Ever felt bewildered in the puzzle of injection molded plastic treatments? We will explore this together!
Picking the right surface treatment for molded plastic products depends on knowing what is needed for both function and looks. Abrasion resistance is important. Electrical insulation matters too. Desired texture or gloss affects the choice.
I remember a time when I needed to choose the right finish for a product line. The key is to balance how it works with how it looks. For example, if durability against scratches is required, spraying or plating might be considered. These methods create a strong coating. This is important for things like tool handles that really get used daily.
For a smooth and shiny look, think about vacuum coating. It gives a metallic shine. High-end electronics or cosmetics packaging often use it. For see-through items like optical lenses, choose treatments that keep them clear. Every choice tells a story. Understanding your product’s path helps you pick the best option.
Spraying enhances wear resistance of plastic tool handles.True
Spraying forms a solid coating on plastic, improving wear resistance.
Metal plating improves electrical insulation of plastic parts.False
Metal plating reduces electrical insulation, not suitable for such needs.
- 1. How do functional requirements influence surface treatment selection?
- 2. How Does Appearance Influence Surface Treatment Choices?
- 3. Which Surface Treatments Offer Optimal Electrical Insulation?
- 4. How Can Surface Treatments Enhance Optical Performance?
- 5. What Are the Latest Trends in Plastic Surface Treatments?
- 6. Conclusion
How do functional requirements influence surface treatment selection?
Did you ever think about how the parts inside a product decide its outside look? Let’s explore the interesting area where what a thing does connects with its pretty outside.
Functional requirements influence how surfaces are treated. These needs focus on properties like wear resistance, corrosion protection and optical clarity. The correct treatment helps products look good and work well. Products need to function properly. They also need to please the eye.
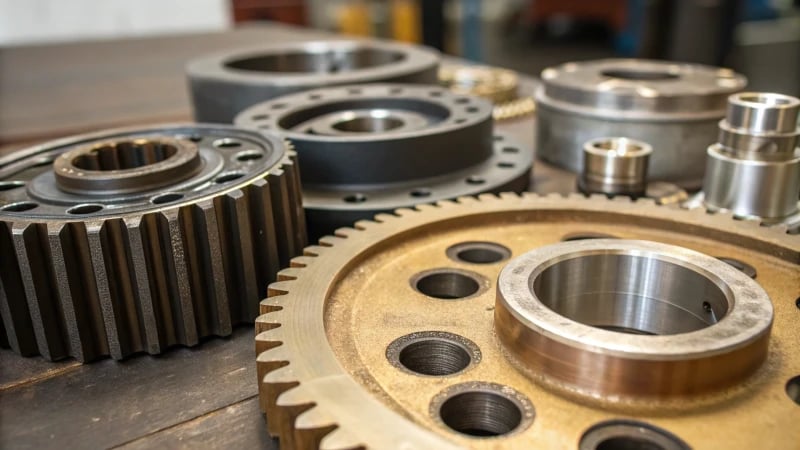
Purpose and Functional Requirements of the Product
The purpose of the product guides the choice of surface treatments. For things like car interiors or tool handles, strong materials are essential to withstand daily wear. Often, spraying or plating proves useful. These methods add style while increasing strength.
To address high corrosion resistance requirements, electroplating acts like armor, protecting from rust. This layer of plating changes everything, keeping products safe and durable, especially for items like chemical industry containers.
Electrical parts need insulation. Techniques like screen printing and laser engraving come in handy. They are non-conductive, ensuring designs remain safe and beautiful without sacrificing design elements.
For high optical performance, optical instruments focus on clarity. Perfectly polished lenses transmit light well, improving both use and style.
Product Appearance Design Requirements
Looks play an important role. Spraying lets me use different colors and gloss levels, ranging from matte to shiny surfaces. Vacuum coating gives a sleek metallic finish, ideal for premium electronics.
Treatment Type | Benefits |
---|---|
Spraying | Custom colors and gloss levels |
Vacuum Coating | Metallic sheen |
Texture changes how a product feels. Smooth finishes come from polishing, while sandblasting creates rough surfaces. These methods really alter how a product appears.
Transparency adds another challenge. Thin coatings keep clarity, especially crucial for see-through parts.
Special Functional Requirements
Some tasks need special features like anti-slip surfaces that may use texture for better grip. It’s satisfying to create surfaces that are both attractive and useful by using techniques such as bite flower processing1. Adding antibacterial agents ensures cleanliness for frequently touched items.
Each surface treatment suits specific needs while also looking good. This approach improves performance while meeting design goals. Every product becomes both beautiful and practical.
Spraying enhances wear resistance of plastic tool handles.True
Spraying forms a solid coating, improving abrasion resistance.
Metal plating is ideal for high electrical insulation.False
Metal plating reduces insulation; non-conductive treatments are better.
How Does Appearance Influence Surface Treatment Choices?
Ever thought about how a product’s appearance affects its surface treatment? It’s more than just keeping it safe. It is the meeting point of design and function, moving together in a complex way.
Look plays a key role in how surfaces get treated. It shapes how a product catches the eye, sells and feels to users. Designers need to find the perfect balance. Looks must go hand in hand with lasting strength and other important needs.
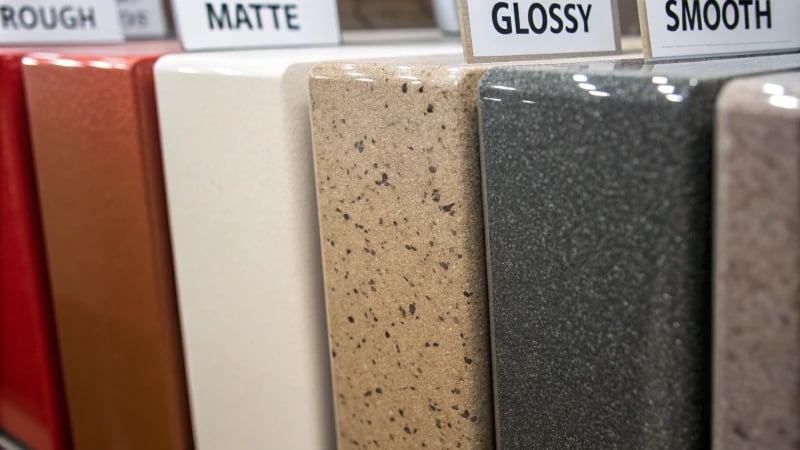
Aesthetic Considerations in Surface Treatments
Designing something new involves diving into colors, textures, and finishes. It’s like painting on a 3D canvas. The choice of surface treatment for plastic parts2 often needs a balance of color, texture, and gloss.
Aesthetic Factor | Surface Treatment Options |
---|---|
Color & Gloss | Spraying, vacuum coating |
Texture | Sandblasting, polishing |
Transparency | Optic coatings, thin films |
Balancing Aesthetics and Functionality
The main challenge is combining beauty with function. While visual appeal is essential, the primary function of a product must not be compromised. Electronic devices need non-conductive surface treatments for electrical insulation yet they also need to look stylish. Functionality and aesthetics must go hand in hand.
For products in harsh environments, treatments like electroplating3 provide both a stylish finish and necessary protection. Products remain both attractive and solid.
Unique Market Positioning Through Design
Innovation helps products shine in a busy market. Innovative surface treatments can differentiate a product in a crowded marketplace. Water transfer printing on electronics creates unique patterns that appeal to many demographics.
Luxury brands use vacuum coating for its metallic luster, aligning with their premium image. This gives products a high-quality feel while meeting needs like scratch resistance.
Importance of Texture in User Experience
Texture affects how a product feels and user interaction. A smooth feel looks nice but might slip from hands; sandblasting tool handles adds grip without losing style.
In ergonomic designs4, texture is key for comfort and safety. Products should meet user needs and look good. This careful approach keeps design exciting and rewarding.
Sandblasting improves wear resistance but affects appearance.True
Sandblasting increases surface roughness for better wear resistance, affecting appearance.
Metal plating enhances electrical insulation of plastic products.False
Metal plating reduces electrical insulation, making it unsuitable for insulating parts.
Which Surface Treatments Offer Optimal Electrical Insulation?
Have you ever looked at electronic parts and wondered how to protect them?
For the best electrical insulation, surface treatments such as screen printing and laser engraving are helpful. They keep the insulation strong. These treatments also let you add custom designs without conducting electricity. This quality is very important for electronic parts.
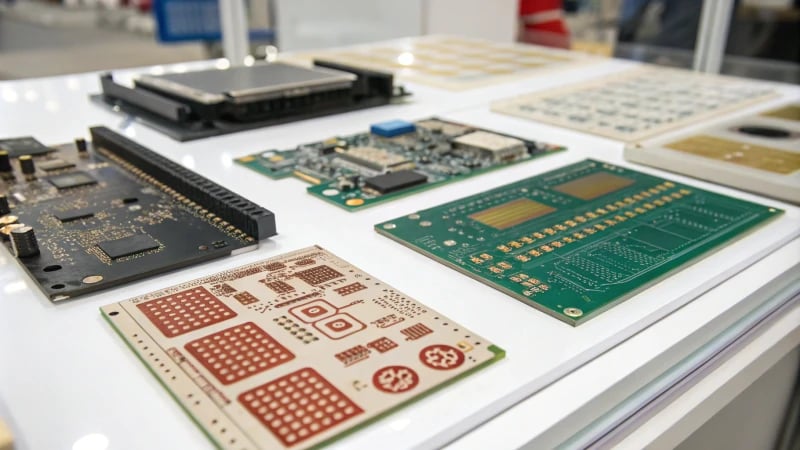
Understanding Surface Treatments for Electrical Insulation
When designing electronic components5, it’s crucial to consider how surface treatments can impact electrical insulation. Imagine working hard on something, only to find a bad surface treatment choice has ruined it. I want to save you that trouble.
Recommended Treatments:
Treatment | Benefits | Considerations |
---|---|---|
Non-Conductive Coatings | Maintains electrical integrity and offers protection against moisture and dust | Customizable for various shapes and sizes |
Why Avoid Metal Plating?
Metal plating looks nice and lasts long, but it’s not good for electrical insulation. The conductive nature of metal layers can lead to potential short circuits or electrical failures. I learned this in an early project when a great circuit board started having problems. Hence, non-conductive6 treatments are preferable.
Exploring Non-Conductive Coatings
Using coatings like silicone and epoxy seems safer. These materials block electricity and protect against things like moisture and dust. It’s like giving your parts a strong cover that doesn’t affect how they work due to their insulating properties7.
Advantages of Non-Conductive Coatings:
- They maintain the component’s electrical integrity.
- They offer additional protection against environmental factors such as moisture and dust.
- They are customizable for various shapes and sizes.
Knowing these details helps designers and makers like Jacky choose the right surface treatments for their products. This ensures that the products remain safe, efficient, and durable in their applications.
Metal plating reduces electrical insulation.True
Metal plating adds a conductive layer, compromising insulation properties.
Sandblasting improves product transparency.False
Sandblasting creates a rough surface, reducing transparency by scattering light.
How Can Surface Treatments Enhance Optical Performance?
Did you ever think about how a small change alters how we view the world on our gadgets?
Surface treatments greatly increase optical performance. These treatments cut down reflections, allow more light to pass through and guard against environmental harm. Techniques such as anti-reflective coatings and polishing really help. They improve the clarity of optical parts. They increase efficiency too.
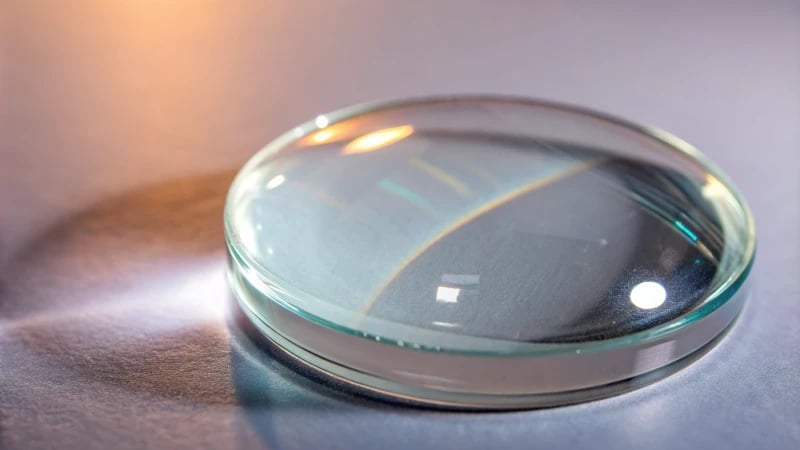
The Role of Anti-Reflective Coatings
I remember my first look through a telescope with special anti-reflective coatings. The change was really noticeable. These coatings work like magic. They cut down reflections and let more light in. This is important for devices like cameras8 and telescopes, where clarity and light transmission are paramount.
Polishing for Enhanced Clarity
Polishing is oddly satisfying. One afternoon, I polished an old pair of binoculars and the improvement was amazing. Polishing makes surfaces smooth, reducing light scattering. This is really important for applications such as laser optics and medical imaging devices where details are crucial.
Surface Treatment Techniques for Different Requirements
Choosing the right surface treatment is like picking the perfect outfit – it depends on your needs. If something must withstand daily use, like tool handles or car parts, spraying or plating probably works best. These methods add a protective layer, increasing durability while maintaining optical clarity.
Technique | Purpose | Benefits |
---|---|---|
Polishing | Clarity | Reduces light scattering |
Anti-Reflective Coating | Transmission | Minimizes reflection |
Spraying/Plating | Durability | Protects against wear |
Products used in harsh environments can benefit from treatments like chemical plating9 to resist corrosion without sacrificing transparency.
Special Functional Requirements
Products sometimes need more than just a good look. They might need to be anti-bacterial or have special textures. PTFE coatings10 resist environmental damage while staying clear. Treatment is tailored to meet specific optical performance11 goals, ensuring that products not only meet but exceed expectations in their field.
Spraying enhances wear resistance of plastic tool handles.True
Spraying forms a solid coating film, increasing wear resistance.
Metal plating improves electrical insulation of plastic shells.False
Metal plating reduces electrical insulation, contrary to requirements.
What Are the Latest Trends in Plastic Surface Treatments?
Do you ever stop and wonder how the surfaces of plastic things we use are treated? Amazing innovation occurs in this area. Creativity is pushing limits. Opportunities are being redefined.
Recent trends in plastic surface treatments focus on green innovations, better automation and using nanotechnology. These changes probably increase the lifespan, look and use of plastics. They also reduce harm to the environment. They help protect nature.
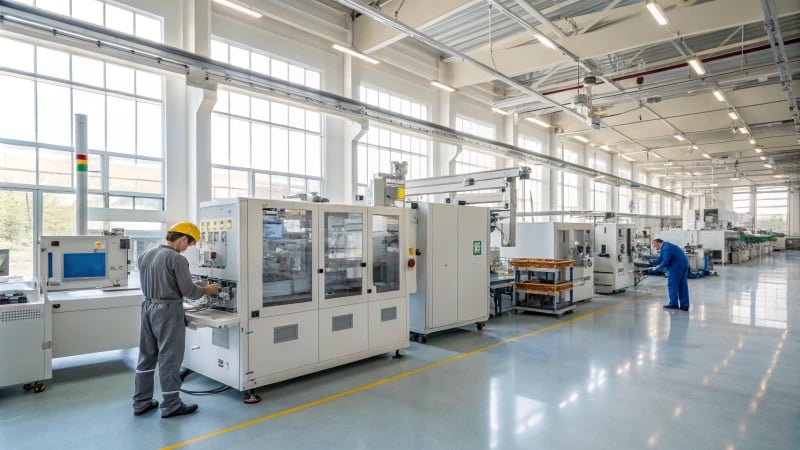
Eco-Friendly Surface Treatments
In an era of increasing environmental awareness, eco-friendly plastic surface treatments12 have gained prominence. Techniques such as water-based coatings and biodegradable films are being used to reduce harmful emissions and waste. These treatments not only preserve the environment but also offer excellent durability and aesthetic appeal.
Advanced Automation in Surface Treatment
Automation is revolutionizing plastic surface treatments. Automated systems enhance precision and efficiency in processes like spraying and plating. Using robots for consistent application13 ensures a high-quality finish, minimizing human error and production time.
Nanotechnology Innovations
Nanotechnology is paving the way for remarkable advancements14 in surface treatments. Nanoscale coatings can significantly enhance properties such as scratch resistance, hydrophobicity, and even self-cleaning capabilities. These coatings offer an unprecedented level of durability and functionality.
Multi-Functional Coatings
Modern surface treatments often incorporate multifunctional properties, combining elements like anti-bacterial, anti-fog, and anti-static capabilities in a single coating. This trend is particularly useful in healthcare and electronics industries where enhanced hygiene and performance are crucial.
Customization and Aesthetic Enhancements
Customization remains a key trend, with techniques like digital printing and laser engraving enabling intricate designs and personalized finishes. This approach meets the demand for unique and visually appealing products without compromising on functional requirements.
Table: Comparison of Plastic Surface Treatments
Treatment Type | Benefits | Challenges |
---|---|---|
Water-Based Coatings | Eco-friendly, durable | Limited color options |
Automated Spraying | Consistent quality, efficient | High initial setup costs |
Nanotechnology Coatings | Enhanced properties, multifunctional | Cost-intensive development |
Digital Printing | Customizable, intricate designs | Requires advanced equipment |
By understanding these trends, designers like Jacky can integrate innovative solutions into their work, enhancing both product performance and sustainability.
Considerations for Selection
When selecting a suitable treatment for injection-molded products, consider factors like purpose, functional requirements, and appearance. For instance, if the product demands high abrasion resistance—think about daily tools or car interiors—options like spraying or plating should be considered. Conversely, for high optical performance needs—such as those required by certain electronic displays—polishing might be more appropriate. These choices greatly impact the final product quality15.
Understanding these trends allows for informed decisions that optimize both design and manufacturing processes, ultimately leading to superior product outcomes.
Spraying enhances plastic wear resistance.True
Spraying forms a solid coating film on plastic surfaces, increasing wear resistance.
Metal plating improves electrical insulation.False
Metal plating reduces electrical insulation, making it unsuitable for such needs.
Conclusion
Choosing the best surface treatment for injection molded plastics involves balancing functionality and aesthetics, considering factors like abrasion resistance, corrosion protection, and optical clarity to enhance product performance.
-
Learn how bite flower processing can enhance grip and anti-slip features on plastic surfaces. ↩
-
Explore the variety of surface treatments available for plastic components to enhance both their visual and functional properties. ↩
-
Understand how electroplating offers both aesthetic benefits and protection against environmental factors. ↩
-
Discover how texture and design influence user comfort and safety in ergonomic products. ↩
-
Understanding electronic components’ role can help identify where optimal insulation is critical. ↩
-
This provides an overview of treatments that don’t interfere with electrical properties. ↩
-
This link explains why silicone and epoxy are preferred for non-conductive coatings. ↩
-
Explore how anti-reflective coatings significantly reduce glare and enhance visual clarity in various optical applications. ↩
-
Learn about how chemical plating can enhance durability and maintain optical properties in challenging environments. ↩
-
Discover the use of PTFE coatings for superior resistance and transparency in optical devices. ↩
-
Find strategies to maximize the efficiency and clarity of optical products through tailored surface treatments. ↩
-
Explore how eco-friendly surface treatments are reducing environmental impact while enhancing durability. ↩
-
Learn about the benefits of using automation for precision and efficiency in plastic treatments. ↩
-
Discover how nanotechnology is transforming plastic coatings with advanced properties. ↩
-
Understand how choosing the right treatment affects product quality and functionality. ↩