Designing plastic molded parts can feel like a daunting task, but it doesn’t have to be!
The best practices for designing plastic molded parts include analyzing product requirements, selecting suitable materials, ensuring structural uniformity, optimizing mold design, and refining production processes.
While the basics offer a solid starting point, delving deeper into each aspect can significantly elevate your design’s efficiency and reliability. Let’s explore the intricacies together!
Material selection impacts durability of molded parts.True
Material properties like chemical resistance and heat resistance determine durability.
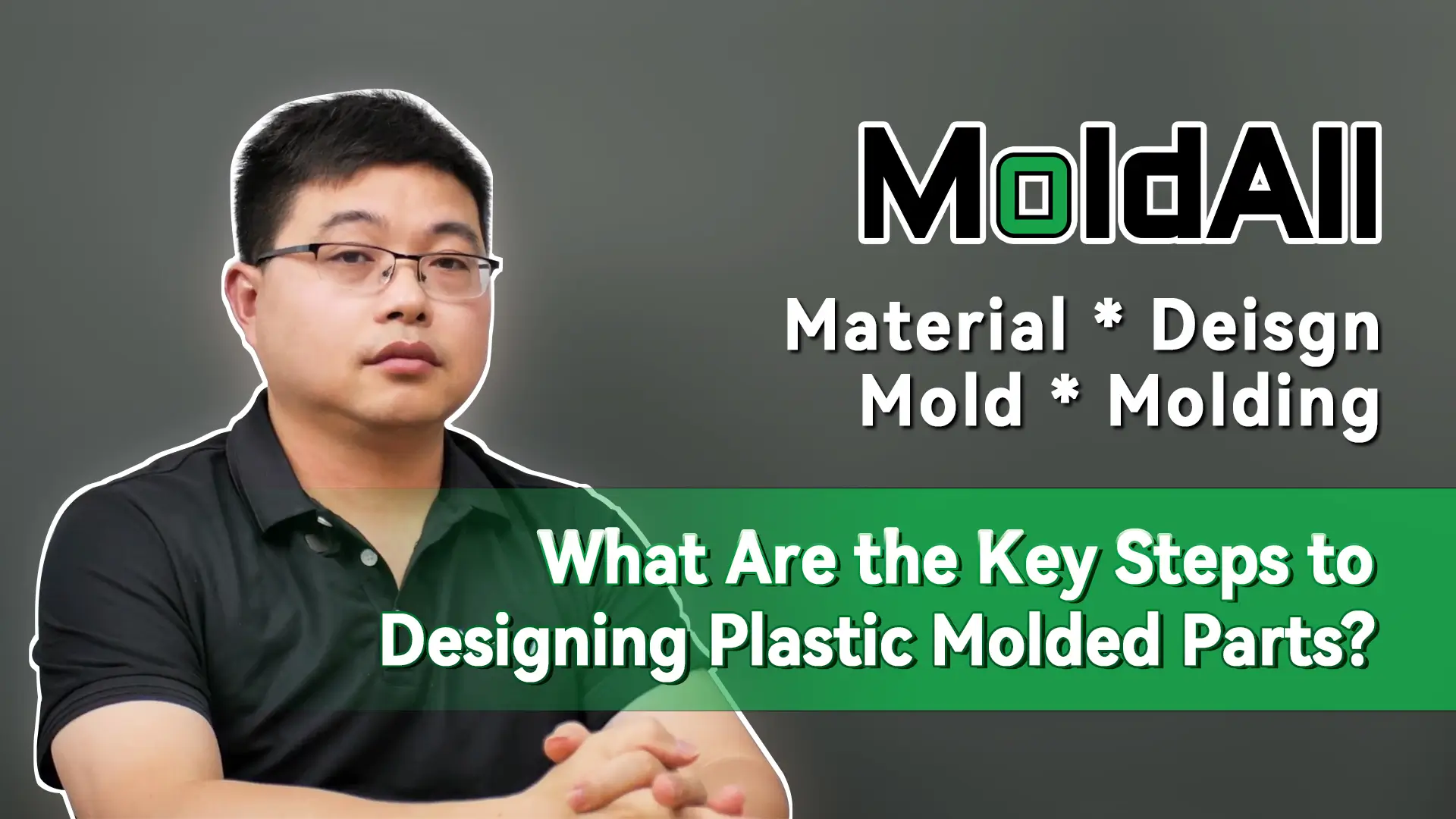
How Does Product Function Influence Design Choices?
Understanding product function is critical in shaping design decisions, particularly in plastic injection molding.
Product function dictates design choices by determining material selection, structural features, and manufacturing processes. For instance, the need for high strength or chemical resistance will guide both material and design parameters.
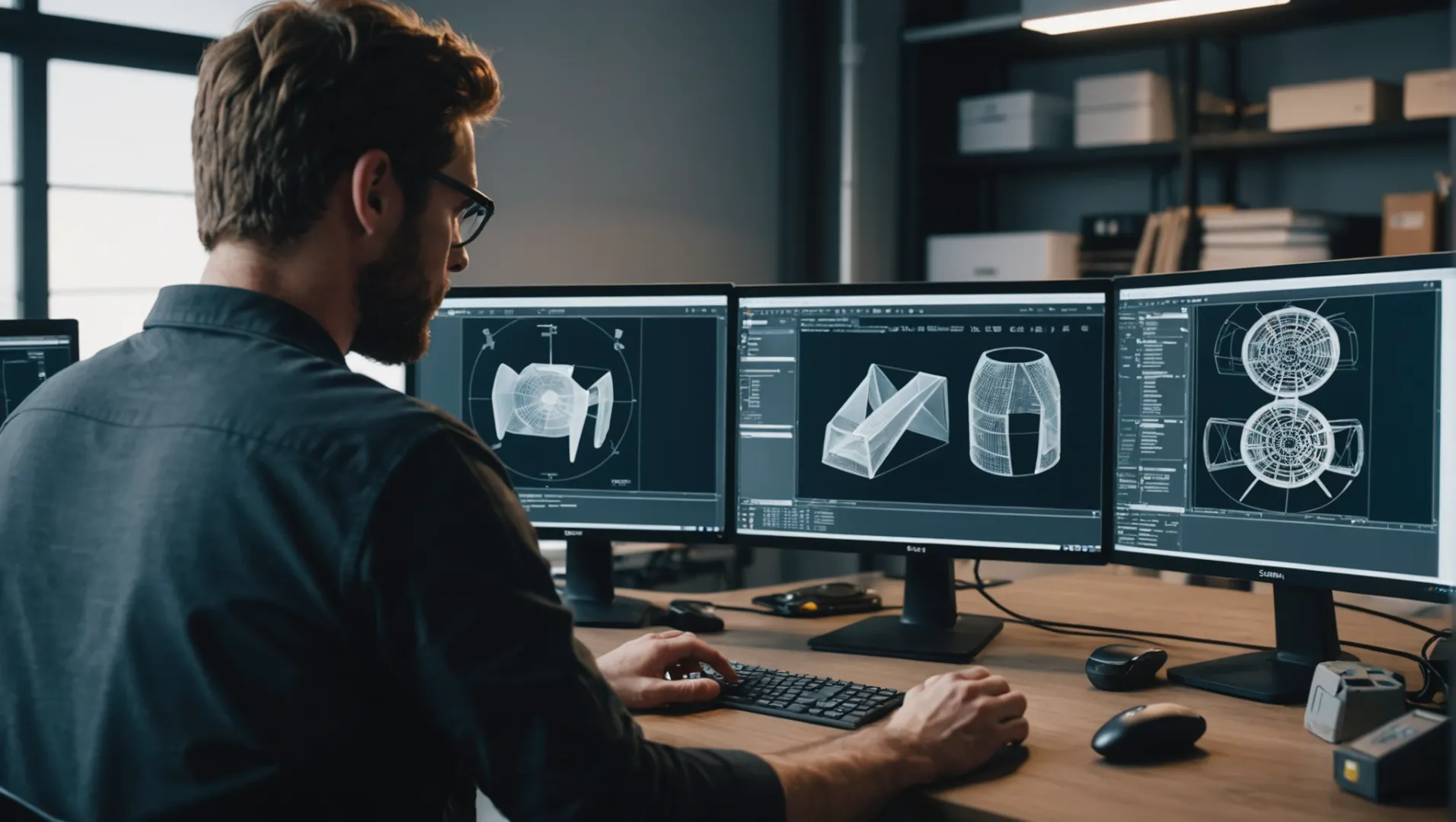
Analyzing Product Functionality
Before embarking on the design of a plastic injection molded part1, it is essential to conduct a thorough analysis of its intended function. This involves understanding the environment in which the product will operate, including stress factors, temperature variations, and potential chemical exposure.
By defining these parameters, you can establish the fundamental requirements for your design. For instance, if a product must endure significant mechanical stress, it may necessitate the use of materials with high tensile strength or the incorporation of structural reinforcements such as ribs.
Material Selection and Product Function
The role of material selection2 cannot be overstated in aligning design with product functionality. Different applications require different material properties. For example:
- Heat Resistance: Products operating in high-temperature environments demand plastics that can withstand elevated temperatures without deforming.
- Chemical Resistance: If the product will interact with corrosive substances, selecting a chemically resistant plastic is crucial to ensuring durability.
A comparative table could illustrate material options based on common functional requirements:
Functional Requirement | Recommended Material | Key Properties |
---|---|---|
High Strength | Polycarbonate (PC) | High impact resistance, clarity |
Chemical Resistance | Polypropylene (PP) | Resists acids and alkalis |
Heat Resistance | Polyetherimide (PEI) | Withstands high temperatures |
Structural Design Considerations
Structural aspects of design are equally influenced by product function. Wall thickness uniformity is a significant consideration because it affects the cooling rate and integrity of the molded part. For example, non-uniform wall thickness can lead to warping or stress concentrations.
The incorporation of features such as ribs can enhance strength without significantly increasing weight. Designing these elements requires a balance between meeting functional requirements and optimizing for manufacturability.
Manufacturing Process Alignment
Finally, the chosen manufacturing process must align with the functional demands of the product. This includes selecting the appropriate injection molding parameters and ensuring that the mold design facilitates ease of production while maintaining part quality.
Factors such as gate location and cooling system design must be optimized to enhance material flow and minimize defects.
Each design choice, from material selection to mold configuration, plays a pivotal role in ensuring that the final product not only meets its intended function but also excels in performance.
Material selection affects product function in design.True
Choosing the right material ensures the product meets its functional needs.
Wall thickness doesn't impact molded part integrity.False
Uniform wall thickness is crucial to avoid defects like warping.
What Factors Should Guide Material Selection?
Choosing the right material is crucial in plastic part design, impacting function, durability, and cost.
Material selection is guided by product function, environmental conditions, plastic properties, and cost considerations. Evaluate stress, temperature, chemical exposure, and performance needs to choose materials like ABS for strength or PP for corrosion resistance.
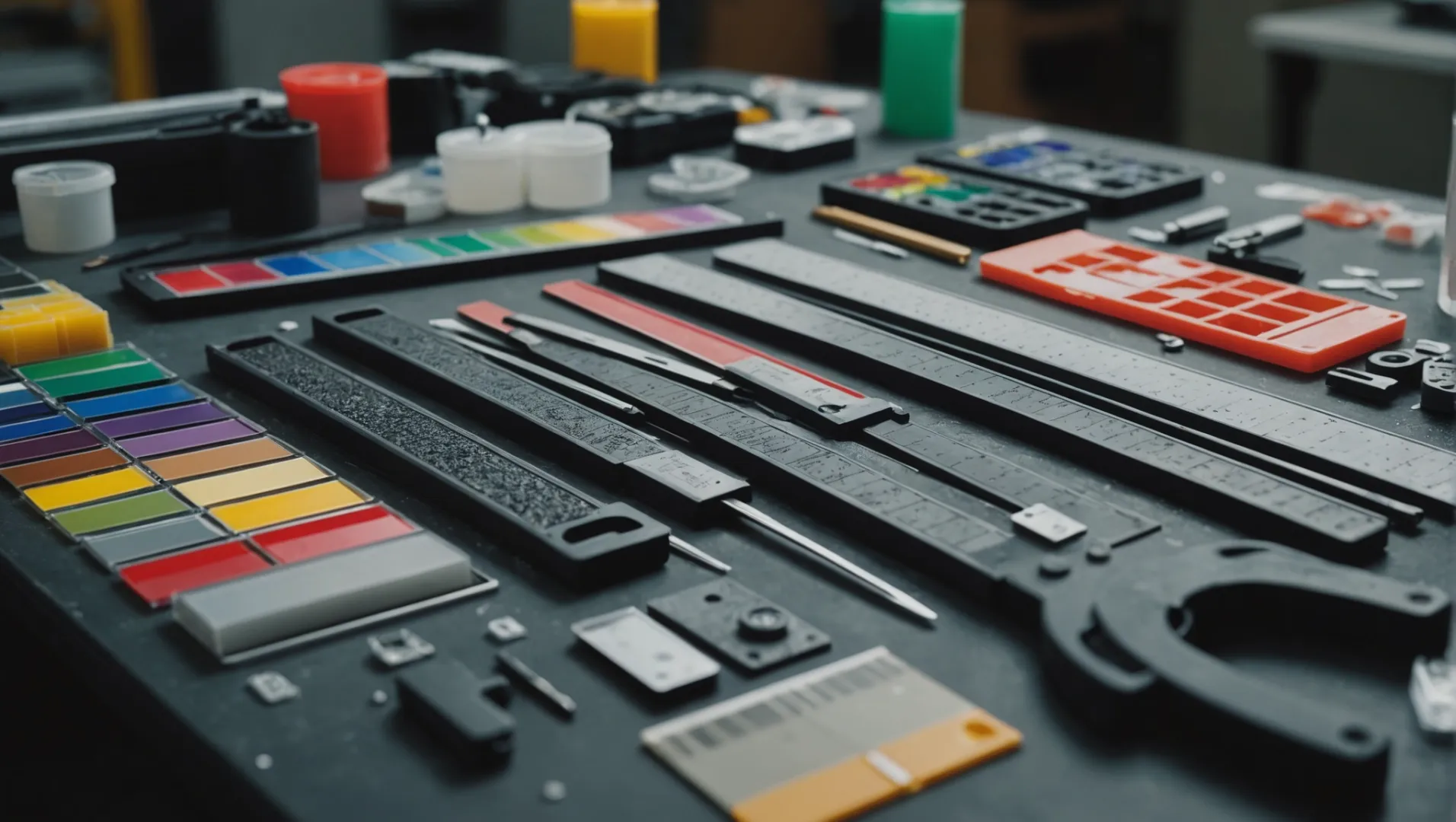
Understanding Product Functionality and Environmental Conditions
The primary guide for selecting materials is understanding the product’s intended function and the environment it will encounter. Begin by evaluating the stress levels the component will endure. For example, parts exposed to high mechanical stress might require a durable plastic like Polycarbonate (PC). If your product operates in high-temperature conditions, materials with excellent heat resistance3 are necessary.
Next, consider chemical exposure. Plastics vary significantly in their chemical resistance. For instance, if the product will contact acidic or corrosive substances, choose a material like Polypropylene (PP), known for its superior chemical resistance.
Evaluating Plastic Properties
The intrinsic properties of plastics play a pivotal role in selection. Here are key properties to consider:
- Flowability: Good flowability allows for easier molding of complex shapes and reduces defects.
- Shrinkage: Different plastics shrink at varying rates during cooling. Accounting for shrinkage ensures dimensional accuracy.
- Heat Resistance: Essential for products used near heat sources or in high-temperature environments.
- Chemical Resistance: Protects the integrity of the product when exposed to various chemicals.
Property | Ideal Material Example | Applications |
---|---|---|
High Flowability | ABS | Electrical housings |
Low Shrinkage | PC | Optical components |
Heat Resistance | PC | Electronic housings |
Chemical Resistance | PP | Food packaging, lab equipment |
Cost and Availability Considerations
While functionality and properties are crucial, cost and material availability often determine final choices. It’s essential to balance performance with budget constraints. For instance, while PC offers excellent properties, its higher cost might lead designers to consider ABS when budget limits are strict.
In conclusion, material selection is a multifaceted decision involving an analysis of functional demands, environmental conditions, and intrinsic plastic properties while considering cost efficiency. Exploring material databases4 can further aid in making informed decisions.
ABS is ideal for high mechanical stress applications.False
Polycarbonate (PC) is recommended for high mechanical stress, not ABS.
PP is suitable for environments with chemical exposure.True
Polypropylene (PP) has superior chemical resistance, ideal for such conditions.
Why Is Structural Uniformity Crucial in Molded Parts?
Ensuring structural uniformity in molded parts is key to avoiding defects and enhancing durability.
Structural uniformity in molded parts is vital to prevent warping, ensure consistent performance, and improve the overall quality of the product. It involves maintaining even wall thickness, appropriate rib design, and precise demolding slopes during the design process.
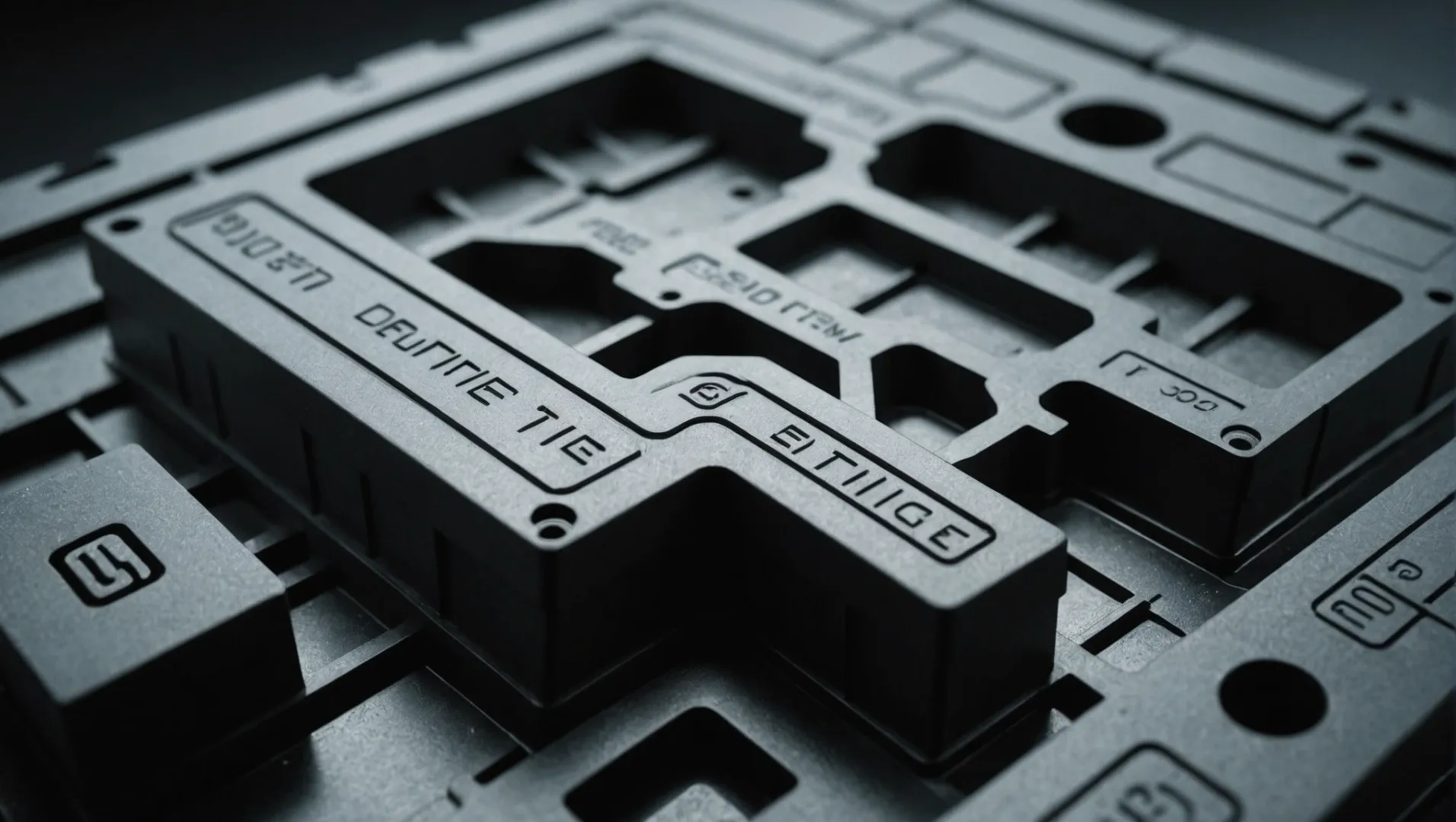
The Importance of Wall Thickness Uniformity
In the realm of injection molding, the uniformity of wall thickness5 is a fundamental aspect that directly impacts the quality and functionality of the final product. Variations in thickness can lead to uneven cooling rates, resulting in internal stresses that cause warping or deformation. For optimal results, maintaining a consistent wall thickness within a range of 1 to 6 mm is advisable.
Effects of Uneven Cooling
Uneven cooling due to inconsistent wall thickness can introduce significant issues. For example, thicker sections cool slower than thinner ones, leading to differential shrinkage which can cause warping or bending of the part. This not only affects the aesthetic but also the functional integrity of the component.
Rib Design Considerations
Ribs are often integrated into molded parts to enhance their structural strength without significantly increasing weight. However, the design of these ribs must be carefully managed to avoid stress concentration and potential cracking.
- Height and Width Ratios: The height of a rib should generally be 2-3 times the wall thickness, while its width should be between 0.5-0.8 times the wall thickness.
- Stress Distribution: Proper rib placement helps distribute stress evenly across the part, which is crucial for maintaining the integrity of complex components under load.
Demolding Slope Precision
The design of the demolding slope is another critical element ensuring structural uniformity. This feature facilitates the easy removal of parts from the mold without causing damage or distortion.
- Slope Angle: Typically, a demolding slope between 0.5° and 2° is recommended depending on material properties and part geometry.
- Impact on Surface Quality: Correctly designed slopes prevent surface damage, preserving both the appearance and functionality of the part.
Fillet Integration for Stress Reduction
Adding fillets at sharp corners can significantly reduce stress concentration areas. These rounded edges promote better material flow during molding and reduce the likelihood of cracking under stress.
A well-considered fillet radius, generally 0.25-0.75 times the wall thickness, not only enhances strength but also prolongs product life by minimizing weak points where fractures might initiate.
In summary, achieving structural uniformity in molded parts requires meticulous attention to design details such as wall thickness, rib dimensions, demolding slopes, and fillet radii. By addressing these factors, designers can significantly enhance both the quality and performance of plastic injection molded parts.
Uneven wall thickness causes warping in molded parts.True
Inconsistent thickness leads to uneven cooling, causing warping.
Rib height should be 5 times the wall thickness for strength.False
Rib height should be 2-3 times the wall thickness.
How Can Mold Design Impact Product Quality?
Delving into mold design reveals its crucial role in determining the quality of the final product.
Mold design impacts product quality through considerations like parting surface selection, gate location, cooling systems, and structural integrity, ensuring defect-free products.
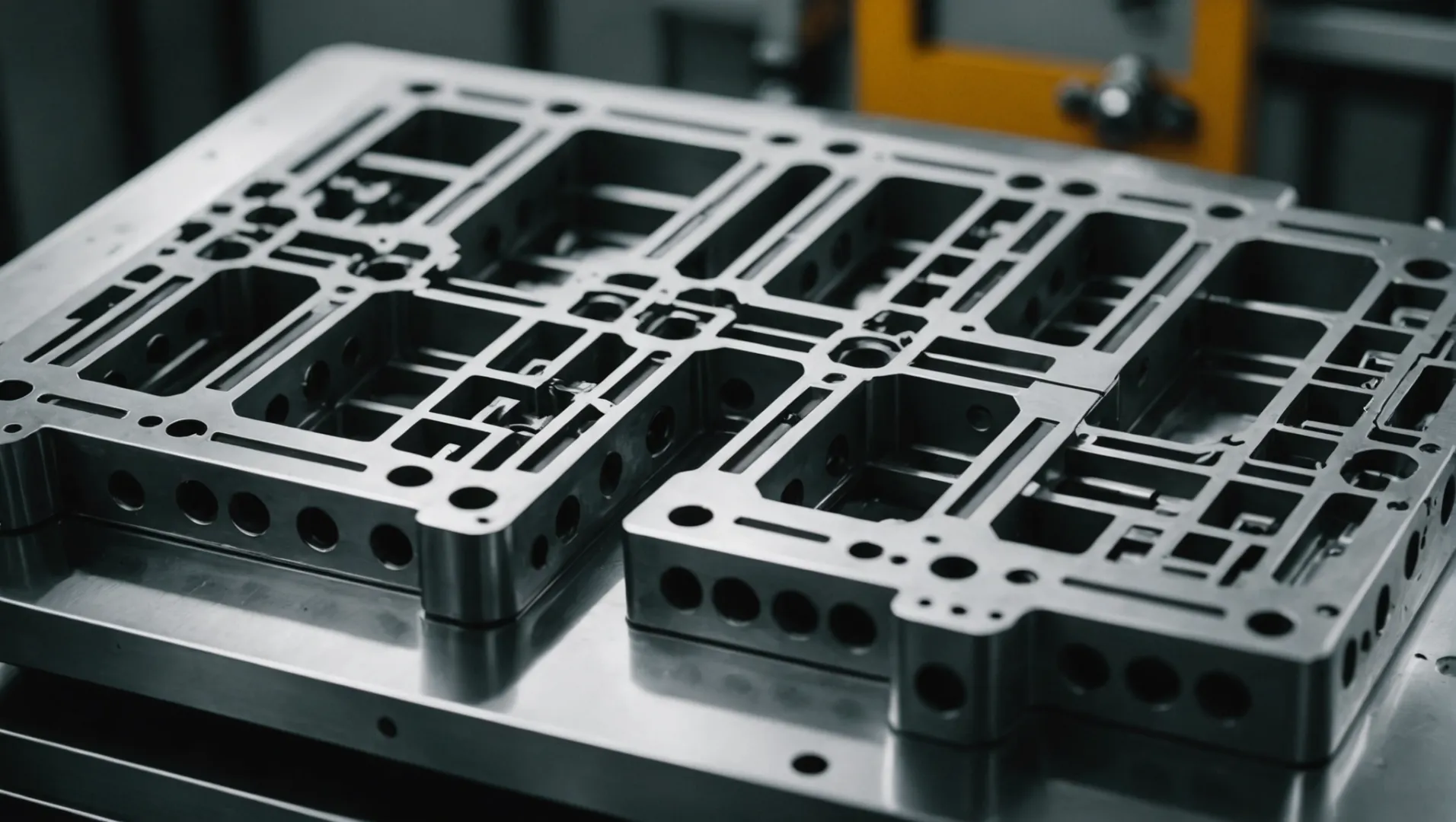
The Importance of Parting Surface Selection
Choosing the correct parting surface in mold design is critical for ensuring both functionality and aesthetics. A well-chosen parting surface facilitates seamless mold processing6 and efficient product demolding. It should ideally be at the maximum contour of the product to prevent leaving visible lines on crucial surfaces, maintaining the product’s visual appeal.
Gate Location and Types
The placement and type of gate used in mold design directly influence the flow and fill of the material. Gates should be strategically located at thicker sections of the product to aid uniform filling and avoid defects like voids or weld lines. Types of gates—such as direct, side, or point gates—must be chosen based on specific product needs and mold structures to optimize the injection process.
Gate Type | Best Use Case |
---|---|
Direct | Large parts needing high flow |
Side | Smaller parts where appearance is critical |
Point | Multi-cavity molds with a balanced flow |
Cooling System Design
An efficiently designed cooling system is paramount to achieving high-quality molded parts. This system must account for the mold’s structure, material properties, and injection parameters. By ensuring uniform temperature control throughout the mold, issues like warping or residual stress can be minimized, enhancing the overall durability and precision of the final product.
A well-planned cooling layout7 often incorporates uniformly distributed water channels to maintain a consistent cooling rate across the mold. This prevents local overheating or overcooling, which could lead to defects.
Structural Integrity and Uniformity
Ensuring uniform wall thickness is vital to avoid warping or internal stresses during the cooling phase. For instance, maintaining a wall thickness between 1-6 mm helps ensure even cooling and robust structural integrity. Additionally, incorporating features such as reinforcing ribs can improve strength without compromising on weight or material efficiency.
Designers should carefully plan these structural elements to avoid stress concentrations that could compromise the product’s integrity during use. By considering these factors, mold designers can significantly influence not only the quality but also the longevity of the injection-molded products.
In summary, every aspect of mold design—from parting surfaces to cooling systems—plays a pivotal role in shaping product quality and performance.
Parting surfaces affect product aesthetics.True
Correct parting surfaces prevent visible lines, enhancing visual appeal.
Uniform wall thickness causes warping.False
Uniform wall thickness prevents warping by ensuring even cooling.
Conclusion
By applying these best practices, you can enhance the functionality and efficiency of your plastic molded parts. Reflect on these strategies for your future designs.
-
Explore how product function shapes design in injection molding.: They assess the part design and make modifications and recommendations based on key product requirements including product usage and function. ↩
-
Learn about key factors in selecting materials for molded parts.: Use this plastic materials comparison chart to identify which injection molding materials will meet your product specifications. ↩
-
Discover top heat-resistant plastics suitable for high-temperature applications.: A thermoplastic’s chemical and heat resistance can be equal to or better than a thermoset’s. Here are five plastics that can handle the heat. ↩
-
Access comprehensive material databases to refine your plastic selection process.: Plastics Technology covers technical and business Information for Plastics Processors in Injection Molding, Extrusion, Blow Molding, Plastic Additives, … ↩
-
Learn why consistent wall thickness prevents defects like warping.: Uniform wall thickness is a critical factor in injection molding techniques. Without it, your product may have a variety of critical and non-critical design … ↩
-
Learn about optimal parting surface choices for better aesthetics and function.: Definition of parting surface The parting surfaces provide support to the mold during the injection process and help to distribute the molten … ↩
-
Understand how effective cooling prevents defects like warping and stress.: An improper injection mold cooling process, then, will almost always result in part defects that require rework or discard. The cooling process … ↩