In the fast-paced world of manufacturing, understanding wear resistance can be a game-changer for engineers and product designers alike.
To improve wear resistance in injection molded parts, focus on material selection, mold design, injection molding processes, and surface treatment. These strategies enhance durability by selecting suitable materials, optimizing mold design, adjusting processing parameters, and applying protective coatings.
Let’s dive deeper into each strategy—these insights could be the key to unlocking greater durability and efficiency in your projects.
PTFE enhances wear resistance in injection molded parts.True
PTFE's low friction and high durability make it ideal for wear resistance.
How Does Material Selection Affect Wear Resistance?
The materials used in injection molded parts significantly influence their wear resistance. Choosing the right material can lead to longer-lasting, more durable products, making it a critical decision for engineers.
Material selection affects wear resistance by determining the friction coefficient, hardness, and ability to withstand environmental conditions. Opting for materials like PTFE or UHMWPE enhances durability due to their inherent properties.
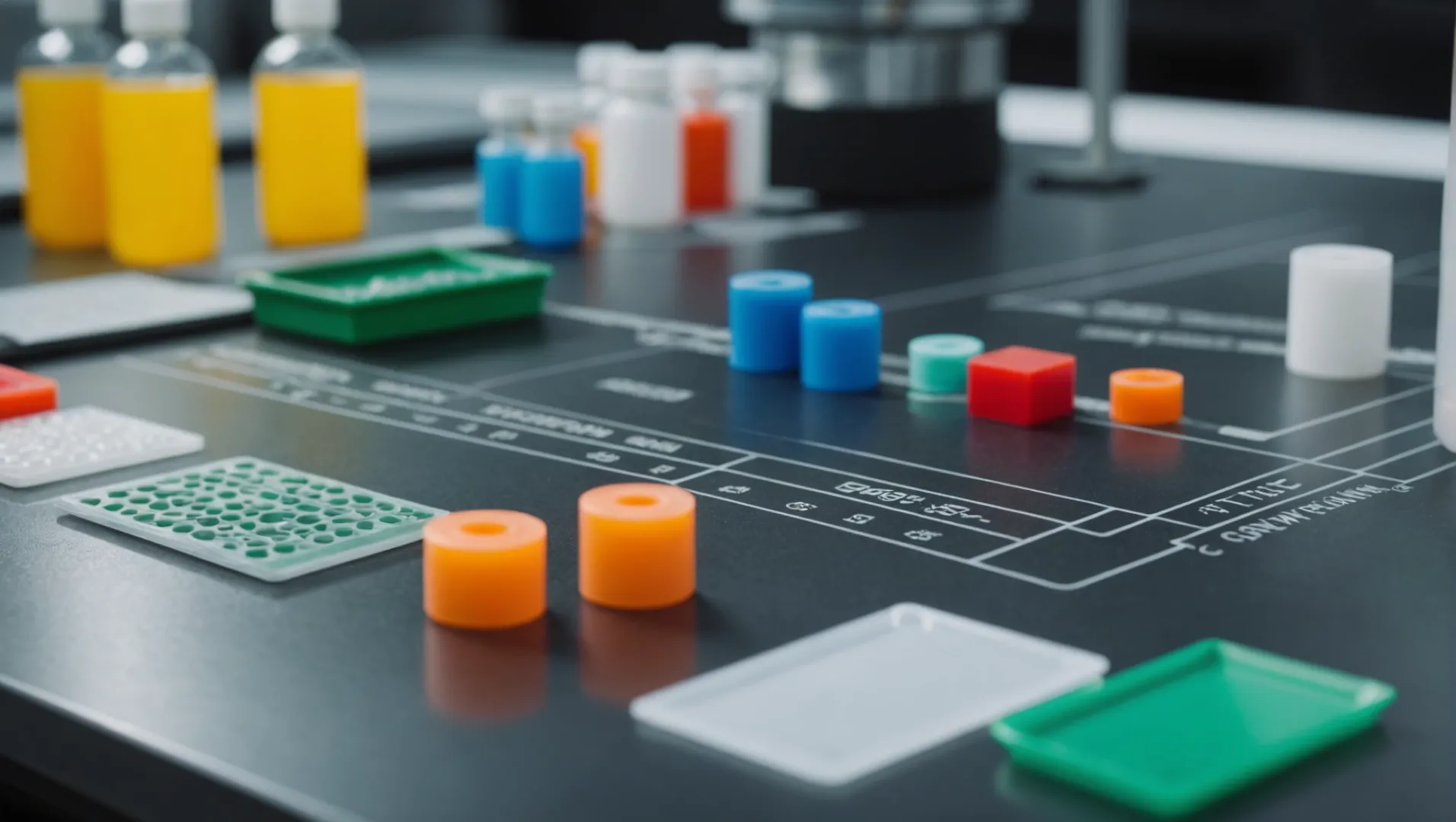
Selecting High-Wear-Resistant Plastics
Choosing highly wear-resistant plastics is essential. Polytetrafluoroethylene (PTFE) and ultra-high molecular weight polyethylene (UHMWPE) are top choices due to their low friction coefficients and excellent wear resistance. These materials maintain performance even in harsh environments.
For specific applications, engineering plastics with added wear-resistant fillers can be employed. Consider engineering plastics with fillers1 like nylon and polycarbonate reinforced with glass fiber, carbon fiber, or molybdenum disulfide to significantly improve wear resistance.
The Role of Material Hardness
Material hardness directly influences wear resistance. Generally, harder materials provide better wear resistance. However, it’s crucial to balance hardness with toughness since excessive hardness can lead to brittleness. This balance can be achieved through hardness adjustment techniques2 such as heat treatment.
Considering Environmental Factors
The operating environment also plays a role in material selection. Materials should be chosen based on their ability to resist the specific conditions they will encounter, such as temperature fluctuations, exposure to chemicals, or abrasive elements.
A Balancing Act: Cost vs. Performance
While selecting materials, cost must be weighed against performance. Advanced materials with superior wear resistance may be more expensive but could result in lower maintenance costs and longer part lifespan, offering savings in the long run.
Material Type | Wear Resistance | Cost Efficiency |
---|---|---|
PTFE | High | Moderate |
UHMWPE | High | Moderate |
Nylon with Fillers | Moderate to High | Cost-effective |
Polycarbonate with Fillers | Moderate to High | Cost-effective |
In conclusion, by choosing the appropriate material, engineers can significantly enhance the wear resistance of injection molded parts, ensuring longevity and performance efficiency.
PTFE enhances wear resistance due to low friction.True
PTFE has a low friction coefficient, improving wear resistance.
Material hardness does not affect wear resistance.False
Harder materials generally offer better wear resistance.
Why Is Mold Design Crucial for Durability?
Mold design is a critical factor influencing the durability and performance of injection molded parts. Effective mold design can enhance wear resistance, ensuring longer-lasting products.
Mold design is crucial for durability because it minimizes stress concentration, optimizes cooling, and selects appropriate materials, enhancing wear resistance and overall performance of injection molded parts.
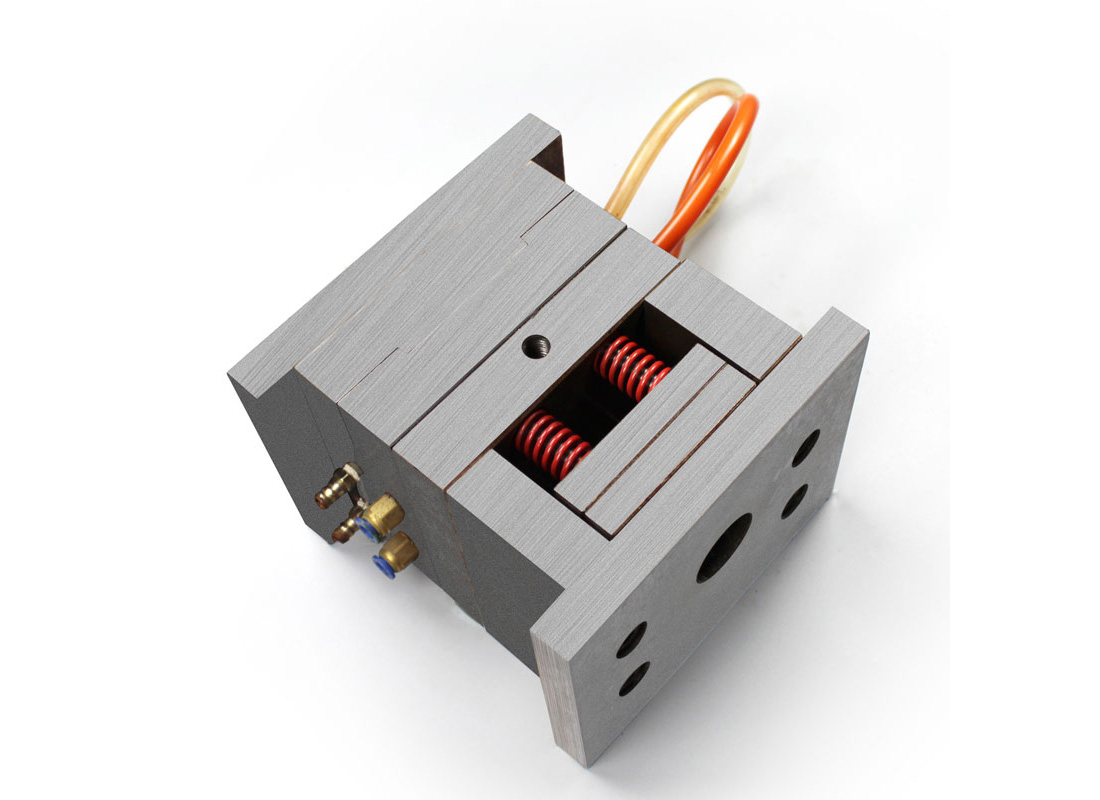
Importance of Mold Structure Optimization
The structural design of a mold significantly affects the durability of injection molded parts. By optimizing the mold structure, manufacturers can reduce stress concentration, which often leads to premature wear and tear. A uniform wall thickness is essential as it allows for even distribution of stress across the part. Avoiding sharp corners and transitions further helps in preventing stress points, thus enhancing the part’s durability.
Another critical aspect is the cooling system within the mold. A well-designed cooling system ensures uniform cooling of the molded part, reducing internal stress caused by uneven temperature distribution. This not only improves the wear resistance but also enhances the overall quality of the part. Implementing such designs can lead to a significant reduction in defects and improve the lifespan of the product.
Selecting Suitable Mold Materials
The choice of mold materials plays a pivotal role in determining the quality and wear resistance of injection molded parts. Materials with high hardness and excellent wear resistance, such as high-quality alloy steel and cemented carbide, are preferred. These materials can withstand the rigors of repeated use without degrading quickly.
Additionally, surface treatments like hard chrome plating and nitriding can be applied to molds to increase their surface hardness and wear resistance. These treatments extend the mold’s service life and improve the surface quality of the finished product.
Practical Examples and Case Studies
Consider a scenario where nylon gears3 are produced using a poorly designed mold. The lack of attention to detail in mold structure leads to stress concentration at certain points, causing cracks over time. Conversely, when a similar product is manufactured using a well-optimized mold with a uniform cooling system, the gears demonstrate significantly higher durability and wear resistance.
In another example, utilizing high-quality alloy steel molds4 with appropriate surface treatments has proven beneficial in automotive applications. The enhanced mold design results in parts that maintain structural integrity under high-stress conditions, showcasing the importance of proper material selection and design in prolonging part life.
By examining these case studies5, it’s evident that thoughtful mold design is indispensable for achieving durable injection molded components.
Uniform wall thickness reduces stress concentration.True
Even stress distribution prevents weak points, enhancing durability.
Sharp corners in molds increase part durability.False
Sharp corners create stress points, leading to premature wear.
What Role Does the Injection Molding Process Play in Wear Resistance?
The injection molding process is crucial for enhancing wear resistance in molded components, impacting their longevity and performance.
The injection molding process significantly influences wear resistance by controlling temperature, pressure, and cooling time to optimize material properties and reduce internal stress.
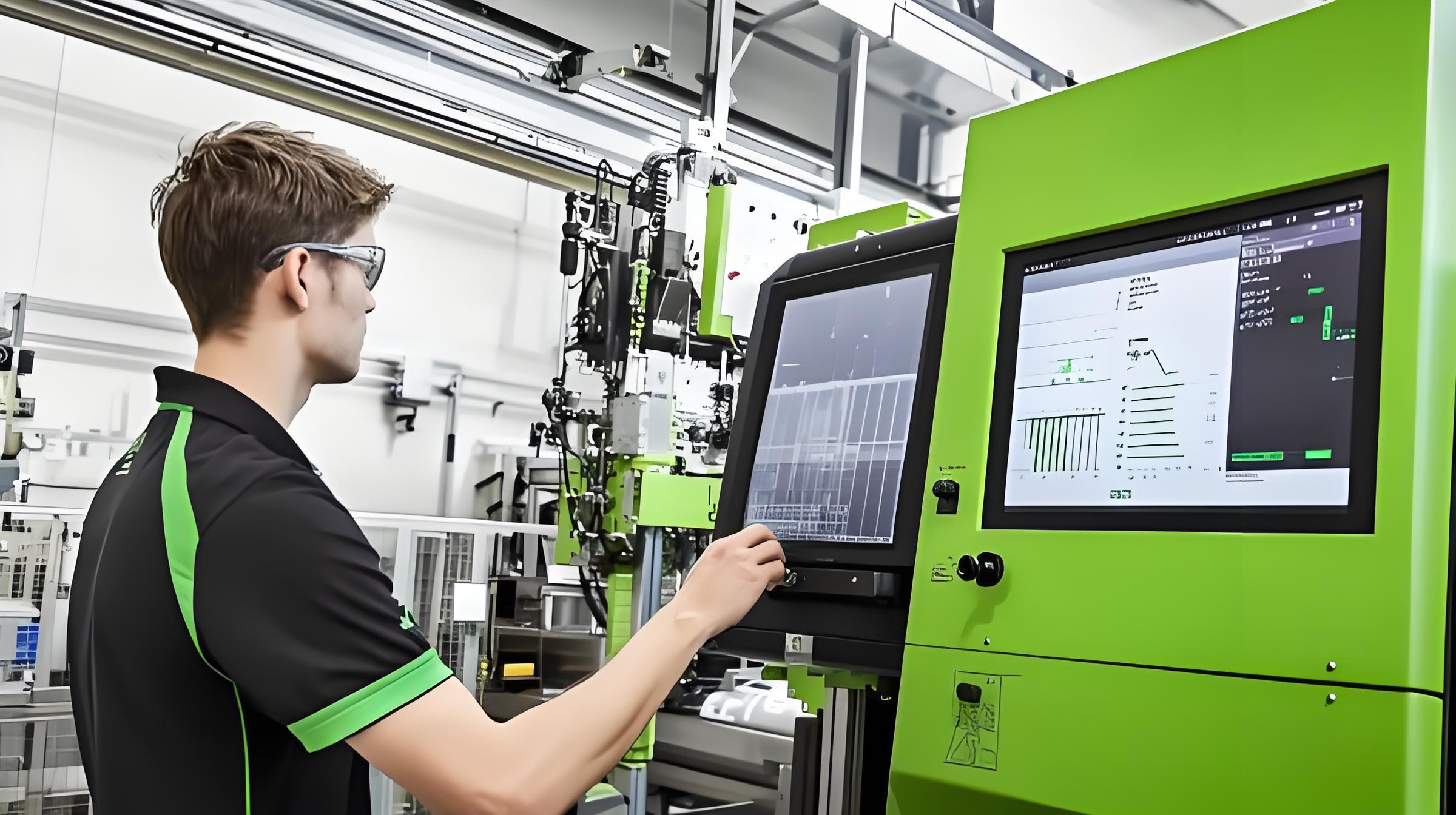
Controlling Injection Molding Temperature
The temperature during injection molding6 plays a pivotal role in determining the wear resistance of the final product. By ensuring the plastic material is fully melted and maintains optimal fluidity, the risk of defects is minimized. However, it’s essential to balance this with the risk of overheating, which can degrade material properties. Each plastic type has its ideal temperature range that must be adhered to.
- Example: Using UHMWPE requires precise temperature control to maintain its low friction and high durability properties.
Adjusting Injection Pressure and Speed
Injection pressure and speed are crucial parameters that need to be fine-tuned to ensure the material fills the mold cavity uniformly. This reduces defects such as voids or shrinkage, which can compromise wear resistance. These parameters should be adjusted considering the mold’s design, material choice, and part dimensions.
- Example: For complex designs with intricate features, a slower injection speed may be beneficial to prevent stress concentration.
Optimizing Cooling Time
Proper cooling time is essential to prevent the formation of internal stresses that could reduce wear resistance. Cooling too quickly or too slowly can lead to dimensional instability or increased brittleness. The cooling time should be calculated based on the material’s thermal properties and the part’s geometry.
- Example: A part made from polycarbonate might require longer cooling times compared to nylon due to its higher thermal resistance.
Injection Molding Process Parameters Table
Parameter | Impact on Wear Resistance | Example Material |
---|---|---|
Temperature | Influences material flow and integrity | UHMWPE |
Pressure | Affects mold fill and defect reduction | PTFE |
Speed | Reduces stress concentration | Nylon with fillers |
Cooling Time | Controls stress and dimensional stability | Polycarbonate |
In conclusion, precise control over the injection molding process not only enhances wear resistance but also improves the overall quality and lifespan of injection molded parts. This necessitates a detailed understanding of material behavior under different processing conditions.
Temperature affects wear resistance in molding.True
Temperature control ensures optimal material properties, reducing defects.
Cooling time doesn't impact wear resistance.False
Improper cooling can cause internal stresses, affecting durability.
How Can Surface Treatments Enhance Component Longevity?
Surface treatments play a crucial role in enhancing the longevity of components by providing additional layers of protection against wear and environmental factors.
Surface treatments like coatings and hardening processes enhance component longevity by improving wear resistance, reducing friction, and protecting against corrosion. These treatments tailor the surface properties to specific application needs, ensuring components last longer under operational stresses.
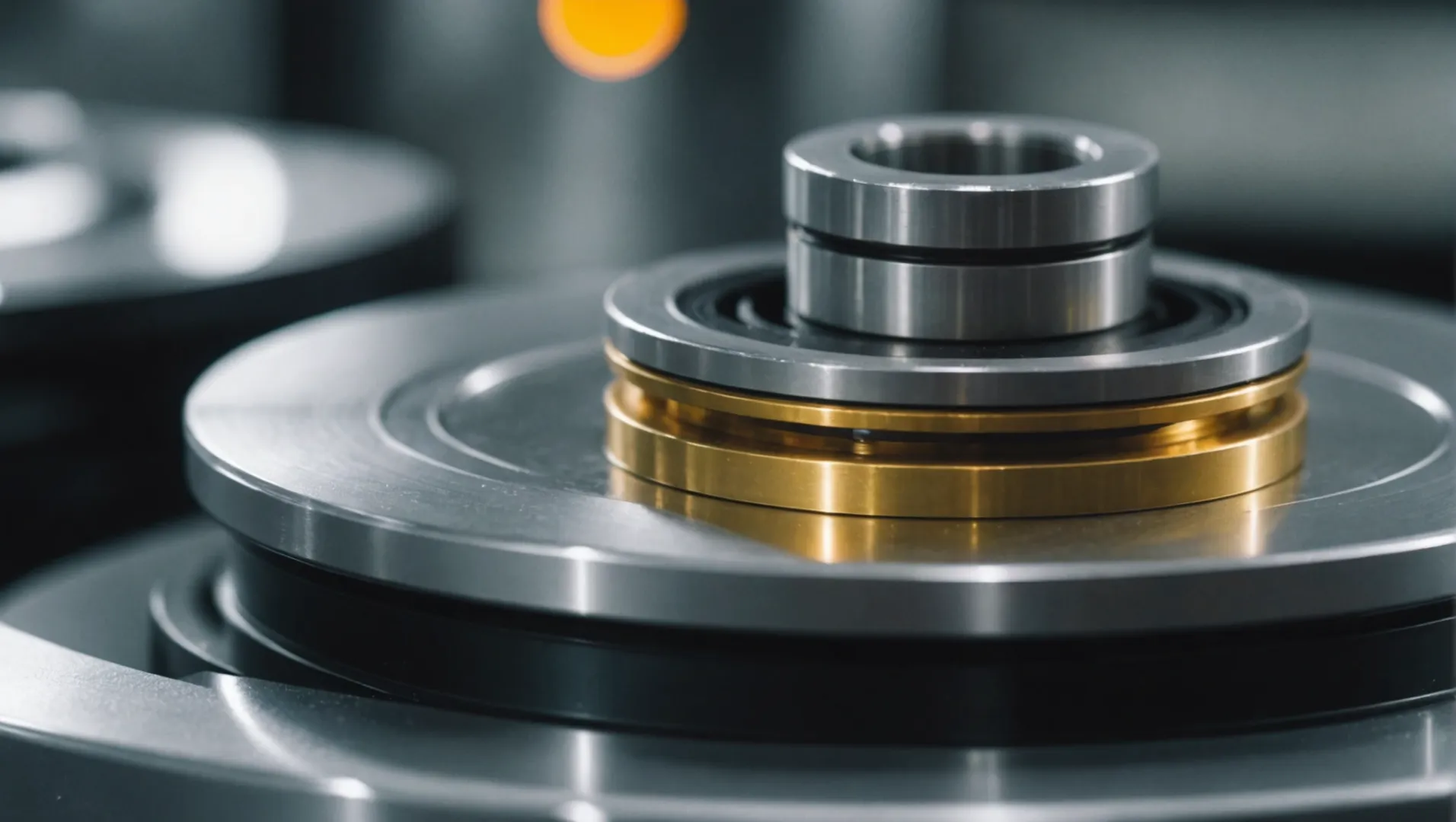
Understanding Surface Treatments
Surface treatments are methodologies applied to component surfaces to enhance their properties without altering the core material. These techniques focus on improving wear resistance, reducing friction, and safeguarding against corrosion.
Types of Surface Treatments
-
Coating Treatments
- Coatings such as polyurethane or ceramic provide a hard, protective layer on components. This treatment is particularly beneficial for injection molded parts exposed to harsh environments. These coatings exhibit high hardness and low friction, making them ideal for applications where wear resistance is crucial.
- The selection of coating materials must consider the specific use environment7 and compatibility with the base material to ensure longevity and adhesion.
-
Surface Hardening
- Techniques like flame quenching and induction hardening enhance the surface hardness, improving wear resistance. These are well-suited for components with high stress exposure, such as gears or bearings.
- It’s vital to control temperature and time during hardening to avoid adverse effects on the component’s integrity.
Benefits of Surface Treatments
- Enhanced Durability: By reducing surface wear, these treatments significantly extend component life.
- Corrosion Resistance: Many coatings also protect against environmental factors, preventing rust and degradation.
- Cost-Efficiency: Longer-lasting components reduce the need for frequent replacements, leading to cost savings over time.
Considerations for Effective Surface Treatment
To maximize the benefits of surface treatments, it’s essential to:
- Evaluate the operational environment of the component to select appropriate treatment methods.
- Consider adhesion properties between the coating and substrate to prevent delamination.
- Ensure that treatment processes do not negatively impact other component properties, such as flexibility or toughness.
Proper implementation8 of surface treatments can transform component performance, offering a strategic advantage in durability and reliability.
Surface treatments only improve component aesthetics.False
Surface treatments enhance durability and resistance, not just aesthetics.
Coatings can increase a component's wear resistance.True
Coatings provide a hard layer that reduces friction and wear.
Conclusion
By selecting the right materials and optimizing processes, engineers can significantly boost the wear resistance of injection molded parts.
-
Explore how fillers enhance plastic’s durability and reduce wear.: We review approaches for improvement of tribological properties of polymers based on inclusion of fillers. The fillers can be metallic or … ↩
-
Learn methods to balance hardness and toughness in materials.: Improve the hardness of plastics by blending is to blend high-hardness resin with low-hardness resin to improve its overall hardness. The common … ↩
-
Explore how mold design affects nylon gear longevity.: Nylon offers extremely tough mechanical properties: high tensile strength, impact resistance, and great shock absorption. With specialized … ↩
-
Understand advantages of using superior alloy steel molds.: Utilize steel molds for plastic molding to ensure precision, durability, and high-quality output, leading to improved efficiency and cost-effectiveness. ↩
-
Gain insights from real-world examples on mold design.: ICOMold is here to make sure our customers get their injection mold tooling and CNC milling projects completed quickly and accurately. ↩
-
Understand how temperature adjustments impact material properties during injection molding.: Temperature plays an essential role in injection molding, as it affects the viscosity of the molten material and the cooling time. ↩
-
Find the best coatings for durability in tough conditions.: PEO forms hard, dense and wear-resistant coatings for lightweight metals such as aluminium, titanium and magnesium. When compared directly to … ↩
-
Learn about how surface treatments enhance engineering components.: Ability to use a variety of materials · Design the product you want to design · Ability to work with other processes · Standardising manufacturing processes. ↩