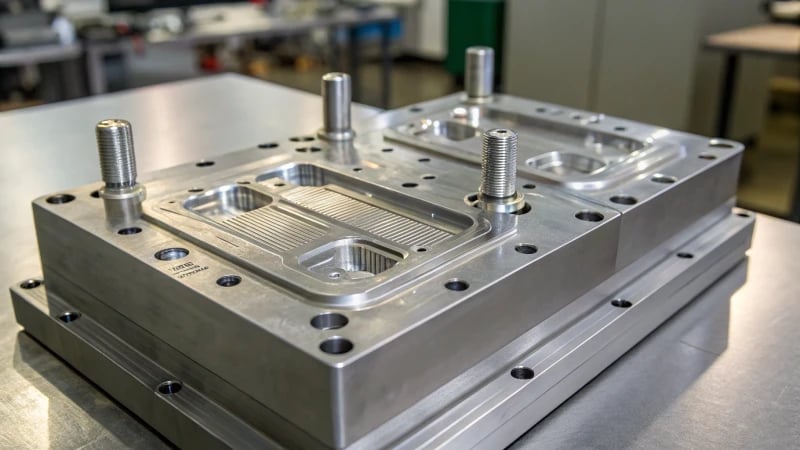
How Can You Design Effective Molds for Thin-Wall Injection Molding?
Designing effective molds for thin-wall injection molding involves several key strategies. Focus on optimizing material flow and ensuring uniform wall thickness to prevent defects like warping or shrinkage. Precise temperature control is crucial for consistent results, while selecting appropriate materials ...
DESIGN
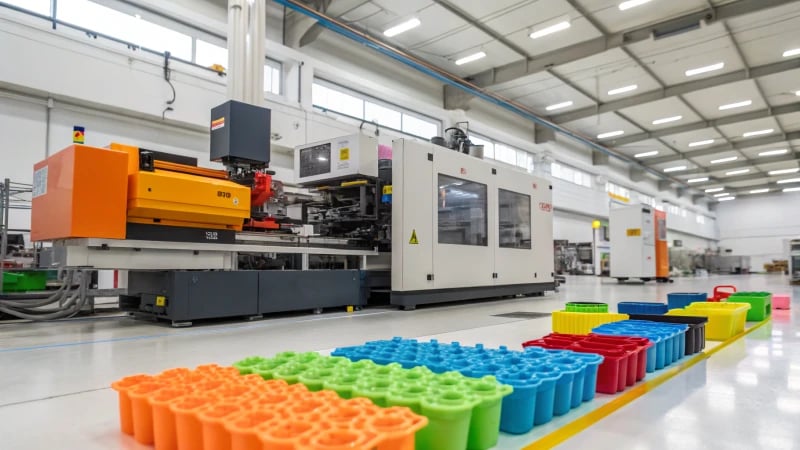
How Promising Are Multi-Material and Multi-Color Injection Molding Technologies?
This blog explores the transformative potential of multi-material and multi-color injection molding technologies in manufacturing. These innovations boost design creativity, streamline production processes, and enhance product functionality while reducing costs. However, they also pose challenges regarding recycling complexities and integration ...
OPTIMIZATION
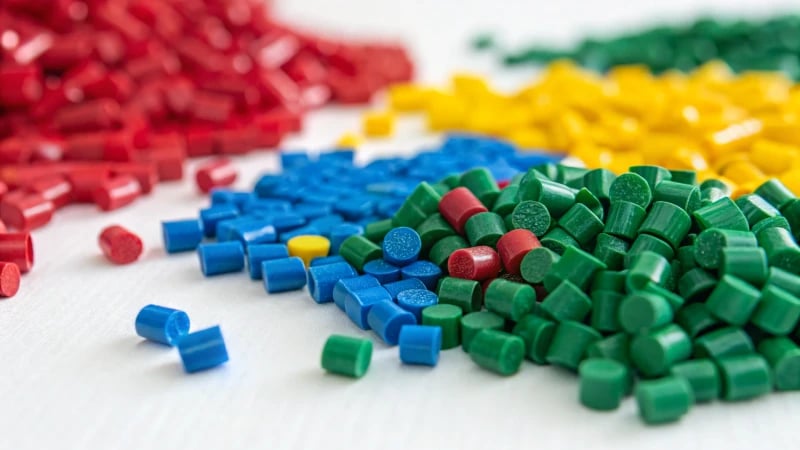
How Does the Choice of Materials Impact the Recyclability of Injection-Molded Parts?
The choice of materials in injection molding is crucial for recyclability. Thermoplastics, such as Polypropylene (PP) and Polyethylene (PE), are more recyclable than thermosets due to their ability to be re-melted and reshaped. This article explores how selecting the right ...
Materials Recommendations
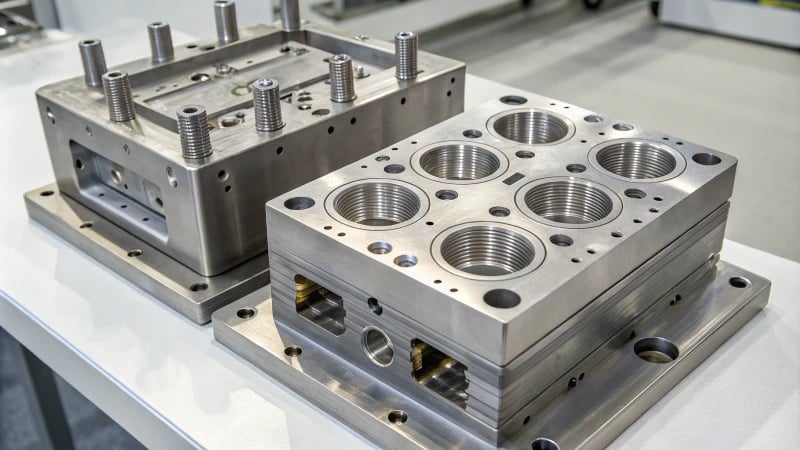
What Are the Essential Factors in Designing Multi-Cavity Molds?
Designing multi-cavity molds requires understanding essential factors such as material selection, cavity balance, cooling system design, and efficient ejection methods. These elements are crucial for achieving high production efficiency and consistent product quality. Material choices impact durability and cost-effectiveness while ...
DESIGN

How Does Automation Lower Labor Costs in Injection Molding?
Automation is revolutionizing the injection molding industry by significantly lowering labor costs. By taking over manual tasks, automated systems enhance production efficiency, ensure consistent quality, and minimize errors. This shift allows human resources to focus on strategic roles rather than ...
DEVELOPMENT
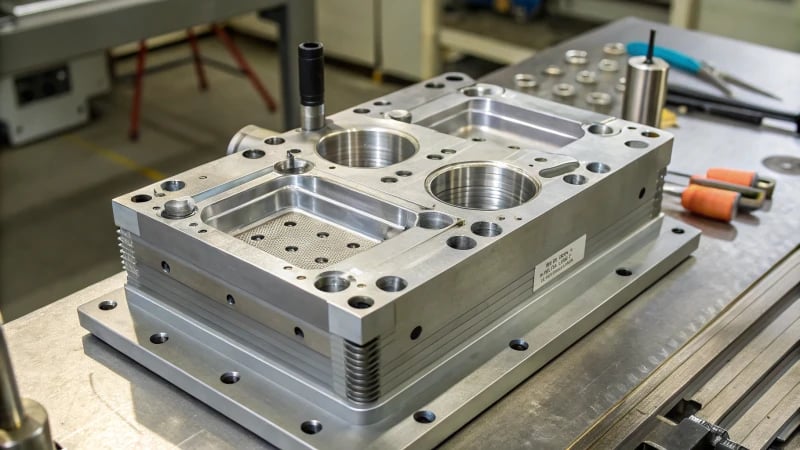
What Are the Best Practices for Core and Cavity Placement in Injection Molding?
In injection molding, effective core and cavity placement is crucial for minimizing defects and maximizing efficiency. Key practices include ensuring precise alignment, considering parting line locations, maintaining balanced wall thickness, and selecting appropriate materials. These strategies not only enhance product ...
MANUFACTURING
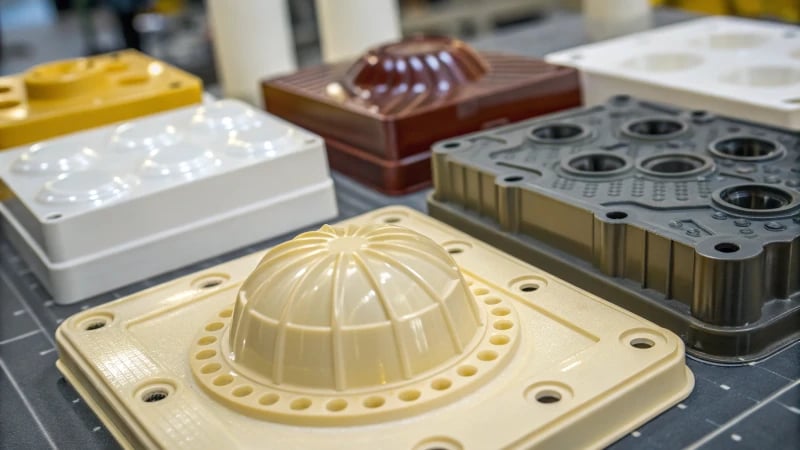
How Do Additives Impact the Properties of Injection-Molded Parts?
Additives play a crucial role in injection molding by modifying the properties of plastics to meet specific design requirements. They can enhance strength, flexibility, and durability through various types such as stabilizers, plasticizers, colorants, and reinforcements. Stabilizers protect against environmental ...
OPTIMIZATION

What Are the Cutting-Edge Trends in Injection Molding Technology?
The latest trends in injection molding technology focus on automation, sustainability, and novel materials. These advancements are revolutionizing the manufacturing industry by improving efficiency, minimizing environmental footprints, and creating new opportunities for designers. Automation enhances precision with robotics and sensors, ...
DEVELOPMENT
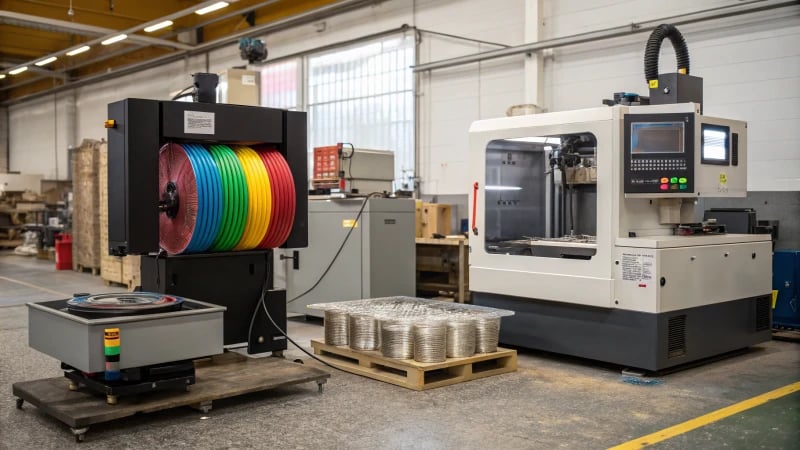
What Are the Most Effective Rapid Prototyping Techniques for Mold Making?
This blog post delves into the most effective rapid prototyping techniques for mold making. It covers 3D printing, CNC machining, and injection molding—each offering unique advantages in speed, precision, and cost-effectiveness. The article emphasizes how these methods can significantly enhance ...
MANUFACTURING