All Posts
blog & article
read our latest newsletter
Whether you’re curious about material selection, product design, mold design, mold making and injection molding, feel free to ask us anything. Our team is ready to provide the guidance and insights you need.

How Can an Injection Molding Machine Produce Plastic Spoons?
This article explores the fascinating process of producing plastic spoons using injection molding machines. It details how these machines melt plastic pellets and inject molten plastic into spoon-shaped molds under high pressure. The method ensures high precision and efficiency while ...
MANUFACTURING
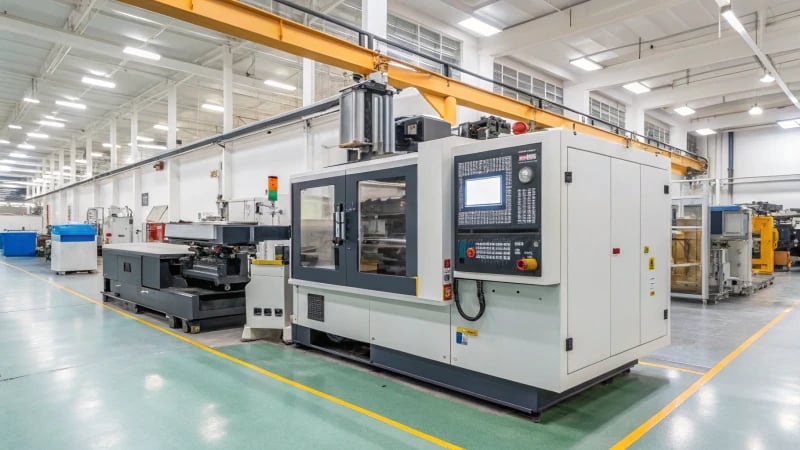
How Do You Determine the Capacity of a Plastic Injection Molding Machine?
Understanding the capacity of plastic injection molding machines involves three key factors: clamping force, shot volume, and production rate. Clamping force, measured in tons, ensures molds remain closed during injection to prevent defects. Shot volume indicates the maximum amount of ...
MANUFACTURING
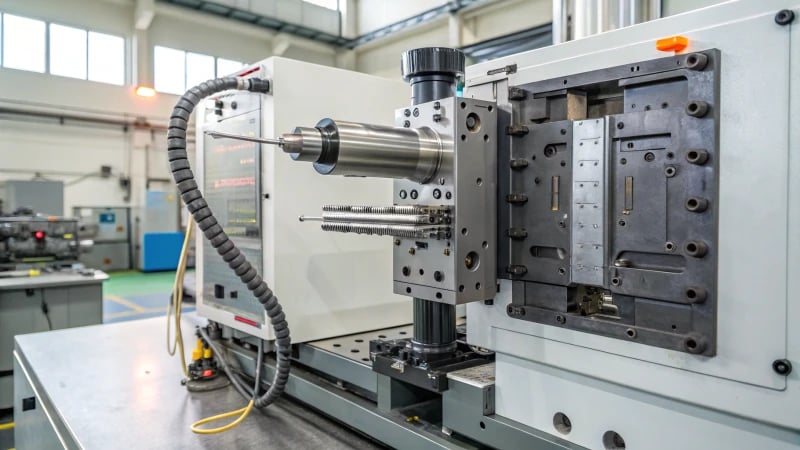
Can One Injection Molding Machine Fit Any Mold?
This article explores why one injection molding machine cannot fit every mold. It discusses critical factors such as clamping force, injection capacity, mold size, and pressure requirements that influence compatibility. Understanding these elements is crucial for product designers to avoid ...
MANUFACTURING
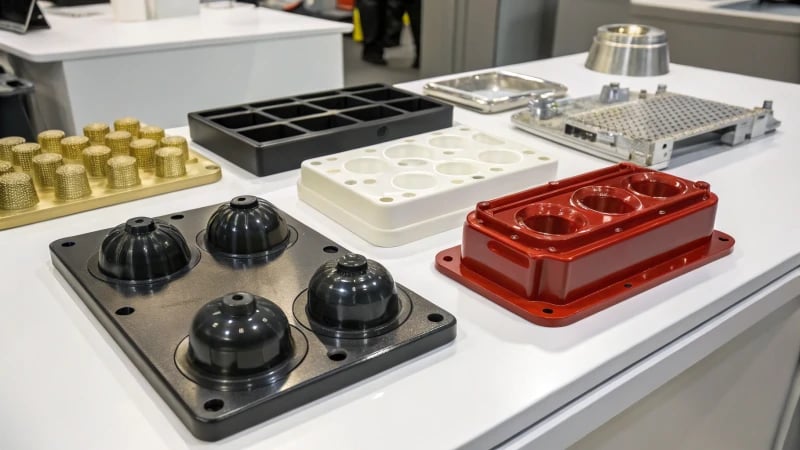
What Are the Most Common Surface Finishing Techniques for Injection Molded Parts?
This article delves into the most common surface finishing techniques for injection molded parts, such as painting, electroplating, hot stamping, silk screening, pad printing, laser engraving, frosting, and polishing. Each method is designed to enhance both the appearance and performance ...
MANUFACTURING
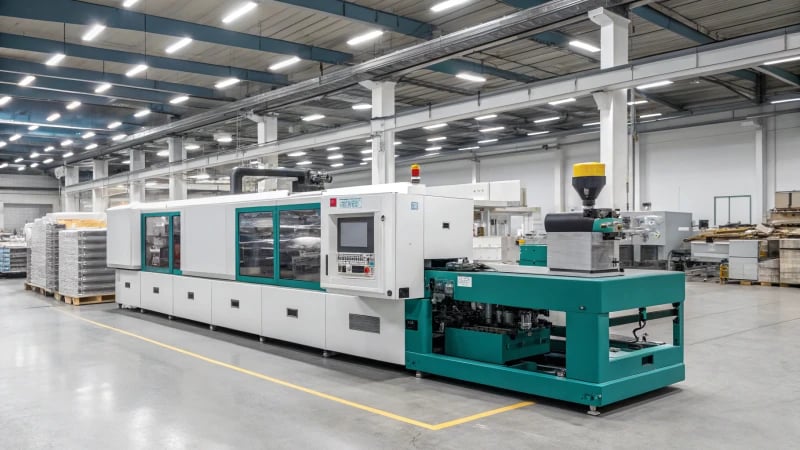
What Impact Will Global Market Trends Have on the Injection Molding Industry?
The injection molding industry is undergoing significant transformation due to global market trends. Increasing demand for lightweight components in the automotive sector, personalized designs in home appliances, and sustainable practices are reshaping manufacturing processes. The rise of electric vehicles necessitates ...
DEVELOPMENT
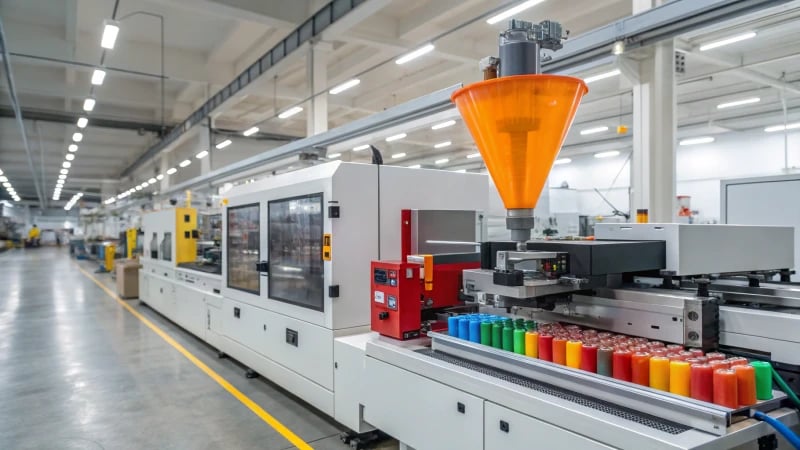
How Does the Injection Rate Affect Injection Molding Efficiency?
Understanding the injection rate is crucial in injection molding as it directly impacts part quality, surface finish, and overall efficiency. A well-calibrated injection rate ensures complete mold filling while minimizing defects such as air entrapment or short shots. Factors influencing ...
MANUFACTURING
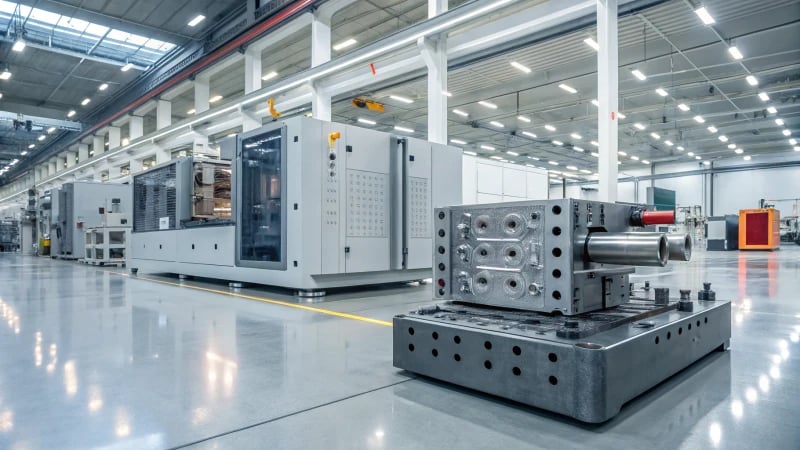
What Challenges Do Startups Face in Injection Molding?
Startups entering the injection molding industry encounter significant hurdles, including exorbitant equipment and mold costs, difficulties in attracting skilled talent, and intense market competition. These challenges necessitate careful strategic planning and effective resource management to ensure growth and sustainability. Funding ...
MANUFACTURING
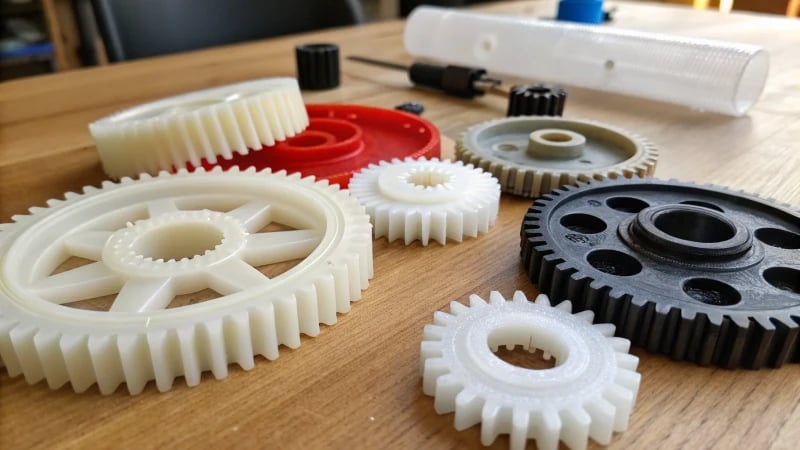
How Can You Texture Injection Molded Surfaces Effectively?
This article delves into various methods for effectively texturing injection molded surfaces. Techniques such as Electrical Discharge Machining (EDM), chemical etching, laser texture processing, and mechanical engraving are explored. Each method offers unique benefits tailored to specific design needs and ...
MANUFACTURING
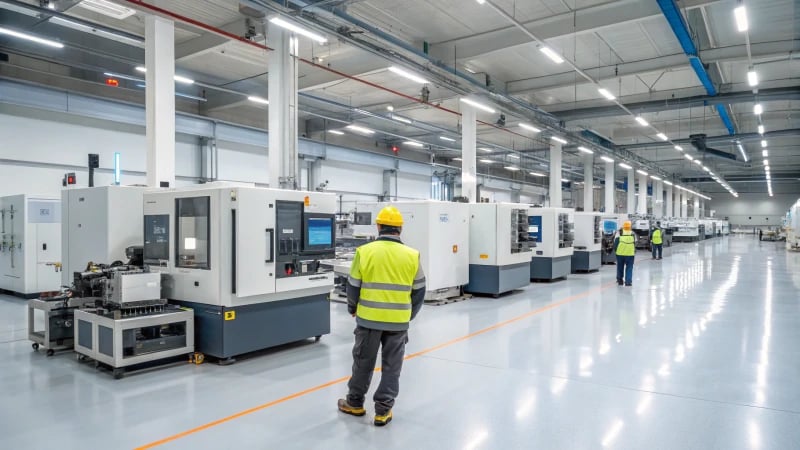
How Can You Ensure Quality Consistency from Suppliers in Injection Molding?
This article explores strategies for ensuring quality consistency from suppliers in injection molding. It emphasizes the importance of thorough supplier evaluations, clear contract agreements detailing quality standards, vigilant production oversight, and ongoing quality improvement measures. By implementing a structured approach ...
Quality Inspection
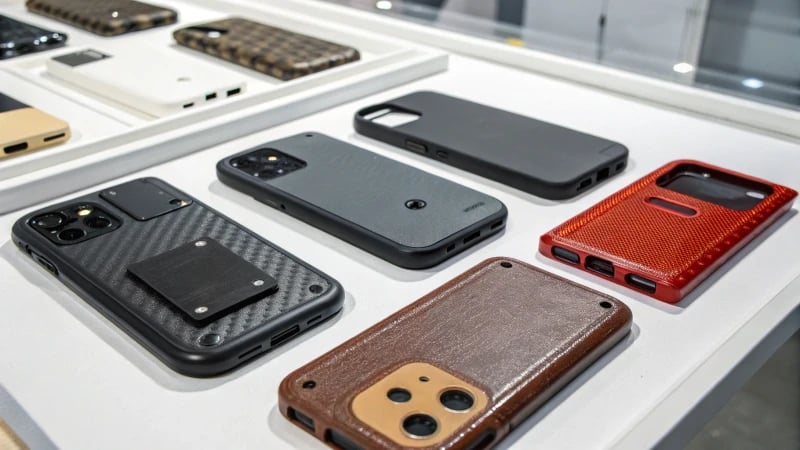
What Are the Key Standards for Injection Molded Electronic Casings?
This article explores the essential standards for designing injection molded electronic casings. It covers critical aspects such as dimension and tolerance controls, material performance requirements, appearance quality considerations, functionality standards like electromagnetic compatibility (EMC), waterproofing ratings, and rigorous quality inspection ...
Quality Inspection
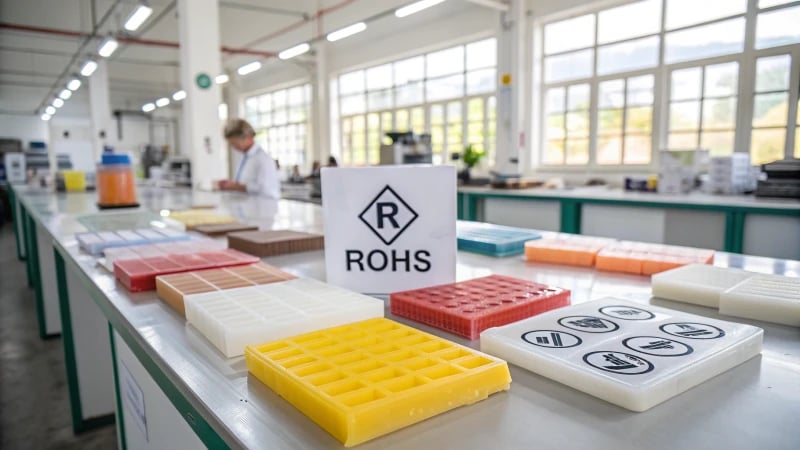
What Impact Do RoHS Directives Have on Injection Molding Materials?
The RoHS Directive significantly influences injection molding materials by enforcing strict restrictions on hazardous substances like heavy metals and brominated flame retardants. This shift compels manufacturers to seek alternative, compliant materials, often leading to increased production costs due to higher ...
MANUFACTURING
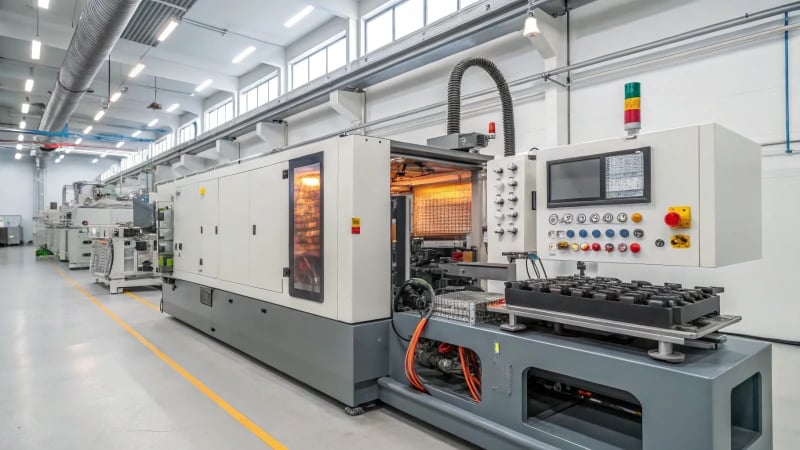
What Key Design Considerations Ensure Success in Injection Molding High-Temperature Parts?
This article explores essential design considerations for injection molding high-temperature parts. It emphasizes the importance of selecting appropriate materials like PPS and PEEK based on temperature tolerance, ensuring uniform wall thickness to prevent thermal stress, and implementing effective heat dissipation ...
DESIGN
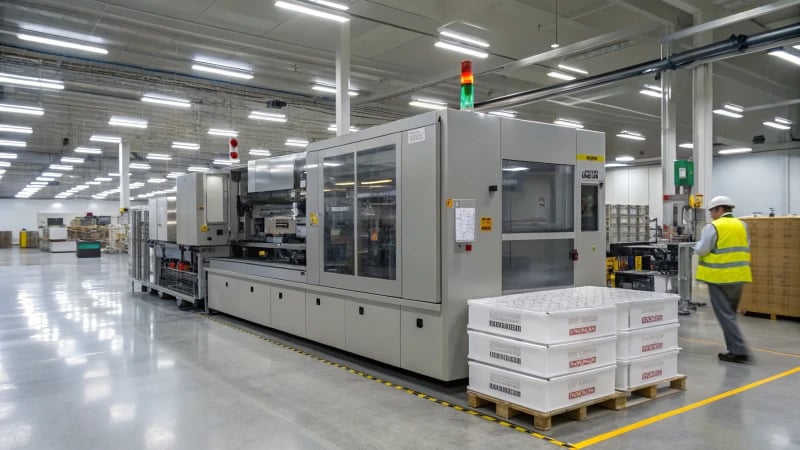
What Are the Steps to Comply with REACH Regulations in Injection Molding?
Navigating REACH compliance in injection molding is crucial for product safety and market access. This article provides a comprehensive overview of the necessary steps, including selecting compliant materials, managing suppliers effectively, maintaining rigorous process controls, and keeping detailed records. By ...
MANUFACTURING
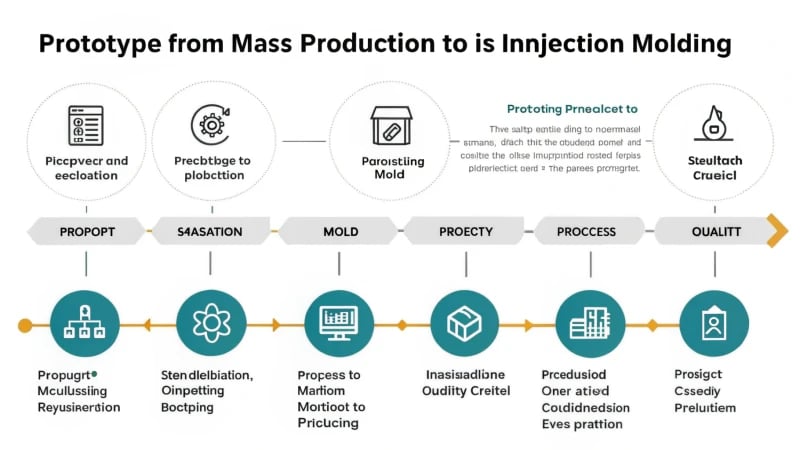
What Are the Key Steps to Transition from Prototype to Mass Production in Injection Molding?
This article outlines the essential steps for transitioning from prototype to mass production in injection molding. Key stages include thorough evaluation of prototypes, optimization of molds based on performance tests, standardization of process parameters through experimental design methods, and establishment ...
MANUFACTURING
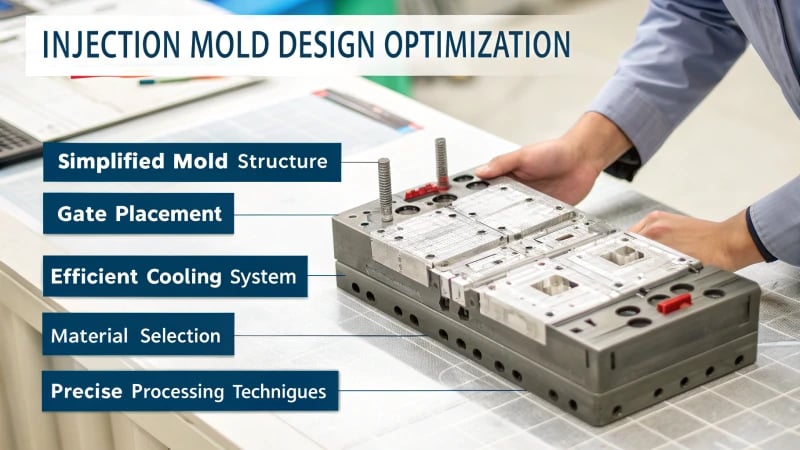
What Are the Key DFM Principles for Optimizing Injection Mold Design?
This article explores essential Design for Manufacturing (DFM) principles crucial for optimizing injection mold design. It emphasizes the importance of simplifying mold structures, strategically placing gates, designing efficient cooling systems, selecting appropriate materials, and ensuring precise processing. Each principle plays ...
MANUFACTURING
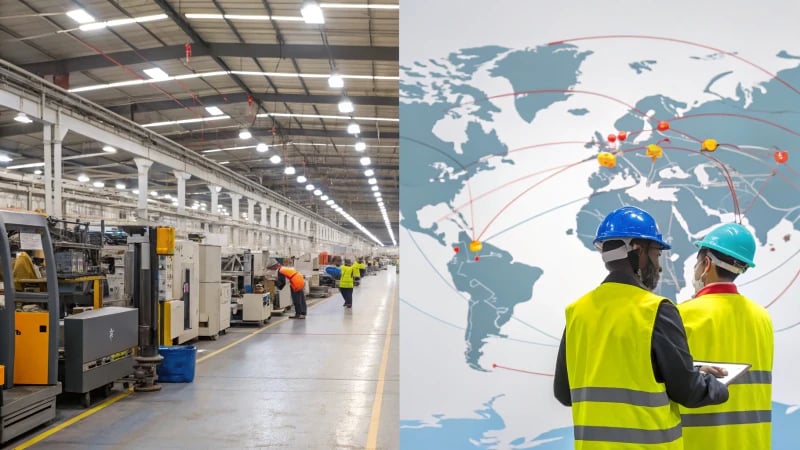
Local vs. Global Suppliers in Injection Molding: What Are the Benefits?
This article explores the advantages of choosing local injection molding suppliers over global ones. Local suppliers provide significant benefits such as lower transportation costs, quicker response times, and better service flexibility. Their proximity reduces risks associated with shipping delays and ...
Find Suppliers
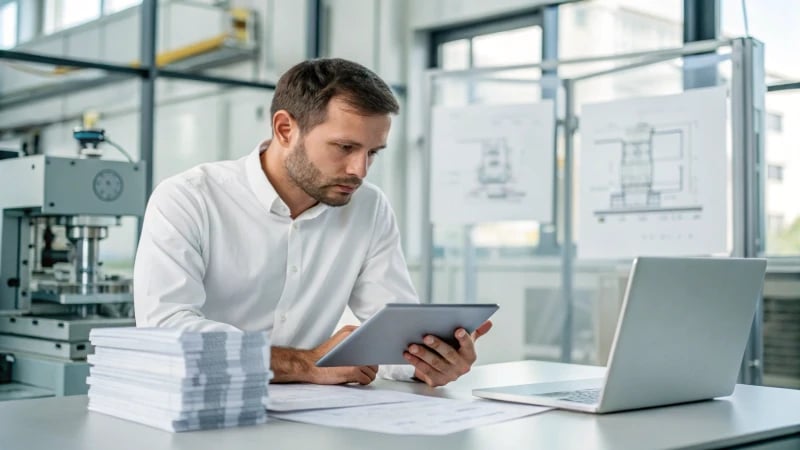
How Do You Calculate the Cost Per Part in Injection Molding?
Calculating the cost per part in injection molding involves understanding various components such as material costs, mold expenses, processing costs (energy and labor), and additional factors like packaging and transportation. By accurately estimating each element—using tools like 3D modeling software ...
Price Evaluation
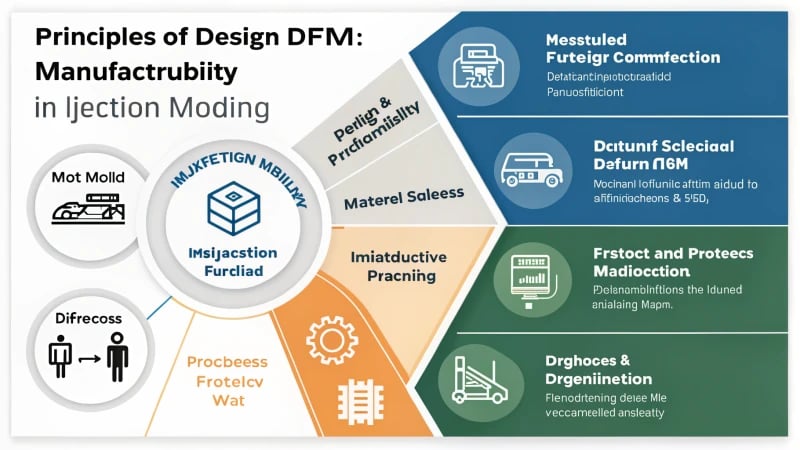
How Does Design for Manufacturability (DFM) Enhance Injection Molding?
This article explores how Design for Manufacturability (DFM) enhances injection molding by focusing on product structure design, mold design, and material selection. Key principles include maintaining uniform wall thickness to prevent defects like warping and shrinkage, strategically designing ribs for ...
MANUFACTURING
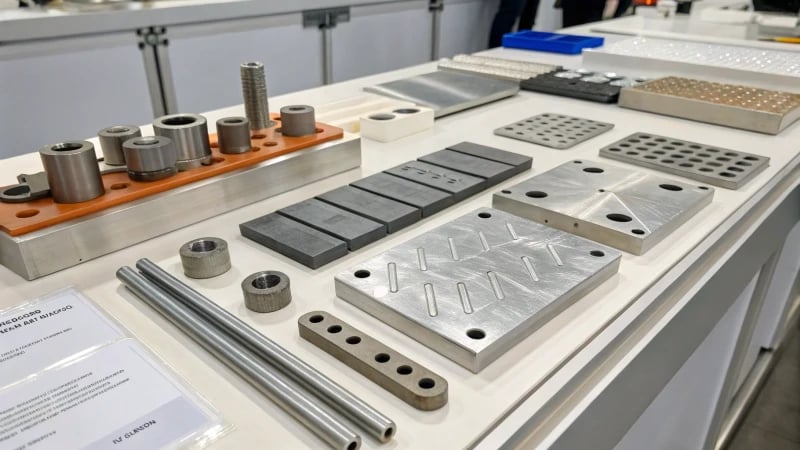
Which Mold Materials Are Ideal for High-Temperature Injection Molding?
Choosing the right mold material is crucial for high-temperature injection molding. Materials such as H13 steel and the HMAX series offer exceptional heat resistance and wear durability. Stainless steel provides corrosion resistance while hard alloys excel in toughness. Ultracur3D® RG3280 ...
Materials Recommendations
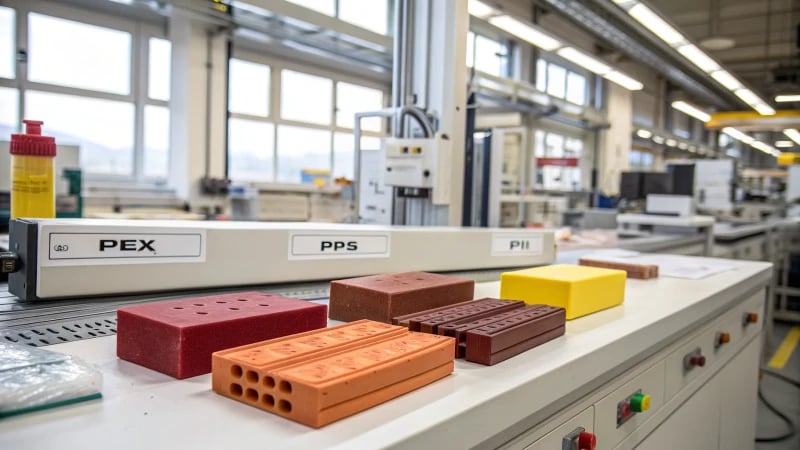
What Are the Best Materials for High-Temperature Injection Molding?
Choosing the right materials for high-temperature injection molding is crucial for project success. This article discusses top materials like PEEK, PPS, and PI while considering factors such as heat resistance, mechanical properties, chemical stability, processing performance, cost-effectiveness, and availability. Understanding ...
Materials Recommendations
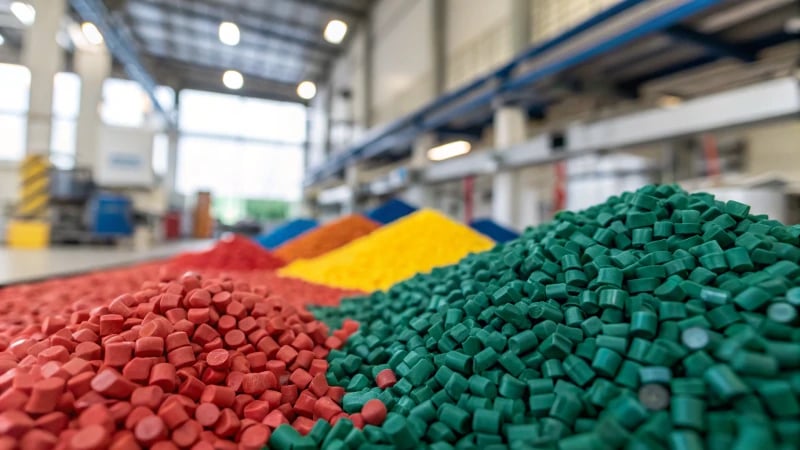
What Key Factors Should You Consider When Using Recycled Plastics for Injection Molding?
This blog post explores key factors to consider when using recycled plastics for injection molding. It emphasizes the importance of material quality, compatibility, and contamination management to maintain product integrity. The author shares personal experiences and practical solutions for designers ...
MANUFACTURING
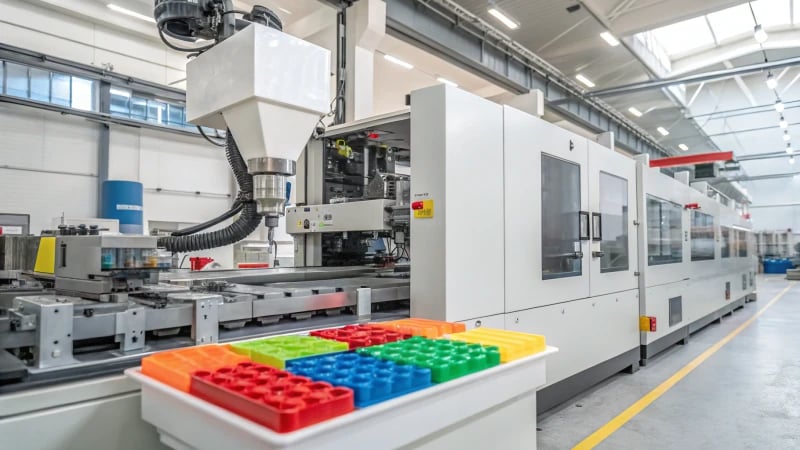
Can Injection Molding Effectively Produce Both Plastic and Metal Parts?
Injection molding is a versatile manufacturing process ideal for producing intricate plastic parts at scale. Its adaptability to various materials allows for efficient large-scale production of complex shapes, making it cost-effective. However, when it comes to metal parts, the process ...
MANUFACTURING
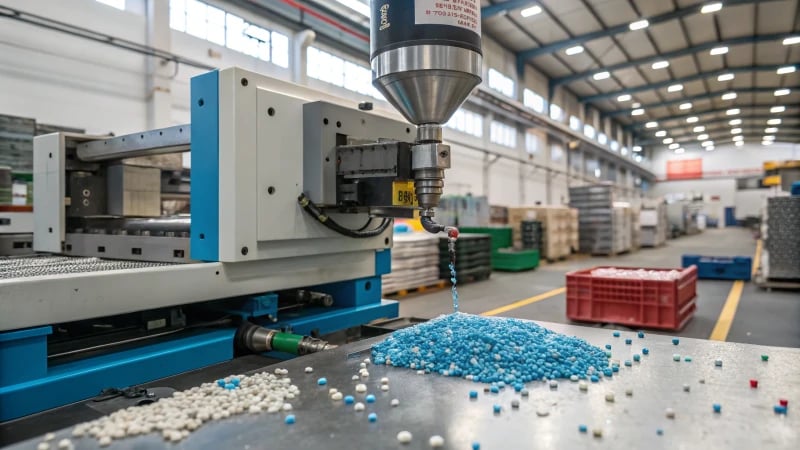
What Factors Determine the Right Size of Injection Molding Machine?
Selecting the appropriate size for an injection molding machine is essential for optimizing production efficiency and product quality. Key factors include material type, shot size, clamping force, and technical specifications. Each element plays a vital role in ensuring that the ...
MANUFACTURING
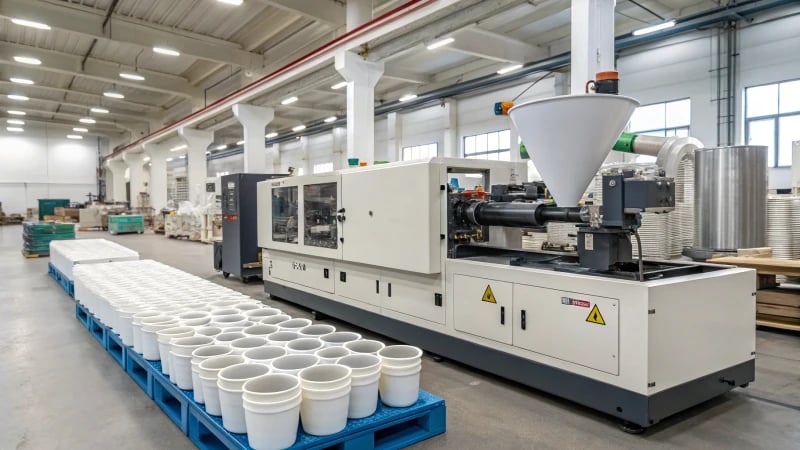
What Factors Determine the Right Cooling Time in Injection Molding?
Understanding the right cooling time in injection molding is crucial for optimizing production efficiency and ensuring high-quality products. Key factors include part thickness, material properties, and mold design. Thicker parts require longer cooling times due to increased heat retention, while ...
MANUFACTURING
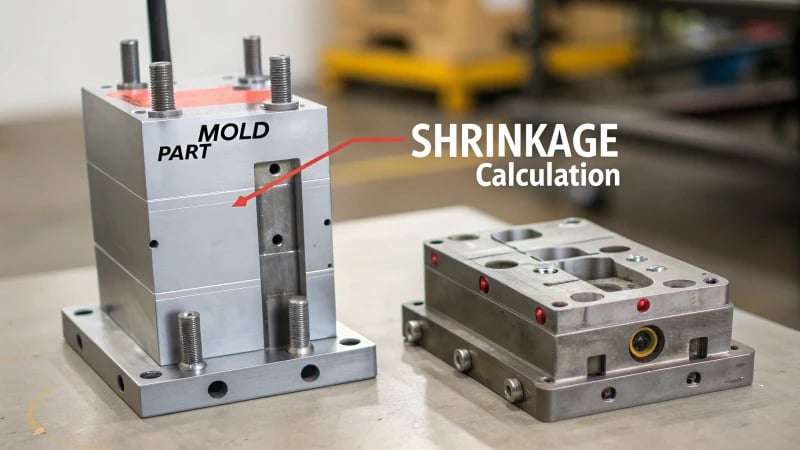
How Do You Calculate Shrinkage in Injection Molding?
Calculating shrinkage in injection molding is crucial for achieving accurate part dimensions. This article outlines the formula for shrinkage calculation and discusses factors influencing it, including material properties, mold design considerations, and processing conditions. By understanding these elements, designers can ...
DESIGN
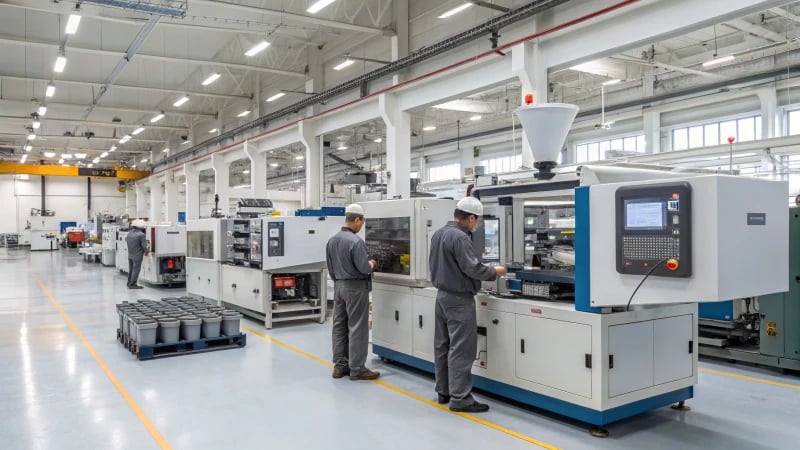
How Can You Optimize Cycle Time in Injection Molding?
In the competitive landscape of injection molding, optimizing cycle time is crucial for enhancing production efficiency. Key strategies include refining mold design, choosing appropriate materials with high thermal conductivity, and embracing automation technologies. By understanding the components of cycle time—processing, ...
OPTIMIZATION
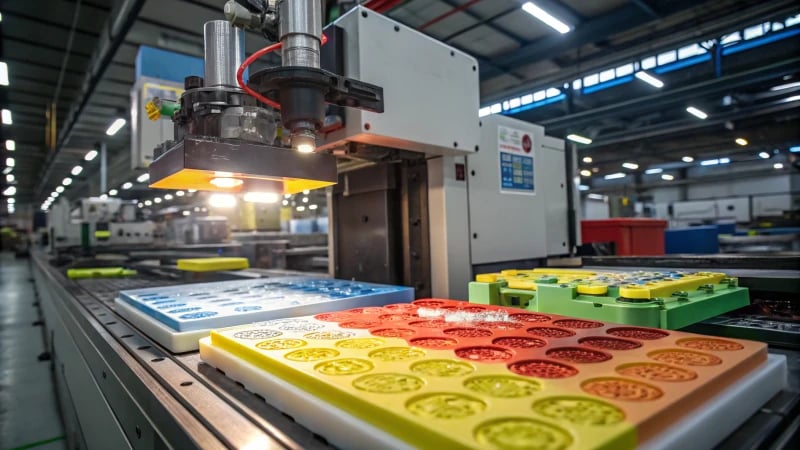
What Are the Steps to Apply Advanced In-Mold Decoration in Injection Molding?
Advanced in-mold decoration (IMD) is a transformative process that integrates decorative graphics into plastic components during injection molding. This technique not only elevates the aesthetic appeal of products but also ensures durability and longevity, making it a preferred choice across ...
MANUFACTURING
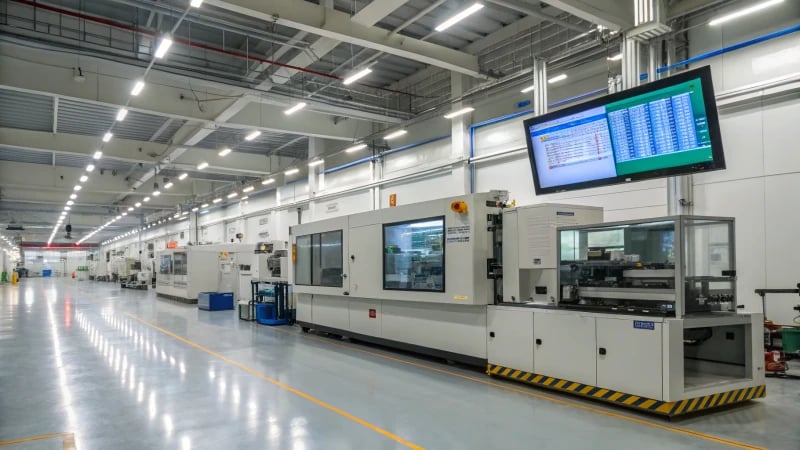
How Can You Effectively Monitor and Control the Qualified Rate After Injection Molding?
Effective monitoring and control of qualified rates in injection molding hinge on implementing strong quality assurance protocols, utilizing real-time data analytics for process oversight, and fostering a culture of continuous improvement. Key checks such as dimensional verification, visual inspections, mechanical ...
Quality Inspection

What is the Process of Injection Molding UHMWPE?
This blog post explores the intricate process of injection molding Ultra High Molecular Weight Polyethylene (UHMWPE). It highlights its exceptional properties such as durability, low friction, and wear resistance, making it ideal for various applications in industries like medical devices, ...
MANUFACTURING
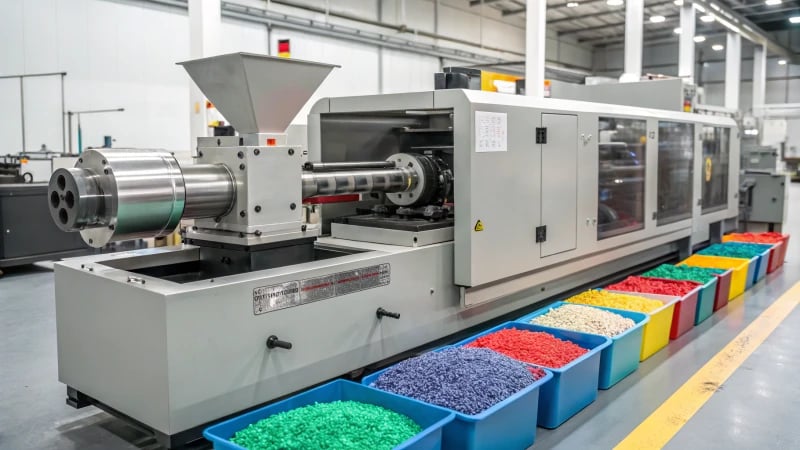
What Are the Key Differences in Injection Molding for Large vs. Small Parts?
This article explores the key differences in injection molding processes for large versus small parts. It highlights how factors such as mold design complexity, material selection, and machinery needs vary with part size. Large parts require robust materials and larger ...
MANUFACTURING