Do you want to change your injection-molded products into beautiful, high-quality items? Discover different surface finish choices to improve your designs!
The top surface finishes for injection molding include paint, electroplating, texture treatments and film processing. Each method provides its own unique advantages. These methods improve appearance and functionality. They also help lower costs. Learning about these options really helps in making smart choices for product designs.
I have worked in product design for many years. The right finish is very important. It is not just about how things look. It is about creating a special experience for users. This guide shows the best surface finishes. Options include vibrant paint and sleek electroplating. Each option affects both looks and function. Design a toy or a high-end electronic part. These tips probably help with good choices. These choices should connect with your audience.
Paint finishes enhance the aesthetics of injection-molded products.True
Paint finishes improve the visual appeal of injection-molded items, making them more attractive to consumers.
Electroplating is the least effective surface finish option.False
Electroplating is often considered one of the most effective methods for enhancing durability and appearance, contradicting this claim.
- 1. What Should You Really Consider When Choosing a Surface Finish?
- 2. How Do Surface Finishes Affect Product Performance and Durability?
- 3. What Are the Cost Implications of Different Surface Treatment Techniques?
- 4. Can Surface Finishes Be Combined for Enhanced Results?
- 5. What Are the Industry Standards for Surface Finishes in Injection Molding?
- 6. How Do I Select the Right Surface Finish for My Specific Application?
- 7. Conclusion
What Should You Really Consider When Choosing a Surface Finish?
Picking the best surface finish might seem too much, but it should not feel stressful! I have explored this area before. I am here to share the important aspects that truly impact your products’ performance and looks.
Consider the material properties when choosing a surface finish. Think about the intended application. It’s crucial to remember the aesthetic requirements. Also, evaluate cost-effectiveness. Reflect on the environmental impact. Check regulatory standards. These elements really matter for achieving optimal functionality and appeal.
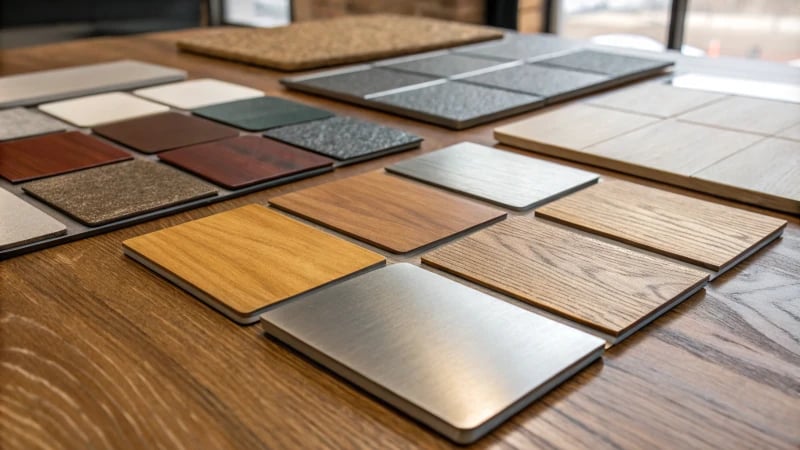
When selecting a surface finish, several factors come into play that can significantly influence the product’s functionality and aesthetics. Understanding these factors is crucial for designers and manufacturers alike.
Material Properties
The type of material used for the product is a primary consideration. Different materials react uniquely to various finishing techniques. For example, plastic can be treated with methods like powder coating1 for durability, while metals might benefit from electroplating2 to enhance appearance and corrosion resistance.
- Durability: Check how well the finish handles wear and tear.
- Adhesion: The finish needs to stick well to the base material.
Intended Application
Another critical factor is the product’s intended use. Products used in harsh environments may require finishes that enhance corrosion resistance or durability. For instance, outdoor equipment often employs powder coatings3 due to their resilience against elements.
Application | Recommended Finish | Benefits |
---|---|---|
Outdoor furniture | Powder Coating | High durability, weather resistance |
Automotive parts | Electroplating | Aesthetic appeal, corrosion resistance |
Electronic devices | Paint Finish | Customization, improved feel |
Aesthetic Requirements
The visual aspect of the product is vital, especially in consumer-oriented markets. The choice of finish can impact color, texture, and overall appeal. Methods such as spray painting4 allow for vibrant colors and textures that can attract consumers. It’s essential to choose a finish that aligns with the product’s branding and market positioning.
Cost-Effectiveness
Budget constraints often dictate the choice of surface finishes. While high-end finishes may offer superior performance and aesthetics, they can also significantly increase production costs. It’s crucial to balance quality with cost; hence, exploring decorative films5 as a lower-cost option might be beneficial for certain applications.
Environmental Considerations
With an increasing focus on sustainability, many manufacturers are considering the environmental impact of their surface finishes. Eco-friendly options are becoming more available, such as water-based paints or solvent-free coatings. Evaluating the environmental footprint of different treatments is becoming essential for many organizations aiming to comply with regulations and consumer expectations.
Regulatory Standards
Compliance with industry standards can also influence your choice of surface finish. Different industries have specific regulations regarding the types of coatings that can be used, particularly in sectors like food and pharmaceuticals where safety is paramount. Always ensure that your selected finish meets any relevant standards to avoid regulatory issues.
By considering these key factors—material properties, intended application, aesthetic requirements, cost-effectiveness, environmental considerations, and regulatory standards—you can make informed decisions that enhance both the performance and appeal of your products.
Plastic surfaces require different finishes than metals.True
Different materials react uniquely to finishing techniques, necessitating tailored approaches for plastics and metals to ensure durability and aesthetic appeal.
Eco-friendly finishes are often more expensive than traditional ones.False
While eco-friendly options may be available, they can sometimes lead to higher costs compared to conventional finishes, impacting budget considerations.
How Do Surface Finishes Affect Product Performance and Durability?
Have you ever thought about how a simple finish changes a product from common to amazing? Join me as we discover the magic of surface treatments. Surface treatments improve how things work and last in design and manufacturing.
Surface finishes influence how well a product works and how long it lasts. They improve looks and guard against damage and weather. Techniques such as electroplating and powder coating increase resistance to scratches and rust. Products typically last longer and work better with these methods. Finishes help protect and beautify.
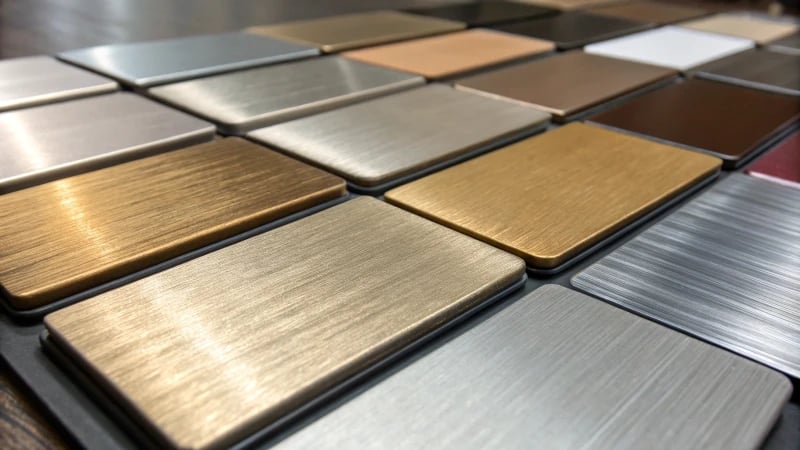
Surface finishes play a critical role in determining the overall performance and durability of products, particularly in manufacturing and design contexts. The application of various surface treatments can enhance both the aesthetic appeal and functional properties of a product. Let’s explore some common surface treatments and how they impact performance.
Paint Finish
1. Ordinary Spray Painting
Ordinary spray painting is a prevalent surface treatment that involves evenly spraying paint onto the product’s surface. This method is effective in providing a decorative finish that can conceal defects. For example, toys and electronic shells benefit from vibrant colors, enhancing their visual appeal while offering basic corrosion resistance.
2. Electrostatic Spray Painting
This method utilizes charged paint particles that adhere to the product’s surface through electrostatic forces. It is ideal for parts requiring high appearance quality, such as automotive interiors. The uniform coating results in better wear resistance, making it a preferred choice for high-end applications.
3. Powder Coating
Powder coating involves applying a dry powder that is then cured under heat, creating a thick, durable layer. This method is widely used for outdoor products as it provides excellent chemical and abrasion resistance. Common applications include metal furniture and outdoor equipment, ensuring long-lasting protection against environmental factors.
Surface Treatment Type | Key Benefit | Common Applications |
---|---|---|
Ordinary Spray Painting | Aesthetic enhancement | Toys, electronic shells |
Electrostatic Spray Painting | Improved adhesion | Automotive interior parts |
Powder Coating | Excellent durability | Outdoor facilities, metal furniture |
Electroplating Treatment
1. Chemical Plating
Chemical plating forms a metal layer on plastic surfaces using chemical reactions without electrical current. This technique enhances hardness and corrosion resistance, making it ideal for electronic connectors needing high conductivity.
2. Electroplating
Through electrolysis, this process deposits metals such as nickel or chromium on products, providing a shiny finish and improved durability. For instance, chrome-plated sanitary ware not only looks appealing but also offers enhanced corrosion resistance.
Surface Texture Treatment
1. Sandblasting
Sandblasting creates tiny pits on the surface, improving grip and aesthetics by hiding small scratches. This treatment is commonly found on tool handles and handheld devices, where user experience is paramount.
2. Leather Texture Treatment
Molding products with a leather-like texture can elevate their appearance significantly. This treatment is frequently applied in automotive interiors to enhance luxury and tactile feedback.
Film Processing
1. Protective Film Laminating
Applying a protective film to products prevents scratches during handling or use. Transparent films are popular for smartphone screens, reducing reflections while safeguarding against damage.
2. Decorative Film
Films with patterns can quickly change a product’s appearance at a low cost. For example, wood grain films are applied to home appliances to mimic the look of wooden materials.
Understanding these surface treatments and their implications on product performance can greatly influence design choices and manufacturing processes. The interplay between aesthetic enhancements and functional benefits is crucial for ensuring product longevity and user satisfaction.
Powder coating enhances outdoor product durability.True
Powder coating provides excellent chemical and abrasion resistance, making it ideal for outdoor products exposed to environmental factors.
Electrostatic spray painting improves wear resistance.True
Electrostatic spray painting results in a uniform coating that significantly enhances the wear resistance of high-quality parts.
What Are the Cost Implications of Different Surface Treatment Techniques?
Ever thought about how your choice of surface treatment techniques affects your project budget? Understanding these cost effects is essential. This knowledge allows decisions that balance beauty and practicality.
The cost of surface treatment techniques changes based on factors like material type, labor and equipment investment. Knowing these details helps in deciding the budget correctly to match your project needs and goals. It’s really important to understand these factors.
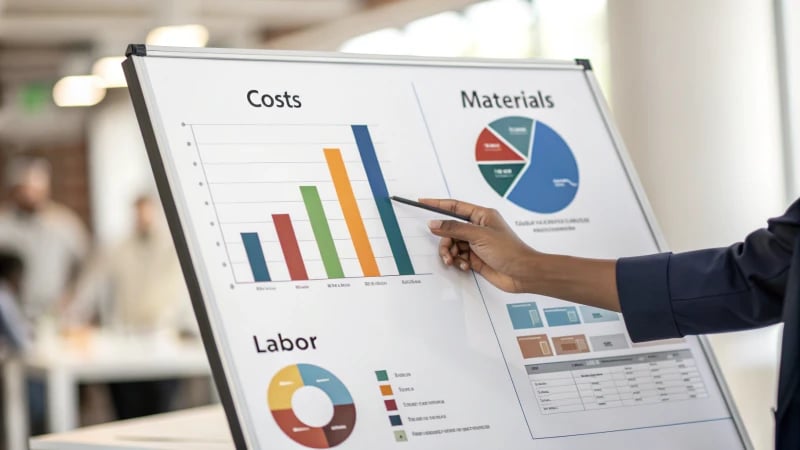
My Journey with Surface Treatments
I remember being deeply involved in a project. I was struggling with the budget while trying to create eye-catching designs. That was when I realized the importance of surface treatments. They impact not only the appearance but also the cost. Surface treatments are crucial for both looks and the overall budget. Each method comes with its own unique costs and benefits. These factors really affect how long the product lasts and how it looks. Let’s explore this topic together. I want to share what I learned during my journey.
Overview of Surface Treatment Techniques and Their Costs
Understanding the cost implications of various surface treatment techniques is essential for product designers like Jacky, who need to balance aesthetics with budget constraints. Each treatment method has its own cost structure and impact on the final product quality.
Cost Analysis of Common Surface Treatment Techniques
Here’s a detailed breakdown of some popular surface treatments:
Treatment Type | Cost Range (per unit) | Advantages | Disadvantages |
---|---|---|---|
Ordinary Spray Painting | $2 – $5 | Good decoration, covers defects | Can be labor-intensive |
Electrostatic Spray Painting | $3 – $7 | High paint utilization, smooth finish | Initial setup cost can be high |
Powder Coating | $4 – $10 | Thick, durable, excellent resistance | Requires special equipment |
Chemical Plating | $5 – $12 | Uniform coating for complex shapes | Chemical handling and safety concerns |
Electroplating | $6 – $15 | Decorative metallic finish | Environmental regulations on waste |
Sandblasting | $3 – $8 | Hides scratches, anti-slip properties | Surface roughness can be an issue |
Leather Texture Treatment | $2 – $5 | Upscale appearance | Higher mold costs |
Laser Engraving | $10 – $25 | High precision designs | Higher upfront costs |
Factors Influencing Costs
Several factors influence the costs associated with surface treatment techniques:
- Material Costs: The type of materials used (e.g., types of paint or powder) can significantly affect overall expenses.
- Labor Costs: Some treatments require more manual labor, which can increase costs. For instance, ordinary spray painting6 may be less expensive in terms of materials but requires skilled labor.
- Equipment Investment: Techniques like powder coating and electroplating may require substantial initial investments in equipment, impacting the overall cost structure.
- Volume of Production: High production volumes may reduce the per-unit cost due to economies of scale.
Budgeting for Surface Treatments
When budgeting for surface treatments, it’s crucial to consider not only the direct costs but also the long-term benefits:
- Durability: Treatments like powder coating may have higher upfront costs but can provide significant long-term savings due to their durability.
- Aesthetic Appeal: A better finish can enhance product appeal, potentially leading to higher sales prices.
- Functionality Improvements: Some treatments improve product performance, such as corrosion resistance from electroplating, which may reduce warranty claims and repairs.
By carefully analyzing the cost implications of each technique, designers can make informed decisions that align with both budgetary constraints and product requirements. Understanding these factors ensures that investments in surface treatments yield the best returns in terms of both functionality and marketability.
Further Research Recommendations
To delve deeper into cost implications and effective strategies for surface treatment selection, consider exploring:
Cost comparison of different surface treatments .
Best practices for budgeting in manufacturing .
Long-term benefits of surface finishes .
Powder coating is more expensive than ordinary spray painting.True
Powder coating costs range from $4 to $10, while ordinary spray painting ranges from $2 to $5 per unit, making powder coating pricier.
Electroplating improves corrosion resistance in products.True
Electroplating provides a protective metallic finish, enhancing durability and reducing the likelihood of corrosion-related issues in treated products.
Can Surface Finishes Be Combined for Enhanced Results?
Have you ever thought about the wonders that happen when different surface finishes mix? Let’s dive into the exciting world of surface treatments. These treatments combine to improve product performance! They really do.
Certainly! Different surface finishes together often improve product performance by using each treatment’s strengths. For instance, paint adds beauty. Electroplating provides durability. This creates a strong combination. Beauty and longevity both improve.
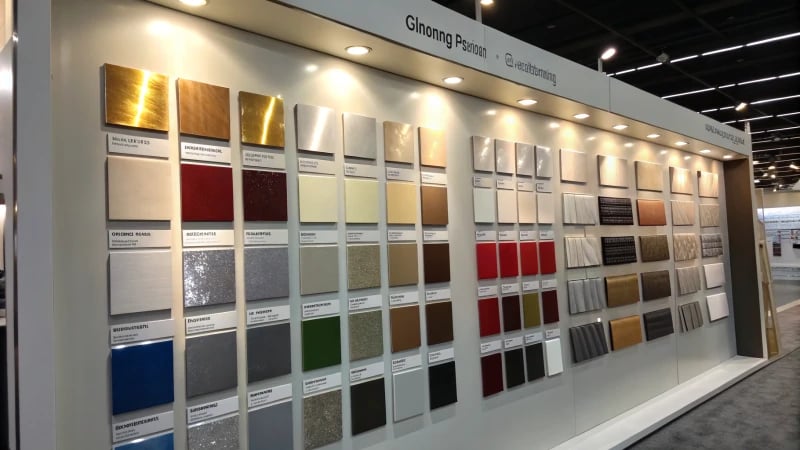
Understanding Surface Finishes
Combining surface finishes can lead to enhanced product performance by leveraging the unique benefits of different treatments. For instance, a product can gain improved aesthetics from paint finishes while also enhancing durability through electroplating.
Consider the example of automotive parts: combining electrostatic spray painting with powder coating can yield a visually appealing yet robust surface. The powder coating offers excellent chemical resistance, while the electrostatic paint can provide a smooth, colorful finish. This dual approach not only improves corrosion resistance but also elevates the product’s market appeal.
The Role of Different Treatments
Treatment Type | Key Benefits | Suitable Applications |
---|---|---|
Ordinary Spray Painting | Good decoration, color variety, covers defects | Toys, electronic product shells |
Electrostatic Spray | Uniform coating, high adhesion | Automotive interior parts |
Powder Coating | Thick, durable, chemical resistance | Outdoor furniture, industrial products |
Chemical Plating | Uniform metal layer, improved conductivity | Electronic connectors |
Electroplating | Decorative finish, enhanced corrosion resistance | Sanitary ware products |
Sandblasting | Anti-slip properties, hides scratches | Handheld equipment shells |
By exploring these combinations, manufacturers can innovate and meet the diverse needs of their products.
Enhancing Performance Characteristics
When surface finishes are combined, the potential for improved performance characteristics is significant. For example, the application of a protective film over a powder-coated surface can offer additional protection against scratches during handling. This not only extends the life of the product but also maintains its aesthetic appeal over time.
Moreover, laser engraving combined with a protective coating can enhance personalization while ensuring durability. Fine patterns or logos can be engraved, providing a unique appearance while the protective layer safeguards against wear and tear.
Considerations for Combination
While combining surface finishes can yield excellent results, there are several considerations to keep in mind:
- Compatibility: Ensure that the finishes used are compatible with each other to prevent issues such as peeling or chipping.
- Process Complexity: Combining finishes may require more complex manufacturing processes, which could impact production time and costs.
- Testing and Standards: It’s crucial to conduct thorough testing to ensure that the combined finishes meet industry standards for durability and performance.
This exploration into combining surface finishes highlights innovative practices that can lead to superior product outcomes. For further insights on specific treatments and their applications, explore our detailed analysis7.
Understanding the synergy between various surface treatments opens doors to creativity and efficiency in manufacturing. By leveraging the strengths of multiple finishing techniques, designers like Jacky can create products that not only look great but perform exceptionally well in their intended environments.
Combining surface finishes improves product performance.True
Combining different surface treatments enhances performance by utilizing their unique benefits, leading to better durability and aesthetics.
Electrostatic spray painting offers poor adhesion.False
Contrary to this claim, electrostatic spray painting provides high adhesion, making it suitable for automotive interior parts.
What Are the Industry Standards for Surface Finishes in Injection Molding?
Have you ever thought about how your favorite gadget got its shiny look? People use specific rules in injection molding to get smooth surfaces. These rules change your product’s appearance. The product looks and feels better.
Surface finishes in injection molding fall into different categories defined by SPI grades A to D. These grades set specific quality levels for different uses. High-end consumer electronics often demand a mirror-like finish. Industrial parts focus more on function.
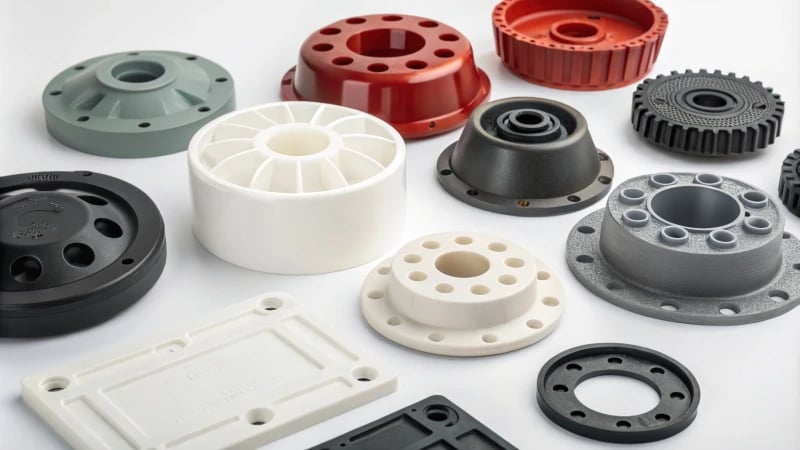
Understanding Injection Molding Surface Finishes
Injection molding is a critical process in manufacturing plastic components, where the surface finish plays a significant role in the aesthetics and functionality of the final product. Industry standards for surface finishes ensure that products meet the required specifications for quality and performance.
Key Standards: SPI Grades
The Society of the Plastics Industry (SPI) has established a grading system that categorizes surface finishes from A to D:
Grade | Finish Quality | Typical Applications |
---|---|---|
A | Mirror-like finish | High-end consumer electronics |
B | Glossy finish | Automotive interior parts |
C | Matte finish | Toys and household products |
D | Rough finish | Industrial applications and utility parts |
For example, grade A finishes are often used in luxury items where appearance is paramount, while grade D finishes may be acceptable for functional components where aesthetics are less critical.
Surface Treatment Options
Post-processing treatments can enhance the surface finish beyond the basic molding process. Here are some common options:
-
Paint Finishes: Common techniques include ordinary spray painting and electrostatic spray painting. These methods improve appearance while providing additional protection against corrosion.
- Ordinary Spray Painting: Used for colorful, decorative finishes on consumer products like toys.
- Electrostatic Spray Painting: Provides a smooth coating with better adhesion, ideal for automotive parts.
-
Electroplating Treatments: Chemical and electroplating processes deposit metal layers onto surfaces, enhancing durability and aesthetic appeal.
- Electroplating: Often applied to plastic parts in the sanitary ware industry for a mirror-like finish that improves corrosion resistance.
- Chemical Plating: Utilized for complex shapes requiring uniform metal deposition without current.
-
Surface Texturing: Techniques such as sandblasting create a textured finish that can hide imperfections and improve grip.
- Laser Engraving: Allows for high precision in adding logos or decorative patterns, enhancing brand recognition.
-
Film Processing: Protective films can be applied to prevent scratches during handling or usage.
- Decorative Films: Provide an affordable way to change the product’s appearance quickly, such as applying wood grain films to appliances.
Importance of Compliance
Adhering to these industry standards not only ensures that products meet customer expectations but also facilitates smoother production processes. Understanding these requirements can significantly impact both the design and manufacturing phases of product development.
To learn more about specific techniques and their uses, visit surface treatment options8.
In summary, knowing the standards for surface finishes in injection molding is essential for designers and manufacturers aiming for high-quality production. By leveraging various surface treatments and adhering to established standards, businesses can enhance product appeal and functionality.
SPI grades categorize surface finishes from A to D.True
The Society of the Plastics Industry (SPI) uses a grading system to classify surface finishes, impacting quality and application suitability.
Electroplating enhances durability of plastic surfaces.True
Electroplating applies metal layers to plastic, improving both aesthetic appeal and resistance to corrosion, crucial for many applications.
How Do I Select the Right Surface Finish for My Specific Application?
Choosing the right surface finish may seem overwhelming with so many choices. This task really requires patience and attention. Breaking it into small steps makes it simpler. Let me show how I approach this process!
Selecting the right surface finish needs understanding of your specific needs. Evaluate various treatment options carefully. Weigh costs against benefits. Test different finishes by creating prototypes. Consult with experts to inform your decision. Functionality and aesthetic appeal should both be present in your product design. Both should be there.
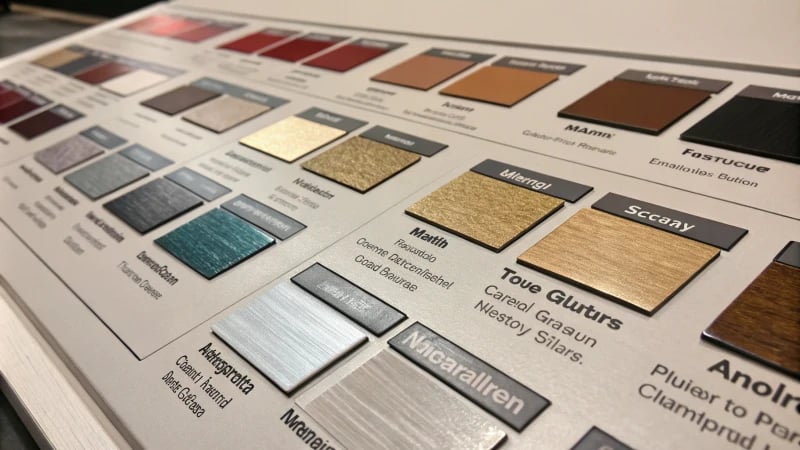
Understand Your Application Needs
Before selecting a surface finish, it is crucial to understand the specific requirements of your application. Consider the following factors:
-
Functionality: Will the finish enhance the product’s performance? For example, a rough finish may provide better grip on handles and tools.
-
Aesthetics: How important is appearance? A polished finish might be ideal for consumer products, while a matte finish could be suitable for industrial applications.
-
Durability: Will the product face wear and tear? Finishes like powder coating or electroplating can enhance durability and corrosion resistance.
Exploring these considerations will help you make informed decisions tailored to your needs.
Common Surface Treatment Options
Here are some common surface treatments you might consider:
Treatment Type | Description | Best Use Cases |
---|---|---|
Paint Finish | Ordinary spray painting for good decoration and color coverage. | Toys, electronic product shells |
Electrostatic Spray | Charged paint particles create a uniform coating. | Automotive interior parts |
Powder Coating | Provides a thicker layer with excellent chemical and abrasion resistance. | Outdoor furniture, metal structures |
Chemical Plating | Deposits metal using a chemical reducing agent without current. | Electronic connectors requiring conductivity |
Electroplating | Metal deposition through electrolysis for decorative finishes. | Plastic sanitary ware for a mirror-like finish |
Sandblasting | Creates a frosted texture, good for hiding scratches and improving grip. | Handheld equipment shells |
Laser Engraving | High precision engraving for fine patterns and logos. | High-end electronics |
Evaluating Cost vs. Benefit
While selecting a surface finish, it’s essential to evaluate the cost implications against the benefits. Higher-end finishes like electroplating may offer superior aesthetics and durability, but they often come with a higher price tag.
Consider performing a cost-benefit analysis:
- Calculate the initial costs of different finishes.
- Assess potential long-term savings through increased durability or reduced maintenance.
- Factor in the aesthetic value that might lead to higher sales or customer satisfaction.
Testing and Prototyping
Before finalizing your choice, consider creating prototypes with different finishes. Testing prototypes can reveal how each finish holds up in real-world scenarios.
- Conduct abrasion tests to see how well finishes resist wear.
- Evaluate aesthetic preferences through focus groups or customer feedback.
- Assess functionality by testing grip, visibility, and usability with each finish type.
Seek Expert Guidance
If you’re uncertain about the best choice, consult industry experts or manufacturers specializing in surface finishes. They can provide valuable insights based on your specific application and help you navigate through the options available in the market.
Consider looking into surface treatment standards9 or material properties10 to further educate yourself on the subject.
Rough finishes enhance grip on tools and handles.True
Rough surface finishes improve friction, making them ideal for applications requiring better grip, such as tools and handles.
Electroplating is the most cost-effective surface finish.False
While electroplating provides excellent aesthetics and durability, it is generally more expensive compared to other finishes like paint or powder coating.
Conclusion
Discover top surface finish options for injection molding that enhance product aesthetics and functionality while considering cost-effectiveness and environmental impact.
-
This link offers deeper insights into surface finishes’ impact on product quality and performance, perfect for enhancing your understanding. ↩
-
Explore different types of surface finishes available in the market to broaden your knowledge base. ↩
-
Learn about cost-effective finishing options that maintain quality without exceeding budgets. ↩
-
Gain insights into eco-friendly surface finishing methods that comply with environmental standards. ↩
-
Understand industry regulations regarding surface finishes to ensure compliance in your projects. ↩
-
Discover how to optimize your budget by understanding the cost implications of various surface treatment methods. This link provides essential insights. ↩
-
Discover the best practices for combining surface finishes to maximize durability and aesthetics in manufacturing. ↩
-
This link provides comprehensive information on SPI grades and their significance in ensuring quality in injection molded products. ↩
-
Explore comprehensive guides on surface finishing options and their applications to make informed choices for your projects. ↩
-
Explore comprehensive guides on surface finishing options and their applications to make informed choices for your projects. ↩